Fery
International Hazard
   
Posts: 1026
Registered: 27-8-2019
Location: Czechoslovakia
Member Is Offline
|
|
Azelaic acid
Azelaic acid is used in medicine to treat mild to moderate acne and rosacea. A burning feeling is induced after its application, no wonder, it is a
diprotic acid with pKa1=4,55 pKa2=5,50 (pKa1 is slightly stronger than acetic acid).
It also inhibits synthesis of melanin (competitive inhibitor of tyrosinase) in hyperactive melanocytes so it is used in treatment of
hyperpigmentations.
It is used in polyamides synthesis (PA69, PA109, PA129).
Put 101 g of castor oil, 13 g of NaOH, 100 ml of 90 % isopropanol (azeotrope of isopropanol with water) into 500 ml flask and reflux for 3 hours.
(Perhaps 1 hour would be sufficient?)
Some Na ricinoleate stays undissolved. Do not allow it to cool down as more of it solidifies. While still hot, detach reflux condenser and add 200 ml
of hot water (80 C), stirr and heat until it dissolves. Do not add boiling water as it could boil out isopropanol vigorously (water/isopropanol
azeotrope b.p. 80 C). Transfer into 1000 ml flask or beaker and wash the reflux flask with extra 200 ml of hot water and put it into 1000 ml flask
together. Then you are finally allowed to cool it down and the soap stays dissolved. Ricinoleate soap is more soluble than other soaps thanks to -OH
in the middle of molecule.
Add 75 ml of 37% H2SO4 (Pb accumulator acid concentration) and mix thoroughly to release free acid from the soap, free ricinoleic acid separates as
upper layer. The final pH of bottom layer must about 2 - acidic to Congo red or methyl orange (Litmus paper could turn red due to acidity of fat
acids).
Wash the product twice with 300 ml of warm water in separatory funnel (especially removing isopropanol and glycerol is necessary for oxidation of the
acid in the following step).
There is no need to dry out the ricinoleic acid, it could be used as it is in crude form for the next steps. It is apt to polymerize but leaving it to stay overnight does not hurt and tomorrow is another day (a lot of work is still pending).
Yield 96 g (very likely due content of small amount of water).
Oxidation is performed in few batches. Rather do not try it at once (just my suggestion).
Put 50 ml of water into 1000 ml flask, add 2 g of NaOH, dissolve, add 12 g of ricinoleic acid, dissolve by slightly warming.
Dissolve 32 g of KMnO4 in 350 ml of warm water (35 C) in 1000 ml beaker, remember it does not dissolve completely at 20 C.
Add the KMnO4 solution into the flask in about 10 portions during 15 minutes with vigorous stirring. The reaction is exothermic, keep the temperature
at most 75 C. I warn you again: do not add KMnO4 faster, do not add it in big portions, stir the mixture vigorously. The mixture contains a soap and
guess what happens if it reaches boiling point or if the KMnO4 decomposes rapidly at high temperature and releases O2. I suggest you also to have a 10
l bucket at hand - if some foam starts to escape the flask put it quickly into the bucket not to spoil your desk. Also have 1 g of oxalic acid
dissolved in 10 ml of water at hand to destroy droplets of KMnO4 solution or MnO2 also.
Filter out the MnO2 and wash it twice on filter with water (both times approx the same volume of water as the volume of wet MnO2) and add the washings
into the filtrate together.
Acidify the filtrate with 37% H2SO4 to methylorange (pH below 3, better is 2) very slowly by adding in 1 ml portions while mild stirring. Slow
evolution of very small bubbles of CO2 happens during addition of the first half of H2SO4 and it brings oily wastes to the surface (pKa of long chain
monocarboxylic acids is higher so they are released from their salts first while azelaic acid salts still stay as 2- or at least 1- anions soluble in
water). After adding all H2SO4 a formation of azelaic acid crystals and settling down is already visible if the solution is not too warm. Put into
fridge to cool to 4 C overnight.
Remove floating semisolid layer and discard it (31,5 g perhaps polymerized ricinoleic acid, palmitic acid, 3-keto-nonanoic acid).
Filter crystals of crude azelaic acid. Put crystals into 1 l flask with 600 ml of water, attach condenser and steam distill out monocarboxylic acids -
at the beginning the distillate is an emulsion - perhaps 3-keto-nonanoic and heptanoic acids? After collecting about 100 ml of distillate it the
distillate is already clear water so monocarboxylic acids removed and then stop distilling, transfer still hot solution from the flask into a beaker,
cool down to allow to crystallize product and put into fridge to 4 C to crystallize more.
Recrystallize from 250 ml of water (dissolve in boiling water, filter quickly, cool down to 4 C). The solubility of azelaic acid at 4 C is very low so
don't be afraid of washing crystals with ice cold water on filter thoroughly.
m.p. 105-106 C which is very good
Melting point/freezing point 106,5 C
Yield 7,4 g (C9H16O4 0,039 mol) from 6 batches of 12 g ricinoleic acid (from total 72 g of ricinoleic acid = 0,24 mol) 16% quite poor. Perhaps boiling
down the filtrate and washings from MnO2 could help to increase the yield but very likely it wouldn't help too much as solubility of azelaic acid in
cold water is quite low? Also do not boil down so much that K2SO4, Na2SO4 crystallize. Boiling the MnO2 suspension would coagulate particles but when
it is alkalic the unreacted soap foams a lot (palmitate ?) - I tried that. So everyone acidifies first, then boils to coagulate without risk of
foaming - but filtering cold MnO2 is easier than hot and after acidification the solution must stay hot otherwise azelaic acid precipitates. Also MnO2
from alkalic solution is quite pure and could be recovered easily. Perhaps some azelaic acid stayed dissolved in the upper semisolid waste layer from
which it could be extracted by hot water?
I recovered 1,4 g of impure azelaic acid by boiling down water from 2 recrystallizations from about 1 liter to 50 ml and crystallizing on cooling
down.
Additional helpful info and my thoughts:
https://en.wikipedia.org/wiki/Oxidation_of_primary_alcohols_...
KMnO4 is decomposed in water, resulting in formation of manganese dioxide (MnO2) and gaseous oxygen. This decomposition is catalyzed by acid, base and
MnO2. As the extent of this decomposition is difficult to estimate during the oxidation of primary alcohols, the quantity of KMnO4 must be adjusted
during the oxidation by adding it sequentially until the oxidation is complete.
I've choosen IPA because when some amount stays dissolved in ricinoleic acid it consumes less KMnO4 than ethanol. But IPA could be better soluble in
ricinoleic acid than ethanol so harder to wash it out?
Everyone uses KOH+ethanol for saponification as K soaps are better soluble. I wanted to try whether it could be done with NaOH instead.
Solubility of azelaic acid in water 2,1 g/l 20 C, 22 g/l 50 C.
Use 1 g of oxalic acid in 10 ml of water to clean glass from brown spots of MnO2.
Saponification and Purification of Free Fatty Acids here.
Manuals also use ethanol instead of isopropanol as KOH is soluble in ethanol. No problemo.
Do not use smaller dish than 1000 ml for the oxidation at the above scale (12 g of ricinoleic acid) - using smaller flask leads into foaming out,
using smaller beaker you risk spoiling droplets of KMnO4 solution.
It is suggested to boil the mixture to coagulate MnO2 (easier filtration) but never boil mixture containing soap!!!
Direct oxidation of castor oil with water solution of KMnO4 is not good idea as glycerol would consume some KMnO4 so oxidation of ricinoleic acid is
better and the best is ricinoleate soap which is dissolved in water.
|
|
Fery
International Hazard
   
Posts: 1026
Registered: 27-8-2019
Location: Czechoslovakia
Member Is Offline
|
|
saponification (it should not be heated by direct flame, but I did it for taking better photo)
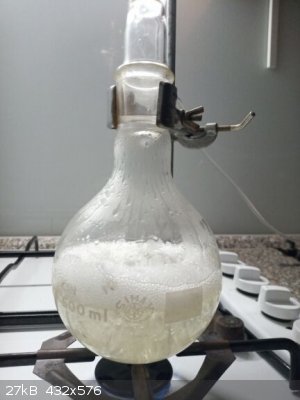
some Na ricinoleate stays undissolved
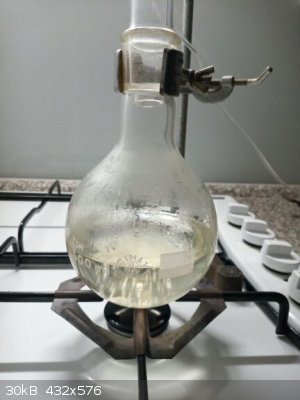
diluted soap solution before adding H2SO4
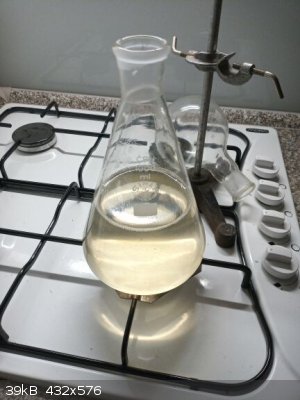
after acidifying
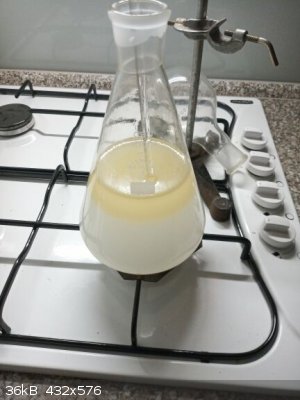
crude ricinoleic acid
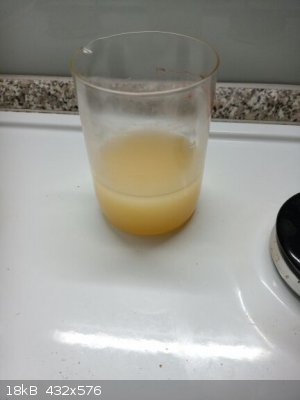
before oxidation (i batch of 12 g of ricinoleic acid)
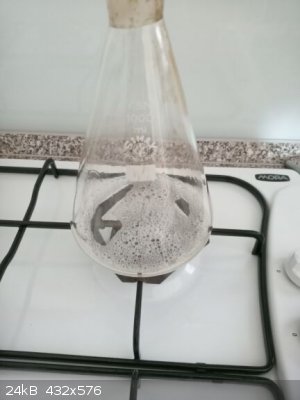
performing oxidation (must be stirred, this is only for taking a photo)
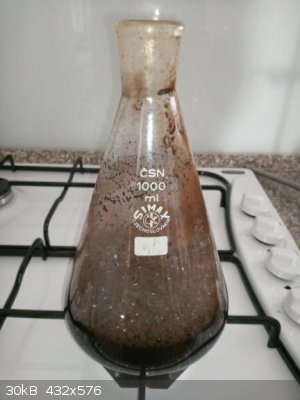
after removing impurities by steam and allowing to cool down (6 batches collected together = from 72 g of ricinoleic acid total)
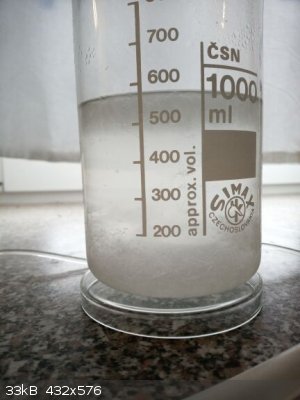
31,5 g of semisolid waste removed floating at surface (from 72 g of ricinoleic acid)
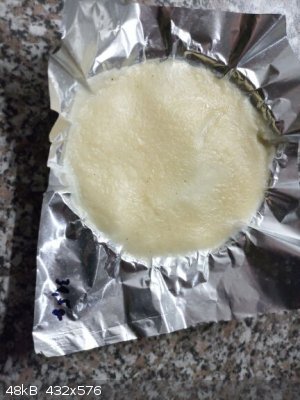
7,4 g of azelaic acid after last recrystallization and drying out from 72 g of ricinoleic acid, yield 16%, quite poor, huh?
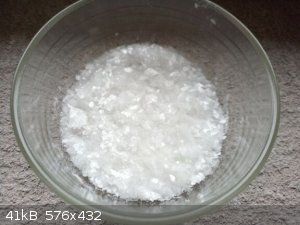
[Edited on 21-12-2019 by Fery]
|
|
DraconicAcid
International Hazard
   
Posts: 4356
Registered: 1-2-2013
Location: The tiniest college campus ever....
Member Is Offline
Mood: Semi-victorious.
|
|
Interesting. I know azelaic acid is nonanedioic acid because I recently compiled a list of the archaic names for the straight-chain alcohols and
acids (I needed the distraction while marking organic exams), but I don't recognize ricinoleic acid.
Please remember: "Filtrate" is not a verb.
Write up your lab reports the way your instructor wants them, not the way your ex-instructor wants them.
|
|
Boffis
International Hazard
   
Posts: 1879
Registered: 1-5-2011
Member Is Offline
Mood: No Mood
|
|
Nice work and an interesting write up. A couple of points that I have found from experience with KMnO4 oxidations. Most importantly is that it is best
to use KOH with the permanganate and to do the final acidification with HCl because potassium chloride is more soluble than either sodium of potassium
sulphates and has a flatter solubility curve so has a lesser tendency to crystallise on cooling. The use of NaOH to dissolve the crude ricinoleic acid
prior to oxidation is not a big issue if HCl is used to precipitate the free acid.
When I did a lot of work preparing heterocyclic and alicyclic dicarboxylic acids by oxidizing various systems with alkali permanganate I found that 30
to 40% of the total yield was recovered from the MnO2 filter cake by boiling it was more water and filtering atleast once but sometime up to 3 times.
See http://www.sciencemadness.org/talk/viewthread.php?tid=21978&...
Have you tried boiling the 31.5g of semisolid scum with water to see if you can extract more azelaic acid from it?
|
|
Fery
International Hazard
   
Posts: 1026
Registered: 27-8-2019
Location: Czechoslovakia
Member Is Offline
|
|
Hi Boffis,
I did not yet try boiling the 31.5 g of semisolid scum, this is what I would like to try. I'm curious why the yield was so low. Very likely most of
KMnO4 decomposed in strong alkaline environment with presence of MnO2 (the wiki link about oxidation of alcohols with KMnO4).
Original method from orgsyn.org acidifies first and then filters MnO2 but I tried to filter first and then acidify (clean MnO2 separation which could
be used for other things, possibility to use HCl, OK to filter cold solution no need to keep it hot, etc). I washed it twice so I believe no
substantial loses in MnO2 (I even tried to boil it to coagulate MnO2 particles just after the oxidation step but it foamed a lot so it was boiling for
only a very short time).
It is not very clear from my initial post but after performing 6 batches of oxidation (6x12 g = 72 g of ricinoleic acid total) I merged everything
together. Missing 24 g of ricinoleic acid was the first batch which revealed to be too much for 1 l flask, some foam escaped the flask so the amount
was uncertain so I discarded it completely to have exact numbers for calculating yield.
So the filtration, steam distillation, recrystallization was performed at once, only oxidation was in 6 batches. During oxidation the stirring was
using my hand (similar as with titration flask, I just had to use kettle-holder, so this experiment is suitable also for everyone not owning magnetic
stirrer).
Anyway the yield was terrible low so I already started an experiment from oleic acid instead (no -OH group so less KMnO4 wasted and also nonanoic acid
as a byproduct) but I'll be able to continue/resume in January 2020 (oxidation part already finished, not yet separation either purification). I'll
perform MnO2 washing 3 times with boiling water, Boffis thank you very much for your advice, 30-40% adhering to MnO2 is substantial (it perhaps
behaves like chromatographic adsorbent).
Then I would like to perform 35% H2O2 oxidation of oleic acid with H2WO4 catalyzer - this seems to be the cleanest way and better yields (already have
reagents, but not yet time) - with 8-fold amount of H2O2 in single step experiment or 2 steps experiment where the first step with H2O2 and second
step with NaOCl.
I have about 5 kg of KOH as well about 5 l of HCl in stock with a possibility to buy quickly when depleted, I just wanted to try with the most
available chemicals (NaOH, Pb accumulator H2SO4 as a lot of users here have limited access to chemicals, I think the most limited chemical for some
forumers here is KMnO4, small amounts of KMnO4 like 5-10 grams could be bought in pharmacy as it is used for treatment of mycotic infections of feet
but the experiment requires much more than 5 g).
I hope oleic acid gives better yield (ricinoleic acid consumes some KMnO4 to oxidize -OH to =O), I already found 1 disadvantage of oleic acid (lower
solubility of Na soap than Na ricinoleate) but the advantage is nonanoic (pelargonic) acid byproduct so I'll try to separate this acid also (I have
various aliphatic monocarboxylic acids only upto C8, so I'm still missing this C9 acid and from dicarboxylic I was missing pimelic and azelaic that's
why I started this experiment).
I had good yields of KMnO4 oxidation of toluene to benzoic acid and naphtalene to phtalic acid about 25 years ago but this 16% yield with ricinoleic
acid is quite mystery for me (in the http://orgsyn.org/Content/pdfs/procedures/CV2P0053.pdf they had yields 32-36%), but I changed a lot of steps - oxidation not at once but in
batches, putting KMnO4 slowly into ricinoleic acid - not ricinoleic acid into KMnO4 at once, filtering out MnO2 after oxidation - not after
acidification when it must be hot solution otherwise precipitation of azaleic acid, saponification with NaOH instead of KOH, perhaps some
polymerization of ricinoleic acid, ...).
|
|
Fery
International Hazard
   
Posts: 1026
Registered: 27-8-2019
Location: Czechoslovakia
Member Is Offline
|
|
Quote: Originally posted by Boffis  | Have you tried boiling the 31.5g of semisolid scum with water to see if you can extract more azelaic acid from it? |
Extra 2,2 g of azaleic acid was obtained this way: The 31,5 g of semisolid waste (the picture with aluminium foil) was boiled with 250 ml of water for
few minutes while well stirring, then quickly gravity filtered twice at highest temperature possible (small amount of oily mess passes the first
filtration but is captured at the second one), the volume of filtrate boiled down to 100 ml, cooled to 4 C in fridge, crystals filtered and air dried.
|
|
Tsjerk
International Hazard
   
Posts: 3032
Registered: 20-4-2005
Location: Netherlands
Member Is Offline
Mood: Mood
|
|
Nice! Has there been any actual publication anywhere on this procedure? Or did you come up with it yourself?
Of course I could have looked myself...
[Edited on 16-1-2020 by Tsjerk]
Attachment: 3016_en.pdf (165kB) This file has been downloaded 437 times
|
|
unionised
International Hazard
   
Posts: 5128
Registered: 1-11-2003
Location: UK
Member Is Offline
Mood: No Mood
|
|
Quote: Originally posted by DraconicAcid  | Interesting. I know azelaic acid is nonanedioic acid because I recently compiled a list of the archaic names for the straight-chain alcohols and
acids (I needed the distraction while marking organic exams), but I don't recognize ricinoleic acid. |
Oh
My!
Such
Good
Apple
Pie.
Sweet
As
Sugar.
Ricinoleic acid is the dominant acid in castor oil.
12-hydroxy-9-cis-octadecenoic acid
The name is (like "ricin") is derived from ricinus communis the castor oil plant.
|
|
DraconicAcid
International Hazard
   
Posts: 4356
Registered: 1-2-2013
Location: The tiniest college campus ever....
Member Is Offline
Mood: Semi-victorious.
|
|
I remember my first-year organic prof telling us that mnemonic, but he didn't expect us to actually learn the archaic names.
My current colleague uses "isoamyl alcohol" in one lab, but insists that we shouldn't use the name "oxalic acid" anymore; it's "ethanedioic acid".
Please remember: "Filtrate" is not a verb.
Write up your lab reports the way your instructor wants them, not the way your ex-instructor wants them.
|
|
Tsjerk
International Hazard
   
Posts: 3032
Registered: 20-4-2005
Location: Netherlands
Member Is Offline
Mood: Mood
|
|
Pffff, the troubles... Archaic names are fine, if you don't know one you Google it. We all know tens of thousands of words.. You can remember a couple
more.
Malic, maleic and malonic acids are a bit confusing, but that is more of an exception.
There is even an archaic name used in IUPAC... Look at this IUPAC name... Good luck pronouncing that without using the archaic name.
I wouldn't take anyone serious who would insist oxalic acid is inappropriate in any way. Can I then stop using formic acid and
Acetic acid? GAA for glacial acetic acid? Formaldehyde? Etc.
[Edited on 16-1-2020 by Tsjerk]
Attachment: 7827781.mol (3kB) This file has been downloaded 357 times
|
|
Fery
International Hazard
   
Posts: 1026
Registered: 27-8-2019
Location: Czechoslovakia
Member Is Offline
|
|
Tsjerk I found the method here http://orgsyn.org/Content/pdfs/procedures/CV2P0053.pdf
I changed it a little.
!!! But do not start from castor oil for producing azelaic acid - very low yield !!!
The ricinoleic acid has the only one advantage - its soaps are from the best soluble in water. So if you want to cook a special soap for your
girlfriend, wife, partner, maidservant, slave girl, ... then make the soap from castor oil.
But when you goal is to obtain as much azelaic acid as possible, do not start from castor oil. I'll post a method with better yield soon.
|
|
unionised
International Hazard
   
Posts: 5128
Registered: 1-11-2003
Location: UK
Member Is Offline
Mood: No Mood
|
|
Just out of idle curiosity, if you use oleic acid you should get nonanoic acid as the by-product.
But what do you get as a by-product from ricinoleic acid?
Is it the keto acid?
Does it cleave or decarboxylate or anything interesting?
|
|
Fery
International Hazard
   
Posts: 1026
Registered: 27-8-2019
Location: Czechoslovakia
Member Is Offline
|
|
unionised yes the oleic acid gave 70% yield of azelaic acid but I should complete report and post it here
From ricinoleic acid one of the product is 3-ketononanoic acid but due to yield 20% of azelaic acid (vs. 70% from oleic acid) I suspect 3-ketononanoic
acid is quickly oxidized and decarboxylated to heptanoic acid which consumes a lot of KMnO4 which is then missing for cleaving ricinoleic acid so the
terrible yield 20% (and a lot of semisolid mess 31,5 g in my case from 72 g of ricinoleic acid - the picture with aluminium foil). This is just my
theory without any proof - based on the yields difference 20% vs 70% for ricinoleic vs. oleic acid and a lot of something looking as unreacted
reactant for ricinoleic acid. Is somebody here with a practical experience or at least theoretical knowledge whether aliphatic 3-ketoacid could be
further oxidized and decarboxylated using 10% water solution of KMnO4 at temperatures approx 70 C in alkaline environment and presence of MnO2? Not
the exact info but the closest what I've found was oxidising malonic acid with alkaline KMnO4 here:
https://sci-hub.tw/https://pubs.rsc.org/en/content/articlelanding/1954/JR/jr9540002456#!divAbstract
Also KMnO4 decomposes to O2 which is autocatalysed by MnO2 so it is hard to estimate which reaction went at which extent. Awful frothing caused by
microbubbles of O2 in soap solution was hard to fight that's why I reversed reactants addition to overcome this problem and run the reaction under
some at least slight control (the original method from orgsyn suggest to add soap into KMnO4 at once, I added KMnO4 into soap in portions) - it is
easier to defeat few liters of foam in 15 minutes (my method) than in 15 seconds (orgsyn method).
I also plane the orgsyn method just not from ricinoleic but only from oleic, perhaps it will give even better yield than 70% (I suspect adding soap
into KMnO4 could reduce autocatalysed decomposition of KMnO4 into O2 + MnO2).
But I'm definitely looking forward oleic acid + H2O2 catalyzed by H2WO4 as there is no need to process huge amounts of MnO2 though I have 1 L Buchner
funnel and yes I know the trick of putting a pile of filter papers into Buchner funnel and progressively removing the uppermost filterpaper everytime the filtration
rate drops too much - page 15 in this pdf link - working with huge mass of wet fine freshly precipitated MnO2 is inevitably very dirty and long
lasting task that's why I'm looking forward cleaner H2O2 method.
[Edited on 19-1-2020 by Fery]
|
|
unionised
International Hazard
   
Posts: 5128
Registered: 1-11-2003
Location: UK
Member Is Offline
Mood: No Mood
|
|
I never tried it but I could be talked into believing that the keto acid would be in equilibrium with the enol form, and that's a clear candidate for
reaction with permanganate.
I'm also fairly sure it's a beta keto acid, and those decarboxylate at the drop of a hat.
|
|
Tsjerk
International Hazard
   
Posts: 3032
Registered: 20-4-2005
Location: Netherlands
Member Is Offline
Mood: Mood
|
|
Yes, MnO2 is a bitch, it is an oxidizer and a catalyst at the same time. Nice if you want to go from organic to CO2, but hard when you need something
in between. Please report on your H2O2 experiments!
|
|
Fery
International Hazard
   
Posts: 1026
Registered: 27-8-2019
Location: Czechoslovakia
Member Is Offline
|
|
unionised that's it, you are right !
Tsjerk I'm currently out of my lab and will be back in 1 week, then I explore still the KMnO4 route just with reversed order (adding soap into KMnO4)
with some of my improvement (not at once, but let's say only into 1/3 of the final amount of KMnO4, filter out MnO2 and repeat - maybe that could
reduce KMnO4 decomposition - I just want to reduce KMnO4 wasting to develop the most efficient method - it's matter not only for economy but also less
MnO2 the easier separation), then I'll focus on H2O2 way (this way has 2 variants too - using so much H2O2 to obtain products or use less H2O2 to
obtain dihydroxy fatty acid in first step and then using NaOCl for cleavage in the second step)
|
|
Fery
International Hazard
   
Posts: 1026
Registered: 27-8-2019
Location: Czechoslovakia
Member Is Offline
|
|
azelaic acid from oleic acid - yield 70%
15 g NaOH + 150 ml 90% IPA, dissolve as much as you can - some NaOH stays undissolved, well KOH + ethanol should be better, but...
Add 100 g SOHO (Sunflower Oil High Oleic acid, label on my flask claimed oleic acid > 95%) - I believe olive oil should work too.
Reflux, after 30 minutes add slowly about 40 ml of water in small portions (until NaOH dissolves) and reflux further 30 min (total 1 hour - perhaps it
is enough but a lot of researchers reflux for 3 hours...).
While still warm, acidify with warm 10% H2SO4 to methylorange (pH = 2) and add a small excess of H2SO4, pour into separatory funnel and shake
vigorously (there is excess of H2SO4 so all Na salts are decomposed into free fatty acids).
Wash 2x with 300 ml of warm water (oleic acid m.p. 13-14 C hence do not use cold water).
Yield 91 g of crude oleic acid (282,47 g/mol = 0,322 mol).
Divide oleic acid into 4 equal portions (about 23 grams).
To every portion add solution of 5 g of NaOH in 20 ml of water, stir and warm upto boil and add more water until soap dissolves (about 200 ml), then
cool down to 50 C (using NaOH was bad idea as Na soaps are worse soluble than K soaps, but Na perhaps has 1 advantage - read later).
Vigorous stir and add warm solution of 71 g of KMnO4 in 750 ml of water (35 C) in approx 20 portions during 30 minutes, keeping T at most 75 C.
I performed it in 1 l flask but I recommend 2 l flask (I lost a veeeery little of foam in 1 batch of the 4).
So I used 284 g of KMnO4 totally to oxidize the 91 g of oleic acid.
Filter out MnO2 while still hot and wash MnO2 twice with boiling water of the same volume as the volume of MnO2. Use vacuum filtration as it is very
slow process. Collect all filtrates together.
Let the filtrates to cool down and put into fridge to 4 C. White precipitates settle at the bottom (I believe Na salts - unreacted oleic acid in a
form of Na oleate, then very probably also Na palmitate and Na stearate coming from the oil where is never 100% oleic acid, and I can't exclude also a
choice of ??? Na nonanoate ??? ) - this is the only one advantage of using NaOH to dissolve oleic acid prior its oxidation instead of using KOH.
Filter out using vacuum.
Evaporate filtrate to about 500 ml and put into a beaker (I used subboiling temperature for half a day so evaporation was without boiling thus without
frothing - maybe boiling is possible too??? if the amount of soap is low).
To the solution in the beaker add 50% H2SO4 slowly dropwise while stirring. Evolution of CO2 happens, which brings substances with lower density to
the surface (and everything adhering to bubbles too) - nonanoic acid (and also small amount of oleic acid, stearic acid, palmitic acid which which did
not precipitate as Na soap).
When the solution starts to appear milky, interrupt H2SO4 addition, let the solution to cool down and put into fridge. Mechanically separate the upper
semisolid layer (nonanoic acid contaminated with azelaic acid and with fatty acids). Transfer the semisolid upper layer into 1 L flask with 600 ml of
water and perform steam distillation til the distillate does not contain organics anymore (approx 100-200 ml of water necessary to distill out every 1
ml of the nonanoic acid, I collected 10g of nonanoic acid). Let the distillation flask to cool down and put into fridge to 4 C, filter out azelaic
acid (12,5 g slightly wet, no need to dry out completely).
Add more H2SO4 dropwise to the beaker to make it acidic to methylorange (pH = 2), pour into 1 l distillation flask and start distillation, collect
distillate in a form of emulsion, stop distillation when the condensate is clear. Add this portion of nonanoic acid from the distillate to the
previous main fraction of nonanoic acid. If the starting oil contained linoleic acid also some hexanoic acid should be present. Solubility of hexanoic
acid is 1.082 g/100 mL, solubility of nonanoic acid is 202.7 mg/L at 20°C so maybe hexanoic acid stays in water.
Filter the content from the distillation flask while still hot, cool down, put into fridge to 4 C and let to crystallize overnight. Suspension of
azelaic acid, K2SO4, Na2SO4.10H2O in concentrated sulfates solution is obtained. Density of sulfate crystalls is at least twice the density of water
and the crystalls are quite big (few mm). Azelaic acid is in a form of small crystals or better to say amorphous particles which density is only
slightly higher than density of conc. solution of K2SO4 and Na2SO4 in water. Separate azelaic acid mechanically by well stirring the mixture and
quickly decanting, sulfates stay at bottom (flotation), also perform 2 additional flotation separations with 2x 100 ml of ice cold water which washes
out remainders of azelaic acid and dissolves only little of sulphates. Filter out azelaic acid. Put together to the first fraction from the
distillation flask.
Recrystal twice from water.
Yield 42,3 g (188,22 g/mol = 0,225 mol, 70%)
Note the amount of KMnO4 284 g = 1,8 mol (approx 6 times the amount of oleic acid 0,322 mol) so almost one half of KMnO4 just decomposed to O2 and
MnO2 so I would like to investigate ways to reduce the KMnO4 consumption (economy factor and less of dirty work when filtering MnO2).
garti1982.pdf table I - KMnO4/oleic molar ratio 4:1 yield AZA 84%, ratio 6:1 yield AZA 87% - I'll try to reduce KMnO4 ratio from 6:1 to 4:1
https://sci-hub.tw/https://www.sciencedirect.com/science/art...
Now what to do with nonanoic acid fraction.
I obtained 10,6 g of crude nonanoic acid. It is strange because the yield of azelaic acid was 42,3 g so I got approx 3x lower yield of nonanoic acid
and it had to be lost in some way (perhaps precipitating as Na with soaps ??? or pehaps I had to distill further - I stopped when collected approx 1,5
L of water distillate).
Another strange observation - m.p. of nonanoic acid 12,5 C but my sample did not solidify in fridge at 4 C but it did in freezer at -18 C so its m.p.
is somewhere in this range (perhaps massive contamination but with what??? I can exclude hexanoic acid coming from possible linoleic acid from the
SOHO oil as I have more than 1 L of hexanoic acid in stock and I know its smell very well and no traces of such smell in my sample...).
Further investigation of nonanoic acid fraction is required (I'm looking forward the H2O2 oxidation method where it should not be lost). Nonanoic acid
obtained by KMnO4 way is in low yield (losses) and too low m.p. (impurities). I do not have microscale distillation apparatus, all my smallest flasks
are 100 ml where 10 ml couldn't be distilled efficiently.
Nonanoic acid is interesting stuff. People with epilepsy may benefit from ketogenic diet. That's why nonanoic acid was investigated and its
antiepileptic effect was observed. But valproic acid won (2-propylpentanoic acid, its Na salt) although it has teratogenic effect (women planing
pregnancy must be switched to other substance like lamotrigine). I believe valproic acid (which does not occur in nature) won because it is
metabolised slowlier and nonanoic acid lost because metabolised too fast (it is very inconvenient to take pills e.g. 5 times a day). 4-methyloctanoic
acid was also researched. Various medium chain fatty acids too (btw. goat milk is rich on them).
Nonanoic acid is also used as cat repellent.
https://echa.europa.eu/documents/10162/f4351610-c2de-c078-0f...
photos will follow soon
|
|
Fery
International Hazard
   
Posts: 1026
Registered: 27-8-2019
Location: Czechoslovakia
Member Is Offline
|
|
photos - azelaic acid from oleic acid by KMnO4 oxidation
saponification - reactants from the left: beaker with 100 g of sunflower oil high oleic acid, bottle with the oil, flask with 150 ml isopropanol + 15
g NaOH
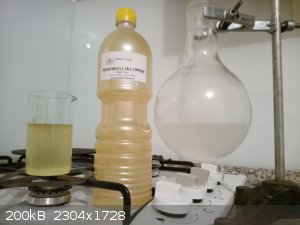
saponification - reflux
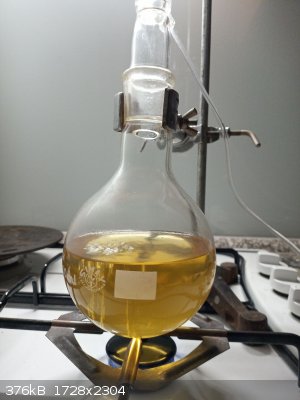
91 g oleic acid
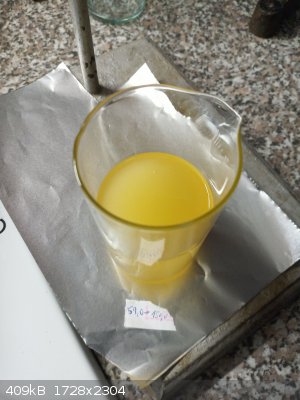
32 g oleic acid + 5 g NaOH + 200 ml H2O
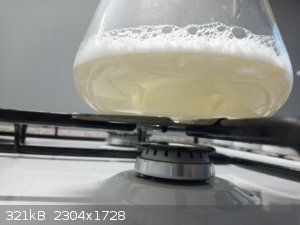
oxidation of Na oleate with KMnO4 (front flask), solution of KMnO4 in beaker (behind)
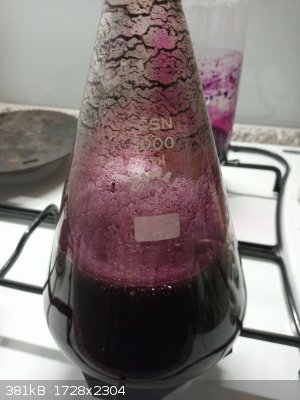
filtering out MnO2, huge Buchner funnel + vacuum necessary, very slow and dirty process
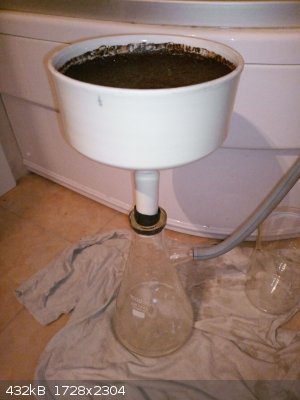
filtering out white soaps - picture missing (I forgot to take a picture)
evaporating filtrates from 4 L to 0,5 L, took half a day, temperature kept just below boil
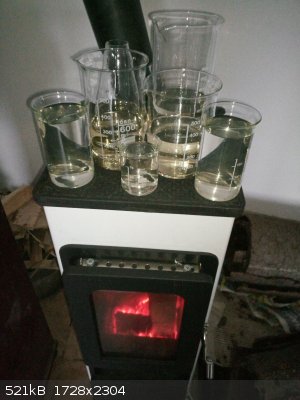
partial acidification of concentrated filtrates with H2SO4
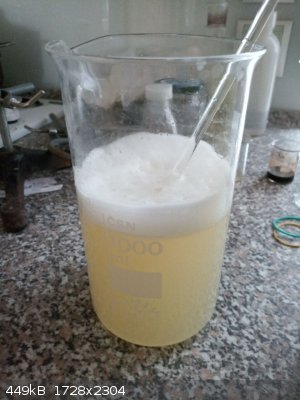
upper semisolid layer separated mechanically and transferred from the beaker into a flask with 650 ml of water to perform steam distillation
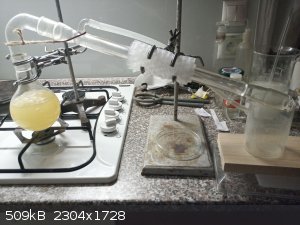
performing steam distillation, nonanoic acid passes as a distillate, azelaic acid washed into water phase which stays in the flask, H2O must be added
few times into flask to continue, 10 g of nonanoic acid obtained in 1,5 L of H2O distillate, see the light effect at the edge of nonanoic acid / water
in the beaker
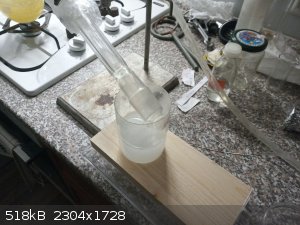
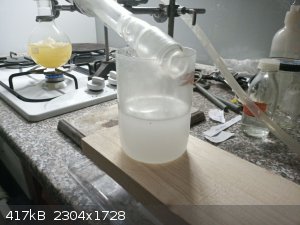
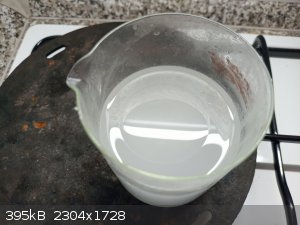
10 g of nonanoic acid obtained yet (upper layer in separatory funnel)
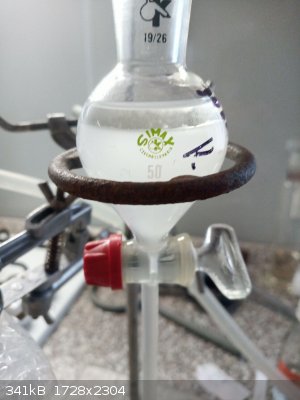
after full acidification of the content in the beaker to pH 2 and separating azelaic acid suspension in water using flotation and decantation + 2x
extra 100 ml of ice cold water washes, heavier and bigger crystals of K2SO4 + Na2SO4.10H2O stay at the bottom of the beaker
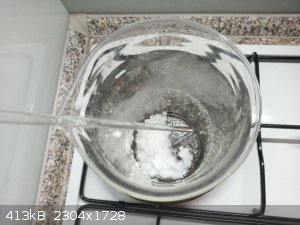
suspension of azelaic acid in formerly concentrated ice cold solution of sulphates + 2x 100 ml of ice cold water quick washings (this ensures
sulphates won't precipitate later anymore) transferred into distillation flask (the beaker with sulphates behind)
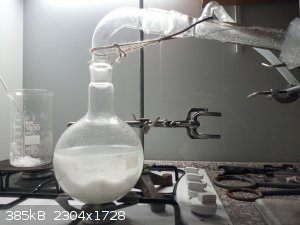
less than 1 g of nonanoic acid steam distilled out in 100 ml of water (bigger beaker in right), distillation stopped when distillate clear (smaller
beaker in left), azelaic acid stays dissolved in the water in the flask, which is later cooled down and crystallized (the flask is out of the picture)
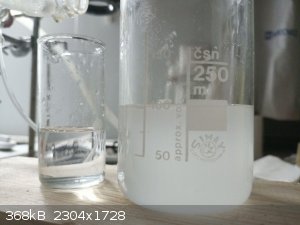
12,5 g of wet azelaic acid from upper semisolid layer obtained at partial acidification and first steam distillation separation (left), 10,6 g of
nonanoic acid in amber flask (middle, collected together from both steam distillations), biggest fraction of azelaic acid after full acidification,
flotation+decantation and removing small amount of nonanoic acid by second steam distillation (right)
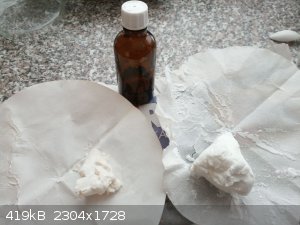
pure azelaic acid after 2 recrystallizations from water, seems I hit the limits of my fritte :-D
|
|
Fery
International Hazard
   
Posts: 1026
Registered: 27-8-2019
Location: Czechoslovakia
Member Is Offline
|
|
azelaic acid - most efficient method related to KMnO4
This experiment focused on squeezing KMnO4 as much as possible:
Oxidation was performed in 3 steps with 1/3 of KMnO4 instead of the whole KMnO4 at once (that prevented reaching too high temperature).
The molar ratio oleic acid : KMnO4 = 1 : 3 (so in every step molar ratio was used 1:1, in the first step this ensured that no oleic acid stayed
unoxidized - every molecule of oleic acid needs to attach 1 molecule of MnO4-) this is only slight excess of KMnO4, 1 molecule of oleic acid requires
4 molecules of O and from 3 molecules of KMnO4 there are 4 and 1/2 molecules of O
Among the 3 oxidation steps, MnO2 was always filtered out with a hope to decrease KMnO4 decomposition to KOH + MnO2 + O2 which is autocatalyzed by
MnO2 and KOH.
The precipitated MnO2 was extracted with boiling water thrice (but 5 times would be even better or using twofold volume of water).
Temperature of oxidation reaction started at 20 C and never exceeded 40 C.
saponification: 102,5 g SOHO + 25,2 g 85% KOH + 100 ml C2H5OH
crude oleic acid yield 98,0 g
22,9 g 85% KOH + 300 ml H2O dissolved, added all 98,0 g of oleic acid, mixed thoroughly with massive glass stick (thick soap jelly mass, at least 6 mm
diameter glass stick required, narrower glass stick could easily break), then added extra 200 ml of water and warmed upto 100 C while vigorous
stirring - soap dissolved at the end, then cooled down to 25 C (soap stayed dissolved, total volume 650 ml now)
165 g KMnO4 totally which was divided into 3 portions
3 x 55,0 g KMnO4
55,0 g KMnO4 dissolved in 750 ml of 35 C water in 3 L Erlenmeyer flask and poured into 6 L RBF, then dissolved the remaining crystals in 3 L
Erlenmeyer flask with 150 ml of water and finally flushed the Erlenmeyer flask with 100 ml of water and poured everything into 6 L RBF. Then cooled
the KMnO4 solution in RBF down to 20 C by submersing the flask into a bucket with 10 C cold water while stirring (do not overcool the flask as then
the KMnO4 would start to crystallize, the target KMnO4 solution temperature is 20 C). Temperature of the obtained KMnO4 solution is very important,
the higher T the higher rate of KMnO4 decomposition and thus lower yield. Do not dissolve KMnO4 in the 6 L flask directly as it is then hard to see
whether whole KMnO4 dissolved or only partially. Do not try to dissolve it in 20 C water, it would last too long, dissolve in 35 C and then cool down
to 20 C, this is the best method.
While vigorous stirring the 650 ml of soap with temperature 25 C was added into the 6 L flask with fully dissolved 55,0 g of KMnO4 in 1 l of water
with temperature 20 C.
Note if the temperatures were higher the reaction proceeded faster and more heat was produced and more KMnO4 decomposed. The reaction was completed in
few seconds and the final T stayed below 40 C.
The 6 L RBF was at the end half-full so contained about 1 L of froth (cool, less than 1 L of oxygen, less than 1 g of O2 by KMnO4 decomposition).
The mixture was vacuum filtered on 1 L Buchner funnel and filtrate was collected.
The wet MnO2 was boiled with 700 ml of water for 5 minutes while vigorous stirring by hand and glass stick, this prevented frothing and bumping
substantively (no more than 2-3 cm of foam at the surface), then cooled down and vacuum filtered. The MnO2 was then reprocessed the same way twice
again, so totally 3 times boiled and filtered (plus the first filtration of the content of 6 L RBF before boiling the MnO2 in water, so total 4
filtrations performed). I recommend to wash it no 3x but 5x (look at the pictures and you'll understand) or using double amount of water (1,5 L) if
you want only 3 washings - the yield could be even better (I approximate 10-20 % increase in yield).
The collected filtrates evaporated at subboiling temperatures down to 650 ml.
This oxidation step was repeated 2 times again by pouring the obtained 650 ml partially oxidized solution into KMnO4 solution (so total 3 oxidations
and KMnO4 consumption 3 x 55,0 g = 165 g). For the first 2 oxidations the KMnO4 color disappeared in few seconds, for the third one there was still
KMnO4 color observed after 3 hours, then the rest of permanganate was decomposed by heating the 6 L RBF on a steam bath while stirring.
The solution from the last oxidation was processed the same way as in previous experiment.
yields:
15,2 g nonanoic acid
16,3 g azelaic acid extra pure after 2 recrystallizations from each 800 ml of water
10,6 g azelaic acid second grade quality obtained by concentrating all 3 mother liquors to 200 ml (in the first one a lot of higher density sulfates
from which lighter azelaic acid was decanted) and twice recrystallized from 200 ml of boiling water, then cooled down to 20 C and finally cooled down
to 4 C in fridge
This experiment proven that it is essential to keep the T lower, 70 C in previous experiments were too much, 40 C here was much better.
photos will follow
[Edited on 21-2-2020 by Fery]
|
|
Fery
International Hazard
   
Posts: 1026
Registered: 27-8-2019
Location: Czechoslovakia
Member Is Offline
|
|
saponification:
102,5 g SOHO + 25,2 g 85% KOH + 100 ml 95% C2H5OH
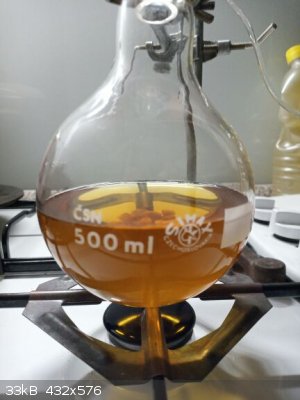
crude oleic acid, yield 98,0 g
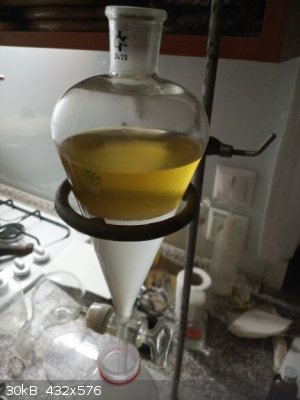
oxidation, round 1 of 3:
before oxidation: 6 L RBF with 55 g KMnO4 in 1 L of water, 1 L beaker with 650 ml solution of potassium oleate from 98,0 g of crude oleic acid + 22,9
g 85% KOH
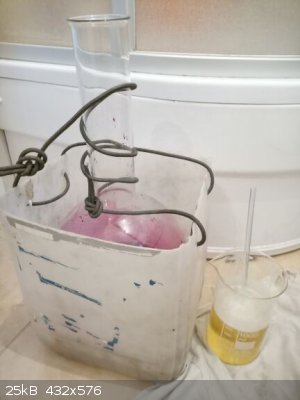
oxidation, round 1 of 3, after oxidation (reaction done in few seconds)
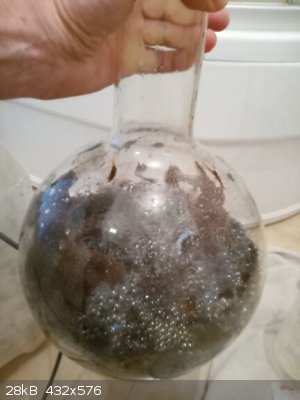
oxidation, round 1 of 3, after oxidation, the primary filtrate of the content from 6 L RBF on the left side and the filtrate from the last 3rd boiling
of MnO2 on the right side - that's why I recommend 5 boilings of MnO2 or using twofold volumes of water for all 3 boils, here you can see how nasty is
this fine MnO2, it simply behaves like chromatographic adsorbent
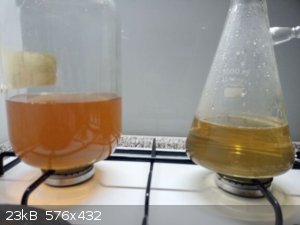
oxidation, round 1 of 3, after oxidation, comparisons of the filtrates from the 1st boil of MnO2 on the right side, from the 2nd boil in the middle,
from the last 3rd boil on the left side (the primary filtrate not yet here, no place here for it yet...)
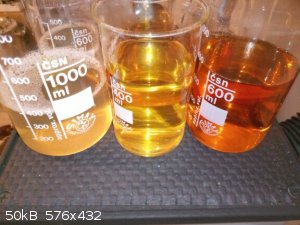
oxidation, round 2 of 3, before oxidation:
empty 6 L RBF on the left behind, concentrated solution from the 1st round of oxidation in the 1 L beaker in front, 3 L Erlenmeyer flask with solution
of KMnO4 on the right - do not try to dissolve KMnO4 directly in the oxidation vessel, it is impossible to see whether all crystals dissolved or not
yet, dissolve the KMnO4 in different flask in 35 C water, transfer into reactor, cool down to 20 C on 10 C water bath, that's the fastest way of
preparing 20 C solution of 55 g KMnO4 in 1 L of water
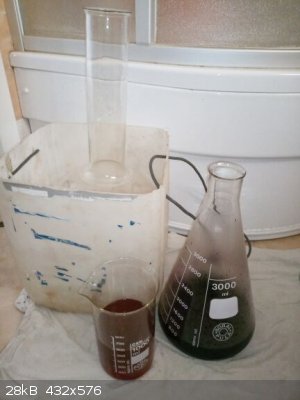
oxidation, round 2 of 3, before oxidation, 55 g KMnO4 in 1 L of water already in the 6 L RBF, cooled down to 20 C using 10 C water bath
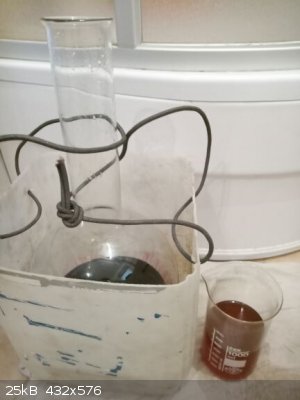
oxidation, round 2 of 3, after oxidation, almost no frothing
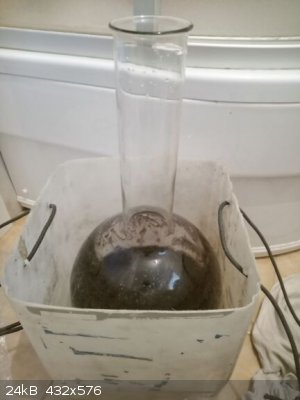
oxidation, round 2 of 3, after oxidation, a view through the neck of flask
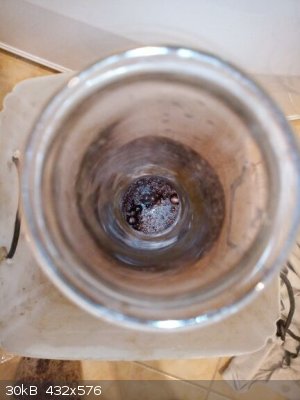
oxidation, round 2 of 3, after oxidation, preparing for filtering out MnO2
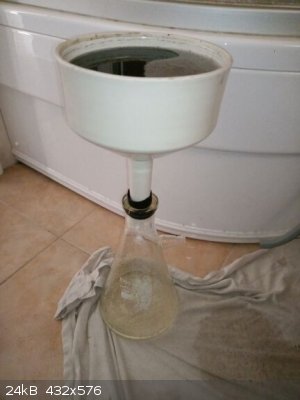
oxidation, round 2 of 3, after oxidation, filtered MnO2 which had to be boiled with its own volume of water for 3 times, filtrates collected and
concentrated
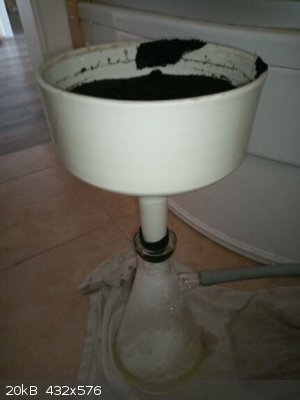
oxidation, round 2 of 3, after oxidation, after boiling MnO2 with water for 5 minutes (it almost boiled over, I recommend to use bigger beaker,
luckily thick glass stick and vigorous manual stirring managed to keep it inside)
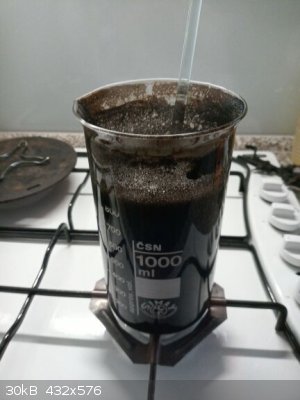
oxidation, round 2 of 3, after oxidation, comparison of primary filtrate on the left side, filtrate from 1st boil of MnO2, 2nd boil of MnO2, 3rd boil
of MnO2 on the right side, interesting that the filtrate from the 1st boil is always darker than the primary filtrate, this is for all 3 oxidation
rounds (on the round 1 of 3 the same visible when comparing photos), so here is clearly visible how important is to boil the fresh fine voluminous
MnO2 precipitate to coagulate it as much as possible
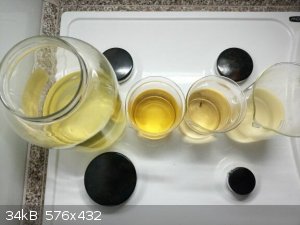
photos from oxidation round 3 of 3 not included, everything similar, just the KMnO4 did not lose color after 3 hours, so it was necessary to heat the
6 L RBF on steam bath while stirring until no more KMnO4 color and also the color of filtrates more pale than in previous step
final product, 16,3 g of very pure azelaic acid dried in the air in the evaporating dish for 2 weeks on the left side, 10,6 g of lower grade purity
azelaic acid obtained by concentrating mother liquors and then 2 recrystallizations from 200 ml of distilled water on the right side (very slow
cooling from not too much concentrated solution produces lustrous leaf crystals, while from concentrated solution on rapid cooling the crystals are
very fine snow-white)
picture of 15,2 g nonanoic acid not included
|
|
|