Pages:
1
..
4
5
6
7
8
..
10 |
Hennig Brand
International Hazard
   
Posts: 1284
Registered: 7-6-2009
Member Is Offline
Mood: No Mood
|
|
The sulfides are what are typically used though aren't they? From the little bit I have seen there has been a lot of trouble getting other reducers
and methods to work as easily or reliably as the sulfide ones. Using that sulfide solution seemed so simple and straight forward compared to
everything I have read about here and on the old Rogue Sci forum. It is worthwhile to experiment with alternatives though, that's for sure.
If the amount of sulfur contamination is very small is it still much of a problem? Is the sulfur hard to remove during recrystallization processes?
"A risk-free world is a very dull world, one from which we are apt to learn little of consequence." -Geerat Vermeij
|
|
Rosco Bodine
Banned
Posts: 6370
Registered: 29-9-2004
Member Is Offline
Mood: analytical
|
|
The references are obscure and I have been looking for more information. But the reaction using sulfide reduction does produce byproduct impurities
and it is an original or early method upon which there is likely to be possible improvement. The level of impurities ultimately in the DDNP and what
are the effects is unknown. It may or may not make any difference whether the reduction is done using sulfide or using another method.
Attachment: Page 45 Picramic Acid article Color_Trade_Journal_Vol_1.pdf (209kB) This file has been downloaded 933 times
Attachment: Pages from The Chemical Gazette.pdf (179kB) This file has been downloaded 749 times
The attachment for the Chemical Gazette article was giving me some difficulty as an attachment because the file name was too long. I have edited it
and reattached the article which is described more in my earlier post a couple of pages back in this thread linked here
http://www.sciencemadness.org/talk/viewthread.php?tid=433&am...
It seems to me based on the Gazette article and the German language article page 9 charts posted on the first page of the thread by Axt, that ferrous
sulfate could be used for the reduction of either ammonium or sodium picrate in aqueous solution, and that if the reduction was carried out in the
presence of iron filings, it would allow for a more concentrated reaction mixture. What should occur is that the ferrous sulfate would be oxidized to
ferric sulfate byproduct as it reduced the soluble picrate to soluble picramate, but the ferric sulfate would then react with the free elemental iron
and be reduced right back to the ferrous sulfate which would again react with the soluble picrate. So the ferrous sulfate would be a continually
regenerated reducing agent formed from the ferric salt in contact with elemental iron. Ferric Chloride would accomplish the same thing and the
presence of chloride may even be better if the chloride facilitates depolarization of the iron so it is in better contact with the solution that is
reacting. The iron filings I believe would ultimately be converted to the black oxide as an inert insoluble by product. Diluting and heating and
filtering the hot reaction mixture of the insoluble byproducts, and then acidifying should precipitate pure picramic acid on cooling. Zinc or
aluminum or magnesium metal filings or their amalgams may work equally well or better in the same general scheme for reduction. Probably a manganese
or copper salt could also work in similar way as the iron salt as a regenerable reducing agent being regenerated by contact with the iron or zinc or
aluminum or magnesium which would reduce the higher oxidation state of that salt to the lower oxidation state where it would react again reducing
unreacted picrate to picramate. The process described in the German language article attached by Axt on the first page stated that for a 6 hour
reaction the yield of picramate was 100% so the reaction should go to completion and the resulting picramic acid end product should be pure.
[Edited on 6-2-2014 by Rosco Bodine]
|
|
Hennig Brand
International Hazard
   
Posts: 1284
Registered: 7-6-2009
Member Is Offline
Mood: No Mood
|
|
I am not yet getting anywhere near 100% yields with the method I am using, but I believe my picramate is very pure given the yields of DDNP obtained
from it. A melting point could easily be taken, to determine purity, but my melting point apparatus is not close enough to get to for the next little
while.
The sulfur contamination issue made me remember something I forgot to point out earlier. During the hydrogen sulfide gas generation process there was
some sulfur sublimation and deposition going on. You can see it in the attached picture. There was no evidence that the sulfur made it past the cold
steel tube, however, as even after 1.5 hours the vinyl tubing between the steel tubing and the diffuser/bubbler was perfectly clear showing no signs
of deposited sulfur. Ambient temperature was about minus 200C, of course, which would have really helped keep the sulfur vapor from
traveling very far in the steel tube.
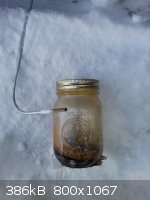
[Edited on 6-2-2014 by Hennig Brand]
"A risk-free world is a very dull world, one from which we are apt to learn little of consequence." -Geerat Vermeij
|
|
Rosco Bodine
Banned
Posts: 6370
Registered: 29-9-2004
Member Is Offline
Mood: analytical
|
|
One thing you can recognize from the early literature circa mid 19th century describing the sulfide reduction is that the picramic acid had not yet
been correctly identified structurally nor its formula been written correctly, nor had even the name picramic acid yet been designated for the
material as was done by Girard. Girard reviewed the technology and described his own method for avoiding the use of sulfide for the reduction, so it
would seem that it was a pursuit of an improved synthetic method which was reasonably a motivation for Girard who reasonably would not have been
striving to improve upon already achieved perfection. I don't know for certain but it just seems reasonable that Girard would have been describing
what was believed by himself to be an improvement to the means of making the compound picramic acid which he named. It is probably a simpler method
and produces a higher yield of purer product without having to deal with a toxic and unpleasant reagent which produces a less pure product by a more
difficult route.
|
|
Hennig Brand
International Hazard
   
Posts: 1284
Registered: 7-6-2009
Member Is Offline
Mood: No Mood
|
|
I can see how producing picramic acid by an alternate method would be important for Girard even if it wasn't a superior method. His method may still
be very good, or superior even, I don't know.
I am now curious as to how the military makes theirs. That would likely be very telling.
Not surprisingly I am having difficulty finding information about commercial processes for picramic acid and DDNP production. I found the information
below from the following website. Not sure if the information is reliable though, meaning these may not be the processes used industrially.
http://pubchem.ncbi.nlm.nih.gov/summary/summary.cgi?cid=4921...
"Use and Manufacturing
Methods of Manufacturing
•REDUCTION OF 2,4,6-TRINITROPHENOL WITH SODIUM HYDROSULFIDE
•Prepd from picric acid, concentrated NH4OH, & H2S followed by acetic acid neutralization of ammonium salt. Prepn of ammonium salt from picric
acid, aq NH3-soln, & ammonium sulfide."
I may do a little more digging. I would like to know more about commercial production.
[Edited on 7-2-2014 by Hennig Brand]
"A risk-free world is a very dull world, one from which we are apt to learn little of consequence." -Geerat Vermeij
|
|
Rosco Bodine
Banned
Posts: 6370
Registered: 29-9-2004
Member Is Offline
Mood: analytical
|
|
On page 1 fourth post up from the bottom of the page Axt
posted about the work of Lyons and Smith who reported yields of 100% using regenerable ferrous chloride derived from a catalytic amount of Ferric
Chloride and iron filings.
It is on page 9 of the pdf that Axt attached.
http://www.sciencemadness.org/talk/viewthread.php?tid=433&am...
http://www.sciencemadness.org/talk/files.php?pid=47358&a...
You can't do better than 100% yield and have to be doing something right for that to happen.
I have looked for any English language version of the paper which was about work done by American chemists at an American university, even though it
was published in a German journal. I am not finding any copublication of the article in English.
[Edited on 7-2-2014 by Rosco Bodine]
|
|
Hennig Brand
International Hazard
   
Posts: 1284
Registered: 7-6-2009
Member Is Offline
Mood: No Mood
|
|
The following came out of a college or university level lab manual. The lab manual has a series of hydrogen sulfide experiments. A pdf of the whole
manual is attached below as well.
"Experiment C. Reaction between H2S (g) and NaOH (aq). Hydrogen sulfide reacts readily with 6 M NaOH. The reaction is:
H2S(g) + NaOH(aq)-> NaHS(aq) + H2O(l)
1. Pour 25 mL 6 M NaOH into a 150 mL beaker. Use the H2S(g) that remains from Experiments A and B or prepare a fresh syringeful of H2S as described
above. It is unnecessary to wash the gas for this experiment.
2. Remove the latex syringe cap from the H2S-filled syringe, and suction a few millilitres of NaOH(aq) into the syringe. Hydrogen sulfide reacts
instantaneously with the NaOH(aq). The plunger may move rapidly inward and/or the NaOH solution will be drawn rapidly into the syringe. The reaction
is so rapid, it could be surprising. The beaker is used because the beaker walls will contain any splashed NaOH(aq). This solution can be slowly
discarded down the drain with large amounts of water. If possible, use a sink in the hood and wear gloves."
It seems I was making some wrong assumptions earlier in this thread. Sodium hydrosulfide is what I think is produced exclusively by bubbling hydrogen
sulfide into a sodium hydroxide solution, even though many webpages say that it is sodium sulfide. It is also nice to know that hydrogen sulfide is
converted almost instantly on contact with the sodium hydroxide solution. I am much less nervous to make sodium hydrosulfide solutions now. If made in
small quantities, done outside and using a little common sense the risks are manageable. However, one should probably arrange to be somewhere else
when the gas generator is producing. I used twice as much sodium hydroxide and water this time, because I wanted more sodium hydrosulfide and twice
the column height meant much greater contact time between the hydrogen sulfide and the sodium hydroxide solution (though it may not matter much).
Also attached is the first page of the section on Sodium Hydrosulfide from "The Encyclopedia of Chemical Technology". I just took a picture of it with
my phone and attached it as a jpg. I might get a better scan of the whole section later. From reading the sodium hydrosulfide and sodium sulfide
sections, bubbling hydrogen sulfide gas into a sodium hydroxide solution is the process used to make sodium hydrosulfide not sodium sulfide.
Attached is a picture of about 90mL of sodium hydrosulfide solution freshly prepared. It is a little cloudy this time which is different than last
time. A little sulphur vapor made it over into the solution maybe.
Attachment: H2S Hydrogen Sulfide Experiments.pdf (150kB) This file has been downloaded 1176 times
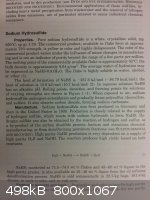
The sodium hydroxide solution, which H2S was bubbled into, was about 80 mL and contained 8g of sodium hydroxide (about a 2.5 molar solution of sodium
hydroxide).
[Edited on 18-2-2014 by Hennig Brand]
"A risk-free world is a very dull world, one from which we are apt to learn little of consequence." -Geerat Vermeij
|
|
Rosco Bodine
Banned
Posts: 6370
Registered: 29-9-2004
Member Is Offline
Mood: analytical
|
|
If you want to go with the sulfide reduction method then there is some useful solubility and reaction data in US2346550 Production of concentrated
sodium hydrosulphide solutions
Attachment: US2346550 Production of concentrated sodium hydrosulphide solutions.pdf (725kB) This file has been downloaded 808 times
|
|
Hennig Brand
International Hazard
   
Posts: 1284
Registered: 7-6-2009
Member Is Offline
Mood: No Mood
|
|
Thanks, so according to that patent sodium sulfide is formed first and then converted to sodium hydrosulfide. Other methods may be better than the
sulfide reduction method, it's just that I am familiar with it now and I know it works.
Also, I hope I didn't trivialize the dangers associated hydrogen sulfide gas in my last post. Hydrogen sulfide gas can be handled with reasonable
safety, but it is a very serious poison and in very small doses. The last two times and made the sulfide solution, I was very careful, however, at the
end when disassembling the apparatus I ended up breathing in a small amount of the diluted gas. It was just enough to make my throat a bit soar and my
eyes irritated and make me feel a little off. It takes several days for the symptoms to completely go away too. I contacted a safety equipment company
in my area and a gas mask with cartridges for H2S can be had for less than $50 (half mask), or about $100 for full face coverage. The gas masks are
rated "escape", which means don't hang out in a poison gas area, but it would still provide some protection when disassembling the H2S generator
apparatus.
The effects on my body of inhaling even tiny amounts of diluted H2S really emphasize how serious a poison H2S really is.
"A risk-free world is a very dull world, one from which we are apt to learn little of consequence." -Geerat Vermeij
|
|
roXefeller
Hazard to Others
 
Posts: 463
Registered: 9-9-2013
Location: 13 Colonies
Member Is Offline
Mood: 220 221 whatever it takes
|
|
Something they teach at fire academy is olfactory fatigue. A strong dose of H2S can actually overwhelm your senses. Such that you go back into the
plume thinking it has cleared. But really you'll just die cause you can't smell it.
|
|
papaya
National Hazard
  
Posts: 615
Registered: 4-4-2013
Member Is Offline
Mood: reactive
|
|
Hennig, why do you generate H2S first and then dissolve it into base, instead of directly dissolving sulfur in NaOH? Is it because you get purer
hydrosulfide instead of polysulfides+thiosulfate mixture?
|
|
Hennig Brand
International Hazard
   
Posts: 1284
Registered: 7-6-2009
Member Is Offline
Mood: No Mood
|
|
Ideas For Reducing The Poisoning Risk Associated With Hydrogen Sulfide Generation
Apart from dealing with toxic H2S, the process is very straightforward giving high yields and, yes, a very pure product. From what I have
read it seemed like the best option to obtain a high purity sulfide reducing agent. Hydrogen sulfide is extremely poisonous, though, and I won't be
doing this again until I have found or developed a little better process. I still have a bit of a sore throat, and feel a little unhealthy, and that
is from fairly mild exposure close to 2 days ago. Very dangerous stuff indeed!
In the absence of a good fume hood a strong electrical fan could be placed just over the generator as it was disassembled. What would be even better
would be to have the type of blower fan that connects to large flexible air hose so that the H2S gas could be lead safely away from the
work area during disassembly. With a decent fan, and maybe also a H2S rated gas mask, disassembling the gas generator would be much safer.
Ok, I think I have a simple yet effective solution to the poisoning by gas generator disassembly problem. Hydrogen sulfide is fairly soluble in water
(ca. 0.12 mol/l or 4.1g/l at 200C & ca.0.15 mol/l or 5.1 g/l at 100C). Values taken from "The solubility of gases in
distilled water and seawater-V. Hydrogen Sulfide", by A.A. Douabul and J.P.Riley
The volume of hydrogen sulfide in the glass mason jar used was about 450mL (or less) and was not under pressure. Using the simple 22.4 L/mol rule for
ideal gases at STP, it was found that the mason jar could contain as much as 0.02 moles or about 0.68g of H2S. Given that 170 mL of water
at 200C can absorb that amount of hydrogen sulfide, a 2 gallon bucket of cool water would absorb it easily. The idea was to let the reactor
cool undisturbed and then immerse it in a bucket of water. Two bricks could be placed on the bottom of the bucket, with space between them. The
generator vessel (mason jar) could be flipped upside down under water before the rubber stopper or top was removed and then placed over the two bricks
so that the water could contact the gas. Another brick or dense object would need to be placed over the top of the jar to hold it down. A little
sodium hydroxide could be added to the bucket of water beforehand if converting the hydrogen sulfide to sodium (hydro)sulfide seemed advantageous. A
little sodium hydroxide in the water would greatly increase the speed of absorbtion.
The process could maybe be improved, but I think the general idea is sound and would greatly increase safety. I guess a person could hold the jar
under a sprinkler system when it was opened. Or even better a sprinkler system
that was spraying sodium hydroxide solution (ouch!) Shouldn't make jokes, but I couldn't resist.
The smartest thing, now that I am starting to fully understand the seriousness of the poison issue, would be to use a much smaller vessel so that a
much smaller quantity of poison gas would be left in the vessel after production was finished. The reason a larger one was used was because it put the
screw top with stopper well away from the heat source below. It also allowed most of the sublimed sulfur to deposit in the jar so that it didn't end
up in the delivery tube. The 16 oz size is also the most common for a mason jar (I think).
Ok, I think this is the best idea yet. The top of the mason jar, or rubber stopper, could have installed a small hose barb the size that is needed to
attach an aquarium pump air line. This would either have to have a small valve or some other way of keeping it closed during the generation process
and be safely opened after generation. When gas production is complete, simply attach an aquarium air pump and pump air into the reactor which will
dilute and carry (or force) the H2S out of the generator and through the bubbler where it is safely absorbed. It might be a good idea to
use a fresh sodium hydroxide solution since the one used during generation should be very saturated or close to it and therefore have less absorbtion
ability. Also pumping air (oxygen) into the prepared sodium hydrosulfide solution will convert some of the sodium hydrosulfide to polysulfides, which
is also undesirable.
[Edited on 20-2-2014 by Hennig Brand]
"A risk-free world is a very dull world, one from which we are apt to learn little of consequence." -Geerat Vermeij
|
|
Hennig Brand
International Hazard
   
Posts: 1284
Registered: 7-6-2009
Member Is Offline
Mood: No Mood
|
|
H2S Hydrogen Sulfide Toxicity Information
Here is a link and two pdfs which provide very good information regarding the poisoning dangers associated with hydrogen sulfide gas. The link is for
a good medical information page regarding hydrogen sulfide toxicity.
http://emedicine.medscape.com/article/815139-overview
Attachment: Hydrogen Sulfide Hazardous Substance Fact Sheet.pdf (79kB) This file has been downloaded 3557 times
Attachment: Hydrogen Sulfide Workplace Health and Safety Bulletin.pdf (187kB) This file has been downloaded 2257 times
There was enough H2S in that mason jar to potentially kill me, which is a very sobering thought.
[Edited on 19-2-2014 by Hennig Brand]
"A risk-free world is a very dull world, one from which we are apt to learn little of consequence." -Geerat Vermeij
|
|
Hennig Brand
International Hazard
   
Posts: 1284
Registered: 7-6-2009
Member Is Offline
Mood: No Mood
|
|
I drew a little diagram to illustrate the concept from the last hydrogen sulfide generator idea above. A check valve wouldn't have to be used, but it
would be one way of allowing the process to be operated completely remotely. In fact rather than aerate the precious sodium hydrosulfide solution, I
would probably just collect the solution from the graduated cylinder and then retire to a safe location before turning on the pump and just letting it
vent to the atmosphere. As long as it was done outside and there were no people or animals close by it shouldn't be a problem.
Basic diagram is attached.
Attachment: Hydrogen Sulfide Generation System.pdf (64kB) This file has been downloaded 830 times
"A risk-free world is a very dull world, one from which we are apt to learn little of consequence." -Geerat Vermeij
|
|
roXefeller
Hazard to Others
 
Posts: 463
Registered: 9-9-2013
Location: 13 Colonies
Member Is Offline
Mood: 220 221 whatever it takes
|
|
I think the last time I bought an aquarium pump it came with a check valve intended to keep water from electricity. With this inline with the barb
connection, you could leave that configuration from the beginning and power on the pump remotely after swapping jars.
|
|
Hennig Brand
International Hazard
   
Posts: 1284
Registered: 7-6-2009
Member Is Offline
Mood: No Mood
|
|
Before doing the system flush, putting the bubbler in some sodium hydroxide solution or even plain water would be a good idea if for no other reason
than to provide a visual indication that the pump is functioning properly and that the system is actually being flushed out. Of course a little sodium
hydroxide in the water will greatly increase absorption and it doesn't have to be high purity sodium hydroxide either in this case.
"A risk-free world is a very dull world, one from which we are apt to learn little of consequence." -Geerat Vermeij
|
|
Hennig Brand
International Hazard
   
Posts: 1284
Registered: 7-6-2009
Member Is Offline
Mood: No Mood
|
|
Picric Acid Solubility in Methanol-Water Mixtures
Attached is a jpg of a snip-it from a journal article regarding solubility of picric acid in various solvents. The article title is, "The solubility
of Picric Acid in Mixed Solvents Part I. Water-Alcohol and Water-Acetone Mixtures".
The table should serve as a guide when trying to decide how much methanol to use, if the method involving methanol is used.
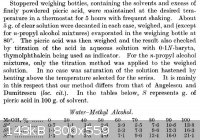
[Edited on 23-3-2014 by Hennig Brand]
"A risk-free world is a very dull world, one from which we are apt to learn little of consequence." -Geerat Vermeij
|
|
Rosco Bodine
Banned
Posts: 6370
Registered: 29-9-2004
Member Is Offline
Mood: analytical
|
|
If you have the entire journal article please post the pdf. Thanks.
I have speculated it may be possible to form a lead styphnate / lead picrate compound salt by treatment of a suspension of basic lead styphnate with
picric acid and something like a moist hot methanol or acetone solution of picric acid added to a like solvent for suspension of the basic lead
styphnate could work for this, if such a double salt is possible.
|
|
Hennig Brand
International Hazard
   
Posts: 1284
Registered: 7-6-2009
Member Is Offline
Mood: No Mood
|
|
The Solubility of Picric Acid in Mixed Solvents. Part I. Water-Alcohol and Water-Acetone Mixtures.
By James Cooper Duff and Edwin John Bills.
Six pages: three in the first file and three in the second.
Edit:
Since you have merged and reduced the two files I deleted the two oversized segments.
[Edited on 24-3-2014 by Hennig Brand]
"A risk-free world is a very dull world, one from which we are apt to learn little of consequence." -Geerat Vermeij
|
|
Rosco Bodine
Banned
Posts: 6370
Registered: 29-9-2004
Member Is Offline
Mood: analytical
|
|
Here is a merged and reduced file size
The Solubility of Picric Acid in Mixed Solvents - Part I Water-Alcohol and Water-Acetone Mixtures
Attachment: Solubility of Picric Acid in Mixed Solvents - Part I Water-Alcohol and Water-Acetone Mixtures.pdf (102kB) This file has been downloaded 2007 times
|
|
roXefeller
Hazard to Others
 
Posts: 463
Registered: 9-9-2013
Location: 13 Colonies
Member Is Offline
Mood: 220 221 whatever it takes
|
|
Did you find that a better reclamation was achieved from the dissolved picramic acid by using the MeOH/water solvent? It seems like it would be easy
to precipitate by water addition. I found horrible yields of 40-50% during this reduction and I suspect it was from the red solvent that I couldn't
precipitate more from.
|
|
Hennig Brand
International Hazard
   
Posts: 1284
Registered: 7-6-2009
Member Is Offline
Mood: No Mood
|
|
Yeah, I don't have the mono-reduction process all figured out yet either. I have had yields ranging from 50-80% and usually I have been for the most
part unsure why I got the yield I got which likely means as usual I am not being careful enough with the quantities used and to control the reaction
conditions.
Remember when we discussed the fact that when forming sodium hydrosulfide there would be sodium hydroxide left in solution if not enough hydrogen
sulfide gas was bubbled through. We were under the impression that it probably wouldn't matter that much if a little extra sodium hydroxide was
present in the reduction reaction mixture. After more carefully reading the Hodgson and Ward paper, on mono-reduction of picric acid, it is clear that
their results indicate that we were wrong and that increases in alkalinity results in formation of larger and larger quantities of sulfide dyes. I
have noticed that my best yields were obtained when I used a rather large excess of methanol (100mL for a 5g picric acid reduction) because at the
time I wasn't sure how much to use, and also no excess of sodium hydroxide was added to the reaction mixture. That higher yield of picramic acid (79%)
was also obtained using the first batch of sodium hydrosulfide solution prepared, which I believe had essentially no sodium hydroxide contamination.
The alkalinity of the reaction mixture would have been quite low. The last sodium hydrosulfide solution I made the generator stopped producing earlier
than I wanted and I believe there wasn't as high a conversion as the first time around. The color of the sodium (hydro) sulfide solution was much less
dark yellow the second time around and seemed to have less reducing power per unit volume during the reduction process. I have been using this less
concentrated sodium hydrosulfide solution, and a slight excess of sodium hydroxide as well, for the last few reductions and I have been getting
approximately 50% yields. Using methanol and not water as well as keeping the alkalinity low in the mono-reduction reaction mixture would appear to be
vital for obtaining high yields of picramic acid by this method. Sulfide dye by-product formation is increased with increasing alkalinity of the
reduction reaction mixture.
Something else to take note of, according to the above authors, picramic acid when subjected to aqueous sodium sulfide in the presence of sodium
hydroxide, at 50-600C, does not produce any sulfide dye.
There is a lot of useful information in that paper, which is attached earlier in this thread. I only gave it a quick run through before, because I was
so focused on experimenting with the DDNP end product. It looks like yields in the high 80s could be easily obtained if quantities and reaction
conditions were carefully controlled (especially alkalinity).
[Edited on 25-3-2014 by Hennig Brand]
"A risk-free world is a very dull world, one from which we are apt to learn little of consequence." -Geerat Vermeij
|
|
Rosco Bodine
Banned
Posts: 6370
Registered: 29-9-2004
Member Is Offline
Mood: analytical
|
|
The purity of the picramic acid used as the precursor for production of the DDNP could be important. It is likely that higher yields of the picramic
acid may be obtained with less work using the reduction by soluble ferrous compounds described early in the thread. The expected byproduct Fe3O4 and
any unreacted iron filings would be magnetic, and probably dense also which should facilitate separation by decantation and filtering of the picramate
value soluble in hot liquid. Which picramate is most soluble in a hot reaction mixture I do not know but the soluble picramate reportedly will not
react with soluble iron to precipitate a ferrous or ferric picramate as complication. Ammonium picramate would seem to be a good candidate for a
ferrous reduction scheme. Or there is a reduction scheme reported to produce a quantitative yield of picramic acid that is found early in the thread.
This would seem to be the first place to go looking for an alternative to use of sulfur for a reductant. If a higher yield reduction is not desired
then the reduction method reportedly producing a 100% yield of the picramic acid should of course be avoided.
|
|
Hennig Brand
International Hazard
   
Posts: 1284
Registered: 7-6-2009
Member Is Offline
Mood: No Mood
|
|
There are other methods, maybe some of them even better than the sulfide ones. Right now I am familiar with the one I am using, and there is a fair
bit of information in the literature about it, which is an obvious advantage at least for the short term. I feel that 90%, or close to 90% yields can
be easily produced by the sulfide method. I don't believe that the picramic acid produced is defective in anyway and I also believe that it can be
purified at more than one point along the way to DDNP, and after, if desired.
Once I have mastered this process I will maybe look into the others. Honestly, if I could easily get 90% yields of picramic acid, for the quantities I
use, I would be very happy.
"A risk-free world is a very dull world, one from which we are apt to learn little of consequence." -Geerat Vermeij
|
|
Rosco Bodine
Banned
Posts: 6370
Registered: 29-9-2004
Member Is Offline
Mood: analytical
|
|
Ferrous sulfate is cheap and safe.
9 moles FeSO4 solution and 18 moles NH4HCO3 or NH4OH or perhaps just use NaOH solution added separately and simultaneously in a parallel proportional
molar addition with stirring per mole of warm 30C sodium picrate solution should be about right for the reduction, with subsequent raising to maybe
80C and decanting and filtering of the hot solution, and acidifying to slight acidity and near complete decolorizing of the solution to precipitate
the only slightly soluble free picramic acid. The picramates are color dyes so the endpoint is visual on the acidification. I better check my
stoichiometry because I could be off and just did this one in my head. Don't bother checking the literature because it probably isn't there. 
The strategy that would be best I think is to calculate a drip rate for the ferrous sulfate into the slightly basic sodium picrate solution and then
make the additions of ammonium bicarbonate as solid sprinkled into the stirred mixture at a rate that stays slightly ahead of the ferrous sulfate to
keep the reaction mixture slightly basic. Similarly if using a liquid base the additions of base should lead by a small amount the ferrous sulfate
addition in order to keep the reaction system alkaline. Whether magnetic stirring may be good here or not is unknown since the byproduct Fe3O4 is
going to be magnetic. The magnetic interaction could be helpful or interfering, but my best guess it could be helpful and may present no issue.
[Edited on 25-3-2014 by Rosco Bodine]
|
|
Pages:
1
..
4
5
6
7
8
..
10 |