Pages:
1
2
3
4 |
Heptylene
Hazard to Others
 
Posts: 319
Registered: 22-10-2016
Member Is Offline
Mood: No Mood
|
|
Ostwald reactor from platinized silica wool
I started a thread recently on making platinized silica wool from e-cigarette wick and platinum metal. The goal was to use the catalyst in a reactor based on the Ostwald process
to make nitric acid (or nitrate/nitrites). Since the original thread was about the catalyst and specifically the silica support I used, I'm creating
this new thread to report my progress in making the reactor.
The main idea behind the reactor is to pass a mixture of ammonia and excess air in a tube containing a finely dividied platinum catalyst preheated to
red heat. If the ammonia air mixuture is right andthe flowrate is appropriate and a bunch of other things work out, you should obtain a
mixture of nitrogen oxides and air which can be dissolved in water to make nitric acid.
I just did a pilot run with a source of 2.5 moles of ammonia gas to gauge how well the catalyst work, and get a feel for the different parameters that
are important.
Experimental
The setup I used can be seen in the attachments w/ close ups of the different parts. The first part in the setup is the vacuum pump, the output of
which supplies the air for the reaction. The input has a needle valve to control the air flowrate. The air goes into the three neck flask containing
NH4NO3 (235 g of 85 % ammonium nitrate fertilizer in this run). The addition funnel contained 100 g of NaOH in water (solution density 1.53 g/ml).
To start the reactor, NaOH solution was dripped at a rate of about 1 drop/second and the catalyst tube was heated to red heat with a blowtorch. The
air flowrate was the adjusted to maintain continuous oxidation without additional heat. About 10 large bubbles per second were coming through in the
absorption flask.
Immediately a brown gas was seen forming inside the tube and white smoke appeared in the suckback trap. A tube at the end of the setup leading outside
to vent excess gases was also spewing white smoke for the whole run. After the reaction is started, no much else to besides enjoying the show. At one
point the plastic tube coming out of the reactor tube melted from the hot exhaust gases. The air flowrate was decreased to mitigate the reaction.
Results
At the end of the run, I tested the pH of the solution in the absorption flask: strongly basic! Obviously a lot of ammonia passed through the reactor
without being oxidized, even though enough heat was generated to keep the catalyst red hot.
Discussion
A major problem with this run was that too much NH3 passed through the catalyst without being oxidized. This in turn was due to a too low air flowrate
(not enough to oxidize all the NH3) or too high NH3 flowrate. Unfortunately high flowrates tended to push the catalyst towards the end of the tube,
I'll have to somehow hold it in place next time. And at high flowrates the hot gases didn't have to time to tool down enough before reaching the
plastic tubes, which melted it releasing NOx and NH3 everywhere.
The generator worked relatively well, stirring was surprisingly not an issue and the "waste" leftover is actually mostly sodium nitrate which will be
useful. But I think too much ammonia is produced too quickly even at the slowest addition rate my funnel allows. (Quick calculation: adding 1 drop
NaOH = 0.05 ml <=> ca. 1 mmol <=> 25 ml pure NH3 released.)
I haven't yet decided how to cool the exhaust gases from the catalyst tube. A fan would be practical but might not be sufficient.
This post is getting long, I might add other remarks later.
Anyway if you have ideas for improvement or experiences with those kind of reactors...
EDIT: pictures and legends: the setup, the red hot catalyst and the plastic tube that melted from the hot gasses.
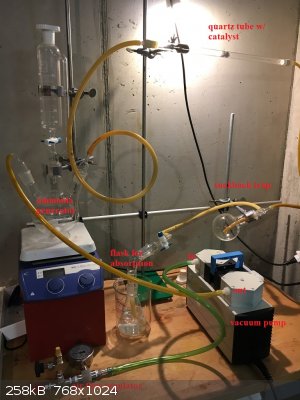 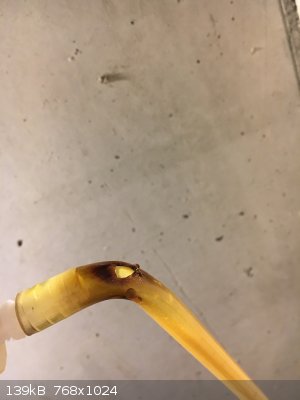
[Edited on 15-7-2018 by Heptylene]
|
|
JJay
International Hazard
   
Posts: 3440
Registered: 15-10-2015
Member Is Offline
|
|
I assume you're using a halogenated plastic for the hoses. I have been meaning to try cooling a quartz tube by wrapping copper tubing around it and
running water through it. I've read that it's much easier to wrap copper tubing if you pack it with table salt.
|
|
Heptylene
Hazard to Others
 
Posts: 319
Registered: 22-10-2016
Member Is Offline
Mood: No Mood
|
|
What do you mean by halogenated plastic? PTFE? The tubes are soft PVC, which is not really chemically resistant but its all I can find easily. I guess
PTFE would actually be a significant improvement over PVC, especially in terms of temperature resistance.
|
|
VSEPR_VOID
National Hazard
  
Posts: 719
Registered: 1-9-2017
Member Is Offline
Mood: Fullerenes
|
|
you should pack the excess space in the reaction tube with glass wool or calcium chloride.
[Edited on 15-7-2018 by VSEPR_VOID]
Within cells interlinked
Within cells interlinked
Within cells interlinked
|
|
unionised
International Hazard
   
Posts: 5128
Registered: 1-11-2003
Location: UK
Member Is Offline
Mood: No Mood
|
|
Quote: Originally posted by VSEPR_VOID  | you should pack the excess space in the reaction tube with glass wool or calcium chloride.
[Edited on 15-7-2018 by VSEPR_VOID] |
Why?
|
|
Heptylene
Hazard to Others
 
Posts: 319
Registered: 22-10-2016
Member Is Offline
Mood: No Mood
|
|
The catalyst mesh has some resistance to gas flow and is pushed along the length of the tube if the flowrate is too high.
Actually packing the whole tube with silica wool might make the pressure in the system to high to be practical (pressure difference scales with length
of packing). Maybe packing with small rocks? Calcium chloride is not suitable because some water is generated by the reaction which condenses further.
The CaCl2 would turn to a solution and contaminate everything. I was thinking of hooking the catalyst to the entrace of the tube with some titanium
wire, I'll see if this work.
@YamYamMan: Yes the flowrate was likely too high. I'll likely make more catalyst, I just need more silica wool. Oxygen is out of the question, its
infinitely more expensive than air. Unless I happen to find a working oxygen concentrator on the street.
Ah also a problem I forgot to mention: the catalyst tends to cool down if the flow is unstable, and if it cools down too much the reaction doesn't
start again. I'll probably add a nichrome wire heating element around the reactor at some point.
|
|
unionised
International Hazard
   
Posts: 5128
Registered: 1-11-2003
Location: UK
Member Is Offline
Mood: No Mood
|
|
Wet CaCl2 will react with nitric acid to form Cl2 and NOCl/ NO2Cl etc.
Silica/ glass wool would be an idea to keep the catalyst in place.
I'm not sure, but I think it might help with cooling the gas after the reaction.
|
|
Heptylene
Hazard to Others
 
Posts: 319
Registered: 22-10-2016
Member Is Offline
Mood: No Mood
|
|
Quote: Originally posted by unionised  | Wet CaCl2 will react with nitric acid to form Cl2 and NOCl/ NO2Cl etc.
Silica/ glass wool would be an idea to keep the catalyst in place.
I'm not sure, but I think it might help with cooling the gas after the reaction. |
Yes actually I could just tie the catalyst in place with some of that silica thread! Probably even better than titanium, I don't know if titanium
holds up to 1000 °C nitric acid vapor
|
|
WGTR
National Hazard
  
Posts: 971
Registered: 29-9-2013
Location: Online
Member Is Offline
Mood: Outline
|
|
I have an unfinished project or two floating around the forum that is related to making nitric acid/nitrates through various means, even though I have
no problems obtaining any chemicals that I need from sources like Fisher or Sigma, etc.
If I were to tackle the Ostwald process, what kind of budget for supplies and equipment would interest people here, who might want to duplicate the
procedure? Starting almost from scratch I think $100 would be a stretch, but perhaps $200 would do it. This would include buying a variac or PID
controller, some firebrick, platinum, etc. A lot of things could be reused for other projects. I don't have time to do things like this solely for
my own amusement, being way too busy these days. However, I might be willing to set some time aside if I thought the procedure would be useful to a
number of people here.
Anyway Heptylene, even though I haven't been commenting on the thread, I've been following your efforts with enjoyment. A few
suggestions that I'd like to throw out there that might be useful:
1. The quartz tube is a bit short after the catalyst. There's not much room for cooling the exit gasses before it hits your plastic tubing. Quartz
tubing of this size is rather inexpensive by the foot, perhaps just get a longer piece.
2. To hold the catalyst in place, perhaps push it into place by using a smaller diameter length of quartz tubing inside the larger reaction tube. The
idea is that the smaller tube would prevent the catalyst from getting blown down the larger tube during operation.
3. Preheat the gasses electrically with something like this: https://www.sciencemadness.org/whisper/viewthread.php?tid=55... It allows you to experiment with various fuel-air mixtures, without worrying
about the self-sustainability of the reaction at the catalyst. The catalyst could be located just outside of the furnace, where it would be heated by
the pre-heated gasses.
4. Minding the flammability limits of ammonia in air, mix up a batch of ammonia-air in a bag using known quantities of both, instead of trying to
generate and use it directly. This removes several variables and makes the results more meaningful and duplicable. Placing the bag inside of a
container like this http://www.sciencemadness.org/talk/viewthread.php?tid=71282&... makes flow control very easy. The compressed air filling the container is
separated from the gas mixture by the plastic bag, and the air flow going into the container can be measured easily with a simple rotameter.
Certainly a larger container can be used, once you figure out the best fuel-air ratio.
5. Given a long enough quartz tube, drill through the sides of a plastic storage container, such that the reaction tube will fit through it
horizontally after it exits the tube furnace. Maybe drill the holes oversized a bit so that a cloth or paper towel can be wrapped tightly around the
tube where it enters/exits the container to plug up the opening. Fill up the container with water for cooling. The paper towels should remain
continually moist.
Thanks for posting your efforts. I know it takes a lot of time, not just for the lab work, but also for posting and editing.
|
|
JJay
International Hazard
   
Posts: 3440
Registered: 15-10-2015
Member Is Offline
|
|
Quote: Originally posted by Heptylene  | What do you mean by halogenated plastic? PTFE? The tubes are soft PVC, which is not really chemically resistant but its all I can find easily. I guess
PTFE would actually be a significant improvement over PVC, especially in terms of temperature resistance. |
PVC is a halogenated plastic... it can withstand some nitric acid, although it is not completely impervious to it. PTFE would be better, of course.
|
|
Heptylene
Hazard to Others
 
Posts: 319
Registered: 22-10-2016
Member Is Offline
Mood: No Mood
|
|
@WGTR That's some really nice advice! I'll adress each point in order:
1. I'll probably don't buy a longer tube as those are pretty expensive. From a quick search on eBay on the order of 50 $ for 1 meter length. I already
have three 50 cm tubes 18 mm OD, I might be able to connect them somehow. Ironically it would be pretty hard to fuse two tube together...
2. I'll see if I can do that with some extra silica wick holding the catalyst (think like a kite in the wind inside the tube). If that doesn't work
I'll try your idea, it looks robust.
3. Pre-heating is a good idea, it would probably save on the quantity of catalyst needed. Heating the catalyst itself is definitely planned as
re-lighting it with a blowtorch is impractical. And any ammonia that passes over when the catalyst is cold will neutralize the product... Pre-heating
would just be adding some more wire so no big deal.
4. The gas bag idea is nice but seems impractical for large quantities (Maybe with a large garbage bag inside a 55 gallon drum?). Chemetix used thermal decomposition of urea as a mean to produce ammonia (+ CO2) on demand (although I recall the rate of production of ammonia
was a bit too low to be practical). But a gas bag is surely the easiest way to measure exactly how much ammonia goes through the reactor so I might
give it a shot at some point.
5. Excellent suggestion, I'm definitely going to try that! Actually I just thought of something along the same lines: Instead of used a towel dipping
in water maybe an ultrasonic mister could deposit water on the tube continuously. Then again a towel is cheaper that an ultrasonic mister.
@JJay Oops my bad, PVC is indeed halogenated! For some reason I thought the chlorine was removed during the polymerization of vinyl chloride...
|
|
VSEPR_VOID
National Hazard
  
Posts: 719
Registered: 1-9-2017
Member Is Offline
Mood: Fullerenes
|
|
Is there a better material for coating in platinum than glass wool? What about activated carbon as a substrate?
Within cells interlinked
Within cells interlinked
Within cells interlinked
|
|
WGTR
National Hazard
  
Posts: 971
Registered: 29-9-2013
Location: Online
Member Is Offline
Mood: Outline
|
|
I'm going to post these references here, since I think they will be useful to the thread.
The Gauze Catalyst in Ammonia Oxidation
G. A. Perley, and M. W. Varrell
Ind. Eng. Chem., 1929, 21 (3), pp 222–223
DOI: 10.1021/ie50231a007
Publication Date: March 1929
Attachment: perley1929.pdf (301kB) This file has been downloaded 722 times
-------------------------------------------------------------
The following reference is referred to by the previous one:
Temperature Control in Ammonia Oxidation
G. A. Perley, R. P. Smith
pp 258–260
Publication Date: March 1925 (Article)
DOI: 10.1021/ie50183a011
Attachment: perley1925.pdf (426kB) This file has been downloaded 681 times
[Edited on 7-18-2018 by WGTR]
|
|
WGTR
National Hazard
  
Posts: 971
Registered: 29-9-2013
Location: Online
Member Is Offline
Mood: Outline
|
|
I think that even graphite would be attacked by oxygen at 800-1000C, so activated carbon probably wouldn't work well in my thinking.
The trick is also to pick a substrate that will effect the decomposition of ammonia and/or nitric oxide much more slowly than the platinum catalyzes
the oxidation of ammonia to nitric oxide. Even platinum catalyzes the decomposition of nitric oxide, but more slowly, so if the reaction zone is thin
and the reactant flow rates and temperature are optimal, then 90-100% efficiency can be obtained. Silica doesn't seem to have an effect on ammonia or
nitric oxide at high temperatures, so it's a good choice for tubing, and as a catalyst support.
Heptylene, I find it interesting that so many people on eBay sell quartz tubing in such impractically short lengths. It's like they
think everyone wants 18" long tubing or something. I suppose it saves on shipping costs. Anyway, there are other suppliers online that will sell it
by the foot for pretty reasonable costs, but there's always that shipping charge that makes it impractical to just buy a single stick.
One that I see is Mountain Glass (if you're in the US). https://www.mountainglass.com/Quartz-Tube-12mm-x-2mm-4ft
Shipping will add probably $10 to that. Technical Glass also looks good, but they have a $50 minimum. http://www.technicalglass.com/product_pages/fused_quartz_tub...
I priced some platinum gauze. For small quantities that requires some pretty crazy money. The price scales more attractively if I wanted a full
square meter of it (If I wanted to mortgage the house, ha ha!). I'm thinking that it may be more practical to make our own, since we're only talking
about a screen sized to fit into a 10mm tube.
I used a 110 mesh polyester stencil (from my screen printing days) as a template, and weaved a small screen using 40 AWG copper wire. I had to do it
under a microscope just to see that the wire went through the right holes. The result looked like a metal screen, so I guess the idea would work.
The question would be how to remove the polyester mesh from the screen, but I suspect that boiling sodium hydroxide solution would dissolve it.
Anyway, the cheapest place that I could find 3 mil platinum/10% rhodium wire is from Omega (https://www.omega.com/pptst/SPPL.html). The wire is sold by the inch, and I'm thinking that 1 foot might be enough. That would come out to about
$25 + $13 (!!!!!) shipping. Surepure Chemicals offers 5 mil pure platinum wire in 5 foot lengths for $85 + $15 shipping, so about $100. I'm
currently undecided on which way I'd go with that.
If the flowmeter is compatible with ammonia (would probably have to be stainless instead of brass fittings), then it would be possible to just store
the ammonia separately in a free-standing bag without the secondary containment vessel, and meter out the ammonia directly.
Even if you want to generate ammonia directly, I still think it's important to use a storage bag as a buffer, much like a windchest stores air from
the blowers for a pipe organ. For example, a plastic bag is weighted slightly with a rigid piece of cardboard and a magazine or something. One
rubber tube enters the bag from the gas generator, and then another tube goes from the bag to the flowmeter, with a flow that can be adjusted
periodically with the knob on the flowmeter. That way the reaction in the quartz tube is decoupled from the reaction conditions in the ammonia
generator at a given instant. You don't need the pressure in the system to be high, just a fraction of a psi.
I just discovered that Walmart sells 20 gallon Ziploc bags. Those are massive. Something that size could store 2 cubic feet easily. If the seal is
as gas-tight as the smaller 1 gallon bags, then these might be a good choice as storage or as a buffer.
|
|
WGTR
National Hazard
  
Posts: 971
Registered: 29-9-2013
Location: Online
Member Is Offline
Mood: Outline
|
|
I decided to post some resources for silica/ceramic cloth, thread, and bulk fiber below. Maybe they will be useful to someone.
-------------------------------------------------------------------------------
From www.ceramicfiberonline.com:
Ceramic Fiber: Bulk alumina-silica fiber, 25 lbs per box, rated to 1260C, price: $49
-------------------------------------------------------------------------------
From Armil CFS:
Silica Cloth: 96% silica, 0.036" x 36" x 36", Price: $40
-------------------------------------------------------------------------------
From Vitcas:
Silica Fiber Sewing Thread: Good to 1400C, Price: £80.00
Silica Fiber Cloth: 0.7mm x 1m square, good to 1000C, Price: £12.99
|
|
wg48
National Hazard
  
Posts: 821
Registered: 21-11-2015
Member Is Offline
Mood: No Mood
|
|
Quote: Originally posted by WGTR  |
The trick is also to pick a substrate that will effect the decomposition of ammonia and/or nitric oxide much more slowly than the platinum catalyzes
the oxidation of ammonia to nitric oxide. Even platinum catalyzes the decomposition of nitric oxide, but more slowly, so if the reaction zone is thin
and the reactant flow rates and temperature are optimal, then 90-100% efficiency can be obtained.
|
I am surprised that a single thin catalytic mesh with 80 threads per inch (so the wirers are about 1/160in dia) can achieve 90% efficiency with a
residence time of only about 1ms.
For example the length of a the catalyst of catalytic converter for a car is say 12in long or 1000 times the thickness of a 80 thread mesh. I guess
its due to different flow velocity and catalyst efficiency.
[Edited on 19-7-2018 by wg48]
Borosilicate glass:
Good temperature resistance and good thermal shock resistance but finite.
For normal, standard service typically 200-230°C, for short-term (minutes) service max 400°C
Maximum thermal shock resistance is 160°C
|
|
WGTR
National Hazard
  
Posts: 971
Registered: 29-9-2013
Location: Online
Member Is Offline
Mood: Outline
|
|
This is currently unfinished, and I'm kind of in a hurry right at the moment, but I've uploaded a picture of the condensor. It is intended to be
mounted vertically on a board. The left side is the bottom, and the right side faces upward.
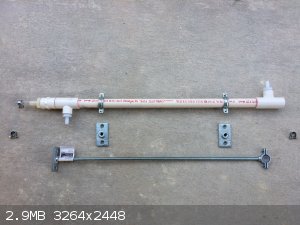
Here's the parts list:
From Home Depot:
1. (1x) 3/4" PVC pipe, 2 ft. Part # 22075 Price $1.55 ea.
2. (2x) 3/4" slip x 1/2" FIP x 3/4" slip PVC tee. Part # C402-101 Price $1.14 ea.
3. (1x) 3/8" all-thread, 2 ft. Part # 802167 Price$1.97 ea
4. (1x) 3/4" slip x 3/4" FIP PVC adaptor. Part # C435-007 Price $0.74 ea.
5. (1x) 1/2" barb x 3/4" MIP adaptor, nylon. Part # 800229 Price $2.24 ea.
From Lowe's:
1. (2x) 3/8" barb x 1/2" MIP, nylon. Part # 877100 Price $1.89 ea.
2. (2x) 3/4" split ring pipe hanger. Part # 302049 Price $1.67 ea.
3. (1x) 1/2" split ring pipe hanger. Part # 302044 Price $1.68 ea.
3. (3x) 3/8" ceiling bracket. Part # 301689 Price $2.24 ea.
4. (1x) 5/8" OD x 1/2" ID clear tubing 10 ft. Part # 814319 Price $4.59 ea.
5. (1x) 1/2" OD x 3/8" ID c;ear tubing 10 ft. Part # 879263 Price $4.18 ea.
6. (1x) 3/4" OD x 5/8" ID clear tubing 10 ft. Part # 814320 Price $7.99 ea.
7. (1x) 3-pack 0.956" rubber diverter. Part # 891223 Price $1.49 ea.
From Napa Auto Parts:
1. 5/8" -> 9/16" fuel injection hose clamp. Part # 7051227 Price $0.99 ea.
2. 1/2" -> 7/16" fuel injection hose clamp. Part # 7051225 Price $0.99 ea.
I'm still waiting on the 8mm x 6mm x 4' quartz tube, but it will slide all the way through the PVC pipe and out either end. The bottom end has a
plastic hose barb connector that the quartz tube will slide through. The short piece of clear tubing on the end of the barb is intended to provide a
water-tight seal. If you look closely you can see that there are two pieces of clear tubing, a smaller piece inside of the larger one. A 5/8" fuel
injection clamp is there to provide a seal between the clear tubing and the quartz tube.
Cool water will flow in through the bottom barb fitting, and out the top one. The condensor is intended to be completely open on the top. The water
flow rate will have to be adjusted such that gravity is sufficient to keep water from spilling out the top of the condensor. I discovered that the
hardware store also sells a fitting that adapts from a barb fitting to a standard garden hose fitting. Interesting.
The condensor will be positioned into place using a pair of 3/4" split ring pipe hangers. These things have a threaded 3/8" hole in the bottom that
accepts a length of 3/8" all-thread. The other end of the all-thread screws into a ceiling bracket, that I am going to mount on a 2 X 4. If one
drills out a hole through the wood under the bracket, then it is possible to screw a standard length of all-thread through the board (maybe a 6" long
piece?). This means that you can adjust the precise stand-off of the pipe hangers without cutting each piece of all-thread to an exact length. I'll
show this later.
The 2' piece of all-thread shown at the bottom of the picture shows how the hanger and the bracket fits together, although I'll be using shorter
pieces of all-thread.
The "hot end" of the quartz tube will fit into the tube furnace that I referred to earlier. It's about 18" long. Right now the condensor is about 2'
long. I may cut it and shorten it a bit later, so that a 4' long piece of quartz is long enough.
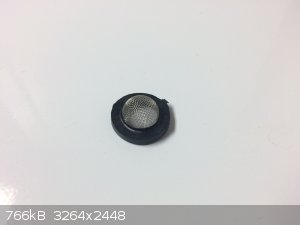
This is a rubber diverter that I picked up in the store. It's made to fit inside of a garden hose fitting to pick up debris and stuff. I think the
screen is stainless steel, but I'm not sure yet. I'm planning to cut it carefully to squeeze tightly inside of the quartz tube, and provide a support
for the catalyst. Once up to temperature the screen may anneal and fall out of the tube, meaning that I'll have to think about this a bit. Maybe a
thin quartz rod placed into the tube would support the screen.
|
|
Heptylene
Hazard to Others
 
Posts: 319
Registered: 22-10-2016
Member Is Offline
Mood: No Mood
|
|
@WGTR That cooling design is really neat! Looking forward to seeing it when its finished.
|
|
RogueRose
International Hazard
   
Posts: 1595
Registered: 16-6-2014
Member Is Offline
|
|
I didn't read the OPs last couple posts, so IDK if he figured out a way to keep the catalyst from being blown to the back of the tube. I was thinking
that you might want to try finding a gravel quarry/pit, gravel dump or gravel driveway (if you have a limestone area) where there is often solid white
rocks incorperated into the grey limestone. These are quartz rocks, some are beautiful and you can see the crystal structure in them and I've found
ones 3"x4"x2" in size. They break nicely and could be filed down with something like a dremel (IDK if a metal file would work). They may be heavy
enough to hold the catalyst in place, you could put a few in line and it would allow air flow around them as well as not contaminate your product with
anything that isn't already there.
I know I used to be able to pick up a bucket full of solid quartz rock when they would dump a new load on the driveway. I have some samples I'll post
pics of if you aren't sure what I'm talking about.
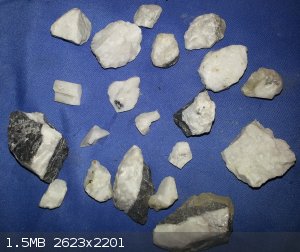
[Edited on 7-24-2018 by RogueRose]
|
|
WGTR
National Hazard
  
Posts: 971
Registered: 29-9-2013
Location: Online
Member Is Offline
Mood: Outline
|
|
Thanks Heptylene! Glancing back over my previous post, I'd like to clarify that I posted a parts list in case I GHBAB (got hit by a
bus). I wouldn't suggest anyone buy those exact parts until I get everything assembled, as some of the parts may change.
I just put in an order for several sizes of quartz tubing. The idea is that a metal screen will be mounted inside of a tube to support the catalyst,
then a smaller tube will telescope into the larger one to keep the screen positioned correctly. Another bit of tubing could be on the other side of
the screen, allowing gravity to clamp the screen in between the two pieces of tubing inside the larger tube.
I have some 6mm x 8mm and 4mm x 6mm borosilicate tubing. It just so happens that the smaller tube telescopes smoothly into the larger one, with just
a bit of extra clearance. I talked with the glass supplier and was informed that I just got lucky with those results. Their tubing has a tolerance
on the OD of +/- 2%, and a tolerance on the wall thickness of +/- 10%. It may telescope that way, or it may not.
For that reason I bought a number of different sizes to play with:
1. 4mm x 6.35mm
2. 5mm x 7mm
3. 5mm x 7.25mm
4. 7mm x 9mm
5. 7.5mm x 9.75mm
Possible pairings:
1. Tubes 1 and 4
2. Tubes 2 and 4
3. Tubes 2 and 5
4. Tubes 3 and 5
Thanks for the idea RogueRose. I'm familiar with the type of rock that you're referring to, and have seen them in driveways, etc.
If one is choosy, it's possible to find them with large facets and pretty transparent. It's a possible option. It would be best to get the purest
crystalline samples that you can scrape up, so that there aren't other minerals present that could decompose the product. It would probably be best
to leach them in nitric acid beforehand to make sure they are chemically "clean".
[Edited on 7-24-2018 by WGTR]
|
|
RogueRose
International Hazard
   
Posts: 1595
Registered: 16-6-2014
Member Is Offline
|
|
Quote: Originally posted by WGTR  |
Thanks for the idea RogueRose. I'm familiar with the type of rock that you're referring to, and have seen them in driveways, etc.
If one is choosy, it's possible to find them with large facets and pretty transparent. It's a possible option. It would be best to get the purest
crystalline samples that you can scrape up, so that there aren't other minerals present that could decompose the product. It would probably be best
to leach them in nitric acid beforehand to make sure they are chemically "clean".
[Edited on 7-24-2018 by WGTR] |
I agree about them being pure. These came out of a muddy driveway and haven't been washed yet so they aren't as bright as they could have been. O
have a nice collection of pure white crystal rocks that look like they were cut almost like diamonds (sharp angles and flat sides). I threw in some
of the mixed ones with the limestone, just to show comparison.
I actually found that these are easily found at night with a good (focused) flashlight as the white REALLY stands out on the ultra pure ones, and your
field of view is limited to the beam, so you aren't over-stimulated by all the stones surrounding you all the time while hunting. These can be heated
with MAPP gas * oxy and no fumes come off and no oxide forms. They can also be dunked in water and only rarely do they split (probably an internal
flaw or stress point).
They are actually pretty interesting for being a common rock found in driveways!
|
|
Chemetix
Hazard to Others
 
Posts: 376
Registered: 23-9-2016
Location: Oztrayleeyah
Member Is Offline
Mood: Wavering between lucidity and madness
|
|
Smashed up brick or tiles have a great surface area and chemically neutral, It worked with cobalt, platinum oxide would also work.
|
|
WGTR
National Hazard
  
Posts: 971
Registered: 29-9-2013
Location: Online
Member Is Offline
Mood: Outline
|
|
I attached some more reading for the thread's enjoyment. The figures show yields of N2 and NO for various temperatures over a ceria
catalyst, and also the ability of ceria to catalyze the oxidation of NO to NO2. I happen to have about 200g of CeO2 that I
picked up on eBay for cheap some time ago.
Characterization of Ceria’s Interaction with NOx and NH3
Li Zhang, John Pierce, Victor L. Leung, Di Wang, and William S. Epling
J. Phys. Chem. C, 2013, 117 (16), pp 8282–8289
DOI: 10.1021/jp401442e
Publication Date (Web): April 1, 2013
Attachment: zhang2013.pdf (2MB) This file has been downloaded 693 times
----------------------------------------------------------
Here's some general, but interesting information:
Oxidation of Ammonia
Gray B. Taylor
Ind. Eng. Chem., 1927, 19 (11), pp 1250–1252
DOI: 10.1021/ie50215a017
Publication Date: November 1927
Attachment: taylor1927.pdf (454kB) This file has been downloaded 699 times
----------------------------------------------------------
Page 150 describes the preparation of CuO/CeO2 catalyst pellets by using acetic acid as a binder. Interesting idea...
Selective Catalytic Oxidation of Ammonia to Nitrogen on CuO-CeO 2 Bimetallic Oxide Catalysts
Hung, Aerosol and Air Quality Research,
Vol. 6, No. 2, pp. 150-169, 2006
Attachment: 4_AAQR-06-06-OA-0004_150-169.pdf (744kB) This file has been downloaded 708 times
[Edited on 7-27-2018 by WGTR]
|
|
WGTR
National Hazard
  
Posts: 971
Registered: 29-9-2013
Location: Online
Member Is Offline
Mood: Outline
|
|
Quote: Originally posted by Chemetix  | Smashed up brick or tiles have a great surface area and chemically neutral, It worked with cobalt, platinum oxide would also work.
|
I don't doubt you for an instant. From observing your fascinating results, and also from a lot of reading, I've seen that a lot of different things
can be used to oxidize ammonia to nitric oxide, so long as certain reaction conditions are minded.
From my understanding platinum is so popular in industry for several reasons. When mixed with a bit of rhodium, platinum mesh happens to be a very
convenient and durable material to use under the temperatures and conditions of the reaction. Once started, the reactor can run for several months at
least, before the catalyst loses about 5% of its weight and needs to be recycled. It the reactor cooled down or stopped for whatever reason, the
nitric acid doesn't go all ommm nommm nommm nomm on the catalyst, since it's well, platinum. Also, it seems to be the most efficient and stable
material that delivers predictable results.
In spite of its high initial cost, in industry the platinum expense is insignificant. Considering the amount of platinum that is consumed for every
pound of acid produced and the cost of the ammonia, I remember reading that even a 1% increase in oxidation efficiency easily pays for the cost of the
platinum that is consumed. In our case we're just making bits of acid for the lab, and a single liter of acid may cost quite a bit when shipping is
considered. Maybe a 50 lb. bag of urea would costs $20 or less. At that point it doesn't matter if efficiency is 90%, 80%, or even 50%, and a lot of
different catalysts and oxidation conditions can be used.
What I'm attempting to do is develop a process that is directly repeatable by others and can be well-documented. In other words, I'm trying to use
materials that I can either post the part numbers for, or demonstrate how to synthesize the various materials needed from scratch. An example of that
would be when I was demonstrating how to make solar cells, and showed how to synthesize the anatase form of titania from the pottery grade rutile
form, rather than trying to source the difficult-to-find anatase form directly. If I use ceria as a catalyst, I'd like to react the oxide to a
soluble salt, precipitate and calcinate it, and then form it into beads of a certain size. That way my ceria is the same as everyone else's.
Hopefully I have enough time to do that.
|
|
WGTR
National Hazard
  
Posts: 971
Registered: 29-9-2013
Location: Online
Member Is Offline
Mood: Outline
|
|
It looks like my quartz tubing will arrive Wednesday, so I'll start picking things up again later this week. I'm going to be working late for most of
the week, and might be a bit scarce for a while.
My ceria samples seem to be dissolving well, so I should have enough to try out some different catalyst designs.
|
|
Pages:
1
2
3
4 |