Melgar
Anti-Spam Agent
   
Posts: 2004
Registered: 23-2-2010
Location: Connecticut
Member Is Offline
Mood: Estrified
|
|
Galinstan-activated aluminum: an inexpensive, easy-to-use, easy-to-store, nontoxic alternative to Al/Hg reduction
A lot has been written regarding using aluminum/gallium alloys as reducing agents in organic chemistry, or as a source of hydrogen gas when mixed with
water. However, the gallium content of these alloys needs to be quite high in order to produce a reaction, which is less than ideal, considering
gallium doesn't participate directly in the reaction, and is several orders of magnitude more expensive than commercially-pure (99%+) aluminum.
Galinstan (Gallium + Indium + Tin) is a low-melting-point alloy that melts at a lower temperature than ice, containing gallium as the majority of its
makeup. This alloy can be prepared simply by heating 68% (by mass) Ga, 22% In, and 10% Sn. The tin may need elevated temperatures to dissolve,
although a Ga/In alloy will still be liquid at room temperature. Commercial galinstan also has small amounts of antimony and bismuth in it (<1.5%
wt.) to lower the melting point and improve other physical properties.
Preparation of the galinstan alloy
To 34g of molten gallium (35˚C) was added 11g of indium scrap. The indium readily dissolved, but left behind a significant amount of papery indium
oxide that floated on the surface of the alloy. 0.5g of additional indium was added to compensate for the indium oxide that didn't dissolve. The
indium oxide was removed and saved for possible use later.
For the tin source, rosin-core lead-free electrical solder was selected, mainly due to it being readily available, but also due to the fact that it
contained 5% antimony (the other 95% being tin), which was noted in a German patent to improve the alloy's physical properties. 8g of solder was
removed from the spool, and heated with a propane torch in a stainless steel crucible. The rosin was burnt off, until only a thin lump of molten
solder was left in the crucible. The lump was weighed, and found to have only lost about 0.5g as a result of burning the solder. 2.5g was cut off
the solder lump with wire cutters, leaving 5g that was added to the alloy. Unlike the indium, the tin did not readily dissolve, and so the alloy was
heated with a propane torch in a pyrex test tube to about 200˚C, at which point the solder mixed with the rest of the alloy. A solidified droplet of
bismuth was added at this point, that had formed earlier when doing an experiment with molten bismuth. The droplet was not weighed. It dissolved
readily at the higher temperature. The alloy was allowed to cool, and moved to a separate holding vial. The alloy had wetted the inside of the test
tube, and this was removed by adding a very dilute aqueous HCl solution and shaking. The alloy collected in a large droplet at the bottom of the test
tube, and was removed with a pipette and added to the rest of the metal. (Aside: I think the reason this works is that the HCl creates like charges on
the surfaces of both the glass and the metal, which subsequently repel each other. This also works with dilute NaOH, though not quite as well.)
Preparation of the aluminum/galinstan alloy
For the aluminum source, I used dollar-store aluminum cooking pots that had clearly been stamped out of sheets. 1100 aluminum alloy works
particularly well for stamp-pressing, and is 99% aluminum, which accounts for its softness. Aluminum electrical wire also works, although the
preferred alloy these days is usually only 98.5% pure. Casting aluminum and structural aluminum are the least pure aluminum alloys, and should be
avoided. The two main impurities in aluminum are iron and silicon, which can be tested for by dissolving a small sample thoroughly in clear
half-strength hydrochloric acid. Yellow color indicates iron, while an insoluble light brown precipitate indicates the presence of silicon.
For melting the aluminum, you will need some sort of crucible. I bought mine from a jewelers' supply shop for $5, but it only needs to be able to
withstand 600-800˚C, so material is not that critical. You can use an indentation in concrete or a large enough rock as a crucible if you have to,
since you won't actually be pouring any molten metal. These would be better than using a steel crucible, which would contaminate the melt to an
unacceptable level. You'll need something to stir with; graphite rods are ideal, but if you're doing this outside and smoke isn't a problem, you can
use a stick. It will gradually burn away, but will only form charcoal and ash, neither of which will contaminate the aluminum. Really, just don't
use anything metal for stirring unless you know what you're doing. You'll also need a heat source that can apply enough heat to keep all your
aluminum molten at once. A propane hand torch with a one-pound tank like the one pictured can keep about 50g of aluminum molten at once. For
reference, this is 50g of melted-down aluminum:

If you don't know how much aluminum you'll be able to melt at the start, you can cut up your source into pieces and do something like this to keep
track of how much metal you're melting:
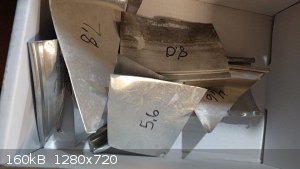
Start melting down aluminum, until you have the desired amount of molten metal, or until you reach the limit of how much metal your heat source can
keep molten at once. If necessary, you can cool it down, weigh it, then melt it again. Now weigh out an amount of galinstan equal to about 5% the
mass of your aluminum. Smaller amounts can work, just not as consistently. Larger percentages of galinstan will cause the aluminum to react more
quickly. After much trial and error though, I've settled on 5% as the best balance between allowing a smooth, predictable reaction and keeping
galinstan use low due to its relative expense compared to aluminum. You can weigh the galinstan in paper (preferably low-ash filter paper) then set
it all into the molten aluminum to minimize splatter. As soon as the two mix, you'll notice the consistency change. The melting point drops, and
it's easier to keep molten. You'll also notice that it forms a cement-like phase before it solidifies, unlike pure aluminum. It is critical
at this stage to throughly mix the two metals. Once the metals are thoroughly mixed, the molten metal can be covered and allowed to cool to
below 100˚C. At this point, the metal should have the approximate strength and physical properties of unfired clay; that is, not much strength at
all, and the metal should be easy to break using two pairs of pliers to grip it:
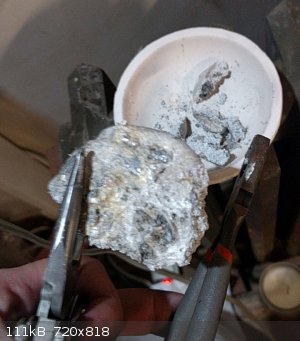
If the metal is too hard to break in spots, that's usually a sign that those spots didn't get enough galinstan mixed into them and will probably need
to be remelted with more galinstan in order to make them useful as a reductive agent. This is a good time to break up the metal into small pieces and
store it, preferably in an airtight glass jar. When added to water or alcohol, the metal will gradually break up into grains about the size of sand,
so you don't need to manually break it up into very small pieces. This alloy reacts slowly with air, and can be handled with dry hands, even without
gloves. The only danger in handling it, is if your hands are wet, and either you touch it or a small piece of it sticks to your skin, it can generate
enough heat from the reaction with water to burn you, though not very badly.
Typical reaction conditions
Substrates are initially dissolved in either water, a lower primary alcohol, or a mixture thereof, which act as hydrogen donors for the reduction.
Isopropanol can work, however under anhydrous conditions, it will react with aluminum to form aluminum isopropoxide, which can reduce ketones into alcohols, and transform aldehydes into esters.
For reductions in methanol, ethanol, and water, nitroalkanes are reduced to amines in excellent yields. Nitroolefins are reduced into their
corresponding alkyl amines due to a rearrangement that produces an imine. Reductive amination also proceeds smoothly. Stirring is highly
recommended, since this is a heterogeneous reagent, although in my experience, the alloy usually generates enough hydrogen bubbles to adequately
circulate the solution. Reaction rate can be controlled by the application of heating or cooling.
This reagent is also a convenient hydrogen source when added to water, and can be used as a more reactive form of aluminum in a number of reactions.
For example, it can be added to a solution of iodine in diethyl ether to give an ether solution of aluminum triiodide. It can also be reacted with
isopropyl alcohol to give aluminum isopropoxide, which can catalyze the conversion of ketones to alcohols in the presence of isopropanol, and
secondary alcohols to ketones in the presence of acetone.
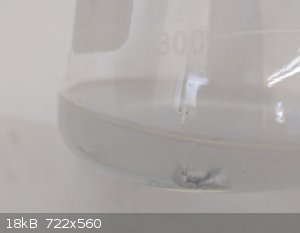
[Edited on 10/19/16 by Melgar]
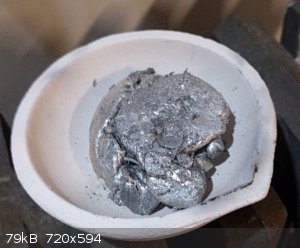
|
|
careysub
International Hazard
   
Posts: 1339
Registered: 4-8-2014
Location: Coastal Sage Scrub Biome
Member Is Offline
Mood: Lowest quantum state
|
|
No one has commented publicly yet, so I just want to say that I am glad to see this write up (indeed, I requested that one be prepared on another
thread).
Soluble mercury compounds are very hazardous materials, so a procedure that dispenses with them is a major step forward in green chemistry!
About that which we cannot speak, we must remain silent.
-Wittgenstein
Some things can never be spoken
Some things cannot be pronounced
That word does not exist in any language
It will never be uttered by a human mouth
- The Talking Heads
|
|
brubei
Hazard to Others
 
Posts: 188
Registered: 8-3-2015
Location: France
Member Is Offline
Mood: No Mood
|
|
Nice but it needs some sources.
|
|
Maroboduus
Hazard to Others
 
Posts: 257
Registered: 14-9-2016
Location: 26 Ancho Street
Member Is Offline
Mood: vacant
|
|
So, is the 'cement like phase' the aluminum coming out of solution?
Is the final result something like aluminum in a Galinstan matrix?
|
|
careysub
International Hazard
   
Posts: 1339
Registered: 4-8-2014
Location: Coastal Sage Scrub Biome
Member Is Offline
Mood: Lowest quantum state
|
|
Quote: Originally posted by Maroboduus  | So, is the 'cement like phase' the aluminum coming out of solution?
Is the final result something like aluminum in a Galinstan matrix?
|
I believe what is being described is the formation of a non-ductile mass of aluminum, due to gallium segregating at grain boundaries and causing
embrittlement.
So the aluminum is simply solidifying and forming crystals, and the gallium is coming out of solution along grain boundaries.
This is a well known phenomenon with aluminum and gallium, see for example this paper, "Brittle-to-ductile transition in polycrystalline aluminum
containing gallium in the grain boundaries".
This work is producing an alloy essentially identical with the 95/5 alloy mentioned here (and their conference paper is also attached).
http://www.purdue.edu/uns/x/2008a/080219WoodallAluminum.html
Attachment: woodall2008.pdf (519kB) This file has been downloaded 1718 times
[Edited on 19-10-2016 by careysub]
Attachment: itoh2010.pdf (3.2MB) This file has been downloaded 1359 times
About that which we cannot speak, we must remain silent.
-Wittgenstein
Some things can never be spoken
Some things cannot be pronounced
That word does not exist in any language
It will never be uttered by a human mouth
- The Talking Heads
|
|
careysub
International Hazard
   
Posts: 1339
Registered: 4-8-2014
Location: Coastal Sage Scrub Biome
Member Is Offline
Mood: Lowest quantum state
|
|
See also this presentation:
Attachment: production_woodallziebarth.pdf (643kB) This file has been downloaded 1436 times
About that which we cannot speak, we must remain silent.
-Wittgenstein
Some things can never be spoken
Some things cannot be pronounced
That word does not exist in any language
It will never be uttered by a human mouth
- The Talking Heads
|
|
Melgar
Anti-Spam Agent
   
Posts: 2004
Registered: 23-2-2010
Location: Connecticut
Member Is Offline
Mood: Estrified
|
|
Wow, they figured out a lot of the same stuff I did, but with better equipment and a better understanding of chemistry.
They also refer to the "Al-Ga-In-Sn" system. I was going to initially call this alloy "Algalinstan", but then decided that "Galinstan-activated
aluminum" sounded more professional.
As far as references, believe it or not, I never used any. I think back in 2009 I heard about aluminum and gallium forming a hydrogen-generating
alloy, but with the downside of requiring a lot of gallium. You couldn't get gallium quite as easily then, so I used galinstan from a mercury-free
thermometer. I also had a bunch of aluminum Chilean one-peso coins, each of which was worth 1/5 of a cent, and I found that if I put a drop of
galinstan on one, and scratched at the coin through the drop with a knife, I could get them to mix, which would make the metal extremely reactive with
water. I found a reference on the Hive or Rhodium or one of those sites about reductive amination with aluminum dissolved in gallium, and found that
reductive amination also worked with what I had. It would also reduce nitromethane to methylamine, which could be detected very easily by smell.
When I finally was able to get pure gallium, I found that alloys of aluminum and gallium were nowhere near as reactive as aluminum and galinstan, so I
just played around with ratios until I found one that worked consistently, and was slow enough that it approximated the reaction speed of an Al/Hg
reduction. This was back in 2009 or 2010. I posted about it, but never did a detailed writeup, just experimented a lot with it.
|
|
Melgar
Anti-Spam Agent
   
Posts: 2004
Registered: 23-2-2010
Location: Connecticut
Member Is Offline
Mood: Estrified
|
|
Just for the record, I found this page, which indicates the specific reactions that Al/Hg amalgam undergoes:
http://reag.paperplane.io/00000072.htm
I imagine this alloy behaves similarly, unless any of the metals catalyze additional reduction reactions. One thing that that page doesn't mention is
that after reducing a nitroolefin to an amino-olefin (enamine), the enamine rearranges into an imine, which is easily reduced under these conditions.
(Vogel, 5th ed. 769) However, there can be side reactions that produce dimerization before it gets to that point.
|
|
Melgar
Anti-Spam Agent
   
Posts: 2004
Registered: 23-2-2010
Location: Connecticut
Member Is Offline
Mood: Estrified
|
|
Another thing I'm discovering as I do more experiments with this reaction, is that aluminum purity seems to be very important for determining
reactivity. Aluminum alloys typically only vary by 1-2% for metal content, but the reactivities of those alloys vary wildly. Also, I've found that
these pans are MUCH more reactive, after being melted down, than any other aluminum source I've used:
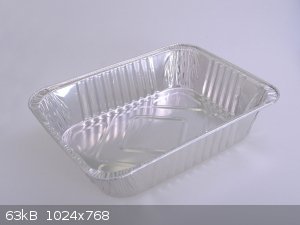
Preliminary research points towards 3004 aluminum as the likeliest contender, and the added magnesium could be what's increasing the reactivity. I
have yet to determine if or how magnesium changes the reducing activity of the alloy though. I'm having a hard time determining how aluminum reacts
with organochlorides and organobromides, though magnesium's reactions with organohalides are extremely well-documented. The only thing that I seem to
be able to find are warnings that methylene chloride and chloroform can undergo very energetic reactions in the presence of aluminum, but there's no
indication of what the products of that reaction would be. Presumably it'd result in various chlorinated alkanes and alkenes? There may just be no
information about the reaction products because the reaction is useless for synthetic purposes.
As far as reducing galinstan content in order to reduce reactivity of the resulting alloy, it doesn't work very well below 5% or so. I did 97%
aluminum, but then the galinstan doesn't diffuse throughout the metal uniformly, and different pieces of the resulting alloy vary a lot in their
reactivities. Another thing that I intend to try is an alloy composed of a eutectic mixture of just indium and gallium instead of galinstan. That
ends up being 3:1 based on mass of gallium to indium. It melts at 15˚C, which is 59˚F. Stannous chloride could then be added to a reaction mixture
as needed in order to fine-tune reaction rate. However, it seems to make the most sense to try running the reaction with only group 13 elements
(aluminum, gallium, and indium) at some point, to characterize it in its simplest form. Since tin is in group 14, it would seem to be most likely to
contribute to variation from the Al/Hg reaction.
One last observation: getting zinc or zinc salts into your reaction mixture is a mess, and I would recommend avoiding it as much as possible. Zinc
barely dissolves in galinstan, but is plated onto it if aluminum metal is present. This results in thick, dark gray zinc mud everywhere, which can
reduce gallium metal out of solution. Normally, gallium is reduced back onto the dissolving aluminum, and so the amount of gallium in the solution is
always quite low. Zinc can interfere with this equilibrium though, pulling more and more gallium out of the reacting alloy until it's no longer able
to form a liquid phase and the reaction stops. So to anyone thinking about trying to use zinc dust to reclaim galinstan: it wouldnt' work, and would
probably make your job a lot harder. Instead, try this:
To the collected and washed sludge from a dissolving aluminum reaction, slowly add 20% HCl solution until it becomes clear or stops dissolving.
Filter, then slowly add small pieces of aluminum (NOT dust!) to the liquid, waiting a few minutes after each piece to see how vigorously it reacts.
Hydrogen bubbles should evolve, and eventually, parts of the surface should form a liquid phase. The fraction of the metal in the liquid phase should
gradually increase, eventually getting you back your galinstan. This galinstan will be less pure though, due to impurities from the aluminum that
dissolved during the initial reaction. If you're tempted to try reducing the metals with zinc, just don't. In practice, it dissolves at a similar
rate as gallium, and the component metals of galinstan do not combine in a liquid phase like they do when using aluminum. Gallium seems to alloy with
the zinc, forming a higher-melting-point alloy than pure gallium, and then the other metals can't combine with gallium to form a liquid-phase alloy.
It just results in a mess, without much to show for your efforts.
|
|
Googolplex
Harmless
Posts: 5
Registered: 22-6-2017
Member Is Offline
Mood: No Mood
|
|
Quote: Originally posted by Melgar  |
Larger percentages of galinstan will cause the aluminum to react more quickly. After much trial and error though, I've settled on 5% as the best
balance between allowing a smooth, predictable reaction and keeping galinstan use low due to its relative expense compared to aluminum.
[Edited on 10/19/16 by Melgar] |
If you say "a smooth, predictable reaction". Can you give me a reference, like the a amount of aluminium and galinstan used and their reaction time?
Would it be possible to use the Aluminium and Galinstan as it is, for reduction reactions (in-situ)? What I mean is without melting Al or fusing Al
before you gone do the actual reduction reactions. Its should still be liquid beneed room temperature. And therefore I suppose it still will attack
the aluminium in the MeOH, I dont know if i'm right
Thought experiment that I thinking about :
In a three-neck round bottom flask fixed with a condenser I put 27.5g aluminium (99.995%) granules (2 - 3mm), 750 mL of lab grade MeOH. In a a
dropping funnel I mix 25g of ketone, 20g of nitromethane with 25 mL of MeOH. Now I drop the Galinstan in the round bottom flask. And wait until the
reaction starts. Then open the valve of the dropping funnel as it would be empty in about 40 - 45 min.
Will this work, do nothing or take longer than 45 min for all the aluminium to be comsunt by the Galinstan? I'm thinking this way because I think the
Al/Galinstan reduction reaction is to vigorous and would result in a short reaction time and temperatures above 50°C. It's very important that it
goes for 40 - 45 min, without exceeding 50°C.
|
|
Melgar
Anti-Spam Agent
   
Posts: 2004
Registered: 23-2-2010
Location: Connecticut
Member Is Offline
Mood: Estrified
|
|
Quote: Originally posted by Googolplex  | If you say "a smooth, predictable reaction". Can you give me a reference, like the a amount of aluminium and galinstan used and their reaction time?
|
I hesitated to answer this question at first, because I'd made some new developments, and am still sorting out the implications of them. I'm finding
though, that a 1:10 to 1:5 ratio is better, since it leaves much less sludge. The reaction is much more vigorous though, and I've been experimenting
with ways of slowing it that can improve selectivity. Nothing conclusive yet though.
Quote: | Would it be possible to use the Aluminium and Galinstan as it is, for reduction reactions (in-situ)? What I mean is without melting Al or fusing Al
before you gone do the actual reduction reactions. Its should still be liquid beneed room temperature. And therefore I suppose it still will attack
the aluminium in the MeOH, I dont know if i'm right
|
Both aluminum and galinstan form oxide layers, and it's not that easy to get them to mix. Nearly impossible when they're wet. The easiest way is to
put a drop of galinstan on solid, dry aluminum, then scratch at the aluminum through the drop. Eventually, you'll see black streaks in the aluminum,
indicating that an alloy is forming. After this happens for a while, it can be carefully added to a solution, if you try to make sure to keep the
mass intact.
This works especially well with Chilean one-peso aluminum coins, which are worth about a fifth of a cent. I wish I knew where I could get more, but
they're rare even in Chile, since they're worth so little.
Quote: | Thought experiment that I thinking about :
In a three-neck round bottom flask fixed with a condenser I put 27.5g aluminium (99.995%) granules (2 - 3mm), 750 mL of lab grade MeOH. In a a
dropping funnel I mix 25g of ketone, 20g of nitromethane with 25 mL of MeOH. Now I drop the Galinstan in the round bottom flask. And wait until the
reaction starts. Then open the valve of the dropping funnel as it would be empty in about 40 - 45 min.
Will this work, do nothing or take longer than 45 min for all the aluminium to be comsunt by the Galinstan? I'm thinking this way because I think the
Al/Galinstan reduction reaction is to vigorous and would result in a short reaction time and temperatures above 50°C. It's very important that it
goes for 40 - 45 min, without exceeding 50°C.
|
You can slow the reaction by using as little water as possible initially, then adding water dropwise to speed it up. Also, ethanol is the best
solvent for this reaction, hands down. Isopropanol is okay, on second thought, and the isopropoxide reaction hasn't proven to be a real problem, only
a theoretical one.
I have developed an alternate method, that I was waiting until I has pictures and yields to post, but I'll give you the brief version. The idea was
to develop a procedure as close to a typical Al/Hg as possible, for an accurate comparison of yields. Anyway:
Heat water with aluminum foil pieces in it to 50-60˚C. Thicker foil is better, the stuff that disposable serving trays are made of works quite well.
While stirring it well, add a solution of three parts* of gallium chloride. Continue stirring for about five minutes, allowing it to cool.** Add
one part indium chloride solution, dropwise, with continued stirring. There should be few if any bubbles visible during the InCl3 addition. If you
see the reaction rate increase visibly, stop the addition, pour off the water and replace it with alcohol. Continue to stir for 2-3 minutes. Add
stannous chloride dropwise, until a reaction becomes obvious. If the water has been replaced with alcohol, add everything to the main reaction flask,
otherwise pour off the water, rinse with alcohol, then add to the main reaction flask. Heat the reaction with stirring, until the substrate has all
reacted, then do the workup the same as you would Al/Hg, though any Hg precautions are obviously not necessary.
* Parts by mass of the metal. The ideal ratio of gallium to indium is 3:1, but the optimal ratio to aluminum is far less obvious.
** Don't heat the water with your stirring hotplate. Heat it over a flame or something, then stir it on a cool hotplate [sic].
The first step in the process of learning something is admitting that you don't know it already.
I'm givin' the spam shields max power at full warp, but they just dinna have the power! We're gonna have to evacuate to new forum software!
|
|
stoichiometric_steve
National Hazard
  
Posts: 827
Registered: 14-12-2005
Member Is Offline
Mood: satyric
|
|
Have you ever come around to that?
Quote: Originally posted by Melgar  |
While stirring it well, add a solution of three parts* of gallium chloride.
* Parts by mass of the metal. The ideal ratio of gallium to indium is 3:1, but the optimal ratio to aluminum is far less obvious.
|
So what are the optimal ratios of Al, Ga, In and Sn used per mole of substrate?
|
|
fusso
International Hazard
   
Posts: 1922
Registered: 23-6-2017
Location: 4 ∥ universes ahead of you
Member Is Offline
|
|
Quote: Originally posted by Melgar  | This works especially well with Chilean one-peso aluminum coins, which are worth about a fifth of a cent. I wish I knew where I could get more, but
they're rare even in Chile, since they're worth so little. | What's the melt value of 1 chile peso coins?
You can also use 1 JPY coins. They're very common in japan. They worth ~1 US cent each.
|
|
arkoma
Redneck Overlord
     
Posts: 1763
Registered: 3-2-2014
Location: On a Big Blue Marble hurtling through space
Member Is Offline
Mood: украї́нська
|
|
I love this place.........great work Melgar, and within my reach.
"We believe the knowledge and cultural heritage of mankind should be accessible to all people around the world, regardless of their wealth, social
status, nationality, citizenship, etc" z-lib
|
|
Melgar
Anti-Spam Agent
   
Posts: 2004
Registered: 23-2-2010
Location: Connecticut
Member Is Offline
Mood: Estrified
|
|
I initially hoped that this alloy could be used for organic reductions, but am now resigned to the reality that there are far too many uncontrollable
variables for that to happen. One factor that I hadn't anticipated is how many suppliers simply make up the metal content of the alloys they're
selling, or change the alloys they use in their products on a frequent basis. Magnesium in the aluminum alloy can greatly accelerate the reaction
rate, and also reduce its selectivity.
Thanks for reminding me to update this. I never had conclusive enough results to add anything new though. I did research theory some more though,
and realized that mercury not only exposes aluminum metal to the solution, but it is responsible for a much larger change in hydrogen overvoltage than
I would expect from galinstan. So this cannot substitute for Al/Hg for as many reactions as I anticipated it could. However, it's still important to
publish negative results, and so here they are.
That being said, this alloy is still quite useful as an activated form of aluminum. It can be added to alcohols to form aluminum alkoxides, or added
to a nonpolar solvent with elemental iodine to form aluminum triiodide. It reacts much more readily with alkyl halides than unalloyed aluminum. It
also can evolve hydrogen at a neutral pH, for a prolonged period of time, and without generating any toxic products. And it can perform plenty of
very simple reductions. For instance, adding it to DMSO is an easy way to generate dimethyl sulfide. And I'm sure it has plenty of other uses as an
easily-obtained alloy that will react vigorously with water at a neutral pH. But at the present, results are too difficult to reproduce to recommend
its use as a replacement for Al/Hg.
The first step in the process of learning something is admitting that you don't know it already.
I'm givin' the spam shields max power at full warp, but they just dinna have the power! We're gonna have to evacuate to new forum software!
|
|
Tdep
National Hazard
  
Posts: 519
Registered: 31-1-2013
Location: Laser broken since Feb 2020 lol
Member Is Offline
Mood: PhD is done! It isn't good but it's over lol
|
|
Hey, this thread and general idea of Ga/Al reduction I think deserves an attempt to be published. I can't find anything in the literature about it,
and it could do well if it had a 'green' chemistry spin to it.
It doesn't have to be a world changing reduction agent to be published. If there's some interesting results from low levels of magnesium, that's good
data.
The exact aluminium alloy used in a reduction isn't something that people think about (I believe), and if you show that it makes a difference, that's
a neat paper.
Chose a reduction that runs easily and gives an easily measurable outcome. Then, vary the alloy and observe the change in results. There probably
needs to be some sort of elemental analysis on the alloys (just throw some money at a company that can do that) and then hey, outcomes.
"The influence of Magnesium on the Replacement of Hg/Al Reductions with Ga/Al"
(i'm sitting in my office bored with my own research lol)
|
|
ChemistryGhost
Hazard to Others
 
Posts: 113
Registered: 5-7-2012
Member Is Offline
Mood: Supercooled
|
|
Can the aluminum galinstan amalgam be used to reduce phenylbutanone and ammonia to form an amine?
"Imagination is more important than knowledge" ~Einstein
|
|
karlos³
International Hazard
   
Posts: 1520
Registered: 10-1-2011
Location: yes!
Member Is Offline
Mood: oxazolidinic 8)
|
|
If it works, what I doubt, it will give a very low yield at most.
Ammonia forms imines very badly.
But there is an alternative reaction, which works probably the best for the preparation of primary amines from ketones.
I tried it too.
Read here: http://www.sciencemadness.org/talk/viewthread.php?tid=20153
|
|
ChemistryGhost
Hazard to Others
 
Posts: 113
Registered: 5-7-2012
Member Is Offline
Mood: Supercooled
|
|
I think that using ammonium acetate instead of ammonia will increase yield. What I like about the idea of aluminum galinstan is that it doesn't use
toxic mercury.
"Imagination is more important than knowledge" ~Einstein
|
|
karlos³
International Hazard
   
Posts: 1520
Registered: 10-1-2011
Location: yes!
Member Is Offline
Mood: oxazolidinic 8)
|
|
If you refer to the LabTop writeups regarding the ammonium acetate, I tried that with L-PAC and no, it does not increase yield.
Only with cyanoborohydride this is true, but it will not work with Al/Hg or Al/Ga, and with NaBH4 it gave the same shitty outcome as alcoholic ammonia
would give.
Well, then check the nickel-zinc reductive amination regarding toxicity.
Nickel is not harmless though, but it plays in the amateur league opposed to the profi league where mercury is seated in, of course.
You might like this method even better, because I can confirm(and I heard from others that they could reproduce it) that this reduction system
resulted in high yields for them as well as it did for me.
|
|
ChemistryGhost
Hazard to Others
 
Posts: 113
Registered: 5-7-2012
Member Is Offline
Mood: Supercooled
|
|
Cool.
"Imagination is more important than knowledge" ~Einstein
|
|
ChemistryGhost
Hazard to Others
 
Posts: 113
Registered: 5-7-2012
Member Is Offline
Mood: Supercooled
|
|
Can aluminum galinstan be used to reduce Phenyl-2-Butanone and ethylamine to N,α-Diethylphenylethylamine? Since it's an ethyl group and not ammonia,
yields should be higher.
"Imagination is more important than knowledge" ~Einstein
|
|
Fluorite
Hazard to Others
 
Posts: 139
Registered: 26-12-2018
Location: United Arab Emirates
Member Is Offline
|
|
is this alloy useful for dehydrating alcohols? instead of using magnesium?
|
|
|