Pages:
1
2 |
crazyboy
Hazard to Others
 
Posts: 436
Registered: 31-1-2008
Member Is Offline
Mood: Marginally insane
|
|
Pyrolysis of plastic for fuel
I saw a video where plastics were distilled in an oxygen free environment to make a flammable liquid which was claimed to be diesel like. Here it is:
https://www.youtube.com/watch?v=4G34HQQqHRw
This got me interested, I have heard of polystyrene pyrolyis to produce styrene, would any other plastic make medium chain alkanes? Here's a very long
thread on the subject which I haven't read all the way: http://www.energeticforum.com/renewable-energy/7040-how-turn... he claims 17 cents a liter which seems too low to me.
http://www.sciencemadness.org/talk/viewthread.php?tid=24683#... This thread touched on the subject but most of the discussion centered around PVC
for some reason. I'm more interested in polyethylene as various forms are very common in commercial and residential waste streams.
I've attached two PDFs of interest, one shows that pyrolysis products from "assorted plastics" yielded a product comparable to diesel and ran in an
unmodified engine. Unfortunately an unspecified catalyst was used and the plastic composition is a mystery. The other paper shows medium chain
parafins were produced by thermal decomposition of HDPE without catalyst.
What do you guys think? I'm not in a position to start distilling lots of waste plastic but you could imagine if you could run the product in an
unmodified diesel engine you could get lots of waste plastic for free and if you had solar or wind on your property use that to distill the plastic
and potentially generate your own fuel or store your energy in liquid form.
Attachment: Pyrolysis of HDPE in a diesel engine.pdf (777kB) This file has been downloaded 1161 times
Attachment: Pyrolysis of polyethylene.pdf (2.6MB) This file has been downloaded 1389 times
|
|
j_sum1
Administrator
      
Posts: 6320
Registered: 4-10-2014
Location: At home
Member Is Offline
Mood: Most of the ducks are in a row
|
|
I think it is something that should be done more often. There is so much energy locked up in waste plastic, to throw it away is nearly criminal and
that s before we start talking about the environmental detriments of said plastics.
As for the specifics of your question, I believe the issue that comes up most often with repurposing plastic products is the huge mixture of chemicals
that arise both from the main polymer and also from additives and contaminants. This complexifies any processes and leads to a lot of unknowns in
your product stream. In the case of diesel fuel, you really want some assurance that your product is going to be non-polluting as a fuel. (Or at
least no worse than diesel already is.) That is a difficult thing to guarantee.
On the other hand, if you devise/adapt a method that is practical then you are onto a sure winner here.
|
|
phlogiston
International Hazard
   
Posts: 1379
Registered: 26-4-2008
Location: Neon Thorium Erbium Lanthanum Neodymium Sulphur
Member Is Offline
Mood: pyrophoric
|
|
Isn't plastic waste already being incinerated and the heat commonly used for electricity production?
If your goal is environmental, you should also consider the gasses and soot vented during pyrolysis and the possible additional emissions from the car
running on this fuel.
It seems likely to me that thorough incineration in a plant built fot that purpose and of which the emmissions are properly monitored will perform
better overall.
-----
"If a rocket goes up, who cares where it comes down, that's not my concern said Wernher von Braun" - Tom Lehrer
|
|
froot
Hazard to Others
 
Posts: 347
Registered: 23-10-2003
Location: South Africa
Member Is Offline
Mood: refluxed
|
|
De-polymerising plastic is your goal and pyrolysis is one way to do it although it is energy intensive and your product will be random. It 'boils'
down to how much energy you throw at the process vs the energy in your product before you even start considering the quality of your product.
Find an efficient way to crack a polyethylene chain for example at predetermined points of the polymer to either produce fuel or recycled feedstock to
the plastic industry and you'll be on the road to riches.
We salute the improvement of the human genome by honoring those who remove themselves from it.
Of necessity, this honor is generally bestowed posthumously. - www.darwinawards.com
|
|
blogfast25
International Hazard
   
Posts: 10562
Registered: 3-2-2008
Location: Neverland
Member Is Offline
Mood: No Mood
|
|
I must say I'm amazed at the degree of depolymerisation obtained in 4 h @ 350 C and w/o any catalyst used at all.
The energy cost works out at about 8 pence/kg of product, very roughly:
1 kWh = £0.10
6 kW x 4 h = 24 kWh = £2.4 for 30 kg (single reactor pass end-product)
So 8 p/kg (twice that for a two pass product, obviously)
Factor in some 'economy of scale' for much larger depolymerisers, residual heat recovery from the hot, finished product and a decent but cheap
catalyst and the possibilities seem endless.
Something just sounds too good to be true but ra ra, what is it? 
And of course it's a fossil fuel 'in disguise'...
[Edited on 12-6-2015 by blogfast25]
|
|
Dr.Bob
International Hazard
   
Posts: 2733
Registered: 26-1-2011
Location: USA - NC
Member Is Offline
Mood: No Mood
|
|
For plastics that are not easily recyclable, it would make more sense to me to just have more municipal incinerators with heat recovery electric
generators and scrubbers, and burn all of the non-recyclable trash. Burying it is stupid, and burning it will provide ash that is high is some
minerals, so it might even be profitable to use it as feedstock one day. But Pyrolysis could generate some power, I have seen an actual pilot plant
system for this, but it is not nearly as easy or profitable as claimed. The energy input is large to start and then tapers off if you have good
energy recovery systems, but the output is far less that expected, as there is a large amount of moisture in most trash streams, and the system has to
remove that as steam, which removes a lot of energy from the system. My understanding is that for every 2000 pounds of trash/waste, it can generate
about 50 gallons of crude fuel, which is not good enough for running an engine without further purification and other treatments (hydrotreating?) to
get the fuel either more like diesel or gasoline, as both have tight specs. But the system cost over a million to build (government grant pricing,
however), and can only produce a 100 gallons per day right now. So you would need to get the capital price down a lot and the throughput up to make
it practical. Plus even for garbage, you need someone to haul it to you, a place to store it, and about 100 government permits to operate the
system.
|
|
crazyboy
Hazard to Others
 
Posts: 436
Registered: 31-1-2008
Member Is Offline
Mood: Marginally insane
|
|
Quote: Originally posted by froot  | De-polymerising plastic is your goal and pyrolysis is one way to do it although it is energy intensive and your product will be random. It 'boils'
down to how much energy you throw at the process vs the energy in your product before you even start considering the quality of your product.
Find an efficient way to crack a polyethylene chain for example at predetermined points of the polymer to either produce fuel or recycled feedstock to
the plastic industry and you'll be on the road to riches. |
Thermal decomposition isn't very energy intensive, as shown by the guy who was able to produce the hydrocarbon mix for 17 cents per liter. Why would
you need to crack it at a predetermined point? Diesel is a mix of various chain lengths and thermal decomp results in mostly C9-C20 chains which is
basically what diesel is.
Quote: |
My understanding is that for every 2000 pounds of trash/waste, it can generate about 50 gallons of crude fuel, which is not good enough for running an
engine without further purification and other treatments
|
50 gallons per 2000 pounds translates to 0.2 liters per kilogram. The guy from the energetics forum claimed he was getting 1L/kilo. The first paper I
posted indicates that the products are effectively a drop in replacement for diesel. Additionally on the second page of that forum post the guy says
he bought 1 ton of shredded plastic from a recycling place for $50. 2000Lbs is about 900Kg if he gets about 1L/Kg that's 900L of fuel or 230 gallons.
Might not be right for the guy living in suburbia but could be very appealing to someone living off the grid, gas or diesel doesn't have an infinite
shelf life, only a a year or two if I recall. Plastic does and if you could buy it at $50 a ton you could store it in a silo and generate diesel for
your truck or generator from solar as you go. The only issue I see is the potential environmental cost, but if you can dispose of the ash safely than
its really no worse than buying diesel from the gas station.
[Edited on 13-6-2015 by crazyboy]
|
|
phlogiston
International Hazard
   
Posts: 1379
Registered: 26-4-2008
Location: Neon Thorium Erbium Lanthanum Neodymium Sulphur
Member Is Offline
Mood: pyrophoric
|
|
The main problem with long term storage of gas and diesel is that the most volatile components evaporate. If you can obtain a sufficiently well sealed
container, it should be possible to store it pretty much indefinitely.
-----
"If a rocket goes up, who cares where it comes down, that's not my concern said Wernher von Braun" - Tom Lehrer
|
|
blogfast25
International Hazard
   
Posts: 10562
Registered: 3-2-2008
Location: Neverland
Member Is Offline
Mood: No Mood
|
|
Quote: Originally posted by crazyboy  |
50 gallons per 2000 pounds translates to 0.2 liters per kilogram. The guy from the energetics forum claimed he was getting 1L/kilo. The first paper I
posted indicates that the products are effectively a drop in replacement for diesel. Additionally on the second page of that forum post the guy says
he bought 1 ton of shredded plastic from a recycling place for $50. 2000Lbs is about 900Kg if he gets about 1L/Kg that's 900L of fuel or 230 gallons.
|
The 1 L/kg number is of course much closer to the 0.2 one. What goes in must come out and at 0.2 L/kg that would require a very high (and unrealistic)
degree of depolymerisation to 80 % gases (C < 4, basically).
I think if you're going to put depolymerised plastic into your car tank, you'll have to pay tax on it, which is a great disincentive for most people.
Use as home-heating diesel?
|
|
Dr.Bob
International Hazard
   
Posts: 2733
Registered: 26-1-2011
Location: USA - NC
Member Is Offline
Mood: No Mood
|
|
The number I posted was for a mixed trash system, so likely much less usable material, plus water, glass, etc, thus the low recovery. But since most
plastic is much less then 1 kg/1L in density, I think it would be very hard to generate any real recovery near 1 kg/ L, as the mix of material
recovered will include gases, liquid and ash, so the usable fuel would be more likely to be about 500 g per 1L at best in the real world.
You can put nearly any fuel in your vehicle, but if you burn anything that is not ASTM certified (what you buy at the gas station) then your engine
warranty is voided. And many fuels from pyrolysis could contain things that might not be ideal for an engine. Just like you can burn straight
veggie oil in a diesel engine, but it will ash up quickly and be destroyed eventually. But burning quality biodiesel at 5-85% in regular diesel will
not damage most diesels. Don't believe everything people claim on the internet or even in papers. I don't think the author of a paper will warranty
your engine...
And while most alternative fuels are taxed when sold, and the law requires it, you could likely add a little alternative fuel to your tank every so
often and not get caught. I have known several people to add waste MTBE, iso-octane, benzene, toluene, methanol, ethanol, etc to their gas tank in
small amounts, and it is fine if done in small amounts. Just don't use n-alkanes such as n-octane or n-hexane, as that will lower your octane rating
badly and kill your engine.
|
|
Cloner
Hazard to Others
 
Posts: 150
Registered: 7-12-2004
Member Is Offline
Mood: apocalyptic
|
|
I heated some waste PE in a test tube over an oxidizing bunsen flame, for 5 minutes. About 20% of low MW combustible gases evolved.
The residue is a brittle wax which smells of hydrocarbon. Clearly, oligomers have formed.
In a separate experiment, petroleum was heated to a low reflux onto small amount of iron sponge (also heated with oxidizing bunsen flame)in a test
tube. There is a continuous evolution of alkenes, but this is a very slow process. The wax from the earlier experiment does not generate appreciable
amounts of alkene in this setup, because of it not refluxing.
|
|
aga
Forum Drunkard
   
Posts: 7030
Registered: 25-3-2014
Member Is Offline
|
|
When i tried PVC pyrolysis, 260C was when the action happened (decomposition gasses started coming out).
|
|
kecskesajt
Hazard to Others
 
Posts: 299
Registered: 7-12-2014
Location: Hungary
Member Is Offline
Mood: No Mood
|
|
Quote: Originally posted by Cloner  | I heated some waste PE in a test tube over an oxidizing bunsen flame, for 5 minutes. About 20% of low MW combustible gases evolved.
The residue is a brittle wax which smells of hydrocarbon. Clearly, oligomers have formed.
In a separate experiment, petroleum was heated to a low reflux onto small amount of iron sponge (also heated with oxidizing bunsen flame)in a test
tube. There is a continuous evolution of alkenes, but this is a very slow process. The wax from the earlier experiment does not generate appreciable
amounts of alkene in this setup, because of it not refluxing. |
Look at this video.The person is using clay pot pieces.It might be faster
http://youtube.com/watch?v=7M7RY04KKBs
|
|
blogfast25
International Hazard
   
Posts: 10562
Registered: 3-2-2008
Location: Neverland
Member Is Offline
Mood: No Mood
|
|
Quote: Originally posted by aga  | When i tried PVC pyrolysis, 260C was when the action happened (decomposition gasses started coming out). |
I really think you should continue those experiments, using test tubes ('boiling tubes') and a more 'quantitative' set up. A Bunsen should provide
ample heat to get to a high degree of depolymerisation. A train of simple wash bottles/condensers culminating in a simple gazometer should provide
ample useful information re. HCl generated and gaseous and liquifiable decomposition products.
|
|
blogfast25
International Hazard
   
Posts: 10562
Registered: 3-2-2008
Location: Neverland
Member Is Offline
Mood: No Mood
|
|
Nice find.
Tip for future experimenters: wrapping ordinary (NR or SBR based) rubber stoppers in teflon tape ('gas tape') can protect them quite adequately from
high heat/corrosive gases (HCl e.g., in the case of halogenated polymers)
|
|
kecskesajt
Hazard to Others
 
Posts: 299
Registered: 7-12-2014
Location: Hungary
Member Is Offline
Mood: No Mood
|
|
Wow my father have a dozen of PTFE tape.And OMG,Im burned some tape inside the house :O.I noticed how shitty smell it has.
|
|
xfusion44
Hazard to Others
 
Posts: 223
Registered: 6-8-2014
Location: Europe
Member Is Offline
Mood: Nostalgic
|
|
I thought it'd be helpful if I'd post some pictures of my plastic pyrolysis apparatus design for those of you, who are just starting with pyrolysis of
plastic 
Remove the threaded plastic piece:
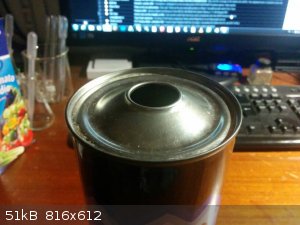
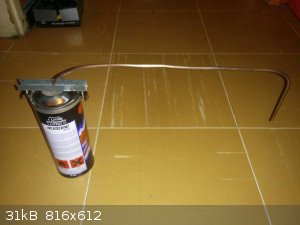
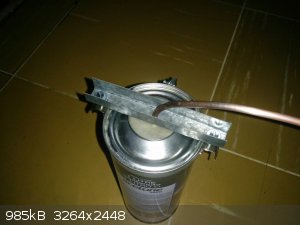
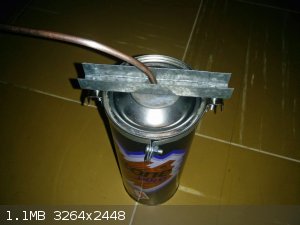
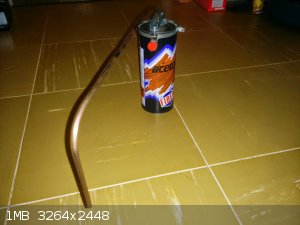
On the end of copper tube where it's attached, there is round piece of copper sheet soldered on and gaps are sealed by PTFE tape.
End product:
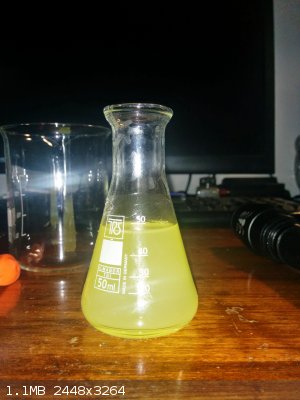
Not all plastic was consumed in making those 50 ml's of product, it was just a test run.
PS: procedure: throw pieces of plastic into the can, close it and place bunsen burner underneath it, dip the end of the tube into beaker/container
with cold water and wait for your product to collect on the water's surface. (hot plate can't be used, since it can't reach plastic's boiling point),
also you may need to replace or let water cool down every once in a while, since it heats up due to hot plastic pyrolyis product that condenses in it
which may result in boiling water splattering your product all over the place and/or loss of product due to insufficient cooling and excessive
evaporation.
BR, xfusion
[Edited on 25-6-2015 by xfusion44]
[Edited on 25-6-2015 by xfusion44]
|
|
blogfast25
International Hazard
   
Posts: 10562
Registered: 3-2-2008
Location: Neverland
Member Is Offline
Mood: No Mood
|
|
Be careful heating cans that aren't designed for that, with flammable liquids forming inside!  
Also, create a little copper coil and run it through running water, to act as a more efficient condenser.
An anti-suckback valve is also to be recommended, to avoid violent steam explosions in case of suck back.
A mass balance would also have made it more scientific: how much plastic did you start from, how much residue did you end up with and how much liquid
product?
[Edited on 25-6-2015 by blogfast25]
|
|
xfusion44
Hazard to Others
 
Posts: 223
Registered: 6-8-2014
Location: Europe
Member Is Offline
Mood: Nostalgic
|
|
Quote: Originally posted by blogfast25  | Be careful heating cans that aren't designed for that, with flammable liquids forming inside!  
Also, create a little copper coil and run it through running water, to act as a more efficient condenser.
An anti-suckback valve is also to be recommended, to avoid violent steam explosions in case of suck back.
A mass balance would also have made it more scientific: how much plastic did you start from, how much residue did you end up with and how much liquid
product?
[Edited on 25-6-2015 by blogfast25] |
Product is not very flammable, don't worry It's not even so easy to ignite it
directly with lighter.
I tried to avoid suck back with removing tube from water before turning off the flame, but it did happen to me, when I ran out of gas It wasn't so violent as the mass of plastic inside is not big and also walls of the
can are thin, so they can cool down really fast. (I don't even remember steam coming from the tube) But yeah, valve would be recommended (in this case
implosion could happen).
I thought about the coil running through water, but I didn't have enough pipe. If I'd do it this way, I could even avoid using suck back valve.
I know it would be a lot better to write down how much plastic I've used and how much product I've got, but at the time I was just wondering if this
would make a good fuel and unfortunately I didn't weigh the plastic, but I'd say that about 1g of plastic is enough to make 1ml of product, so maybe
about 50 grams for the quantity on picture (just my guess). Somewhere I also saw, that 1kg of plastic is enough to make 1l of fuel, so that would be
possible I think. Depends on the type of plastic too, I'd say.
Thanks for all of the safety tips 
xfusion
|
|
aga
Forum Drunkard
   
Posts: 7030
Registered: 25-3-2014
Member Is Offline
|
|
Did you use all one type of plastic or a mixture ?
This may help identification :-
http://www.garrison.hawaii.army.mil/sustainability/images/Pl...
|
|
blogfast25
International Hazard
   
Posts: 10562
Registered: 3-2-2008
Location: Neverland
Member Is Offline
Mood: No Mood
|
|
Incidentally, polyprop should be slightly easier to depolymerise (than PE) due to the tertiary carbon in its structure.
|
|
Dr.Bob
International Hazard
   
Posts: 2733
Registered: 26-1-2011
Location: USA - NC
Member Is Offline
Mood: No Mood
|
|
Yes, knowing the plastic used is key, as each plastic is likely to provide a different liquid upon heating, some of which would be better then others
for fuel. For example, Acrylic is easy to depolymerize into methyl methacrylate, but if you put it into your gas tank, it would eventually
re-polyumerize, and that might not be good for your fuel pump. I would think that polystyrene would be practical, but again, styene can polymerize,
so in practice, most industrial pyrolysis systems hydrogenate the fuel to remove unsaturated bonds, as they can be problems if activated towards
polymerization. Unsaturated bonds do tend to make the fuel more liquid that the equivalent saturated hydrocarbon (lower MP), which can be useful for
diesels to prevent gelling (freezing) in the winter.
|
|
aga
Forum Drunkard
   
Posts: 7030
Registered: 25-3-2014
Member Is Offline
|
|
PVC goes to loads of HCl and foul smelling carbon.
Tried that with a few 100g PVC.
|
|
xfusion44
Hazard to Others
 
Posts: 223
Registered: 6-8-2014
Location: Europe
Member Is Offline
Mood: Nostalgic
|
|
At first I wanted to use one type... But then I ended up with mixture (mostly PS and PE). I think I'll try with only one type when I'll have some time
too, because I'm interested to see different colors, flammabilities and other properties when using certain plastic 
xfusion
|
|
aga
Forum Drunkard
   
Posts: 7030
Registered: 25-3-2014
Member Is Offline
|
|
dear xfusion44.
I love your enthusiasm to try stuff out, and applaud your making of a Pyrolysis rig out of scrap stuff, and especially for Doing It.
It is Wonderful, Exciting, Fun and really Good to see Stuff happen.
It isn't Science though is it ?
'Science' is your Next Step, where you present Evidence, and not just What You Did.
Get only 1 kind of Plastic, weigh it as best you can.
(ebay: 0.01g scales are dirt cheap)
Pyrolyse it, and measure, and write down everything you can : temperature(s), time, what you see, what you smell - everything !
e.g. weigh the water & collection vessel before & after. The difference is how much stuff you got. If you see smokey stuff coming out of the
collection vessel, note the time, temperature and what it looks like, what colour it is.
Do it like that and many people here can analyse and work out stuff from what You Did that neither you nor i could dream of (yet).
[Edited on 26-6-2015 by aga]
|
|
Pages:
1
2 |