Pages:
1
2 |
Arcaeca
Hazard to Self

Posts: 70
Registered: 24-8-2019
Location: Kansas, USA
Member Is Offline
Mood: brøthér, can you spare some B̲̺̹̙̑́̓́ͧ̎ͭ̈́͜L̰̦̼̻͈͖̺͔̇̇̿ͪ̓̃̽ͦŲ̘̲̻͔̀͌͑͑̊͛̑̀͊̕E̐ͮͯ͆̔̾͘͏҉̥̫
|
|
Making ultramarine
It me, the pigment guy
It occurred to me that since I have sulfur powder laying around from when I was going to try to use it to make CaS (until I found out that it's easier
to just reduce CaSO4 by burning it with C in a crucible), I might as well try to use it to make ultramarine. The procedure listed by
Wikipedia requires powdered sulfur, powdered charcoal, sodium carbonate, sodium sulfate and iron-free kaolin, although I know HTME has made it before
without (as far as I know) the sodium sulfate. You mix them all together (100 parts kaolin, 100 parts sodium carbonate, 60 parts powdered sulfur and
12 parts charcoal, according to https://pubs.acs.org/doi/10.1021/ed026p552) and then heat the living crap out of it, at least 750 C, for several hours.
I have powdered charcoal and powdered sulfur; I have calcium carbonate (chalk) but opted to use some charcoal/wood ash which I gather is probably
mostly sodium or potassium carbonate. The problem is the kaolin; I've purified clay from my backyard before by filtering most of the
dirt/sand/twigs out of it, so I have clay on hand (even dried clay that I can grind up), but I'm fairly sure it's not kaolin - if for no other reason
than it has a reddish-brownish tinge to it that pure kaolin does not.
But when I did grind it up into a powder and put all 4 of these things tightly packed in a 6 oz graphite crucible - covered with a rock for half that
time as a makeshift cover to approximate anaerobic conditions - and heated with a blowtorch for 3 hours, the result was... grey. Maybe a slight bluish
undertone, but not blue.
Anyone know how pure the ingredients have to be to get a good result?
|
|
phlogiston
International Hazard
   
Posts: 1379
Registered: 26-4-2008
Location: Neon Thorium Erbium Lanthanum Neodymium Sulphur
Member Is Offline
Mood: pyrophoric
|
|
Wood ash is not mostly sodium or potassium carbonate. I've extracted potash and fund the yield pretty low for a given volume of ash. Most of the
volume at least is something else. I suspect it is mostly silica.
Wikipedia specifically states that the clay used is to be iron-free. No reference given though.
If your clay is not white, iron is very likely among the impurities.
Are you limiting yourself to use only materials you can source yourself from nature or with no extra budget, or would buying some pure kaolin and soda
be allowable?
They are not expensive and that would be the first I'd try.
[Edited on 27-9-2019 by phlogiston]
-----
"If a rocket goes up, who cares where it comes down, that's not my concern said Wernher von Braun" - Tom Lehrer
|
|
rockyit98
Hazard to Others
 
Posts: 283
Registered: 12-4-2019
Location: The Known Universe
Member Is Offline
Mood: no mood is a good mood
|
|
fire brick are made from aluminium silicate which is kaolin.maybe check local pottery store they must have kaolin . sodium carbonate can by from a
supermarket as baking soda (sodium bicarbonate),also Potassium sodium tartrate ( Rochelle salt) will decompose into sodium and potassium
carbonate.sodium sulfate can get from adding baking soda to Epsom salt.
you can get "kaolin" from clay by heating it with molten NaOH and adding water after the mix cool down.filtering the sodium silicates and Aluminate
and leaving it to absorb CO2 from air.
"A mind is a terrible thing to lose"-Meisner
|
|
fusso
International Hazard
   
Posts: 1922
Registered: 23-6-2017
Location: 4 ∥ universes ahead of you
Member Is Offline
|
|
But wheres the blue colour?
|
|
12thealchemist
Hazard to Others
 
Posts: 181
Registered: 1-1-2014
Location: The Isle of Albion
Member Is Offline
Mood: Rare and Earthy
|
|
From wikipedia:
Quote: |
The pigment consists primarily of a zeolite-based mineral containing small amounts of polysulfides. It occurs in nature as a proximate component of
lapis lazuli containing a blue cubic mineral called lazurite. ...... The major component of lazurite is a complex sulfur-containing
sodium-silicate (Na8–10Al6Si6O24S2–4), which makes ultramarine the most complex of all
mineral pigments. Some chloride is often present in the crystal lattice as well. The blue color of the pigment is due to the
S3−• radical anion, which contains an unpaired electron. |
|
|
Arcaeca
Hazard to Self

Posts: 70
Registered: 24-8-2019
Location: Kansas, USA
Member Is Offline
Mood: brøthér, can you spare some B̲̺̹̙̑́̓́ͧ̎ͭ̈́͜L̰̦̼̻͈͖̺͔̇̇̿ͪ̓̃̽ͦŲ̘̲̻͔̀͌͑͑̊͛̑̀͊̕E̐ͮͯ͆̔̾͘͏҉̥̫
|
|
Quote: Originally posted by phlogiston  | Are you limiting yourself to use only materials you can source yourself from nature or with no extra budget, or would buying some pure kaolin and soda
be allowable? |
Best way I know how to explain it is that I'm limiting myself to materials that are easy enough to source that:
I don't have to order them from a chemical supplier (but can get them from e.g. a hardware or grocery store), and
that people in, say, 300 BC would've had access to - so either straight from nature or 1 or 2 steps removed and not requiring any fully
synthetic chemicals that have only been made available by the Industrial Revolution
So obviously kaolin and soda ash fulfill both criteria; it's just that if I can make it work with what I already have on hand, I might as well try,
instead of spending more money that i don't have to.
Quote: Originally posted by rockyit98  | you can get "kaolin" from clay by heating it with molten NaOH and adding water after the mix cool down.filtering the sodium silicates and Aluminate
and leaving it to absorb CO2 from air. |
How much NaOH for how much ground clay? The clay doesn't sinter during the process dos it? And is the CO2 just supposed to make carbonic acid in the
water to neutralize the NaOH? If so can you speed up the process with e.g. HCl?
I'm having trouble finding a pottery supply store nearby to buy kaolin from, which is why I'm looking at making it myself.
|
|
rockyit98
Hazard to Others
 
Posts: 283
Registered: 12-4-2019
Location: The Known Universe
Member Is Offline
Mood: no mood is a good mood
|
|
Quote: Originally posted by Arcaeca  |
How much NaOH for how much ground clay? The clay doesn't sinter during the process dos it? And is the CO2 just supposed to make carbonic acid in the
water to neutralize the NaOH? If so can you speed up the process with e.g. HCl? |
Precious Metal Refining & Recovery, Episode 16: Aluminum From Dirt
Cody'sLab https://www.youtube.com/watch?v=qkyPvhapxQs
"A mind is a terrible thing to lose"-Meisner
|
|
Arcaeca
Hazard to Self

Posts: 70
Registered: 24-8-2019
Location: Kansas, USA
Member Is Offline
Mood: brøthér, can you spare some B̲̺̹̙̑́̓́ͧ̎ͭ̈́͜L̰̦̼̻͈͖̺͔̇̇̿ͪ̓̃̽ͦŲ̘̲̻͔̀͌͑͑̊͛̑̀͊̕E̐ͮͯ͆̔̾͘͏҉̥̫
|
|
So I went to the nearest wholesale pottery supply store I know of that sells dry powdered kaplin and picked up 10 lbs of it. Then I tried redoing the
procedure with kaolin instead of my backyard clay, and chalk powder instead of wood ash which should hopefully be a better source of carbonate. The
propane tank was running low around the 3 hour mark the blowtorch went out, so I think the heat output was just never high enough for the crucible to
get up to the required temperature. The result was pretty much the same grey as last time.
So then I swapped out the propane tank for a new, full one and retried for a 4th time with the same kaolin/chalk/sulfur/charcoal mixture. With the
blowtorch on almost full blast, aimed at the bottom of the crucible, covered, for 4.5 hours. And it's still just grey.
I can't think of anything else I can even do. Buy actual sodium carbonate instead of trying to sub in calcium carbonate (as chalk)? But I can't
imagine why that would make a difference. Is it still just not getting hot enough - do I need an actual kiln?
Attached: on the left, the darker grey powder produced after 4.5 hours of firing; on the right, the light, unfired powder.
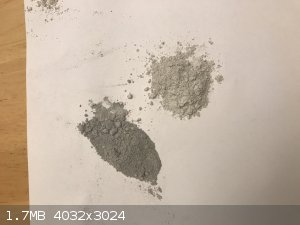
[Edited on 9-29-2019 by Arcaeca]
|
|
Metacelsus
International Hazard
   
Posts: 2541
Registered: 26-12-2012
Location: Boston, MA
Member Is Offline
Mood: Double, double, toil and trouble
|
|
What kind of chalk did you use? Blackboard chalk is calcium sulfate.
And I think that actual sodium carbonate would be necessary. You could use washing soda, or heat baking soda until it decomposes.
|
|
rockyit98
Hazard to Others
 
Posts: 283
Registered: 12-4-2019
Location: The Known Universe
Member Is Offline
Mood: no mood is a good mood
|
|
@Arcaeca
OMG where to begin,you just can't mix some ingredients together and heat it in a ghetto setup and hope it would be fine.ultramarine is one of the most
complex inorganic pigment out there (Na8–10Al6Si6O24S2–4) you need to invest in electric kiln. it not that hard to build one yourself. i'm sure
there is number of post and YT videos that tell you how.maybe less than 100$.over time you will save much more money because efficiency and
electricity been ,much cheaper. i build mine that can get up to 1100C for just under 50$ with PID and 25L capacity. you really need Na2CO3, chalk
powder wouldn't cut it. find a patent or scientific a paper that goes over the process.
"A mind is a terrible thing to lose"-Meisner
|
|
unionised
International Hazard
   
Posts: 5128
Registered: 1-11-2003
Location: UK
Member Is Offline
Mood: No Mood
|
|
Just like they did in 1814.
|
|
Arcaeca
Hazard to Self

Posts: 70
Registered: 24-8-2019
Location: Kansas, USA
Member Is Offline
Mood: brøthér, can you spare some B̲̺̹̙̑́̓́ͧ̎ͭ̈́͜L̰̦̼̻͈͖̺͔̇̇̿ͪ̓̃̽ͦŲ̘̲̻͔̀͌͑͑̊͛̑̀͊̕E̐ͮͯ͆̔̾͘͏҉̥̫
|
|
MSDS: https://www.irwin.com/uploads/documents/62_IRWIN_Chalk_SDS_-...
|
|
Arcaeca
Hazard to Self

Posts: 70
Registered: 24-8-2019
Location: Kansas, USA
Member Is Offline
Mood: brøthér, can you spare some B̲̺̹̙̑́̓́ͧ̎ͭ̈́͜L̰̦̼̻͈͖̺͔̇̇̿ͪ̓̃̽ͦŲ̘̲̻͔̀͌͑͑̊͛̑̀͊̕E̐ͮͯ͆̔̾͘͏҉̥̫
|
|
You know, I just realized that sodium is actually incorporated into the structure of ultramarine. I thought using chalk would be fine because the
sodium carbonate is only needed for the carbonate ion, but in fact I do need the sodium after all. Oops.
So I put a bunch of baking soda on a baking sheet and put it in the oven at 200 degrees Fahrenheit for a little over an hour to decompose it to sodium
carbonate. Then I repeated the previous procedure with this sodium carbonate instead of chalk - mix with kaolin, sulfur and charcoal, tightly pack
into a crucible, heat with a blowtorch (about a centimeter and a half from the base of the crucible) for 3 hours and then uncover... and...
...it's darker, but no bluer.
I can't think of anything else I could've done, other than if the crucible simply isn't getting hot enough. But I simply can't afford a box furnace
like ideally you'd want to use, which run several hundred USD. Another blowtorch would only put me out another $20 or so, but something tells me even
2 blowtorches aimed at the crucible still won't give me blue.
|
|
MrHomeScientist
International Hazard
   
Posts: 1806
Registered: 24-10-2010
Location: Flerovium
Member Is Offline
Mood: No Mood
|
|
Two torches would help it heat up faster, but may not ultimately get it any hotter. You should try some sort of insulation. My first "furnace" was
made of six hard firebricks: one for the floor, one for the lid, and four on their sides as walls. Nothing mortared together at all. The only labor
needed was to drill a hole in the bottom brick for the torch burner. That helps a lot, and is very inexpensive. Plenty of room for improvement,
obviously, but it might give you that extra little push that you need.
|
|
unionised
International Hazard
   
Posts: 5128
Registered: 1-11-2003
Location: UK
Member Is Offline
Mood: No Mood
|
|
Is it just me who thinks this synthesis- while well documented- is as fishy as Grimsby?
While the mix is on the way to 750C it goes through the boiling point of sulphur and into the range where any sulphur that's left would react with
carbon to form the very volatile CS2.
At best, I'd try putting the sulphur at the bottom and a "lid" of Na2CO3 on top to try to keep the stuff all in the same place.
|
|
Arcaeca
Hazard to Self

Posts: 70
Registered: 24-8-2019
Location: Kansas, USA
Member Is Offline
Mood: brøthér, can you spare some B̲̺̹̙̑́̓́ͧ̎ͭ̈́͜L̰̦̼̻͈͖̺͔̇̇̿ͪ̓̃̽ͦŲ̘̲̻͔̀͌͑͑̊͛̑̀͊̕E̐ͮͯ͆̔̾͘͏҉̥̫
|
|
Quote: Originally posted by unionised  | At best, I'd try putting the sulphur at the bottom and a "lid" of Na2CO3 on top to try to keep the stuff all in the same place.
|
I'm fairy sure the mixture has to be well-mixed, but I'm sure it wouldn't hurt to put a little extra sodium carbonate on top.
Anyway, I bought a bunch of bricks and pavers (not firebricks... just regular bricks) and a 3/8" masonry drill bit to make a makeshift kiln; general
set up looks like this but I'm not actually going to fire anything in it until I get my hands on some gloves that can handle the heat.
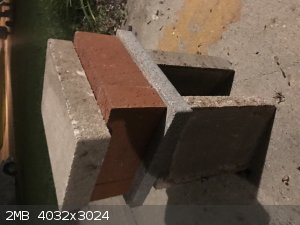
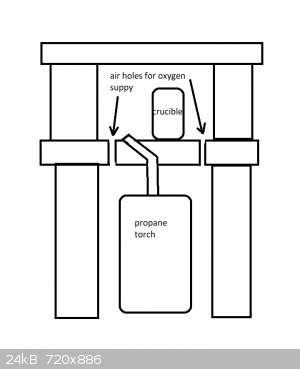
[Edited on 10-1-2019 by Arcaeca]
|
|
MrHomeScientist
International Hazard
   
Posts: 1806
Registered: 24-10-2010
Location: Flerovium
Member Is Offline
Mood: No Mood
|
|
Nice! I'm interested to see if that helps you.
One word of caution, though: since those aren't firebricks, they aren't meant for high heat (obviously). I'd advise heating them slowly (if possible)
to bake out any moisture. Pockets of moisture can flash boil and crack the brick or even make little explosions that send brick shrapnel flying. It
might be worth firing it first with nothing in it, just to make sure it holds up.
I know this is just a quick thing that you don't want to spend a lot of money on, but I thought I'd post some tips on furnace design in case you want
to incorporate that down the line. Metalcasting is one of my other hobbies, so I've acquired a lot of information on furnaces!
Here's a good design that I use, from "The Hobbyist's Guide to Casting Metal, 2nd Edition":
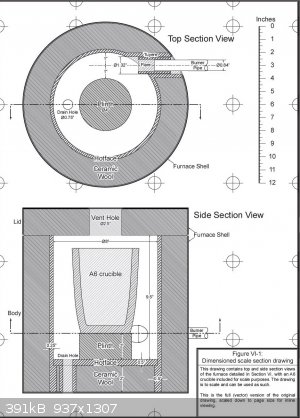
The important points:
The burner enters the furnace right at the bottom of the crucible, offset to the side. This way, the flame spirals around the crucible and
rises, to evenly heat it. The crucible sits on a plinth (firebrick) to put it out of the direct path of the flame.
Don't put the burner flame directly on the crucible, but there's no need to point it completely away from it. Try to have it come in at an angle
close to the crucible. You can hit it directly if it's not heating enough, but this will shorten crucible life.
Oxygen intake probably isn't necessary; the burner draws in its own air (if the air intake is positioned outside the furnace). My brick furnace
didn't have intakes - I think the hole for the burner was wide enough for gases to flow.
There is a vent hole at the top for exhaust gases. You might want to move your lid back a tad to let the exhaust escape.
Of course, this is all in an ideal world where you have infinite time and budget. Like I said, my first furnace didn't have any of this and it worked
just fine. My only concern with your current setup is that the bricks aren't meant for heat, and could fail. I'd test it first, and make sure they're
completely moisture-free by pre-heating them.
|
|
Arcaeca
Hazard to Self

Posts: 70
Registered: 24-8-2019
Location: Kansas, USA
Member Is Offline
Mood: brøthér, can you spare some B̲̺̹̙̑́̓́ͧ̎ͭ̈́͜L̰̦̼̻͈͖̺͔̇̇̿ͪ̓̃̽ͦŲ̘̲̻͔̀͌͑͑̊͛̑̀͊̕E̐ͮͯ͆̔̾͘͏҉̥̫
|
|
My design includes air intakes because the nozzle of the propane torch would be physically inside the kiln, not right below a hole in the bottom. The
edgestones I'm using for the base aren't quite tall enough to give the torch that much clearance. So the propane would have to ignite using the oxygen
actually in the kiln itself, not directly below the kiln, and that's going to run out quickly if it doesn't have some way of being replenished. Or so
my thought process goes.
Thinking of also picking up a tube of firebrick fireplace mortar to coat the insides to reduce the rate of heat loss to the brick walls themselves;
the stuff I'm looking at is rated for up to 2000 F.
|
|
wg48temp9
National Hazard
  
Posts: 786
Registered: 30-12-2018
Location: not so United Kingdom
Member Is Offline
|
|
Yes you have to use dry bricks and heat slowly at first.
The grey blocks look like they are cement blocks so they will crumble and crack as the cement dehydrates.
I would mount the crucible as is described in the procedure in hole in the top of the furnace. That may be important to reduce the combustion gasses
getting in to the crucible when the lid is removed.
I wounder if the reaction mixture could be heated in a microwave oven as it contains carbon and ionic salts.
I am wg48 but not on my usual pc hence the temp handle.
Thank goodness for Fleming and the fungi.
Old codger' lives matters, wear a mask and help save them.
Be aware of demagoguery, keep your frontal lobes fully engaged.
I don't know who invented mRNA vaccines but they should get a fancy medal and I hope they made a shed load of money from it.
|
|
Arcaeca
Hazard to Self

Posts: 70
Registered: 24-8-2019
Location: Kansas, USA
Member Is Offline
Mood: brøthér, can you spare some B̲̺̹̙̑́̓́ͧ̎ͭ̈́͜L̰̦̼̻͈͖̺͔̇̇̿ͪ̓̃̽ͦŲ̘̲̻͔̀͌͑͑̊͛̑̀͊̕E̐ͮͯ͆̔̾͘͏҉̥̫
|
|
Okay, so almost 2 weeks later, after building the kiln, mortaring up all the holes that the heat would've escaped through, curing the mortar, drilling
an exhaust hole in the top and 2 air intake holes in the bottom, setting up some cardboard ducts and using them to push air into the firing chamber
with a fan, and buying some fiberglass gloves rated for 2000 degrees Fahrenheit, I fired up the kiln.
The ultramarine powder is still just dark grey.
I have no idea what else could be wrong besides just simply still not getting hot enough (target temperature is, what, like 1400 F?). Only other thing
I can think of is to just pump way more propane and way more air in, e.g. with a stronger fan and a hooking the blowtorch up to a 20 lb propane tank
instead of a 1 lb canister, which would require a converter.
Or I could scrap the combustion altogether and try to heat it with wires? But the wires would have to get so hot they'd melt themselves before getting
the crucible up to the target temperature.
|
|
Twospoons
International Hazard
   
Posts: 1329
Registered: 26-7-2004
Location: Middle Earth
Member Is Offline
Mood: A trace of hope...
|
|
From Wikipedia:
Quote: |
The preparation is typically made in steps: The first part of the process takes place at 700 to 750 °C in a closed furnace, so that sulfur, carbon
and organic substances give reducing conditions. This yields a yellow-green product sometimes used as a pigment. In the second step, air or sulfur
dioxide at 350 to 450 °C is used to oxidise sulfide in the intermediate product to S2 and Sn chromophore molecules, resulting in the blue (or purple,
pink or red) pigment.[8]
|
Could it be you are not getting enough air to the mix in the second step? If you are using an enclosed "kiln" arrangement with a gas flame, there may
be very little oxygen available.
For the second step maybe you could replace the gas flame with a hot air gun - my one can reach 600C, which is plenty hot enough.
Helicopter: "helico" -> spiral, "pter" -> with wings
|
|
WGTR
National Hazard
  
Posts: 971
Registered: 29-9-2013
Location: Online
Member Is Offline
Mood: Outline
|
|
Sodium carbonate and sodium sulfate melt around 800-900C.
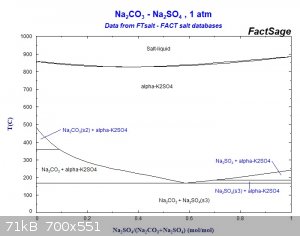
http://www.crct.polymtl.ca/FACT/phase_diagram.php?file=Na2CO...
Adding sodium to a clay fluxes it (and lowers its firing temperature). I suspect that the process may result in a fairly coherent mass if fired to
about 750C for an hour or two.
The stated yield is rather low (1-3g) in the documentation, and the experimenter is directed to carefully pick through the product and select the
appropriately-colored parts for further processing. I do not know if the product is supposed to be located in the hottest area of the crucible, near
the top, or where exactly. It is also possible that the heating-time/results depend on how tightly the crucible lid fits during the initial firing.
I have attached an interesting document regarding the reduction from sulfate to sulfide in a sodium carbonate/sulfate melt, when mixed with charcoal.
It might help explain a bit more about what is going on. Have fun!
Attachment: cameron1983.pdf (1MB) This file has been downloaded 440 times
|
|
Arcaeca
Hazard to Self

Posts: 70
Registered: 24-8-2019
Location: Kansas, USA
Member Is Offline
Mood: brøthér, can you spare some B̲̺̹̙̑́̓́ͧ̎ͭ̈́͜L̰̦̼̻͈͖̺͔̇̇̿ͪ̓̃̽ͦŲ̘̲̻͔̀͌͑͑̊͛̑̀͊̕E̐ͮͯ͆̔̾͘͏҉̥̫
|
|
Mega-bump
Okay, so I dug a big hole and built a makeshift draft furnace out of brick, and then filled it up with as much charcoal as I had on hand. That was
enough to fill it up about 1/3 of the way, so I kept having to add sticks faster than the furnace could burn them. The natural draft wasn't a good
enough oxygen supply to keep the charcoal burning, so I forced air in my taking the fan in my bedroom and aiming it straight at the opening at the
bottom of the furnace.
Result:
It's no longer completely grey. Definitely some blue in there! I mean, not much, but it's an improvement.
I'll try it again tomorrow with a better fuel supply and see what that gets me.
|
|
Metacelsus
International Hazard
   
Posts: 2541
Registered: 26-12-2012
Location: Boston, MA
Member Is Offline
Mood: Double, double, toil and trouble
|
|
Looks interesting, please keep us updated. Is there any practical way for you to measure to the temperature in there?
|
|
G-Coupled
Hazard to Others
 
Posts: 287
Registered: 9-3-2017
Member Is Offline
Mood: Slightly triturated
|
|
Hey, that's looking better! 
Maybe you would have more joy with an electrically powered furnace using NiChrome resistance wire or similar? The designs are pretty simple, even with
a basic working knowledge of electronics.
|
|
Pages:
1
2 |