RogueRose
International Hazard
   
Posts: 1593
Registered: 16-6-2014
Member Is Offline
|
|
Coiling condensor (copper tubing) - best method to not kink or flatten?
I've seen a lot of people say to fill the copper tubing with salt to keep it from collapsing while winding it around a pipe. I've heard people say to
use sand and other say to never use sand. Others say to use water making 100% sure no air is in the tube and then seal the ends. The last seems the
easiest method to clean out but has the possibility of failure if there is air (which is difficult to see through copper).
This issue is most noticably a problem with 1/4" or smaller pipe.
I've tried the salt method and it was impossible to get out afterwards with 1/4" tubing. I tried using 100 psi while the salt was dry and then tried
boiling for days, then lots of other failed methods.
Does anyone have any methods which are successful for bending tubing?
|
|
j_sum1
Administrator
      
Posts: 6321
Registered: 4-10-2014
Location: At home
Member Is Offline
Mood: Most of the ducks are in a row
|
|
Why not use a pipe bender the same as your plumber uses?
|
|
hissingnoise
International Hazard
   
Posts: 3940
Registered: 26-12-2002
Member Is Offline
Mood: Pulverulescent!
|
|
You could just put a water jacket on it, and not need bending!
|
|
Photonic
Harmless
Posts: 36
Registered: 29-5-2016
Member Is Offline
Mood: No Mood
|
|
I've seen wax been used with great success. Plug one end pour in hot wax and then bend. Just heat the copper to remove and you can always use a
solvent to get anything that is left behind.
|
|
plastics
Hazard to Others
 
Posts: 141
Registered: 6-11-2009
Member Is Offline
Mood: No Mood
|
|
Below is my first attempt at coiling a copper tube
4m of 4mm OD copper tubing. Crimped one end and filled with extra dry table salt with careful tamping between additions. The tubing was straight and
hung out an upstairs window to allow filling via small funnel. Other end crimped and then wound around 22mm copper pipe by hand. Combination of care
and brute force.
One end sawn off and salt removed by careful tapping and rotating. Also stuck it in the oven a few times and after cooling crushed salt grains came
out quite easily. No water required
End result coil 160mm in length, 30mm OD - just fits inside some 32mm OD pipe which forms the outer wall of the condenser.
For some reason I wanted one of the tubing limbs to pass through the centre of the coil. I just put this length through the lumen of the 22mm pipe
before I started. The first coil is the most difficult and most likely to occlude on bending. It sort of lies almost 90 degrees perpendicular to the
long axis of the coil, but in doing so, does not increase the overall coil diameter.
[Edited on 25-6-2016 by plastics]
[Edited on 25-6-2016 by plastics]
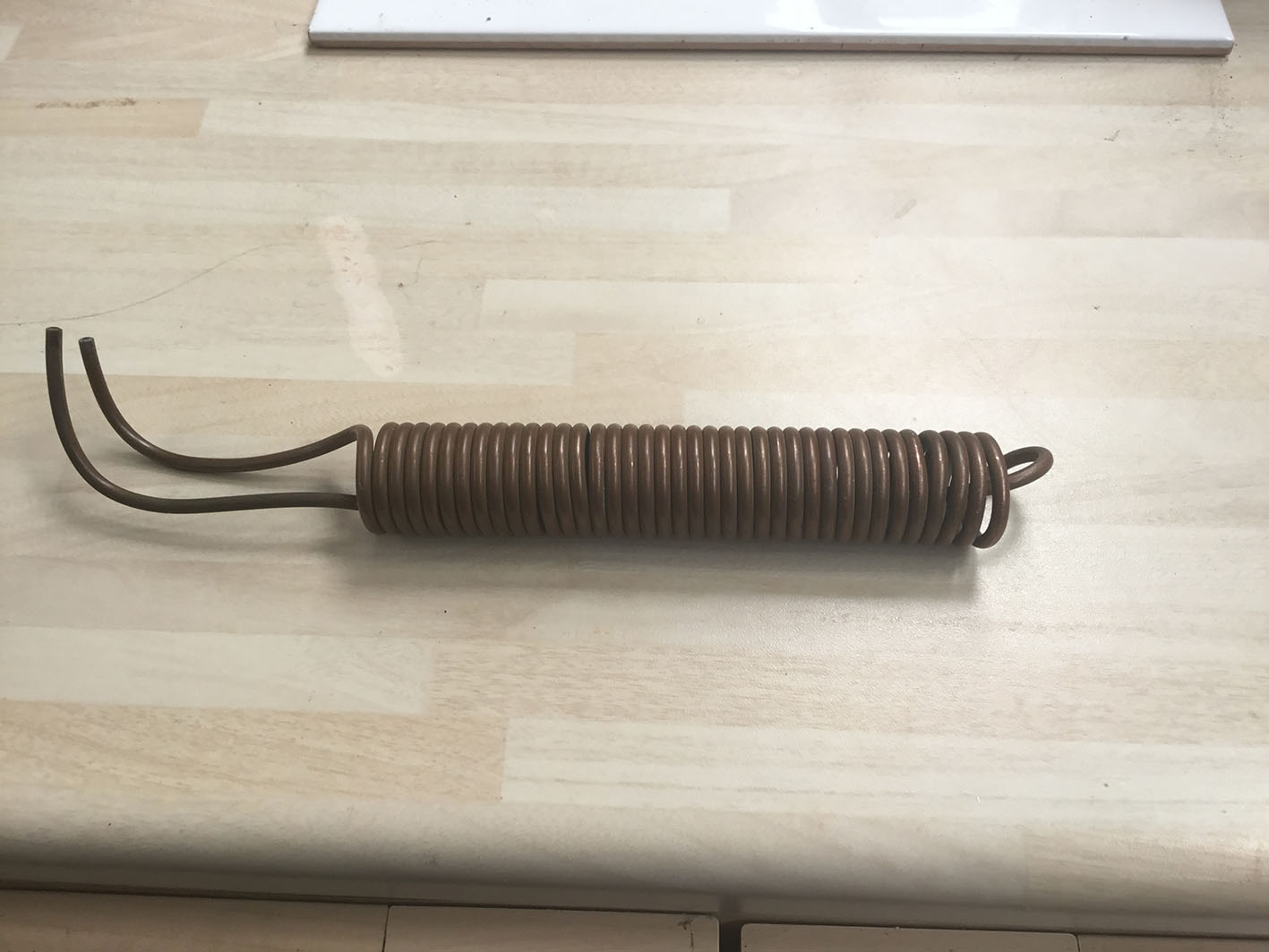
[Edited on 25-6-2016 by plastics]
|
|
unionised
International Hazard
   
Posts: 5126
Registered: 1-11-2003
Location: UK
Member Is Offline
Mood: No Mood
|
|
One option is to fill it with water, freeze it, bend it and thaw it.
|
|
morganbw
National Hazard
  
Posts: 561
Registered: 23-11-2014
Member Is Offline
Mood: No Mood
|
|
fill it full with sand. then do as you will, it will not kink.
|
|
macckone
Dispenser of practical lab wisdom
   
Posts: 2168
Registered: 1-3-2013
Location: Over a mile high
Member Is Offline
Mood: Electrical
|
|
Salt works as does water.
Sand is more difficult to remove.
I like epsom salt as it does not corrode copper like table salt.
|
|
AmineFellow
Harmless
Posts: 1
Registered: 27-6-2016
Member Is Offline
Mood: No Mood
|
|
Very fine sand works, or do as the old moonshiners and use sugar.
Tape/plug one end, fill it, tape/plug the other end, then coil around a rolling pin or telephone pole, depending on the size of your condensor.
I've used both sand and sugar, and they work equally well for the first part, but the sugar was easier to remove with hot water, while the sand got
packed EXTREMELY tight, and it took a few wire coat hangers to break the barriers.
[Edited on 6-29-2016 by AmineFellow]
|
|
Arg0nAddict
Hazard to Self

Posts: 54
Registered: 8-6-2016
Location: PNW
Member Is Offline
Mood: Mercuric
|
|
----
/u/unionised is 100% correct, that is what we do at work sometimes. I am a food grade/ASME metal fabricator and this is how its done in the field when
a mandrel is not spec'd out for the diameter..
----
(5 Steps to Make Copper Coils)
The night before I fill with water and pinch the ends a little not so it be capped off just to prevent leaky leaky. #1
Stick in Freezer. #2
Make Your Coil. #3
Stick in Freezer. #4
Let Ice melt under the sun or in hot water don't use a torch.
----
The problem with sand is an OSHA safety thing; sand obviously falls out so have you pack it real tight and cap both ends, it just adds unnecessary
stress which could stretch the material, start a stress fracture eventually, not to mention the scratches that could promote biological shite which is
a big no no. Also if the sand was wet and is now packed tight and capped there's a risk for a little boom (maybe). Ice truly is best for beginners
since it flattens less and looks pretty, salt is okay, but the best way is without a filler at all but it takes practice.
----
(I sell Copper Condensers among other things)
I will be selling custom copper condensers within my store. I am just waiting on my business loan card to come. Actual Material Fee or you may
supply your own material and then 50% total cost Up Front. (so I know Ill at least get paid half). #1
Just draw out a diagram and have good measurements then ill send a quote and time line. Nobody will beat my prices. #2
Payment:
PayPal & PayPal Here - 5% Fee, Bitcoin & Circle - No Fee, #3
Amazon Gift cards sometimes - 5% fee, Cash or Bank Transfer - No Fee #4
----
|
|