Pages:
1
..
3
4
5
6
7
..
18 |
j_sum1
Administrator
      
Posts: 6324
Registered: 4-10-2014
Location: At home
Member Is Offline
Mood: Most of the ducks are in a row
|
|
Not deliberately copying pinkhippo1: I also had this idea. I too have constructed a lab jack.
The jack itself was free from a wrecker's yard. I has the melamine shelving lying around (Although I intend at some stage to replace it with a 10mm
thick polypropylene chopping board). There are some angle brackets keeping the top steady. Surprisingly, I didn't have anything suitable on my scrap
pile. So, for a couple of bucks, plus bolts, I have a 220mm jack that extends from about 100mm to 400mm.
|
|
The Volatile Chemist
International Hazard
   
Posts: 1981
Registered: 22-3-2014
Location: 'Stil' in the lab...
Member Is Offline
Mood: Copious
|
|
Very nice! Though the picture makes it look rather precarious...
|
|
j_sum1
Administrator
      
Posts: 6324
Registered: 4-10-2014
Location: At home
Member Is Offline
Mood: Most of the ducks are in a row
|
|
Dead graduated pipette -- chipped on the end and the markings faded off.
I also had a string of 3mm spherical neodymium magnets doing nothing.
Now I have a nice glass stir-bar retriever.
|
|
NedsHead
Hazard to Others
 
Posts: 409
Registered: 9-12-2014
Location: South Australia
Member Is Offline
Mood: No Mood
|
|
I think we can all guess where this is going
|
|
aga
Forum Drunkard
   
Posts: 7030
Registered: 25-3-2014
Member Is Offline
|
|
Ball Mill !
Hmm.
That's probably the best way to 'activate' charcoal at low temperatures.
Definitely have to try that.
[Edited on 11-10-2015 by aga]
|
|
NedsHead
Hazard to Others
 
Posts: 409
Registered: 9-12-2014
Location: South Australia
Member Is Offline
Mood: No Mood
|
|
yep, I've wanted one for years and decided its time for action, I should have it finished in a few days, the old 1/4hp motor is a bit overkill but
it'll do for now
|
|
aga
Forum Drunkard
   
Posts: 7030
Registered: 25-3-2014
Member Is Offline
|
|
Well, i've been meaning to build one for ages too, and today's attempt at Tin Chloride was a disaster, so guess what i did instead ?
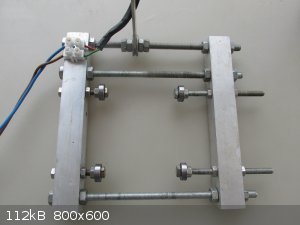
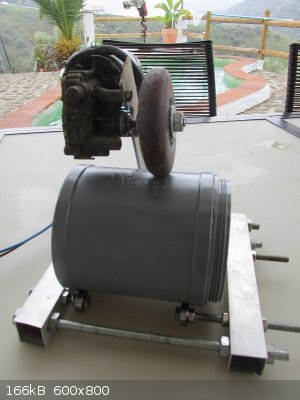
The barrel is a pvc straight coupler with an end cap on one end and a screw cap on the other.
Inside is a straight piece that was cut from some PVC pipe and is held in place by slots cut into the flanges of the end caps, and PVC cement.
The motor is a windscreen wiper motor that is free-running. The wheel on top is from a kids' scooter. The output shaft of the motor had to be
extended, so an 8mm thread was drilled/tapped into a 10mm bolt. It isn't perfectly stright & true, but good enough.
Here's a video of it working :
Attachment: working.mp4 (451kB) This file has been downloaded 1031 times
[Edited on 11-10-2015 by aga]
|
|
deltaH
Dangerous source of unreferenced speculation
   
Posts: 1663
Registered: 30-9-2013
Location: South Africa
Member Is Offline
Mood: Heavily protonated
|
|
Very nice!
|
|
aga
Forum Drunkard
   
Posts: 7030
Registered: 25-3-2014
Member Is Offline
|
|
No Ball mill is complete without Balls right ?
To make Lead Balls, you need a Mould.
To make a Mould, you need a suitable material and a tool.
Small Al ingots smelted from scrap were available, so one of those was used.
Pb melts at 327 C, Al at 660 C, so no fear of the Al melting, and Al is so much easier to machine than Steel.
Speaking of Steel, a mild steel Washer is very very round isn't it ?
Also a lot harder than Aluminium, so a washer was welded to a bit of scrap threaded bar, then the edges were ground down with an angle grinder to
create a cutting edge on each side.
This tool was used to drill a hemisphere into two parts of the Al ingot, which was then cut in half with a hacksaw.
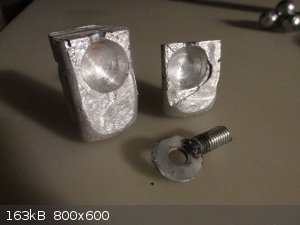
The two mould halves were clamped together in a small vice and a hole was drilled in the top to allow access.
These were then guaged with a small drill bit poked through the access hole to 'feel' the edges and the halves were tapped into place, then clamped
tightly.
Lead was melted in a 40ml porcelain cruicible and poured into the hole until the excess began running over the sides.
Amazingly quick and simple process with just a plumbers' butane blowtorch.
The lead ball can be removed from the mould almost instantly, it cools so fast in Al. .
Result : 5 lead balls ~25mm diameter each weighing 78g +/- 0.2g !!!
Astounding that they are so close in weight given the crude setup and no finishing processing done, apart from chopping off the 'sprue' where the lead
went in and some bits where the mould leaks.
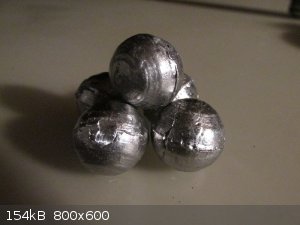
For Scale, here they are next to the SM standard reference :-
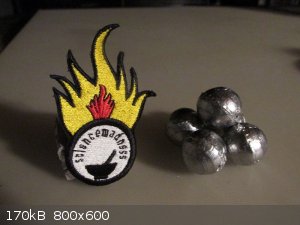
Ball Mill : Done at Last !!
Many thanks to NedsHead for the inspiration.
(a 40ml porcelain cruicible and a pillar drill table were harmed in the making of these balls).
[Edited on 11-10-2015 by aga]
[Edited on 11-10-2015 by aga]
|
|
NedsHead
Hazard to Others
 
Posts: 409
Registered: 9-12-2014
Location: South Australia
Member Is Offline
Mood: No Mood
|
|
Nice work aga! Those mill balls are perfect, I've been racking my brain with what to do about grinding media and was considering buying an expensive
length of round stock brass and cutting it up, seeing your success I think I'll give casting lead a go.
|
|
aga
Forum Drunkard
   
Posts: 7030
Registered: 25-3-2014
Member Is Offline
|
|
Go for It !
It certainly works, as you can see.
Avoid using useful Labware for the Melt - use an empty tin can instead.
I need a new cruicible now as i did not heat the porcelain evenly (it broke).
The Mould does not need to be Precise either.
Some gaps just means that you have to (very easily) trim off any excess with wire cutters or scissors.
I wrecked my bench press drill table by over-tightening it when i tried to mill the Al surfaces to make them flatter for a better seal.
Edit:
You Made My Day.
It is very rarely that i can start and finish a project (=happiness) at all (due to the nature of the work i usually do).
Even rarer that a project can be done in 1 day (=Very happy).
[Edited on 11-10-2015 by aga]
|
|
j_sum1
Administrator
      
Posts: 6324
Registered: 4-10-2014
Location: At home
Member Is Offline
Mood: Most of the ducks are in a row
|
|
Hate to burst your bubble aga. But you didn't consider buying some round fishing sinkers?
|
|
aga
Forum Drunkard
   
Posts: 7030
Registered: 25-3-2014
Member Is Offline
|
|
Entire thing done in 1 day with stuff i already had.
No Shopping (=1 hour round trip, at least. No Point on a Sunday as they are all closed).
No re-moulding pear-shaped sinkers into a more round shape.
No extracting the steel wire intended for nylon fishing line.
No Difficulties at all.
It proves that i can Do It Myself, whether the Shops are open or not.
Enjoyed it all and am happy with the result.
This Bubble is Unburstable.
|
|
j_sum1
Administrator
      
Posts: 6324
Registered: 4-10-2014
Location: At home
Member Is Offline
Mood: Most of the ducks are in a row
|
|
Yeah. I have a fishing shop five minutes walk away. Open seven days. Most of the lead I have came from there anyway. I may as well buy it
spherical if I want spheres.
Not to mention I don't have a spare Al ingot or the ability to weld a washer onto a shaft.
Again an example of what works for one may not work for another.
Nice work btw. Happy milling.
|
|
NedsHead
Hazard to Others
 
Posts: 409
Registered: 9-12-2014
Location: South Australia
Member Is Offline
Mood: No Mood
|
|
Spot on, what you have achieved in a day would have taken me all week!
I'll definitely give casting a try but my biggest problem is I don't have the tooling to make a mould but I have another idea, I can get polystyrene
balls of all different sizes from a local arts and crafts shop,
if I were to bury some appropriate sized polystyrene balls in casting sand and bore a small hole leading to each one and pour the molten lead down the
hole it should burn up the polystyrene and fill the void, what do you think?
[Edited on 12-10-2015 by NedsHead]
|
|
j_sum1
Administrator
      
Posts: 6324
Registered: 4-10-2014
Location: At home
Member Is Offline
Mood: Most of the ducks are in a row
|
|
Wax is typically used for investment casting. You can heat up your mould and pour it out. Then cast your metal and break the moulds to get your
result. Fiddly, but there are fewer limits on the kinds of shapes that can be cast.
You could try polystyrene and try leaving it in there. Might be messy though. Do in a fume hood.
|
|
Oscilllator
National Hazard
  
Posts: 659
Registered: 8-10-2012
Location: The aqueous layer
Member Is Offline
Mood: No Mood
|
|
NedsHead that sounds like a great idea. You've probably heard of it but that method of casting is known to work very well with aluminium (I myself
have used it with great success) so I don't see any reason why it wouldn't work using lead.
If you can't find any polystyrene balls though, don't fret - misshapen lumps probably work just as well for the purposes of ball milling. You may even
find that they become spherical with time due to wear.
|
|
aga
Forum Drunkard
   
Posts: 7030
Registered: 25-3-2014
Member Is Offline
|
|
As it happens, i have some experience with Casting molten metal ...
If you can get a polystryene ball, just bury it in some sand and pour the lead in (obviously leave a little bit exposed).
Yes, it smells. Not too nasty outdoors, and very brief indeed.
Sand casting is great fun.
Use some talcum powder on the polystyrene ball to get a better finish.
|
|
NedsHead
Hazard to Others
 
Posts: 409
Registered: 9-12-2014
Location: South Australia
Member Is Offline
Mood: No Mood
|
|
My biggest concern is the expanding gasses from the polystyrene may damage the mould, using wax and then heating and pouring it out is a great idea
Edit: thanks aga, I'll try that first
Oscilllator, yeah I've seen this method used for casting aluminium, I hope it works with lead too
[Edited on 12-10-2015 by NedsHead]
[Edited on 12-10-2015 by NedsHead]
|
|
nux vomica
Hazard to Others
 
Posts: 267
Registered: 18-7-2013
Member Is Offline
Mood: No Mood
|
|
You could slways buy a sinker mold
|
|
aga
Forum Drunkard
   
Posts: 7030
Registered: 25-3-2014
Member Is Offline
|
|
Quote: | My biggest concern is the expanding gasses from the polystyrene may damage the mould |
Using the least dense polystyrene ball you can find, the 'mould' is just the loose sand surrounding it.
I have not actually tried this 'investment casting' method with Lead, just Aluminium.
Quote: | You could slways buy a sinker mold |
Could always just buy the Mill and the Balls ready made, just not on a Sunday ...
http://www.unitednuclear.com/index.php?main_page=index&c...
|
|
nux vomica
Hazard to Others
 
Posts: 267
Registered: 18-7-2013
Member Is Offline
Mood: No Mood
|
|
Just trying to help out aga nobody had mentioned sinker molds , I've made my own ball molds before and a sinker mold is less work to cast the balls,
I get bored after 20 casts and you need 40 to 50 balls at least for the average mill, the sinker mold cuts the time down a lot .
Gives you an excuse to go fishing as well with any extra balls you cast.
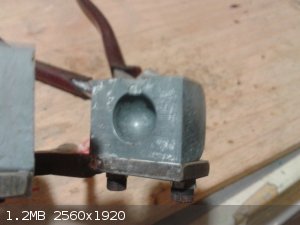
[Edited on 12-10-2015 by nux vomica]
|
|
aga
Forum Drunkard
   
Posts: 7030
Registered: 25-3-2014
Member Is Offline
|
|
I definitely need to make one of those.
|
|
NedsHead
Hazard to Others
 
Posts: 409
Registered: 9-12-2014
Location: South Australia
Member Is Offline
Mood: No Mood
|
|
Almost done! I just need to fit some legs underneath and some rubber feet. She isn't pretty but she spins
|
|
aga
Forum Drunkard
   
Posts: 7030
Registered: 25-3-2014
Member Is Offline
|
|
Cool ! What you got for the Barrel ?
|
|
Pages:
1
..
3
4
5
6
7
..
18 |