Pages:
1
2
3
4 |
mux
Harmless
Posts: 31
Registered: 11-12-2016
Member Is Offline
Mood: No Mood
|
|
Building an open source hot plate stirrer - feature requests!
Introduction
I'm an aerospace/electrical engineer by trade and I guess if anything fits, I'm a 'chemistry enthusiast'. Nonetheless, I follow the obvious youtube
channels and do some remedial chemistry by myself and recently I found the need to get a hot plate/magnetic stirrer combo.
Fucking hell. 500 bucks for such a piece of crap? Are you mad?
Putting on my electrical engineer/systems engineer hat, so much is wrong with pretty much every hot plate in the world. First of all, they're almost
without exception crap build quality (I've had a half a dozen apart, but NurdRage's examples also didn't look too peachy) - no real attempts at
chemically sealing them, a lot of them have obvious single points of failure (heating wire, magnetic stir motor, inaccessible fuses, non-spillproof
rotary encoders, etc.) and some design decisions are without any technical merit. Why use high emissivity ceramic tops? Just because you can then
boast 1500W heating capacity? *
On the DIY front, most people seem to stick with computer fans with neodymium magnets on them combined with cheap heating mantles, or possibly
silicone heaters. That's fine for aqueous chemistry, but it won't get to 400-500C as you'd need for some more hardcore distillation (dry distillation,
high boiling point solvents, etc.).
The answer: an open source, properly engineered hot plate stirrer
So as with all things in life, the only way to do it right is to do it yourself. The perfect recipe for no free time. All joking aside, a few
missing/really expensive features really bug me in anything I can buy, so I'm heavily inclined to build something for myself and then open source/sell
it so other people can benefit.
Features it will have:
Wifi connectivity. My chemistry lab is not next to my Redditing computer. Also, I don't want to risk my health just to babysit a reaction. A hot
plate stirrer should be programmable or at least remotely accessible. This seems to me like the absolute minimum feature.
Decent surface area. I'm thinking of 20x20cm (8x8")
Decent heating capacity, I'm thinking of 1-1.5kW, using multiple parallel heaters so that one heater failure won't effectively render your hot
plate broken. Heater failures seem to be the major cause of hot plate failure.
Remote temperature sensing. You don't want the hot plate to be 500C, you want your condensing column to be at 105C. Basically: type-K
thermocouple connections that you can plug into the side
Solid-state magnetic stirrer (i.e. no moving parts) up to about 2000rpm. I'm amazed this is only standard fare in high-end hot plates.
Very minimal physical user interface. Buttons and displays are the first thing to break. Touch screens or fancy displays just seem like a waste
of money. Obviously you do need an emergency stop, a basic way to adjust temperature and a basic way to adjust stirrer RPM
All of this should be doable with a materials budget of about $50ish, so a DIY kit price (no soldering, just bolting together) of around $100-130ish.
Roughly the price of a meth lab auction hot plate.
Help me!
As said before, I'm mostly just solving an obvious electronic and/or system design problem. I see crappy electronics, I want to make them better. I'm
not a seasoned chemist.
Am I doing the wrong things? Is this a worthless idea? Has this been done 10 times already and I just missed it when looking around?
If not, what features are you missing and/or which of my decisions seem wrong.
A few constraints:
Due to manufacturing constraints, the plate will be aluminum with an optional spray-on ceramic enamel coating.
Due to time constraints, this project won't be done for a long time. Think months or a year, not weeks. Getting to a prototype is quick, making
a kit, documenting and debugging takes 10x as long.
I'm not sticking to any open source hardware/software license in particular. Don't bother with any requirements on this front. It will be open
source in the sense of all design files being available. You may need paid software to open/view them and you may need expensive equipment to make it.
* Quick aside: I understand why these things are $500+ and people still buy them, I understand the concept of professional/educational lab budgets and
needing to buy everything in one place, etc. etc.
** this post is formatted weirdly
|
|
aga
Forum Drunkard
   
Posts: 7030
Registered: 25-3-2014
Member Is Offline
|
|
I got mine about 2 years ago for around €100 (new) and it still works fine, despite being very badly treated.
If/when the electronics fail (dissolve !) i'll probably rig up something to add a few features, such as remote control.
Perhaps a replacement/upgrade board for a cheap hotplate/stirrer would be easier than building the whole thing from scratch.
|
|
gdflp
Super Moderator
     
Posts: 1320
Registered: 14-2-2014
Location: NY, USA
Member Is Offline
Mood: Staring at code
|
|
Interesting ideas you have, though this has been a prospect on the forum for a while(DIY hot plate). None have succeeded AFAIK with a final product
that I would consider superior to a good commercial product made by a company like Corning or IKA.
If you do truly succeed with designing a hot plate with the stated features and price point, I think that quite a few members on here will be
interested, especially those who are just starting out.
Out of curiosity, which hot plates have you taken apart? New-ish hot plates on the cheaper end, or older hot plates from Corning/IKA/etc? Many
members on here, including myself, use these older hot plates, available quite cheap used, and I've never heard of an issue with the build quality
before.
Quote: Originally posted by mux  | Why use high emissivity ceramic tops? Just because you can then boast 1500W heating capacity? *
|
There are several reasons that ceramic tops are used on commercial hot plates. One is simply chemical resistance, as these tops are substantially
more resistant to chemical attack than the aluminum tops(though notably susceptible to attack by heated strong bases).
They do allow substantially higher surface temperatures to be attained as well, this is a place where I think your design is lacking. I'd be hard
pressed to believe there isn't a reason that there aren't any commercial hot plates with aluminum tops that spec surface temps of 500°C without good
reason, you may run into substantial structural issues if nothing else. Typically, aluminum variants max out in the neighborhood of 300°C.
Unfortunately, going with a ceramic plate will increase the cost of the build as well, not to mention sourcing a suitable material.
Ceramic also has a substantially higher heat capacity than aluminum, which results in a more stable surface temperature; this is very important in
some situations.
|
|
Texium
Administrator
      
Posts: 4619
Registered: 11-1-2014
Location: Salt Lake City
Member Is Offline
Mood: PhD candidate!
|
|
Yeah ceramic hot plates are superior to aluminum ones for their chemical resistance alone. I would never buy an aluminum hotplate simply because I
know that if I had a corrosive mixture boil over it would likely be ruined instantly. The ceramic top of my old 1970s Thermolyne has had to hold off
hot conc. sulfuric acid on multiple occasions.
If such a hot plate as described was available (with a ceramic top), I would certainly buy one. Although I love my old relic, I have been dreaming of
having thermocouple control for a while now, I just haven't been able to justify the expense.
|
|
Sulaiman
International Hazard
   
Posts: 3723
Registered: 8-2-2015
Location: 3rd rock from the sun
Member Is Offline
|
|
I think that if you make a quality build then adding features in electronics is relatively cheap,
and once you have control & monitoring for power & stirring
then you may as well add IoT, usb, WiFi, device net .......
I doubt that pople will buy a hotplate stirrer from a small manufacturer based on alledged/unproven quality alone
you need better bells and whistles than the competition
voice command / speech synthesis / braile interface etc.
poly-phase rotating fields is not enough
- you need a 'centralising' force on the stirbar, easily done with magnets, not as easy as you may hope using external coils.
(I am dabbling in this area, if you have success please keep us updated as I'm considering stirring for a hot air bath)
[Edited on 11-12-2016 by Sulaiman]
CAUTION : Hobby Chemist, not Professional or even Amateur
|
|
m1tanker78
National Hazard
  
Posts: 685
Registered: 5-1-2011
Member Is Offline
Mood: No Mood
|
|
I set out to do basically the same thing some months ago out of necessity. I got tired of having good heating without stirring or stirring with
laughable heating. I cobbled together a brushless dc motor (with magnetic rotary encoder), programmable logic brain, bluetooth communication,
bare-bones android app to monitor and control functions, disposable Al plate/sheet top, Al sheet shrouds for various flasks and a digital heat gun
providing the hot air bath. I hacked the heat gun so that the FPGA can read the current setting and send button presses to make adjustments to
temperature and fan speed. There were 4 ports set aside for temperature measurement.
One major feature I began work on but didn't have time to develop was a stall detector. I can't tell you how many times I left
a slurry stirring only to come back and see that the insolubles had settled and the stir bar was simply rotating about its longitudinal axis --
sometimes just bouncing around in the flask. The stirrer has to be slowed or stopped in order for the stir bar to reengage. Doing so is trivial but
detecting when the stir bar disengages is not so trivial in my experience.
The bluetooth link was quite buggy sometimes but that's what I had on hand at the time. A wifi link with an external antenna would be sweet.
Chemical CURIOSITY KILLED THE CATalyst.
|
|
mux
Harmless
Posts: 31
Registered: 11-12-2016
Member Is Offline
Mood: No Mood
|
|
Quote: Originally posted by aga  | (...)
Perhaps a replacement/upgrade board for a cheap hotplate/stirrer would be easier than building the whole thing from scratch. |
This doesn't really solve a bunch of issues, like badly designed mica/nichrome heaters. And not unimportantly: cheap ebay hot plates can just go away
or be totally different 6 months on. It's hard to design against an ever-changing platform. Don't get me wrong though, I'd love to reduce the scope of
the project.
----
I see there are some misconceptions about aluminum tops. Aluminum can withstand 500C, it just can't withstand 700C nichrome wire and it has a fairly
high coefficient of thermal expansion, which means you get issues at high temperature gradients. This is fixable with good design and different types
of heaters. I've done a high-temperature aluminum project before for work. All of this isn't to say I'm a know-it-all and all manufacturers are all
wrong, just that the temperature argument doesn't pass the sniff test. Relatively pure alloys, non-precipitation hardened, annealed, should work fine
up to 500ish C.
Also, 'ceramic' tops aren't always ceramic. A lot of them are aluminum or steel with a ceramic surface (generally alumina). For chemical inertness,
alumina enamel should suffice - it's the exact same stuff used for fume hood resurfacing and hot plate resurfacing. This should be exactly as inert to
everything but the nastiest of chemicals (e.g. HF - although that can be fixed with some PTFE tape).
Quote: Originally posted by gdflp  |
Ceramic also has a substantially higher heat capacity than aluminum, which results in a more stable surface temperature; this is very important in
some situations. |
That's a slight physics misconception, it's not dependent on heat capacity but on the quotient of heat flux on conductivity. Higher conductivity or
lower heat flux = better distribution. Capacity only makes a hot plate more dangerous (by retaining heat after the heater is turned off).
----
Quote: Originally posted by gdflp  | Interesting ideas you have, though this has been a prospect on the forum for a while(DIY hot plate). None have succeeded AFAIK with a final product
that I would consider superior to a good commercial product made by a company like Corning or IKA. |
I'm very aware of this. IMO there's a distinct lack of proper engineering going on in most DIY hot plate projects. Also documentation. The objective
here is to provide a good foundation to work from for other people, or possibly even a decent product (although I'm sure iteration 1 won't please
everyone).
Quote: Originally posted by gdflp  | Out of curiosity, which hot plates have you taken apart? New-ish hot plates on the cheaper end, or older hot plates from Corning/IKA/etc? Many
members on here, including myself, use these older hot plates, available quite cheap used, and I've never heard of an issue with the build quality
before. |
It's super hard to judge build quality without taking stuff apart. I've most recently taken apart a set of IKA hot plates, before that... Weidinger, a
Dutch branded one (forgot exactly which) and a cheap chinese one. These all used mica heaters (a big no-no, although I understand why, it's cheap and
provides high temperature at good isotropy), had horrible electronics (yes, even the IKA, it was just a big pile of poop inside) and so on. On the
outside, only the chinese one had any sort of hint that it wasn't great. Mechanical stability, looks, etc. are generally great. Just don't open them.
----
Quote: Originally posted by Sulaiman  |
I doubt that pople will buy a hotplate stirrer from a small manufacturer based on alledged/unproven quality alone
you need better bells and whistles than the competition
voice command / speech synthesis / braile interface etc.
|
Of course. I'm not (primarily) making a product, I'm making a foundational, open-source design. Even if I produce nothing but one for myself, other
people can copy and improve this instead of having to reinvent the wheel or making design mistakes.
Quote: Originally posted by Sulaiman  |
poly-phase rotating fields is not enough
- you need a 'centralising' force on the stirbar, easily done with magnets, not as easy as you may hope using external coils.
(I am dabbling in this area, if you have success please keep us updated as I'm considering stirring for a hot air bath) |
Very good point. I was actually thinking about this over the afternoon - how do they do this in magnetic stirrers? I think the answer is in one hot
plate that I tore down: they slightly angle the solenoids inward (or outward) to make an effective magnetic trap. I'm definitely making a standalone
stirrer first before attempting the hot plate-stirrer combo, so I can test and optimize this.
------------
Quote: Originally posted by m1tanker78  | (...)
One major feature I began work on but didn't have time to develop was a stall detector. I can't tell you how many times I left
a slurry stirring only to come back and see that the insolubles had settled and the stir bar was simply rotating about its longitudinal axis --
sometimes just bouncing around in the flask. The stirrer has to be slowed or stopped in order for the stir bar to reengage. Doing so is trivial but
detecting when the stir bar disengages is not so trivial in my experience.
The bluetooth link was quite buggy sometimes but that's what I had on hand at the time. A wifi link with an external antenna would be sweet.
|
The 'best' way to detect stall is the same as in electric motors: measure the phase angle of current and/or continuously measure current. Ideally, in
a 3-phase (6-pole) motor, you just see sinusoidal current as you apply voltage over the poles. If the stir bar (rotor) stalls, one position will
consume a lot of current while the 'motor' position perpendicular to that consumes almost none. By either seeing a wildly varying phase angle or big
changes in current consumption over the magnetic field rotation period, you can determine that the stir bar is either stalled or not keeping up. That
info can also be used to save power (and thus unintentional heating) - just turn down the current until the stir bar stalls.
Do you have a link to your project? Have you documented it somewhere? I'd love to see as many (failed and successful) projects as possible, I too
wouldn't like to reinvent the wheel too much and/or fall in the same traps as others did before.
[Edited on 11-12-2016 by mux]
|
|
Fulmen
International Hazard
   
Posts: 1725
Registered: 24-9-2005
Member Is Offline
Mood: Bored
|
|
For the stirrer I suspect one could use a step-motor driver. These are dirt cheap and could be controlled by something as simple as a astable
multivibrator.
We're not banging rocks together here. We know how to put a man back together.
|
|
Dr.Bob
International Hazard
   
Posts: 2753
Registered: 26-1-2011
Location: USA - NC
Member Is Offline
Mood: Mildly disgruntled scientist
|
|
I've used a lot of hotplates. For my money, I have seen more long lasting Corning ones than any other, by a large margin. I have used IKA ones,
they are nice when new, but seem to fail quickly, and it has been hard to get parts for them or get them repaired. The Corning ones are pretty good,
and last forever. The best electronic ones I have seen are made by Variomag, and they stir well, and have no moving parts, and stir well.
|
|
HeYBrO
Hazard to Others
 
Posts: 289
Registered: 6-12-2013
Location: 'straya
Member Is Offline
Mood:
|
|
Those are some interesting ideas mux! a member has already "made" a hotplate stirrer if you're curious to see: https://www.sciencemadness.org/whisper/viewthread.php?tid=23... . Obviously it doesn't meet your requirements but maybe it is useful none the
less.
[Edited on 12-12-2016 by HeYBrO]
|
|
mux
Harmless
Posts: 31
Registered: 11-12-2016
Member Is Offline
Mood: No Mood
|
|
Quote: Originally posted by Fulmen  | For the stirrer I suspect one could use a step-motor driver. These are dirt cheap and could be controlled by something as simple as a astable
multivibrator. |
Any kind of mechanical stirrer motor is not acceptable; that's an easy point of failure in a machine that could regularly get over boiling
temperatures in the main unit.
That would also require something else than rare earth magnets, as their Curie temperatures are too low. And that gets nasty quick. That's why solid
state seems like the absolute way to go: no moving parts, high temperature tolerance, high reliability, infinite variability (practically).
|
|
Fulmen
International Hazard
   
Posts: 1725
Registered: 24-9-2005
Member Is Offline
Mood: Bored
|
|
Mux: Sorry for not being clear, I was thinking of a stepper driver for controlling 4 electromagnets. You basically end up with a 4-step motor.
We're not banging rocks together here. We know how to put a man back together.
|
|
mux
Harmless
Posts: 31
Registered: 11-12-2016
Member Is Offline
Mood: No Mood
|
|
Ah, excuse me. Yes, of course, the only problem being that a 4-quadrant control would not have a deterministic rotation direction, so the 'better'
mixing methods (back and forth mixing, vibration mixing) wouldn't be easy. Although that can just be fixed by using a second stepper driver...
That's more of an implementation question, though. Plenty of microcontrollers have phase shifted PWM outputs, some up to 12, so I can just as well use
one of those and build up discrete coil drivers. I've got plenty of experience with that. The actual choice of parts comes down to (software)
complexity and cost. That's a bit further down the road.
|
|
Fulmen
International Hazard
   
Posts: 1725
Registered: 24-9-2005
Member Is Offline
Mood: Bored
|
|
A stepper driver has full control over the direction, that's the beauty of it. And even a 3$ A4988 driver can microstep (usually 16 steps), giving a
5.6° step angle. That should provide a much smoother operation than many commercial stirrers. I would strongly recommend that you start with this, as
more people are interested in (and capable of) building a stirrer than a complete hotplate.
I started looking into this as I desperately need a good stirrer (and a stirrer hot plate now that my old ICA has died). But I can't design
electromagnets, and didn't feel like spending hours winding coils by trial and error.
We're not banging rocks together here. We know how to put a man back together.
|
|
Sulaiman
International Hazard
   
Posts: 3723
Registered: 8-2-2015
Location: 3rd rock from the sun
Member Is Offline
|
|
I work in an electronics repair company - anything industrial
repair cost is often not important - resuming production is,
I can usually replace or have rewound transformers and motors,
compatible belts, bearings etc. are easily found
failure of a custom coil or a read-protected micro would mean a write-off.
Reliability is good, so is repairability,
where possible, it would be good if you could use 'standard' parts that are likely to be available in a few years.
A robust, repairable hotplate stirrer could become a classic.
To the point where I would be more likely to buy a well documented kit than a well made product,
because your target market is likely to want to modify/enhance the kit model.
... saves a fortune on assembly costs too 
. add a hole tapped for retort clamp-stand rods
. if a spot has precise temperature control it could be used for melting point determination
. a removable wind shield that also keeps heat around flasks, beakers etc. would be nice
A small added benefit would be to design the product for postage ... as small and light as possible.
__________________________________________________
A related question: for my mag-stirrer experimenting I bought these
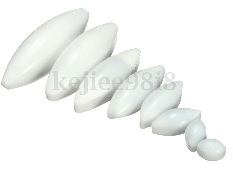
I found difficulty getting them to spin stably under various conditions,
has anyone tried this shape ?
are they more or less stable than the round rod type ?
CAUTION : Hobby Chemist, not Professional or even Amateur
|
|
mux
Harmless
Posts: 31
Registered: 11-12-2016
Member Is Offline
Mood: No Mood
|
|
Quote: Originally posted by Fulmen  | A stepper driver has full control over the direction, that's the beauty of it. And even a 3$ A4988 driver can microstep (usually 16 steps), giving a
5.6° step angle. That should provide a much smoother operation than many commercial stirrers. I would strongly recommend that you start with this, as
more people are interested in (and capable of) building a stirrer than a complete hotplate.
I started looking into this as I desperately need a good stirrer (and a stirrer hot plate now that my old ICA has died). But I can't design
electromagnets, and didn't feel like spending hours winding coils by trial and error. |
I'm aware of these little chips; have used many of them for 3D printers and such. Unfortunately, you're not dealing with a stepper motor here. Even
stepper motors, when they slip excessively (e.g. when you're not putting enough current through the coils) will be able to reverse spontaneously! A
stir bar + solenoids is essentially a very high slip motor, so I'm fairly sure that although stirring low viscosity solutions would be fine, large
stir bars or very viscous/powder compounds will not go well with a 4-pole stator. I could be wrong of course, but I do know a thing or two about
electric machines and a 6-pole solution would be preferable in this situation. Also for centering the stir bar and avoiding spinout.
But of course: the proof of the pudding is in the eating. I'll begin designing a strirrer and testing that concept. I have a couple different
roundbottom and erlenmeyer flasks to test with, although I'll have to look into stir bars (I see that there are many fancy shapes).
--------------------------
Quote: Originally posted by Sulaiman  | (...)
where possible, it would be good if you could use 'standard' parts that are likely to be available in a few years.
A robust, repairable hotplate stirrer could become a classic. |
Absolutely, 100%. I'm a tiny electronic design company, I can't afford getting custom made stuff anyway. Aside from mechanical parts that have to be
milled or 3D printed (which IMO are bearable costs considering typical retail prices of these devices - I'll keep it to 2.5D operations), all the
electronics can be made using 100% multi-supplier parts.
Quote: Originally posted by Sulaiman  |
To the point where I would be more likely to buy a well documented kit than a well made product,
because your target market is likely to want to modify/enhance the kit model.
... saves a fortune on assembly costs too |
This is why I'm specifically making this an open source project. I don't necessarily want to make this into a business. It'll either be a kit or a
limited release. Also, postage can get pretty bad overseas (I'm in Europe).
Quote: Originally posted by Sulaiman  |
. add a hole tapped for retort clamp-stand rods
. if a spot has precise temperature control it could be used for melting point determination
. a removable wind shield that also keeps heat around flasks, beakers etc. would be nice
.A small added benefit would be to design the product for postage ... as small and light as possible.
|
All great suggestions. Given that I'm starting with the stirrer, that one will almost certainly have a standardized lab stand connection. Not sure if
a tapped hole is the best way to go, depends a lot on the weight I suppose.
Instead of a wind shield, I'll probably do what I do with my 3D printer: have a little rubber or silica mat with several cutouts that you can drape
over the surface. Basically anything low-emissivity and low conductance will work here. Proper wind shields have the problem of not necessarily
fitting on any apparatus, and then it becomes an annoying thing to store.
Postage is going to be an issue either way, because I don't see this ever weighing less than 0.5kg or fitting in a 1" thick box, i.e. it'll definitely
fall outside standard sizes for bubble envelopes. For Europe this still isn't a problem (I live in the Netherlands, postage within the EU is cheap
enough), but for the US that may mean it'll have to go through a secondary reseller or just be a design that people build for themselves. Again, I'm
not building this to be sold in the hundreds or thousands, I don't really take the logistics too seriously at this point.
Quote: Originally posted by Sulaiman  |
A related question: for my mag-stirrer experimenting I bought these
I found difficulty getting them to spin stably under various conditions,
has anyone tried this shape ?
are they more or less stable than the round rod type ? |
Same question here. Can somebody enlighten us about different rod shapes? I've seen some weird ones in catalogues; little ringed rods, plus-shaped
cross-sections, etc. What should I be testing with?
Related: I'll be doing a big Fisher Scientific chemical order this week, do they have anything special stir-bar related that I should buy? They're
having an end of year sale with super cheap nitric acid etc., so I'm like a kid in a candy store right now.
|
|
Fulmen
International Hazard
   
Posts: 1725
Registered: 24-9-2005
Member Is Offline
Mood: Bored
|
|
Quote: Originally posted by mux  | Even stepper motors, when they slip excessively ... will be able to reverse spontaneously |
Ummm... A 4 pole "stepper" does create a directional rotating field. With excessive slip one could end up with a harmonic situation where it acts like
a 2-pole, but is this really realistic? And wouldn't this be possible with any number of poles using a common straight stir-bar?
But as you say, the proof is in the eating. And don't let perfection be the enemy of good, unless you use a mechanically linked stirrer I think there
is always some risk of slippage or spinout.
We're not banging rocks together here. We know how to put a man back together.
|
|
mux
Harmless
Posts: 31
Registered: 11-12-2016
Member Is Offline
Mood: No Mood
|
|
These questions are probably a bit premature, and focus a bit too much on implementation details that honestly I don't even know if they're relevant
anyway. It could well be that I don't even have enough space to put in more than 4 poles after doing the calculations on required field strength. I'll
come back to this when the design process is a bit further along.
I'd like to recenter the discussion on big picture stuff first: what features are missing, which are bogus and is that a spider on the wall?
|
|
Sulaiman
International Hazard
   
Posts: 3723
Registered: 8-2-2015
Location: 3rd rock from the sun
Member Is Offline
|
|
AFAIK stir bars rotate synchronously with the applied rotating magnetic field
ANY slip causes chaos.
(there is a phase delay rotation angle as torque is increased)
a mechanical rotating permanent magnet dipole
or three-phase (6-pole) appear to me to be the only viable choices,
theoretically 3 coils could provide a controlable rotating field
what I want is something like 3 Helmholtz coils,
producing maximum field strength and gradienfs near the centre.... tbd
CAUTION : Hobby Chemist, not Professional or even Amateur
|
|
mux
Harmless
Posts: 31
Registered: 11-12-2016
Member Is Offline
Mood: No Mood
|
|
Yes, that was my initial idea as well. Exactly.
I've just done some back of the envelope calculations on attainable field strength, and it's not too great. It's looking like I can reasonably expect
to generate something in the order of 100mT - maybe 150mT - with 2A drive current, about 8W power consumption and a suitably small solenoid (about
1cm3 winding volume). That's about 1/3rd the typical field strength from a neodymium magnet as found in DIY stirrers. I mean, it's in the right type
of order of magnitude, but it's clearly going to be a challenge.
I'm going to build a little calculation/iteration design tool to optimize this and do some FEM modeling to see how I can get the shape of the magnetic
field just right.
|
|
Bert
Super Administrator
       
Posts: 2821
Registered: 12-3-2004
Member Is Offline
Mood: " I think we are all going to die. I think that love is an illusion. We are flawed, my darling".
|
|
My favorite stirring hot plate uses a quartz heating element under a glass top. 16 years, plenty of spills and other mistakes, and only a few
scratches on that quartz glass.
Bibby Sterilin. I have not seen another like it, and got it new for about USA $250.00 delivered. Heck of a deal. It is set up with a socket and
removeable jumpers for remote control of heating, so a PID or such can be used. The stirring is controlled only from the unit. Does have a socket for
a support rod, horizontal and out the back, rather than vertical and on top.
http://www.bibby-scientific.com/
Yes, it would be nice to monitor and adjust the stirring and temperature from an iphone.
I suspect that by the time one adds all the nice features desired, this is not going to be cheaper. But possibly having your equipment user
designed/customized would make it worthwhile regardless of any savings?
Rapopart’s Rules for critical commentary:
1. Attempt to re-express your target’s position so clearly, vividly and fairly that your target says: “Thanks, I wish I’d thought of putting it
that way.”
2. List any points of agreement (especially if they are not matters of general or widespread agreement).
3. Mention anything you have learned from your target.
4. Only then are you permitted to say so much as a word of rebuttal or criticism.
Anatol Rapoport was a Russian-born American mathematical psychologist (1911-2007).
|
|
mux
Harmless
Posts: 31
Registered: 11-12-2016
Member Is Offline
Mood: No Mood
|
|
There is no additional hardware cost to the connectivity features. As a rough guide, the major costs are, from most expensive to cheapest:
- Electrical safety certification ($1000ish in-all, or $2500+ if I want an official registration) one-time
- Milling parts ($10-15 per unit)
- Heater ($10 per unit)
- Electronics (<$10)
- Assembly ($4-6 per unit)
- Power supply ($5ish, not sure yet)
For reference; an ESP8266 module costs $2 and provides wi-fi functionality. Add another dollar for an FCC/EU certified one. Adding in a thermocouple
connector and readout is less than a dollar. These kinds of features are cheap, but they do tend to become a hurdle to completion as software
complexity balloons. So you do want to keep those in check, even though they don't add significant dollar amounts to the final product.
It's a hard requirement to stay on budget. If I go over budget, features get scrapped starting from the least requested features. All pricing will be
done from multiple suppliers.
If this turns out to be sufficiently popular (and again, I'm not aiming for that), a certified reference design will explicitly NOT be customizable.
Customize it, do (almost) anything differently from the prescribed design, and you void any and all guarantees of electrical safety. If this stays
niche enough, you can usually get away with pretty much everything, you just can't blame anyone if you blow your fuses or if your house burns down.
|
|
Fulmen
International Hazard
   
Posts: 1725
Registered: 24-9-2005
Member Is Offline
Mood: Bored
|
|
*thinking* You're right, it must run synchronous. But that applies to mechanically driven permanent magnets as well, doesn't it? My IKAMAG has a
permanent magnet, and it's not immune to overspeed.
Quote: Originally posted by mux  |
I've just done some back of the envelope calculations on attainable field strength, and it's not too great ... That's about 1/3rd the typical field
strength from a neodymium magnet as found in DIY stirrers. |
That's about where I stopped myself, I just didn't know enough about magnets and required field strengths to build a well designed unit.
However, the small commercial units I've seen didn't have particularly strong coils. Even my old IKAMAG has a fairly weak magnet compared to modern
neodymium magnets. And while not perfect for any and all application they seems to work OK for most uses.
We're not banging rocks together here. We know how to put a man back together.
|
|
careysub
International Hazard
   
Posts: 1339
Registered: 4-8-2014
Location: Coastal Sage Scrub Biome
Member Is Offline
Mood: Lowest quantum state
|
|
Quote: Originally posted by zts16  | Yeah ceramic hot plates are superior to aluminum ones for their chemical resistance alone. I would never buy an aluminum hotplate simply because I
know that if I had a corrosive mixture boil over it would likely be ruined instantly. |
OTOH, with a home-build aluminum top stirrer the aluminum plate could be cheaply replaced after such an incident, about $5.
About that which we cannot speak, we must remain silent.
-Wittgenstein
Some things can never be spoken
Some things cannot be pronounced
That word does not exist in any language
It will never be uttered by a human mouth
- The Talking Heads
|
|
mux
Harmless
Posts: 31
Registered: 11-12-2016
Member Is Offline
Mood: No Mood
|
|
Quote: Originally posted by Fulmen  |
That's about where I stopped myself, I just didn't know enough about magnets and required field strengths to build a well designed unit.
However, the small commercial units I've seen didn't have particularly strong coils. Even my old IKAMAG has a fairly weak magnet compared to modern
neodymium magnets. And while not perfect for any and all application they seems to work OK for most uses. |
I've just purchased a few comparatively monstrous stir bars (11x54mm) from eBay (location said UK, so they should arrive soon), I'll be experimenting
with that in one of my Erlenmeyer flasks with some... yoghurt or something. That should be pretty much the worst-case situation.
I have a bunch of A4988s (on a 3D printer dev board) as well, I'll wind a couple coils with 28AWG magnet wire and see how that works. That should give
me a good experimental setup to independently test required field strength, distance from the stir bar, distance between magnets, etc. Expect a video
on this somewhere in the next 2 weeks.
|
|
Pages:
1
2
3
4 |