Pages:
1
2
3
4
5
6 |
deltaH
Dangerous source of unreferenced speculation
   
Posts: 1663
Registered: 30-9-2013
Location: South Africa
Member Is Offline
Mood: Heavily protonated
|
|
Thank your for your time and efforts, fulmen. It's greatly appreciated.
I think I might dabble with this a bit further. Will update here.
[Edited on 18-3-2015 by deltaH]
|
|
Fulmen
International Hazard
   
Posts: 1725
Registered: 24-9-2005
Member Is Offline
Mood: Bored
|
|
Go ahead, maybe you'll get lucky. It's not unreasonable to expect variations due to both methodology and raw materials, but for me that is a bit of a
turnoff. It's like brand-specific recipes where no-one can tell you what makes that brand important. If you can't get that one you have to go through
the pain of random testing. The sugar-based propellants greatest advantage is that they work with any brand of commonly available consumer products.
But from what I could gather factices often exhibit poor shear strength. Yet I read it was also used as a rubber substitute. Bit was that only as an
dilutant or also as a replacement? If used as a pure substitute then clearly better results are possible to achieve.
We're not banging rocks together here. We know how to put a man back together.
|
|
deltaH
Dangerous source of unreferenced speculation
   
Posts: 1663
Registered: 30-9-2013
Location: South Africa
Member Is Offline
Mood: Heavily protonated
|
|
While luck plays a factor as with all things in life, product and formulation development is very tough. Something like this may takes months of
research to perfect. I don't think it's going to be about brands used or anything like that, I just think the science is a lot more complex.
For example, I think the formation of either a magnesium or calcium soap is important, but also think that that will hardly proceed with MgO and
ordinary oils, unless you cook it at very high temperatures for a day. If you look carefully at that African agricultural research paper attached
earlier (Ebewele et al, 2013), you'll notice that the rubber seed oil they used had a ridiculously high content of free fatty acid, I think
something like 38%. That is completely unusual for normal OTC and refined oils and this is also why simple MgO neutralised that particular oil easily.
But when I tried to saponify sunflower oil low in free fatty acid using lime and heating, I did not achieve any significant conversion. So there is
the first problem, saponification (hydrolysis of triglycerides) does not proceed easily with alkali earth oxides, while on the other hand, these react
easily with free fatty acids. In the case of linseed oil, the free fatty acid content would be much much too low, so very little saponification would
have happened under the conditions you were using. If it did, the oil would have gelled there and then, possibly even solidified. Then
vulcanising would have hardened it even further. Anyway, there's a lot to explore here and many possibilities. It's not just about optimisation, it's
about studying the system and solving its problems.
What I think I'd like to try first is saponifying linseed oil with lye by normal soap-making methods (and an OTC phase transfer catalyst) that I'm
used to. Then I would neutralise it with hydrochloric acid to precipitate and salt out the free fatty acids. Those aught to easily react with MgO or
lime at elevated temperature. They should also stink significantly less when vulcanising because you've purified it and removed glycerine. Ideally,
one would distill the fatty acids under reduced pressure or with steam, but I don't have the apparatus for that. If one distilled it, you could ditch
the useless saturated and monounsaturated fatty acids that detract from hardness.
Industry straight steam strips the starting oil to obtain fatty acids, relying on the high temperature of the superheated steam to hydrolyse and crack
the oil, but that's not something the amateur couldn't easily set up, plus the initial stripped fatty acids have to be redistilled to isolate the
desired fraction of polyunsaturates.
[Edited on 19-3-2015 by deltaH]
|
|
deltaH
Dangerous source of unreferenced speculation
   
Posts: 1663
Registered: 30-9-2013
Location: South Africa
Member Is Offline
Mood: Heavily protonated
|
|
STEP 1: Saponification of linseed oil
Bought a 750ml bottle of light brown raw linseed oil at my hardware store today. It was about halfway in cost between cooking oils and olive oil, so
not too bad.
I dissolved 35g NaOH in 35g tap water with gentle swirling in a 500ml polypropylene plasticware with a good rubber sealed lid and side snap wings.
Then 5ml didecyldimethylammonium chloride (30% w/w solution, black algaecide for pools) was added in one portion as phase transfer catalyst and
formed a white milky precipitate (presumably sodium chloride). 250g Raw linseed (flax seed) oil was then quickly added to the very hot solution, the
lid secured tightly and then contents was shook by hand, making sure to firmly hold the lid and base down in a pincer grasp because the pressure
increases slightly. The hot emulsion was then shaken by hand at a leisurely pace for several minutes until it thickened (trace reached) and resembled
mustard after which it was set aside to react further overnight.
I'm pleased with the saponification so far.
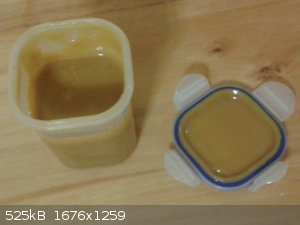
EDIT: I had a brainwave, I was going to acidify and isolate the fatty acids tomorrow, but I just realise that I can simply cook this soap up with a
concentrated Epsom salt solution to form and salt out the magnesium soap directly (since it is insoluble). I can then mix this with catalyst, NaNO3
and sulphur, compress and then bake to vulcanise.
UPDATE: To quote fulmen, look like it's taking its sweet time
Next morning, it's a little firmer but still not fully saponified in my opinion. I'm going to put the container in a small dish with water and boil it
slowly for a couple of hours to speed things up. Perhaps my phase transfer catalyst isn't working as well as I'd hoped.
[Edited on 21-3-2015 by deltaH]
|
|
deltaH
Dangerous source of unreferenced speculation
   
Posts: 1663
Registered: 30-9-2013
Location: South Africa
Member Is Offline
Mood: Heavily protonated
|
|
Quote: Originally posted by Bert  | From personal experience, flammable oils, either of organic or mineral origin in VERY small percentages will greatly slow a solid fuel or other
pyrotechnic mixture-
This is done deliberately to make "oiled stars" that are intended to smolder all the way back to the ground (or water... I would only fire these over
a body of water, deep snow, etc.). A friend who was less cautious calls these "FSAFOYH" stars (as in "flaming shit falls on your head").
Some will add a % or two of oil in a fast evaporating solvent to black powder rocket fuels that are too fast burning for the intended motor size, then
dry off the solvent. If done correctly, the remaining oil slows the fuel down just enough to prevent a CATO- add just a little bit more, and they
sometimes won't leave the ground! |
I'm hoping (though can't promise) to ditch the really inert waxy unsaponifiable matter, saturated fatty acids and maybe monounsaturates as well. Their
soaps aren't very soluble, so when I boil up my saponified linseed mass, I should be able to skim them off before adding magnesium sulfate to
precipitate the magnesium soaps.
I should be left with something enriched in polyunsaturates if all goes well (which it seldom does ) which should be far more reactive.
Finally, I have a bottle of ferric nitrate nonahydrate. I'm going to add a few percent to the final mix with sulfur and oxidiser. This should
decompose on heating (during vulcanisation) to a ferric oxyhydroxide/sulfide that I'm hoping will serve as a cracking catalyst for the organics when
burning. I'm borrowing here from industry that use 'iron muds' to crack very heavy petroleum oils/tar.
[Edited on 21-3-2015 by deltaH]
|
|
deltaH
Dangerous source of unreferenced speculation
   
Posts: 1663
Registered: 30-9-2013
Location: South Africa
Member Is Offline
Mood: Heavily protonated
|
|
STEP 1: Saponification of linseed oil - UPDATE
Yay, saponification complete, placing the PP container in simmering water for three hours did the trick and produced an interesting linseed oil
soap... a first for me 
Now on to salting out and Mg ion exchange with Epsom salt.
|
|
PHILOU Zrealone
International Hazard
   
Posts: 2893
Registered: 20-5-2002
Location: Brussel
Member Is Offline
Mood: Bis-diazo-dinitro-hydroquinonic
|
|
Just a few side notes!
1°) Ca(OH)2 would also provide precipitated unsoluble soap and may be cheaper than Mg soap.
2°) Mixing cationic soap with anionic soap result in a waxy unsoluble precipitate and ruins the soap effect of both cationic and anionic surfactants.
(C10H21)2N(CH3)2Cl + NaO2C-R --> (C10H21)2N(CH3)2O2C-R+ NaCl
didecyldimethylammonium linseed-oleate
3°) It may be good to test for sorbic acid or sorbates with sulfur... sorbic acid is CH3-CH=CH-CH=CH-CO2H (2,4-hexadienoic acid) it contains two
unsaturations and may lead to sulfide/disulfide crosslinkage.
[Edited on 21-3-2015 by PHILOU Zrealone]
PH Z (PHILOU Zrealone)
"Physic is all what never works; Chemistry is all what stinks and explodes!"-"Life that deadly disease, sexually transmitted."(W.Allen)
|
|
deltaH
Dangerous source of unreferenced speculation
   
Posts: 1663
Registered: 30-9-2013
Location: South Africa
Member Is Offline
Mood: Heavily protonated
|
|
STEP 2: Magnesium ion exchange and salting out
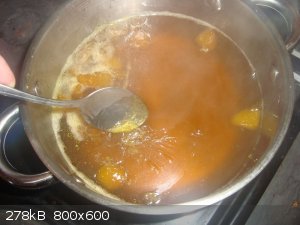
[1] Simmered my linseed soap with 1000ml water for 90 minutes. Most of it dissolved, but a few gelatinous blobs remained insoluble.
[2] Carefully poured out the solution using a spoon to hold back the floating insoluble bits.
[3] The clear solution in a stainless steel bowl, hopefully somewhat enriched in unsaturated fatty acid soaps (wishful thinking )
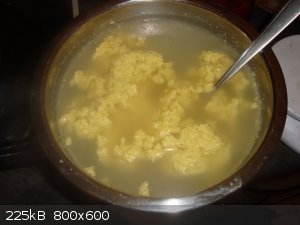
[4] Added 100g Epsom salt (MgSO4.7H2O) in one go into the hot soap solution while stirring gently. It immediately precipitated 'curds'.
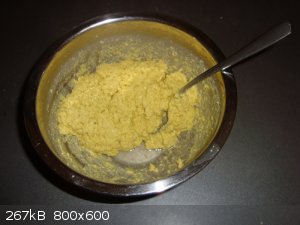
[5] Carefully poured out the slightly milky liquid using a spoon to hold back the curds. I was careful to not squish the curds in the process as they
were very soft and I wanted to maintain their granular form for washing. I washed twice with tap water and stirred very gently when washing.
[6] After my final wash and decant, I used my hands to compress the magnesium linolate precipitate. It felt like a very soft and fatty dough.
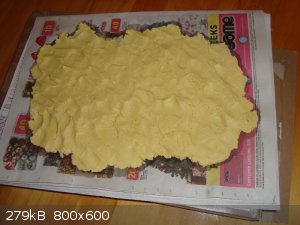
[7] Spread out the product on several sheet of newspaper to soak up the excess water. Some ink transfer occurred on the underside, but I'm not too
bothered by that.
All-in-all, this was great fun!
[Edited on 22-3-2015 by deltaH]
|
|
deltaH
Dangerous source of unreferenced speculation
   
Posts: 1663
Registered: 30-9-2013
Location: South Africa
Member Is Offline
Mood: Heavily protonated
|
|
Quote: Originally posted by PHILOU Zrealone  | Just a few side notes!
1°) Ca(OH)2 would also provide precipitated unsoluble soap and may be cheaper than Mg soap.
2°) Mixing cationic soap with anionic soap result in a waxy precipitate and ruins the soap effect of both cationic and anionic surfactants.
(C10H21)2N(CH3)2Cl + NaO2C-R --> (C10H21)2N(CH3)2O2C-R+ NaCl
didecyldimethylammonium linseed-oleate |
[1] Yes, but I had a packet of Epsom salts for the bath that I never used 
[2] I've experienced this with close to one-to-one mixes, but not so much with small amounts. I cannot know if this helped or not for sure without
rigorous comparison with a control, but I figured it wouldn't hurt much to have a little in there in case it could help.
***********
I decided against letting the product dry out as the little bit on my hand started to go slightly tacky as it was drying and I was worried this was
the beginning of radical polymerisation.
Most of the excess water had been absorbed into my newspaper anyhow, the remaining product resembled a soft dough with a similar light yellow colour.
I transferred to a sandwich bag and keeping it closed with air squeezed out until I decide what to do with it exactly.
The last thing that I want is for it to become really hard and useless.  
[Edited on 21-3-2015 by deltaH]
|
|
PHILOU Zrealone
International Hazard
   
Posts: 2893
Registered: 20-5-2002
Location: Brussel
Member Is Offline
Mood: Bis-diazo-dinitro-hydroquinonic
|
|
Maybe the few unsoluble gunky blobs are from the DMDD-ammonium-lineseed oleate.
The DDMDD ammonium chloride as phase transfer is of no use because as soon as NaOH/water hydrolyses the oil, it forms a soluble anionic soap that will
be the phase transfert catalyst increasing the saponification speed.
But DDMDD ammonium chloride might be a good idea (for a deviated project) in a 1/1 fashion with sodium lineseed oleate to get mineral-less (No
Magnesium/No Calcium) factice rubber starting material?
PH Z (PHILOU Zrealone)
"Physic is all what never works; Chemistry is all what stinks and explodes!"-"Life that deadly disease, sexually transmitted."(W.Allen)
|
|
deltaH
Dangerous source of unreferenced speculation
   
Posts: 1663
Registered: 30-9-2013
Location: South Africa
Member Is Offline
Mood: Heavily protonated
|
|
Quote: | Maybe the few unsoluble gunky blobs are from the DMDD-ammonium-lineseed oleate. |
They were still soluble in fresh water and were soapy, like store bought transparent soap. While I cannot discount this for sure, it also resembled
what I frequently observed with ordinary saponification of other oils, e.g. olive oil etc. There's always hard to dissolve blobs that are nevertheless
soapy. I don't think this was the complex of the two as you say, but it could be so. It could also be simple saturation 
Quote: | But DDMDD ammonium chloride might be a good idea (for a deviated project) in a 1/1 fashion with sodium lineseed oleate to get mineral-less (No
Magnesium/No Calcium) factice rubber starting material? |
The one-to-one aspect is not that great, with things like Mg and Ca, you have at least two unsaturated 'strings' to cross link. Also the DMDD is
completely saturated and large, not that great for the hardness of the final product I think, nor reactivity. I'm really trying to maximise the degree
of unsaturation as much as possible, in that respect, I'm pleased to see yellow colours 
****************************
[Oh, forgot to mention that I don't think the magnesium linolate is totally insoluble... I managed to wash it off my hands fairly easily and it was
soapy to the feel. It might be less soluble than sodium, but I wouldn't say insoluble, it's more like another kind of soap and very soft like an oily
dough.]
EDIT: I take that back, some of it clinging to the pot was really hard to wash out, I think there was some residual sodium linolate in the paste that
made it easier to dissolve.
There's probably a fair bit of moisture in there still and not to sure what to do about it. From its marvelous consistency, I'm very tempted for a
step 3 to just add the other powdered dry ingredients (S + NaNO3 + Fe(NO3)3.9H2O) and 'knead the dough' before baking in a mold to set, but the water
in there could cause problems.
A desiccator with inert atmosphere/vacuum would have been handy right about now 
[Edited on 22-3-2015 by deltaH]
|
|
deltaH
Dangerous source of unreferenced speculation
   
Posts: 1663
Registered: 30-9-2013
Location: South Africa
Member Is Offline
Mood: Heavily protonated
|
|
I need some advice on my formulation stoichiometry for my step 3:
I've made a spreadsheet with the following design parameters:
[1] Amount of NaNO3 to target formation of CO and H2O from the fuel (in reality there will be some mix with H2 and CO2 because of the water-gas shift
equilibrium and iron catalyst present which is active for this reaction). I'm using fulmen's suggestion to run fuel-rich, which I
think is a great idea.
[2] Enough sulfur to form all Na2S from the NaNO3
...and assumed my magnesium linolate is in fact pure magnesium linolenate (the other fatty acids in there should make only minor differences to the
final weight of oxidant required etc.)
Now for the ferric nitrate. In the presence of basic soap, it's not unreasonable to assume that the ions would swop to a degree, forming ferric
linolate and magnesium nitrate. In a way I'm pleased about this if it happens as ferric linolate would be a three prong soap and so can result in a
more cross-linked factice (harder?) as well as dispersing the iron catalyst better in the material to favour cracking of the oils.
This results in an iron mass fraction of 1.3%, but that will go up in drying. This seems like a reasonable number.
What are your thoughts/suggestions on my composition formulation I've laid out?
Simplifying, this rounds off to:
• 6 parts NaNO3
• 2 parts magnesium linolate
• 1 part sulfur
• 1 part ferric nitrate nonahydrate
all by mass.
Planning to grind a small amount of these together in a mortar and pestle and then see what to do next, compress and bake is one option. This is
obviously not castable, would have to go the liquid free fatty acid route if one wanted to make something castable, but it's a good way to check what
the final material would be like physically and if it will burn. Still worried about the water that needs to come off... hope that doesn't mess
everything up.
***********
Just realised I should have salted out and ion-exchanged using ferric nitrate in step 2 to make ferric linolate directly, stupid of me If I had some ferrous sulphate, even better, oh well, next batch...
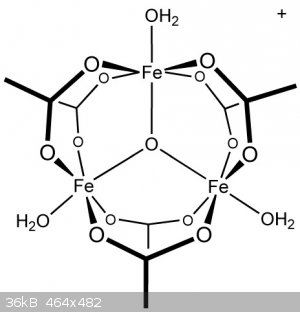
This is the structure of the iron clusters in ferric acetate according to Wikipedia. This seems too good to be true for my materials, now I have to
try to make ferric linoleate using my ferric nitrate to salt out.
That beast has six freakin' legs!!!
[Edited on 22-3-2015 by deltaH]
|
|
deltaH
Dangerous source of unreferenced speculation
   
Posts: 1663
Registered: 30-9-2013
Location: South Africa
Member Is Offline
Mood: Heavily protonated
|
|
Quote: Originally posted by PHILOU Zrealone  |
The DDMDD ammonium chloride as phase transfer is of no use because as soon as NaOH/water hydrolyses the oil, it forms a soluble anionic soap that will
be the phase transfert catalyst increasing the saponification speed. |
I'm making another batch of sodium 'linolate' because I want to try salting out with ferric nitrate this time to prepare ferric 'linolate'.
For comparison, I didn't use the quaternary ammonium salt this time around and indeed, while reaching trace was slower (about doubly so), there is no
major reason to use it since it proceeds nevertheless, so you were right!
|
|
aga
Forum Drunkard
   
Posts: 7030
Registered: 25-3-2014
Member Is Offline
|
|
I'd never heard of Factice until you started this thread. Thanks !
Trying it out (simple factice) was a little smelly and messy, and didn't work out too well.
Olive oil and Sunflower oil were used: 50g oil, 12.5g Sulphur, 5g Sodium Carbonate.
Air was bubbled through the oil for 15 minutes, then the oil heated to 140C, the reactants added, and the heat removed once the reaction kicked off.
Sunflower oil reacted a LOT faster than the olive oil.
Both results are a viscous orange/dark brown liquid. The sunflower version is a lot more viscous.
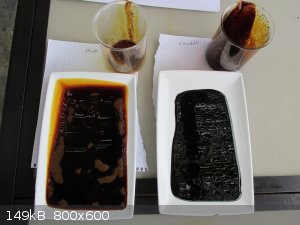
[Edited on 22-3-2015 by aga]
|
|
deltaH
Dangerous source of unreferenced speculation
   
Posts: 1663
Registered: 30-9-2013
Location: South Africa
Member Is Offline
Mood: Heavily protonated
|
|
Wow aga, I'm amazed you tolerated the smell of that so well!
Nice photo's BTW, you make tar look about as good as it possibly can look in your third photo
The olive oil one looks like crude oil (probably smells similar but much stronger) and the final one looks more like tar.
To produce rubbery factices, you really do need a 'drying oil', cooking oils just don't have enough linolenic acid derived triglycerides.
My second batch of sodium soap of linseed oil is nearly finished, about to do the 90 minute dissolution before attempting an iron ion exchange and
salting out of ferric 'linolate'.
|
|
aga
Forum Drunkard
   
Posts: 7030
Registered: 25-3-2014
Member Is Offline
|
|
Yeah, the smell is pretty 'orrible.
Doing this in an apartment would have the neighbours either calling the police, fire brigade, or possibly an Ambulance, thinking that if you naturally
made that smell, you'd be seriously unwell.
|
|
blogfast25
International Hazard
   
Posts: 10562
Registered: 3-2-2008
Location: Neverland
Member Is Offline
Mood: No Mood
|
|
Quote: Originally posted by deltaH  |
My second batch of sodium soap of linseed oil is nearly finished, about to do the 90 minute dissolution before attempting an iron ion exchange and
salting out of ferric 'linolate'.
|
What's the interest in ferric linolate?
|
|
Metacelsus
International Hazard
   
Posts: 2539
Registered: 26-12-2012
Location: Boston, MA
Member Is Offline
Mood: Double, double, toil and trouble
|
|
Iron(iii) accelerates the burn rate of solid rocket fuel. For example, the Space Shuttle boosters used it at 0.4%.
https://en.wikipedia.org/wiki/Space_Shuttle_Solid_Rocket_Boo...
[Edited on 22-3-2015 by Cheddite Cheese]
|
|
deltaH
Dangerous source of unreferenced speculation
   
Posts: 1663
Registered: 30-9-2013
Location: South Africa
Member Is Offline
Mood: Heavily protonated
|
|
Exactly Cheddite Cheese. I'm hoping to cross-link the ferric linolate with sulphur by heat treatment to make a factice, the iron is
then already in there and nicely dispersed, plus the iron itself may help cross-links the polymer, see the structure of the ferric acetate I attached
above, it has six 'legs' which in my case will be polyunsaturated fatty acids instead.
|
|
blogfast25
International Hazard
   
Posts: 10562
Registered: 3-2-2008
Location: Neverland
Member Is Offline
Mood: No Mood
|
|
As regards that phase transfer catalyst, any soap making crafts site will show you it isn't needed. Saponification with NaOH or KOH takes a while but
proceeds well and to completion, with just about any triglyceride. I prepared crude oleic acid that way, years ago.
Good luck with vulcanising your mixture of ferric linolate, NaNO3 and sulphur, though! Make sure you don't blow yourself up...
[Edited on 22-3-2015 by blogfast25]
|
|
deltaH
Dangerous source of unreferenced speculation
   
Posts: 1663
Registered: 30-9-2013
Location: South Africa
Member Is Offline
Mood: Heavily protonated
|
|
STEP 2b: Iron ion exchange and salting out with ferric nitrate
The ferric nitrate didn't yield as practical a result as the magnesium sulphate did.
The product appears to be a semi-fluid and the solution remaining still appears quite red. Not so sure what's going on here. I think the salting out
effect is not working as well with the nitrate as it did for sulphate, but it worked in part, so letting it cool and will try to isolate the red-brown
semifluid gloop that's floating on top. Definitely not as well behaved as the magnesium sulphate salting out.
Perhaps this would have worked better with ferrous sulphate?
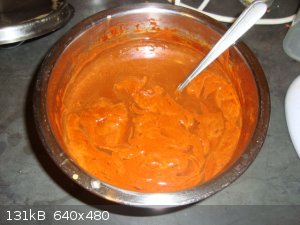
In some way, this gloop resembles the oil dough consistency of the magnesium 'linolate', but it's so soft that it's actually runny. Seems like the
higher the cation charge, the softer the resulting polyunsaturated soap, which makes sense.
I think I'm going to put this into my freezer to see if I can harden the ferric linolate... it's hard to work with it in this thick semi-fluid gloop
state.
Interestingly, this might actually be close to a castable material!
[Edited on 22-3-2015 by deltaH]
|
|
blogfast25
International Hazard
   
Posts: 10562
Registered: 3-2-2008
Location: Neverland
Member Is Offline
Mood: No Mood
|
|
Quote: Originally posted by deltaH  |
The product appears to be a semi-fluid and the solution remaining still appears quite red. Not so sure what's going on here. I think the salting out
effect is not working as well with the nitrate as it did for sulphate, but it worked in part, so letting it cool and will try to isolate the red-brown
semifluid gloop that's floating on top. Definitely not as well behaved as the magnesium sulphate salting out.
Perhaps this would have worked better with ferrous sulphate?
|
Have you taken into account just how insoluble Fe(OH)3 is? Depending on concentration it starts precipitating from pH 4 to 5.
I bet part of your solids is Fe(OH)3, perhaps part of it in the peptised form.
Perhaps using a ferrous salt, followed by air oxidation of the 'ferrous linolate' would work better.
Alternatively use much smaller amounts of iron, it's supposed to act as a catalyst in the combustion, I think? If so, large amounts would not be
necessary.
[Edited on 22-3-2015 by blogfast25]
|
|
deltaH
Dangerous source of unreferenced speculation
   
Posts: 1663
Registered: 30-9-2013
Location: South Africa
Member Is Offline
Mood: Heavily protonated
|
|
Thanks blogfast for the suggestions. I have an excess of ferric nitrate in there since I used 100g and there once again remained a
fair amount of insoluble sodium linolate behind when I dissolved it in the step prior, so the pH of the solution is acidic. I'm relying on the
insolubility of the product to force it out of solution.
It looks like it worked, it's just that the physical form of the product makes it cumbersome to separate, it's a runny gloop, but low temperature
might help a lot (freezer). If I can just get it to firm up a little, I can manipulate it better and wash.
I definitely think using ferrous sulphate is the way to go, it should ion exchange and salt out in a similar fashion to what the magnesium suphate
did, I just didn't have any on hand, but had the nitrate 
In the end, it should matter what oxidation state the iron's in, the active catalyst I imagine would probably be reduced iron anyhow. I want a lot in
there because the iron is going to be a lot less active with all that sulphur that probably poisons it. That said... I do know that ferric oxides
speed up the burn of sugar+sulphur+saltpeter from personal experience, in-spite of the sulphur, but again, I used a few percent there, not hundreds of
ppm's as one would normally work a catalyst.
|
|
blogfast25
International Hazard
   
Posts: 10562
Registered: 3-2-2008
Location: Neverland
Member Is Offline
Mood: No Mood
|
|
I've not read this thread from A to Z so I might be b*llshitting here but unintentionally.
Wouldn't it be simpler and more controllable to isolate the linolenic acid, dry it properly and then thoroughly mix in the sulphur, 'active' ferric
oxide and sodium nitrate? Then mould and crosslink?
That would give far more control over the actual composition of the propellant, I think.
[Edited on 22-3-2015 by blogfast25]
|
|
deltaH
Dangerous source of unreferenced speculation
   
Posts: 1663
Registered: 30-9-2013
Location: South Africa
Member Is Offline
Mood: Heavily protonated
|
|
Yes, that was the original plan of sorts, but one of the problems with factice rubber is that it's soft. I found a paper on the first page of this
thread that used magnesium oxide in the factice formulation to make a harder factice, so I hypothesised that the harder factice was because a
magnesium soap was forming which then also vulcanised by way of the double bonds... a double whammy.
I just figured that I could make a reasonably pure magnesium soap off the bat instead of isolating the free fatty acids first and then using magnesium
oxide, but ultimately, the free acid route is the route to go for a castable formulation.
However, the iron soap is changing matters, since the ferric linolate is runny, it might be castable as is. Anyhow, early days and lots of work in
store. The ferric linolate may also benefit from a magnesium oxide addition if it has a high fatty acid content to it in terms of hardening the final
factice product.
[Edited on 22-3-2015 by deltaH]
|
|
Pages:
1
2
3
4
5
6 |