Pages:
1
2
3
4 |
Melgar
Anti-Spam Agent
   
Posts: 2004
Registered: 23-2-2010
Location: Connecticut
Member Is Offline
Mood: Estrified
|
|
How practical would it be to drive the stirrer with a belt? That way, you could use any old cheap, high-speed DC motor to drive it, just by using a
high gear ratio, and place the motor to the side, where it won't be in any danger of overheating or being affected by the magnetic field of the
permanent magnet? I mean, if the goal is low cost, you can't do much better than that.
|
|
Sulaiman
International Hazard
   
Posts: 3698
Registered: 8-2-2015
Location: 3rd rock from the sun
Member Is Offline
|
|
very practical.
I have repaired famous brand multi-position hotplate-stirrers that used rubber belts, one motor to turn up to 8 stirrers.
CAUTION : Hobby Chemist, not Professional or even Amateur
|
|
Fulmen
International Hazard
   
Posts: 1718
Registered: 24-9-2005
Member Is Offline
Mood: Bored
|
|
Mux: I see your point, although as kmno4 showed it can be done quite simple. At lest test this configuration before making a decision, I have a
suspicion it could improve performance noticeably. Wether you use this for increased torque or reduced power consumption is up to you, but it just
might put this in the range where a simple stepper driver would work. I know I'm fixated on these, but when one looks at cost, simplicity and
availability it's really hard to ignore that solution.
We're not banging rocks together here. We know how to put a man back together.
|
|
mux
Harmless
Posts: 31
Registered: 11-12-2016
Member Is Offline
Mood: No Mood
|
|
Quote: Originally posted by Fulmen  | (...) it might put this in the range where a simple stepper driver would work. I know I'm fixated on these, but when one looks at cost, simplicity and
availability it's really hard to ignore that solution. |
Well, it's already well within the range of stepper drivers, because I'm already getting sufficient torque without the pointy bits with A4983's. So
you're already vindicated. However, I have to stress that the proof of concept stage is very far removed from appliance-like 'it just works'. My
comments aren't meant to shoot down helpful suggestions, I just want to immediately name pros and cons so people know what I'm aiming for. For
instance:
Quote: Originally posted by Melgar  | How practical would it be to drive the stirrer with a belt? That way, you could use any old cheap, high-speed DC motor to drive it, just by using a
high gear ratio, and place the motor to the side, where it won't be in any danger of overheating or being affected by the magnetic field of the
permanent magnet? I mean, if the goal is low cost, you can't do much better than that. |
That belt is more temperature sensitive than the motor, but that's not the sensitivity issue here! I should clarify more because the motor suggestion
keeps coming back in one way or another.
Motors can be really cheap - under a dollar a piece including shipping from eBay. Incredible, really. Unfortunately, you get what you pay for. Cheap
motors have either bushings or really loose-tolerance bearings, which means as they rotate, they'll just rattle themselves loose over time. As torque
scales with current, at high current (and thus high torque, e.g. at low RPM) you'll generally burn through the enamel of the windings. Brushed motors
spark and erode over time. Basically: it'll work just fine for a bit, but it's bad design practice to fit a high reliability instrument with this kind
of motor.
Also, these motors generally have plastic backs (low melting temperature) and low Curie temperature laminations. What do you think the sprocket or
belt guide is made of? Nylon, crimped onto the shaft. Even if it's actively cooled, things can still easily get up to the Tg of plastics (70-80C) when
the hot plate is at 500C. After a few hundred cycles, that plastic will slip on the shaft. Or you need active cooling, meaning a fan, meaning the fan
will eventually fail because that's what fans do, also meaning you get dust inside everywhere.
So what do you need? You need a motor with decent torque at low speed, a decent speed range, that keeps cool at low speeds, no brushes that wear out
or really long-lived brushes, a proper thrust bearing in the back and a decent tolerance regular ball bearing in the front and no overly temperature.
These, unfortunately, are not cheap. Think ~$10, maybe even more at the quantities we're using here. And you'll likely have to order it custom (there
are standardized ways to designate motors, so you can ostensibly make it second supplier that way).
Four or six ferrite-cored inductors cost ~$0.50. The driver chip is another $2. No thermal issues (Tc of ferrite is well over the melting point of the
solder used to connect them up), no longevity issues, no supply issues and certainly cheaper than a quality motor. And it can be manufactured in an
automated way, no hand assembly of moving mechanical parts. An electrical engineer's wet dream.
|
|
Melgar
Anti-Spam Agent
   
Posts: 2004
Registered: 23-2-2010
Location: Connecticut
Member Is Offline
Mood: Estrified
|
|
Quote: Originally posted by Sulaiman  | very practical.
I have repaired famous brand multi-position hotplate-stirrers that used rubber belts, one motor to turn up to 8 stirrers. |
Interesting. Considering that ink jet printers typically have at least three DC motors in them, and several belts as well, the only thing that would
need to be purchased would be the second wheel, and most likely, some bearings. Skateboard bearings are usually very high quality for the price, so
assuming someone can find a discarded ink jet printer, (in my experience, not hard to find at all) the rest would be easy to source. And, like you
say, you can run multiple stirrers from a single motor.
|
|
Melgar
Anti-Spam Agent
   
Posts: 2004
Registered: 23-2-2010
Location: Connecticut
Member Is Offline
Mood: Estrified
|
|
Quote: Originally posted by mux  |
That belt is more temperature sensitive than the motor, but that's not the sensitivity issue here! I should clarify more because the motor suggestion
keeps coming back in one way or another. |
Well, considering that every magnetic stirrer I've ever seen or used has been motor-driven, that's to be expected. The belt and second wheel could be
easily shielded with, say, aluminum, possibly coated with furnace cement or plaster, if that became an issue. Then you'd have only the shaft and
magnet protruding through the shielding. The shaft could be stainless steel, which has really low thermal conductivity for a metal, and is probably
the most commonly-used material for shafts at this scale anyway.
Quote: | Motors can be really cheap - under a dollar a piece including shipping from eBay. Incredible, really. Unfortunately, you get what you pay for. Cheap
motors have either bushings or really loose-tolerance bearings, which means as they rotate, they'll just rattle themselves loose over time. As torque
scales with current, at high current (and thus high torque, e.g. at low RPM) you'll generally burn through the enamel of the windings. Brushed motors
spark and erode over time. Basically: it'll work just fine for a bit, but it's bad design practice to fit a high reliability instrument with this kind
of motor. |
You know, sometimes I feel like an idiot on these forums, since a lot of y'all were chemistry majors and I was a mechanical engineering major. But
you're in my wheelhouse now, and seem to have totally missed my point regarding motors. That being, you can rotate a shaft at lower speeds by driving
it with a belt, using a very small wheel on the motor, and a much larger wheel on the shaft you're trying to rotate. That way, the motor can spin at
higher speed and lower torque, thus avoiding the sort of coil burnout you're referring to.
Quote: | Also, these motors generally have plastic backs (low melting temperature) and low Curie temperature laminations. What do you think the sprocket or
belt guide is made of? Nylon, crimped onto the shaft. Even if it's actively cooled, things can still easily get up to the Tg of plastics (70-80C) when
the hot plate is at 500C. After a few hundred cycles, that plastic will slip on the shaft. Or you need active cooling, meaning a fan, meaning the fan
will eventually fail because that's what fans do, also meaning you get dust inside everywhere. |
And everything will eventually die with the heat death of the universe. I don't see your point. And you apparently failed to see mine too, since one
of the other major advantages of using a belt drive would be that you can drive the magnet from a short distance away, where temperatures are much
lower.
Quote: | So what do you need? You need a motor with decent torque at low speed, a decent speed range, that keeps cool at low speeds, no brushes that wear out
or really long-lived brushes, a proper thrust bearing in the back and a decent tolerance regular ball bearing in the front and no overly temperature.
These, unfortunately, are not cheap. Think ~$10, maybe even more at the quantities we're using here. And you'll likely have to order it custom (there
are standardized ways to designate motors, so you can ostensibly make it second supplier that way). |
Uh, no. I can virtually always find DC motors for free when I look for them, and in all the projects I've ever built, I've never had one burn out
that I didn't run with the expressed purpose of burning it out. (ie, measuring what factors are indicative of a motor about to burn out.) And even
these motors were surprisingly difficult to burn out, even when packed in fiberglass insulation, with a mixture of sandblasting grit and sugar poured
into their cases. We've come a long way since the days of Michael Faraday, and even cheap DC motors can be surprisingly resilient.
Quote: | Four or six ferrite-cored inductors cost ~$0.50. The driver chip is another $2. No thermal issues (Tc of ferrite is well over the melting point of the
solder used to connect them up), no longevity issues, no supply issues and certainly cheaper than a quality motor. And it can be manufactured in an
automated way, no hand assembly of moving mechanical parts. |
How many transistors do you think are on that chip? What happens if one of them fails? How likely is it that you did your calculations are
wrong and the voltage spike from shutting off the inductors fries your board? Electrical failures are at least as common as mechanical ones, and much
more difficult to see coming.
Quote: | An electrical engineer's wet dream. |
Hence, the reason that mechanical devices tend to be designed by mechanical engineers.
|
|
mux
Harmless
Posts: 31
Registered: 11-12-2016
Member Is Offline
Mood: No Mood
|
|
It seems like you're missing my point, possibly on purpose (because I refute your refutations in the text itself!). This topic is not to bicker at
each other, this thread is here to help each other primarily.
But, to go into the as-yet partially unaddressed issues. First of all - salvaged parts are not an option here; this is a uniform design, I can't
depend on people having specific salvaged parts.
Second - I'm not disputing that motors can work. They clearly can, because a large part of stirrers already use them. It's just that I don't see
sufficiently cheap motors doing the job. Anything that would work is pretty expensive - too expensive to fit this project's budget, given that I am
shooting for a certain degree of reliability and performance. We're not talking qualitative statements here, we're purely talking about quantitatively
limiting design space.
Look inside any reasonable quality hotplate stirrer and look at the motor inside. It's not a cheap 6V DC no-name motor. It's a brand name motor with
proper bearings and fairly high power rating. You don't find those for nearly the budget I'm on. And going with a cheaper motor means you need to add
other stuff to account for the points on which the cheaper motors have skimped, or adding little milled motor holders to account for differences in
sizing of motors as suppliers change. This, again, is not going to be cheap.
Anything can be engineered, you can solve any nail-problem with any hammer-solution, it's just that finding the optimum is the true art.
I've looked into buying motors for this job. I have not found anything. Can you find something better? I'm specifically looking for:
- Sub-$4 complete assembly
- At least two long-term suppliers
- near enough to 0.1Nm torque at 10-2000RPM (0.05Nm is okay, 0.01 is too weak)
- Hard-brushed or non-brushed (i.e. 5000+ h lifespan)
- Can be side-loaded and axially loaded (order single digit N)
- Has a datasheet
[Edited on 25-12-2016 by mux]
[Edited on 25-12-2016 by mux]
|
|
Fulmen
International Hazard
   
Posts: 1718
Registered: 24-9-2005
Member Is Offline
Mood: Bored
|
|
I'm with mux here, for a build like this the motor-less design is perfect. The drivers are a few dollars and the inductors can be wound using very
simple equipment. Once you start dealing with motors and belts you quickly end up with a more complex support structure as well.
Mux: You could try simply bolting the coils to a steel plate (turning them into two horse shoe magnets), even without the "arrows" this should
increase field strength. Using steel bolts in stead of ferrite cores shouldn't affect the performance as long as you design the coils for it.
[Edited on 25-12-16 by Fulmen]
We're not banging rocks together here. We know how to put a man back together.
|
|
Sulaiman
International Hazard
   
Posts: 3698
Registered: 8-2-2015
Location: 3rd rock from the sun
Member Is Offline
|
|
if possible do not use thick steel plates or large steel nuts/bolts as part of an a.c. magnetic circuit as eddy-current heating will be a problem
(3000 rpm= 50 Hz etc.)
air, powdered or thin strip steel etc are prefered.
CAUTION : Hobby Chemist, not Professional or even Amateur
|
|
Melgar
Anti-Spam Agent
   
Posts: 2004
Registered: 23-2-2010
Location: Connecticut
Member Is Offline
Mood: Estrified
|
|
Quote: Originally posted by mux  | First of all - salvaged parts are not an option here; this is a uniform design, I can't depend on people having specific salvaged parts.
|
You could design it using the most commonly-used parts available, that can be found either off-the-shelf, or in salvaged equipment. That would seem
to be the best solution, as we don't want to assume that nothing that we design will ever break or need replacing. We could then compile a list of
sources for parts that can be used to replace anything in the design.
Quote: | Second - I'm not disputing that motors can work. They clearly can, because a large part of stirrers already use them. It's just that I don't see
sufficiently cheap motors doing the job. Anything that would work is pretty expensive - too expensive to fit this project's budget, given that I am
shooting for a certain degree of reliability and performance. We're not talking qualitative statements here, we're purely talking about quantitatively
limiting design space. |
Then how come solid-state stirrers are always orders of magnitude more expensive than motor-driven ones, and seen to be aimed at applications where
motor-driven stirrers wouldn't work as well? This is the part of your point that made no sense at all to me. It's trivial to thermally isolate the
motor from the hotplate, so you DON'T need a motor that can withstand all of the thermal stresses that you're talking about. And most magnetic
stirrers that I've seen have had fans mounted directly on their own shafts as a means of circulating air past the motor. That, combined with the fact
that heat tends to rise, and the motor is typically located below the plate, is usually all the protection a motor needs.
Quote: | Look inside any reasonable quality hotplate stirrer and look at the motor inside. It's not a cheap 6V DC no-name motor. It's a brand name motor with
proper bearings and fairly high power rating. You don't find those for nearly the budget I'm on. And going with a cheaper motor means you need to add
other stuff to account for the points on which the cheaper motors have skimped, or adding little milled motor holders to account for differences in
sizing of motors as suppliers change. This, again, is not going to be cheap. |
This might be because a lot of scientific equipment was made in the US or Western Europe until fairly recently, and was often overdesigned. Not that
that's a problem, but if you open up any of the newer Chinese-made devices, their motors are nothing special. Also, for holding the motor in place,
it's pretty common practice to have mounting holes on the front face of the motor, so that its diameter and length can be variable, thus allowing the
engineers to swap out the motor for a different one if it proves to be inadequate, without having to redesign the whole product. This also provides
the motor with a heat sink, if it needs one. So this problem you speak of has already been solved in industry, you just didn't realize it. For more
information, see here:
http://reprap.org/wiki/NEMA_Motor
This is just for stepper motors, which are more than adequate to meet a hotplate's needs, (an but will require a controller chip for fancy stuff like
oscillating stirring. If you just want a DC motor that can work at low speeds without burning out
Quote: | Anything can be engineered, you can solve any nail-problem with any hammer-solution, it's just that finding the optimum is the true art.
|
I totally agree, which is why I think your "wet dream" comment is pretty telling of what kind of hammer you're holding. In this situation though, I
think it's important to not depart too far from the tried-and-true solutions that are already out there, since then you're far more likely to run into
an unforeseen problem that it's beyond your means to solve.
Quote: | I've looked into buying motors for this job. I have not found anything. Can you find something better? I'm specifically looking for:
- Sub-$4 complete assembly
- At least two long-term suppliers
- near enough to 0.1Nm torque at 10-2000RPM (0.05Nm is okay, 0.01 is too weak)
- Hard-brushed or non-brushed (i.e. 5000+ h lifespan)
- Can be side-loaded and axially loaded (order single digit N)
- Has a datasheet |
Two of these specification requirements seem absurd to me. As long as you get a motor with a standard mount, there's no need to lock in to any
specific supplier. Also, 10-2000 rpm? 10 RPM is one rotation every six seconds. Why on earth would you need something that slow? In any case, your
best bet is probably a brushless DC motor, or maybe even a stepper motor, since they're fairly cheap, commonly found in appliances in case someone
wants to build one themselves for even less money, can either be controlled by an inexpensive IC or an Arduino if someone wants to get fancy, they
don't have brushes (as the name implies, and neither does a stepper), a brushless DC motor has a huge speed range at near-constant torque, and you can
even do fancy stuff like rotate back and forth, presumably using an Arduino for controlling it.
Your $4 for the entire assembly requirement seem a bit unrealistic to me. First of all, unless your time is worth less than $1 an hour, winding your
own ferrite cores is going to be tedious as hell. And even if your components can handle the voltage spikes from them, are you 100% sure that every
one of them can handle those spikes for 5000 hours? Are you taking the PCB cost into consideration?
I'm quite certain that an alnico magnet, a standard-mount brushless DC motor, and the controller, could be had for under $10, but I can't imagine
you're taking every cost into consideration if you think you can build an induction one for that cheaply.
|
|
Sulaiman
International Hazard
   
Posts: 3698
Registered: 8-2-2015
Location: 3rd rock from the sun
Member Is Offline
|
|
If you are looking for a motor that has proven long life in a high temperature environment,
with integral heatshield and enough power, yet simple to operate with no sparks,
I suggest an electric oven fan, e.g. £13 retail eBay UK, bulk must be really cheap.
and guaranteed alternate suppliers for the forseeable futire.
CAUTION : Hobby Chemist, not Professional or even Amateur
|
|
mux
Harmless
Posts: 31
Registered: 11-12-2016
Member Is Offline
Mood: No Mood
|
|
Quote: Originally posted by Melgar  |
I'm quite certain that an alnico magnet, a standard-mount brushless DC motor, and the controller, could be had for under $10, but I can't imagine
you're taking every cost into consideration if you think you can build an induction one for that cheaply. |
What I'm trying to get at here is that I'm more than 'pretty sure' that it won't, because I did some preliminary component sourcing and so far got the
opposite. As much as I appreciate your input (and I do, very much so, this kind of stuff needs to be looked at critically, don't get me wrong when I
counter your arguments), at this point I need concrete sources, with full cost analysis, not (educated) guesses. Without a hard
counter to what I'm building now, I will continue down this path until I either succeed or fail.
In fact, a significant part of the additional cost in engineering a motor-driven solution is in assembly - my time. An inductive drive costs so little
because everything is cheap: I can buy inductors off the shelf for $0.20/pc which are essentially pre-wound ferrite cores and the mounting complexity
is all contained in the PCB.
Sulaiman again confirms my suspicion that any kind of motor that would comply with my mechanical and environmental constraints would be significantly
over budget. Note that those 13 GBP do not include mounting, electrical drive and the like.
---------------------
In other news, I'm back from my holiday, so I'll be slowly chipping away at this project. During the holiday I couldn't resist building a very
preliminary mechanical and electrical design for a stirrer-only project:
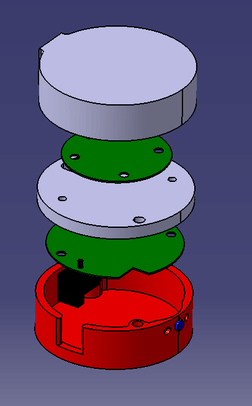
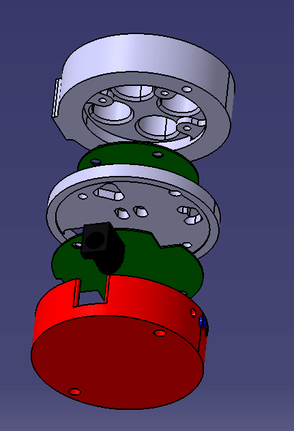
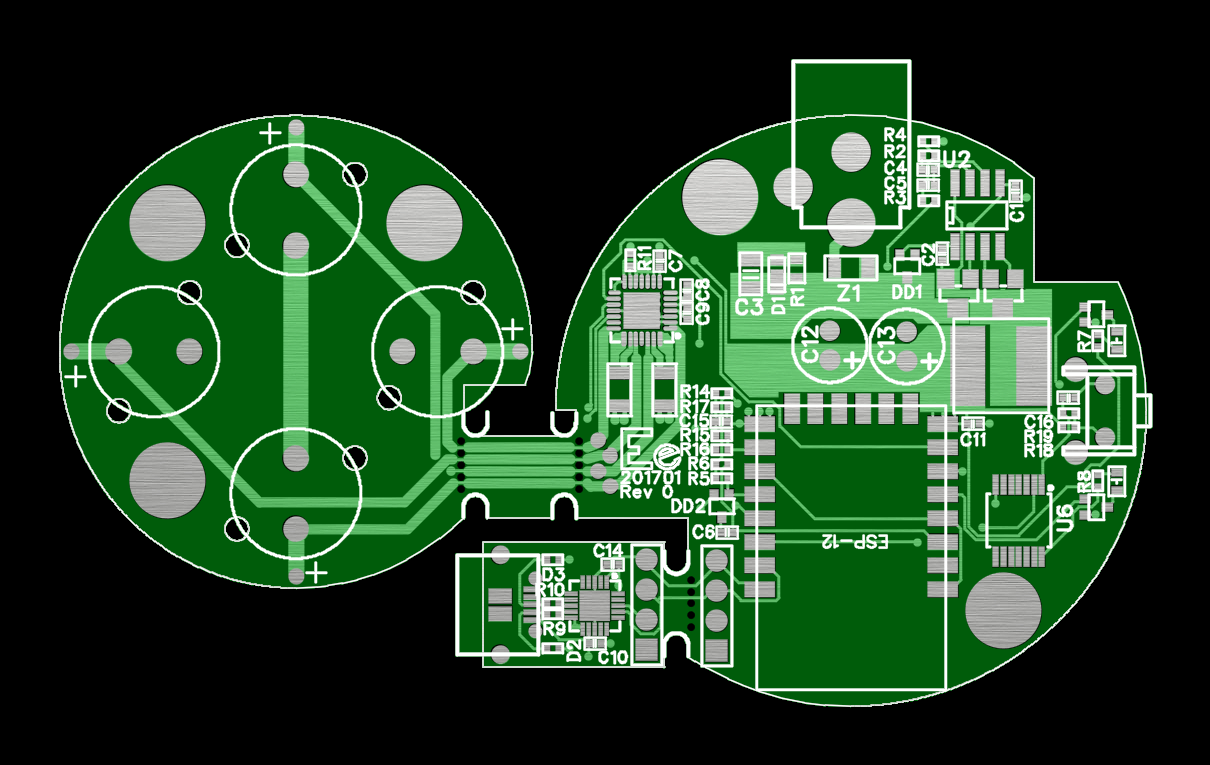
What you're seeing here is an exploded view of the mechanical design as well as the (again, super-preliminary, this-wont-actually-work) electronics.
The mechanical design is an exploded view, showing the overall shape (bit like a hockey puck). It's made of a top aluminum block which houses the
inductors (which sit on their own round-ish PCB), a middle aluminum disc which mounts the second PCB and acts as a heatsink for the driver and a
bottom plastic cover because.. well, wifi is screened pretty effectively by aluminum otherwise. Power entry is through the black connector and a
little button is on the front. Mounting the stirrer can be with either standard 60mm clamps or with an M10 thread in the back (also fairly standard
among retort supplies).
The PCB is shaped... weirdly. This is mostly for testing purposes. Really, it's 3 PCBs all stitched together in such a way that they can be easily
broken apart. On the left is the inductor mounting PCB, on the right is the main electronics (dominated by the big wi-fi module, some power management
and the driver chip) and in the bottom is a USB to serial PCB to program the ESP8266. This can all be assembled in one go and tested, and then before
mounting it in the enclosure it's broken apart into the separate PCBs.
This design is NOT meant to be any kind of idea of how the final product would look or work. I mainly just wanted to have some kind of baseline as to
how big everything would be and how the costing would look. So as of now, these are just pretty pictures to look at.
[Edited on 8-1-2017 by mux]
|
|
Sulaiman
International Hazard
   
Posts: 3698
Registered: 8-2-2015
Location: 3rd rock from the sun
Member Is Offline
|
|
As a repair enginner, the first things I saw were;
. electrolytic capacitors in a hot unventilated enclosure, at least use solid/polymer capacitors
. no way to replace the capacitors - could you use lands that protrude beyond the capacitor leads ... then they will be easier to replace.
(to get old ones off, grip with pliers etc. and twist cw/ccw/cw/ccw... starting gently, the body will come away without damaging the tracks, allowing
de-soldering of the remaining bits of leads)
the same applies to the lands for the indutors.
[Edited on 8-1-2017 by Sulaiman]
CAUTION : Hobby Chemist, not Professional or even Amateur
|
|
mux
Harmless
Posts: 31
Registered: 11-12-2016
Member Is Offline
Mood: No Mood
|
|
Note that this is just a stirrer, this is not designed to become warm at all. The electrolytics are designed to be safe life.
Most round lands you see are actually through holes, but my PCB rendering program for some reason doesn't render them as such. So yeah, the inductors
and caps are in fact through hole components
|
|
Sulaiman
International Hazard
   
Posts: 3698
Registered: 8-2-2015
Location: 3rd rock from the sun
Member Is Offline
|
|
Your magnetic circuits are very open,
if the pcb ends of the electromagnets were magnetically joined, even with moderate airgaps (e.g. 1.6mm)
your electrical power dissipation in the coils would be 1/4 of that if not magnetically connected.
if air gap = x2, then A.t = x2 so I2.R = x4
and the aluminium surrounding the coils/inductors/electromagnets will act like shorted-turns.
[Edited on 8-1-2017 by Sulaiman]
CAUTION : Hobby Chemist, not Professional or even Amateur
|
|
mux
Harmless
Posts: 31
Registered: 11-12-2016
Member Is Offline
Mood: No Mood
|
|
That is an excellent point. Hmm... Obviously, there will be a sizable air gap to the stir bar anyway, but the way it is now, it's a woefully
inadequate magnetic circuit. Can't believe I haven't thought about that in this design. I'm stupid sometimes.
The aluminum won't really do much, all of the interaction is purely magnetic (i.e. eddy currents). Because of the low permittivity, the dissipative
effects will not be too distinct from air. We're not dealing with sufficiently high-frequency magnetic fields here, worst case at 3krpm it's doing
50Hz. Here, I'll show you:
https://www.youtube.com/watch?v=m9rnNJsbNa0
|
|
wg48
National Hazard
  
Posts: 821
Registered: 21-11-2015
Member Is Offline
Mood: No Mood
|
|
Quote: Originally posted by mux  | That is an excellent point. Hmm... Obviously, there will be a sizable air gap to the stir bar anyway, but the way it is now, it's a woefully
inadequate magnetic circuit. Can't believe I haven't thought about that in this design. I'm stupid sometimes.
The aluminum won't really do much, all of the interaction is purely magnetic (i.e. eddy currents). Because of the low permittivity, the dissipative
effects will not be too distinct from air. We're not dealing with sufficiently high-frequency magnetic fields here, worst case at 3krpm it's doing
50Hz. Here, I'll show you:
https://www.youtube.com/watch?v=m9rnNJsbNa0 |
Interesting video. I am curious about the parameters of your set up.
How many turns on the coils and what is the peak current and voltage?
Was the voltage applied to the coils a squarewave and what frequency? It looks a lot slower than 50Hz.
Did you try the same with water in the beaker and perhaps cooking oil? When the distance between the coils and the stir bar is increased (in water or
cooking oil) what is the distance when it looses lock and at what freqency?
How thick is your aluminium sheet and by how much does it reduce the maxium height to remain locked at a given frequency?
|
|
mux
Harmless
Posts: 31
Registered: 11-12-2016
Member Is Offline
Mood: No Mood
|
|
These are just silly prototype experiments. Yes, I'm currently using this to stir my cordial, it works just fine with liquids, can even liberate a
stir bar from some loose soluble powder. It's a magnetic stirrer like any other.
I'm currently using an A4983 stepper driver at 200mA through some random inductors, unknown number of turns and magnetic field strength. Its maximum
rotation speed is 600rpm atm because of software limitations.
Like any other stirrer, it's only effective pretty close to the stirrer. Go beyond 2-3cm (1in) and it barely stirs anymore. The sheet you see is 2mm.
That's about the minimum thickness to avoid the magnet from sticking to the ferrite cores.
|
|
mux
Harmless
Posts: 31
Registered: 11-12-2016
Member Is Offline
Mood: No Mood
|
|
I've got another question for the seasoned stirrer people around here. I suppose everyone.
Please excuse the lack of appropriate glassware (I seem to have misplaced my big meth-making 5L roundbottom) as well as photography gear. I swear I'm
a professional!
https://www.youtube.com/watch?v=2lI-i23f_Gc
In this video I'm inducing spinout/decoupling at 2500rpm. After the stir bar spins out, it pretty much won't ever properly start again. It just
vibrates in place. This is with a monstrously big (54mm) stir bar, so that may have something to do with it, but even my normal-sized stir bar won't
neatly start spinning if I just immediately start it up at 2500rpm. The speed has to be ramped up slowly, and even then (as you can see a bit further
in the video) it sometimes destabilizes briefly.
Now, when ramping up the speed slowly and eventually plateauing, it's stable and will work for hours (well, only tested that once, but it seems rock
solid).
I've worked with a grand total of one magnetic stirrer before in my life, and I do remember getting it to work in some glassware used to be annoying
to impossible, while it would reliably work in roundbottoms and such. Is this just a fact of life, or do I have serious centering issues?
|
|
Sulaiman
International Hazard
   
Posts: 3698
Registered: 8-2-2015
Location: 3rd rock from the sun
Member Is Offline
|
|
if you use magnetic stirbars they must rotate synchronously with the rotating magnetic field,
as torque load on the spinbar increases, it will lag the applied field by an ever increasing angle, theoretical maximum 90 degrees, then fly away.
to get it spinning again you need some random chaos to get the spinbar moving close enough to synchronous with the rotating field that it can be
'captured'
or slow down the rotating field to a near stop then ramp up again, but not so far or fast this time 
that's my understanding so far.
This does raise the potential for very high speed rotating magnetic fields coupling to non-ferrous conductive disks
(ptfe coated aluminium, pure platinum, catalytic disks ...)
EDIT: it just occured to me, when you do experiments again,
put LEDs (e.g. red/green in one package for +/- current) near the respective electromagnets,
which indicate electromagnet voltage, or preferably current (magnetic field proportional to current).
That way a video could be analysed frame-by-frame, or in slo-mo to see if the above is true.
It would look 'cool' with LED magnetic field rotation indicators too
[Edited on 9-1-2017 by Sulaiman]
CAUTION : Hobby Chemist, not Professional or even Amateur
|
|
JJay
International Hazard
   
Posts: 3440
Registered: 15-10-2015
Member Is Offline
|
|
Just FYI, a 5L is not a big "meth-making round bottom." I know there's a cultural disconnect here, but a 22L is a big meth-making round bottom. A 5L
would probably be used for purifying solvents.
Not to harsh your buzz, but while some means of automating control might be appreciated, you would do well to follow industry standards instead of
simply putting your stirrer on the Internet. What if hackers break into my stirrer and cause a fire, etc...
and don't presume to lecture me on Internet security with a false sense of superiority; WiFi in a stirrer is just an unnecessary and undesirable
gimmick.
|
|
Sulaiman
International Hazard
   
Posts: 3698
Registered: 8-2-2015
Location: 3rd rock from the sun
Member Is Offline
|
|
As an inexperienced hobby chemist, one thing that I would like is
to be able to set up an experiment (especially distillation, reflux etc.) and once apparently stable,
be able to leave it un-attended until I get either a 'FINISHED' signal, or an 'ALARM' signal.
The most important ALARM signal, and a minimum requirement,
would be an isolated relay contact that is closed ONLY when the equipment is working 'properly'
In industry this is the E-STOP, EMERGENCY STOP signal line
that can be daisy-chained through all monitored nodes,
if any equipment detects a fault, or has no power, the E-STOP line will not pass the current required to enable operations down the line to continue.
The E-STOP line commonly operates on a 24 Vdc line, (but not neccessarily)
the end of line usually has a 24 V relay (or optocoupler etc.) that operates when all intermediate nodes (equipment with isolated relay contacts,
E_STOP switches, breakable wire barriers ....) are operating 'nominally', to produce an enable signal for processes/power to continue.
Each node should monitor the incomming E-STOP signal,
if not present that constitutes a fault so the heater-stirrer should take appropriate action
(e.g. immediate cessation of heating, stirring continued for a time ...)
Ideally I would like the heater-stirrer to detect out-of range temperature and loss of spinbar rotation as faults.
[Edited on 9-1-2017 by Sulaiman]
[Edited on 9-1-2017 by Sulaiman]
CAUTION : Hobby Chemist, not Professional or even Amateur
|
|
mux
Harmless
Posts: 31
Registered: 11-12-2016
Member Is Offline
Mood: No Mood
|
|
Sulaiman: Sure, I'll see what i can do w.r.t. the LED idea. That's not a bad idea.
JJay: I'm just joking around ;-) As for the Wi-Fi comment:
Well, you seem fairly determined that you don't want it, so... don't buy this stirrer . The reality is that I don't see how people hacking into your stirrer could fuck up anything, especially if it's an encrypted connection
and the stirrer has a password protected interface. Let's be real here: anyone determined and close enough to hack your stirrer can just... mess with
the knobs on a physical stirrer as well.
Wi-fi connectivity is different from an open connection to the internet. If your local network is compromised to the point where they can mess with
your stirrer, they can also mess with your other personal electronics. The stirrer, again, seems to me to be way down the list of things to worry
about. I'm aware of the IoT security hazard, but in this case any true hazard introduced by the stirrer is just as much introduced by having WiFi or a
cellphone in the first place. The specific comment a bout a stirrer causing a fire is a design defect by itself, that should never happen under any
circumstance. This seems like the weakest possible argument you can have against wifi connectivity. If you have explosive, flammable or delicate
chemicals in your lab, it's already in a fumehood with proper fire protocol in place. It's not like you're keeping this stirrer under your bed. Same
goes for a wi-fi connected hot plate.
On the other hand, the convenience granted by this type of connection is very significant, at least in the use case I'm designing it for. I don't do
chemistry fulltime in a lab. My 'lab' is a small corner of my garage or electronics workspace and my experiments can take hours, even overnight to
finish. I'm not babysitting that. Robots should do that.
And in order to program that robot, there should be an interface that requires the least possible additional effort from the user and creator.
Physical interfaces (e.g. a little touch screen or graphical interface) are complex, cumbersome and expensive. A web interface offers practically
infinite compatibility, can be easily (re)designed and updated to fit any use case and can have much higher information content and programmability.
THAT is why I'm convinced wifi to be core to this design.
|
|
JJay
International Hazard
   
Posts: 3440
Registered: 15-10-2015
Member Is Offline
|
|
Nah, you just think idiots will buy your stirrer if it has WiFi. We both know it would be better if it could be part of an integrated solution that
could work in places with heavy electromagnetic interference such as most any heavy industrial environment; even USB would be vastly superior to WiFI.
If you want WiFi, you could connect it to a controller that has WiFi. You're incredibly confused here; you're actually suggesting that allowing
hackers to control your machinery and industrial processes without authorization is no worse than letting them read your cell phone contacts.
That's not the point though; the point is, WiFi is inferior. I could use a vanilla USB interface connected to a controller that has WiFi if I wanted
it.
People, can we really take this guy seriously? I think he's a fraud.
|
|
Sulaiman
International Hazard
   
Posts: 3698
Registered: 8-2-2015
Location: 3rd rock from the sun
Member Is Offline
|
|
Wi-Fi is neccessary because inside the stirbar thermal and spatial sensors, and LED bars that display the temperature and spin speed whilst spinning.
like the propellor-clock https://www.youtube.com/results?search_query=propellor+clock
                      
I want one
P.S. as far as I can tell, a huge market for heater-stirrers is the 'vaping' community ... money no object, iphone interface mandatory.
as are elegant lines and sexy displays, precise speed and temperature not important.
[Edited on 9-1-2017 by Sulaiman]
CAUTION : Hobby Chemist, not Professional or even Amateur
|
|
Pages:
1
2
3
4 |
|