Pages:
1
2
3 |
gnitseretni
Hazard to Others
 
Posts: 282
Registered: 5-1-2007
Location: Colombia
Member Is Offline
Mood: No Mood
|
|
Electroforming Copper Liners
I managed to electroform two copper liners. I did a quick writeup on it (with lots of pics) that shows how I made them. Thought I'd share it in case
others would like to try it 
Attachment: Electroforming Copper Liners.pdf (281kB) This file has been downloaded 3298 times
|
|
quicksilver
International Hazard
   
Posts: 1820
Registered: 7-9-2005
Location: Inches from the keyboard....
Member Is Offline
Mood: ~-=SWINGS=-~
|
|
It's a unique and impressive idea. And from the amount of times it's been downloaded, people are taking a look. The major issue in a SC is the liner.
With a utilitarian format like this the concept could broaden.
|
|
bbartlog
International Hazard
   
Posts: 1139
Registered: 27-8-2009
Location: Unmoored in time
Member Is Offline
Mood: No Mood
|
|
Nice pictures and idea. Consider trying to apply a conductive coating of some sort so as to make separation trivial (graphite?), but it might well
just provide one more way to goof things up.
The blisters may be controllable by adjusting the current level, but given your power supply this might not be practical.
|
|
gnitseretni
Hazard to Others
 
Posts: 282
Registered: 5-1-2007
Location: Colombia
Member Is Offline
Mood: No Mood
|
|
Nah, it came off with hardly any effort at all, so no graphite coating needed.
Btw, I found out that those "blisters" are called "nodules", for which the cause could be many things from what I've read.
One cause could be that I didn't have my anode inside a "bag", like commercial platers have, to keep particles out of the solution. Another cause
could be that I didn't agitate the solution, which again commercial platers do. I also didn't cover my container to keep dust and what not from
getting in my solution 
I also didn't use a suppressor, which according to a patent I found "tends to give a more uniform current distribution over the surface of the
substrate and allows the metal deposition to proceed with a global leveling."
I also didn't use brighteners, levelers, wetting agents and whatever else they use in there. But I'm not in the business of making liners, so I don't
mind having to clean up the few I do make 
EDIT: That patent mentioned several examples of suppressors, and one was polyethylene glycol, which is sold as Miralax at Walgreens. $7 for 4oz. Thing
is you only need to use 200ppm 
[Edited on 3-7-2010 by gnitseretni]
[Edited on 3-7-2010 by gnitseretni]
|
|
gnitseretni
Hazard to Others
 
Posts: 282
Registered: 5-1-2007
Location: Colombia
Member Is Offline
Mood: No Mood
|
|
I just took a better look at my aluminum cone and it got attacked by the plating solution, right above where the copper was forming(at the surface of
the solution). It etched a groove all around, about as deep as it is wide.
Next time (with a new alu cone) I'll submerge the alu cone a little more than what I want plated and plate for like just a minute or so. Then I'll
slightly raise the cone out of the solution a little bit and continue plating. That should prevent it from happening again.
|
|
12AX7
Post Harlot
   
Posts: 4803
Registered: 8-3-2005
Location: oscillating
Member Is Offline
Mood: informative
|
|
Have you tried thiourea (contained in Tarn-X)?
Good to know copper releases easily from aluminum.
Tim
|
|
gnitseretni
Hazard to Others
 
Posts: 282
Registered: 5-1-2007
Location: Colombia
Member Is Offline
Mood: No Mood
|
|
Haven't tried thiourea yet.
First I'd like to try to get some agitation going and place my anode inside a "bag" and see if that changes anything. I'm thinking/hoping it will,
because every time I lift my anode out of the solution, this copper sludge runs off and some of these particles may cling to the cone; and because I
don't use additives, it just plates over these particles forming nodules; the use of additives slows down the plating on high spots, so the rest can
catch up. Well, that's if I understood right.
|
|
Mr. Wizard
International Hazard
   
Posts: 1042
Registered: 30-3-2003
Member Is Offline
Mood: No Mood
|
|
I read somewhere that Tarn-x was supposed to improve copper plating too. I was copper plating some 250 grain lead castings using a rotating plastic
drum in a copper sulfate solution. The rotation was to eliminate the dendrites or fingers that formed when the plating was stationary. I had good
results, but the copper had a flat reddish color to it. In an effort to improve the finish and smoothness I added some Tarn-x to the solution and got
a yellow cloud of crap in the tank, and eventually a dark precipitate in the bottom that ruined the plating and required a thorough cleaning. I'm
guessing the yellow was sulfur and the dark precipitate was CuS.
What results have you had with Tarn-x 12AT7? How did you use it? I happen to have some of the polyethylene glycol powder too.
Obviously copper deposits where the current flows. The current will flow the most where it is closest to the copper anode. That's why dendrites or
little fingers of copper would form on my castings, then continue to grow preferentially , as they formed the shortest path.
[Edited on 4-7-2010 by Mr. Wizard]
|
|
Aqua_Fortis_100%
Hazard to Others
 
Posts: 302
Registered: 24-12-2006
Location: Brazil
Member Is Offline
Mood: †
|
|
Very nice write up indeed..
Simple, cheap and giving good results..
Now, good SCs are much more affordable to home experimenter!
gnitseretni, I cant find these aluminium "bullet caps" on hardware stores.. There are similair products to this?
At leats I can try to make a massive Al cone similair of this with green sand box, if I could not find anything similair on market...
Anyway, thanks for that info!
"The secret of freedom lies in educating people, whereas the secret of tyranny is in keeping them ignorant."
|
|
gnitseretni
Hazard to Others
 
Posts: 282
Registered: 5-1-2007
Location: Colombia
Member Is Offline
Mood: No Mood
|
|
Not that I know off. They were cast aluminum, maybe you can cast your own?
|
|
quicksilver
International Hazard
   
Posts: 1820
Registered: 7-9-2005
Location: Inches from the keyboard....
Member Is Offline
Mood: ~-=SWINGS=-~
|
|
The idea is a damn good one because it's easy to build on. For "forms" aluminum or otherwise, you can look to chain-link fence "caps", decorative cups
or things of that nature. You only really need one "good" one with enough volume to allow trimming, etc. Ideally, you'd collect several in various
angles or you may choose to experiment with the geometry as a whole.
|
|
Contrabasso
Hazard to Others
 
Posts: 277
Registered: 2-4-2008
Member Is Offline
Mood: No Mood
|
|
Copper plates very nicely from a pyrophosphate solution. Stainless steel doesn't adhere plating very well, so some stainless articles may make good
formers and separate easily. Alternatively drill a fine hole at the point and temp bridge it with wax, then use an air line to blow the copper off.
Also a conductive release agent could be made from graphite and a grease or oil.
http://www.pfonline.com/articles/pfd0014.html
[Edited on 4-7-2010 by Contrabasso]
|
|
gnitseretni
Hazard to Others
 
Posts: 282
Registered: 5-1-2007
Location: Colombia
Member Is Offline
Mood: No Mood
|
|
Thanks for that link.
"low chloride will also cause treeing and nodulation of the deposit."
Uh, could someone pass the salt please
|
|
Contrabasso
Hazard to Others
 
Posts: 277
Registered: 2-4-2008
Member Is Offline
Mood: No Mood
|
|
Yes copper plates easily, with a little research an adequate plating coat can be applied without proprietory brighteners. I's prefer to plate using a
supply capable of a few amp though. Put the same amount of metal on in much less time. The method of getting the forming OFF is good too.
Added
A good coat of lacquer on the cathode, exposing only where you want metal to deposit may help the surface level etching. Or the former will start to
grip subsequent products.
[Edited on 5-7-2010 by Contrabasso]
|
|
12AX7
Post Harlot
   
Posts: 4803
Registered: 8-3-2005
Location: oscillating
Member Is Offline
Mood: informative
|
|
I only ever saw a white or blue precipitate when adding Tarn-X, which I presume arises from the soap. (Ingredients listed in MSDS are thiourea 5-7%,
sulfamic acid 3-5%, disodium cocoamphodipropionate <1%, methanol <0.05%, balance water.) There is no sulfur compound; perhaps you had some
Cu(I) in solution which precipitated?
A little chloride is usually also prescribed. This tends to form a white scum of CuCl on the anode, which probably causes it to dissolve evenly.
I've gotten reasonable results with Tarn-X. Instead of a knobby, crystalline deposit with poor bond, I got a strong, fairly flat, sparkling pink
deposit. Though still visible, the crystals were smaller and more dense.
Tim
|
|
gnitseretni
Hazard to Others
 
Posts: 282
Registered: 5-1-2007
Location: Colombia
Member Is Offline
Mood: No Mood
|
|
My anode is black. Which, according to that article Contrabasso linked to, is supposed to happen. So maybe that white scum is from using Tarn-X. I
suppose I'll find out, I got me some Tarn-X as well. If my math is right, 2 drops is all it takes.
|
|
quicksilver
International Hazard
   
Posts: 1820
Registered: 7-9-2005
Location: Inches from the keyboard....
Member Is Offline
Mood: ~-=SWINGS=-~
|
|
@ gnitseretni :
THANK YOU.
I received the liner you made and it's damn nice! I wish I had a decent camera that could show the idiosyncrasies of the design. It's slightly heavier
as it ascends to the cone tip and quite even (I didn't measure it finer than 1/100 via a caliper). It is really impressive and I believe it will
function better than most.
I appreciate you sending me the sample; but what's more, now that I've seen them I am quite impressed with the overall concept.
Edit:
I can say with confidence that this is a more than workable concept. It's a damn good one: a real quality & unique addition. I am not sure (until
I try making several of them) if they require an element of "technique" to get them looking as good as the sample, but the concept is worth learning.
There are quite a few people that say that a good cone liner is the majority of a SC. I don't know if I'd go that far but it IS extremely significant
and can really make a difference. TTBoMK an energetic materiel needs to exceed a VoD of 4K to make it a viable candidate for use in a SC. I know that
quite a few materials will punch a promising hole if attention is paid to detail of SC construction.
A fascinating thing would be to learn what is the SLOWEST materiel that could be made to pop a clean hole in a witness plate.
[Edited on 12-7-2010 by quicksilver]
|
|
gnitseretni
Hazard to Others
 
Posts: 282
Registered: 5-1-2007
Location: Colombia
Member Is Offline
Mood: No Mood
|
|
You're welcome, Quicksilver 
I finished electroforming another cone last night. Looks quite a bit better, still not without imperfections but far better than my previous cones.
http://img251.imageshack.us/img251/8513/41868127.jpg
http://img291.imageshack.us/img291/9675/31811618.jpg
http://img199.imageshack.us/img199/4364/79664855.jpg
http://img5.imageshack.us/img5/4412/85027335.jpg
Here's a picture while I was electroforming:
http://img3.imageshack.us/img3/7489/picture004je.jpg
(The alu cone is covered in copper due to the spattering of the first agitator.)
I changed the bath composition (included some additives) plus I added agitation. I made a mechanical agitator myself, but it wasn't working when I
checked on it the next morning. So I stopped electroforming and went to Petco and got me an aquarium air pump and continued electroforming.
I'll electroform another cone sometime, because that morning when I checked on it to find that my homemade agitator had quit on me, some "treeing" had
formed. I don't know if that was due to the agitator quitting on me or not. It could have stopped working anywhere in between 9 the night before and 7
that morning. So I'd like to try again and see what the result will be when using an agitator that doesn't quit on me 
But even if it doesn't improve, I can live with that.
|
|
Mr. Wizard
International Hazard
   
Posts: 1042
Registered: 30-3-2003
Member Is Offline
Mood: No Mood
|
|
I saw an example of electroforming using Cerrosafe or Wood's Metal alloy which will melt in hot water. In this example the original shape was cast
into plaster or some other easily used material. The Cerrosafe metal was cast into the mold to form a base for the Copper to be deposited upon, with a
connecting wire added. After the thickness was correct the whole item was placed in hot water and the Cerrosafe metal recovered as it flowed out of
the electroformed shell.
A quick search reveals it is $20 US for 1/2 pound to $25 a pound.
|
|
quicksilver
International Hazard
   
Posts: 1820
Registered: 7-9-2005
Location: Inches from the keyboard....
Member Is Offline
Mood: ~-=SWINGS=-~
|
|
You can get woods metal in many re-loading supplier places (on-line) but I think that IS just about the best price if I remember correctly.
You should see these liners: They are impressive. If the same technique were used with a variety of metals I am fairly comfortable they would turn out
OK. I'm sure you could add tin, etc. I also know that government surplus often has metal powders (tin, nickle, antimony, moly, Al, copper). There was
a place in town that sold same (in pound units) from a very large container.
|
|
gnitseretni
Hazard to Others
 
Posts: 282
Registered: 5-1-2007
Location: Colombia
Member Is Offline
Mood: No Mood
|
|
I tried plating onto one of those low melting point alloys, but it didn't work for me. The copper wouldn't stick at all, it would sink to the bottom
of the container. Lead is the problem. But I found some silver solder, lead free, that might just work.
|
|
quicksilver
International Hazard
   
Posts: 1820
Registered: 7-9-2005
Location: Inches from the keyboard....
Member Is Offline
Mood: ~-=SWINGS=-~
|
|
I was thinking that one of the most difficult hurdles to overcome is the possible need for a variety of "cone forms".
It may be that using other elemental materials in forms may yield results (but raising the cost & complexity). The need for a dielectric form that
would release the plated materiel has an element of complexity that can be challenging.
|
|
gnitseretni
Hazard to Others
 
Posts: 282
Registered: 5-1-2007
Location: Colombia
Member Is Offline
Mood: No Mood
|
|
Here's a bath composition for plating onto solder in case someone wants to try it.
http://www.larrylawson.net/plating.htm
|
|
Hennig Brand
International Hazard
   
Posts: 1284
Registered: 7-6-2009
Member Is Offline
Mood: No Mood
|
|
I originally posted this in the unconventional shaped charge thread. It was suggested to me that this was a more suitable place to post it, so here it
is.
The first picture shows some of the aluminum cone forms that were made on a lathe. The big one is 2", the next biggest is 1.25" then three are 3/4"
and one tiny 3/8" form. Sixty degrees was chosen for the cones angles. I am plating one 3/4" form right now in the very crude set up shown in the last
picture.
I plated a couple of 3/8" cones already because 3/8" was the only aluminum round stock I had in my junk pile. I noticed it was difficult to get the
cone off of the aluminum form without damaging the cone, the form, or both (at least for small cones). In the first picture is shown what I think will
be a good solution. The end of the aluminum form is drilled and tapped (the one in the plating bath is tapped for standard 1/4" coarse thread, which
is what the threads are on standard hardware store 1/4" threaded rod). The short piece of heavy gauge 3/4" copper plumbing pipe in the first picture
fits almost perfectly over the 3/4" aluminum form. The fender washer (large washer with small hole), goes over the other end of the short piece of
pipe and the steel nut is turned with a wrench to force the copper cone off the form with very even pressure and hopefully without damaging the form
or the liner. It is what is called a puller. It is possible to apply some serious pressure without damaging anything if done right.
Now I just need some short pieces of pipe that fit well over the other aluminum forms.
I am a big fan of this electroforming method to form copper cones. I just became aware of it about 2 weeks ago, but I already have a 2kg bag of copper
sulfate and some aluminum forms to play with.
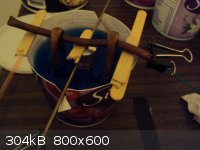
Almost forgot, the picture in the middle shows a variac which I use to adjust the voltage to the plating electrodes. There is a small linear DC power
supply (not shown) between it and the electrodes.
[Edited on 11-9-2011 by Hennig Brand]
|
|
gnitseretni
Hazard to Others
 
Posts: 282
Registered: 5-1-2007
Location: Colombia
Member Is Offline
Mood: No Mood
|
|
Nice forms. I like the method you described of getting the cones off the forms. Let us know how it works out.
|
|
Pages:
1
2
3 |