Pages:
1
..
64
65
66
67
68 |
Bert
Super Administrator
       
Posts: 2821
Registered: 12-3-2004
Member Is Offline
Mood: " I think we are all going to die. I think that love is an illusion. We are flawed, my darling".
|
|
Those who don't learn history are doomed to repeat it!
If anyone new is reading, who haven't been following this thread since the beginning? (Thread has been running 17 + years, now 65 pages long!)
You REALLY would benefit by at least skimming through this huge beast of a thread. Frankly, it OUGHT to get curated and a table of contents created.
NOTE: Click on quoted thread headers "originally posted by" , there are PICTURES you will want to see
For a start:
Electroplated copper cones, user neonpulse presented a workable solution, take a look here:
Quote: Originally posted by NeonPulse  | So i recently decided to try making another electroplated liner. For this process i filled a plastic funnel with car body filler and after it hardened
i shaped a tip on the end as it was flat. The angle of the funnel is around 55-57 degrees. The resin form was sanded with some 800 grit sandpaper
after this it was then coated with 3 nice even coats with a conductive silver paint. copper wire was threaded through 4 pre drilled holes on the base
of the form and it was plated as usual. the coating of copper onto the form was nice and even all around and there was no thin or bare spots. In a
previous experiment only one coat of the silver was applied but this produced poor results and a rather slow plating which was uneven in places. I
also think the plating bath attacked the coating before a layer of copper was plated to protect it so 3 coats is needed for a faster plating and
better coverage all round.The coating goes on very easily and any brush strokes with an artist's brush level out on drying leaving a nice even surface
to plate onto. Using this process opens up an avenue to create liners of many sizes and shapes. fluted, trumpet and bi-angled or stepped liners are
possible as long as you can form them out of the resin. i guess most materials that can be shaped conically or otherwise can be used (sealing porous
surfaces first) and there also is no real limit to the size that can be formed like with cutting metal forms on a lathe. The cone was very easy to
remove from the form and the paint stuck to the inside of the liner which is very easily removed with some acetone if it is a problem. The drawbacks
are the general cost of a liner as a whole unit, the silver paint is pretty expensive at $10 for a mere 3mls vial but it really does go a long way if
used sparingly. throw in the costs of the body filler, copper sulfate, Cu metal, acid and electricity to plate and you have a pretty expensive liner
to produce. I haven't any access to a lathe so spinning liners is out for me else i would certainly attempt it. 
|
Regarding hammered and/or other techniques in mechanically press formed cones, the good Dr. Liptakov (user name Laboratory of Liptakov) informed us of
an easily home made tooling setup and demonstrated a simple anneal/bash/anneal/bash technique beginning from a flattened scrap of common copper water
pipe:
Quote: Originally posted by Laboratory of Liptakov  | Needless to invent an aluminum insert. Needless to test copper plating. Needless to produce glass exploding shrapnel. Producing a steel mandrel with
an angle of 84 degrees. A 0.55 mm Cu sheet strength. Or 1 mm. Hammer. Wooden chopping block. Steel rectangle. Propane-butane torch. The annealing.
Production takes 10 minutes. No lathe. The pictorial compilation hopefully everyone will understand. Loaded: Cyklonan III. 25 grams. Density 1.2 g /
cc. Bar diameter 26 mm. Distanc 39 mm. Steel 20 mm.
LL
|
So. Go "back to the future". No flux capacitor required.
Rapopart’s Rules for critical commentary:
1. Attempt to re-express your target’s position so clearly, vividly and fairly that your target says: “Thanks, I wish I’d thought of putting it
that way.”
2. List any points of agreement (especially if they are not matters of general or widespread agreement).
3. Mention anything you have learned from your target.
4. Only then are you permitted to say so much as a word of rebuttal or criticism.
Anatol Rapoport was a Russian-born American mathematical psychologist (1911-2007).
|
|
Herr Haber
International Hazard
   
Posts: 1236
Registered: 29-1-2016
Member Is Offline
Mood: No Mood
|
|
Maybe I didnt understand the context but copper is not harder than steel !
https://www.metalsupermarkets.com/metal-hardness-testing-met...
The spirit of adventure was upon me. Having nitric acid and copper, I had only to learn what the words 'act upon' meant. - Ira Remsen
|
|
Microtek
National Hazard
  
Posts: 869
Registered: 23-9-2002
Member Is Offline
Mood: No Mood
|
|
Also, though the word 'steel' has been changed to aluminum, that really isn't a problem. The much greater thickness of the mold means that it is the
copper plate that deforms rather than the aluminum mold.
|
|
Fantasma4500
International Hazard
   
Posts: 1681
Registered: 12-12-2012
Location: Dysrope (aka europe)
Member Is Offline
Mood: dangerously practical
|
|
yes, agree- however with repetitions it will wear down, i tried to press a square brass plate and it carved a slight bit into my mold
maybe with a chamfering and super smooth grinding of the edges of the copper plate aluminium mold could be used- this is mostly just theoretical,
unless if someone was to cast it then steel is much more readily available than aluminium, at least where im from. even wood will wear down steel over
time
|
|
Bert
Super Administrator
       
Posts: 2821
Registered: 12-3-2004
Member Is Offline
Mood: " I think we are all going to die. I think that love is an illusion. We are flawed, my darling".
|
|
Quote: Originally posted by Fantasma4500  | if someone was to cast it then steel is much more readily available than aluminium, at least where im from. even wood will wear down steel over time
|
"Casting" steel is not a trivial thing, especially if you want it to be a uniform steel object without faults and having some desired level of hardnes
rather than cast iron when you're done. MP for steel would be around 1,300°C, AFAICR.
Brass is way harder than annealed copper, I'd avoid trying to press form most "brass" alloys. Additionally, on annealing brass with 10% zinc, you may
well vaporize some zinc if you're not careful.
A lower mp copper alloy which might suit an amateur casting forms for pressing copper with is called "gunmetal":
88% copper
8–10% tin
2–4% zinc
MP around 1,000°C. Lost wax would be do-able and for small forms, there are jewelry maker type MICROWAVE CRUCIBLES.
Rapopart’s Rules for critical commentary:
1. Attempt to re-express your target’s position so clearly, vividly and fairly that your target says: “Thanks, I wish I’d thought of putting it
that way.”
2. List any points of agreement (especially if they are not matters of general or widespread agreement).
3. Mention anything you have learned from your target.
4. Only then are you permitted to say so much as a word of rebuttal or criticism.
Anatol Rapoport was a Russian-born American mathematical psychologist (1911-2007).
|
|
Fantasma4500
International Hazard
   
Posts: 1681
Registered: 12-12-2012
Location: Dysrope (aka europe)
Member Is Offline
Mood: dangerously practical
|
|
oh, i meant it as in- steel as in solid steel rod is much more readily available. ive barely seen steel melted in amateur settings done right once-
the secret was that he used a decently built air-wood furnace and sealed the steel into clay
copper-aluminium alloy should also be doable, this site claims it melts at 548*C which just makes no sense in my world since aluminium is about 660*C
on its own?
https://www.americanelements.com/meltingpoint.html
aluminium wool is very neat for anyone wanting to cast, can be bought cheaply on wish, doesnt take up much heat and takes very high temperature
|
|
Microtek
National Hazard
  
Posts: 869
Registered: 23-9-2002
Member Is Offline
Mood: No Mood
|
|
I assume you mean alumina wool? I think casting is just about the least convenient way to prepare either the die or the liner itself.
I would prefer deep drawing, spinning, turning or electroforming (or CNC milling) over casting. If you go for turning or milling the liner directly,
consider making it from brass instead of pure copper (since brass is MUCH easier to machine than copper in my experience).
|
|
Bert
Super Administrator
       
Posts: 2821
Registered: 12-3-2004
Member Is Offline
Mood: " I think we are all going to die. I think that love is an illusion. We are flawed, my darling".
|
|
Copper is soft and acts STICKY. Wants to deform rather than cut, chips want to bond to cutting tool edges and screw things up.
In the old days , WHOLE COWS MILK was sometimes used as a machining lubricant for pure copper?! Mostly consisting of water, good cooling properties.
The milk fat acted a bit like what we now call "water soluble cutting oils". Bet it discolored the metal though.
[Edited on 2-22-2023 by Bert]
Rapopart’s Rules for critical commentary:
1. Attempt to re-express your target’s position so clearly, vividly and fairly that your target says: “Thanks, I wish I’d thought of putting it
that way.”
2. List any points of agreement (especially if they are not matters of general or widespread agreement).
3. Mention anything you have learned from your target.
4. Only then are you permitted to say so much as a word of rebuttal or criticism.
Anatol Rapoport was a Russian-born American mathematical psychologist (1911-2007).
|
|
Fantasma4500
International Hazard
   
Posts: 1681
Registered: 12-12-2012
Location: Dysrope (aka europe)
Member Is Offline
Mood: dangerously practical
|
|
this effect is also seen with zinc and aluminium, aluminium has the added issue that its oxide is extremely hard and despite the metal being so soft,
drilling and machining aluminium will effectively wear down whatever tool used, even tungsten carbide as both Al2O3 and tungsten carbide is a 9 in
mohs hardness
as for lubrication, boiling oil with sulfur can work, i have used bandsaw cutting fluid for spraying while drilling holes and works very well, a
suspension of water and sulfurized oil should do for anticorrosion, i have also used a water mix of glycol with some food dye in it, - just for my own
sake. sulfurized oils are probably not very good for you can i imagine there could be similar effect as sulfite preservatives upon exposure. cutting
fluid surely tastes like engine oil
looking into MSDS i find one claiming cutting fluid being composed of ethanolamine and triethylamine ANYHOW this is well-offtopic by now.
so lets conclude its ideal to have the die made of steel, machined, shouldnt take long to have a die machined manually, just turn the lathe at 45
degrees- or 60 if youre feeling lucky, and cut into a piece of round steel
|
|
PLSHY
Hazard to Self

Posts: 91
Registered: 30-7-2023
Member Is Offline
|
|
I found a very novel charge structure, the truncated supercharged charge, which can obtain about 15% higher penetration than the ordinary cone, I made
it, and plan to start it with 260mlEGDN , if you want to know more data and specific content, you can reply and ask me, if many people pay attention,
I will open a separate post
Attachment: trim.90069319-B185-4A8B-B8C1-E82B286AC412.MOV (5.1MB) This file has been downloaded 265 times
|
|
PLSHY
Hazard to Self

Posts: 91
Registered: 30-7-2023
Member Is Offline
|
|
After thinking about it, I decided to attach a structure diagram and related documents. The truncated material is tungsten plate with a thickness of
5mm. I will start it tomorrow, and I will attach detailed data after it is started.
https://doi.org/10.1016/j.dt.2022.09.017
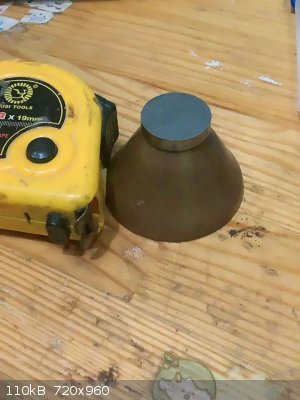
|
|
Microtek
National Hazard
  
Posts: 869
Registered: 23-9-2002
Member Is Offline
Mood: No Mood
|
|
Interesting. How did you produce the liner? Also, that is a lot of EGDN, please be careful of both accidental initiation and all the fragments that
such a hefty steel pipe will produce.
|
|
Cubane538
Harmless
Posts: 18
Registered: 30-7-2023
Member Is Offline
|
|
Hi guys,
I'm trying to make copper cone by electroforming on lead, it's going to be 32 hours since I started the cell, but it's seems to be not working!!
The layer of copper on lead cone is very thin...
I'm using 5v 700mA Samsung travel adaptor and 400ml copper sulphate solution. 60g copper sulphate dissolved in it. And 15 ml sulphuric acid for better
conduction.
I don't know why it's not forming copper layer!!
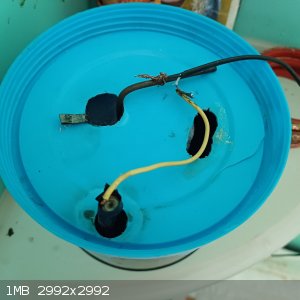
[Edited on 3-8-2023 by Cubane538]
[Edited on 3-8-2023 by Cubane538]
|
|
PLSHY
Hazard to Self

Posts: 91
Registered: 30-7-2023
Member Is Offline
|
|
I successfully booted it up yesterday with a 390g EGDN, unfortunately the phone didn't save the video due to the high temperature. I live in the
tropic, and yesterday's temperature reached above 35 degrees Celsius. My cover is composed of tungsten plates and copper adapters customized online.
Next, I will attach three pictures, which are the appearance of the copper adapters before processing, the damage effect, and detailed parameters.
It's a pity that the target I chose was too small, so the jet was missed, but it still caused 10cm of penetration. If there is no miss, I believe
that the penetration depth of more than 20cm can be achieved, and I will conduct a second experiment later. The standoff is 10cm, which is 1.8 times
the diameter.
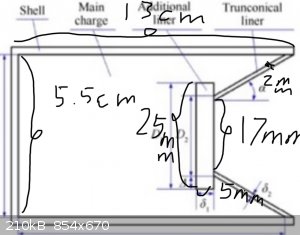
[Edited on 3-8-2023 by PLSHY]
|
|
underground
National Hazard
  
Posts: 702
Registered: 10-10-2013
Location: Europe
Member Is Offline
|
|
Quote: Originally posted by Cubane538  | Hi guys,
I'm trying to make copper cone by electroforming on lead, it's going to be 32 hours since I started the cell, but it's seems to be not working!!
The layer of copper on lead cone is very thin...
I'm using 5v 700mA Samsung travel adaptor and 400ml copper sulphate solution. 60g copper sulphate dissolved in it. And 15 ml sulphuric acid for better
conduction.
I don't know why it's not forming copper layer!!
[Edited on 3-8-2023 by Cubane538]
[Edited on 3-8-2023 by Cubane538] |
60g of CuSO4 is too little in my opinion. H2SO4 can not dissolve Cu so the only Cu you are going to plate is from the dissolved CuSO4
|
|
Cubane538
Harmless
Posts: 18
Registered: 30-7-2023
Member Is Offline
|
|
Quote: Originally posted by underground  | Quote: Originally posted by Cubane538  | Hi guys,
I'm trying to make copper cone by electroforming on lead, it's going to be 32 hours since I started the cell, but it's seems to be not working!!
The layer of copper on lead cone is very thin...
I'm using 5v 700mA Samsung travel adaptor and 400ml copper sulphate solution. 60g copper sulphate dissolved in it. And 15 ml sulphuric acid for better
conduction.
I don't know why it's not forming copper layer!!
[Edited on 3-8-2023 by Cubane538]
[Edited on 3-8-2023 by Cubane538] |
60g of CuSO4 is too little in my opinion. H2SO4 can not dissolve Cu so the only Cu you are going to plate is from the dissolved CuSO4
|
Yes you're right 60 gram is too less!
That's why I added 36 grams more copper sulphate and 10ml of sulphuric acid.
And now it seems to be the copper layer is forming but slowly!!
|
|
underground
National Hazard
  
Posts: 702
Registered: 10-10-2013
Location: Europe
Member Is Offline
|
|
You want the slow forming, the slower the better, also try to use a magnetic stirrer while plating for even better results.
|
|
Cubane538
Harmless
Posts: 18
Registered: 30-7-2023
Member Is Offline
|
|
Quote: Originally posted by underground  | You want the slow forming, the slower the better, also try to use a magnetic stirrer while plating for even better results. |
What is the best thickness of copper liner for shape charge?
|
|
dettoo456
Hazard to Others
 
Posts: 242
Registered: 12-9-2021
Member Is Offline
|
|
Shaped charge liners between 1.5 to 3mm thick are generally easy to form (machining wise) and perform well for most applications. Anything thicker
than that up to around 5mm will do better but they are progressively more expensive and difficult to produce. EFP’s are usually produced with
thicker liners.
|
|
Cubane538
Harmless
Posts: 18
Registered: 30-7-2023
Member Is Offline
|
|
Quote: Originally posted by dettoo456  | Shaped charge liners between 1.5 to 3mm thick are generally easy to form (machining wise) and perform well for most applications. Anything thicker
than that up to around 5mm will do better but they are progressively more expensive and difficult to produce. EFP’s are usually produced with
thicker liners.
|
I'm using electroforming method to make copper liner.
Will the more thick liner will give more penetration?
|
|
Microtek
National Hazard
  
Posts: 869
Registered: 23-9-2002
Member Is Offline
Mood: No Mood
|
|
The liner thickness should be about 1-1.5% of the diameter at the base of the cone, so the optimal thickness is dependent on how large a charge you
are making. It is also dependent on other parameters, but since you are going for a solid copper cone, those other parameters can be ignored.
|
|
MineMan
International Hazard
   
Posts: 1004
Registered: 29-3-2015
Member Is Offline
Mood: No Mood
|
|
Quote: Originally posted by PLSHY  | I successfully booted it up yesterday with a 390g EGDN, unfortunately the phone didn't save the video due to the high temperature. I live in the
tropic, and yesterday's temperature reached above 35 degrees Celsius. My cover is composed of tungsten plates and copper adapters customized online.
Next, I will attach three pictures, which are the appearance of the copper adapters before processing, the damage effect, and detailed parameters.
It's a pity that the target I chose was too small, so the jet was missed, but it still caused 10cm of penetration. If there is no miss, I believe
that the penetration depth of more than 20cm can be achieved, and I will conduct a second experiment later. The standoff is 10cm, which is 1.8 times
the diameter.
[Edited on 3-8-2023 by PLSHY] |
Nice! Looked like some sputtering there, according to the paper a clean entrance hole should be expected. Maybe your cap isn’t lined right. You
could also use far less EM. For oil perf charges they use about an ounce of EM for an ounce of liner
|
|
PLSHY
Hazard to Self

Posts: 91
Registered: 30-7-2023
Member Is Offline
|
|
stamping
|
|
PLSHY
Hazard to Self

Posts: 91
Registered: 30-7-2023
Member Is Offline
|
|
stamping
|
|
Microtek
National Hazard
  
Posts: 869
Registered: 23-9-2002
Member Is Offline
Mood: No Mood
|
|
Nice cone. How did you stamp it? Deep drawing?
|
|
Pages:
1
..
64
65
66
67
68 |