Pages:
1
2 |
markx
National Hazard
  
Posts: 646
Registered: 7-8-2003
Location: Northern kingdom
Member Is Offline
Mood: Very Jolly
|
|
Carburizing experiments
This dwells more into the realm of metalworking, but perhaps it is interesting to some people...
Since I have access to a decent electrical furnace with good temperature control, I thought to try some case hardening experiments just for the fun of
it. Basically one takes a piece of low carbon steel and chucks it into a reasonably tightly closed metal container that is filled with a mixture of
carbon bearing material and some activators. Then heats the lot up to a predetermined tempetarture in the range of 700-1000C and keeps it soaking
there for a period of time. Usually from a few hours to in excess of ten hours depending on the expected case depth.
What will happen is that carbon begins to diffuse into the metal aided by the heat and activators and turns the simple cheap and soft material into a
rather interesting composite that has a heat treatable outer case which is hard, but the inner core shall mostly remain soft and ductile.
Depending on the choice of activators and the heating time, the carbon enriched zone depth can be controlled and thus one can turn a simple mild steel
component into something that has a little more function and value.
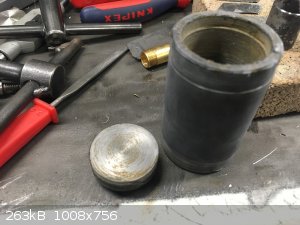
Fig.1 A simple mild steel compartment to house the carburizing mixture and the workpiece(s).
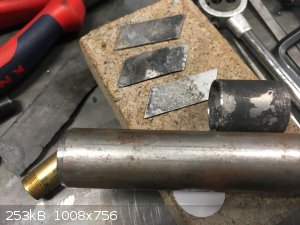
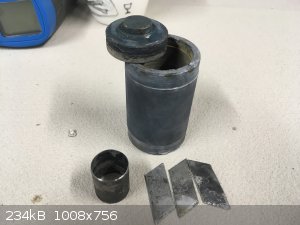
Fig2. Pieces of old utility knife blade and a mild steel pipe were chosen as the victims of carbon enrichment
The carburizing vessel was packed with the following concoction:
10% wood charcoal
10% SrCO3
80% Na2CO3
The carbonates act as activators for the carbon diffusion process and help it along.
The thermal carburizing treatment was conducted according to following
regimen:
700C for 2 hours
raising of temperature to 950C during 1 hour
keeping at 950C for 3 hours
slow cool off in the furnace (about 12h)
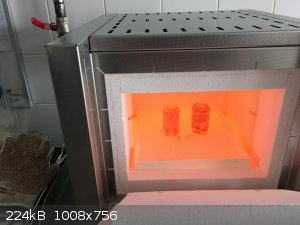
Fig. 3 Specimens being cooked at 950C in the furnace
Since both the mild steel pipe and the blades had a thickness of only 1mm, I expected them to carburize completely with a uniform high carbon content
throughout the whole of the material. I did not have to be dissappointed, all specimens had acquired a very high carbon content (probably well in
excess of 1% C). This was confirmed with a quick water quench from about 900C and scraping /spark tests. Specimens were extremely brittle after the
quench, even to the point where it was impossible to form a cutting edge on them. The material would simply fall apart during sharpening. A bit of
annealing fixed that nicely. Metal files could not touch the quenched samples and they were hard enough to leave a scrape mark on lathe hard jaws.
The utility knife blades already had a decent carbon content before carburizing (0,8%C SK-5 steel), but after the treatment their carbon content had
clearly risen even higher.
The blade would distort during water quench heavily, that will not happen with original SK-5 steel (at least not to my experience so far), but is
prevalent in steels that have a carbon content in excess of 1% (like russian Y13A 1,3%C).
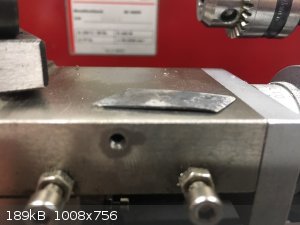
Fig. 4 Carburized and water quenched utility blade sample displaying a massive deformation after quench
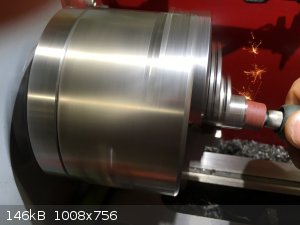
Fig. 5 Carburized mild steel pipe being formed into a circular cutter on lathe and displaying a characteristic high carbon steel spark
To assess the formed case depth in the current heating regime I also conducted a test with a beefier metal sample. A mild construction steel round
stock of 19mm diameter.
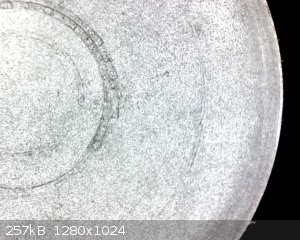
Fig. 6 The mild steel round stock post carburizing treatment, displaying a visible carbon enriched zone at the outer edge after facing off and being
etched with nitric acid
The visible darker edge has a depth of about 1,5-1,6mm when measured, but spark testing revealed that the higher carbon zone extended several
millimeters deeper than the visible etchant marking would suggest. That is quite surprising as I would have expected the case depth to be much
shallower under these conditions. On the order of about a millimeter at best.....go figure 
To try something more exotic I also decided to put a piece of stainless alloy through the carburizing treatment, but on a modified heat regime:
950C 2 hours
slow cool off in furnace (about 12h)
The reason being that I chucked the additional sample into the furnace when the mild steel samples had already gone through the 700C preheat and were
an hour into the 950C treatment.
The exact stainless alloy designation was unknown, but it was an austenitic (non magnetic) type like 304.
The result was quite interesting....literature suggests that stainless alloys form a carbon diffusion barrier at higher carburizing temperatures (in
excess of 600C) and hence the achieved case depth would be very shallow. To counter that and allow a deeper case to be formed, lower temperatures and
very agressive activators (halides, hydrogen chloride etc.) are used. Furthermore the formation of chromium carbide on the surface is known to deplete
the alloy of chromium and hence promote corrosion of the treated part as no more is available to form the protective oxide layer on stainless surface.
The sample came out of the carburizing vessel after the slow cool off bearing a dark grey hard coating without any further heat treatment. The surface
could not be scratched with a metal file. Further heat treatment at 900C following a water quench was tried on a separate piece cut off from the
sample, but seemingly it did not alter the hardness of the coat or substrate material. This suggests that the outer hard coating is mainly composed of
carbides.
The sample had not formed any scale, pitting or other surface defects during the carburizing treatment. The hard coat had preserved all the previous
details...light scratches, cutting marks etc and except for the color change one could not tell that it had been through a 950C heat cycle.
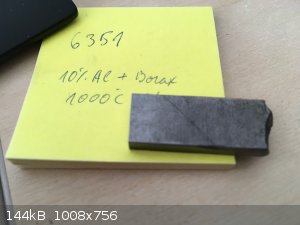
Fig. 7 The stainless alloy sample after carburizing with one edge ground off on a diamond wheel and polished to reveal inner details
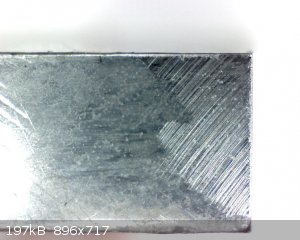
Fig. 8 The stainless sample post carburizing and grinding to reveal the case/base alloy interface
The camera does not capture the case depth and to be honest it was really hard to notice, but the visually affected depth of the sample was about
0,5mm. There was a faint frame around outer edges of the sample extending below the actual carbide bearing hard layer which was very thin...perhaps on
the order of 100 microns, but without special instruments it is difficult to assess.
Which was also ineresting was the effect that the hardness of the inner core material of the sample below the carbide layer and the faint frame
indicating possibly carbon diffusion or other structural changes had risen quite considerably also and seemingly uniformly throughout the cross cut of
the sample. The initial stainless alloy was quite soft (comparable to mild steel) and could be worked with a metal file easily. The carburized sample
was much tougher in the core region and one had to apply quite a bit more effort to leave file marks on the sample.
I do not have the proper means at the moment to measure surface hardness quantitatively, so please forgive the anecdotal comparative methods that I
had to use, but it is amateur metal research after all
Exact science is a figment of imagination.......
|
|
Fulmen
International Hazard
   
Posts: 1716
Registered: 24-9-2005
Member Is Online
Mood: Bored
|
|
Well done. I have done a bit of work on carburizing myself, it's a simple fix when quality steel is in short supply. I do wonder how you ended up with
your mix, usually it's 90% charcoal and 10% activators. But it seems to work...
The process is based on the CO<=>CO2+C equilibrium, CO2 from the activators (and oxidized charcoal from trapped air) forms CO in the carbon-rich
environment. This diffuses into the low-carbon steel where the reaction reverses to form CO2 and carbon. The CO2 can then diffuse out and repeat the
cycle.
As for testing you should try 5% nital etchant, this will color the carburized layer dark. r
We're not banging rocks together here. We know how to put a man back together.
|
|
markx
National Hazard
  
Posts: 646
Registered: 7-8-2003
Location: Northern kingdom
Member Is Offline
Mood: Very Jolly
|
|
Quote: Originally posted by Fulmen  |
I do wonder how you ended up with your mix, usually it's 90% charcoal and 10% activators. But it seems to work...
As for testing you should try 5% nital etchant, this will color the carburized layer dark. r |
I like to use such rogue approach from time to time (also in my daily development job): reverse ratios and head in the general opposite direction of
previous attempts.
Not too seldom it has revealed interesting results 
I also plan to do some boriding experiments in borax/reducer mix (Al powder should work as the reducing agent). Of course the sale of borax has just
been prohibited to general public....for gods sake where does it all end.
Exact science is a figment of imagination.......
|
|
MrHomeScientist
International Hazard
   
Posts: 1806
Registered: 24-10-2010
Location: Flerovium
Member Is Offline
Mood: No Mood
|
|
Really? What's wrong with borax?
Very interesting work, by the way!
|
|
Ubya
International Hazard
   
Posts: 1247
Registered: 23-11-2017
Location: Rome-Italy
Member Is Offline
Mood: I'm a maddo scientisto!!!
|
|
In Italy borax and boric acid were banned from normal shops many years ago.... Go figure
---------------------------------------------------------------------
feel free to correct my grammar, or any mistakes i make
---------------------------------------------------------------------
|
|
unionised
International Hazard
   
Posts: 5126
Registered: 1-11-2003
Location: UK
Member Is Offline
Mood: No Mood
|
|
It's a reproductive toxin.
And the "powers that be" don't see any legitimate home use for it.
|
|
markx
National Hazard
  
Posts: 646
Registered: 7-8-2003
Location: Northern kingdom
Member Is Offline
Mood: Very Jolly
|
|
Update regarding boriding attempt:
I took a piece of the same mild steel pipe that was also used as the precursor in last carburizing attempts and added another machined mild steel part
and a disc of 304 stainless.
All three specimens were packed into the carburizing vessel and packed with the following mixture:
10% Al powder (PAP-1)
90% Borax
The vessel was placed into the electric furnace, heated to 1000C and kept there for 2 hours. After that the lot cooled down overnight in the furnace.
During the heating phase one could notice faint green flames escaping the boriding vessel through the sealing surface of the lid under slight pressure
when temperature had reached an excess of 900C. Clearly there was a reaction going on inside. The furnace door was kept shut for the rest of the
heating cycle to avoid boron bearing fumes entering the lab. Furnace exhaust took care of the off gases. Hopefully 
The next morning everything had cooled down to 50C, the vessel was removed from furnace and pried open. The metal parts on the inside of the vessel
had melted into a solid cake of borax on the bottom and getting them out from this mess proved to be a challenge.
After about an hour of sokaing the vessel in hot flowing water it became possible to remove the parts.
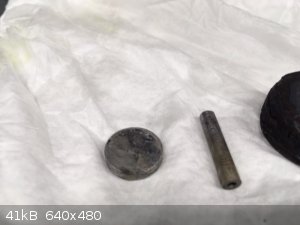
Fig. 1 The 304 stainless disk and a mild steel piece were removed first (the stainless looks very much like after the carburizing treatment: a light
grey hard coat on surface)
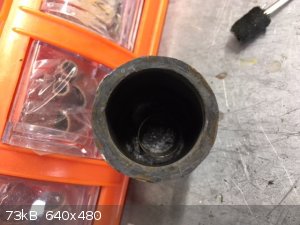
Fig. 2 The mild steel pipe was lodged tight in the vessel and was slightly deformed by the violent removal process
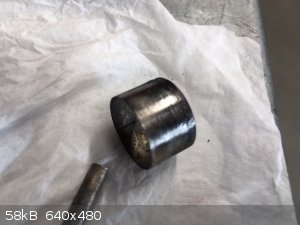
Fig. 3 The mild steel pipe section after removal and clening with a wire brush on angle grinder (there is ununiform surface appearance with shiny and
dull areas. The dull areas seem harder and wire wheel does not polish them)
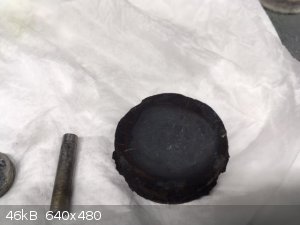
Fig. 4 The lid of the boriding vessel displaying a neat dark grey coating on the side facing into the boriding vessel
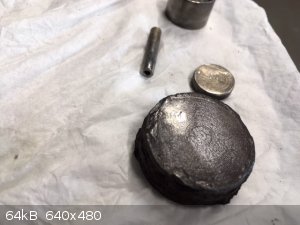
Fig. 5 The lid of the vessel after an attempt to grind with a coarse dremel emery wheel (no success in the middle area that had the grey coating
apparent)
All the parts were removed and cleaned in the soft annealed state that they had acquired during the slow cooling of the furnace and were not heat
treated to alter their hardness.
All parts had a very hard outer layer formed on them although the core was annealed and soft. The pipe section could be deformed even pressing between
bare fingers. But metal file would not cut into the surface and the hard layer could not be removed with a high speed dremel emery wheel. The abrasive
would simply skate over the surface without striking a single spark and just leaving a shiny spot on the part. The dremel wheel would slightly deform
the softer core under the hard surface layer and thus flatten some fine details previously visible on the part, but would not cut into the metal.
So it would seem that a boride bearing layer has indeed formed on the parts under the conditions employed. Although the layer is inherently thin, I
would believe perhaps on the order of just some microns considering the rather short residence time of just 2 hours at 1000C.
Perhaps it would also be beneficial to place the boriding vessel into a preheated furnace at already on the working temperature to minimize possible
side reactions and losses during heat up time.
Exact science is a figment of imagination.......
|
|
Fulmen
International Hazard
   
Posts: 1716
Registered: 24-9-2005
Member Is Online
Mood: Bored
|
|
Boriding is comparable to nitrocarburizing in that it forms hard iron boride rather than martensite like carburizing (and regular heat treatment)
does.
I don't know if you can get the process to work at lower temperatures, but it would be worth a try. This would allow you to surface harden heat
treated steel without destroying the original HT.
We're not banging rocks together here. We know how to put a man back together.
|
|
markx
National Hazard
  
Posts: 646
Registered: 7-8-2003
Location: Northern kingdom
Member Is Offline
Mood: Very Jolly
|
|
Quote: Originally posted by Fulmen  | Boriding is comparable to nitrocarburizing in that it forms hard iron boride rather than martensite like carburizing (and regular heat treatment)
does.
I don't know if you can get the process to work at lower temperatures, but it would be worth a try. This would allow you to surface harden heat
treated steel without destroying the original HT. |
I trust for thermal pack boriding to work in a temperature range that would leave the original heat treatment unaffected is improbable at best.
Usually the process requires in excess of 1000C to work at a reasonable rate. For lower temperature in the range of 500-600C an electrochemical
boriding method exists, but that approach is quite technically challenging for an amateur setup. Even these temperatures would destroy most steel heat
treatments anyway (except for perhaps high alloy tool steels that have a high temperature tolerance).
By the way I heat treated the boriding vessel lid with a propane torch and a water quench (it had been carburized by the previous experiments anyway
and had absorbed enough carbon to harden properly). If one tries to grind it with the dremel wheel, it seems like there is literally no abrasive
involved. The wheel just skates over surface and even machining marks that were flattened before by the deformation of abrasive particles hitting the
surface are now preserved. Quite amazing this boride coat.
Exact science is a figment of imagination.......
|
|
Fulmen
International Hazard
   
Posts: 1716
Registered: 24-9-2005
Member Is Online
Mood: Bored
|
|
Actually many low alloy steels are tempered at those temperatures. Currently I'm working on a rifle bolt made from 4340, tempered at 550°C it has a
yield strength of appr 1100MPa. Adding a tough wear-resistant coating on such parts can be very beneficial, that's why ferritic nitrocarburizing has
become so popular.
We're not banging rocks together here. We know how to put a man back together.
|
|
BromicAcid
International Hazard
   
Posts: 3246
Registered: 13-7-2003
Location: Wisconsin
Member Is Offline
Mood: Rock n' Roll
|
|
Very interesting, thanks for sharing!
|
|
markx
National Hazard
  
Posts: 646
Registered: 7-8-2003
Location: Northern kingdom
Member Is Offline
Mood: Very Jolly
|
|
Quote: Originally posted by Fulmen  | Actually many low alloy steels are tempered at those temperatures. Currently I'm working on a rifle bolt made from 4340, tempered at 550°C it has a
yield strength of appr 1100MPa. Adding a tough wear-resistant coating on such parts can be very beneficial, that's why ferritic nitrocarburizing has
become so popular. |
The downside being that nitrocarburizing often utilizes molten cyanide as the main component of the bath....although I think that some cyanide free
compositions are also available.
Retaining the original heat treat with boriding techniques might still be tough, but if the process could be driven on lower temperatures then that
would be great 
Attached article describes electrochemical techniques of producing borided surfaces at lower temperature ranges using composite molten salt baths:
Attachment: MoltenSaltBathsElectrochemicalBoriding.pdf (739kB) This file has been downloaded 598 times
Exact science is a figment of imagination.......
|
|
macckone
Dispenser of practical lab wisdom
   
Posts: 2168
Registered: 1-3-2013
Location: Over a mile high
Member Is Offline
Mood: Electrical
|
|
Primitive nitrocarburizing methods for steel used blood, skins and sometimes the bodies of slaves or other captives. Obviously our current methods
are more consistent and result in a lot less death and dismemberment.
This is very cool work btw.
|
|
Fulmen
International Hazard
   
Posts: 1716
Registered: 24-9-2005
Member Is Online
Mood: Bored
|
|
From my research most baths today are cyanate-based, so they should be quite safe. The trouble with these methods are that they often require more
specialized equipment and/or wastes costly or hard-to-find chemicals. Carburizing is a simple way to add some strength and wear resistance to simple,
low-stressed parts once you have a furnace.
Most of these other methods end up being much more suitable for semi-continuous operation or require very fine process control. Or they waste too much
materials, increasing both cost and the need for waste management. So keep up the good work, nice to see someone else working on the same field.
Next time try reducing the temp a bit and remove the parts while hot. They should be perfectly shielded from air by the molten boron oxide, I
routinely use boric acid for this when heat treating finished parts. They come out clean even after prolonged soaks at 850°C.
We're not banging rocks together here. We know how to put a man back together.
|
|
macckone
Dispenser of practical lab wisdom
   
Posts: 2168
Registered: 1-3-2013
Location: Over a mile high
Member Is Offline
Mood: Electrical
|
|
I wonder if cyanoacrylates might be good for nitrocarburization.
Acrylic plastics are readily available as is superglue although methylcyanoacrylate has a lower amount of hydrogen than ethylcyanoacrylate.
|
|
markx
National Hazard
  
Posts: 646
Registered: 7-8-2003
Location: Northern kingdom
Member Is Offline
Mood: Very Jolly
|
|
Quote: Originally posted by macckone  | I wonder if cyanoacrylates might be good for nitrocarburization.
Acrylic plastics are readily available as is superglue although methylcyanoacrylate has a lower amount of hydrogen than ethylcyanoacrylate.
|
I trust they shall decompose way before one reaches a temperature range where interaction with the metal becomes prevalent. In essence only carbon
shall remain behind and enter the steel as would happen with any carbon containig material be it of natural or synthetic in origin.
Exact science is a figment of imagination.......
|
|
Fulmen
International Hazard
   
Posts: 1716
Registered: 24-9-2005
Member Is Online
Mood: Bored
|
|
Could possibly work in a gas furnace. For a "solid pack" or liquid bath process I don't see them surviving the temperatures needed. In order to get
reasonable diffusion rates I suspect you need at least 4-500°C.
We're not banging rocks together here. We know how to put a man back together.
|
|
macckone
Dispenser of practical lab wisdom
   
Posts: 2168
Registered: 1-3-2013
Location: Over a mile high
Member Is Offline
Mood: Electrical
|
|
Cyanoacrylates seem to be more resistant than one would expect. They release hydrogen cyanide at high temp which would preclude their use indoors.
But most of the other compounds used for this purpose do as well. It would really depend on the skin depth you are shooting for. A couple of mils is
'better' than full penetration as full penetration makes the article hard but brittle while you want a hard surface but malleable center.
|
|
markx
National Hazard
  
Posts: 646
Registered: 7-8-2003
Location: Northern kingdom
Member Is Offline
Mood: Very Jolly
|
|
Well for the sake of argument I can try it out....I have coupious amounts of cyanoacrylates available and it is easy to encrust them to the subject
metal with the help of sodium carbonate.
Say the same heat treatment regime for practical purposes should then produce a hardened "outer skin" on the subject ferrous alloy without further
heat treatments if nitrocarburisation takes place in the presence of cyanoacrylates....
I shall place the mild steel specimen into preheated furnace to minimize the losses during heat up period.
Exact science is a figment of imagination.......
|
|
macckone
Dispenser of practical lab wisdom
   
Posts: 2168
Registered: 1-3-2013
Location: Over a mile high
Member Is Offline
Mood: Electrical
|
|
This could be interesting. It would certainly change the face of amateur nitrocarburization.
A lot of the compounds normally used are not readily available to amateurs as previously noted.
It might also be a use for all of the solidified tubes of cyanoacrylate scattered across the globe.
|
|
markx
National Hazard
  
Posts: 646
Registered: 7-8-2003
Location: Northern kingdom
Member Is Offline
Mood: Very Jolly
|
|
Allrighty then....I did try the nitrocarburisation experiment with cyanoacrylates.
A dead center is machined out of mild steel, the tip is covered in cyanoacrylate and cured with sodium carbonate in several layers. The lot is then
packed into the carburizing vessel, buried in sodium carbonate layer (tip downwards) and off into the furnace it all goes....
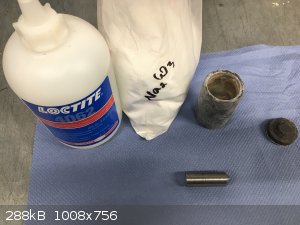
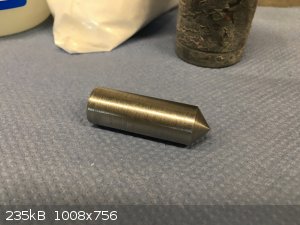
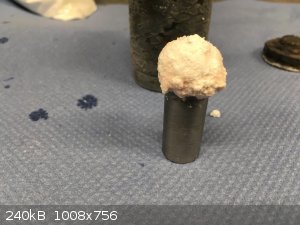
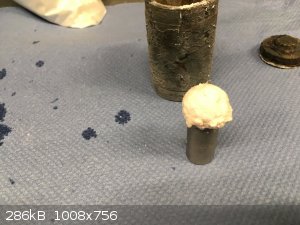
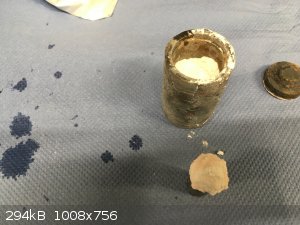
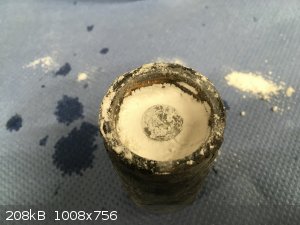
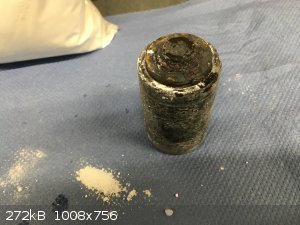
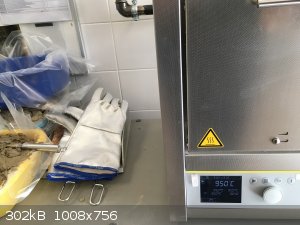
I did not have time today to wait for countless hours, so the merry hell was fired for two hours at 950C with the vessel placed into the furnace when
it had reached the setpoint temperature. For practical purposes all of the organics shall decompose way before the 2 hours are over. All that wants to
fly out will be gone and all that remains shall be in the vessel. So I figured that for first try the 2 hour heat cycle should be ok.
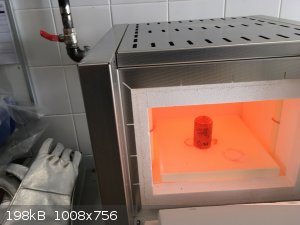
The vessel was removed from the hot furnace and placed into a bowl of water to cool it down. Not a full quench, but rather a slow boil down to room
temperature. Then the lot was washed under flowing water to loosen the lid and out came such a "thing".
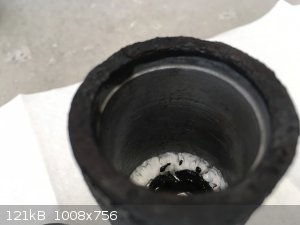
The whole contents of the vessel smelled precariously like almonds, so I flushed everything with coupious amounts of water to clean up any possible
cyanide that may have formed in the vessel and gotten trapped there.
In the vessel bottom one can see the charred shadow of the cyanoacrylate resin in a solidified pool of sodium carbonate. So if nothing else then at
least a thin high carbon case has been formed on the dead center's tip area.
There is a slight coloration difference between the area that was covered in cyanoaclrylate and the rest....so something. Sure enough when I tried the
file test, both the tip and the tail of the dead center were soft. Does a nitrocarburized layer need additional heat treatment or should it be hard
even without a oil or water quench? I'm not sure....
Sooo....I heated the dead center up to about 850C in a propane flame and water quenched it. Well the tip area hardened and the tail remained soft. So
there is a case, but I have no idea wether it is a nitride/carbon case or just a carbon case.....
Below one can observe two dead centers I made...the smaller one is machined from high carbon steel and heat treated with the same water quench, the
bigger one is the subject of the nitrocarburizing experiment. For practical purposes both are very hard in the tip area after a water quench and with
simple methods I can not really evalutate a difference between them.
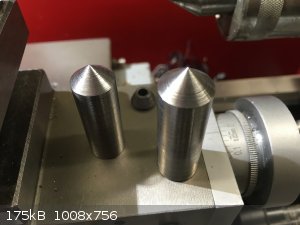
Sigh.....well it is inconclusive at best. I'm sure the same outcome would have been reached if I had wrapped a garbage bag around the tip of the mild
steel dead center...or any other carbon source of organic nature for that matter.
Since I was really not inclined to destroy the functional heat treated and cleaned up center with grinding and etching tests, I opted to black oxide
coat them both and just use them in the lathe to turn stuff between centers as intended.
Two dead centers and two cutting tool holders for mini lathe post degrease and pre oxide coat...into the magnetite bath....and then out. A thing of
beauty 
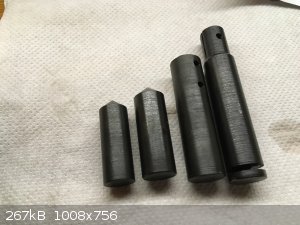
In fact I hoped that the black oxide coating process would reveal the differences in surface structure if there was a nitiride case at the tip of the
bigger center ( a difference in the coloration shade of the coat, the sheen or dynamics of formation). But really it all just coated black quite
evenly ....
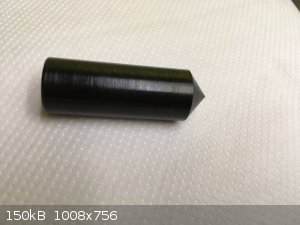
More experimentation is needed....and in milder conditions! The 950C setpoint is really overkill for nitrocarburizing and really it should be done
around 550-750C region...
Exact science is a figment of imagination.......
|
|
macckone
Dispenser of practical lab wisdom
   
Posts: 2168
Registered: 1-3-2013
Location: Over a mile high
Member Is Offline
Mood: Electrical
|
|
Based on your description of the odor of almonds it sounds like cyanide is being formed, which is expected.
The temperature is way too high for nitrogen induction as intended.
450C - 520C for nitriding and 540-580 for nitrocarburization:
https://www.machinedesign.com/materials/benefits-nitriding-a...
https://www.paulo.com/case-hardening-basics-nitrocarburizing...
Most of these are using ammonia gas which is doable but a cyanide in situ from methylcyanoacrylate would be easier.
Salt bath nitriding which is more similar to this (uses cyanide) is 400C to 560C but this uses the hard to get compounds. I would shoot for 450C and
go for nitride only. It supposedly takes less than an hour. The case thickness is fairly thin unlike carburization where the case is thick but this
supposedly gives better tolerances as it prevents warping from quenching and carbon entrainment.
Reviewing some of the ancient methods, it seems swords were wrapped in bloody leather and thrown in the forge until the leather disintegrated (around
400C max) then removed and quenched. I don't know that this actually added anything to the blade or if it was just ritual. Certainly it could not
add much more than quenching a blade in the living body of an available slave or prisoner since metal of that time was already high carbon. So much
of the pre-enlightenment period was based on superstition and not even trial and error but just ritual. It actually seems very horrific with little
to no benefit.
|
|
Fulmen
International Hazard
   
Posts: 1716
Registered: 24-9-2005
Member Is Online
Mood: Bored
|
|
I agree, back off the throttle a bit. Nothing good comes from heating steel more than you have to. One of the huge benefits with nitrocarburization is
the low process temperature, that's what you're after. I dabble with heat treating, and something like 4340 heat treated to 1000+MPa is tempered at
around 550°C. This is an extremely useful material for high-stress parts, and very compatible with nitrides.
We're not banging rocks together here. We know how to put a man back together.
|
|
royalallen
Harmless
Posts: 1
Registered: 30-9-2018
Member Is Offline
|
|
The temperature is way too high for nitrogen induction
|
|
markx
National Hazard
  
Posts: 646
Registered: 7-8-2003
Location: Northern kingdom
Member Is Offline
Mood: Very Jolly
|
|
Indeed....I also repeated the procedure with mild steel gadgets at 500C (2h in furnace). As far as I can recognize from a spark test a carbon case has
definitely formed at the surface of the metal samples. The parts became heat treatable and hardened considerably on the surface after a water quench.
Straight out of the furnace and after cooling (without any further heat treatments) the parts were perhaphs slightly harder at the surface than
untreated metal from the same source, but the layer was definitely very thin.
I shall add pictures later.
Surface appearance hinted little to nothing about a definite change having occurred in surface layer....part were perhaps a little darker than before
treatment, but still mostly shiny and seemed uaffected as far as any scale forming or other changes. Which is a good thing as far as keeping
dimensional tolerances goes
Exact science is a figment of imagination.......
|
|
Pages:
1
2 |