Pages:
1
2
3
4 |
metalresearcher
National Hazard
  
Posts: 758
Registered: 7-9-2010
Member Is Offline
Mood: Reactive
|
|
Good ideas !
Now I made two other small scale retort pipes one of them (the middle in the picture below labeled 'Na') was used before with the larger retort last
Saturday. At that experiment Na vapor was leaking from the retort.
Now I heated it to red hot in the middle to bend and after heating I quenched it in water and what happened .....?
Hissing and bright yellow sparks appearing and pops with a yellow flash which was clearly that sodium metal wast still in the tube (despite the tube
was lying for two days in open air and a part of it heated to red hot shortly before).
A made a new one from the same tube (labeled 'K' on top of the picture) which I will use for K2CO3 + C for making potassium metal.
|
|
peach
Bon Vivant
   
Posts: 1428
Registered: 14-11-2008
Member Is Offline
Mood: No Mood
|
|
Now is the time to up the care level, as it sounds like you're on the way to a lump, possibly of special K.
|
|
metalresearcher
National Hazard
  
Posts: 758
Registered: 7-9-2010
Member Is Offline
Mood: Reactive
|
|
Just found a solution for the oil capture :I use a 32mm (1 1/4") test tube filled with motor oil in which the condensing tube is partly immersed. Due
to the narrow nature of the test tube the suckback issue is addressed as well.
It fits any 15mm outer diameter steel tube regardless for very small scale or much larger scale. The test tube holder has an adjustable height.
|
|
Rogeryermaw
National Hazard
  
Posts: 656
Registered: 18-8-2010
Member Is Offline
Mood: No Mood
|
|
nice work! that should definitely address any stability issue with your receiver and hopefully protect you from the worst of your possible fire
hazards. you've been working like a man possessed!
|
|
peach
Bon Vivant
   
Posts: 1428
Registered: 14-11-2008
Member Is Offline
Mood: No Mood
|
|
That's a smart bit of thinking, particularly the holder on the bottom with the adjustable height. Elegant, simple, effective. 
{edit}Stick a small computer fan on there pointing at the bottom of the tube?{edited}
[Edited on 28-9-2010 by peach]
|
|
metalresearcher
National Hazard
  
Posts: 758
Registered: 7-9-2010
Member Is Offline
Mood: Reactive
|
|
Thanks for your comments. I tested it and it worked fine. Now I tried potassium now with K2CO3 + C but the bottom of the retort got overheated /
attacked / melted ????
On the right there is the weld, I saw it nearly white hot in the furnace what happened ??
Melting cannot occur as steel melts @ 1500oC, but to be honest I was rather close due to the blinding light yellow glow ....
I can peek my S thermocouple into the chamber but temperature is VERY HARD to measure. When the moving air in the chamber i, sday, 1300oC then the
steel can differ more than 100 degrees.
What do you guys think about the damage to the retort ?
Tomorrow a next try.
|
|
Magpie
lab constructor
   
Posts: 5939
Registered: 1-11-2003
Location: USA
Member Is Offline
Mood: Chemistry: the subtle science.
|
|
Caustic embrittlement? Maybe it's time for stainless steel, or other high nickel alloy.
The single most important condition for a successful synthesis is good mixing - Nicodem
|
|
peach
Bon Vivant
   
Posts: 1428
Registered: 14-11-2008
Member Is Offline
Mood: No Mood
|
|
The melting thing goes back to the jet fuel and 9/11 thing. The melting point is where it's going to flow like a liquid, but it'll be warping and
drooping before that even under it's own weight.
With the precise temperature control being difficult with fire involved, it's equally possible a hot spot appeared on the steel and it's melted.
I'd skip all the wondering and fiddling with variables and go straight to something like 316 now. The guys who do exhaust systems may be able to get
some higher grade stainless as off cuts for experimenting with.
Avoid drawn stainless tubing. It's going to cost a fortune and the drawn nature isn't necessary at lower pressures.
|
|
Panache
International Hazard
   
Posts: 1290
Registered: 18-10-2007
Member Is Offline
Mood: Instead of being my deliverance, she had a resemblance to a Kat named Frankenstein
|
|
this may be yet another stupid question but instead of trying to seal the end of a pipe why not just have a pipe bent into a tight u with both ends
entering the oil and the rxn mixture packed into the u-section in the furnace?
Also the virtue of stainless is not its inertness at those temps however it's mechanical strength. if you find a scrap yard near a university with a
decent engineering department they always have annealed tube offcuts, these annealed seamless pieces can be readily bent far more easily than steel,
once bent they can't be unbent though.
Fantastic thread btw
[Edited on 29-9-2010 by Panache]
|
|
metalresearcher
National Hazard
  
Posts: 758
Registered: 7-9-2010
Member Is Offline
Mood: Reactive
|
|
Good idea that U-tube, as I have destroyed two squeezed-end-tubes tonight with the same leaking issue at the weld at the squeeze.
|
|
Panache
International Hazard
   
Posts: 1290
Registered: 18-10-2007
Member Is Offline
Mood: Instead of being my deliverance, she had a resemblance to a Kat named Frankenstein
|
|
Sweet! (pumps fist in air), unfortunately, now encouraged, i'm sure to spit out hundreds of useless stupid ideas chasing that feeling.

|
|
bbartlog
International Hazard
   
Posts: 1139
Registered: 27-8-2009
Location: Unmoored in time
Member Is Offline
Mood: No Mood
|
|
Quote: | Melting cannot occur as steel melts @ 1500oC |
But you have carbon in your tube. And once the carbon content of steel reaches two percent, you're entering cast iron territory (mp: 1100C or
thereabouts). With various intermediates between, of course. It sounds to me like the carbon is diffusing into the steel and lowering the melting
point. Nickel plating the inside of the vessel (assuming it's practical) should help this problem.
|
|
metalresearcher
National Hazard
  
Posts: 758
Registered: 7-9-2010
Member Is Offline
Mood: Reactive
|
|
@bbartlog
But nickel also absorbs carbon... and nickel plating steel is not a simple job .....
The best option is chrome steel (ANSI 430) but that is hard to get in tubing .....
So for me the only option is using thicker walled plain steel tubes without weld or threaded seams.
|
|
metalresearcher
National Hazard
  
Posts: 758
Registered: 7-9-2010
Member Is Offline
Mood: Reactive
|
|
Next attempt: I tried the U-tube , thanks to @Panache.
I bent a 15mm pipe and filled it with the rxn mxture Na2CO3 + 2C a little bit more C than stoiciometrically requirfed (weight ratio Na2CO3 : C = 106
: 24) to remove the last traces of oxygen in the vessel. I had a receiver made from a glass jar of which the top half is cut off.
I had to tap with a hammer to the tube to ensure the mixture gets in the U.
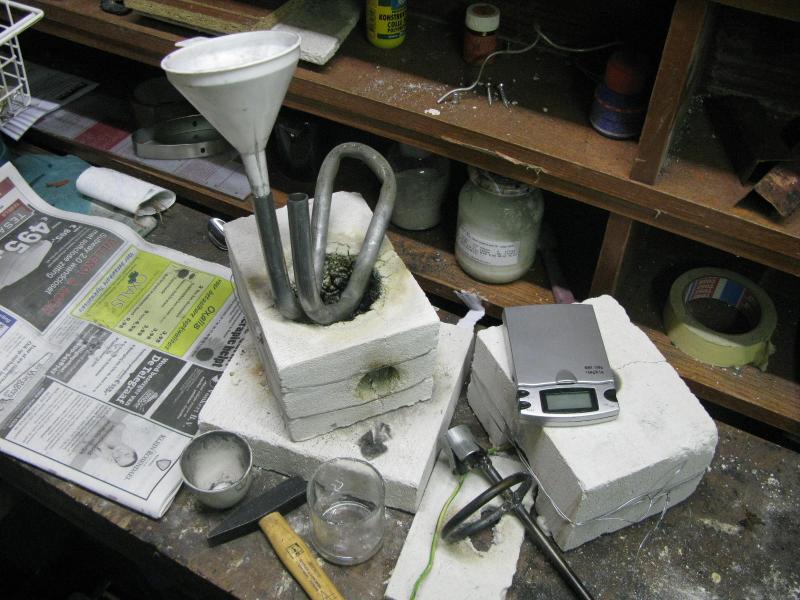
Then I put the stuff into the furnace and protected the oil bath with a piece of Fermacell fire retardant board with some pieces of Rockwool roof
isulation on it. Here the setup except the lid of the furnace.
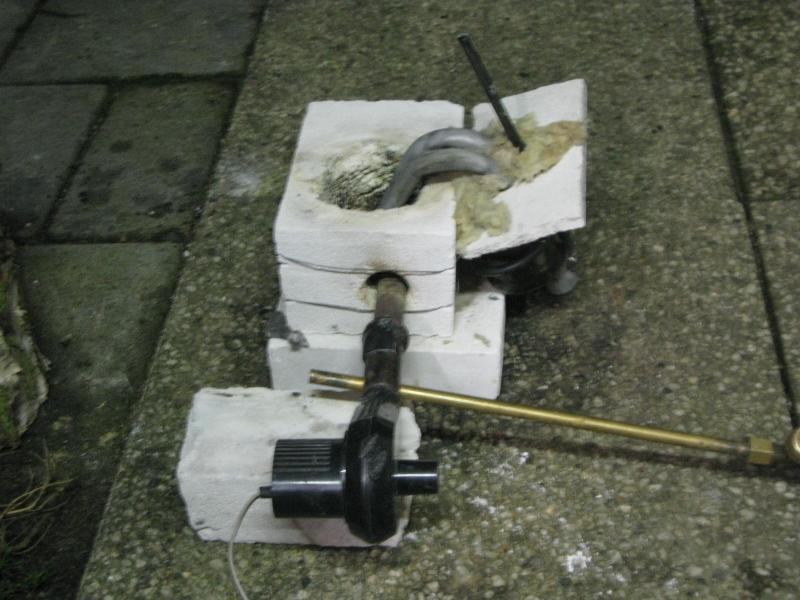
After a few minutes the oil began to bubble heavily and sodium colored flames appeared above the Fermacell board and the tubes got yello hot so I had
to lower the flame.
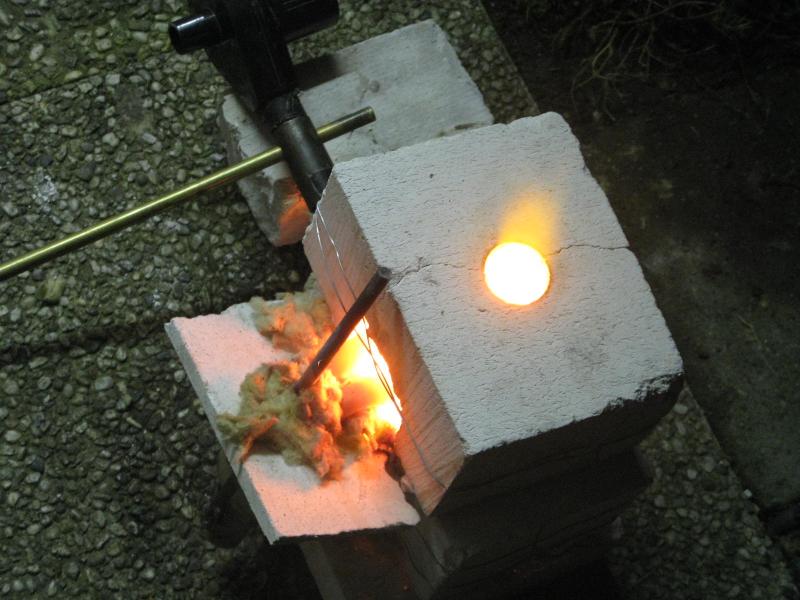
But despite all these measures, the oil caught fire. I put some Rockwool blankets over the receiver Then I saw what I feared: ywellow flames and
white fumes from the furnace and looking inside I saw bright yellow flames coming from the hotetst part of the U. The 9/11 effect: overheating steel
even without seams it collapsed under its own weight like the Twin Towers.
Now the oil is still cooling and I am curious whether some sodium is there......
This WAS the retort ....
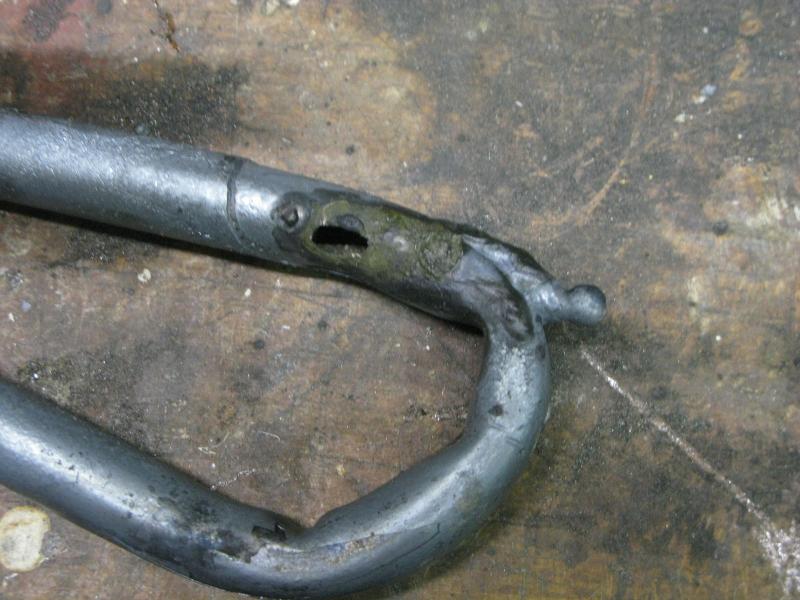
As seen here it is clearly MELTED .....
I googled many times to search how commercial production took place by the end of the 19th century.They also used this approach. As there was no
stainless steel at that time what did they use for the vessel ??
Later on I poured some water into it and this happened .....
<object width="425" height="344"><param name="movie" value="http://www.youtube.com/v/FnzfSYaONmA?hl=en&fs=1"></param><param
name="allowFullScreen" value="true"></param><param name="allowscriptaccess" value="always"></param><embed
src="http://www.youtube.com/v/FnzfSYaONmA?hl=en&fs=1" type="application/x-shockwave-flash" allowscriptaccess="always" allowfullscreen="true"
width="425" height="344"></embed></object>
[Edited on 2010-10-2 by metalresearcher]
|
|
peach
Bon Vivant
   
Posts: 1428
Registered: 14-11-2008
Member Is Offline
Mood: No Mood
|
|
Looks like you have sodium there.
Nightinhawk, a guy on youtube who's fireworks cracky, has had a lot of luck with the NaOH / Mg thermite style pot method.
There are a lot of variables in the retort. If you're not going with upgrading the steel yet, I would suggest knocking the atmosphere out as a
variable altogether, by purging it with argon. If you don't already have it, or use it on a regular basis, or have a neighbour who can donate his
cylinder for a few minutes, it may be cheaper and easier to change the steel.
In the olden days, I expect they managed by dealing with low yields, tons of fiddling and a lot of care. Knowing the olden dayzers, they were probably
using very thick walled tubing too.
I seriously think you should upgrade to stainless. There are grades specifically designed to retain their strength at high temperatures, for use in
jet engines. I'm sure it's possible with lesser materials if they were doing it all the way back then, but those were their particle accelerators at
the time. The stainless will be more expensive, but not by any significant amount compared to the high purity crucibles and platinums.
Surely you must be getting tired by now of seeing those things seize up / melt? The tiredness and your time has a price as well.
A fairly obvious warning that I doubt you need, but be careful adding water from something like a cup or watering can. I've seen one guy do the same
in one of these videos and the sodium spat back at him, and got him. If you suddenly make a break through, there could be a lump of it trapped in the
tube, which may then explode when the watering can method is applied.
My own silly story along those lines... I was melting lead water mains pipe in a pan buried in a fire. I knew there was water still on it because I
could hear the violent boiling as I added them and they melted. One of them didn't play along and, with the bore acting as a barrel, shot molten lead
12ft across the garden in a shotgun effect. Luckily, I was siding to the side of it when that happened. But that's only boring old lead.
I don't know how true it is, but I've heard stories from people running industrial induction melters that have mentioned something to do with the load
being incorrect, or the power supply, and the magnetic activity actually shotgunning the charge vertically back out. 
<object width="660" height="525"><param name="movie"
value="http://www.youtube.com/v/908rjHQ5mmc?fs=1&hl=en_GB&color1=0x5d1719&color2=0xcd311b&border=1"></param>&
lt;param name="allowFullScreen" value="true"></param><param name="allowscriptaccess" value="always"></param><embed
src="http://www.youtube.com/v/908rjHQ5mmc?fs=1&hl=en_GB&color1=0x5d1719&color2=0xcd311b&border=1"
type="application/x-shockwave-flash" allowscriptaccess="always" allowfullscreen="true" width="660" height="525"></embed></object>
<object width="660" height="525"><param name="movie"
value="http://www.youtube.com/v/faorfmRkCv0?fs=1&hl=en_GB&color1=0x5d1719&color2=0xcd311b&border=1"></param>&
lt;param name="allowFullScreen" value="true"></param><param name="allowscriptaccess" value="always"></param><embed
src="http://www.youtube.com/v/faorfmRkCv0?fs=1&hl=en_GB&color1=0x5d1719&color2=0xcd311b&border=1"
type="application/x-shockwave-flash" allowscriptaccess="always" allowfullscreen="true" width="660" height="525"></embed></object>
[Edited on 1-10-2010 by peach]
|
|
metalresearcher
National Hazard
  
Posts: 758
Registered: 7-9-2010
Member Is Offline
Mood: Reactive
|
|
Quote: Originally posted by peach  | Looks like you have sodium there.
Nightinhawk, a guy on youtube who's fireworks cracky, has had a lot of luck with the NaOH / Mg thermite style pot method.
|
I know this video I'll have to try it yet, get sink cleaner as a source for NaOH.
I am already considering this, first finding a steel workshop here in the neighborhood where they process SS tubes of 1/2".
I think bending can only be done while hot (which I already do with the ordinary steel tubes).
Quote: Originally posted by peach  |
A fairly obvious warning that I doubt you need, but be careful adding water from something like a cup or watering can. I've seen one guy do the same
in one of these videos and the sodium spat back at him, and got him. If you suddenly make a break through, there could be a lump of it trapped in the
tube, which may then explode when the watering can method is applied.
My own silly story along those lines... I was melting lead water mains pipe in a pan buried in a fire. I knew there was water still on it because I
could hear the violent boiling as I added them and they melted.
|
When doing this I wore a face mask for the reasons you mension. I am experiences with metal melting , not lead but copper silver and gold, which are
much hotter. Once I had an explosion when pouring gold in a metal mold which I thought it was moisture free. Luckily I wore a face mask and the mold
was placed in a wok so all gold particles could be collected and nothing was lost.
|
|
peach
Bon Vivant
   
Posts: 1428
Registered: 14-11-2008
Member Is Offline
Mood: No Mood
|
|
Try asking at the garages who do exhaust repairs. Some of them may be able to get stainless for fancy manifolds. I saw the guys making one at a metal
fabrication place I did my work experience at in my teens, and their primary product was oil storage tanks for industrial heaters, ladders and beer
keg carts. 
Provided the wall thickness of the stainless is low, it shouldn't need heating. Swagelock is high purity stainless, and can be bent quite easily into
complex tubing arrays. The Kurt ?Schreckling? guy who wrote "How to build gas turbine" bends the blades on the Inconel turbine blank with a little
tool that looks exactly like a tap & handle, but with a slot in the end for the blade rather than a screw thread.
Hottest thing I've melted and cast? Aluminium. I was originally going for iron but then the garage needed knocking down and rebuilding from the
foundations up.
Still got the iron contact capable refractory though, so it's probably in the works. The only reason I'd be interested in iron and those temperatures
is a bit of artistic casting and machine tools. But the latter requires specific control of things like the carbon and the way it comes out on cooling
down to produce a casting that isn't a pile of rubbish. As you probably know, there are many, many different cast iron structures in terms of the form
the carbon deposits in. The right ones last forever, the wrong ones fracture on cooling.
[Edited on 2-10-2010 by peach]
|
|
metalresearcher
National Hazard
  
Posts: 758
Registered: 7-9-2010
Member Is Offline
Mood: Reactive
|
|
The problem when bending the tubes is that they flatten or get very kinky at the bend location. A plumber's pipe bender (local hardware shop $50) can
resolve this problem but the radius is too large to fit the U in a furnace.
EDIT: I just found by Google an interesting article on tube bending:
http://www.hinesbending.com/BASICTUBEBENDINGGUIDE.pdf
[Edited on 2010-10-2 by metalresearcher]
|
|
watson.fawkes
International Hazard
   
Posts: 2793
Registered: 16-8-2008
Member Is Offline
Mood: No Mood
|
|
A old-timer trick for bending is to
pack the tube with sand first. The sand has to stay put and not slough out under pressure, so that means sealing the ends, too. For that, a wood plug
screwed into the side of the tube suffices.
|
|
Rogeryermaw
National Hazard
  
Posts: 656
Registered: 18-8-2010
Member Is Offline
Mood: No Mood
|
|
look up a hickey bender. they are made for bending tight radius or unusual bends. don't know what they would call it in germany but they can produce
much tighter bend than a normal pipe bender. ya i know it sounds weird but it's no joke. i have experience with them. i have run so much electrical
conduit i still have dreams about it.....
not sure exactly what bend radius you can produce but it may help with your kinking problem.
[Edited on 2-10-2010 by Rogeryermaw]
|
|
metalresearcher
National Hazard
  
Posts: 758
Registered: 7-9-2010
Member Is Offline
Mood: Reactive
|
|
@watson.fawkes :
Your sand-filling trick seems to work ! I bought 2 kg of bird cage sand at a pet supply shop for only $2. I squeezed the tube at one end, filled it
with sand and hammered firmly a wooden slat about 3cm, completely filling the diameter, into the other end and sawed the wood off. Then I bent it
(heard the sand crackling) and the result was considerably less flattening, wrinkles and kinks.
|
|
peach
Bon Vivant
   
Posts: 1428
Registered: 14-11-2008
Member Is Offline
Mood: No Mood
|
|
Yep, I know of the sand trick also.
Plumbers use a big spring that goes in the pipe and does a similar thing, stops it kinking in on it's self. The sand works better because it's finer
and makes more contact, so it spreads the load and stops it collecting in points as wrinkles and kinks.
They use ice for bending the pipes on brass instruments. Fill with water, freeze, bend, let it melt out, for a super smooth wrinkle free result.
To expand the tubes to have them tightly mate with each other for joining, they push a slightly too large BB into the pipe, then force it through by
pushing slightly smaller ones in behind it. The big one, obviously, stretches the pipe.
Plumbers have expanding hand tools that push into the end of the pipe, the grips are squeezed and a reverse collet type thingymehjiggy opens the pipe
a bit for soldering. Saves buying more preformed joints and cuts down the number of joints. The fewer joints you have, the quicker the work gets
finished.... 
It's possible squirty expanding foam may work as a replacement for ice, but it'll be more prone to collapse I expect. And it'll be a bitch to clean
out by comparison.
[Edited on 2-10-2010 by peach]
|
|
Rogeryermaw
National Hazard
  
Posts: 656
Registered: 18-8-2010
Member Is Offline
Mood: No Mood
|
|
there is also a spreader tool that a/c guys use that looks like a series of progressively larger cones stacked on top of each other. you insert it
into the end apply hammer liberally and voila! spreads the end to be a perfect fit on another pipe the diameter of the original. i'll dig mine up and
post a pic.
|
|
watson.fawkes
International Hazard
   
Posts: 2793
Registered: 16-8-2008
Member Is Offline
Mood: No Mood
|
|
Quote: Originally posted by Rogeryermaw  | there is also a spreader tool that a/c guys use that looks like a series of progressively larger cones stacked on top of each other
| I've got a Ridgid one, tool #562 for 1/4 ID tubing. Here a link to Google Products for one; photo from their site. The smallest diameter goes inside the tubing, the second one is the expanded diameter, the third
one acts as a stop to keep it from getting too far down the tube. They're a standard tool for mating coolant lines to be brazed.
|
|
metalresearcher
National Hazard
  
Posts: 758
Registered: 7-9-2010
Member Is Offline
Mood: Reactive
|
|
Thanks for all tips ! Ialready bent a steel pipe with sand and with success.
But I am looking around where I can get SS tubes as this is better. I also need them for other (non-chemistry) purposes.
I tried another approach with the steel tube: put it into a steel container filled with sand. This enables more evenly distribution of the heat over
the vessel as there is no direct contact with the gas flames.
After 10 minutes of heavy bubbling of the oil the bubbling suddenly stopped, but I did not see Na colored flames or fumes coming from the sandbox.
The result afterwards was a little bit of Na metal in the tube.
The sand stops the leaking if there is a leak.
But I won't do this experiment again untilI have SS tubes.
EDIT: And I am thinking about using the same fine sand for capturing the Na and eliminating the stinking, polluting and flammable oil.
<hr />
Here a top view of the tube vessel in the sandbox after the session.
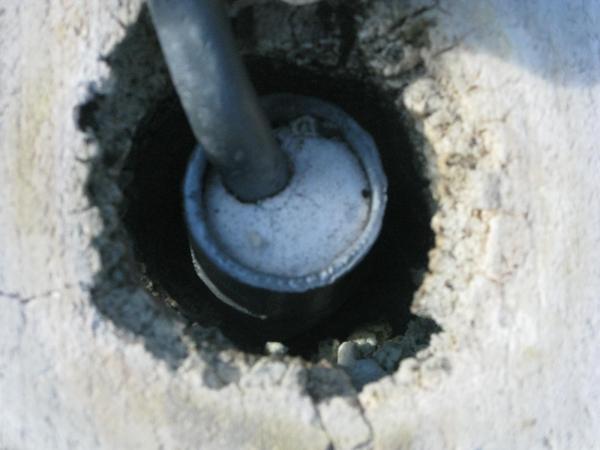
<hr />
Here a view of the complete setup taken out of the furnace after the session.
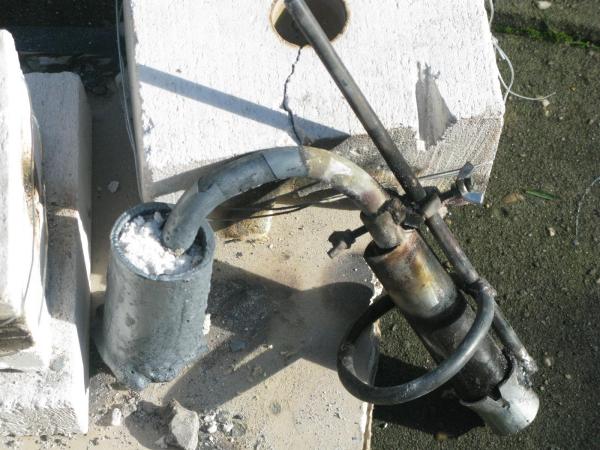
[Edited on 2010-10-3 by metalresearcher]
|
|
Pages:
1
2
3
4 |