Pages:
1
2
3
4 |
Fleaker
International Hazard
   
Posts: 1252
Registered: 19-6-2005
Member Is Offline
Mood: nucleophilic
|
|
The Synthesis of Sulfur Trioxide and Oleum: the vanadium (V) oxide-catalyzed method
(Note: Yes, it's about time, I know. I promised this a long while back and my lab partner and I just finally got to it. Before going to prepublication
for strenuous review/criticism, NERV and I decided to put it here until we've finished the work. Let us emphasize that this first lot of
pictures and tests are merely proof of concept--that our catalyst works and it's feasible on a small scale. For now
it will be written in a colloquial style, and will then be brought up to the standards of proper scientific discourse. Only then will it be in
prepublication for your review.)
Now, for your enjoyment, Fleaker and NERV's first foray into the much anticipated synthesis of your friend and ours, sulfur trioxide!
While Garage chemist's method is admirable, it is limited to small scale use as the persulfate is relatively expensive. It also requires high
temperatures and is hazardous as well. Sulfur trioxide is extremely aggressive at high temperatures and will attack most all things organic.
It forms thick, corrosive acid fogs that can blind or cause pulmonary edema. However, us lot on SMDB are not timid chemists, we know what we're up
against and what we're after That's why you're reading this 
Since this was a test, no special effort was made to include flow meters on both ends. This was a basic test just to check for catalytic activity. In
fact, it was more of a "hey, do you have free time today? Oh, so do I! Excellent, shall we meet up and see if we can make some sulfur trioxide in a
improvised setup?" Despite the impromptu decision, today's results were encouraging.
As garage chemist noted, oleum is very useful stuff for organic synthesis, and I can't even begin to list all of the interesting things one could do
with it. Sadly, it's expensive and rather hard to find thus explaining our impasse.
Alright, onto the science:
Sulfuric acid is used in many industrial processes and is one of the most produced chemicals in the world. Current industrial production of sulfuric
acid is based upon these reactions occurring between 400-700 degrees Celsius:
S(s) + O2(g) → SO2(g)
2 SO2 + O2(g) → 2 SO3(g) (in presence of V2O5)
H2SO4(l) + SO3 → H2S2O7(l)
which is then diluted with water:
H2S2O7(l) + H2O(l) → 2 H2SO4(l)
In this first proof-of-concept run, we cheated. We did not start from sulfur; instead we used anhydrous sulfur dioxide stored as a liquid in a lecture
bottle. Our fume hood's compressed air line was used as the source of oxygen for the process. This was done out of convenience.
Reagents utilized:
(1) lecture bottle of SO2
500mL ACS pyridine (to test for SO2)
compressed air
120mL 17.4M ammonia solution
15g technical grade (old) vanadium pentoxide
1g potassium sulfate (hydrated)
10mL dH20
Glassware and miscellanea:
10mL beaker
250mL beaker
glass stir rod
large porcelain evaporating dish
large stand with cast iron ring
Meker and Tiril burners
Forceps and tongs
Mullite fiber (kaowool)
Apparatus/reaction tube was constructed from:
(1) 55 (edit) centimeter segment of 2.54 cm diameter stainless 316 Swagelock brand tubing. All fittings were flanged stainless and reduced from 1
inch/2.54 cm to 0.25"/0.635cm. No valves were used. A glass wye was used to connect the pressurized air supply with the SO2 cylinder. Both gases mixed
in a neoprene tube (input) which fitted over a stainless barbed adapter and injected into the packed tube. The reaction vessel was housed in a 1200
deg. Celsius tube furnace.
Output was a Silex brand high temperature silicone tube that was friction-connected with a twist of copper wire. The output temperature was measured
with a thermocouple. The output gas product went into a measured volume of water, hopefully reacting with the water to form H2SO4.
Catalyst Preparation
The amounts used in this preparation were empirical (i.e. V2O5 was added to ammonia solution until it would no longer dissolve). 15g of orange V2O5
was added with stirring to 120mL of concentrated ammonia water forming a yellow solution of ammonium vanadate. A small amount remained undissolved. To
this turbid solution, 1g of potassium sulfate was added.
About 30 grams of 1/2" (1.25 cm) Kaowool fiber blanket were shredded into small pieces and placed in a large evaporating dish. The solution was then
poured over top and worked into the mullite substrate with gloved hands, thoroughly coating each piece. These pieces were then picked up in forceps
and heated to decompose the metavanadate.
The pyrolysis and subsequent loss of ammonia occurring as follows:
2 NH4VO3 → V2O5(s) + 2 NH3 + H2O at approximately 220 deg. Celsius.
Having both limited time and patience, we heated the material at a much higher temperature with two different methods: direct heating via the flame of
a methane-fired Tiril burner, and indirectly by heating the evaporating dish with the catalyst and substrate to 700 deg. Celsius (red incandescence).
A half of the catalyst was heated via the former method, a half by the latter. In both cases, it took several minutes of strong heating to remove the
ammonia and decompose the yellow ammonium metavanadate to the red colour, vanadium pentoxide. On pieces heated directly, there was carbonization.* On
pieces heated indirectly, there was melting of the V2O5 which formed a red-brown glaze on the porcelain.
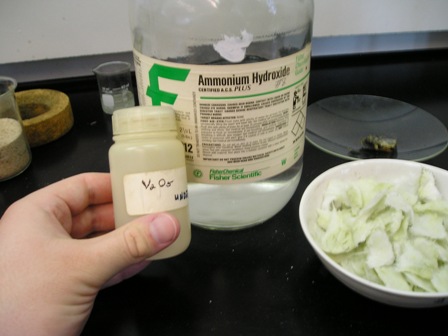
The conversion is complete upon loss of ammonia and conversion to a red-brown covered woolly mass.
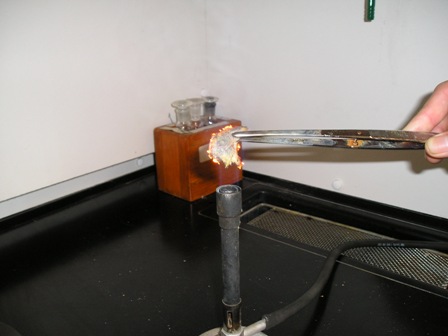
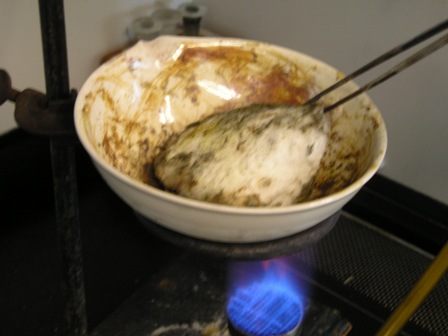
(that red material is V2O5 that melted and glazed itself onto the porcelain)
The following are pictures of the test setup.
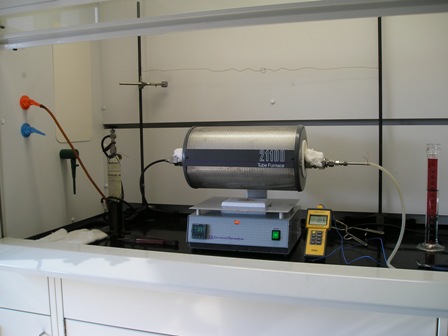
(The whole apparatus)
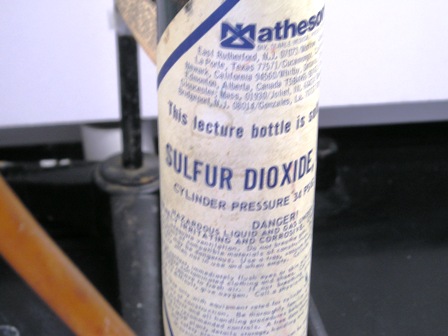
(the sulfur dioxide cylinder)
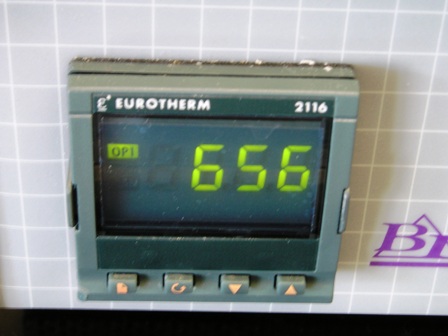
Experimental: Observations and Qualitative Analysis
The reaction tube was loaded with the catalyst. In fact, it was so packed that it was difficult for me to blow air through the tube. We had the tube
furnace preheating while we made the catalyst, so when we put the cold reaction tube in, the temperature dropped. We plugged both ends of the tube
furnace with more kaowool to act as insulation. Being low on time (we were both very hungry), I thought it was a good idea to kick up the temperature
by another 100 Celsius from 550 to 650 degrees. We then proceeded to connect the hoses and turned on the compressed air to get a sense of how much to
flow through (measured by the rate of bubbles in the 250mL graduated cylinder on the output side).
While I watched the output, NERV adjusted the gas flow. We guesstimated that we needed about 2.5X the volume of air to SO2 (assuming 20% atmospheric
O2 and no competing side reactions like NOx formation). During the air flow-through at 660 deg. Celsius, we noticed a goodly amount of steam exiting
through the output (which was not submerged at this point). Realizing that we had made a mistake and had not dehydrated the catalyst enough, we let
the air continue to run to remove any moisture still left in the tube**.
The Silex tubing was rated to 280 deg. Celsius, and it was holding up remarkably well***. Using the thermocouple, a peak temperature during flow
through of 167*C was obtained. This was due to heat dissipation from the air flowing through the stainless, since the metal itself does not conduct
heat very well.
After we opened the the sulfur dioxide bottle, we saw very little for the first minute or so, then immediately a dense, thick fog was noted, as thick
as anything dry ice could produce. I licked my finger and gave a swirl in the fog. I tasted it and it was very sour. This opaque mist was apparently
much denser than air: it overflowed the graduated cylinder and onto the epoxy counter tops where the lower hood baffle removed it. Like us, you are
now probably wondering if it is sulfur dioxide/sulfurous acid mix. We have an answer: at various intervals we used pyridine on a Kimwipe to test for
the presence of sulfur dioxide. Any sulfur dioxide and the pyridine soaked paper will turn a nice yellow colour. In no case did we see any yellow
colour until we tried with pure SO2 from the bottle.
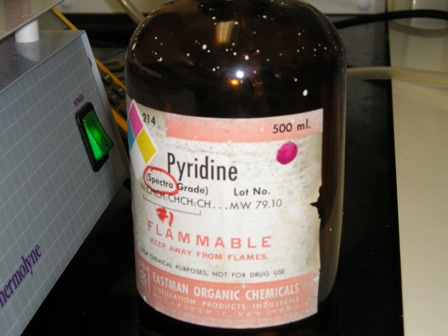
(Just the bottle: next time we'll be sure to get a shot of the yellow complex formed. No complaining--I had to smell pyridine, whose odour I HATE and
NERV adores )
Right before we called it quits, the reaction of the water and the output gases became extremely violent and almost boiled over. It was at that point
when we noticed that our tubing had become very very hot (we burned ourselves in our haste to pull it out of the cylinder to prevent an overflow) and
had been severely corroded by the vapors passing through the tube. We turned off the furnace and let the air continue to run.
As soon as is convenient, I hope to precipitate any barium sulfate and sulfite and then to test the residue with XRD to confirm sulfate presence. When
we run again on Monday, we will bubble the SO3 into some barium hydroxide solution.
We preserved a sample of the ''sulfuric acid'':
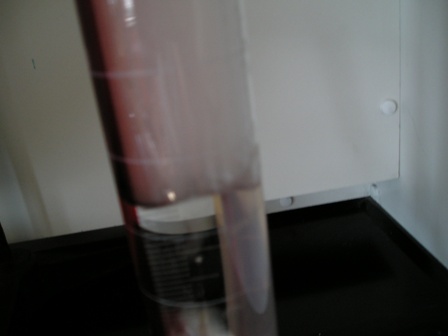
(The cylinder with bubbling tube removed, this is post reaction, most of the mist was gone.)
What went wrong, and the lessons learned:
*This carbonization probably rendered some of the catalyst inert. Pity. Oh, by the way, V2O5 melts to a nice red-brown liquid at red heat 
**However, we foolishly forgot to recall that our compressed air source was full of humidity. Once the reaction was underway, this produced a sulfuric
acid fog and probably ruined some of the catalyst. Utterly stupid of us not to put a drying tube in there. Effectively killed yields in an otherwise
efficient reaction.
***That is until the sulfur trioxide came over. Residual moisture in the tube and the acid mist formed (see above note) charring the silicone
tubing. The heat formed was intense, the reaction tube must have really warmed up, I observed a 5 deg. Celsius raise in temperature on the digital
display while the thermocouple (touched against the Silex) indicated a 100 degree rise!! To us, it seemed that the reaction was that of the SO3 and
any water (along with the silicone).
**Have pH meter on hand, more analytical equipment etc.
Conclusions:
We probably made sulfur trioxide. Definitely, need more qualitative tests. I am rather convinced. Whatever was produced almost ate through
the tubing and was getting quite violent towards the end. Probably should have used some schlenckware and massed it out and filled with H2SO4 and got
a mass difference (making H2SO7). Whoops. We'll give that a shot next time.
Much more to come! This is just the start. Soon we will have a working sulfur burner, but before that, we hope to have a better prepared catalyst and
a more quantitative system setup with flow meters for more precise reactant control. It will be less of an improvised set up. However, today's work
confirmed the production of SO3, how much of it is unknown. Next week's installation should peg that down. I, Fleaker, am still busy with some other
work (which may pop up in General Chemistry)
Unfortunately, NERV has an even tighter schedule than I do, his free time being relegated to Fridays. Quite unfortunate.
We just hope that we can make this method somewhat viable for the hobbyist. This is obviously a technochemistry project, but we believe it can be made
to work on the cheap with modifications.
As always, feel free to U2U us, we're keen to hear thoughts and suggestions. And yes, when we're churning out large quantities of oleum, there will be
some made available to our chemistry confederates. If all goes well, NERV and I would like to post on thionyl chloride and other compounds synthesized
with oleum.
Best regards,
Fleaker & NERV
As an ending note, please excuse misspellings, typos, and grammatical clumsiness. It is late and I am tired and if it's glaring or you can't
understand something, don't clog up the thread, U2U me and I'll fix it. Thanks.
For reference:
US patents No. 4285927 and 4539309 which we cite as source of information.
[Edited on 4-8-2007 by Fleaker]
[Edited on 4-8-2007 by Fleaker]
Neither flask nor beaker.
"Kid, you don't even know just what you don't know. "
--The Dark Lord Sauron
|
|
Sauron
International Hazard
   
Posts: 5351
Registered: 22-12-2006
Location: Barad-Dur, Mordor
Member Is Offline
Mood: metastable
|
|
I'll follow your progress with rapt attention, as I have a 2" ID x 12" tube furnace, and a supply of V2O5 on hand.
SO2 is restricted here, so I'll have to make and liquify mine own and load it into sample cylinder w/valve.
|
|
garage chemist
chemical wizard
   
Posts: 1803
Registered: 16-8-2004
Location: Germany
Member Is Offline
Mood: No Mood
|
|
Great documentation, I like it!
One thing: a little moisture in the air that is mixed with the SO2 is usually of no concern, since the temperature in the catalyst tube is above the
boiling point of H2SO4. I just means some SO3 comes out as H2SO4 vapor, which means slightly reduced yield when SO3 is the desired product.
And you should definately lead the output gases into conc H2SO4 and not into water. Gaseous SO3 just forms a H2SO4 fog, and the absorption is very
bad.
If you use conc H2SO4, you can distill the SO3 out of it afterwards and therefore directly weigh the amount of SO3 you made.
It is usually impossible to completely convert SO2 into SO3 with only one catalyst tube. Why your pyridine test for SO2 was negative I do not know.
Otherwise, great work! I plan on trying this as well with my tube furnace whose quartz working tube should arrive soon.
Unfortunately I only have a small amount of vanadium compound (ammonium vanadate).
I might try using perlite as carrier for the catalyst, do you think that could work?
|
|
BromicAcid
International Hazard
   
Posts: 3247
Registered: 13-7-2003
Location: Wisconsin
Member Is Offline
Mood: Rock n' Roll
|
|
Excellent! Great to see nice documentation on a matter so dear to our hearts, these are the kinds of threads I really love to see around here, good
luck!
The sulfur burner that you intend to make seems to be one of the sticking points, I remember AxeHandle had quite some difficulty with it (and never
got a satisfactory one), though there were some good ideas in that thread.
|
|
Fleaker
International Hazard
   
Posts: 1252
Registered: 19-6-2005
Member Is Offline
Mood: nucleophilic
|
|
Thanks all of for your replies. Not_important U2U'ed me last night and I caught it this morning, his advice on lowering the temperature and using a
different substrate was in line with what the patents had suggested. I used this mullite fiber blanket because I had a lot of it on hand (I sell
kaowool, great material for furnace building, and passable as a substrate). I'll probably go to the pool supply later today and get some diatomaceous
earth. During the catalyst preparation and after we packed it into the stainless tube, we noted one problem with it: kaowool insulates too well, even
when wet with ammonia. This made it very difficult to decompose the ammonium vanadate completely and moreover, it seems now very likely that the
decomposition water was reabsorbed by the kaowool. We saw water vapour coming out of the line when we did our initial flow through of air.
@garage chemist, both NERV and I can say that any sulfuric acid mist produced is troublesome. Your method will definitely be used in subsequent runs.
Your earlier work with the persulfate route inspired us to look for a cheaper way. I do not know why we did not see more SO2 using the pyridine test.
Although our tube was filled with quite a bit of catalyst, it could not have been that efficient. My only speculation would be that SO2 was forming
sulfurous acid from residual water left in the Silex tube. With respect to perlite, that is a good idea. Now I'm curious. The only problem I see is
that it has less surface area than silica or diatoms and also, it insulates too well. I think a conductive yet porous catalyst is what is needed.
So, on the agenda now are:
a.) a working sulfur burner (and no, we're not too proud to ask for plans, tips, and advice--Sauron maybe?)
b.) a better stainless set up, valves
c.) flow meters for air, SO2 consumptions and subsequent maths involved.
d.) Use pre-dried air! I'm thinking 18M sulfuric acid gas bubbler for the pre-dry.
e.) analytical testing for SO3 produced (perhaps saturate 80% n-propanol water then titrate with barium chloride. I'd have to find a suitable
indicator)
f.) collect SO3 into H2SO4 as recommended by garage chemist, distill for mass and yield.
I can get sulfur dioxide easily and relatively cheaply (in large cylinders, not in these convenient lecture bottles), but sulfur is still cheaper. As
simple as going to the garden supply, buying a 25 kilo sack for $15. In designing a sulfur burner, I recall my experience designing oil fired furnaces
and building my own oil burners. Why? Oil is hard to burn, it also must be hot to make it fluid enough to go through the orifice and be atomised. I
plan on having a reservoir for the sulfur and keep that heated electrically at 130 deg. Celsius. That (at reasonable temperatures) is when it is at
its most viscous. Then I would draw it into a burning chamber with compressed air, using a venturi effect to siphon the sulfur from its melting pot.
I am fairly certain that I must use a propane preheated furnace (to say 550 deg. Celsius) for it to burn and not just spray on the refractory walls.
In order to recover the sulfur dioxide and scrub out any sulfur particulate, I would need a flue which is lined with some material that the sulfur
could condense upon (perhaps Kaowool? ). The flue is then connected to a tee
which is connected to a dry air supply and then the catalyst tube. Seems like a lot of work, doesn't it? I have a furnace and a burner designed to run
like this, so it's a simple modification of buying some PFA tube to run the sulfur in. Building the flue and sulfur scrubber will take some time
though, and I can't promise to have it done before September.
Regards,
Fleaker
Neither flask nor beaker.
"Kid, you don't even know just what you don't know. "
--The Dark Lord Sauron
|
|
Eclectic
National Hazard
  
Posts: 899
Registered: 14-11-2004
Member Is Offline
Mood: Obsessive
|
|
You might try 1/8" bead activated alumina, silica gel, or even molecular sieves as the V2O5 carrier. You should get much better flow through the
catalyst bed. Also, why not use pure welding grade O2 from a tank? The cost should be more than offset by advantage of not having to deal with all
that excess N2 blowing your product out of the condenser. You could lease a tank, use it up, and return it before 30 days and avoid monthly tank
rental.
For a sulfur burner, how about a small jet of O2 burning in vaporized sulfur and impinging on a molten sulfur pool, followed by an afterburner to
complete combustion with excess O2 and feed directly to the catalyst bed? (There may be process control and excess heating issues. )
|
|
Fleaker
International Hazard
   
Posts: 1252
Registered: 19-6-2005
Member Is Offline
Mood: nucleophilic
|
|
O2 is somewhat expensive I suppose, but I agree that it would boost conversion efficiency and prolong catalyst life. For a sulfur burner using that, I
think it would greatly help, but it would be an intense reaction, very high heat being produced. That would mean SO2 produced would react to SO3. That
mixture would then be passed into the V2O5 bed. That's a good idea, more efficient. I believe my sulfur burner is more suited to bulk production. If
it goes anything like burning waste vegetable oil (in terms of flow rate), then it will probably be burned about 5.5L/hour!! That's quite a bit of
sulfur. Of course that 's running full out, flow could be adjusted by the velocity of the air being put through the tubes. 
I know I do not want to use perlite because it is too insulating, and kaowool we will only use to hold our other substrate in the catalyst tube
(picture plugs at each end). Inside that I want to use diatomaceous earth with V2O5 and K2SO4 on it, and perhaps I'll give it a shot with zeolite,
even though they are expensive and diatomaceous earth would work just as well. I don't know if it's speculation on whether or not they would improve
flow rates--to me, it would seem just as bad as a tube stuffed with kaowool.
Neither flask nor beaker.
"Kid, you don't even know just what you don't know. "
--The Dark Lord Sauron
|
|
The_Davster
A pnictogen
     
Posts: 2861
Registered: 18-11-2003
Member Is Offline
Mood: .
|
|
*remembers my unused resistance wire and couple hundred grams of V2O5*
...hmmm....
Anyway, great work, I was worried when I did not see this in prepub today, until I found it elsewhere. I have always wanted to try to do this, but
less than stellar ventilation prevents this. I look forward to following the progress of this!
|
|
Eclectic
National Hazard
  
Posts: 899
Registered: 14-11-2004
Member Is Offline
Mood: Obsessive
|
|
I have a book on H2SO4 manufacture that indicates that the catalyst is V2O5 in molten K2SO4, or better, Cs2SO4. I'd be worried that a powdered
catalyst might compact and block the tube. Any beaded desiccant should work as a carrier that would guarantee free flow paths through the bed. Silca
gel beaded kitty litter, activated alumina drier for compressed air, used mol. sieve beads, etc.
Studies also indicated that dry V2O5 on a carrier did not work well, a molten K2, Rb2, or Cs2, SO4 salt is needed as a promoter.
[Edited on 8-4-2007 by Eclectic]
|
|
The_Davster
A pnictogen
     
Posts: 2861
Registered: 18-11-2003
Member Is Offline
Mood: .
|
|
I wonder if one could make an ammonium vanadate solution, and then use that for addition to a hot alumium tri-sec-butoxide(or other alkoxide)
producing, after calcining, V2O5 doped alumina sol-gel with very high surface area? Before calcining the gel could be absorbed onto porous material,
like molecular sieves, and then calcined hopefully giving a loose mix of ultra high surface area vanadium catalyst.
Hmm I just may make something like that for kicks, and to motivate me to at some point try to make oleum myself.
|
|
Magpie
lab constructor
   
Posts: 5939
Registered: 1-11-2003
Location: USA
Member Is Offline
Mood: Chemistry: the subtle science.
|
|
Nice going Fleaker and NERV! I agree with Bromic that it is indeed nice to see a full development project with pictures and all the details.
Although I am not familiar with all the possible uses of SO3 just the mention of thionyl chloride has got me salivating. 
I think your use of commercial liquified SO2 and the possible use of compressed O2 sound like the way to go initially as you go after optimizing the
heart of the project, which has to be the catalytic converter. When the main issues there are resolved you can always go after the feed streams to
optimize the system for OTC.
It does sound like beads of some optimum diameter would be good for both heat transfer and uniform gas flow through the tube. If the V2O5 could be
incorporated right into a porous bead that would seem to be ideal.
I like the looks of your new hood. Is this the one you and NERV have built? If
so I'd like to know the details, perhaps in another thread. It looks pretty wide.
I'm glad you are taking such good care of NERV. Please don't forget his daily 4PM feeding of pyridine.
The single most important condition for a successful synthesis is good mixing - Nicodem
|
|
Sauron
International Hazard
   
Posts: 5351
Registered: 22-12-2006
Location: Barad-Dur, Mordor
Member Is Offline
Mood: metastable
|
|
As I see it, the main technical problem is that the SO3 will emerge from the tube reactor quite hot and the dissolution of SO3 in H2SO4 (even
anhydrous acid) is also quite exothermic so what is needed is a recirculating loop of H2SO4 and efficient heat exchanger to remove all that heat.
Otherwise you will just have SO3 distilling out of the oleum about as fast as it is created. I think only a PTFE pump (diaphragm or peristaltic -
cf.Masterflex) is going to be suitable. And then only once the SO3 is down to temperatures tolerable for PTFE tubing.
The SS obviously is inadequate for the tube reactor section, you might want to investigate monel to see whether or not it stands up to 650 C SO3
vapor. You have a reason for eschewing Vycor?
|
|
Fleaker
International Hazard
   
Posts: 1252
Registered: 19-6-2005
Member Is Offline
Mood: nucleophilic
|
|
I had the stainless tubing on hand. It really is not affected by the SO3, in fact, stainless 316 is what is used industrially from what I've seen at
refineries. Vycor, monel, and stainless are all expensive, but even flanged swagelock is about 1/3 the price of the monel and 1/2 the price of the
quartz. Just the small amount of fittings I used there and that pipe would probably cost about 550USD.
Well Sauron, it just so happens that I have a pump with a PTFE diaphragm. I also have a plan to cool down the SO3 temperature: I have a 4 foot section
of stainless 1/4" tubing that's been curled into a coil (misery to do this!). I could wrap this with cold rags to help dissipate heat. I don't think I
have the right diameter PFA tube so I'll have to rough it with silex again. I think the tube should be alright so long as temperatures aren't so high.
Neither flask nor beaker.
"Kid, you don't even know just what you don't know. "
--The Dark Lord Sauron
|
|
Rosco Bodine
Banned
Posts: 6370
Registered: 29-9-2004
Member Is Offline
Mood: analytical
|
|
For V2O5 your intitiation temperature is 400-450C and the reaction arrest temperature is ~620C .
Definitely forget about the silicone tubing on the output side .
You probably don't need to actively heat the entire length of the catalyst chamber ...just heat the input end and then wrap the rest of the length
with some sort of insulation . The exothermic oxidation should provide the heating for the length of the catalyst section which is only insulated .
You could probably put a thermocouple on the
unheated section and adjust your flow rate until the heat of reaction is sufficient to keep the catalyst at a good working temperature .
Flowmeters are probably not necessary . If you use a
constant diameter precision orifice like 16 or 18 gauge
hypodermic needles ....then you can calculate your mix ratios from pressure gauge readings and just use regulators to set your mix ratio .
The mixed air and SO2 needs to be preheated to about 450C
before it enters the catalyst at about the same initiation temperature .
[Edited on 5-8-2007 by Rosco Bodine]
|
|
Sauron
International Hazard
   
Posts: 5351
Registered: 22-12-2006
Location: Barad-Dur, Mordor
Member Is Offline
Mood: metastable
|
|
I quite understand about the cost factor of the materials. However you are dealing with a substance you can't afford to release as it might cost you
more than money.
I must have misread your earier post about the SS tube, I thought you said it was almost eaten through? If the SO3 did not phase it then fine.
I have 2 liters of 65% oleum (Merck) for which I paid about $1750 a few years ago. Each liter is about 2 Kg and so there's c.2.6 Kg SO3 in there and
ready to be distilled out. In Thailand SO3 is hard to buy but oleum is easy if you have the $$ and 65% is the highest concentration I have seen
offered commercially.
I figured, better to buy it this way and if I need 20% or 30% oleum I can dilute with H2SO4 with huge cost advantages to importing the lower strength
oleum. But as yet these two bottles have never been opened. Expensive stuff at 70 cents a gram based on SO3.
|
|
evil_lurker
National Hazard
  
Posts: 767
Registered: 12-3-2005
Location: United States of Elbonia
Member Is Offline
Mood: On the wagon again.
|
|
One almost needs a stainless steel ball to pyrex ball and socket due to the extreme temps involved.
I'd consider using something like an Ace Glass 7658-232 stainless steel 1/2" NPT to 28/15 ball joint, hooked to a custom made 90º three way 28/15
socket to 24/40 male and female adapter (not for sure on the size of this one since I've never farted around with ball and socket joints) then just
hook it onto a reflux condensor and flask... then when the reaction is complete just measure the difference in flask weight to calculate the SO3
content of the H2SO4.
For a catalyst support I'd try 3A sieves as a substrate due to their small size and calcine the V2O5 on them.
www.stpats.com has some rather cheap 1/4" SS needle valves for flow regulation.
Not all chemicals are bad. Without chemicals such as hydrogen and oxygen, for example, there would be no way to make water, a vital ingredient in
beer.
|
|
Sauron
International Hazard
   
Posts: 5351
Registered: 22-12-2006
Location: Barad-Dur, Mordor
Member Is Offline
Mood: metastable
|
|
Stainless SJ balls and sockets are available, a little pricey.
You've got to be careful not to condense the SO3 too low or you into the alpha-explosion problem (see Merck Index for explanation.)
This stuff is tricky in more ways than the obvious ones.
|
|
evil_lurker
National Hazard
  
Posts: 767
Registered: 12-3-2005
Location: United States of Elbonia
Member Is Offline
Mood: On the wagon again.
|
|
So basically what your saying is that when condensing the SO3 you should not go under 65ºC or so lest the alpha version forms, and upon heating above
the melting point it will cause an abrubt pressure rise in the vessel shattering the apparatus?
That don't seem right...
I guess it would be best to directly distill into H2SO4 in a flask with a cooling jacket then right?
[Edited on 5-8-2007 by evil_lurker]
Not all chemicals are bad. Without chemicals such as hydrogen and oxygen, for example, there would be no way to make water, a vital ingredient in
beer.
|
|
Eclectic
National Hazard
  
Posts: 899
Registered: 14-11-2004
Member Is Offline
Mood: Obsessive
|
|
You also have a problem with the SO3 solidifying and blocking the condenser if the temperature is too low.
|
|
Sauron
International Hazard
   
Posts: 5351
Registered: 22-12-2006
Location: Barad-Dur, Mordor
Member Is Offline
Mood: metastable
|
|
Oleum is also solid at some concentrations, but all of those are rather high. So it's not something to worry about unless you make a LOT of SO3
relative to the sulfuric acid.
Funny stuff!
|
|
garage chemist
chemical wizard
   
Posts: 1803
Registered: 16-8-2004
Location: Germany
Member Is Offline
Mood: No Mood
|
|
Oleum does have a melting point maximum of nearly 40°C at 50% SO3, but at 65% SO3 it is liquid at room temperature again. So you can have either the
20-30% oleum or the 65% oleum as liquids, but concentrations in between that are solids.
Over 65% SO3 the melting point again rises.
There is a melting point curve for the H2O/H2SO4/SO3 system in Ullmann, which is really interesting. Did you know that 98% acid freezes at about
-1°C, but 96% acid of commerce freezes at -15°C, and technical 66°Be acid (93%) at -26°C?
[Edited on 5-8-2007 by garage chemist]
|
|
Fleaker
International Hazard
   
Posts: 1252
Registered: 19-6-2005
Member Is Offline
Mood: nucleophilic
|
|
Quote: | Originally posted by evil_lurker
One almost needs a stainless steel ball to pyrex ball and socket due to the extreme temps involved.
I'd consider using something like an Ace Glass 7658-232 stainless steel 1/2" NPT to 28/15 ball joint, hooked to a custom made 90º three way 28/15
socket to 24/40 male and female adapter (not for sure on the size of this one since I've never farted around with ball and socket joints) then just
hook it onto a reflux condensor and flask... then when the reaction is complete just measure the difference in flask weight to calculate the SO3
content of the H2SO4.
For a catalyst support I'd try 3A sieves as a substrate due to their small size and calcine the V2O5 on them.
www.stpats.com has some rather cheap 1/4" SS needle valves for flow regulation. |
I think I might use some zeolite, but not much. Diatoms are cheaper. I also thought about making a few spirals of stainless steel mesh and coating it
with V2O5. The ends will still need to be plugged with the kaowool. NERV and I now feel that catalyst preparation (at the proper temperatures, in
proper atmosphere) is key.
Somewhere around here I have a balljoint and some steel-to-glass fittings. I'd like to avoid it if at all possible as it doesn't really add anything
to the setup. Keep in mind that this reaction tube was something whipped together in the course of a few minutes--we have much more fittings that we
can use. The finished apparatus will hopefully be all metal, so more durable. Also, NERV suggested using some of our 1/8" stainless tubing at the
output, then connecting it to that coil of 1/4" (which might well be 1/8"-- I need to look at it again). This would decrease the temperature til well
withing PFA's limit. That would then be connected to a large glass fritted bubbler in a flask.
@Rosco, from what I've read in the patents, it's 420-800 C. See US patent 4285927, claim 1. Broad temperature range for obvious reasons. It bears
mentioning that to achieve the 99.9% efficiency with their catalyst (essentially just V2O5 slurry on diatomaceous earth), it is necessary to pass the
gas through several different times, cooling in between. All based on the equilibrium situation. The higher it gets, the less efficient but the faster
it goes.
An excerpt:
"The reason is that the reaction gas temperature elevates about 2.0.degree. C. per increase of 1.0 mol % of conversion in case of using a gas
containing 7.0 mol % of SO.sub.2 and the elevation of temperature is proportional to approximately SO.sub.2 concentration, because the oxidation
reaction of sulfur dioxide is exothermic and it is carried out adiabatically in an industrial reactor. Furtermore, if a raw gas containing SO.sub.2 in
a concentration of 21 mol % is used, the gas temperature elevates 6.degree. C. per increase of 1 mol % of conversion. In an industrial reactor, the
vanadium catalyst is used by packing in it dividing three or four layers, but an inlet gas temperature of the first layer is usually controlled to
about 430.degree. C. Thus, if 7.0 mol % of SO.sub.2 containing gas is used as raw material and it is reacted in a 75 mol % of conversion in the first
layer as usual, the outlet gas temperature of the first layer becomes 580.degree. C. (=2.times.75+430) on calculation in case of neglecting heat loss
in the reactor. However, when 21 mol % of SO.sub.2 containing gas is used, it should be kept in mind that the outlet gas temperature of the first
layer becomes high temperature such as 670.degree. C. (=6.times.40+430), even if the conversion in the first layer is controlled down to only 40 mol
%.
Judging from former common sense, it has been thought that it is impossible to adopt such high outlet gas temperature of the catalyst layer with
respect to heat resistance of a material of the reactor. But good heat resistant metallic materials have been applied recently, so a catalyst which
can be resistant to a high temperature of more than 650.degree. C. and can maintain its activity for a long period of time is required as a catalyst
to be charged into the first or second layer of the reactor.
In an oxidation reaction of SO.sub.2 to SO.sub.3, the higher the temperature becomes, the lower an equilibrium conversion which can be reached
theoritically becomes in spite of existence of the catalyst. Thus, once the reaction in each catalyst layers reach to the equilibrium at each
temperature respectively it cannot proceed no more, even if excess catalyst is packed into the layers. Therefore, a reacted gas approached to this
point is cooled to approximately an initial inlet temperature by means of a heat exchanger and then introduced into the next catalyst layer to proceed
the reaction. "
Neither flask nor beaker.
"Kid, you don't even know just what you don't know. "
--The Dark Lord Sauron
|
|
Eclectic
National Hazard
  
Posts: 899
Registered: 14-11-2004
Member Is Offline
Mood: Obsessive
|
|
Do you have any porcelain raschig rings or berl saddles for distillation column packing? They should work well also as a catalyst carrier.
|
|
Fleaker
International Hazard
   
Posts: 1252
Registered: 19-6-2005
Member Is Offline
Mood: nucleophilic
|
|
I have only the borosilicate glass ones.
Also, I'm running low on V2O5, I only had about 20g of it to begin with. Anyone have any spare that I could buy and have overnighted?
Neither flask nor beaker.
"Kid, you don't even know just what you don't know. "
--The Dark Lord Sauron
|
|
Sauron
International Hazard
   
Posts: 5351
Registered: 22-12-2006
Location: Barad-Dur, Mordor
Member Is Offline
Mood: metastable
|
|
After some cogitation, the hot output side of the tube reactor should be connected to a SS coil that is cooled by a loop maintained at about 100 C,
this is to bring the SO3 down to a manageable temperature.
It is then introduced into a continuously stirred loop reactor charged with a relativelt large volume of anhydrous H2SO4 (since any water present
would destroy the SO3 you worked hard to make) which is recirculated through a second cooling coil in a loop maintained at RT. This is to get rid of
the heat produced by the dissolution of the SO3 in the anhydrous acid as well as the heat transferred from the still 100 C SO3.
You can continue this process till you have 20-30% oleum in the second loop.
In the first loop you do not need to heat the coolant initially, the SO3 will do that. You just need to be able to regulate it to max 100 C. That is
easy enough if water is your coolant. Just take off the steam to a condenser (remote to your system) and add more water to replace it at same rate the
steam comes off. As long as the system is not pressurized the water can't superheat.
If you know the rate of SO3 production and its temperature then you can easily calculate the amount of heat to be removed th get the vapor down to 100
C and therefore the design parameters of the first cooling loop.
Ditto, the heat of dissolution of SO3 in 100% H2SO4 is a known number of kcal/mass and the heat of the 100 C SO3 to the acid is on top of that so the
volume of the second loop and cooling capacity of the chillers needed is easily estimated.
The rest is just plumbing.
|
|
Pages:
1
2
3
4 |