metalresearcher
National Hazard
  
Posts: 758
Registered: 7-9-2010
Member Is Offline
Mood: Reactive
|
|
SO3 from CaSO4 is it possible ?
There is a thread running in this forum about SO3 from NaHSO4. But when I heat CaSO4 to yellow hot, a slight pungent SO2 (SO3 ?) odor appears .
So I think about making a device with a Haldenwanger porcelain crucible with a sealed lid to heat CaSO4 to about 1000oC and capture the SO3.
In contrary to NaHSO4, CaSO4 is widely available.
Is this feasible or am I talking nonsense ?
|
|
Hydrazinium
Harmless
Posts: 9
Registered: 6-1-2011
Member Is Offline
Mood: No Mood
|
|
The reaction:
CaSO<sub>4</sub> ======> CaO + SO<sub>3</sub>
to my calculation is associated with an enthalpy change of 189.81 J K<sup>-1</sup> mol<sup>-1</sup>, and enthalpy of -403.3 kJ
mol<sup>-1</sup>, so the reaction should be product favoured at some temperature. Driving off the SO<sub>x</sub> should help
shift the equilibrium to the right.
I think...
[Edited on 2011-1-14 by Hydrazinium]
|
|
DougTheMapper
Hazard to Others
 
Posts: 145
Registered: 20-7-2008
Location: Michigan, USA
Member Is Offline
Mood: Energetic
|
|
CaSO4 -> CaO + SO3
The problem is that the temperature required to decompose the sulfate makes apparatus impractical. There are several things going against you:
1. If the CaSO4 is not completely dry there will be a whole bunch of steam released at it dehydrates. Heating to 250C before introducing it to the
crucible will alleviate this.
2. Sealing the crucible is a bad idea. At the temperatures required, SO3 is a gas, so you'll end up pressurizing your crucible.
3. A sealed crucible for batch conversion is not likely to work well; upon cooling, the SO3 and CaO are likely to react to re-form the CaSO4 unless
separated.
4. Separation of the SO3 gas from the CaO during the reaction will be difficult since any tubes and connections will not only have to withstand the
1000C but will also have to be resistant to acid attack, which eliminates the use of most refractory oxides like alumina and magnesia. This also goes
for the sealant to hold the lid on the crucible.
For all practical purposes, I would not consider this a viable method to produce SO3. If you must use a sulfate to make SO3, try copper II sulfate.
The process is similar but decomposition occurs at a much lower temperature.
[Edited on 14-1-2011 by DougTheMapper]
Victor Grignard is a methylated spirit.
|
|
Hydrazinium
Harmless
Posts: 9
Registered: 6-1-2011
Member Is Offline
Mood: No Mood
|
|
I would certainly say that it is precluded by practical issues, but is feasible. You could use quartz tube I believe to lead off the
SO<sub>3</sub>. In general, I would say that the issue with these difficulties would be far more than that of finding
NaHSO<sub>4</sub>.
[Edited on 2011-1-14 by Hydrazinium]
|
|
not_important
International Hazard
   
Posts: 3873
Registered: 21-7-2006
Member Is Offline
Mood: No Mood
|
|
This has been covered before, including a few months ago where some unfounded speculation based on ways to lower the temperature needed.
First, the temperatures needed are high:
Quote: | . Pure CaSO4 is known to be very stable under oxidizing conditions at FBC bed temperatures (800-900.DEG.C.). However, the temperature of burning fuel
particles or the temperature near fuel feed points where volatile matter combustion occurs are considered to be higher than the average bed
temperature. In addition, there exist coal ash particles around the sulfated limestone particles (or fine sulfated limestone powders around coal
particles), and the temperature of CaSO4 decomposition may be affected by the coexistence. The objective of this work is to evaluate the decomposition
rate of CaSO4 mixed with coal ash. The mixture was heated up to 1350.DEG.C. in oxidizing atmosphere, measuring SO2 release and weight change of the
mixture. Pure CaSO4 was found to be very stable and decomposition occurred only at higher temperatures than 1250.DEG.C.. When coal ash was mixed with
CaSO4, the decomposition and SO2 release occurred at relatively lower temperatures, for example, 1000.DEG.C. |
http://sciencelinks.jp/j-east/article/200601/000020060105A10...
Second, at the temperatures needed SO3 is unfavored compared to SO2 + O2.
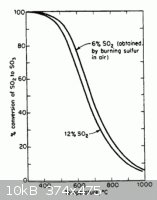
One one of te previous threads on the topic there was information on a reference for the decomposition temperature of various metal sulfates. It too
noted that mainly SO2 was the offgas for most sulfates examined.
|
|
metalresearcher
National Hazard
  
Posts: 758
Registered: 7-9-2010
Member Is Offline
Mood: Reactive
|
|
But with NaHSO4, the same issues appear: require quartz tubing but at a lower temperature.
According to http://en.wikipedia.org/wiki/Sulfur_trioxide :
1. Dehydration at 315°C:
2 NaHSO4 → Na2S2O7 + H2O
2. Cracking at 460°C:
Na2S2O7 → Na2SO4 + SO3
460oC is just possible with standard borosilicate glass.
I found on ebay a UK source for NaHSO4 which seems reasonable:
http://cgi.ebay.co.uk/1Kg-Sodium-Bisulphate-bisulfate-Hydrog...
[Edited on 2011-1-14 by metalresearcher]
|
|
peach
Bon Vivant
   
Posts: 1428
Registered: 14-11-2008
Member Is Offline
Mood: No Mood
|
|
This is another example where Sedit's proposed ceramic chemistry gear may be of use. Again, particularly if it can be made to get that hot with
microwave heating.
|
|
The WiZard is In
International Hazard
   
Posts: 1617
Registered: 3-4-2010
Member Is Offline
Mood: No Mood
|
|
Quote: Originally posted by metalresearcher  | There is a thread running in this forum about SO3 from NaHSO4. But when I heat CaSO4 to yellow hot, a slight pungent SO2 (SO3 ?) odor appears .
So I think about making a device with a Haldenwanger porcelain crucible with a sealed lid to heat CaSO4 to about 1000oC and capture the SO3.
In contrary to NaHSO4, CaSO4 is widely available.
Is this feasible or am I talking nonsense ?
|
"Sulphur dioxide is produced from calcium sulphate by
Chem. Fabr. vorm. Weiler-ter Meer, Ger. P. 307772
A mixture of calcium sulphate and calcium sulphide
is heated above 1000o, whereby sulphur dioxide is
formed in accordance with the equation
3CaSO4 + CaS + 4CaO + 4SO2
[Rapidly above 700o - CaSO4 + 3C = CaS + CO2 + 2CO]
Wilfrid Wyld
Raw Materials for the Manufacture of Sulphuric Acid
and the Manufacture of Sulphur Dioxide
Sulphur from the Sulphates of Alkaline Earths
Gruney and Jackson
Edinburgh 1923
djh
----
Iron pyrites have long been burned to produce SO2,
anyone remember the British poisonous beer problem
of some time ago?
|
|
bbartlog
International Hazard
   
Posts: 1139
Registered: 27-8-2009
Location: Unmoored in time
Member Is Offline
Mood: No Mood
|
|
Seems to me that you're better off converting to one of a variety of other sulfates and then decomposing that, rather than dealing with the fairly
formidable temperatures required to pyrolyze CaSO4.
|
|
bbartlog
International Hazard
   
Posts: 1139
Registered: 27-8-2009
Location: Unmoored in time
Member Is Offline
Mood: No Mood
|
|
Quote: | 3CaSO4 + CaS + 4CaO + 4SO2 |
Well, OK. But I think he wanted SO3. If SO2 is satisfactory then a low temperature route would be conversion to ammonium sulfate via reaction with
ammonium carbonate, followed by thermal decomposition at a mere 300C. On the downside this produces a mess of gaseous products besides SO2 so the
isolation becomes more complicated, so I can see why other routes might be preferred despite the higher temperatures.
|
|
The WiZard is In
International Hazard
   
Posts: 1617
Registered: 3-4-2010
Member Is Offline
Mood: No Mood
|
|
Quote: Originally posted by bbartlog  | Quote: | 3CaSO4 + CaS + 4CaO + 4SO2 |
Well, OK. But I think he wanted SO3. If SO2 is satisfactory then a low temperature route would be conversion to ammonium sulfate via reaction with
ammonium carbonate, followed by thermal decomposition at a mere 300C. On the downside this produces a mess of gaseous products besides SO2 so the
isolation becomes more complicated, so I can see why other routes might be preferred despite the higher temperatures.
|
Picky-picky-picky.
OK from the same book
A process for making sulphur trioxide is described by
W. H. Seamon, Texas (U.S.P. 129089) [actualy 129098]
the compound being produced by fusing a mixture of sodium
sulphate, calcium sulphate, and silca.....
http://tinyurl.com/4ru9b3c
|
|
macckone
Dispenser of practical lab wisdom
   
Posts: 2168
Registered: 1-3-2013
Location: Over a mile high
Member Is Offline
Mood: Electrical
|
|
SO2 is the primary product with thermal decomposition of CaSO4 as previously stated but it is reasonably pure SO2 that can be oxidized by the contact
or lead chamber processes as well as H2O2.
|
|
unionised
International Hazard
   
Posts: 5126
Registered: 1-11-2003
Location: UK
Member Is Offline
Mood: No Mood
|
|
It's an interesting question.
Certainly, other sulphates are available, but I can pick plasterboard out of skips for nothing and that is quite a useful attribute.
Using silica as an "acid" to displace SO3 is attractive for much the same reasons.
One route that strikes me as interesting is the reduction of the sulphate to sulphide, separating H2S, then oxidising H2S in the presence of moisture
to get H2SO4.
I know of two things that will reduce sulphate, one is hot carbon which works well enough. The other is the use of sulphate reducing bacteria which
avoids the high temperatures.
Not sure it's very practical.
Mixing crushed plasterboard with sawdust or whatever other organic waste you have will do the reduction.
Either you can stick it in a crucible in a furnace, or you can put it in a fermenter.
|
|
macckone
Dispenser of practical lab wisdom
   
Posts: 2168
Registered: 1-3-2013
Location: Over a mile high
Member Is Offline
Mood: Electrical
|
|
The reduction to sulfide is relatively low temperature (600C by carbon monoxide with NiFe catalyst).
https://pubs.acs.org/doi/10.1021/ie9901628
Straight carbon probably requires more heat.
HS2 can be partially freed by simply adding water.
|
|
unionised
International Hazard
   
Posts: 5126
Registered: 1-11-2003
Location: UK
Member Is Offline
Mood: No Mood
|
|
If you have hot arbon in air, you have CO.
But the catalyst might be helpful.
This reduction is the usual way of getting soluble barium compounds so it's quite well documented.
[Edited on 28-8-20 by unionised]
|
|
macckone
Dispenser of practical lab wisdom
   
Posts: 2168
Registered: 1-3-2013
Location: Over a mile high
Member Is Offline
Mood: Electrical
|
|
600C is easily within the range of a home chemist.
1000C is a lot harder without a kiln.
The 1923 reference says rapidly above 700C without mentioning a catalyst but also says 1000C is used, so I am going to bet on 1000C being the
practical temperature without an additional catalyst. Which may have been present at 700C.
Possibly an iron compound would accelerate the process without the need to use carbon monoxide.
|
|
unionised
International Hazard
   
Posts: 5126
Registered: 1-11-2003
Location: UK
Member Is Offline
Mood: No Mood
|
|
If you use carbon as an reducing agent at high temperatures, you get CO.
In principle I think iron might act as a reductant, but it's an odd choice. The reduction by Al is well known.
I have done the reaction using BaSO4 in a piece of copper pipe heated with a blowtorch. The copper didn't melt so it was below about 1080 C, but I
think it was above 700.
Melting copper in the flame of a blow torch is within the realms of home chemistry.
I added Na2SO4 which I read somewhere acted as a catalyst.
The CaSO4 reaction may be easier or it may be harder I don't know.
|
|