Pages:
1
2
3
4 |
Twospoons
International Hazard
   
Posts: 1352
Registered: 26-7-2004
Location: Middle Earth
Member Is Offline
Mood: A trace of hope...
|
|
You're right, bugger it! Should have checked my references first. Did find one addtional note about bentonite though - too much can cause
problems with excessive shrinkage. No idea how much is too much - minimum effective suggested is 5%, so the 7% you used should be about right.
|
|
Cyrus
Hazard to Others
 
Posts: 397
Registered: 24-4-2004
Location: Ancient Persia
Member Is Offline
Mood: No Mood
|
|
I fired the test formula for refractory insulating firebricks today, using a wood fire in my backyard ( dug a pit and made a nice little fire.) I was
too lazy to drag out the furnace.
The brick turned out well, the only noticable problem was that I could scratch the stuff with my fingernail.
Maybe I have diamond fingernails or something. 
I coudn't break the very small, about 1 cm thick brick with one hand though, so it's not too weak, it has a nice ring when dropped (lightly
). No cracks though.
I fired a similar sized piece of normal red brick, which cracked in half, but kept its hardness. Also, I made another brick from 10 parts
"fireclay" 4 parts sand, and 1 part bentonite, this was a lousy mix, weak, hard to work, low temp. capability, it wasn't quite dry
when fired, it also cracked halfway through, later I broke it in half, but it was too hard to scratch w/ my fingernail.
I then tested the bricks in an extremely scientific way for thermal conductivity/insulation. Take torch, put on med. setting, point at brick, and
count how many seconds it takes to glow bright yellow. My good formula took 20 seconds, the bad one took 43 seconds, and the red brick never got above
dull red/orange, even after 65 seconds. I would add more sawdust or something like perlite, the brick is plenty crush resistant, it just isn't as
scratch resistant as I would like. I then took the bricks to test them for thermal shock. (my standard test, heat an edge as hot as I can and throw in
bucket of cold water) They all passed. Nothing has ever failed that test, I need a better one.
However, after the lousy formula brick was heated up to yellow heat, it turned soft and crumbly. The "fireclay" I got for free is
worthless. Oh well. Dental cement coming soon.
Another thing, supposedly kyanite or mullite, which is calcined kyanite, hold the clay body together well and prevent cracking from thermal shock.
I'll test that too, both for crucibles and for insulating refractory.
|
|
uber luminal
Hazard to Others
 
Posts: 124
Registered: 25-8-2004
Member Is Offline
Mood: No Mood
|
|
Metalcasting molds
Fair enough.
I didnt post this here becuase molds is something totaly different than crucibles... as you can cast glass or polymers... but anyway,
I wondered... what do you use to cast into?
The typical answer I read about is, to use a fireclay(and sand) which I assume is a Mg based clay. well turns out, no one in my area sells this
magical Fireclay. I was told by distributors that it no longer had a safety or use rating, and thus no one used it anymore. all that was sold was fire
cement, or premade bricks. One vendor told me they could ship in 2 bags of it... for $10 a bag... and $108 shipping.
I have used sand/clay dug up out of river banks, and this seems to work ok, except when i cast with this, the castings form cracks and look like crap.
I am looking for something that can replace the "green sand" that is typically used, such that I can mold something, cast it, and tear down
the mold and reuse the same mold material (it doesnt perminatly harden)
|
|
Cyrus
Hazard to Others
 
Posts: 397
Registered: 24-4-2004
Location: Ancient Persia
Member Is Offline
Mood: No Mood
|
|
Quote: | Originally posted by uber luminal
I am looking for something that can replace the "green sand" that is typically used, such that I can mold something, cast it, and tear down
the mold and reuse the same mold material (it doesnt
perminatly harden) |
Greensand is the way to go.
It's good.
That's why everyone uses it.
You don't WANT to use fireclay, it permanently hardens at high temps.
Bentonite is much better. Any pottery supplier near you should have some.
If not, you only need like 5-10 lbs per 100 lbs of sand, so shipping woudn't be that bad. Use as little water as you can, and yet have it hold
together well, and as fine of SILICA sand as you can, ok 400 mesh is too small, 100 mesh should be fine.
If for some reason this doesn't work, make investment mold stuff from plaster of paris, sand, maybe perlite, etc. This will harden, but if you
crush it up, and heat it in an oven, it can be regenerated.
Anyone have any other suggestions?
|
|
Tacho
National Hazard
  
Posts: 582
Registered: 5-12-2003
Member Is Offline
Mood: No Mood
|
|
Quote: | Originally posted by Cyrus
If I am understanding the site correctly, I just have to mix about 70 % Al2O3 with CaO and H3PO4 so that when heated, Ca3(PO4)2
is formed as a binder for the alumina.
|
I did a test with hardware store lime (hopefully CaOH). I figured since common phosphoric acid has 20% water anyway, it didn't matter if it was
CaO or its hydratated form.
The reaction is one of the most exotermic I have seen without fire. It melted the plastic pot immediately.
Gas evolved, I don't know why. Maybe my lime was mixed with carbonate, maybe it was the water boiling away under the heat.
I had to add some water to continue the reaction. There was NO imediate hardening. I'll check tonight.
|
|
Twospoons
International Hazard
   
Posts: 1352
Registered: 26-7-2004
Location: Middle Earth
Member Is Offline
Mood: A trace of hope...
|
|
Its possible it was all carbonate. Did it say 'lime' (the carbonate) or 'slaked lime' (the hydroxide) ?
|
|
Tacho
National Hazard
  
Posts: 582
Registered: 5-12-2003
Member Is Offline
Mood: No Mood
|
|
Quote: | Originally posted by Twospoons
Its possible it was all carbonate. Did it say 'lime' (the carbonate) or 'slaked lime' (the hydroxide) ?
|
Oh, there is no such ambiguity in portugese. It was the hydroxide, but not reagent or technical grade, just construction stuff.
|
|
ignaro
Harmless
Posts: 14
Registered: 31-8-2004
Location: Argentina...¡Ay!
Member Is Offline
Mood: confused
|
|
Quote: |
Oh, there is no such ambiguity in portugese. It was the hydroxide, but not reagent or technical grade, just construction stuff.
|
There is another ambiguity (a similar one exists in spanish):
There are three limes, I don't know the english names:
-Cal Gorda: made form nearly pure calcium carbonate
-Cal Hidráulica: made from calcium carbonate + 10% to 20% clay
-Cal Magra: made from calcium carbonate + silicium oxide + iron oxides + clay
Problema Insoluble: Denominación habitual para los problemas mal planteados.
|
|
Tacho
National Hazard
  
Posts: 582
Registered: 5-12-2003
Member Is Offline
Mood: No Mood
|
|
Quote: | Originally posted by ignaro
There is another ambiguity (a similar one exists in spanish):
There are three limes, I don't know the english names:
-Cal Gorda: made form nearly pure calcium carbonate
-Cal Hidráulica: made from calcium carbonate + 10% to 20% clay
-Cal Magra: made from calcium carbonate + silicium oxide + iron oxides + clay |
Well, here it goes like this:
"Cal virgem": Calcium oxide - or xxxx-lime
"Cal hidratada" : Calcium hidroxide- or yyyy-lime
I believe they are made FROM calcium carbonate by calcination ( CALcination... humm... I see historical roots here...), and they become hard by
reacting with CO2 in air to become carbonates again.
Carbonate rocks are "calcários" - or zzzz-lime.
|
|
ignaro
Harmless
Posts: 14
Registered: 31-8-2004
Location: Argentina...¡Ay!
Member Is Offline
Mood: confused
|
|
I'am sorry, I don't stated it: Gorda, hidráulica and magra are portuguese words.
(They are also spanish words, with similar meaning, but not strictly related to masonry)
Gorda is used for walls, because it uses CO2 from air.
Hidráulica is used for walls and understructures, because it don't need CO2; it is similar to a portland cement.
Problema Insoluble: Denominación habitual para los problemas mal planteados.
|
|
Cyrus
Hazard to Others
 
Posts: 397
Registered: 24-4-2004
Location: Ancient Persia
Member Is Offline
Mood: No Mood
|
|
Hmm, nice little language discussion.
Anyways, I've been in my "lab" doing more tests, see backyardmetalcasting, but I have to say that the phosphate bonded dental
investment stuff is GREAT!
An hour or two after mixing it, I was hitting some with a hammer to get it from its mold, and it wouldn't budge, I had to drill it out! Today
I'll mix up some clay/graphite/kyanite/grog batches, more details to come. (Of course)
|
|
sarcosuchus
Harmless
Posts: 25
Registered: 16-9-2004
Location: in server hell
Member Is Offline
Mood: sleepy
|
|
some were on a cd ive got is the step by step process for making rocket nozzels useing the al2o3-sodium silicate mix.thought about makeing my own
grinding wheels but it should make real good cruibles for melting all kinds of stuff.l will track it down and upload to ftp as soon as possible
famous last words\"hold my beer and watch this\"
|
|
JohnWW
International Hazard
   
Posts: 2849
Registered: 27-7-2004
Location: New Zealand
Member Is Offline
Mood: No Mood
|
|
Actually, Tacho, Portland cement, the principal ingredient of which is burnt lime, or quicklime, CaO, forms concrete with an aggregate of crushed
rock and sand, or bonds with sand alone to form mortar, on the addition of water (which hydrates it to slaked lime), does so by reaction with the
silica in the sand and crushed rock. It forms calcium silicates, e.g. Ca2SiO4 and CaSiO3 (wollastonite) along with mixed silicates, which crystallize
when the stuff sets. Burnt lime or quicklime is "cal viva" in Spanish and Portuguese.
Other ingredients in Portland cement include gypsum, which is sparingly soluble CaSO4.2H20 which dissolves and then resets; and clinker (slag left
over from steelmaking). Some types also contain powdered clays.
John W.
|
|
ignaro
Harmless
Posts: 14
Registered: 31-8-2004
Location: Argentina...¡Ay!
Member Is Offline
Mood: confused
|
|
And because of such calcium silicates "cal hidráulica" is similar to portland cement.
I find the english name for it: "hidraulic lime". A little obvious, but the earlier term used by Smeaton was "water lime".
Problema Insoluble: Denominación habitual para los problemas mal planteados.
|
|
Gyro
Unregistered
Posts: N/A
Registered: N/A
Member Is Offline
|
|
General Casting and Crucible info
I'm enjoying this thread -- the range of inquiry is fascinating, and revealing some useful chemical and formulation info.
I'd like to add, from a practical standpoint, a few comments for anyone wishing to cast right now, using simple equipment.
I've built a Gingery lathe from scratch, a milling attachment, and a Tesla disk turbine -- all from castings in a charcoal furnace. Some of the
info is available on my website www.sredmond.com .
1.) I've cast probably a hundred aluminum parts using a cast iron crucible -- an ordinary plumber's lead pot. It shows little deterioration.
2.) For crucibles, I've also used at times, food cans, stainless steel canisters (ala Wal-Mart), and a 5" long section of 4" diameter
iron pipe, with a steel bottom welded in.
3.) I have used both fireclay and bentonite for greensand formulation. Both have produced excellent results.
There are a few things to note which I believe have affected the varied results reported here.
First, "fireclay" is a nonspecific term. I recently bought a bag of so-called fireclay from a masonry supplier, which was completely
useless. Yet I earlier bought a bag of AP Green Co. fireclay from a pottery supplier which enabled me to build both my foundry, produce a good quality
greensand and cast my lathe.
The "bad" fireclay wasn't even all clay -- it contained what looked like grog, fines, and other diluents. When I called the
manufacturer (Koppel) the person I spoke to said that it was intended only for plugging old wells, and did contain broken chimney tiles from their
casting operation. Obviously, it's a stretch to call something "clay" that is already vitrified! The greensand I mixed with it had no
bond strength to speak of. A waste of time and money.
If you want to be sure of obtaining a real fireclay, potters use specific named clays which are equivalent. One of them is called Hawthorn 30 or 35.
This is available at ceramic suppliers.
If you want to use a steel or stainless steel crucible to melt aluminum (which I do) and do not mind the somewhat lower purity and quality of the
castings (which I do not), then there are two factors to pay attention to.
The first is that pressure and volume of blast will determine the relative lifespan of any crucible. The second is that crucible wall thickness will
do the same.
With a high pressure blast you can easily exceed 1500 C locally, and in fact burn your crucible right up. Steel burns. Stainless steel burns. You can
put a hole in a crucible of thin stock quite easily, with a high directed blast. If the high localized pressure is coupled high blast volume, then you
will oxidize not only your crucible wall but also your melt.
Blast pressure should be modulated to produce a somewhat reducing atmosphere to protect both the crucible and the melt. Throttle down to get good
mileage! I do this by making the blast pipe discontinuous, and simply moving my air source pipe away from the tuyere source pipe. I adjust continually
to keep a moderate heat going -- especially for aluminum. Heck, it melts at a low enough temp. You don't need steel melting temps. In fact you
can even melt it without a blast in a simple wood fire pit outdoors.
The second factor -- crucible wall thickness also adds to the lifespan. A thicker crucible will spread the heat better than a thin one. Generally
there's a hotspot where fuel and blast come together, and most simple charcoal furnaces will have a crucible sitting on top of fuel, and only one
tuyere blast source. This creates a hot spot that, in a thin can type crucible, will melt through in short order. Again reducing the blast will help
some, and baffling or orienting the blast tangentially will also improve crucible longevity.
I like bentonite a little better than fireclay for greensand, because it has higher bond strength, and requires less water, however, perfectly good
aluminum castings can be made from fireclay greensand as well. Just be sure to get good fireclay. I have never had the post-melt "fire
hardening" problems some others have with fireclay with aluminum melts. I can crumble the greensand fairly easily and break out the casting
without problems -- but perhaps I don't ram as hard as others -- or my fireclay is different than theirs. In fact, if I return the lumps to the
greensand bin, overnight the humidity softens the lumps to sand consistency again. Yes, I return all sand. Eventually the bond strength reduces, and I
rejuvenate with a little more pure clay. The day will come when this won't work, but a LOT of castings will have come off the line before I reach
that point, in my experience.
I would strongly recommend than anyone considering casting read Dave Gingery's book on building a charcoal foundry. It's inexpensive, and
contains most of what you need to know.
Steve Redmond
|
|
Theoretic
National Hazard
  
Posts: 776
Registered: 17-6-2003
Location: London, the Land of Sun, Summer and Snow
Member Is Offline
Mood: eating the souls of dust mites
|
|
Just a suggestion: to get a very hot flame, cheat and use H2 + air/H2 + O2.
|
|
Cyrus
Hazard to Others
 
Posts: 397
Registered: 24-4-2004
Location: Ancient Persia
Member Is Offline
Mood: No Mood
|
|
That's not very practical for most of us, right now I'm working on an oil burner, it'll probably be forced air powered, but a natural
aspirated oil burner is my goal.
I'm still testing ceramic crucible mixes.
BTW clay graphite has better thermal shock resistance than SiC, so that's what I'm working on mostly.
The cera-fina works ok, but is not quite as strong as clay when fired. The best results so far are with about 30% graphite.
And here's a page that is just beautiful!
Enjoy!
http://budgetcastingsupply.com/images/Crucible_Data_Bartley-...
One thing I'd like to clarify about the alumina crucible method proposed by BromicAcid (sodium silicate bonded)- Alumina isn't fluxed by
sodium silicate.
That means the flux is just melting and holding the alumina particles in a glass.
I'm also experimenting with different insulation methods, since perlite melts at too low of temperatures, I'm testing using little styrofoam
spheres to provide porosity.
More to come of course...
[Edited on 20-10-2004 by Cyrus]
|
|
Oxydro
Hazard to Others
 
Posts: 152
Registered: 24-5-2004
Location: NS, Canada
Member Is Offline
Mood: distracted
|
|
(a bit off topic)
Oil burner you say Cyrus... I actually managed to make one of those this past summer. It worked, to a limited extent -- there were problems of fine
tuning that I never got around to fixing.
I already had a charcoal fired furnace (really crappy one, made it out of what I had lying around which meant just "heatsink" concrete), and
to convert it to oil I fed a spiral of copper pipe down the inside, hammered to a small nozzle at the bottom. It was fed from a pop-bottle funnel
with a valve connecting the pipe to the cap of the bottle.
Initially, it worked ok, but it was limited, because after a while, the copper would heat up so much it would start boiling the oil inside it, and the
pressure kept the oil out of the pipe. I really needed a pressurized system or a pump.
Then I screwed up the nozzle design trying to tune it, and I haven't been back to it since... work got in the way and now I've moved away
from my parent's house where it lives. I'm looking to aquire a burner from an oil-fired water-heater and build a better system around that.
[Edited on 20-10-2004 by Oxydro]
|
|
Cyrus
Hazard to Others
 
Posts: 397
Registered: 24-4-2004
Location: Ancient Persia
Member Is Offline
Mood: No Mood
|
|
Yes, I thought of doing something like that, but the copper pipe would be in a burner tube, not the furnace. The problem I discovered is that oil
decomposes around its b.p. or lower to form a black shiny (carbon containing of course) lacquer that sticks to copper very well.
In other words, the pipe will clog over time.
The only solution is to either inject the oil at a low temperature using an atomizing nozzle or injecting it into a chamber at very high temperatures
(the burner) - high enough that the carbon formed will burn off. For this method you will also need an oxidizing atmosphere and lots of turbulence IMO.
I'm making a "test bed" burner to test both designs. For an example of the latter design, see backyardmetalcasting.com (the ursutz
burner)
Also, see the forum on the same site for more of my and others ideas for oil burners.
You know, I ought to start an oil burner thread.
|
|
Cyrus
Hazard to Others
 
Posts: 397
Registered: 24-4-2004
Location: Ancient Persia
Member Is Offline
Mood: No Mood
|
|
I STILL think sugar will work for a phenolic resin! I did some tests today,
and if there were only a way too keep it from bubbling so much, it would be very nice- maybe using a lot of aggregate and little sugar will help.
I've been slip casting a few crucibles out of clay, and even coil-building them! (artistic, I know ) They are about 1.5 mm thick after 10 minutes, I think the clay is too fine, I'll have to try some EPK. I
haven't tried slip casting clay-graphite yet.
The oil burner got fired today, it's sooo cold outside, I think that may have been part of the problem- there was "burning" going on,
but the oil wouldn't vaporize fast enough to create a good flame. I wasn't using my McDonald's oil because it's a solid at STP!
  The only other oil available was waste car oil, which isn't nearly as
energetic.
|
|
rift valley
Hazard to Others
 
Posts: 103
Registered: 24-7-2004
Location: NH
Member Is Offline
Mood: semiconducting
|
|
Today I was in a rush to get some metal melted so I could cast a sculpture for a school project. With no suitable crucible in sight I noticed my
nickel crucible. Nickel melts at +1400 degrees so it should be fine to melt some Al right? I only paused to wonder if the liquid Al might form an
amalgam with the nickel, but it wasn't long before I continued on anyway. Once my furnace got cooking I left to heat up for about a half an hour.
When I got back the furnace was at an extremely bright orange heat, almost yellow. This is what I found.
What was once this

was now this
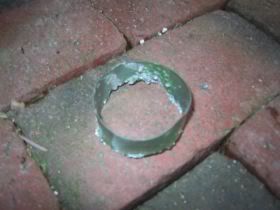
With this in my furnace (cleaning this is going to be a B****, any ideas? I will probably heat the metal up just below its MP so I can easily break it
out)
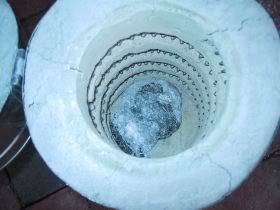
Any ideas on why this happened did the aluminum form an amalgam with the nickel (I thought nickel was very corrosion resistent, or does that not
matter if we're talking about amalgams?) The hottest the furnace could have got up to is around the 1100C range and it was probably well short of
that.
Thanks,
Paul
|
|
Polverone
Now celebrating 21 years of madness
       
Posts: 3186
Registered: 19-5-2002
Location: The Sunny Pacific Northwest
Member Is Offline
Mood: Waiting for spring
|
|
Quote: | Ellern's discussion on p. 279 of "Military and Civilian
Pyrotechnics":
"Mellor cites the phenomenon of a temperature rise of 30 g of molten gold at
1155 deg. C. after addition of only 0.3 g of aluminum. The latter, being cold,
caused an initial drop to 1045 deg., whereupon the tepmerature rose to 1380
deg. C. A perusal of Circular 500, as well as of the bnooks by Kubachewski and
Evans and Kubachewski and Caterall, shows numerous strongly exothermic reactions
between metals as expressed by the heat of formation of arsenides, antimonides,
bismuthides, aluminides, and others."
Palladium and aluminum alloy exothermically, the basis of the article called
Pyrofuze, described ibid., p. 207. Nickel and aluminum alloy exothermically, the
basis of the Pyronol torch. S. H. Fischer and M. C. Grubelich have listed
extensive data on exothermic intermetallic reactions in their article
"Theoretical Energy Release of Thermites, Intermetallics, and Combustible
Metals," pp. 231-286, Proc. Twenty-Fourth International Pyrotechnics Seminar
(1998). |
http://groups.google.ca/groups?hl=en&lr=&selm=cfmi9b...
Note that Ellern's book is available on the FTP site, though I don't recall if it contains any additional information.
PGP Key and corresponding e-mail address
|
|
12AX7
Post Harlot
   
Posts: 4803
Registered: 8-3-2005
Location: oscillating
Member Is Offline
Mood: informative
|
|
Referring to: http://web.met.kth.se/dct/pd/element/Al-Ni.html
You can clearly see that aluminum and nickel have pretty good solubility. Contrast to something like iron, commonly used for crucibles:
http://web.met.kth.se/dct/pd/element/Al-Fe.html
"Bright orange almost yellow" I would call 1800-1900°F = 1000°C. Iron is barely 20% soluble, while nickel is up at 40%. Especially with
such a thin crucible, it simply passed right on through!
I've had tin cans look the same way, just a cylinder left above the liquid level. The trick is to oxidize it before use so you get a layering of
Fe:FeO:Al2O3:Al, rather than Fe immediately touching the Al melt, allowing it to dissolve. Now, I don't know how much nickel will oxidize, but
if it doesn't, I can promise trouble.
So um, yeah... not much else to say besides condolences to your crucible.
BTW, nickel (or more accurately, the Al3Ni particles) will probably strengthen the metal, if you intend to keep it. I'm not sure how much, more
than 1% might embrittle it.
Tim
|
|
chemoleo
Biochemicus Energeticus
   
Posts: 3005
Registered: 23-7-2003
Location: England Germany
Member Is Offline
Mood: crystalline
|
|
That's very interesting, to see this happening at a large scale like this. There's been a thread on intermetallic reactions, have a look at
this (for lateron, thread ID 2202). It also lists the energies generated between the different metals when fusing.
[Edited on 24-3-2005 by chemoleo]
Never Stop to Begin, and Never Begin to Stop...
Tolerance is good. But not with the intolerant! (Wilhelm Busch)
|
|
fizzy
Harmless
Posts: 9
Registered: 10-3-2005
Member Is Offline
Mood: bubbling
|
|
"Corelle ware" crucibles?
I seem to remember that Corning Corelle ware is basically fused silica that has been allowed to do some crystallization.
Is that correct?
Could corelle coffee cups be used as small crucibles?
Up to what temperature?
After all these are only a dollar apiece at the local Salvation Army or Goodwill store.
|
|
Pages:
1
2
3
4 |