Pages:
1
2
3
..
6 |
Chemetix
Hazard to Others
 
Posts: 376
Registered: 23-9-2016
Location: Oztrayleeyah
Member Is Offline
Mood: Wavering between lucidity and madness
|
|
Ostwald style nitric production
After much searching on the site I found lots of postulating and concluding that Ostwald style nitric is all but impossible without the use of
platinum. And as such all but impossible to do back yard style, hence the considerable number of posts in the Birkland nitric thread. It seems more
doable but not very practical.
I have had some recent success with an NO2 generator using urea as a source of ammonia and oxidising with air using cobalt carbonate on sand as a
catalyst.
https://www.sciencemadness.org/whisper/viewthread.php?tid=68...
Now comes the next step, and some questions; is it better to just let the effluent gasses from the NO2 generator condense and form HNO3 with the water
from the ammonia oxidation, or absorb them with a salt like sodium carbonate to form NaNO3 with a little NaNO2. Or continue to process the nitric acid
to form 70%HNO3?
Can you use NO2 directly in some cases, instead of HNO3 and not bother about processing the 70%HNO3 to concentrated nitric?
|
|
Magpie
lab constructor
   
Posts: 5939
Registered: 1-11-2003
Location: USA
Member Is Offline
Mood: Chemistry: the subtle science.
|
|
I have never done this so these are just my opinions:
I once worked in a place that recovered NO2 from a calcination. It was converted to HNO3 using a pressurized absorbtion column. This seems difficult
for a home chemist.
However, if you could recover a dried (or damp) nitrate salt, say NaNO3, or possibly even better, Ca(NO3)2, then this could be treated with con H2SO4.
This should allow you to recover fairly concentrated HNO3 by distillation.
The single most important condition for a successful synthesis is good mixing - Nicodem
|
|
j_sum1
Administrator
      
Posts: 6372
Registered: 4-10-2014
Location: At home
Member Is Offline
Mood: Most of the ducks are in a row
|
|
IIRC (and I may be mistaken) the OP requires elevated temperatures and pressures as well as the catalyst -- around 5-10 atmospheres and greater than
250°C. Then a considerable volume of NO needs to be fed back into the process. (I seem to recall 90% feedback and 10% throughput.) And the
catalyst does degrade relatively quickly -- hence the standard addition of rhodium to the platinum to make it more durable.
Together this presents a number of significant hurdles for the amateur chemist. It is not just finding a cheap catalyst substitute. The engineering
looks to be challenging.
If you can come up with something workable, (a) awesome -- well done and (b) you will find a lot of interest in your work and maybe a few who would
like to replicate it.
|
|
Chemetix
Hazard to Others
 
Posts: 376
Registered: 23-9-2016
Location: Oztrayleeyah
Member Is Offline
Mood: Wavering between lucidity and madness
|
|
Industrial scale nitric is going to use techniques that milk every last mol and kilojoule. In trying to compete with industrial efficiencies I'll
admit defeat right now. However, the small scale has it's advantages. For one thing, the ability to cool the NO2 down and get more N2O4 in the
effluent gas is a gain in efficiency, just the ratio of the volume of the apparatus compared to its' surface area means passive cooling is going to be
more effective.
In the SM library I found Absorption of Nitrous Gasses, a 1933 text but an exhaustive tome on the dynamics of NO2 absorption and quite
instructive.
3NO2 + H2O -> 2HNO3 + NO
Is the critical reaction and implies the feedback step necessary to make the most from the left over NO.
Choice- do you feed it back to the NO stage before the air inlet to get reoxidised or do you let it get absorbed in a tower arrangement and make
nitrous acid (4% @ 25C) which can get oxidised with air to HNO3.?
A set of towers with broken glass to increase surface area would probably be the simplest engineering solution to the absorption of the left over NO.
Because the reaction in the tower: 2HNO2 + O2 -> 2HNO3
would continue to convert the NO into HNO3.
Industry would prefer this reaction to occur:
N2O4 + H2O → HNO2 + HNO3
and the subsequent
2HNO2 + O2 -> 2HNO3
in the tower means no need to pump back your NO, but only if you have N2O4 which is favoured by lower temperatures (higher pressures).
This would mean costly active cooling (or pressure) and power consumption in industrial chemistry, but achievable by passive low energy schemes on
small scale, which means more N2O4 at lower cost on the benchtop. And when you consider you are making nitric, despite the inefficiencies, you are
going to be still miles ahead in terms of of buying retail quantities of acid. So what, you let a bit of NO go up the tail pipe, you've probably got
80% conversion to nitric from urea. An industrial operator would be put against the wall for that sort of efficiency, but a back-yarder? Laughing!
I figure 6n Urea makes a theoretical 11n HNO3 with reoxidation of the formed HNO2 to HNO3. Combined with the left over water from the oxidation of
ammonia after conversion to HNO3 ( including the reoxidation of NO or HNO2) there should be 12n H20
11n HNO3 +12n H20 should be around 76% HNO3 by weight
Even if you achieve the azeotrope with water of 68%, this process is looking pretty good.
Aaaaarh! The catalyst, how long can you run the catalyst for? If you are using Pt/Rh at nearly 1000C you are going to have some problems with burn
through of your gauze plus the volatisation of the metal.
Cobalt oxide on silica (or other refractory) I think is going to cope admirably. I've identified that cobalt seems slower in it's conversion rate and
as such won't generate the rate of localised heating to keep the catalyst bed at self sustaining temperatures. A bitch for industry, but a few tens of
Watts to keep the reaction zone at 700C for a pilot plant is nothing. I thought about using the waste heat from the reactor to power the urea
degenerator. But I don't think there's even enough to do that at small scale.
I think Magpie's suggestion of CaNO2 might just be the best way of concentrating and using the NO2 without concentrating the nitric acid.
I'll try an absorption tower and see what is possible.
[Edited on 16-12-2016 by Chemetix]
|
|
j_sum1
Administrator
      
Posts: 6372
Registered: 4-10-2014
Location: At home
Member Is Offline
Mood: Most of the ducks are in a row
|
|
I like the way you think Chemetix. It all sounds good.
|
|
Chemetix
Hazard to Others
 
Posts: 376
Registered: 23-9-2016
Location: Oztrayleeyah
Member Is Offline
Mood: Wavering between lucidity and madness
|
|
If I were to add a small amount of SO2 to the NO-> NO2 chamber, I'm thinking that NO2 + SO2 -> SO3 + NO would result.
Net effect is the NO would reoxidise, SO3 would suck up the water and become H2SO4 and leave you with Conc. HNO3
A byproduct of the process is concentrated H2SO4.
Quel dommage!
|
|
Fleaker
International Hazard
   
Posts: 1252
Registered: 19-6-2005
Member Is Offline
Mood: nucleophilic
|
|
I know that at large silver refineries (like that of Eastman Kodak) where they dissolve metric tons of silver to make photograde silver nitrate, all
of the nitrogen oxides go through something called a Johnson Scrubber. Which is just a big packed bed scrubber filled with dilute nitric acid and like
10% hydrogen peroxide. I think this is done to firstly convert any NO to NO2 which then becomes HNO3. The scrubber solution gets put into the next
batch for dissolving the silver nitrate. Any leakage gets mopped up with alkaline sodium hydrogen sulfide solution.
Once I did an experiment with an autoclave and 75%Ag 25% Cu (m/m basis) and 30% w/v nitric acid. I loaded a stainless 2 liter Parr with the metal, put
the acid in, and closed the hatch. The pressure of NO2/NO rapidly rose to several hundred PSI. I then introduced pure oxygen into the reactor and
measured an exotherm and a dramatic pressure reduction to near ambient pressure.
I tried again by putting the metal in, pressurizing it all to 50 psi O2 and pumping in nitric acid. The pressure never got above the oxygen
overpressure.
Neither flask nor beaker.
"Kid, you don't even know just what you don't know. "
--The Dark Lord Sauron
|
|
Chemetix
Hazard to Others
 
Posts: 376
Registered: 23-9-2016
Location: Oztrayleeyah
Member Is Offline
Mood: Wavering between lucidity and madness
|
|
I wonder if under the high pressures you didn't end up making something like N2O3 or N2O5?
|
|
WGTR
National Hazard
  
Posts: 972
Registered: 29-9-2013
Location: Online
Member Is Offline
Mood: Outline
|
|
Quote: Originally posted by Chemetix  |
In the SM library I found Absorption of Nitrous Gasses, a 1933 text but an exhaustive tome on the dynamics of NO2 absorption and quite
instructive. |
I bought an original copy of that. Had to have it shipped from Australia to the U.S. I considered it well worth the price, and it occupies a place
of honor on the bookshelf.
If you want to, you can adsorb NO2 onto silica gel.
https://www.sciencemadness.org/whisper/viewthread.php?tid=48...
The NO just passes through unaffected. It's best if the gasses are dry, since water is also adsorbed. In this way, dilute streams of NO2
can be concentrated, allowing an easier conversion into nitric acid, and at a higher acid concentration. Also, the silica gel is a handy way of
storing NO2. To release the NO2 vapors, the silica gel can be heated up. In the linked video, the gasses weren't dried, so
some water was also getting adsorbed.
I'm working (off and on) on a Birkeland-Eyde reactor design. By drying the gasses going into the reactor, allowing the exit gasses time to oxidize,
and then adsorbing the NO2 onto a silica gel column, I'm able to easily measure the efficiency by comparing the before and after weights of
the adsorption tube.
Since you're producing water in the reaction (?), perhaps that could be adsorbed in a drying column right after the gasses cool down, before the NO
has time to oxidize. After time spent in the oxidation chamber, then the resulting gasses could be adsorbed in a second column, that could be
weighed...? Just an idea.
|
|
Chemetix
Hazard to Others
 
Posts: 376
Registered: 23-9-2016
Location: Oztrayleeyah
Member Is Offline
Mood: Wavering between lucidity and madness
|
|
silica adsorption
Quote: |
If you want to, you can adsorb NO2 onto silica gel. |
I saw your silica gel technique and have been ruminating away on the idea. Brilliant strategy I have to say, it offers so many possibilities? Can you
cool down the NO2 soaked gel and the NO2 dimerizes in situ? How much can you store on the gel? Being able to analyse what's going on has been a
concern.
I've been eyeing off an old GC sitting in the corner and wondering if I should resurrect it for analytical work on the reactor. Maybe some gel and a
balance is the quick 'n dirty way.
I have recently taken the design beyond proof of concept and ran an absorption tower as planned (water with broken glass) and was happy with the
results. No obvious NOx was leaving the tower. There were white wisps, but it seemed to be nictric fumes. The product in the tower water was very
weak, but the condensate at the base of the oxidation chamber took paint off my retort stand when a ball joint leaked. It fizzed furiously with
bicarb.
I'm making the most of a few days off to work on the latest incarnation.
Improved flow rates for a start; that sand is too fine, there's only so much you can push through, so a coarser more porous catalyst support. Larger
oxidation chamber (now with vortex action! oooohh!) and a condenser element in the chamber.
I'd be stoked if I could try a boyhood fantasy or running a N2O4 - Hydrazine liquid fueled rocket engine, just a static test would be awesome. It's a
seriously toxic little cocktail if things go to shit; this will need some thinking about. But with NO2 at hand the project is now less of a fantasy.
|
|
Fleaker
International Hazard
   
Posts: 1252
Registered: 19-6-2005
Member Is Offline
Mood: nucleophilic
|
|
What about just absorbing some chloroplatinic acid onto aerogel or molecular sieve and reducing it with hydrogen?
Chemetix, you ever read that book Ignition! in the SM library?
Neither flask nor beaker.
"Kid, you don't even know just what you don't know. "
--The Dark Lord Sauron
|
|
Chemetix
Hazard to Others
 
Posts: 376
Registered: 23-9-2016
Location: Oztrayleeyah
Member Is Offline
Mood: Wavering between lucidity and madness
|
|
Quote: |
What about just absorbing some chloroplatinic acid onto aerogel or molecular sieve and reducing it with hydrogen |
This would work I'm sure; I can at any time use a quartz frit and coat it in platinum lustre paint all of which I have at hand. I have a quantity of
palladium chloride which would reduce onto a frit as well. But the mission has been to avoid the PGMs. This is science madness after all.
There is no greater joy than being told you can't have something and you get to say fine! I'll make it from air, water and dirt! Except perhaps, when
you find a piece of literature that reports a synthesis using some exotic complex of iridium in an even more exotic solvent. And you replicate the
results and improve the yield using hair gel and a dissolved coin.
This is going to be industrial chemistry McGuyver style, sans mullet and rayban aviators. Disappointing to hear the remake is tween Bond. There goes
any new inspiration for the next generation of tinkerers.
Sorry aga- that's why there's a trend to talk more than do. You cant tinker with something unless you have a genius degree and work for a government
department as far as popular culture is concerned. In fact how do you get a screenager to do anything AFK?
Ps. I'll look for ignition! I hadn't seen or had overlooked that one.
[Edited on 22-12-2016 by Chemetix]
|
|
Fleaker
International Hazard
   
Posts: 1252
Registered: 19-6-2005
Member Is Offline
Mood: nucleophilic
|
|
PGMs get no love :-/
Sad state that platinum prices are at now.
Neither flask nor beaker.
"Kid, you don't even know just what you don't know. "
--The Dark Lord Sauron
|
|
WGTR
National Hazard
  
Posts: 972
Registered: 29-9-2013
Location: Online
Member Is Offline
Mood: Outline
|
|
Quote: Originally posted by Chemetix  | There is no greater joy than being told you can't have something and you get to say fine! I'll make it from air, water and dirt![Edited on 22-12-2016
by Chemetix] |
I think we share a fascination with this. There's something to be said about making a salt (NH4NO3) out of air and electricity
(even the water vapor can be condensed from air).
If you include molten carbonate electrolysis, (I've done some of this), then one can isolate solid carbon from the carbon dioxide in air. From there,
carbon monoxide can be synthesized, and then with hydrogen, a whole slew of hydrocarbons.
[Edited on 12-22-2016 by WGTR]
|
|
Chemetix
Hazard to Others
 
Posts: 376
Registered: 23-9-2016
Location: Oztrayleeyah
Member Is Offline
Mood: Wavering between lucidity and madness
|
|
Benchtop Ostwald Pilot Plant Success
Here is the pilot plant.
It's a photo shoot of the unit in operation.
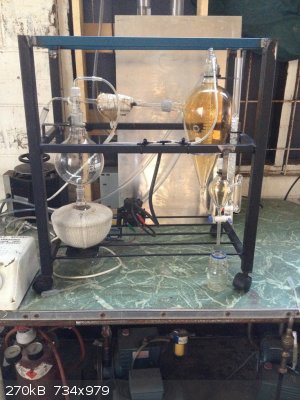
In a converted TV stand you can see the urea decomposer in the mantle front left. The black lump in the middle is the air compressor. The reactor tube
runs into the converted 2L sep. funnel which admits air via the custom condenser fitting. The condensate runs into a reservoir where excess gasses run
to an absorption tower.
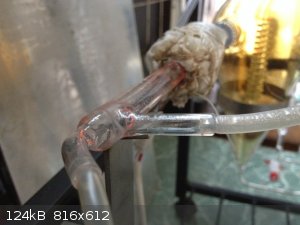
This shot shows where the ammonia air mixture is fed into the reaction zone, the nice red glow is transmitted up the quartz.
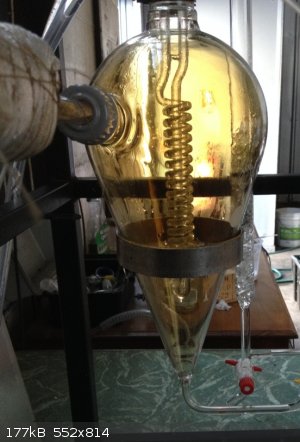
Red fumes; condensation forms on the walls and the condenser. That's nitric, baby! You can see the tower behind it and the take off tap to collect the
tower absorption.
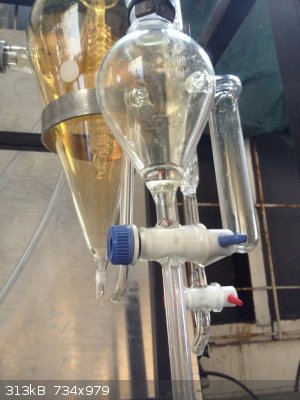
The condensate ends up in this collection flask and you can see the splash head type design to let the outlet gasses pass into the tower. There is
still a lot of fumes, enough to be visibly red, but once they go to the tower there is no evidence of anything leaving the tower. Kind of important
not filling the room with NOx.
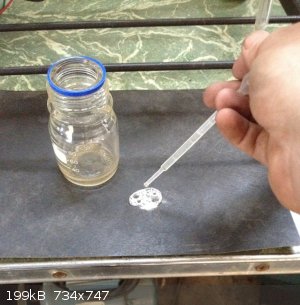
Does it fizz with bicarb? You betcha!
This Christmas. Give the gift of nitric!
[Edited on 24-12-2016 by Chemetix]
[Edited on 24-12-2016 by Chemetix]
|
|
j_sum1
Administrator
      
Posts: 6372
Registered: 4-10-2014
Location: At home
Member Is Offline
Mood: Most of the ducks are in a row
|
|
Unbelievable!
Realy well done. I'm gonna examine those pix closely when I get on a larger screen.
Merry Christmas.
|
|
symboom
International Hazard
   
Posts: 1143
Registered: 11-11-2010
Location: Wrongplanet
Member Is Offline
Mood: Doing science while it is still legal since 2010
|
|
This needs a sticky for the form this is a breakthrough
Not sure if anyone agrees with this reason nitric acid is a big topic
Also did you incorporate silica beads in the process
[Edited on 24-12-2016 by symboom]
|
|
Magpie
lab constructor
   
Posts: 5939
Registered: 1-11-2003
Location: USA
Member Is Offline
Mood: Chemistry: the subtle science.
|
|
Very nice and potentially very valuable to those in the world who have been denied this essential reagent.
Tell us about the air compressor please. What is the pressure in the oxidizer? Is that column open to the atmosphere? What is the strength of the
acid? Can you titrate it?
[Edited on 24-12-2016 by Magpie]
The single most important condition for a successful synthesis is good mixing - Nicodem
|
|
Chemetix
Hazard to Others
 
Posts: 376
Registered: 23-9-2016
Location: Oztrayleeyah
Member Is Offline
Mood: Wavering between lucidity and madness
|
|
Yesterday was it's first real run, I'll do some do some titrations soonish. But the air compressor might as well be an aquarium pump, it's a 24V dc
thing that came out of something, I can't recall what, but it's low power and chugs along on 12V.
There's no real pressure in the system, just the back pressure of the small amount of water being bubbled in the tower which is open to the air. It's
actually a simple system. Don't be put off by all the complicated glassware, I did it this way because I can. I'm sure this could be made with found
items and a bit of creativity. No silica used, yet! I might find a use for it, but drying the gasses seems more effort than it's worth. Although the
ammonia generator spits out a fair amount of water vapour and only dilutes the acid. I could put a condenser coil in the mixing flask to reduce that.
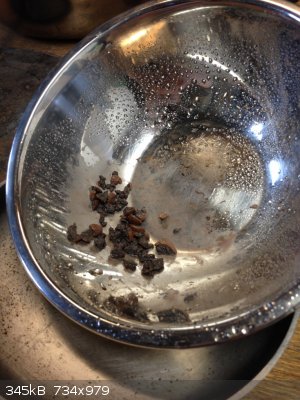
I modified the catalyst in the pilot plant. It's crushed and screened expanded clay balls used as a growing medium. I sieved out the fine stuff and
used another screen to take out the bigger more irregular pieces. A spatula's tip loaded with Co carbonate and a little demineralised water and a good
churning to get it coated. That's it! Better flow rates and seems to work at lower temperature, the current draw was only 1.7A at 24VAC in the heater
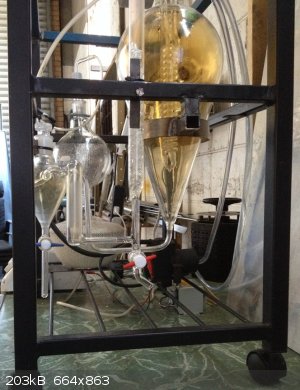
This is the tower, packed with broken glass and a little water. The reservoir with the blue tap holds the concentrated stuff and the exhaust gasses
pass into a vertical anti suck back column before running along a small tube to the base of the tower. The red tap can draw off the dilute acid as
needed.
One other thing to note is the syringe attached to the reactor inlet. (not in this shot by the way)
Slowly draw back 10ml, disconnect the syringe and put a finger over the end quickly, then put the tip into some water. The ammonia dissolves into the
water and the water fills the syringe to replace the volume. You now know what ratio of ammonia to air is being fed to the reactor.
I'll keep you informed of process specs and mods as I make them, the concentration of the acid is going to be the first test.
[Edited on 25-12-2016 by Chemetix]
|
|
Marvin
National Hazard
  
Posts: 995
Registered: 13-10-2002
Member Is Offline
Mood: No Mood
|
|
Quote: Originally posted by Chemetix  | Slowly draw back 10ml, disconnect the syringe and put a finger over the end quickly, then put the tip into some water. The ammonia dissolves into the
water and the water fills the syringe to replace the volume. You now know what ratio of ammonia to air is being fed to the reactor.
| This blows me away, just a brilliant bit of lateral thinking.
|
|
Magpie
lab constructor
   
Posts: 5939
Registered: 1-11-2003
Location: USA
Member Is Offline
Mood: Chemistry: the subtle science.
|
|
This is a really nice project. I have the feeling that you are just getting started on optimizing.
Your ammonia generator is just charged with urea and a little water. Wiki says that a method suitable for lab generation of ammonia is to use urea
mixed with Ca(OH)2. This ties up the CO2 as CaCO3. Would this be an advantage to your process?
[Edited on 25-12-2016 by Magpie]
The single most important condition for a successful synthesis is good mixing - Nicodem
|
|
Chemetix
Hazard to Others
 
Posts: 376
Registered: 23-9-2016
Location: Oztrayleeyah
Member Is Offline
Mood: Wavering between lucidity and madness
|
|
Magpie, that's a fair point, one that I considered early on but discarded for a few reasons.
Making calcium carbonate is a right royal pain in the arse, the generator gets clogged with an insoluble mess that interferes with generation and then
it means either time or chemicals to clean it. The purist in me decided that no unwanted byproducts would be better. There is the fact that the rate
of production would vary and controlling the air ammonia ratio would be harder. The same goes for sodium hydroxide, which I tried; the two sit almost
unreacting in the flask and then give it a little heat VOOOM, too much ammonia.
The Water/Urea reaction is a text book first order reaction, very easy to control the rate with temperature and water concentration. It does generate
a fair bit of water vapour and I think that minimising that will help the final concentration a good deal.
|
|
WGTR
National Hazard
  
Posts: 972
Registered: 29-9-2013
Location: Online
Member Is Offline
Mood: Outline
|
|
If you preheat the gas feed, instead of applying all of the heat to the catalyst area, you can probably operate at a lower temperature overall.
Carbon dioxide is also very soluble in water. Keep that in mind as you sample the gas feed, if this gas is present.
I'm very impressed with your setup; jealous, in fact, but in a good way. Good job!
What do you estimate the gas feed to consist of (even if you think the number isn't very accurate)? It would provide a starting point for future
efforts, at least.
|
|
Chemetix
Hazard to Others
 
Posts: 376
Registered: 23-9-2016
Location: Oztrayleeyah
Member Is Offline
Mood: Wavering between lucidity and madness
|
|
The syringe technique relies on the ammonia absoption being a good deal quicker than the CO2 absorption. Doing a quick dunk in water fills the syringe
in about 30 seconds. I'd say leaving it there for an hour or more would take up most of the CO2. But the quick and dirty result came back with around
6% by volume. I think that around 12% in air is stoichiometrically balanced. It just meant that I turned off the air inlet to the oxidation chamber
and let the excess O2 oxidise the NO. It was obvious that the air bleed wasn't needed at the oxidation chamber because the chamber went a much deeper
colour without it turned on.
It does highlight that the rate of ammonia production is going to be the step that will allow higher production rates, and drying it will mean more
concentrated product.
So far the CO2 doesn't seem to hinder the process aside from being dead volume in the reaction stream.
I think a future project will absorb the ammonia into water to get rid of the CO2 and use the saturated solution to generate ammonia, a passive
recirculating system attached to the urea reaction will be the best way to go, and possibly use the waste heat from the reactor to generate ammonia
from the saturated solution.
I'm liking the suggestions and I think this is going to get a few brains thinking of better ways. I'm really hoping to see some experimentals come to
pass from other members.
It has struck me as I write this that I could do a kit of sorts.
If you PM me I can send a small piece of quartz tube with or without inlets to you for a few dollars US$40-$50. Shipping is variable so I could only
guess at a value. I wish it was cheaper but quartz costs a bit and working with it is slow. (if you were a commercial customer the value would be
easily 3 times the SM price.) I'll send some pre-prepared catalyst if you like.
Sorry if this setup is too much glass-porn for some of you, @WGTR. I work with it and I still love a sexy bit of glassware.
[Edited on 25-12-2016 by Chemetix]
|
|
WGTR
National Hazard
  
Posts: 972
Registered: 29-9-2013
Location: Online
Member Is Offline
Mood: Outline
|
|
OK, so the gas feed appears to be oxygen-rich...that's what I was wondering about.
I like working with glass, too, but i don't have all the fun, expensive, tools. I'm pretty much limited to working with tubing that I get from the
science store in town. Soda-lime is pretty easy to join and work with various hand propane torches, and I can fuse boro if I'm careful. But
quartz...I just can't! I would love to have a glass-blowing lathe!
The kit idea is a good one. My first thought, however, is to see if the reaction temperature can be lowered enough that borosilicate can be used.
That's why I was thinking of preheating, and whether it would give better heat distribution in the catalyst, and hopefully allow a lower maximum
temperature. Quartz, however, is the Cadillac of glass. It doesn't get any better. It's just, as you say, expensive and difficult to work with.
I'm wondering if the blue-indicating silica gel might work as a catalyst. It normally contains a cobalt salt in small amounts. Sorry, I keep
obsessing about silica gel. For ethanol dehydrogenations, I've prepared the catalyst by co-precipitation of the active copper hydroxide with the
inactive magnesium hydroxide support. I think cobalt could work the same way. Starting from a soluble salt makes the starting materials easier to
define for a hobbyist, I think. Maybe something like this would work, and be easier to define and repeat. Just an idea. I'm trying to think of ways
to minimize variables and avoiding the possible issue of "I just did it the way you did, and I couldn't get it to work". If something like "builder's
sand" or clay particles are used, then ideally those materials need to be defined as to purity and provenance, so that others can duplicate it. I can
try to prepare this precipitated catalyst if you want, to see if it has the structure that I hope it will. Let me know the inner diameter of the
catalyst tube.
|
|
Pages:
1
2
3
..
6 |