Pages:
1
2
3
4 |
metalresearcher
National Hazard
  
Posts: 758
Registered: 7-9-2010
Member Is Offline
Mood: Reactive
|
|
Welded retorts are useless > 1000oC
@Rogeryermaw
Thanks, but I cannot find the phpsphorus thread in this forum with the search option.
But I can imagine how it works as P4 can be made by distilling it off from heating Ca3(PO4)2 + charcoal + SiO2 in a similar terort to 1300oC (how did
you do this in a wood fire ??).
Anyway, yesterday I did a third attempt but now with Al = Na2CO3 which (according to http://www.crct.polymtl.ca/equiweb.php) should yield Na vapor @ 900oC and higher.
But NO Na vapor appeared and I tried to prevent to heat the retort over 1200oC by keeping the propane flame very low, but what happened ?
Unlike the Na3CO3 + charcoal mix, no fumes appeared but bright yellow flames from the (welded) bottom of the retort and after cooling I saw holes
(slag from the weld dissolved in liquid Na2CO3 ??) and the bottom of the furnace was glassy.
Maybe the slag holes in the weld are the result of my poor welding experience and/or the steel was zinc plated.
So the Na2CO3 leaked out but where is the aluminum gone ??
Next time I'll use a SEAMLESS retort with only a screw cap on the top.
[Edited on 2010-9-21 by metalresearcher]
|
|
Rogeryermaw
National Hazard
  
Posts: 656
Registered: 18-8-2010
Member Is Offline
Mood: No Mood
|
|
http://www.sciencemadness.org/talk/viewthread.php?tid=65&... is where the retort design is pictured. look further to see the results of
experimentation. the temps are easy to reach with forced air on a wood fire but the technique takes some practice. you have to periodically cycle the
blower on and off. if you just let it run it can cool your retort by moving air over it.
[Edited on 21-9-2010 by Rogeryermaw]
|
|
peach
Bon Vivant
   
Posts: 1428
Registered: 14-11-2008
Member Is Offline
Mood: No Mood
|
|
I'm right in the middle of trying to make sparkly glow in the dark paint, so I'll have to come back and reread the new bits more thoroughly later.
With the inert flush, as much as I like Nitrogen, Argon would probably be a good idea at such high temperatures. Helium would most definitely
not be a good idea (it'll blow out quickly at those kinds of temperatures, and it costs a bomb).
You could give a nickel plating a try before going to the higher priced options. Len is using Nickel, albeit at significantly lower temperatures. He
is also using a lot of current however.
If that's not good enough, plate the crucibles with something from the Platinum group. Iridium is a good idea (for those unsure, Iridium is better for
this kind of thing because it can withstand huge temperatures and still not begin reacting, whilst also retaining it's strength; it's used in some ion
gauges for vacuum work, where the gauge needs to remain close to perfect and tiny traces of atmosphere in the pumping down stages may begin creating
skin oxides, and to prevent the gauge mechanically distorting / skewing when it gets hot).
Nickel is cheap enough to do the entire crucible from it. The platinums are going to make you bankrupt before you've heated anything. Plate the
suckers on. The bulk material can act as the support, with the platinum group acting as the liner. If you're not stirring away or grinding things up
in there and are gentle cleaning it out, the liner should remain in tip top condition for a good while. They use this same idea in high pressure
reactors. Steel for the chamber, borosillicate / quartz / teflons for the liner (FEP, FPA, EFTE & PTFE are all almost identical in terms of their
chemical resistance, but differ a little with regards to their electrical / mechanical / thermal processing properties).
If you need to use a pure platinum group metal for the entire crucible, the idea is out the window immediately versus Len's electro method, which is
going to be far cheaper and it doesn't involve cylinders or thousands of degrees.
[Edited on 21-9-2010 by peach]
|
|
metalresearcher
National Hazard
  
Posts: 758
Registered: 7-9-2010
Member Is Offline
Mood: Reactive
|
|
New try: no leaks anymore
Here again I tried Na2CO3 + powdered charcoal:
Heated it till a bright yellow 1200-1300oC:
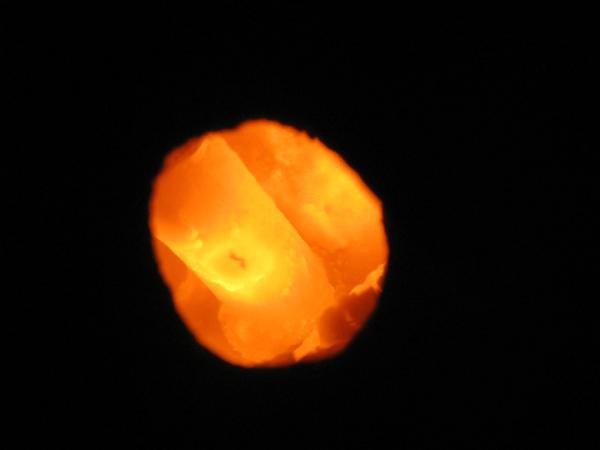
It appeared brighter than on the photo I needed dark goggles to view into the furnace and I saw the outside of the retort was covered with molten
Fe3O4 due to the slightly oxidizing flame.
The oil bath remained bubbling and no fumes coming off the furnace. Then I stopped it after running 15 minutes and let it cool down. Now the welds
kept sealed.
After cooling I tried to reopen the threaded knee but is was so tight that the only option was:

After applying the grinder here a detailed view of the outside retort (was a 3/4" steel tube with a bottom welded onto it). The damage due to
oxidizing is clearly visible.
After opening up I saw some unreacted stuff at the top of the retort, due to the narrowness of the retort.
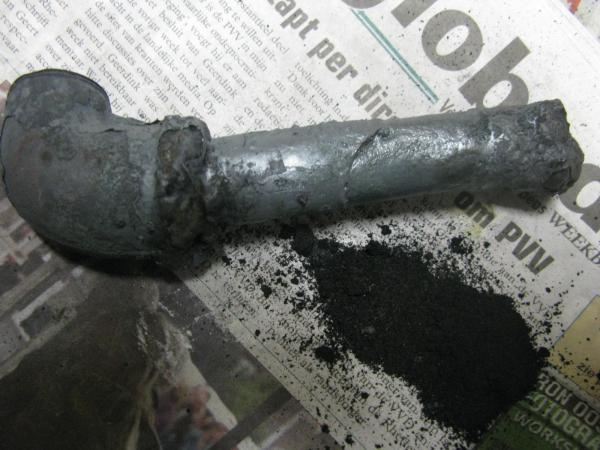
Here a detail of looking into the condensing pipe into the oil bath. Possible some tiny amounts of metallic sodium might be there.
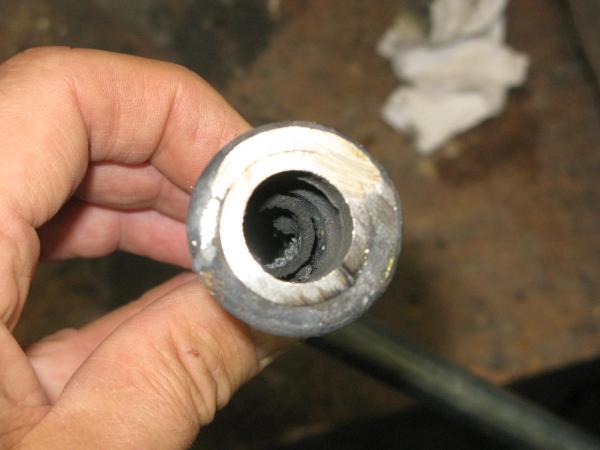
So I filled it with water. I did not see a reaction but I heard a very little bubbling probably due to reaction of a few milligrams of Na with water.
The next time I will use a wider steel tube which is not zinc plated (easier to weld) and thus a larger amount of mixture in it.
|
|
Formatik
National Hazard
  
Posts: 927
Registered: 25-3-2008
Member Is Offline
Mood: equilibrium
|
|
Quote: Originally posted by metalresearcher  | Unlike the Na3CO3 + charcoal mix, no fumes appeared but bright yellow flames from the (welded) bottom of the retort and after cooling I saw holes
(slag from the weld dissolved in liquid Na2CO3 ??) and the bottom of the furnace was glassy.
Maybe the slag holes in the weld are the result of my poor welding experience and/or the steel was zinc plated. |
The aluminium mixture is much more reactive. It does not need any of the same type of heat as charcoal for sure. The bright yellow flame from the
bottom (no flames should be shooting out of the bottom of the container, it suggests too much air is in your apparatus). The flames are due either to
the nature of the deflagration of the mixture (since it is a more reactive redox mixture), or carbon monoxide which is combusting, possibly alongside
combusting sodium vapor (air in there: if you don't have a lot of mixture and the apparatus is airtight, then inert gas flush could help - argon or
nitrogen are indeed good choices).
Quote: | So the Na2CO3 leaked out but where is the aluminum gone ?? |
The reaction may be: 3 Na2CO3 + 4 Al = 2 Al2O3 + 3 CO + 6 Na. So if you can't see any grey aluminium, I'd assume it converted to Al2O3.
Quote: Originally posted by peach  | With the inert flush, as much as I like Nitrogen, Argon would probably be a good idea at such high temperatures. Helium would most definitely
not be a good idea (it'll blow out quickly at those kinds of temperatures, and it costs a bomb). |
Nitrogen works excellent though, I think everyone has been falling back on argon because of the thought alkali might combine with the nitrogen to form
a nitride at higher temperatures. Most don't. Guernsey and Sherman (J. Am. Soc. 47 [1925] 1933) couldn't establish nitride formation by heating sodium
with regular nitrogen to: 800 C to 1000 C, not even in the presence of catalysts, like Fe. Sodium, potassium, rubidium, and caesium don't react when
heated with nitrogen. Lithium does react when heated with nitrogen however, forming the nitride. More references on all this can be found in Gmelin.
|
|
Fleaker
International Hazard
   
Posts: 1252
Registered: 19-6-2005
Member Is Offline
Mood: nucleophilic
|
|
Quote: Originally posted by peach  | I'm right in the middle of trying to make sparkly glow in the dark paint, so I'll have to come back and reread the new bits more thoroughly later.
With the inert flush, as much as I like Nitrogen, Argon would probably be a good idea at such high temperatures. Helium would most definitely
not be a good idea (it'll blow out quickly at those kinds of temperatures, and it costs a bomb).
You could give a nickel plating a try before going to the higher priced options. Len is using Nickel, albeit at significantly lower temperatures. He
is also using a lot of current however.
If that's not good enough, plate the crucibles with something from the Platinum group. Iridium is a good idea (for those unsure, Iridium is better for
this kind of thing because it can withstand huge temperatures and still not begin reacting, whilst also retaining it's strength; it's used in some ion
gauges for vacuum work, where the gauge needs to remain close to perfect and tiny traces of atmosphere in the pumping down stages may begin creating
skin oxides, and to prevent the gauge mechanically distorting / skewing when it gets hot).
Nickel is cheap enough to do the entire crucible from it. The platinums are going to make you bankrupt before you've heated anything. Plate the
suckers on. The bulk material can act as the support, with the platinum group acting as the liner. If you're not stirring away or grinding things up
in there and are gentle cleaning it out, the liner should remain in tip top condition for a good while. They use this same idea in high pressure
reactors. Steel for the chamber, borosillicate / quartz / teflons for the liner (FEP, FPA, EFTE & PTFE are all almost identical in terms of their
chemical resistance, but differ a little with regards to their electrical / mechanical / thermal processing properties).
If you need to use a pure platinum group metal for the entire crucible, the idea is out the window immediately versus Len's electro method, which is
going to be far cheaper and it doesn't involve cylinders or thousands of degrees.
[Edited on 21-9-2010 by peach] |
We need to stop this iridium and platinum metal talk! First off, an iridium retort, if such a thing EVER existed, would cost the equivalent of dozens
of tons of potassium or sodium. The cost would be in fabrication. Ever melted it? I have and it's not fun! Also, you're free to try plating it. We
hobbyists can barely plate an adherent platinum layer! Your best bet would just be to use nickel and flush it out with argon. You don't need or want
platinum or its sister metals.
Nickel is the obvious, cheap choice. Copper would also probably work half decent. Plate it with nickel. Nickel is what's used for cost effective
alkali fusions. Otherwise it's Zr, Ag, or Au.
Neither flask nor beaker.
"Kid, you don't even know just what you don't know. "
--The Dark Lord Sauron
|
|
Satan
Hazard to Others
 
Posts: 126
Registered: 1-5-2009
Member Is Offline
Mood: No Mood
|
|
For high temperature work I made this metal flask, and for sealing threads and space between upper and lower portion of flask I used sodium silicate
paste with some filler (rated to 1350 C).
When welding galvanized steel, you will poison yourself without proper ventilation. Zinc catches on fire, and there is cadmium in fumes from this
smoking flame (old welder told me that). To weld such steel soak galvanized parts in dilute acid for one day (or to the point when hydrogen is no
longer seen bubbling).
In one post there was mentioned teflon for use in sealing threads... For such temperatures its foolish, go read on decomposition products of teflon
and how long those nasty substances stay in your system (years!).
|
|
metalresearcher
National Hazard
  
Posts: 758
Registered: 7-9-2010
Member Is Offline
Mood: Reactive
|
|
I am thinking about something similar, but with no screws and nuts as at > 1200oC lots of Fe3O4 scale destroy the threads .BTW small zinc plated
steel I heat to red hot until no fumes appear anymore. I do this outdoors upwind or in the fume hood, but the idea of diluted H2SO4 might be good
(does this not dissolve the steel as well ?).
Even 3/4" thread gets unusable when heated to over 1200oC.
I think about a steel pipe (wider than the 3/4" I used) with a flat bottom welded onto it with a 90 degree knee as i your picture above it.
Yesterday I cut through the narrow pipe retort with Na2CO3 + Al which I used earlier this week with the angle grinder and I found that on (the cooler)
top of the pipe were pieces of Al metal . So parts of the mixture left unreacted due to clogging the pipe.
Hence the larger diameter.
|
|
peach
Bon Vivant
   
Posts: 1428
Registered: 14-11-2008
Member Is Offline
Mood: No Mood
|
|
If you're referring to any post I've made about using Teflon for threads, that's for sealing bottles. The stuff is going to melt at less than a
quarter of the temperature you're interested in. The fumes are hydrofluoric acid, which is most certainly worthy of a toxic sticker (as it not only
blisters, not toxic on it's own, it systemically rots calcium out of your nervous system / bones / mucles etc).
Zinc fumes, there's actually a thing called 'welders flue', or 'metal workers flue' which is named after what the guys feel after inhaling too much of
it. Like they have a bad cold.
I'm dissolving zinc right now as part of my glow paint endeavor, the casings of zinc based batteries. I've been experimenting with using different
concentrations and sitting it in boiling 95-98% sulphuric. By far the easiest is to drop the zinc in some battery acid and leave it for a day or more.
The iron in the casings isn't as reactive as the zinc, so it tends to get left floating on the surface. Particularly if I use a little less acid than
I actually need to dissolve the zinc in the first place.
With all these seizing threads, rotting, agreeing with fleaker about the cost and effort of platinums, I would suggest you upgrade to at least
stainless over the iron / steel.
There are quite a few places online selling high quality stainless 'black pipe' style ranges; as opposed to Swagelock, which costs a fortune and is
aimed more at gas work.
Here's an example of one. Of interest is that they sell prethreaded, large ID, fairly long pipe nipples that can be used as is for the hot pot. There
are, of coarse, a number of others selling these fittings that may be a lot cheaper. E.g. the sand cast versions from China. These pipes are designed
to deal with high pressures. You don't need that, so a cheaper version likely won't cause many problems. As fleaker also suggests, nickel plate the
entire bastard if it keeps oxidizing / causing problems.
|
|
Rogeryermaw
National Hazard
  
Posts: 656
Registered: 18-8-2010
Member Is Offline
Mood: No Mood
|
|
ya teflon can be nasty agreed. however the results i have had with it have justified its use for me. all the work i have done with it has been
outdoors in a fairly large furnace and it has served its purpose very well. zinc isn't a lot worse than many other metal fumes. the vapors of burning
metals will all kill you at high enough concentrations. it's always advisable to have good ventilation or perform work of this nature outside. even
just burning l.p. gas can get you from exhaust fumes if the combustion is not perfect. i won't let any of this scare me away from experimentation. all
i can hope is that if i die from my work, it serves to help someone else.
|
|
metalresearcher
National Hazard
  
Posts: 758
Registered: 7-9-2010
Member Is Offline
Mood: Reactive
|
|
Read many posts from you all, thanks for that, but is there anyone who really used the retort setup ?
I am curious about experiences on steel retorts (or what their remains are) after heating to temps over 1000oC.
Saturday I'll build a new one to this design:
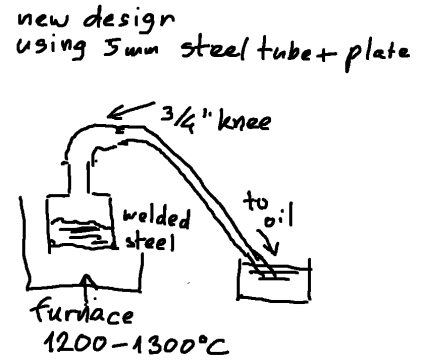
[Edited on 2010-9-23 by metalresearcher]
|
|
Rogeryermaw
National Hazard
  
Posts: 656
Registered: 18-8-2010
Member Is Offline
Mood: No Mood
|
|
well i don't have a way to know exactly what temp i'm reaching but the pipe i have used in the furnace gets bright yellow. i'm using 1" EMT pipe
flattened and welded at one end and a 4" 3/4 rigid nipple welded into the other end. the whole assembly is about 14" long. i have actually been able
to use a couple of them on multiple runs to produce phosphorus with the NaPO3 + Al + SiO2 method. so far the only limiting factor has been getting
slag out of the reactor so i could use it again. it may be that your mixture is eating holes in your reactor?
i wonder if you ran this reaction without silicon dioxide would it yield aluminum phosphate and sodium? or would sodium's higher reactivity stop any
reaction from proceeding at all?
[Edited on 23-9-2010 by Rogeryermaw]
[Edited on 23-9-2010 by Rogeryermaw]
|
|
metalresearcher
National Hazard
  
Posts: 758
Registered: 7-9-2010
Member Is Offline
Mood: Reactive
|
|
It is very difficult to make the retort airtight
I got some 2" black steel tubes from a scrap yard, so I tried the design as sketched in my previous post. I welded a top and bottom onto it and a
1/2: knee on the top (after dezincking the knee as it was galvanized.
Then I filled the retort with Na3CO3 + C but the result was .....
Leaking welds on the top of the retort. It is very hard to make the seams airtight (read: sodium vapor tight).
In the picture below the yellow flame of the leak is clearly to see. And the oil stopped bubbling. So I stopped the furnace and let it cool down and
will reweld the seams.
@Rogerywemaw: how did you keep the P4 making setup airtight ?
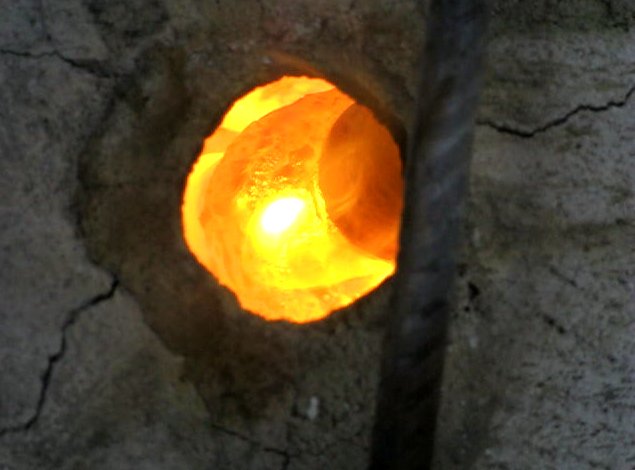
[Edited on 2010-9-25 by metalresearcher]
|
|
Rogeryermaw
National Hazard
  
Posts: 656
Registered: 18-8-2010
Member Is Offline
Mood: No Mood
|
|
i would have to say a mixture of luck and experience. i have been welding for over 20 years. plus, at the threaded sections, people will tell you that
teflon is dangerous and bla bla bla but it works. just don't stand there and huff the fumes. the results speak for themselves. the way i'm using it i
don't think it's vaporizing because after the pipe cools i can peel the old teflon out in one big piece and reapply it.
i also don't think it's that important to remove the zinc unless it will react with your product. burning zinc makes some nasty fumes but if you're
working outside (your videos show you working outside) then just stay upwind from your work area. that's what i do. i may have shortened my lifespan
but i'm still here!
[Edited on 25-9-2010 by Rogeryermaw]
|
|
Formatik
National Hazard
  
Posts: 927
Registered: 25-3-2008
Member Is Offline
Mood: equilibrium
|
|
Zinc will alloy sodium at red-glow according to literature.
|
|
metalresearcher
National Hazard
  
Posts: 758
Registered: 7-9-2010
Member Is Offline
Mood: Reactive
|
|
Smaller scale attempt no leaking anymore
Now I performed a smaller scale test by just using a 15mm steel tube (1/2" inner diameter) of 30cm long which I bent 90 degrees in the center and
squeezed together on one site which I welded together. Then I filled it with Na2CO3 + C so it just filled on the closed side of the bend. So no
threads or other welds anymore which can leak...
I put this closed end into a furnace and the open end in a beaker with motor oil. Then I heated the furnace to 1200oC and saw bubbling in the oil.
Furthermore I saw some precipitation in the oil which I will investigate later.
No leaks appeared as I did not see any sodium yellow flames coming from the bright yellow hot mini retort (bottom right picture: the bright object top
right in the picture is the retort).
I think that the retort of the test yesterday leaked because of the poor welds.
@Rogermeryaw: you are probably a professional welder I am not as I waste 8 electrodes with 100 anp to weld 2 steel plates on both sides of a 2" steel
tube. I feel embarrassed that my welds are such a poor quality....
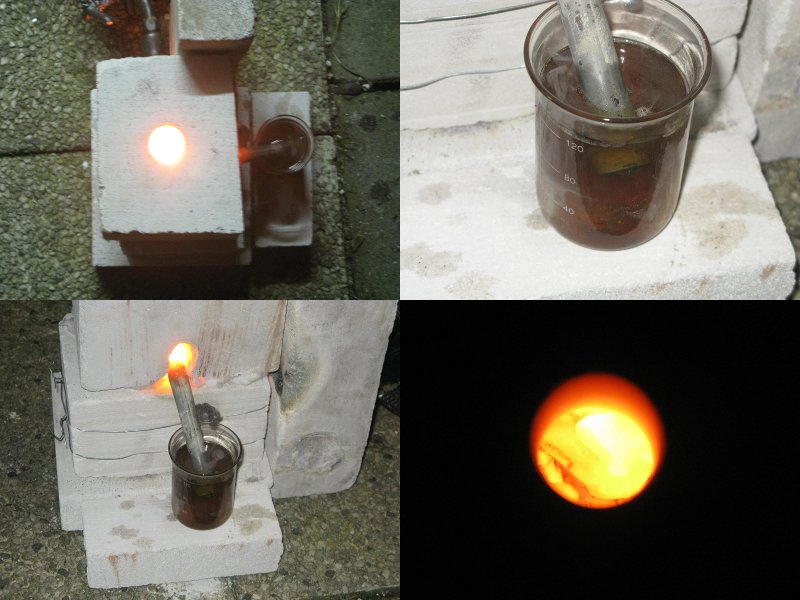
UPDATE : After one hour the precipitation settled at the bottom of the beaker with oil and below a picture of the bottom of the beaker:
Probably no sodium metal but I don't know what the white subsance is.
UPDATE AGAIN: I peeled some substance out of the retort tube and dropped it in water. Yes some bubbling appeared !!!
Then I poured some water in the tube and it started bubbling and hissing and a yellow spark appeared .
YES !!!! I HAVE MADE IT !!! SODIUM METAL !!!!!
But it was frozen in the tube before reaching the oil bath. So I have to preheat the tube a bit more, over 98oC (Na 's melting point).
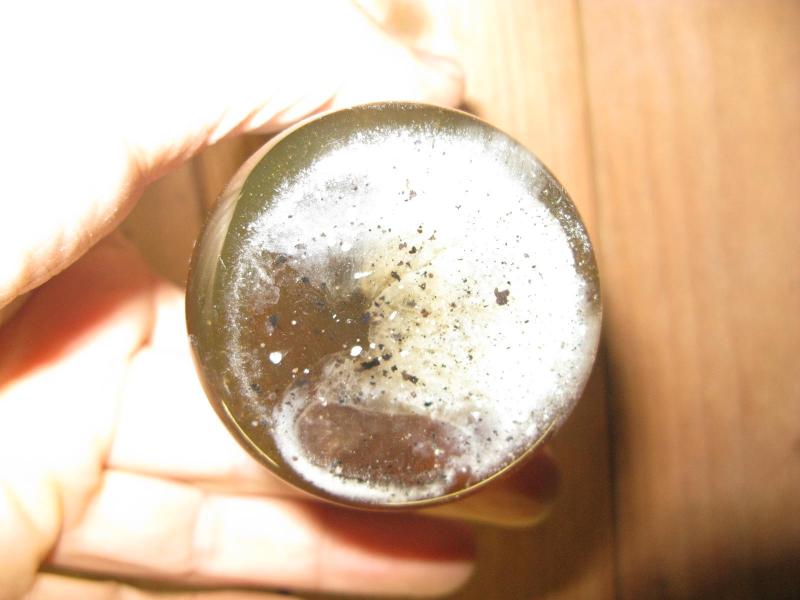
[Edited on 2010-9-26 by metalresearcher]
|
|
Rogeryermaw
National Hazard
  
Posts: 656
Registered: 18-8-2010
Member Is Offline
Mood: No Mood
|
|
Quote: Originally posted by metalresearcher  |
@Rogermeryaw: you are probably a professional welder I am not as I waste 8 electrodes with 100 anp to weld 2 steel plates on both sides of a 2" steel
tube. I feel embarrassed that my welds are such a poor quality....
[Edited on 2010-9-26 by metalresearcher] |
professional no but passionate yes. i started as a child in school and just sort of had an affinity for it. by my third year in industrial metals in
high school i was teaching the first year students (wish i still had my old year books! had some pics of me teaching on the oxy-acetylene rig)
do not ever be embarrassed by your attempts. it's a lot more than many people ever do in their whole lives. besides, i burned a lot of metal learning
the finesse it takes woo it into doing what you want.
[Edited on 26-9-2010 by Rogeryermaw]
|
|
peach
Bon Vivant
   
Posts: 1428
Registered: 14-11-2008
Member Is Offline
Mood: No Mood
|
|
MR, make sure your metal is as clean as you can get it, that the rods aren't the ultra cheap crappy kind and that the welder can dump enough current
through to get it going properly.
To clean things, use an abrasive disc, a sanding disc or a twisted wire wheel cup. All three in an angle grinder, clean just prior to welding so it
can't recontaminate in the meantime. If you put a 75mm sized wire cup in a 3hp angle grinder, it'll annihilate anything on contact and the finish will
look polished to a mirror, without grinding the metal down. And, they squeeze into all the gaps, unlike a disc. But you seriously need a face shield,
as they spit bits of wire out all the time (EYES).
Cheap electrodes won't flux / ignite properly. A guy I used to work for bought 4, 5kg boxes of some that were being thrown out from somewhere. They
were being thrown out for a reason, they were horrible. I've also stick welded with nice 316's and the quality is superb, without even trying it can
look like it's been done with a TIG torch and needed years of experience.
The current is another issue. Theoretically, the arc is hot enough to melt the puddle properly. In practice, if there's not a good amount of current
happening, it'll run too cold, end up brittle, not properly stuck etc. Whilst working for that guy, I told him I'd found a 400amp DC TIG set for
£150. He was laughing and telling me I hadn't. Then I turned up the next day with it and he spent the entire week trying to bargain it back off me
(it was a Thermal Arc, the purple ones). I managed to burn out the industrial, 3 phase wire fuses in the workshop by turning it up.
If you need to, 'cheat'. Use a stick of wood or something to guide the stick in a smooth, constant line. They do it industrially so...
That aside, CONGRADULATIONS on finally getting something that looks right, you've certainly persevered and rapidly as well.
I have a question. Are those normal house building thermo blocks you're using as insulation? Have you got much experience with using them for that?
And how well do they hold up?
I have some real high content alumina refractory. It's incredibly tough to cut and is used to line the ladles in iron foundries (so it has the maximum
temperature rating available for regular, ceramic type refractories). But it also has fairly poor insulating properties. It's used to get the
temperature down to the point where another liner, on the outside, can block the rest of the heat. I've often wondered about, but not tried, using
those thermo blocks as an outer liner for the alumina stuff.
Len has informed us, helpfully, that regular glass wool melts around 800C, so that's another possibility.
I've heard that things like those blocks gradually fall apart over repeated high temperature runs. True, false, how true?
75mm £4, 100mm £7. Used 230mm (9"), 1800W+ (2.5 - 3hp) Makita grinder... there's one on eBay for 99p at the moment.

[Edited on 26-9-2010 by peach]
|
|
Rogeryermaw
National Hazard
  
Posts: 656
Registered: 18-8-2010
Member Is Offline
Mood: No Mood
|
|
a couple of notes: if you are using an arc welder with adjustable currents then you may want to look up a table with regards to current usage based on
metal composition and thickness. also your technique will be the overall judge of the quality of your welds. don't hover too long in one spot or you
can weaken the metal and even burn right through it. the industrial method for producing pretty welds is to use a half circle pattern about 1/4 inch
wide. slower on the bottom half of the circle, left to right then quickly pass over the weld back to the starting point, drop down 1/4 inch and start
your next half circle ect. ect. this technique is mainly for heavier metals quarter inch thick or more. for the thinner stuff you have to move faster
because it vaporizes pretty fast.
|
|
Rogeryermaw
National Hazard
  
Posts: 656
Registered: 18-8-2010
Member Is Offline
Mood: No Mood
|
|
Congratulations MetalResearcher! any plans for a scaled up design? do you think the furnace i used for phosphorus would work well for this? Sodium is
another one of those elements that, while being very useful, is under lock and key by the powers. thanks for your perseverance in this project. keep
up the good work and let us know what developments you make. you know my interest in sodium so i can't wait to give this a try!
|
|
cyanureeves
National Hazard
  
Posts: 744
Registered: 29-8-2010
Location: Mars
Member Is Offline
Mood: No Mood
|
|
good welding advice. you do have to clean and grind down welds to expose wagon tracks(air pockets)and reweld.damn this thread was exciting as heck.i
wanted to shout..monel..inconel.congrats.
|
|
metalresearcher
National Hazard
  
Posts: 758
Registered: 7-9-2010
Member Is Offline
Mood: Reactive
|
|
@peach :
I do have such a steel brush as pictured in your post for my angle grinder, but I didn't use it yet for cleaning the welds, but is is a good idea. Now
I hand brushed it with a steel wire brush.
About the insulating bricks: it is YTONG indoor wall which are available for $3-$5 for a 60x20x7cm block. It is very cheap and amazingly good
insulating and can withstand up till 1400oC. Then it weakens to a pudding like substance.
A furnace like this gets 1300oC within 15 minutes starting from a cold furnace. So the furmace can be reused more than ten times when you don't heat
it over 1400oC.
When using forced draft with a $10 air mattress inflater it gets even hotter with less propane consumption.
@Rogeryermaw :
I already use this 'zig-zag' method, but sometimes I see slag inclusions which tend to leak. That is the reason my rod consumption is so high: I
'repair' these leaks after testing by immersing the retort in water and then applying air pressure on it by a bike pump and then I still see bubbles
appear .....
Upscaling: only when I get the retort COMPLETELY AIRTIGHT, so I have to overcome the welding issues.
First I am going to make K as it freezes at lower temp (63oC) and has a higher vapor pressure (bp 767oC).
Thanks for your tips !
One final question: I use motor oil for capturing the Na metal but there is a fire hazard so close to a hot furnace. Can I also use the non-flammable
vegetable oil ? Or does these fatty acids(?) react with Na or K ?
|
|
peach
Bon Vivant
   
Posts: 1428
Registered: 14-11-2008
Member Is Offline
Mood: No Mood
|
|
Not sure about the fatty acids thing, but it may be an idea to stick with the motor oil.
I'd start bumping the safety up by simply putting a loose fitting lid over the oil. Provided it doesn't start to boil, the lid should help smother it
if it catches.
Fire blankets are sometimes a lot cheaper than extinguishers, particularly if they're a bit grubby. Grubbiness only hurts their wall hanging appeal,
the blanket still works. One of those would help if everything goes tit's up; so you can throw it over.
I'd also FIRMLY fix that can of oil somehow, so it can't topple. Oil fires are, of coarse, not fun at all.
I was having a read about salt earlier, and discovered regular table salt is actually the primary ingredient in powder fire extinguishers (or some of
them anyway), with some other very easy to get things. The salt smothers the fire, simples. Speaking of oil fires, I wonder if we could make an SM
recipe of powder to throw over them.
The cost of commercial powder extinguishers is the cylinder, pressurization and subsequent standardization; it has to sit for a decade and then be
usable by a complete noob who's never read the back of one, instantly, and from a long distances. A 'throw it by hand' method may not be much more
than the cost of a bucket of salt.
[Edited on 27-9-2010 by peach]
|
|
watson.fawkes
International Hazard
   
Posts: 2793
Registered: 16-8-2008
Member Is Offline
Mood: No Mood
|
|
Quote: Originally posted by peach  | Not sure about the fatty acids thing, but it may be an idea to stick with the motor oil.
I'd start bumping the safety up by simply putting a loose fitting lid over the oil. Provided it doesn't start to boil, the lid should help smother it
if it catches. | Oil only starts a fire if it gets hot enough so that its vapor pressure is significant. So
don't let it get hot. Make that lid an insulating lid, say, a piece of metal stuck to an insulating firebrick with construction adhesive. Put a heat
sink on the side of the oil can to keep it cool. Or, once you scale up, running cooling coil through the oil like moonshiner.
|
|
peach
Bon Vivant
   
Posts: 1428
Registered: 14-11-2008
Member Is Offline
Mood: No Mood
|
|
Heatsink / water cooling ideas are good and simple to incorporate. Although, I'd go with the heatsink one over the water, since the latter could
easily make things exponentially worse if something goes wrong (see; Mythbusters, kitchen fires)
The flash point of typical motor oil seems to be around 200C (400F). A number of solders melt around that temperature, so a simple, cheap way to watch
for it is to stick a bit of solder wire on the tin and look out for it going liquid. Rest it at sloping angle and it'll run from one place to the
other, making it easier to see.
The metal processing guys often do something similar, with sample blocks of clean metals to judge the temperature reliably. There are also a number of
crayons you can get to write on blocks. The crayon melts when it's hit that temperature, which is handy for annealing / tempering (not the same thing)
and so on. If you watch videos of them making steel ingots etc, you'll sometimes see them scribbling on the blocks with things like this, whilst
they're steaming hot.
Medical units can buy bags with similar things built in, that read STERILIZED when they've been cooked in the autoclave for the correct amount of
time.
Going yet more off topic, they do something similar with gamma ray processing. Stick tags to the pallets to check they've been dosed correctly.
Temperature indicating crayons, from 40 to 1200C in 120 steps at 1% accuracy

[Edited on 27-9-2010 by peach]
|
|
Pages:
1
2
3
4 |