semiconductive
Hazard to Others
 
Posts: 325
Registered: 12-2-2017
Location: Scappoose Oregon, USA.
Member Is Offline
Mood: Explorative
|
|
Cheap refractory materials for insulation, casting and equipment manufacture.
When doing distilations and both making and using glassware, I've needed insulation for holding heat and covering oddly shaped parts and flasks. So
I'd like to dedicate a thread to making refractory out of plaster, and people telling me their experiences about improving the "state of the art" for
plaster. IF you have tips and tricks, you can skip this first post and just start telling me about them. Especially about getting rid of air
bubbles, water voids, and techniques to make plaster more resistant to shrinking and cracking when strongly heated. (eg: in an oven at 150C or hotter.
)
Construction workers often use a vibrator for getting air bubbles out of freshly poured concrete foundations... something similar would be useful in
getting rid of bubbles in volumetric flasks and bubbles in plaster casts... has anyone seen a cheap version of something like that?
The rest of this post is a bit of a blog for those interested in making their own equipment through castings....
Being able to cast metal, to cast insulation for flasks, and to cast precision glass shapes is VERY handy for amatuers doing chemistry. I'm
especially interested in lost wax style mold making, but without using wax.
I'm not really good with my hands for glass blowing, but there are a lot of companies (makers & hobbiests) who make precision computer printed
plastic from CAD drawings. Even from free CAD programs running on Linux systems. Its a gold mine for making molds without the hassles of hand carving
the wax as is traditionally done in metal casting.
Several forums on the web show how to build kilns for melting metal or glass; The kilns are typically made out of pearlite and plaster. The heating
elements are often just nichrome wire from common objects such as hair dryers, bread toasters or heat guns purchased from hardware stores.
I've already made several kilns using commercial refactory bricks, alumina cement, and now I am going to do plaster to stock my lab with as it's the
lightest weight. As an EE, I've also built computer controls for precise kiln operation at very low cost. So, when I say professional grade .. I mean
that I'm going to take the amateur stuff all the way to perfection.
The cheap refractory materials and heating elements described on the web are useful, but they are fickle. The exact formulas for best results aren't
known. Both plaster and metal elements are sensitive to heating cycles and exposure to chemicals. They are easily ruined by traditional kiln
chemicals like chloride salts (table salt) or carbon monoxide from burning wax. So, I'm strictly interested in new techniques which are low
-toxicity, and suburban house friendly.
Traditional casting methods simply aren't compatible with low cost amateur kilns. Try burning out wax in your kitchen oven. I'll bet your
husband/wife/parent, neighbor, fire department, all tend to get annoyed with you. Kanthal is protected by aluminum oxide, aluminum is eaten by
chlorine or chlorine salts; and is destroyed by carbon monoxide.
In order to combat smoke and replace wax burnout ovens, I've been looking for a non-toxic salt or easily soluble chemical that is solvent selective.
Preferably, a salt that will dissolve in alcohol but not in water. Traditional Wax doesn't dissolve in water, and that is why it can be used with wet
clay or plaster to make molds; Wax won't dissolve while the mold is hardening. However, salts that don't dissolve in water aren't easily found at the
hardware store (that I know of).
I figured out a trick to use more common salts to replace wax when making clay molds; Tip#1) if a salt dissolves in water but not alcohol; it can
replace wax for making clay molds. Clay can be dried of water and then mixed with alcohol to make slip. Then the clay won't dissolve the salt and you
can use salt in place of wax. After firing the clay in a kiln, the clay becomes insoluble in water. You can then rinse out the salt and have a
perfect clay mold in the shape of the salt which is able to take molten metal. I wouldn't recommend clay molds for making glass castings as the glass
will bond to it.
Salts like Epsom salt, calcium chloride, alum powder do not work with this Tip; Those salts either release corrosive chlorine gas when the clay is
being dehydrated/sintered in an oven (and ruin the heating elements), or they melt in their own water of crystallization and ruin the shape of the
mold before the clay has dried. If you find a cheap salt that works, tell me about it!
If you mix salt with CaCO3 or MgCO3 to absorb the water of crystalization, I've generally found that once exposed to kiln heat (400+C) the chalk
mixtures becomes very SLOW to soften in water ever again. So even though mixing salt with a binder gives you a perfect shaped mold ... you can't
remove the carbonate lump from the mold afterward. As an example: I soaked epom salt + MgCO3 after firing in a kiln; I soaked it for three days in
water, and it still was a lump. Basically, those kind of techniques require you to destroy the salt with acid and waste a lot of chemical. It's
expensive and not good.
I do have ONE phosphorous salt, that is difficult to make, which works well. It dissolves in water but not alcohol. It does not destroy kanthal during
heating even to 1400C. (White heat.) I will describe it later, if there's interest: But it's still not as good as something that would easily
dissolve in alcohol, but not in water; A salt with that property could be used with both plaster and clay molds. Plaster molds have the benefit of
being able to cast glass with a smooth surface, and residues can be chemically removed from the glass's surface using baking soda and vinegar.
I've also tried using a bismuth / tin alloy (non-toxic, melts at 150C) to replace wax. Unfortunately, plastic from printing companies can not handle
150C before melting; so I still have to make a plaster molds (a split mold); The metal has practically no surface tension once it melts ... unlike
lead, zinc, or aluminim .. and therefore penetrates the tiniest of cracks and drips into the bottom of your kitchen oven very annoyingly. Besides
which, normal plaster becomes weak after heating in an oven more than about three times; So, the bottom line is that the plaster's properties still
have to be improved before low fusing metals can be used in place of wax for a "lost wax" process and it will require hand carving a mold.
Gypsum plaster is supposed to remain a solid until around 1250C. It's very light weight and inexpensive. There are also many calcium substances that
have melting points in the 1800C+ range,which can be taken advantage of to make a plaster refractory that becomes stronger as it is heated. Eg: add
titanium dioxide, and there's a chance you will get calcium titanate.
Dentists already use plain plaster for molds to make gold castings, but their molds suffer from shrinkage; which means the shape has to be made
smaller to cause the gold to end up at the final correct size. The gold melts and enlarges the plaster cavity as it enters it. The mold is basically
only used once and then thrown away. But,If the plaster could be improved to not shrink .. it would make a better refractory mold.
Gypsum plaster's hardening ability comes from a "hemi-hydrate" being hydrated by water and forming interlocking gypsum crystals. Hardened plaster
partially returns to hemi-hydrate when heated to 150C and above. It can also fuse into anhydrite. This is why molds I put in a regular oven became
fragile after two to three uses of melting bismuth metal. If plaster was truly destroyed by heat, it would be the ideal cheap material to replace wax
for making clay molds. But in reality, it doesn't work. Murphy's law prevails. Plaster shrinks and weakens while forming anhydride, but once the
shrinkage is complete it actually starts sintering and becomes harder as the temperature rises into the kiln range (400+C) This is dead burnt
plaster. Dead burnt plaster is very hard and according to several sources "dissolves in water only on a geological timescale of thousands of years."
Unfortunately, there is a lot of literature on the subject with conflicting answers about what dead burnt plaster is, what temperatures, time, causes
of plaster sintering are. So, the following data is subject to the priviso (we have to know how to make the right kind of dead burnt plaster before
the special cements will be made.)
Here's a NIST document on plaster from the 1940's.
It describes the different kinds of plaster formed due to heating. I don't know how accurate it is, but the results they come up with are similar to
the results I got when experimenting.
http://nvlpubs.nist.gov/nistpubs/jres/27/jresv27n2p191_A1b.p...
Since that time, several special forms of dead burnt plaster have been discovered.
In general, salts with sulfate ions in them can cause dead burnt plaster to partially restore the hemi-hydrate state and allow hardening; but without
a large volumes of crystal being formed. I am wondering if that would reduce shrinkage in plaster when cooked, and help improve the strength....
Unfortunately, I'm unsure that these formulas will really work; because I don't know how burnt the plaster can be and people mean different things by
"dead burnt" in the available literature.
http://pubs.acs.org/doi/pdf/10.1021/ed007p2807
The most well known salt is alum (aluminum sulfate), which can be bought at a grocery store for canning pickels.
A 10% solution restores plaster's setting ability by making keene's cement.
Potassium or sodium sulfates, make something called Mack's cement.
These additives could potentially make plaster denser, and immune to regular oven heat. But I don't know what formulations are likely to work, or how
to cook plaster to transform it into the grade material that the inventors of these cements want.
I have found that just plain old sulfuric acid, applied to plaster cooked above 600C will restore some of it's setting ability. So, it's not like
these formulas are likely to be very complicated. It's just a matter of determining how much time and concentration is needed to get acceptable
results, empirically.
I suspect that many other sulfate salts or even fetilizer (ammonium sulfate) could create similar effects.
If you know gypsum plaster formulas that are particularly strong and resistant to shrinking after being cooked at 150 to 600C, let us know. There's a
lot of applications where it would be useful in making amateur chemistry equipment.
Just plain old pearlite (garden material) sifted through a window screen to get rid of tiny particles, and mixed 50/50 with plaster of Paris by volume
makes a decent refractory brick or insulation for distillation flasks. However, it's not optimized in any way for use under extreme heat and will
likely crack if used much above 120C.
I'd like to know what formulas give stronger or better insulation results, since plaster is used commonly; someone ought to know by now. 
[Edited on 19-12-2017 by semiconductive]
|
|
andy1988
Hazard to Others
 
Posts: 135
Registered: 11-2-2018
Location: NW Americus ([i]in re[/i] Amerigo Vespucci)
Member Is Offline
Mood: No Mood
|
|
Look into silicon dioxide as an additive? Could also add more layers for more insulation, the outer layers being more permanent.
I've got some ideas for a DIY furnace not using plaster, but there are critical things I need to work out.
Just curious, have you looked into making a fused silica crucible before? I think it would handle molten steel. This is something I'm interested in
:-) But I'd need to make it maybe 2'h and 1'd.
[Edited on 12-2-2018 by andy1988]
|
|
Magpie
lab constructor
   
Posts: 5939
Registered: 1-11-2003
Location: USA
Member Is Offline
Mood: Chemistry: the subtle science.
|
|
At one time I wanted to cast a copper round bottom flask using the lost wax technique. But I never got to it. One problem was that casting copper
would require a furnace capable of at least 1200°C, IIRC.
The single most important condition for a successful synthesis is good mixing - Nicodem
|
|
semiconductive
Hazard to Others
 
Posts: 325
Registered: 12-2-2017
Location: Scappoose Oregon, USA.
Member Is Offline
Mood: Explorative
|
|
Quote: Originally posted by Magpie  | At one time I wanted to cast a copper round bottom flask using the lost wax technique. But I never got to it. One problem was that casting copper
would require a furnace capable of at least 1200°C, IIRC. |
Yes. I know what you mean. Brasses have lower melting point but different chemical properties.
It's fairly easy to get molybdenum or to make electric heating elements that go over 1200C. The trick is the refractory, keeping it both cheap and
chemically immune to the heating element by sealing against air. I just talked about that in another thread.
https://www.sciencemadness.org/whisper/viewthread.php?tid=80...
Plaster by itself goes to ~1250C, but would start to dissolve when melting copper. Plaster is often used for casting dental gold ... ~1100C with
overheat, but you have to adjust your mold size for the plaster shrinking under intense heat.
[Edited on 13-2-2018 by semiconductive]
|
|
semiconductive
Hazard to Others
 
Posts: 325
Registered: 12-2-2017
Location: Scappoose Oregon, USA.
Member Is Offline
Mood: Explorative
|
|
Quote: Originally posted by andy1988  | Look into silicon dioxide as an additive? Could also add more layers for more insulation, the outer layers being more permanent.
I've got some ideas for a DIY furnace not using plaster, but there are critical things I need to work out.
Just curious, have you looked into making a fused silica crucible before? I think it would handle molten steel. This is something I'm interested in
:-) But I'd need to make it maybe 2'h and 1'd.
[Edited on 12-2-2018 by andy1988] |
Silica is quite heavy and dense. Silicon carbide is a far better way to go for a crucible. It's has much better thermal conductivity and a super
high melting point.
Plaster is no good as a crucible. It's too effective of an insulator.
For insulation bricks, though...
I've thought of using sodium silicate to harden the surface of the plaster while only using a tiny bit of silica; but the sodium chemically reacts in
waster with the sulfate and displaces the calcium; so you get goo on the face of the plaster instead of penetration. I havn't figured out how to get
the plaster to set with tiny amounts of silica inside, yet.
I've also considered making something called blue smoke as a mold refractory and insulation brick. Blue smoke is foamed silica with 99.9% air space.
That's what was used a long time ago to make the space shuttle tiles for re-entry. Normally blue smoke is made by mixing methyl silicate with an
alcohol, and then pressurizing it under liquid CO2. The CO2 will dissolve out all the water and alcohols, while keeping the silica foamed. If the
CO2 is allowed to leak out very slowly ... like a month; the silica does not collapse and is extremely light. You can take a blowtorch to a half
inch thick piece, while holding it in your bare hand behind ... you won't feel the heat.. but it's complicated to make.
There was also German company which posted a youtube video of a liquid, low pressure process, to achieve the same goal with something other than CO2.
But methyl-silicate is difficult to get, and hard to make in large quantities.
For right now, I'm just using simple and lightweight materials to raise melting points.
Simple things like titanium dioxide (rutile) seem to work when mixed with anhidride. The fusion of the two gives calcium titanate -- perskovite --
MP. 1975C. Since the TIO2 is mixed with plaster and is VERY pourous, it tends to melt extraordinarily slowly even when above it's melting point.
TiO2 is the white pigment in a lot of paints. I got 20lbs of it for like $30 on ebay. Hydrated alumina is another material I bought to experiment
with.
I've also tried fusing magnesium oxide (easily made from epsom salt) with titanium dioxide to seal alumina welder baffles (avaiable from welding
shops, and some auto-parts stores for TIG welders.) It works, and requires white heat to fuse. Straight MgO sublimes slowly, and is a pain. So,
alumina-magneisia or calcium magnesia, are what I'm hoping will make a cheap and decent hard facing for kiln bricks.
Pretty much, you only need a half inch of really high temperature refactory before switching to a lower cost refractory with lower melting point. The
highest heat doesn't penetrate the bricks very far.
In fact, my favorite kiln is inside a wooden box. The canthal elements will melt long before the box gets hot. Good old garden variety vermiculite
is an excellent insulator ... although it breaks down with time. A foot thick wall of that stuff holds serious heat!!!
Most of the electricity wastage is driving the water out of it, but once dry ... the stuff will keep my two cubic foot kiln hot for over 12 hours
with no electricity applied.
[Edited on 13-2-2018 by semiconductive]
|
|
SWIM
National Hazard
  
Posts: 970
Registered: 3-9-2017
Member Is Offline
|
|
Quote: Originally posted by semiconductive  |
Construction workers often use a vibrator for getting air bubbles out of freshly poured concrete foundations... something similar would be useful in
getting rid of bubbles in volumetric flasks and bubbles in plaster casts... has anyone seen a cheap version of something like that?
[Edited on 19-12-2017 by semiconductive] |
Yes, there is an American company named Doc Johnson which makes small versions of these (powered by batteries in most cases), for hobbyists, and other
home uses.
|
|
semiconductive
Hazard to Others
 
Posts: 325
Registered: 12-2-2017
Location: Scappoose Oregon, USA.
Member Is Offline
Mood: Explorative
|
|
Quote: Originally posted by SWIM  | Quote: Originally posted by semiconductive  |
Construction workers often use a vibrator for getting air bubbles out of freshly poured concrete foundations... something similar would be useful in
getting rid of bubbles in volumetric flasks and bubbles in plaster casts... has anyone seen a cheap version of something like that?
[Edited on 19-12-2017 by semiconductive] |
Yes, there is an American company named Doc Johnson which makes small versions of these (powered by batteries in most cases), for hobbyists, and other
home uses.
|
Sweet! I'll have to look them up. But I'd appreciate a link ... because another "doc johnson" makes sex toys.... !
I've attempted to make a buzzer the last two days, but I have doubts it will be powerful enough to be effective. It's definitely not very high
frequency.
I bought a bunch of cell telephone vibrators and have been trying to make a buzzer to remove bubbles. I epoxied two vibrators together and extended
them with a bolt and heat shrink tubing after soldering the wires in series. They run at 2.5V or less, so it takes two of them to withstand a 5V USB
wall plug adapter.
I haven't tested it yet ... but it's the best I could figure out how to do on my own.
In the background of the picture is a plaster of paris + pearlite insulator jacket I made for a 50mL Erlenmeyer flask. This is the jacket I made
before I thought about vibrators. In the foreground are the waterproof cell-phone vibrators and the heat shrunk pair of vibrators that I bought last
week.
To make the jacket, my son used a coke-can as an outside mold after hammering the bottom of the pop can flat. He then put the Erlenmeyer flask inside
(obviously, he didn't get it exactly centered) and we poured a plaster pearlite mix into the can up to the neck of the flask. I don't think I'd
hammer the bottom flat again, though ... but pour something in there that makes a level surface. The can shape is warped at the bottom and getting
rid of that would be easier to do by pre-filling it with something. The can was pretty easy to peel off after scoring it with a razor blade once the
plaster was set.
You can see the air bubble areas on the surface of the plaster. They;re generally along the outside rim near the bottom. There is only one void
going through the plaster. I broke the finished jacket apart to check how far the voids penetrate. That's why there's a rubber band keeping the
pieces together. But a vibrator would have definitely made a better casting.
The only problem with regular plaster as a heat jacket, is that it becomes weak as it drys out. So, I still need to figure out how to make an
anhydride/plaster material or perhaps weak silica gel re-enforcement.
Edit: forgot the picture.
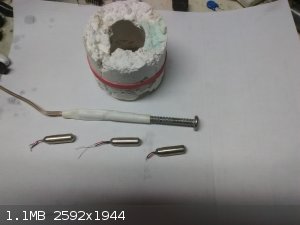
[Edited on 14-2-2018 by semiconductive]
|
|
Bert
Super Administrator
       
Posts: 2821
Registered: 12-3-2004
Member Is Offline
Mood: " I think we are all going to die. I think that love is an illusion. We are flawed, my darling".
|
|
A cheap electric vibratory or orbital sander without the sand paper attached makes a functional vibrator to work air out of thixotropic mixtures
(mud!) or other semi fluid things.
https://community.fornobravo.com/forum/good-background-infor...
|
|
SWIM
National Hazard
  
Posts: 970
Registered: 3-9-2017
Member Is Offline
|
|
Yeah, they make sex toys, but many of them vibrate.
Just get one that doesn't look so, 'realistic' it'd be an embarrassment in the lab.
(Or get borrowed all the time.)
Face it, low-voltage battery power, no venting so they're unlikely to spark a fire, and no need for yet another plug and wire across your work-space.
And they work under water too!
They're actually pretty well adapted to lab uses if you don't need a lot of power.
|
|
Bert
Super Administrator
       
Posts: 2821
Registered: 12-3-2004
Member Is Offline
Mood: " I think we are all going to die. I think that love is an illusion. We are flawed, my darling".
|
|
I NEED MORE POWER!!!
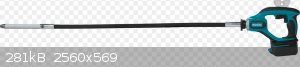
|
|
zed
International Hazard
   
Posts: 2283
Registered: 6-9-2008
Location: Great State of Jefferson, City of Portland
Member Is Offline
Mood: Semi-repentant Sith Lord
|
|
I used to be buddies, with an industrial type, manufacturing jeweler. Molding is done as follows.
You need a vacuum pump, a decent one, with a motor. It doesn't need to pull a super high vacuum, but a hearty one.
Attach a large thick flat metal plate to the top. Route vacuum hose or tube through the bottom of the plate.
Position and seal with grease or gasket, an inverted glass bell housing, over the vacuum outlet on the plate. ( In place of a bell housing, An upside
down pressure cooker might also serve).
Pour your freshly mixed investment into your mold, place it in the chamber. Seal. Turn on the vacuum pump.
This will vibrate hard enough to dislodge bubbles, while the vacuum... simultaneously causes the investment to boil.
Produces a nice clean casting, or mold. Dry it out and bake it. Or, for jewelry, burn it out, and cast metal in it.
Now, you did remember to spray everything with silicone mold release, right? This might prove helpful too.
Since a picture is worth a thousand words, I'll see if I can find something on Youtube.
Oh, also, I have been told, there are many types of plaster.
Crystobalite? I'll check.
OK, about minute 5:00, this guy sort of demos the set-up.
Not my favorite demo ever, but it beat the others, via its brevity.
https://www.youtube.com/watch?v=IGUU-0RBneI
[Edited on 15-2-2018 by zed]
[Edited on 15-2-2018 by zed]
[Edited on 15-2-2018 by zed]
[Edited on 15-2-2018 by zed]
|
|
happyfooddance
National Hazard
  
Posts: 530
Registered: 9-11-2017
Location: Los Angeles, Ca.
Member Is Offline
Mood: No Mood
|
|
Quote: Originally posted by zed  |
Position and seal with grease or gasket, an inverted glass bell housing, over the vacuum outlet on the plate. ( In place of a bell housing, An upside
down pressure cooker might also serve).
|
I have heard of an S.S. pressure cooker imploding under vacuum, so proceed with caution.
|
|
Bert
Super Administrator
       
Posts: 2821
Registered: 12-3-2004
Member Is Offline
Mood: " I think we are all going to die. I think that love is an illusion. We are flawed, my darling".
|
|
There are a ton of vacuum vessels being offered online, courtesy of certain drug extraction tech now popular. Most of them appear to be re-purposed
pressure cookers.
https://www.wired.com/2013/02/hash-oil-explosion/amp
https://www.amazon.com/gp/aw/s/ref=is_s_ss_i_0_15?k=vacuum+c...
The aspiring chemical engineering set seem to be having accidents with flamable vapors mostly, not implosions. But it's certainly a thing to consider.
About 35 years back, I was walking through the machine shop at the U. Physical sciences labs support building. Someone was leak testing the welds on a
new large vacuum chamber, he just threw a sheet of rubber and a (perhaps 3/8" thick? I didn't measure) steel plate over the upward facing end, didn't
want to waste time with correct Cu crush gasket, turning all those bolts. Connected it to a pump and started to evacuate the chamber.
He didn't bother to consult strength of materials, calculate surface area, etc. and do the math, that sheet of steel was plenty strong looking.
About the time I was walking by, the upward facing steel plate on the (secured only by gravity) chamber got sucked in. The chamber was heavy rolled
stainless steel, about 5' tall and perhaps 3' wide. As the plate moved down... The whole chamber moved UP. Really fast.
There was an impressive hole made in the roof, which was light sheet metal with transparent fiberglass panels. Then it CAME BACK. This produced very
mpressive acoustic emmissions: going up, creating the new roof vent and landing, shortly followed by debris.
BOOOM! CRAAAASH!! BOINNNNNNNGGGGGGGG! (tinkle, tinkle, clank)
Well. Memories.
[Edited on 15-2-2018 by Bert]
|
|
OldNubbins
Hazard to Others
 
Posts: 136
Registered: 2-2-2017
Location: CA
Member Is Offline
Mood: Comfortably Numb
|
|
https://youtu.be/6hP0L1hqnPM
I wouldn't recommend it but I have been using a heavy-walled glass vase (similar to the one pictured) for over a year now with a single-stage pump
pulling to -28/29 inHg. I even lapped the lip of it flat with silicon carbide so it seals on an aluminum plate with a little bit of grease. I like to
think it adds a little excitement to an otherwise boring process.
|
|
zed
International Hazard
   
Posts: 2283
Registered: 6-9-2008
Location: Great State of Jefferson, City of Portland
Member Is Offline
Mood: Semi-repentant Sith Lord
|
|
Being a giant, I am generally of the opinion, that bigger is better.
This is decidedly not always the case with vacuum vessels.
If it is gonna be big, it better have the heft to take a heavy load.
Those jewelers of yesteryear, we referred to earlier, usta sometimes boil out their plaster investment via an aspirator pump in line with a 55 gallon
steel drum, set up as a vacuum reservoir.
Pull a pretty hard vacuum in the drum, close the valve to the aspirator, pour the investment, place the bell jar, then open the valve to the vacuum
chamber. Nice!
Apparently, this works pretty well.... for a while. Then, one day, probably at the worst possible time, that 55 gallon drum, collapses like it has
been stepped on by an elephant.
Pressure cooker as bell housing? Maybe. Depends on the thickness of the walls, and the diameter.
|
|
unionised
International Hazard
   
Posts: 5126
Registered: 1-11-2003
Location: UK
Member Is Offline
Mood: No Mood
|
|
Quote: Originally posted by Bert  |
About 35 years back, I was walking through the machine shop at the U. Physical sciences labs support building. Someone was leak testing the welds on a
new large vacuum chamber, he just threw a sheet of rubber and a (perhaps 3/8" thick? I didn't measure) steel plate over the upward facing end, didn't
want to waste time with correct Cu crush gasket, turning all those bolts. Connected it to a pump and started to evacuate the chamber.
He didn't bother to consult strength of materials, calculate surface area, etc. and do the math, that sheet of steel was plenty strong looking.
About the time I was walking by, the upward facing steel plate on the (secured only by gravity) chamber got sucked in. The chamber was heavy rolled
stainless steel, about 5' tall and perhaps 3' wide. As the plate moved down... The whole chamber moved UP. Really fast.
There was an impressive hole made in the roof, which was light sheet metal with transparent fiberglass panels. Then it CAME BACK. This produced very
mpressive acoustic emmissions: going up, creating the new roof vent and landing, shortly followed by debris.
BOOOM! CRAAAASH!! BOINNNNNNNGGGGGGGG! (tinkle, tinkle, clank)
Well. Memories.
[Edited on 15-2-2018 by Bert] |
If I get time I will post the details of the "imploding fish-tank disaster".
In the mean time, be very careful drawing a vacuum on anything that's not engineered for it.
Atmospheric pressure is something of the order of a ton to the square foot.
|
|
semiconductive
Hazard to Others
 
Posts: 325
Registered: 12-2-2017
Location: Scappoose Oregon, USA.
Member Is Offline
Mood: Explorative
|
|
Quote: Originally posted by zed  | I used to be buddies, with an industrial type, manufacturing jeweler. Molding is done as follows.
You need a vacuum pump, a decent one, with a motor. It doesn't need to pull a super high vacuum, but a hearty one.
|
Yes, I've seen a number of people do that. Thanks for the video link.
Did you notice how the video author used a special "burn out oven" to get rid of the wax ring?
If you look on the inside, no heating elements are exposed. He also didn't put down a bowl to catch the wax. In order to burn off the carbons,
often a burn out oven will have an afterburner mounted outside the building to add more fuel and oxygen with a very small outlet hole. The problem is
the massive amount of CO that burning wax in an oven produces. So people but a clean hot burner in a chimney, typically with something like natural
gas or propane. The fire plus extra oxygen burns the black smoke into a clear gas so neighbors don't call the fire department. It's not something
that a home oven does well ...
This is why I've been hoping to find alternatives to wax; such as soluble materials that will dissolve in alcohol but not water. That way, they can
be "rinsed" out rather than burned out. If they are non-hydrocarbon, non-chloride, then even a residue won't hurt normal ceramic kiln elements ... or
cause the neighbors to get mad.
The kinds of things which have some good properties, but would fail due to water solubility are ammonium acetate, ammonium nitrate, ammonium
carbonate.... Those will gassify, but not produce a reducing atmosphere (CO) which ruins heating elements. So they could be sublimed and
re-condensed.
If you come across any water insoluble chemicals that sublime at low temperatures, or produce harmless gasses (CO2 instead of CO); I'm still looking
for something cheap and decent. IF there was only something like urea, but which could be made to dissolve in alcohol but not water ... it'd be
great.
Salts that dissolve in water but not alcohol, are at least partially useful. They can be coated with clay mixed with alcohol; and then after firing,
they can be embedded in plaster while it hardens and a hole poked into it.
Quote: |
Oh, also, I have been told, there are many types of plaster.
Crystobalite? I'll check.
|
Yes, there are dozens of kinds of plaster.
Taking regular plaster, adding a little sulfuric acid to get rid of calcium carbonate, and then spreading it thin and cooking it in the oven to 425F
will convert the plaster to anhydrite; a hard plaster. Adding a little more sulfuric acid, and calcium chloride, can make a very hard set plaster.
(stucco!).
Plaster can also be mixed with salts like potassium chloride which will partially convert the plaster into potassium sulfate. I tried an experiment
where I did that, because I wanted to isolate the potassium sulfate and see if I could use it as a replacement for wax when used with alcohol-clay.
Curiously enough, the more I boiled the KCl - CaSO4 mix in water ... the more water it took up and foamed. The volume expansion was easily 3x that
of normal plaster. This made me thing it would make a better insulator!!! But... as the mix dries, the foam collapses. The effect if very similar to
methyl-silicate being made into "blue smoke." If there was a way to dry the potassium-gypsum mix without collapsing it ... the micro pores would
boost the insulation value of the material a-lot!
[Edited on 18-2-2018 by semiconductive]
|
|
happyfooddance
National Hazard
  
Posts: 530
Registered: 9-11-2017
Location: Los Angeles, Ca.
Member Is Offline
Mood: No Mood
|
|
For increasing insulation, have you tried adding vermiculite? I made some cheap firebricks with a combination of portland cement and vermiculite, they
insulated very well and worked for my purpose.
|
|
NedsHead
Hazard to Others
 
Posts: 409
Registered: 9-12-2014
Location: South Australia
Member Is Offline
Mood: No Mood
|
|
If you do an image search for homemade degassing chambers you'll get some good ideas on design, lots of hobbyists who do resin casting and silicon
molding build their own degassing chambers.
I plan to build one myself someday.
|
|
semiconductive
Hazard to Others
 
Posts: 325
Registered: 12-2-2017
Location: Scappoose Oregon, USA.
Member Is Offline
Mood: Explorative
|
|
Quote: Originally posted by happyfooddance  | For increasing insulation, have you tried adding vermiculite? I made some cheap firebricks with a combination of portland cement and vermiculite, they
insulated very well and worked for my purpose. |
Silica glass and vermiculite also make a decent high temp cement. The problem with vermiculite is that it's fragile and breaks down over time,
especially when exposed to high heat or changing weight on top of it. eg: anything prolonged at 850C-1100C turns it to dust.
I just use it as loose fill in my kilns, and replace it every couple of years.
Plaster, on the other hand, once fired to above 800C becomes hard and surprisingly strong. It shrinks and may develop a surface crack ... but once
the dehydration is complete; it no longer changes or weakens. So, there is room for improvement with plaster given better techniques / formulations.
The only real problem with plaster (out of the box) is that it looses strength at low temperatures (150-200C) if allowed to dry out at those
temperatures. Plaster is a lot like clay ... low firing bisque is very weak, but high fired clay vitrifies. It would be nice if there was a simple
way to improve plasters long-term low temperature strength without resorting to a ceramics kiln.
My only conern with Vermiculite is that I would think it would ex-folliate and break from being handled unless totally encased inside a strong binder.
I could easily see using vermiculite for insulating glassware in a plaster mix ... I mean, vermiculite vs. perlite is just a convenience issue. BUt
with cement, that's going to take a lot of it. Silica cement is heavy.
Vermiculite just sitting as a fire brick makes some sense. I'd expect it to swell and crack with moisture changes if used long term in a kiln.
(>800C = problems.) That's a major reason that calcium additives to clay are a no-no. The calium "calcines" in a kiln, and then swells when
absorbing moisture again. But for lower temps it'd probably be fine.
However, for insulators of Erlenmeyer flasks and digital flow controlled condenser glassware; I'm expecting the jackets to be handled a lot; I'll
take them off, hang them up, put them back on, etc. Vermiculite wouldn't scratch the glassware and plaster won't ... but Portland cement is worse
than sand-paper. I would think that mix would play hell on glassware, wouldn't you?
[Edited on 18-2-2018 by semiconductive]
|
|
happyfooddance
National Hazard
  
Posts: 530
Registered: 9-11-2017
Location: Los Angeles, Ca.
Member Is Offline
Mood: No Mood
|
|
I wouldn't be dragging any glass across it. For annealing glass, I just throw it in a bowl of exfoliated vermiculite anyway, and put the whole bowl in
the kiln.
|
|
|