Pages:
1
2 |
Dan Vizine
National Hazard
  
Posts: 628
Registered: 4-4-2014
Location: Tonawanda, New York
Member Is Offline
Mood: High Resistance
|
|
Thorium metal in coherent form
I currently have about 40 g of thorium powder remaining from my calciothermic reduction of thoria. I've recently decided that I would like to turn
this into coherent pieces.
At one time, quite a number of months ago, a friend of mine told me that he had a contact who was willing to vacuum arc melt thorium. As a chemist, I
didn't really feel the need. I was extremely pleased with the thorium as a steel gray powder. Since then, I've seen advantages to having coherent
pieces and so I asked my friend if his contact was still doing this. He gave me the contact's email address and, based on the fact that I have
received no response in over a week, I have to assume this is no longer a viable option.
It seems it's very hard to find anybody who is willing to use their vacuum arc melting chamber to handle even mildly radioactive material. It all has
to do with cleaning the machine in the end. If they don't feel they can or if it's too much effort, they won't do it.
The hellishly high melting point of thorium, coupled with its relatively high reactivity, essentially rule out any other form of melting. With a
vacuum arc melter, the hearth can be water-cooled copper. With a straight thermal treatment, the crucible has to be able to withstand both the high
temperature and the reactivity. The recommended material is thoria. Then there's the problem of the heat source. You need a molybdenum
disilicide-heated oven, which start at around $20,000. The other option would probably be induction heating, and a machine capable of achieving this
would be expensive. And on top of these difficulties is the fact that you have to maintain an inert atmosphere. Further analytical discussion on this
is pointless, it's way too expensive.
Heeding my own strong recommendation that people look at how it [anything] was done in the past, I did and I found that powder metallurgy is the way
to go. When you think about it, that's no surprise at all. This is the type of thing that powder metallurgy was designed to handle.
Two types of powder have been traditionally compacted in the past to form the "green compacts". They have used powder from calciothermic reductions
and they have used powder from electrolytic deposition. The dendritic nature achieved during electrolytic deposition gives a powder form that is more
readily compacted than the calciothermic reduction product. This is a minor disadvantage, not a show-stopper.
Today I purchased a hardened die set for a powder press. It forms circular compacts 10 mm in diameter. In a 12 ton hydraulic press, if the die set can
handle it, a pressure of around 50 tons per square inch is theoretically achievable. From references that I have seen so far, this would ideally put
me into the normally used range of 40 to 80 tons per square inch. I have doubts that the die set can handle this, though. We'll have to see what we
can do.
Sintering is normally done at 1200°C, and here I fall a little bit short. My Lindburgh tube furnace has a maximum temperature of 1100° C.
I am hoping that perhaps a few repetitions of pressing and heating may compensate for the fact that my pressure and temperature are both just a bit
shy of where they should be. And perhaps this can be addressed during the forging. Forging is something that I have not really given much thought to
yet, but I'm starting to.
[Edited on 7/27/2017 by Dan Vizine]
Attachment: Fabrication of Thorium Powders - JOM 1956 - 078.pdf (1.3MB) This file has been downloaded 588 times
Attachment: php7L7Ido (1.1MB) This file has been downloaded 5908 times
[Edited on 7/27/2017 by Dan Vizine]
"All Your Children Are Poor Unfortunate Victims of Lies You Believe, a Plague Upon Your Ignorance that Keeps the Youth from the Truth They
Deserve"...F. Zappa
|
|
elementcollector1
International Hazard
   
Posts: 2684
Registered: 28-12-2011
Location: The Known Universe
Member Is Offline
Mood: Molten
|
|
My only idea with my limited knowledge on the subject would be to submerge the thorium in a melt that does not boil at its melting point, absorbs
radiation, and in which thorium is not significantly soluble - this would presumably allow you to melt it more safely. However, I cannot seem to find
any phase diagrams with elemental thorium in any of the usual places.
Lead would be the obvious choice for radiation protection, but it boils just 5 degrees C before thorium melts, so that's a no-go. Silver might be a
candidate in terms of density and liquid temperature range, but silver-thorium alloys are confirmed to exist (though I cannot find much more
information than that).
Elements Collected:52/87
Latest Acquired: Cl
Next in Line: Nd
|
|
Fulmen
International Hazard
   
Posts: 1725
Registered: 24-9-2005
Member Is Offline
Mood: Bored
|
|
50 (short) tons/in^2 should be around 700MPa, well within what I'd expect hardened tool steel to withstand.
You are sure you can't jerry-rig something with a TIG-welder?
We're not banging rocks together here. We know how to put a man back together.
|
|
Dan Vizine
National Hazard
  
Posts: 628
Registered: 4-4-2014
Location: Tonawanda, New York
Member Is Offline
Mood: High Resistance
|
|
elementcollector1, if you'll notice in my opening statement I explained that a furnace that will be capable of melting thorium will be prohibitively
expensive. We are talking 1750 C. Plus, I don't want any other metals "co-mingling" with the thorium.
Fulmen, I have a stick welder. Could you be a little bit more specific about what you were suggesting that I weld? My concern is that applying 12 tons
of pressure to a 10 cm diameter tool would cause the tool to bend sideways or some such horrible thing...actually, shatter in this case, I suppose, or
jam somehow. Were you proposing a guide that would somehow stabilize the "ram"?
A picture of the purchased unit is shown. I plan to cut the "rams" down to a small size, so that the combined height of both of them is no more than
about 3/8 of an inch taller than the body of the guide. I won't be making large compacts and I don't foresee a need for more than 3/8 of an inch of
travel. I'll probably start out leaving a half inch and then shorten it once I see what is possible.
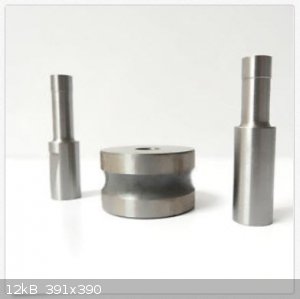
PS. I just realized that the upper ram only needs to be about a half inch long. I'm a little more sanguine about the possibilities of applying 12
tons.
I have also looked a little bit more closely at the ratio between the area of the tool and one square inch. One square inch is 645.16 mm². The face
of the tool is a circle 10 mm across. Calculating the area from pi r squared gives 3.14 times 5² = 3.14 (25) = 78.5 mm².
The ratio is 8.22 to 1. This is the multiplication factor by which the pressure will be increased. Starting out with 12 tons, we see that a
theoretical pressure of 98.6 tons per square inch is possible. I guess my rough estimate was pretty rough.
[Edited on 7/27/2017 by Dan Vizine]
"All Your Children Are Poor Unfortunate Victims of Lies You Believe, a Plague Upon Your Ignorance that Keeps the Youth from the Truth They
Deserve"...F. Zappa
|
|
elementcollector1
International Hazard
   
Posts: 2684
Registered: 28-12-2011
Location: The Known Universe
Member Is Offline
Mood: Molten
|
|
Ah, right. Apologies, I had an idea after reading the first bit and hastily posted it before I forgot.
Do you know what the die set is made of? That would give an idea of how much of a load it can withstand before either undergoing compressive failure
or buckling. If it's tool steel, Euler's buckling formula gives a critical load of about 7.12 x 108 metric tons at half an inch length, and
compressive failure occurs at about 1.08 x 107 metric tons of load (independent of length) according to a Young's Modulus of 140 GPa and a
compressive yield strength of about 1350 MPa. So, if it's tool steel, it theoretically should be just fine.
I used these calculators:
http://www.efunda.com/formulae/solid_mechanics/columns/calc_...
https://skyciv.com/free-moment-of-inertia-calculator/
Elements Collected:52/87
Latest Acquired: Cl
Next in Line: Nd
|
|
Fulmen
International Hazard
   
Posts: 1725
Registered: 24-9-2005
Member Is Offline
Mood: Bored
|
|
Dan: I was talking about TIG (Tungsten Inert Gas). That will provide a tungsten electrode, an arc and inert gas. You might not have a TIG welder, but
they are a thousand times more common than arc furnaces, so borrowing might not be impossible.
As for the die I will have to do some math, but it looks doable. Bending/buckling or seizing due to sideways forces would be my biggest concern as
well. So shortening the rams would be sensible, especially if the press isn't a precision tool. In addition I would use spacers (say large washers)
that support the ends, leaving just a few millimeters of stroke per increment.
Elementcollector: Those seems like the right calculators, but as I prefer to do this math by hand I haven't tried them. One also needs to consider
bulging of the piston, but that requires very accurate measurements of the die tolerances. Also, where did you get 140GPa for steel? it's usually set
to 200. Other than that it looks OK. A yield strength of 1350MPa is quite conservative for tool steel, they can easily reach 1500-2000MPa.
We're not banging rocks together here. We know how to put a man back together.
|
|
phlogiston
International Hazard
   
Posts: 1379
Registered: 26-4-2008
Location: Neon Thorium Erbium Lanthanum Neodymium Sulphur
Member Is Offline
Mood: pyrophoric
|
|
Dan, have you looked into the 'metallex' process?
Briefly: there are three steps. In the first step, a thorium amalgam ('thorium mercuride') is prepared, either electrolytically or by reaction between
thorium tetrachloride and sodium amalgam.
The thorium amalgam forms a solid, kneadable phase ('cheese') that can be filtered of. It contains about 6% Th.
This is then pressed in a steel die that it is probably highly similar to what you have. Some of the mercury escapes via the clearance between the
piston and the die, leaving a puck of a more solid material ThHg alloy, containing about 12% Th.
This is then heated in a furnace under vacuum, moderately at first, and then at 1200 deg C, supposedly leaving a solid piece of Th that is 95%+ of the
density of actual solid Th.
An alternative route to solid Th might be the Arkel-de-Boer process, which supposedly works quite well with Th.
[Edited on 28-7-2017 by phlogiston]
-----
"If a rocket goes up, who cares where it comes down, that's not my concern said Wernher von Braun" - Tom Lehrer
|
|
Dan Vizine
National Hazard
  
Posts: 628
Registered: 4-4-2014
Location: Tonawanda, New York
Member Is Offline
Mood: High Resistance
|
|
Metallex seems to be one variation of what's called activated sintering.
I guess I should make it clear that I'm trying to work within certain limitations. To use the metallex process requires 2 things. It requires 1200°C.
I can do that one way or another. It requires a vacuum. I can do that. I just can't do a vacuum at 1200°C. Out of what would I construct the chamber?
It also means contaminating the thorium, and that's a nonstarter.
I looked extensively into the Van Arkel - de Boer process.
It requires an all quartz reaction vessel with through-seals for molybdenum supports on to which tungsten wires are connected (maybe you could get
away with tungsten through seals, I don't know). The exact temperature of decomposition needs to be known and the only way I can do that is with an
optical pyrometer which I don't have. I haven't looked into the power supply because these factors are already enough to dissuade me. Especially when
there is a proven method which has been used by people decades and decades ago.
and...
About the idea of using a TIG welder, in principle I suppose it's possible to modify a TIG welding head to give sufficient blanketing, but what do I
melt the thorium on? I haven't even been able to find a thoria crucible. I think I read somewhere that berylia would work also. $$$
and...
Because this is a die set I think I just assumed it was hardened steel. I should get a good idea of the hardness of the "rams" when I cut them. If
they don't seem up to the task, I will probably have to obtain some kind of 10 mm hardened tool steel pins or rod.
It's too bad the shanks of drill bits are not hardened the way the flutes are. That would have solved the problem nicely.
[Edited on 7/28/2017 by Dan Vizine]
"All Your Children Are Poor Unfortunate Victims of Lies You Believe, a Plague Upon Your Ignorance that Keeps the Youth from the Truth They
Deserve"...F. Zappa
|
|
bobm4360
Hazard to Self

Posts: 60
Registered: 18-4-2011
Location: On a wretched little island.
Member Is Offline
Mood: No Mood
|
|
Hardened and ground drill blanks aren't expensive, and available from most industrial suppliers. 10mm dowel pins are also available at the same
places. Drill blanks usually run .0002" undersize, and dowel pins the same oversize.
[Edited on 29-7-2017 by bobm4360]
[Edited on 29-7-2017 by bobm4360]
|
|
Fulmen
International Hazard
   
Posts: 1725
Registered: 24-9-2005
Member Is Offline
Mood: Bored
|
|
Quote: Originally posted by Dan Vizine  |
About the idea of using a TIG welder, in principle I suppose it's possible to modify a TIG welding head to give sufficient blanketing, but what do I
melt the thorium on? |
That's for you to figure out :-P Wouldn't water cooled copper work just as well with inert gas as in a vacuum furnace?
We're not banging rocks together here. We know how to put a man back together.
|
|
unionised
International Hazard
   
Posts: 5128
Registered: 1-11-2003
Location: UK
Member Is Offline
Mood: No Mood
|
|
Quote: Originally posted by Dan Vizine  | ...
It requires an all quartz reaction vessel with through-seals for molybdenum supports on to which tungsten wires are connected (maybe you could get
away with tungsten through seals, I don't know). The exact temperature of decomposition needs to be known and the only way I can do that is with an
optical pyrometer which I don't have. I haven't looked into the power supply because these factors are already enough to dissuade me. Especially when
there is a proven method which has been used by people decades and decades ago.
...
I haven't even been able to find a thoria crucible. I think I read somewhere that berylia would work also. $$$
|
An evacuated quartz container with tungsten feed thoughs sounds like a light bulb to me.
Preferably one of the bigger Halogen lamps I think.
You can get a good idea of the temperature of the filament by monitoring the current and voltage- the ratio gives you the resistance and comparing
that to the resistance near room temperature lets you use the filament as its own "resistance thermometer".
Presumably Beryllia is for people who don't think thorium is toxic enough.
;-)
|
|
Fulmen
International Hazard
   
Posts: 1725
Registered: 24-9-2005
Member Is Offline
Mood: Bored
|
|
The Arkel-Boer process is exactly how a halogen lamp works. So in theory you could jerry-rig a large halogen bulb to work as the reaction vessel.
The process has a few problems though:
1. The filament gets embedded in the product.
2. As the filament grows the resistance decreases, so you'll need a high-current adjustable PSU.
We're not banging rocks together here. We know how to put a man back together.
|
|
Dan Vizine
National Hazard
  
Posts: 628
Registered: 4-4-2014
Location: Tonawanda, New York
Member Is Offline
Mood: High Resistance
|
|
bobm4360, that's what I was thinking of, dowel pins. But the hardened and ground drill bit blanks would probably be a better idea since dowel pins
have slightly rounded edges on the face.
Fulmen, yes I could construct a watercooled copper hearth also. And of course the heating area would have to be totally enclosed and protected by
inert gas. I think the idea has merit but it requires me to buy a TIG welder and construct a watercooled copper hearth which is fully enclosed and can
be purged with inert gas during the process. It's not without complications.
Unionised, the idea of using a large metal halide lamp as a reactor is quite ingenious. Excellent resourcefulness, right up there with the TIG welder
idea from Fulmen. One issue that I foresee would be my own possible inability to glassblow ancillary tubing onto the lamp envelope. The idea of using
the filament as its own resistance thermometer will only work in the very beginning, unfortunately. All of that will go out the window as soon as
thorium starts depositing. And so I would still need an optical pyrometer. I believe that I have a suitable high current adjustable PSU. Incidentally,
I've attached an interesting paper on this process.
I really like the idea of the Van Arkel-Boer purification, but the challenges are pretty substantial, likewise with the TIG welder approach. I'm not
dismissing these ideas, but I think that powder metallurgy deserves the 1st go.
I've been collecting all the information that I can on powder metallurgy, particularly that of copper which is said to most closely resemble thorium
in this process. I also need to replace the hydraulic jack on my press before I can proceed. The one I've got has leaky seals and no replacements are
available anywhere. Still, I'm not the kind of guy who likes to just concentrate on the academic side without a little hands-on work of some sort. I
don't have copper powder sitting around, but I do have electrolytic iron. I also have a 3/8 inch die that I constructed and that leaky hydraulic press
that I mentioned so, I figured I would just see what happens.
I loaded about 2 g of iron powder into the die and pressed it for all of 30 seconds with as much pressure as the pump could supply. Judging from the
deflection of the table when the hydraulic pump was new versus what I can see now, I believe that the jack is supplying about half of the force it
should before it tapers off and leaks away. I wasn't at all sure that I would get anything but a pile of crumbly powder when the pressure was
released, but the resulting green compact was a pleasant surprise. The face is smooth enough so that it has a metallic sheen as you can see in the
picture, it reflects light quite strongly.
Normally, during sintering, you want to be at 70% of the absolute temperature. I had never heard this terminology before, but what it means is that
sintering is ideally performed at 70% of the melting point of the metal in degrees Kelvin. The melting point of thorium is 2028° Kelvin. 1200°C
equals 1473° Kelvin, and 1100°C equals 1373° Kelvin. Thus, 1200°C is 72.6% of the absolute temperature, while 1100°C is still 67.7% of the
absolute temperature. So, while I can't achieve 1200° I am at least achieving almost 68% of the absolute temperature instead of the ideal 70%.
My ability to produce usable green compacts ( even with something as hard as iron) along with my ability to reach 68% of the absolute temperature is
very encouraging.
But --
That die that I bought was intended for a mechanical powder press. They don't exert the same forces that hydraulic presses can. I'll be shortening the
rams up considerably, but I still have concerns about the adequacy of this die. Anybody have any interesting sources for a truly heavy duty die,
something that would give me the best 10 mm circular green compacts that I could get?
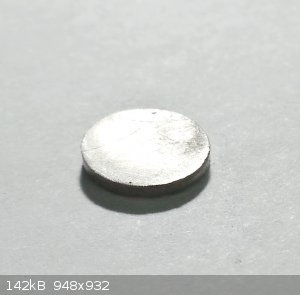
Attachment: Van Arkel and de Boer method - Journal of Metals 1952 - 178.pdf (744kB) This file has been downloaded 521 times
[Edited on 7/31/2017 by Dan Vizine]
"All Your Children Are Poor Unfortunate Victims of Lies You Believe, a Plague Upon Your Ignorance that Keeps the Youth from the Truth They
Deserve"...F. Zappa
|
|
Fulmen
International Hazard
   
Posts: 1725
Registered: 24-9-2005
Member Is Offline
Mood: Bored
|
|
Considering you already have the die, sintering seems like the most sensible approach. What's the density of the iron pellet? I'm eyeballing it to be
at least 50%, that should be enough. I doubt there is any "perfect" temperature for sintering, higher should be better and produce a denser product in
a shorter time. I would be surprised if 68% wasn't enough as long as you can increase holding times.
We're not banging rocks together here. We know how to put a man back together.
|
|
Dan Vizine
National Hazard
  
Posts: 628
Registered: 4-4-2014
Location: Tonawanda, New York
Member Is Offline
Mood: High Resistance
|
|
Hi Fulmen,
I'm not denying that it would be great to be able to reap some of the purification benefits that a more sophisticated method could potentially supply.
I also think that if I were to attempt one of these, I might still be working on it in 2018. And unfortunately that probably takes some of the
interest out of the project for SM members (that I'm not doing these). This is primarily aimed at getting some metallic thorium in coherent form on a
short time scale.
I didn't really examine the pellet any more than to just see if it held together. I let it contact a rare earth magnet and then pulled it away without
the compact breaking. Given that the pressing time was measured in seconds and that it was at a pressure far from the supposedly capability of that
hydraulic jack, this was strictly a throw-away. Better conditions are imminent...
I just bought a new jack on eBay. It was $80, but I could've purchased one for half that amount if I didn't have to have an in-line handle. When I
built this press back in the eighties, I never foresaw the fact that hydraulic pump design would change. It seems like 95+% of hydraulic pumps have
the handle on the side, which makes them too wide to be accommodated.
At least this method will be giving some kind of results within a few weeks at most.The hydraulic jack should arrive this week, and the die shortly
thereafter. I have the tube furnace and the quartz tube. I also have tantalum foil on which to rest the compact when sintering. The only thing I need
to do is refill my ultrahigh purity argon. That is wretchedly expensive for a private individual, $140 vs. ~$40 for 99.995% gas. But since that is
probably just about the final expense in this long, long project, it's got to be done.
When I was in my thirties lugging a tank of this size up the basement stairs was nothing (this is the large-size cylinder, 250 ft.³. It's the only
size you can get UHP in according to my gas vendor), now that I'm 64 it seems to be noticeably harder.
Notice the drip-pan under the pump. The seals REALLY leak a lot!
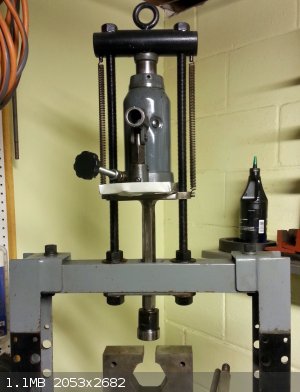
[Edited on 7/31/2017 by Dan Vizine]
"All Your Children Are Poor Unfortunate Victims of Lies You Believe, a Plague Upon Your Ignorance that Keeps the Youth from the Truth They
Deserve"...F. Zappa
|
|
unionised
International Hazard
   
Posts: 5128
Registered: 1-11-2003
Location: UK
Member Is Offline
Mood: No Mood
|
|
Quote: Originally posted by Dan Vizine  |
That die that I bought was intended for a mechanical powder press. They don't exert the same forces that hydraulic presses can. I'll be shortening the
rams up considerably, but I still have concerns about the adequacy of this die. Anybody have any interesting sources for a truly heavy duty die,
something that would give me the best 10 mm circular green compacts that I could get?
[Edited on 7/31/2017 by Dan Vizine] |
Yes
But they are probably horribly expensive, because they are "lab equipment"
http://www.specac.com/products/sample-preparation/dies/spare...
|
|
Dan Vizine
National Hazard
  
Posts: 628
Registered: 4-4-2014
Location: Tonawanda, New York
Member Is Offline
Mood: High Resistance
|
|
Even more so than I imagined. This [picture] is a hardened stainless steel set, not even tungsten carbide.
I expect to get screwed when buying new scientific/technical equipment, but this is more like rape. $895 for a simple SS die.
In the meanwhile, I decided to play with the iron compact a little more. It seems quite strong. I calculated the density of this compact and it's ~
82% of theory. It undoubtedly helped that the iron powder is electrolytic.
8-1-17 The green compact exceeds my most optimistic expectations. Even after such a deficient pressing, the disk can be ground and polished to
reflect light like a mirror.
Well, until the jack and die arrive, there isn't much else to say. I'll pick this up again at that point.
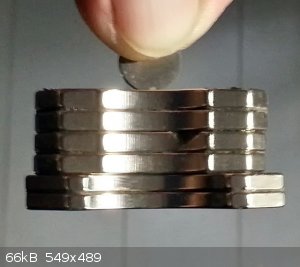
[Edited on 8/1/2017 by Dan Vizine]
"All Your Children Are Poor Unfortunate Victims of Lies You Believe, a Plague Upon Your Ignorance that Keeps the Youth from the Truth They
Deserve"...F. Zappa
|
|
Melgar
Anti-Spam Agent
   
Posts: 2004
Registered: 23-2-2010
Location: Connecticut
Member Is Offline
Mood: Estrified
|
|
What about alloying with something like sodium, that has low melting and boiling points, and is also reactive enough that it wouldn't stick around as
a contaminant in appreciable quantities? I know you already have an apparently-workable solution, but that's just an idea I had while reading the
thread.
When I was getting my mechanical engineering degree, one of the things that we were told is that there's a huge amount of opportunity out there to
improve design by using powder metallurgy. The resulting metal is a lot stronger than people would expect it to be, due to its high resistance to
crack propagation. Its porosity also allows it to absorb lubricants, meaning lubrication isn't needed as often.
The first step in the process of learning something is admitting that you don't know it already.
I'm givin' the spam shields max power at full warp, but they just dinna have the power! We're gonna have to evacuate to new forum software!
|
|
Dan Vizine
National Hazard
  
Posts: 628
Registered: 4-4-2014
Location: Tonawanda, New York
Member Is Offline
Mood: High Resistance
|
|
Hi Melgar,
Are you proposing that the sodium metal would act as a lubricant like the various waxes that are commonly added in the industry? I'm sure that it
would improve the characteristics of the dry compact in the very short run, but there is a chemical problem. To get the sodium out would require
hydrolyzing it. Any hydrogen that is given off could easily react with the thorium metal. To further complicate things, I have no conception of how
easy it would be to wash all of the sodium hydroxide out. Intuition tells me it wouldn't be easy.
I get the feeling that powder metallurgy is not given the respect that it deserves. Everything that I read about the process bears out what you said
in your 2nd paragraph. Strength is supposed to be 2nd only to forged pieces. And I think that when you add in the process called hipping, you can
produce parts that are superior to forged. In fact, I believe that the aeronautics and aerospace industries make certain critical parts this way.
It's going to be very difficult to wait until the Chinese-made die arrives. It has been shipped according to the seller, but the China Post latest
delivery date is August 25th. Let's hope it doesn't come to "latest".
"All Your Children Are Poor Unfortunate Victims of Lies You Believe, a Plague Upon Your Ignorance that Keeps the Youth from the Truth They
Deserve"...F. Zappa
|
|
Melgar
Anti-Spam Agent
   
Posts: 2004
Registered: 23-2-2010
Location: Connecticut
Member Is Offline
Mood: Estrified
|
|
Eh, forget the sodium idea, I don't think it'd work anymore anyway.
The main advantage of powder metallurgy is that it's easier to mold powder than molten metal, as you've demonstrated. You don't have to be pressing
it into a circular die obviously, it can be any shape you want. It also is more or less isotropic after sintering, meaning that when modeling it, you
don't have to account for all the residual stresses that machining, or forging, or casting introduce. You sort of need a "weakest link" mentality
when designing mechanical parts, and powder metallurgy produces components where that weakest link is more easily predicted.
I'm not sure if the porosity would be an issue for you, since it increases surface area (though not appreciably, for most purposes) and of course,
makes it porous such that it can absorb liquids to a degree. This could be problematic when dealing with something radioactive, although I'm not sure
if or how it would.
Wait. Damn, I just realized it was YOUR location that said Tonawanda, NY and not mine. That's where my brother lives, and I lived with him until
four years ago, so a lot of my accounts still list that address. He's just south of Sheridan, a little past where Belmont and Colvin diverge. Any
chance you went to UB? Pretty much everyone intelligent I've met in that area in the science/tech fields seems to be, to some degree. Did my masters
there.
The first step in the process of learning something is admitting that you don't know it already.
I'm givin' the spam shields max power at full warp, but they just dinna have the power! We're gonna have to evacuate to new forum software!
|
|
Dan Vizine
National Hazard
  
Posts: 628
Registered: 4-4-2014
Location: Tonawanda, New York
Member Is Offline
Mood: High Resistance
|
|
Hi Melgar,
I not only went to UB, I currently live only a few miles west of the North campus, in the Green Acres subdivision, not far from Raintree Island. You
turn left off NFB after you pass under the 290 and you're just a couple turns and a few blocks from my house.
"All Your Children Are Poor Unfortunate Victims of Lies You Believe, a Plague Upon Your Ignorance that Keeps the Youth from the Truth They
Deserve"...F. Zappa
|
|
Dan Vizine
National Hazard
  
Posts: 628
Registered: 4-4-2014
Location: Tonawanda, New York
Member Is Offline
Mood: High Resistance
|
|
Wow! Beyond my wildest dreams. Another iron compact, AS PRESSED. Absolutely no sanding, buffing, etc....Sides are brilliant silver, faces shiny silver
(esp. the top, unidirectional pressing).
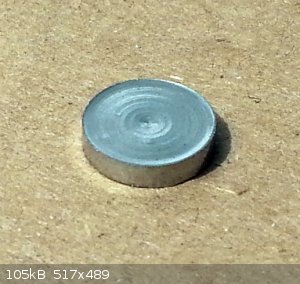
[Edited on 8/11/2017 by Dan Vizine]
"All Your Children Are Poor Unfortunate Victims of Lies You Believe, a Plague Upon Your Ignorance that Keeps the Youth from the Truth They
Deserve"...F. Zappa
|
|
Fulmen
International Hazard
   
Posts: 1725
Registered: 24-9-2005
Member Is Offline
Mood: Bored
|
|
Very nice. What's the density?
We're not banging rocks together here. We know how to put a man back together.
|
|
Dan Vizine
National Hazard
  
Posts: 628
Registered: 4-4-2014
Location: Tonawanda, New York
Member Is Offline
Mood: High Resistance
|
|
The 2 mm high, 10 mm disk weighs 1.05 g for a density of 85% of theoretical.
It wasn't even pressed at 100% pressure, and only for about 3 minutes.
"All Your Children Are Poor Unfortunate Victims of Lies You Believe, a Plague Upon Your Ignorance that Keeps the Youth from the Truth They
Deserve"...F. Zappa
|
|
Fulmen
International Hazard
   
Posts: 1725
Registered: 24-9-2005
Member Is Offline
Mood: Bored
|
|
Looks real promising. Thorium might be harder, but combined with sintering you should be able to get much closer to theoretical density.
Next step would be to sinter the iron at the same relative temperature (950-1000°C), this should give a good indication of what to expect.
[Edited on 14-8-17 by Fulmen]
We're not banging rocks together here. We know how to put a man back together.
|
|
Pages:
1
2 |