Pages:
1
2 |
Magpie
lab constructor
   
Posts: 5939
Registered: 1-11-2003
Location: USA
Member Is Offline
Mood: Chemistry: the subtle science.
|
|
Assuming the following reaction:
3Fe + 4H2O = Fe3O4 + 4H2
Water will have to be continuosly fed from the boiler to replenish that consumed and to flush out the H2.
The single most important condition for a successful synthesis is good mixing - Nicodem
|
|
unionised
International Hazard
   
Posts: 5126
Registered: 1-11-2003
Location: UK
Member Is Offline
Mood: No Mood
|
|
Hang on,
50PSI is not needed
1000 C is not needed.
What's to discuss?
|
|
Fulmen
International Hazard
   
Posts: 1716
Registered: 24-9-2005
Member Is Offline
Mood: Bored
|
|
How did you come to that conclusion? Sure the reaction runs at lower pressures and temperatures, but as I understand it he wants to increase reaction
speed.
We're not banging rocks together here. We know how to put a man back together.
|
|
unionised
International Hazard
   
Posts: 5126
Registered: 1-11-2003
Location: UK
Member Is Offline
Mood: No Mood
|
|
Quote: Originally posted by Fulmen  | How did you come to that conclusion? Sure the reaction runs at lower pressures and temperatures, but as I understand it he wants to increase reaction
speed. |
Which won't happen in a closed container because it will set up an equilibrium.
There are also far simpler ways to make magnetite, but that's a different matter.
|
|
Fulmen
International Hazard
   
Posts: 1716
Registered: 24-9-2005
Member Is Offline
Mood: Bored
|
|
True. There must be a continuous stream of vapor, but that isn't hard to solve. As for the process, I'm guessing he's after solid magnetite.
We're not banging rocks together here. We know how to put a man back together.
|
|
unionised
International Hazard
   
Posts: 5126
Registered: 1-11-2003
Location: UK
Member Is Offline
Mood: No Mood
|
|
Given that it melts around 1600C, solid is the only real option.
There's no reason to think that 50 PSI steam and 1000 C would give particularly big crystals.
|
|
yobbo II
National Hazard
  
Posts: 764
Registered: 28-3-2016
Member Is Offline
Mood: No Mood
|
|
The reaction chamber is not closed as per the diagram at top.
It is easy (imo) to obtain a stream of water vapour through the set up (diagram) using a simple variable weighted valve on the outlet.
As for 'single crystals' or pieces of magnitite read this short thread (same link is above too!).
http://www.sciencemadness.org/talk/viewthread.php?tid=71009
See the patent attached for more info. (using atmospheric pressure and 1000C). I am converting pieces of iron or steal into (similarly shaped) pieces
of magnetite. I am not trying to produce magnetite as a reagent to put into a jar and use somewhere else.
I simply want to increase the pressure of the chamer a bit a bit to see what will happen. As Fulmen suggests it will increase reaction speed.
The seal between chamber and door is what I am wondering about.
Using ordinary steel as a chamber will not work as it cannot be reused and will react itself to form magnetite (I don't want/need crusts of various
shapes of magnetite) and hydrogen.
Attachment: US2727842.pdf (435kB) This file has been downloaded 399 times
|
|
Fulmen
International Hazard
   
Posts: 1716
Registered: 24-9-2005
Member Is Offline
Mood: Bored
|
|
As long as you're going for the boiler approach the seal shouldn't be a problem. A slight leak should be acceptable, after all you need to vent the
hydrogen.
We're not banging rocks together here. We know how to put a man back together.
|
|
Magpie
lab constructor
   
Posts: 5939
Registered: 1-11-2003
Location: USA
Member Is Offline
Mood: Chemistry: the subtle science.
|
|
As you say, ordinary steel and stainless steels aren't going to cut it. A nickel alloy like Hastelloy c276 will likely be best for cost, strength,
machinabiliy, corrosion resistance, and weldability.
The pressure control valve won't be much of a problem as it can be located in a much cooler environment. Just use a pressure gage and a needle valve.
[Edited on 15-1-2017 by Magpie]
[Edited on 15-1-2017 by Magpie]
The single most important condition for a successful synthesis is good mixing - Nicodem
|
|
Magpie
lab constructor
   
Posts: 5939
Registered: 1-11-2003
Location: USA
Member Is Offline
Mood: Chemistry: the subtle science.
|
|
Here you go :
http://www.ebay.com/itm/Galigher-Hastelloy-Sleeve-58253-/270...
18 hrs left on this auction.
or,
https://store.advanceops.ca/products/07190n
[Edited on 16-1-2017 by Magpie]
The single most important condition for a successful synthesis is good mixing - Nicodem
|
|
yobbo II
National Hazard
  
Posts: 764
Registered: 28-3-2016
Member Is Offline
Mood: No Mood
|
|
Maximum Service Temperatures in dry air
Alloy Temperature
°F °C
Inconel 600 2150 1175
310 2100 1150
Inconel 625 1800 982
Hastelloy C276 800 427
304L 1500 816
321 1500 816
316L 1500 816
AL6XN 1000 538
Monel 400 800 427
Bronze 450 232
Brass 450 232
Copper 400 204
Note: the temperature ratings in the table are general guidelines and could change if corrosives are present, such as sulfur, carbon, etc. In some
cases ASME codes will reduce temperature limits too.
Taken from here
http://www.penflex.com/service-temperatures-of-austenitic-st...
It is confusing at to what temperature hastelloy c-276 can be used up to.
The above source says 427C
It would be too much to push it to 1000C.
The inconel 600 will not withstand a highly oxidizing (water vapour) atmosphere at 1000C
|
|
macckone
Dispenser of practical lab wisdom
   
Posts: 2168
Registered: 1-3-2013
Location: Over a mile high
Member Is Offline
Mood: Electrical
|
|
This is one of those speed vs quantity problems.
A much larger container is possible at a lower temp and pressure.
A high temp ceramic isn't going to handle much pressure
But your volume is basically as big as you want for a furnace.
As your pressure and temp go up, your working volume
Decreases rapidly due to material strengths dropping at
Elevated temp.
TZM is the only alloy I find with a service temp that high.
|
|
yobbo II
National Hazard
  
Posts: 764
Registered: 28-3-2016
Member Is Offline
Mood: No Mood
|
|
Perhaps I could make a pipe from some ceramic cement + blanket and put some sort of lapped lid on it with lugs for alloy 600 bolts. Alloy 600 bolts
are available not too expensive, they will withstand 1000C so long as the conditions are not too oxidizing (air is ok)
Could make inconel 600 bolts and nuts from rod
|
|
macckone
Dispenser of practical lab wisdom
   
Posts: 2168
Registered: 1-3-2013
Location: Over a mile high
Member Is Offline
Mood: Electrical
|
|
Not melting is significantly different from having a
decent yield strength. At 1000C there just isn't much
that will withstand any pressure. Honestly, ceramics
are going to be better at that temperature than most
metals. The TZM listed is the only metal that has a
significant yield strength at that temp.
Now you could do a metal outer shell with a ceramic
insulating shell and a heated inner ceramic shell.
Then the outer shell doesn't have to withstand the
temperature and the ceramic doesn't have to
withstand the pressure.
The ammonia production process uses a similar setup.
There the problem is somewhat different as the
inner shell has to deal with hydrogen embrittlement.
The pressure is higher but the temperature is more
reasonable.
|
|
yobbo II
National Hazard
  
Posts: 764
Registered: 28-3-2016
Member Is Offline
Mood: No Mood
|
|
Can anyone see why the following would not work?
There is no need for bolts.
Hopeing that the lapped seal(s) at the end(s) would be ok. If small amounts of water vapour leak that is not a big problem.
The pipe and ends would need to be some sort of nickel alloy so it does not corrode. Pressure is low (less that 50 or probably 10 PSI)
I can weld one end plate on as I only need to get access to the pipe from one end.
Standard garage furnace will be ok. No need to make a metal + ceramic 'special' furnace.
TFYT
Yob
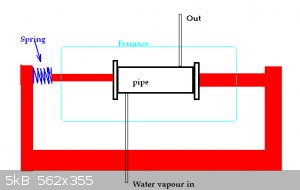
[Edited on 13-3-2017 by yobbo II]
|
|
Pages:
1
2 |