Fery
International Hazard
   
Posts: 1015
Registered: 27-8-2019
Location: Czechoslovakia
Member Is Offline
|
|
allyl alcohol
This is continuation of the synthesis describe in the allyl bromide thread. For allyl bromide, there is OK to use allyl alcohol + water azeotrope. But
for an allyl alcohol ester preparation it is better to have higher alcohol concentration than 72,9 wt %.
here the preparation of allyl alcohol from anhydrous glycerol and 85% formic acid:
https://www.sciencemadness.org/whisper/viewthread.php?tid=15...
the whole thread with allyl bromide:
https://www.sciencemadness.org/whisper/viewthread.php?tid=15...
Here my attempt to concentrate the alcohol:
The distillates (approx 500 ml) were processed this way:
150 g of K2CO3 added (it was an overkill, less could be enough, a lot of did not dissolve), some CO2 evolved (very likely formic acid) and was shaken
few times during 24 hours, then separated the upper layer which was distilled using Vigreux column. On steam bath, 50 ml of condensate collected with
about 2 ml of water phase separated at the bottom (azeotrope allyl formate + allyl alcohol + H2O), thermometer in distillation adapter showed 80 C, no
more distillate obtained, although about 400 ml of mixture still stayed in the distillation flask.
So the steam bath removed and the flask heated using flame burner and boiling plate.
Additional 250 ml of of distillate collected upto 94 C (so totally 300 ml with the first portion from steam bath), and then last 60 ml portion boiling
above 94 C collected separately which was the most concentrated allyl alcohol obtained.
The total 300 ml of distillate in first fractions will be later treated with NaOH to decompose allyl formate and to obtain allyl alcohol again (this
one with lower concentration, then will be salted out using K2CO3 to increase its concentration).
Another interesting concentration method is distilling at slightly reduced pressure 200-300 mm Hg where azeotreope containing 90% of allyl alcohol
should distill, boiling points 60 C at 200 mm Hg, 70 C at 300 mm Hg.
Azeotrope at normal pressure boils at 88,2 C, contains 72,9 wt% of allyl alcohol and has density 0,905 g/ml. Pure allyl alcohol b.p. 97 C.
Densities of allyl alcohol + water mixtures at 20 C are:
0,920 g/ml (65%)
0,911 g/ml (70%)
0,902 g/ml (75%)
0,893 g/ml (80%)
0,884 g/ml (85%)
0,875 g/ml (90%)
0,865 g/ml (95%)
0,854 g/ml (100%)
the table of densities is here: http://www.orgsyn.org/Content/pdfs/procedures/CV1P0042.pdf
I determined the density of my 60 ml last fraction using 50,0 ml calibrated volumetric flask and obtained this result:
29,720 g empty
73,197 g full
43,477g of allyl alcohol 50,0 ml
density 0,86954 g/ml
so according the table of densities it is 93 wt% allyl alcohol
quite good
The allyl formate present in the mixture behaved similarly to benzene - breaking the azeotrope allyl alcohol + H2O, carrying out some of H2O when
distilling ternary azeotrope allyl formate + allyl alcohol + H2O (which is probably richer in H2O than binary azeotrope allyl alcohol + H2O), then
72,9 wt% binary azeotrope distilled which carried out more of water and partially concentrated allyl alcohol distilled at the end.
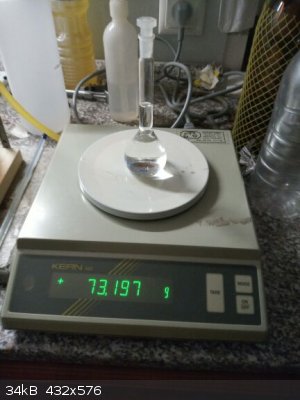
[Edited on 24-2-2020 by Fery]
|
|
Fery
International Hazard
   
Posts: 1015
Registered: 27-8-2019
Location: Czechoslovakia
Member Is Offline
|
|
anhydrous allyl alcohol
To the 300 ml fraction was added 10 g NaOH which dissolved completely and formed bottom water layer. Then another 10 g added which did not dissolve
completely. This was refluxed for 30 minutes and the bottom water layer was separated and discarded. The upper alcohol layer was refluxed 2x with 30 g
K2CO3 each time and the lower water layer discarded, the second rfx was much less efficient than the first one (a lot of K2CO3 did not dissolve at
all) so I decided to change the way to go (the idea when allyl formate distilled in which water bottom layer formed).
The alcohol was transferred into 1 L RBF, the 60 ml fraction (93 wt %) added too and then 200 ml of hexane (if you are focused on maximizing the
yield, probably 50 ml would be enough... hexane boils with some amount of allyl alcohol on distillation which decreases the yield). Boiling chips
added and the flask was stirred in hand vigorously to ensure some of hexane entered the bottom phase and some water and allyl alcohol entered the
upper phase (otherwise sudden vigorous boil onset which could not be coped by the condenser when they mix later spontaneously during rfx !!!). RBF was
inserted into a steam bath, Dean-Stark trap adapter attached with rfx condenser and distillation started. Bottom water phase was collected from the
trap adapter and every 15 ml was treated with K2CO3, after its treatment the bottom water layer discarded and upper concentrated alcohol phase
returned back into the apparatus. This was very slow process and approx. 75 ml of distillate from Dean-Stark trap apparatus was treated by K2CO3 from
which the alcohol layer was returned into the apparatus through the condenser and small funnel on its top after the Dean-Stark trap was again fully
filled with new bottom layer (that ensured that the most of the returned layer did not sink into the Dean-Stark trap but passed through its arm into
the RBF, only after that process the Dean-Stark trap was drained and the liquid treated with K2CO3 as described).
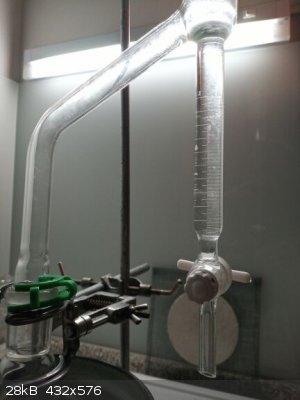
https://en.wikipedia.org/wiki/Azeotrope_tables
Ternary mixture H2O : allyl alcohol : n-hexane boils at 59,7 C and has composition 5 : 5 : 90 wt % which separates spontaneously into upper layer with
composition 0,5 : 3,6 : 95,9 wt% which is returning back into the RBF automatically and bottom layer 80,9 : 17,7 : 0,4 (this layer is treated with
K2CO3 and then returned back into the apparatus manually through the top of condenser after the Dean-Start trap again fully filled with fresh bottom
layer).
This was very slow process and lasted 7 hours. When the treatment with K2CO3 did not yield significantly some water to discard, the dehydratation was
done. Another sign was that the rate at which the bottom phase separated decreased significantly (3-4 times) - there was still some bottom phase but
now without H2O, it was allyl alcohol without water now. The hexane was distilled out in a way that it was drained from the Dean-Stark trap (this is
very quick process for only few minutes).
Allyl alcohol from the 1 L RBF was poured into 500 ml RBF and distilled from an oil bath, collecting fraction 96-98 C (b.p. 97 C lit.).
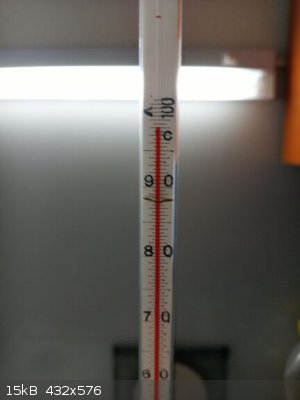
Some K2CO3 stayed in the RBF (it is slightly soluble in allyl alcohol and very soluble in water present in allyl alcohol).
yield:
fraction boiling upto 96 C 56,1 g (250 ml FBF with glass stopper behind the yellow hose)
fraction boiling 96-98 C 131,1 g (amber flask in the front right)
200 ml of hexane enriched with allyl alcohol was kept for allyl valerate esterification (250 ml FBF with glass stopper behind the 56,1 g fraction of
the alcohol).
[Edited on 27-2-2020 by Fery]
|
|
Boffis
International Hazard
   
Posts: 1867
Registered: 1-5-2011
Member Is Offline
Mood: No Mood
|
|
Nice write-up Fery! I particularly like the idea of partially drying the allyl alcohol by azeotropic distillation before using potassium carbonate or
the like.
I have had rather mixed results with azotropic distillation to drive esterification so its good to hear of a success.
[Edited on 29-2-2020 by Boffis]
|
|
Fery
International Hazard
   
Posts: 1015
Registered: 27-8-2019
Location: Czechoslovakia
Member Is Offline
|
|
Boffis it was very slow process (7 hours) but quite efficient. I've chosen a solvent not miscible with water which has its b.p. far enough from the
product (allyl alcohol b.p. 97 C) and which was not too much toxic (unlike benzene). Not pure hexane but a mixture of isomers of hexane could be
easily obtained as Pharma Benzine (hydrogenated fraction with b.p. But the lower b.p. the less water in the azeotrope. So e.g. pentane could be even
easier to separate from allyl alcohol but less efficient in removing water (partial pressure of water much lower at lower temperature).
Here they used CCl4 for dehydratation http://www.orgsyn.org/Content/pdfs/procedures/CV1P0042.pdf
Perhaps it was done in less hours than 7 and during last hours only allyl alcohol separated in the Dean-Stark Trap adapter, I did not check that.
|
|
Johnny Windchimes
Hazard to Self

Posts: 61
Registered: 28-5-2019
Member Is Offline
Mood: Sorry, it's my chimes~!
|
|
This channel may interest you, scoop it up before it gets deleted; unfortunately I'm pretty sure he's going for the synthesis of Safrole via grignard
ultimately....
https://www.youtube.com/watch?v=Npa9Twp3dlo
|
|
Fery
International Hazard
   
Posts: 1015
Registered: 27-8-2019
Location: Czechoslovakia
Member Is Offline
|
|
Thx for the video link, very nice video.
By my experience the inert gas was not necessary (steam replaced the air quickly).
What was important was the heating intensity - too weak heating = acrolein byproduct, too strong heating = too little of glycerin monoformate. Heating
the flask for the first time when it is full of glycerin and for the third time when there is approx 1/3 of original glycerin required different
heating intensity (if you apply the same intensity as for the first run then it is heated approx twice faster for the third run).
What is ultimately is a thermometer inserted into the reaction flask, once it reaches 195 C start collecting the product, upto reaction reaches
temperature 260 C. The distillate below 195 C was collected separately (it is high in formic acid which could be recovered).
And instead of wasting NaOH I just led a hose from the vacuum take off adapter to the outside of my house.
I did not stir the content in the reactor flask, the boiling did the task instead.
Do not use CaCl2 for drying alcohols (used in the video).
|
|
Fery
International Hazard
   
Posts: 1015
Registered: 27-8-2019
Location: Czechoslovakia
Member Is Offline
|
|
allyl alcohol from glycerin and formic acid, for the second time in my life
this is my second synthesis of allyl alcohol in my life, now in advance of preparation of allyl phenoxyacetate (pineapple fragrance)
apparatus: 1 L RBF with 2 necks, 1 neck with thermometer 0-300 C, 1 neck with empty 25 cm long column, distillation head with thermometer 50-150 C,
condenser, vacuum take off adapter to which a hose is connected and its end was led OUTSIDE OF BUILDING (second choice is to submerge into solution of
NaOH), 250 ml receiving flask
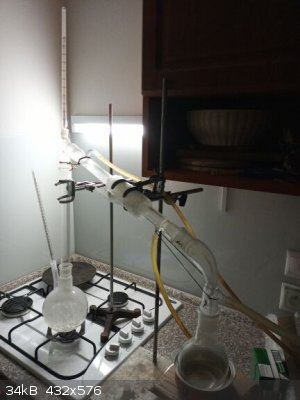
serie No 1
Into 1 L RBF was placed boiling chips, 330 g of anhydrous glycerin, 100 g of 85% formic acid and thoroughly mixed well (not so easy, glycerol is quite
thick syrup, it's better to mix the glycerin in a beaker with most of the acid, pour into flask using a wide (!) funnel (to keep ground glass joints
clean to apply a grass to them later easily) and wash the beaker with the remaining acid and add it into the flask)
serie No 1, round No 1
The 1 L RBF was heated with flame burner using smallest possible flame.
Time +45 minutes the distillation started, T inside flask 130 C, T in head 102 C which raised to 105 C for the most of time.
Time +90 minutes T in head fell to 100 C and was further decreasing, nothing distilled temporary, the content from receiving flask collected and empty
flask attached back into the apparatus. 48,8 g of water and diluted formic acid obtained.
The column was insulated with one sheet of newspaper turned around it in few layers.
When T in flask raised to 210 C the distillation resumed, T in head 97C.
Time +165 minutes the T in flask 255 C, T in head 70 C and falling down, no more distillate in condenser, 108,9 g allyl alcohol collected in receiving
flask which was removed and kept aside
content in 1 L flask at the beginning and at the end
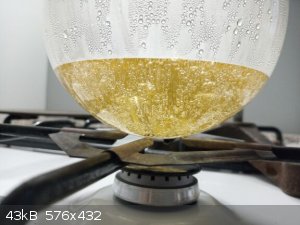
serie No 1, round No 2
thermal insulation from column removed, when the content in 1 L RBF temperature fell to 100 C, 100 g of 85 % formic acid added (now it mixes well
spontaneously as the glycerin is hot), started to heat using the smallest possible flame, which was few times turned off and on to allow reflux for 20
minutes (always just before vapor reached the distillation head the flame was turned off) - this time was to allow esterification to proceed
time +20 minutes T in flask 125 C, T in head 102 C, H2O and diluted formic acid distills, T in head reached 105 C in few minutes and stayed at that
temperature for long time, the removed thermal insulation from column allows some formic acid to flow back into the reaction
time +60 minutes, T in head decreasing to 100 C and further falling down, no more distillate condensing, T in flask 220 C, 55,9 g H2O + formic acid
collected from receiving flask, column thermally insulated with newspaper
then allyl alcohol distills, T in head 97 C, droplets in column observed caried up by CO2 stream evolution from the reaction (that's why I used an
empty column to allow most of droplets to return back into the flask)
time +90 minutes T in head below 70 C and falling down further, no more distillate condensing, T in flask 255 C, 80,5 g allyl alcohol collected from
receiving flask
serie No 1, round No 3
thermal insulation from column removed, when the content in 1 L RBF temperature fell to 100 C, 100 g of 85 % formic acid added, started to heat using
the smallest possible flame, which was few times turned off and on to allow reflux for 20 minutes
time +20 minutes distillation of H2O and diluted formic acid started, T in flask 120 C, T in head 102 C which later raised to 105 C for most of time
time +60 minutes, T in head 100 C and falling down, no more distillate condensing, 62,0 g H2O + diluted formic acid collected in receiving flask,
removed and kept aside
thermal insulation of column installed and soon distillation resumed, now allyl alcohol distilling, T in head 97 C
time +100 minutes, T in head below 70 C, no more distillate condensing, T in flask 260 C, end of round 3, end of serie 1, 53,3 g allyl alcohol
collected from receiving flask, kept aside and thermal insulation from column removed
the content in 1 L RBF approx 50-100 g of red glycerol
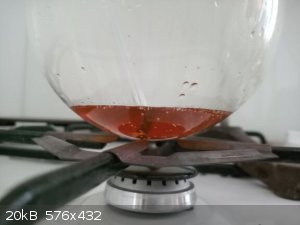
serie No 2
serie No 2, round No 1
into the red remaining glycerol in 1 L RBF was added 270 g of fresh anhydrous glycerol mixed with 100 g of 85 % formic acid and heating started with
lowest possible flame which was few times turned off and on to allow reflux and esterification to proceed for 20 minutes
time +20 minutes, T in flask 130 C, T in head 102 C, distillation of H2O and diluted formic acid, some of formic acid returns back through the column
(that's why thermal insulation of column temporary removed)
time +60 minutes T in flask 200 C, T in head 100 C and falling, condensate from receiving flask removed and kept aside, 48,2 g H2O and diluted formic
acid collected, thermal insulation of column installed back (few turns of newspaper sheet)
soon distillation resumed, now allyl alcohol distilling
time +135 minutes, T in flask 245 C, T in head 65 C and falling, no more distillate condensing, 83,0 g allyl alcohol collected and thermal insulation
from column removed
serie No 2, round No 2
when T in 1 L RBF dropped to 100 C, 100 g 85% formic acid added and heating started with lowest possible flame, which was few times turned off and on
to allow reflux for 20 minutes and the esterification to proceed
time +20 minutes, T in flask 126 C, T in head 102 C, H2O and diluted formic acid distilling, some part of formic acid returns back into the 1 L RBF
through the column
time +25 minutes, T in flask 130 C, T in head 105 C
time +65 minutes, T in flask 210 C, T in head 100 C and falling down, no more distillate condensing, 49,9 g H2O + formic acid removed from receiving
flask
continued heating, thermal insulation to column installed, soon allyl alcohol started to distill
time +120 minutes, T in flask 250 C, T in head dropped to 60 C, no more distillate condensing, 72,5 g allyl alcohol collected from receiving flask,
thermal insulation from column removed
serie No 2, round No 3
when T in 1 L RBF dropped to 100 C, 100 ml 85% formic acid added, heating started with lowest possible flame which was few times turned off and on to
allow reflux for 20 minutes and esterification to proceed
time +20 minutes, distillation started, T in flask 122 C, T in head 102 C and further raising upto 105 C where it stayed for most of time, H2O and
diluted formic acid distilling
time +55 minutes T in flask 215 C, T in head 100 C and falling down, 54,1 g H2O + formic acid collected, thermal insulation to column installed and
continued heating
allyl alcohol started to distill, T in head 97 C
time +115 minutes, T in 1 L RBF 260 C, T in head 60 C, finished, 58,2 g allyl alcohol collected in receiving flask
remainder in 1 L RBF (full flask weighed, then glycerol removed, flask washed with water and dried)
378,9 g - 287,7 g = 91,2 g

the remaining 91,2 g of glycerol could be perhaps later reacted with azeotrope formic acid recovered from distillates (just my idea to use it)
theoretical calculations:
total glycerol reacted 330 + 270 - 91,2 = 508,8 g (5,52 mol)
total 85% formic acid entered the reaction 600 g
total water + formic acid fraction 318,9 g
total crude allyl alcohol fraction 456,4 g
if assuming that the whole difference 330,5 g escaped as CO2 = 7,58 mol which is 1,37 times more than the moles of glycerol reacted. There is a chance
that the glycerol remaining if flask is not pure glycerol, maybe contains some glycerol formate, water, longer carbohydrates etc so more glycerol
reacted... also some acrolein (side reaction) could escape with CO2 as vapors (b.p. 53 C) and maybe some of formic acid decomposed to CO and some of
allyl alcohol as droplets on the walls of flask, column, head, condenser...
workup will follow (recovering some allyl alcohol from H2O + formic acid fraction, I expect distilling it out of the mixture as allyl formate b.p.
83-85 C using a hempel column packed with rashig rings and then decomposing it with NaOH) and concentrating the allyl alcohol fraction (+ decomposing
allyl formate here and neutralisation of formic acid with NaOH, salting out the alcohol using K2CO3 and further dehydratation using Dean-Stark trap
adapter and hexane as a solvent to drive out H2O)
[Edited on 20-10-2020 by Fery]
|
|
Fery
International Hazard
   
Posts: 1015
Registered: 27-8-2019
Location: Czechoslovakia
Member Is Offline
|
|
The fraction weighing 318,9 g (water + formic acid) was poured into 500 ml RBF, boiling stones added, 50 cm Hempel column packed with Rashig rings
attached, insulated with few turns of newspaper, 4 coils of hose turned around the the top of column (just an improvisation instead of regular takeoff
reflux adapter), distillation head with thermometer attached, condenser, vacuum takeoff adapter with outlet to which connected a hose leading outside
of house, 250 ml receiving flask attached to takeoff adapter.
It was fractionated, reflux ratio unknown, seemed to be more drops in receiving flask than dropping back into the distillation flask, 17,3 g of
fraction boiling upto 99 C collected (allyl formate + allyl alcohol + H2O) which was salted out with K2CO3 and yielded 5 ml of allyl formate + allyl
alcohol, only very little of CO2 effervescence observed from the bottom layer (= only very little of formic acid or only very little of the ester
hydrolysis). Then 70 ml of water boiling upto 101 C and 220 ml of fraction boiling upto 107 C collected, at the end approx 5 ml residue stayed in the
distilling flask and something in the column (just when the T reached maximum-boiling azeotropic mixture 107,6 C for azeotropic mixture 77,6 wt%
formic acid and 22,4 wt% water). This diluted formic acid 220 ml fraction will be later used for ethyl formate synthesis.
The 5 ml allyl formate will be later added into main fraction of crude diluted allyl alcohol (456,4 g) and processed further (hydrolysis with K2CO3).
In this experiment I focused on recovery of formic acid without necessity to waste hydroxide to neutralize it and obtain its salt. The recovered
diluted formic acid is OK for ethyl formate synthesis using the method of esterification by reactive distillation. I did not measure its density either titrate its
concentration, I plane just to squeeze as much formic acid from it as possible in the form of ethyl formate.
just a lame attempt to improve the column performance (increase reflux ratio)
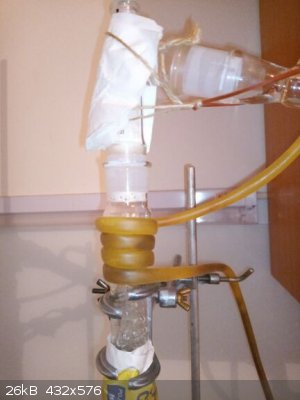
allyl formate in the first fraction immiscible with water, picture from top and bottom
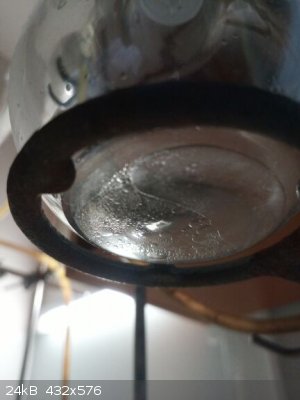
5 ml of allyl formate obtained (top layer) in the first fraction boiling upto 99 C weighing 17,3 g (later salted out using K2CO3 with only very little
of CO2 effervescence from the bottom layer = only traces of formic acid or only very little of hydrolysis of the ester)
|
|
Cou
National Hazard
  
Posts: 958
Registered: 16-5-2013
Member Is Offline
Mood: Mad Scientist
|
|
Allyl alcohol boils at 97 C, and the hexane-water azeotrope boils at 61 C. You might be able to use hexane as a dean-stark solvent for making esters,
and not have to concentrate the allyl alcohol. I don't know if the boiling point of allyl alcohol is low enough to enter the trap and mess up water
separation. the only way to find out is to try it out.
[Edited on 11-3-2020 by Cou]
|
|
Fery
International Hazard
   
Posts: 1015
Registered: 27-8-2019
Location: Czechoslovakia
Member Is Offline
|
|
To 1 L RBF was put 105 g K2CO3, boiling chips, 456,4 g of crude allyl alcohol (outside of building, CO2 evolution due to formic acid and allyl
formate). 25 cm empty column attached (to serve as an air back condenser for reflux in first phase and simple inefficient column in the second phase),
distillation head with thermometer, condenser, vacuum take-off adaper to which outlet a hose leading outside of building was connected, 500 ml
receiving flask.
Using oil bath it was refluxed for 30 minutes at such a low heating that the empty short column managed to condense all vapours (hydrolysing allyl
formate).
Then heating increased and allyl alcohol distilled out, distillation started at 80 C, collected everything upto 100 C.
When weighing the remainder if the distillation flask, the weight was increased by 80 g, this was very likely due to H2O, some of CO2 escaped so the
amount of water removed could be slightly higher. Manipulating the residuum in distilling flask was without tearing (weighing etc). About half of the
residuum crystallized after cooling down to room temperature (KHCO3, K2CO3 very likely, maybe K formate too).
The distillate was treated the same way again, now with 55 g of K2CO3 (perhaps it could be done more conveniently at once using 160 g K2CO3 instead of
105 g + 55 g ???), this second treatment certainly destroyed last traces of allyl formate and further concentrated the allyl alcohol. Now little of
K2CO3 stayed undissolved even after refluxing and heating, which is the optimal situation Now the T in head quickly raised and established to 84 C (when approx 5 ml of distillate collected), then 86 C (approx 15 ml distillate
collected) and further raised only slowly, 88 C when 100 ml collected, 90 C when 150 ml collected, 91 C when 250 ml collected, at the end peak T
raised to 93 C and after some time it started to fall down and drops of water appeared on the inside walls of column instead of previous smooth
alcohol surface (which was so smooth that it was invisible). When weighing the remainder in distillation flask it showed that 20 g of water removed
from the allyl alcohol (again no tears as almost all allyl alcohol already distilled off).
Yield, density, concentration of allyl alcohol was not measured/calculated yet. Tomorrow further dehydratation using hexane and Dean-Stark trap
apparatus is going to follow. Lachrymator kept directly in the receiving flask which was quickly and well stoppered when detaching from the vacuum
take-off adapter.
The apparatus after cooling down was disassembled outside of building.
This setup avoids the necessity to change reflux to distillation - an unnecessary step leading certainly to massive tearing.
This method avoids using separatory funnel and thus significantly decreases the exposure to the lachrymatory compound (today no tears). When
distilling carefully only negligible amount of water distills from saturated K2CO3 solution at the end of distillation and watching distillation head
thermometer could tell when to stop the distillation and also watching the inside wall of the column helps (the first distillation the T raised to 100
C and the second distillation the peak T was 93 C). The uninsulated 25 cm short column reflux ratio was approx 1:1 when calculating drops returning
back into distillation flask and drops falling into receiving flask. Also the distillate is free of K2CO3 unlike when salting out the allyl alcohol
with K2CO3 after which it contains 2,6 % of K2CO3.
according this:
https://sci-hub.st/10.1016/j.fluid.2017.10.025
anhydrous CaCl2 should be good for concentraing the alcohol during distillation
https://www.freepatentsonline.com/2179059.html
CH2Cl2 was used for break azeotrope
here they investigated NaCl (the less powerful, salted out allyl alcohol from 70 to 80 %), various K phosphates and K2CO3 (salted out allyl alcohol
from 70 to 95%)
https://data.epo.org/publication-server/rest/v1.0/publicatio...
using these salts it is possible to concentrate allyl alcohol from a mixture of 70% allyl alcohol + 30% water to 5-10% water
To 300 ml of a solution comprising 70.1% of allyl alcohol and 29.9% of water was added 90 g of potassium carbonate (anhydride), and the mixture was
shaken at room temperature for 10 minutes. A part of the salt was left undissolved, but when the mixture was allowed to stand still, the liquid phase
was separated into two phases.
When the allyl alcohol phase was analyzed, it was found that the water content was reduced to 5.4% and the salt content was 2.6%. In the aqueous
phase, the allyl alcohol content was as low as 0.13%.
https://data.epo.org/publication-server/document?iDocId=3681...
https://data.epo.org/publication-server/pdf-document/EP86108...
the most important experiment:
To 300 ml of a solution comprising 70.1% of allyl alcohol and 29.9% of water was added 90 g of potassium carbonate (anhydride), and the mixture was
shaken at room temperature for 10 minutes. A part of the salt was left undissolved, but when the mixture was allowed to stand still, the liquid phase
was separated into two phases. When the allyl alcohol phase was analyzed, it was found that the water content was reduced to 5.4% and the salt content
was 2.6%. In the aqueous phase, the allyl alcohol content was as low as 0.13%.
Dipotassium hydrogenphosphate (anhydride) reduced H2O to 5% in upper phase, allyl alcohol in water phase was only 0,013% and solubility of the salt in
allyl alcohol only 0,01%.
Potassium phosphate reduced H2O to 4,8% in upper phase.
apparatus, don't forget to connect a hose to the vacuum take-off adapter and lead it outside of building, CO2 evolved caries out some amount of allyl
alcohol which is terrible powerful lachrymator !!!
ground glass joints are not transparent which indicates that I did not use grease, but I used PTFE (teflon) sleeves instead
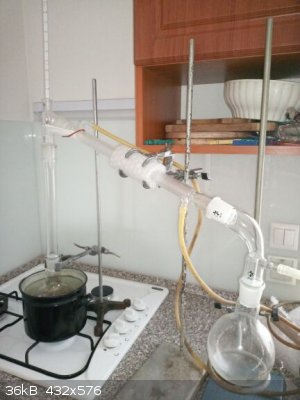
smooth surface inside of column while allyl alcohol distilling (my hand and battery is there only to force my camera to focus to the correct distance)
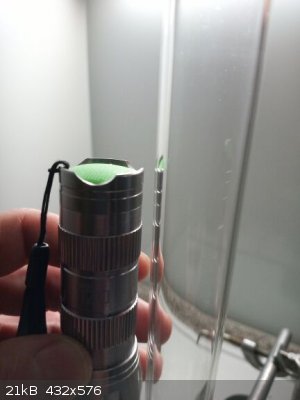
end of distillation, water is distilling
|
|
Fery
International Hazard
   
Posts: 1015
Registered: 27-8-2019
Location: Czechoslovakia
Member Is Offline
|
|
To the 1 L 2-neck RBF was poured 330 g of the crude allyl alcohol from previous steps, boiling stones added.
50 ml of hexanes fraction added (distilled medicinal petrolether through 50 cm hempel column packed with rashig rings, fraction 60-80 C collected so
various isomers of hexane), the hexane was at first used to wash in the original flask containing allyl alcohol and this was only then poured into 1 L
RBF (this washes out allyl alcohol and makes manipulation with glass almost tearless). Also a funnel was used to pour liquids to prevent wetting
ground glass joints thus reducing future leak of lachrymator.
Using Dean-Stark trap apparatus 160 ml of bottom layer collected from the trap after 160 minutes (approx 10 ml every 10 minutes) then the collected
volume ceased (last 3 ml during last 15 minutes).
Distillation interrupted and the apparatus was let to cool down (to be reused later).
The collected distillate in 500 ml RBF was treated with anhydrous K2CO3 added incrementally until it stopped to fully dissolve (75 g totally) flask
tightly closed with a stopper for as much of time as possible. The bottom layer was pipetted out using a balloon attached to a pipette and undissolved
and wet K2CO3 was let in the flask. To the 500 ml RBF were added boiling stones (to prevent bumping in the case the crystals of K2CO3 will dissolve on
heating) and from that 100 ml of allyl alcohol + hexane + water was collected as a distillate.
This 100 ml of allyl alcohol was added back into the 1 L RBF with Dean-Stark trap containing already dehydrated allyl alcohol with hexanes (using the
second neck fitted with only a stopper) and dehydrating process was resumed, now collecting 30 ml of bottom layer from the trap (at the end the rate
of bottom layer formation decreased).
The content remained in 1 L RBF was poured into 500 ml RBF, boiling stones added and distilled through 50 cm long Hempel column (column internal
volume 100 ml) packed with Rashig rings without insulation and without head for taking reflux at desired ratio (the ratio was approximately 3-5 drops
returning back into the distillation flask and 1 drop into receiving flask).
Fraction boiling below 88 C kept aside (hexanes + azeotropes of allyl alcohol + hexanes) could be used for future allyl alcohol dehydratation (though
I do not yet plane anything such)
Fraction boiling 88-96,5 C weighed 102,7 g (approx 80-90% allyl alcohol)
Fraction boiling 96,5-97 C weighed 111,2 g (anhydrous allyl alcohol), at the end the T started to cease when the volume of remainder in distillation
flask was only small
https://en.wikipedia.org/wiki/Azeotrope_tables
ternary mixture H2O : allyl alcohol : n-hexane boils at 59,7 C and has composition 5 : 5 : 90 wt % which separates spontaneously into upper layer with
composition 0,5 : 3,6 : 95,9 wt% and bottom layer 64,4 : 34,8 : 0,8 wt%
according the attached EP86108306NWA1.pdf example 3, K2CO3 is able to salt out allyl alcohol and reduce H2O from 30% (azeotrope) to 5,4%, K2CO3
content in upper allyl alcohol layer 2,6%, allyl alcohol content in bottom phase 0,13%.
Attachment: EP86108306NWA1.pdf (575kB) This file has been downloaded 361 times
It is definitely necessary to distill out the allyl alcohol from the K2CO3 after salting it out otherwise 2,6 % K2CO3 in allyl alcohol binds a lot of
water and makes hexane/Dean Stark trap apparatus dehydratation method very slow.
Also don't forget to always close every apparatus and lead a hose from its outlet outside of building. Also reduce the time allyl alcohol can
evaporate from any open vessel. It is much more toxic than other alcohols and very potent lachrymator.
apparatus with Dean-Stark trap
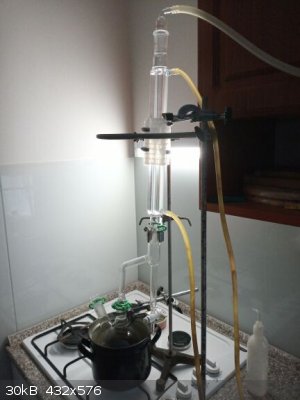
first 10 ml collected in the trap
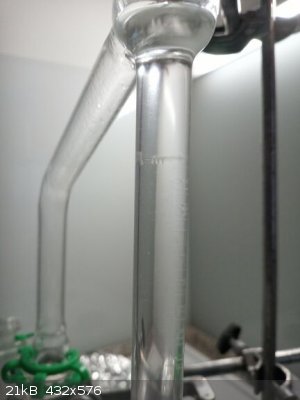
at the end 160 ml of bottom layer collected from the trap (into 500 ml RBF on the right side which was already salted out using 75 g of K2CO3), the
remainder in the 1000 ml RBF on the left side contains hexane and dehydrated allyl alcohol
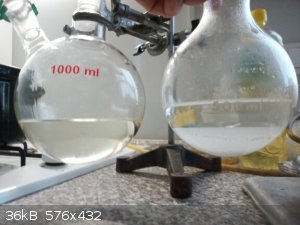
the bottom layer from salted out alcohol was pipetted out using a pipette and balloon, boiling stones added and distilled out directly from the 500 ml
flask which yielded 100 ml of mixture of hexane + allyl alcohol + water which was then poured back into the left flask containing already dehydrated
allyl alcohol with hexane to which Dean-Stark apparatus is still attached and then dehydratation resumed (it is necessary to azeotropically dehydrate
allyl alcohol free of K2CO3 as K2CO3 binds water)
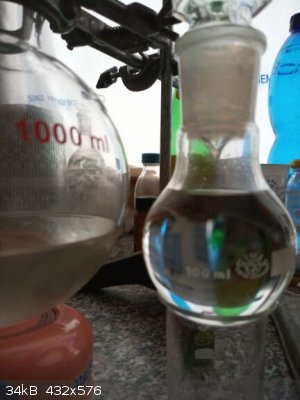
final distillation through colum
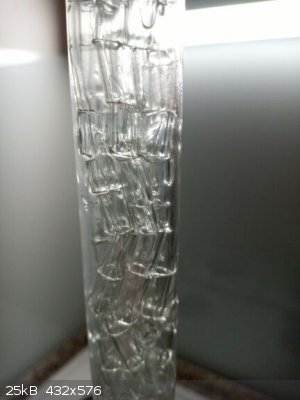
everything boiling upto 88 C kept aside (could be used in future allyl alcohol dehydratation)
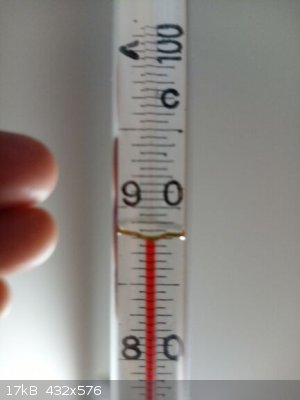
not fully anhydrous but still quite concentrated (approx 80-90%) allyl alcohol collected between 88-96,5 C
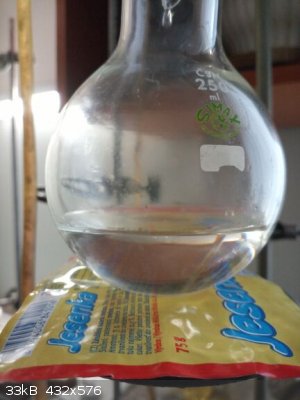
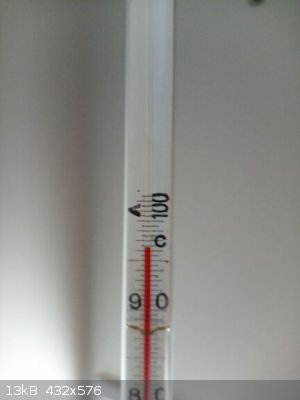
concentrated allyl alcohol collected 96,5-97 C, at the end the T ceased when the remainder in distillation flask was too small
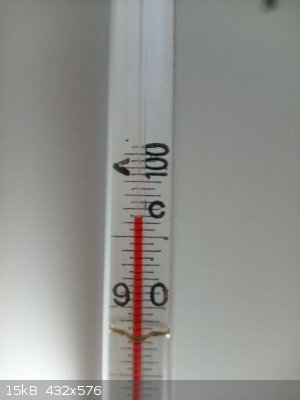
[Edited on 9-11-2020 by Fery]
|
|
Boffis
International Hazard
   
Posts: 1867
Registered: 1-5-2011
Member Is Offline
Mood: No Mood
|
|
Has anyone thought about trying this reaction with higher poly-hydroxyalkanes and sugar alcohols such as dulcitol, mannitol, xylitol, sorbitol and
erythritol?
I raise this point because, recently I stumbled across a couple of papers or articles looking at various chemicals that can be produced from biomass
and their transformation into more useful/ higher value chemicals. Many processes are fermentation based and beyond most amateurs. However, I found
one paper on the effect of formic acid on xylitol and glycerol and another on the erythritol to 3,4-dihydroxy-THF (1,4-anhydro-erythritol). Another
conversion I saw indicates that this can be dehydrated to furan and also that 1,2-glycols of longer chains can be converted to 1-alkene. Xylitol looks
like it may yield furanmethyl formate etc whereas xylose yield furan-carboxaldehyde (furfural). While more aggressive treatment gives
2,4-pentadiene-1-ol.
Childers et al.; A practical and scaleable preparation of 1,4-anhydro-erythritol; Org. Process Res. and Dev.; 2006; v10; p934-936
Arceo et al.; Efficient di-dehydroxylationmethod for the biomass derived polyols glycerol and erythritol; Chem. Comms.; 2009; p3357-3359
|
|
|