Pages:
1
2
3
4
5
..
10 |
Hennig Brand
International Hazard
   
Posts: 1284
Registered: 7-6-2009
Member Is Offline
Mood: No Mood
|
|
The extrusion idea is not a bad one and it is how it is done commercially IIRC. I was thinking of some kind of rotary cutter with rollers for feeding
the sheets into the cutter powered by a hand crank (or motor). The cutting wheel/roller could have little cutters that would take little bites of the
required size out of the sheet as it was fed in. The grains would fall into a collection bin.
I am familiar with the ballistic pendulum. I actually just bought a Shooting Chrony a month or two ago, and have tested the muzzle velocity of just
about every gun and load within reach since then.
[Edited on 10-10-2014 by Hennig Brand]
"A risk-free world is a very dull world, one from which we are apt to learn little of consequence." -Geerat Vermeij
|
|
Bert
Super Administrator
       
Posts: 2821
Registered: 12-3-2004
Member Is Offline
Mood: " I think we are all going to die. I think that love is an illusion. We are flawed, my darling".
|
|
Pasta maker-
The roller part of the machine also works quite well for processing plastic explosive materials, rather easier than rolling a wine bottle over a
sheet of plastique for hours on end.
Rapopart’s Rules for critical commentary:
1. Attempt to re-express your target’s position so clearly, vividly and fairly that your target says: “Thanks, I wish I’d thought of putting it
that way.”
2. List any points of agreement (especially if they are not matters of general or widespread agreement).
3. Mention anything you have learned from your target.
4. Only then are you permitted to say so much as a word of rebuttal or criticism.
Anatol Rapoport was a Russian-born American mathematical psychologist (1911-2007).
|
|
gregxy
Hazard to Others
 
Posts: 421
Registered: 26-5-2006
Member Is Offline
Mood: No Mood
|
|
Shotguns use the fastest burning powers so you are relatively safe performing this type of experiment with a shotgun. Rifles use slow burning powder
so if your home made powder burns faster than the original you will blow up your rifle.
There are computer programs like Quickload which simulate the combustion of powder in the chamber, the pressure generated and calculate the
acceleration of the bullet. It becomes quite complicated since the burn rate is proportional to the pressure in the chamber and many other factors
like the grain size.
Powder makers do things like adding graphite to the power to block the penetration of infrared radiation which slows the heating of the grains and the
burning process. It becomes very complicated.
I wanted to convert my cap and ball black powder revolver to smokeless powder so I calculated the correct load. The original was about 25 grains of
black powder, the calculated load was 6 grains of smokeless powder suitable for a 9mm handgun. I needed to keep the pressure below 10,000PSI since it
is what the gun is designed for. Modern guns use much higher pressures. The ability to use smokeless would be nice since is does not leave residue
that makes it hard to clean the gun.
However I found that the cap could not ignite the smokeless powder
(even though it pushed the bullet 1/2 way down the barrel). So I added a small piece of magicians flash paper (nitro cellulose). The gun would now
fire (weakly) but there was still a bunch of unburned powder left in the
barrel. The large chamber volume and low sectional density of the
spherical bullet work to keep the pressure low, apparently too low to burn
this particular smokeless powder. Maybe a faster powder intended for a
shotgun would work.
|
|
Hennig Brand
International Hazard
   
Posts: 1284
Registered: 7-6-2009
Member Is Offline
Mood: No Mood
|
|
By controlling the viscosity of the NC lacquer, by adjusting the amount of solvent used, it can be made to form the correct thickness by simply
pouring it out onto a flat surface. Nice pasta maker; I imagine it could definitely be made to work. The grain size of the commercial propellant which
came out of the 410 shell was really very small. I have never made more than about a quarter pound of plastic explosive at a time, so the amount of
kneading was minimal (15 minutes maybe), but for larger amounts some decent equipment would definitely be a huge labor saver.
The same smokeless propellants that are used in shotguns are very often used in handguns as well, from what I have seen. The single base propellant
that I made has relatively large average particle size, so I would imagine it would be safe to test in a rifle. Modern rifles are also normally
extremely overbuilt in terms of their ability to withstand pressure. I really don't think that what I am doing is all that dangerous. Once the NC is
no longer in the fibrous form, and given the correct load, it really is very safe material to fire in a gun. This extreme improvement in safety was
what was so revolutionary about Poudre B; that coupled with the much greater performance and almost no smoke production as compared to black powder.
It would be a good idea to examine the grain size of typical commercial rifle powder, specified for the particular rifle used, and also to start with
lighter loads when testing homemade propellant however.
I don't think I would want to go anywhere near the maximum pressure that a gun could withstand. Black powder guns, especially the older ones, were
usually made of much lower strength materials than the modern smokeless propellant types. Being out here in the country, I would tend to test my
powder by simply seeing how it performs in a gun. The percussion caps made for black powder guns are much weaker than the caps made for modern
smokeless propellants. I thought the reason for the graphite coating on propellant grains was to prevent static electricity sparks from igniting the
propellant.
[Edited on 11-10-2014 by Hennig Brand]
"A risk-free world is a very dull world, one from which we are apt to learn little of consequence." -Geerat Vermeij
|
|
Hennig Brand
International Hazard
   
Posts: 1284
Registered: 7-6-2009
Member Is Offline
Mood: No Mood
|
|
Another batch of single base propellant was made from the same batch of homemade nitrocellulose. The propellant was cut up finer this time and loaded
into 410 shells. One shell had the original #4 lead shot and the other was loaded with copper coated BBs. One gram of powder was used in each shell.
The results were counterintuitive; there seemed to be less penetration even though the powder was finer. The balls were only just embedded in the
target.
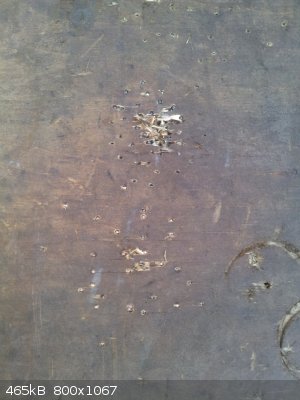
Next, a batch of nitrocellulose with a low level of nitration that was made two years ago was used to make a double base propellant. The
nitrocellulose was dissolved in acetone and then nitroglycerine was added. The composition of the propellant was 60% NC and 40% NG. Even though the
nitrocellulose was much weaker than the nitrocellulose used for the single base propellant, the double base propellant was very powerful. A one gram
load of the homemade propellant seems to have produced similar results as the commercial load when fired at the 3/4" plywood target.
The upper hole, in the following pictures, is from the earlier test with the original powder load (1g of commercial double base powder). The lower
hole is from the later test using 1g of homemade double base. The factory load of #4 lead shot was used in both tests.
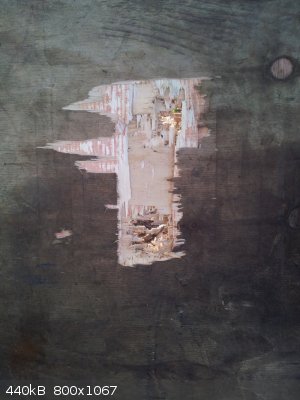
The single base propellant should have performed much better, I think. It is obviously much more difficult to synthesis nitrocellulose with a high
level of nitration than it is to synthesis nitroglycerine. It is also much easier to neutralize residual acidity from NG than it is from NC. NG can be
made with much greater acid economy as well, especially if the spent acids are not recycled. I definitely see some of the advantages of double base
propellants already.
[Edited on 19-10-2014 by Hennig Brand]
"A risk-free world is a very dull world, one from which we are apt to learn little of consequence." -Geerat Vermeij
|
|
Hennig Brand
International Hazard
   
Posts: 1284
Registered: 7-6-2009
Member Is Offline
Mood: No Mood
|
|
The attached tables were taken from the text, “Chemical Analysis of Firearms, Ammunition, and Gunshot Residue” by James Smyth Wallace. The tables
list the formulas for many common single base and double base smokeless propellants, which I thought would be very useful to someone making their own
propellants. The chapter before the one on propellants is on primers, which is also very interesting. Many primer compositions are listed, often with
a bit of description including history of use. The text can be found online.
Attachment: Single and Double Base Propellant Composition Tables.pdf (243kB) This file has been downloaded 1908 times
"A risk-free world is a very dull world, one from which we are apt to learn little of consequence." -Geerat Vermeij
|
|
Hennig Brand
International Hazard
   
Posts: 1284
Registered: 7-6-2009
Member Is Offline
Mood: No Mood
|
|
A test was just performed using a single shot .22 cal. rifle and .22LR rounds with 40 grain bullets. The 0.1g of commercial double base propellant was
removed from one of the rounds and replaced with 0.1g of the homemade double base smokeless propellant. The homemade propellant was screened using a
small kitchen sieve to get reasonably fine grains (the commercial stuff was very fine). The homemade propellant outperformed the commercial propellant
by a significant amount. The factory load gave a muzzle velocity of 1220 fps, while the homemade propellant produced a muzzle velocity of 1329 fps.
Muzzle velocities were measured with a ballistic chronograph.
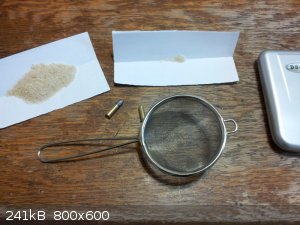
Here is the result of a test using a round which was hot-loaded with the homemade double base. Instead of 0.1g, 0.11g was used. The muzzle velocity of
the bullet was measured as 1437 fps. Now we are really zinging. I don't think I will try and cram any more powder into the tiny .22 cal. cartridge,
though I am sure I could bring the muzzle velocity up to 1600 fps if I really wanted to.
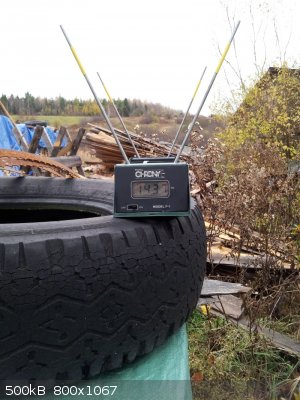
I have included a picture that I meant to post earlier showing the rolling cutter and propellant on a cutting board. The propellant on the board is
homemade single base from earlier tests. The double base propellant, when still slightly damp with acetone, can be cut up very quickly (few minutes)
when done in small quantities at a time (6-10g for example).
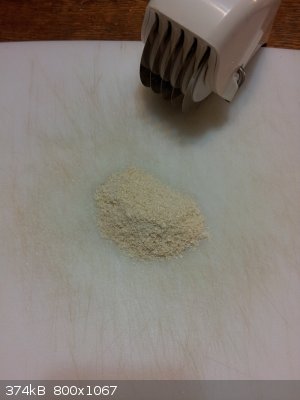
[Edited on 26-10-2014 by Hennig Brand]
"A risk-free world is a very dull world, one from which we are apt to learn little of consequence." -Geerat Vermeij
|
|
Dornier 335A
Hazard to Others
 
Posts: 231
Registered: 10-5-2013
Location: Northern Europe
Member Is Offline
Mood: No Mood
|
|
That's impressive. Why does your propellant perform better than the commercial one? Is it the grain size, or the fact that yours doesn't have other
additives that dilute it?
|
|
Hennig Brand
International Hazard
   
Posts: 1284
Registered: 7-6-2009
Member Is Offline
Mood: No Mood
|
|
Thanks, particle size and lack of diluents could both be factors. Changing particle size, even while keeping everything else the same, can have a big
impact on muzzle velocity. I think most samples of nitroglycerin tend to be fairly pure, however, there can be a lot of variation in the level of
nitration or strength from sample to sample with nitrocellulose. The same simple separation and purification processes that exist for nitroglycerin
are not possible with nitrocellulose. Nitrocellulose also normally makes up the largest proportion by weight of smokeless propellants (60% in my
case). A higher proportion of nitroglycerin would normally make a smokeless propellant more powerful as well. It is very possible that the commercial
propellant has less than 40% nitroglycerin.
Some of the additives/diluents, like a good stabilizer, are very important if the propellant is going to be stored for any length of time; especially
if it will be stored in any quantity.
"A risk-free world is a very dull world, one from which we are apt to learn little of consequence." -Geerat Vermeij
|
|
Rosco Bodine
Banned
Posts: 6370
Registered: 29-9-2004
Member Is Offline
Mood: analytical
|
|
Have you tried nitration of microcrystalline cellulose to produce a single base NC powder that is usable without subsequent granulation? This might
also provide a good starting material for double based ball powder of very fine mesh size.
|
|
Hennig Brand
International Hazard
   
Posts: 1284
Registered: 7-6-2009
Member Is Offline
Mood: No Mood
|
|
I haven't tried it, but it does sound like a possible way to get useful grain size without the need for granulation post reaction. It could be hard to
properly incorporate the stabilizer if the nitrocellulose isn't colloided and the stabilizer isn't dissolved in the solvent though. I have never made
microcrystalline cellulose, but I am interested in it. I remember seeing the thread(s) with what looked like fairly simple processes for producing MCC
for the hobbyist.
"A risk-free world is a very dull world, one from which we are apt to learn little of consequence." -Geerat Vermeij
|
|
specialactivitieSK
Hazard to Self

Posts: 94
Registered: 21-10-2014
Member Is Offline
Mood: No Mood
|
|
Smokeless rocket propellant :
DEGDN : 45 %
NC /12,5%/ : 53 %
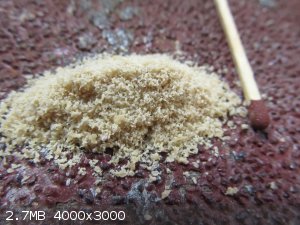
[Edited on 28-10-2014 by specialactivitieSK]
|
|
Hennig Brand
International Hazard
   
Posts: 1284
Registered: 7-6-2009
Member Is Offline
Mood: No Mood
|
|
Estimation of Percentage Nitrogen
Some more cotton was nitrated.
Materials:
9.8g Cotton Balls (oven dried for 60 minutes at 110C)
100g NH4NO3 (oven dried fertilizer grade)
180mL H2SO4 (91% drain cleaner)
Cotton was allowed to nitrate in the mixed acid for about 48 hours in a lightly sealed vessel at room temperature and in the dark. Post nitration, the
product was well washed and allowed to soak in dilute sodium bicarbonate solution for 48 hours before being well rinsed with clean water again.
Yield:
15.96g (dried at room temperature until weight ceased to decrease)
According to the text "Military Explosives", cotton oven dried at 110C would have a moisture content of about 0.5wt%. Cotton which is not oven dried
can easily contain 5-7% moisture content. Using the table in the following patent the moisture content of the air dried, at room temperature,
nitrocellulose should be approximately 2-2.5wt%.
Attachment: Patent With Nitrocellulose Moisture Contents US2312741.pdf (275kB) This file has been downloaded 1444 times
Compared to using a nitrometer the following method of determining percentage nitrogen is fairly crude, however it is a simple method to implement and
it should provide a useful approximation.
Theoretical maximum percentage nitrogen 14.14%; C6H7(NO2)3O5 is the formula for the monomer.
Nitrocellulose trinitrate monomer MW: 297 g/mol
Cellulose monomer MW: 162 g/mol
Assume oven dried cellulose had 0.5wt% water content.
Assume ambient air dried nitrocellulose had 2wt% water content.
Assume that other than water the cotton feed and nitrocellulose product had no impurities.
Assume no losses due to oxidation or loose fibers poured out during washing.
Approximation of Percentage Nitrogen:
Theoretical Yield
0.995 * (9.8g / 162g/mol) * 297g/mol = 17.88g
Percentage Nitrogen
0.98 * (15.96g / 17.88g) * 14.14%N = 12.37%N
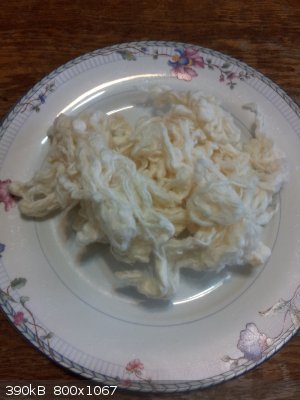
Found the following pdf online, which I thought might be useful. It is a brief overview of a nitrocellulose manufacturing process.
Attachment: Nitrocellulose Manufacturing Process.pdf (64kB) This file has been downloaded 2261 times
[Edited on 6-11-2014 by Hennig Brand]
"A risk-free world is a very dull world, one from which we are apt to learn little of consequence." -Geerat Vermeij
|
|
Hennig Brand
International Hazard
   
Posts: 1284
Registered: 7-6-2009
Member Is Offline
Mood: No Mood
|
|
This should have been included in the last post, but I didn't think to do it at the time.
A simple burn test was performed using less than a gram of the above nitrocellulose product loosely balled up. It burned extremely fast with a huge
whump sound and made a very large fireball which burned all of the hair off the fingers of the hand holding the wooden match. I was a little surprised
at how fast it burned given that the percent nitrogen was estimated to be only about 12.4%. I suppose 12.4% is not really very far from 13% though.
From what I have seen nitrocellulose with this level of nitration makes perfectly serviceable smokeless propellant, especially if used in a double
base formulation with nitroglycerine.
"A risk-free world is a very dull world, one from which we are apt to learn little of consequence." -Geerat Vermeij
|
|
TGT
Harmless
Posts: 46
Registered: 9-11-2014
Member Is Offline
Mood: No Mood
|
|
Hennig Brand, I am thoroughly interested in this thread and am amazed what you have achieved so far. I really never thought smokeless powder
comparable to factory could be made at home. Closest I have got to gun propellant is black powder lol.
One thing I wanted to mention, if you wanted to try using microcrystalline cellulose and don't mind the trouble, you can extract it from certain
brands of ASA that only contain that one additive. I currently have about four ounces of it from making picric acid. Just a thought. Keep up the
great work, I am extremely interested.
TGT
|
|
Microtek
National Hazard
  
Posts: 872
Registered: 23-9-2002
Member Is Offline
Mood: No Mood
|
|
Microcrystalline cellulose is extremely easy to make yourself. Just hydrolyse cotton wool with dilute hydrochloric acid (IIRC 10 % HCl was best). It
takes a couple of hours at ca. 90 C, and then you just filter and wash the product.
|
|
Hennig Brand
International Hazard
   
Posts: 1284
Registered: 7-6-2009
Member Is Offline
Mood: No Mood
|
|
I suppose microcrystalline cellulose would likely be easier to nitrate than a big fluffy piece of cotton. Mixing should be much easier for one.
Just found the following in the "Tri-Nitrocellulose" thread. I believe I read this thread several years ago and just forgot about it.
Quote: Originally posted by Rosco Bodine  | Microcrystalline cellulose should be easily nitratable , but I have never seen it described . IIRC , cellulose flour is what is the name for it as
a food additive and it is soluble like starch , but has a small number like 8 cellulose units which has a crystalline form . There are small bottles
sold as a dietary supplement ,
" soluble fiber " type of material for an inflated price . But the same material is sold cheaply in bulk as a thickener additive for foods , similar
to rice and potato flour . |
Quote: Originally posted by ordenblitz  | Roscoe,
You are correct that microcrystalline cellulose is easy to nitrate, much easier in fact since it is more dense that cotton and you can get more in the
mixed acids. You can stir it more effectively and it nitrates faster since the small crystals are better exposed to the acid. After nitration is
complete, leaving it to stand causes the MCNC to float to the surface of the acid in a dense layer that can be pulled out of a beaker in virtually one
chunk. This brings along less spent acid and allows faster quenching thus keeping the N content as high as possible. Stabilization is a breeze as well
since MCC does not have the tubular cellulose structure that cotton has therefore it traps less sulfuric acid esters. A short boil is all that's
needed. The best thing about MCNC is that it retains the physical characteristics of MCC. It compresses very well in a hard and durable plastic form.
Tabletted material looks very much like ivory.
I know a little bit about this since a while back, I applied for a patent on MCNC. They are slow at the USPTO it's not even in the pending list yet.
My last patent took 1.5 years to show up on the website after filing. |
[Edited on 12-11-2014 by Hennig Brand]
"A risk-free world is a very dull world, one from which we are apt to learn little of consequence." -Geerat Vermeij
|
|
Hennig Brand
International Hazard
   
Posts: 1284
Registered: 7-6-2009
Member Is Offline
Mood: No Mood
|
|
Estimation of Percentage Nitrogen Correction
I made a mistake in the above percentage nitrogen estimation. There was a week between when I performed the post reaction workup and when I actually
did the reporting. I simply forgot, and forgot to write down, that I didn't add the last couple pieces of cotton that were weighed out so the amount
of cotton nitrated was slightly less than reported. The method itself is still correct. Another experiment was just conducted where 4.99g of the same
oven dried cotton was nitrated in the same way but for only 35 hours (which I believe is still a long time past the point of diminishing returns so to
speak). A room temperature, air dried, yield of 8.52g was obtained which corresponds to 12.97%N estimated using the calculation from the first post. I
also found some rough notes for several other nitrocellulose syntheses that were conducted over the past few years, using essentially the same grade
of ammonium nitrate and the same concentration of sulfuric acid, and yields corresponded to percentage nitrogen values between 12.8 and 13.05%N in all
cases. In those earlier nitrations the cotton was not oven dried, so the cotton was assumed to contain 5% water instead of 0.5% (assumed value for the
oven dried cotton).
I also noticed that using significantly less nitration time, less sulfuric acid and ammonium nitrate, than what was used in the above example, still
produced about the same level of nitration. I believe I switched to using larger amounts of sulfuric acid and ammonium nitrate because it made the
process easier and also because it was felt that the level of nitration might be higher. I believed that extra time, especially when using a nitrate
salt instead of HNO3, would increase the level of nitration (this is true up to a point). Here is a link to a couple of yields reported back in 2011
by me in another nitrocellulose thread.
http://www.sciencemadness.org/talk/viewthread.php?tid=13957#...
I knew that percentage nitrogen value seemed awfully low. Sorry about that.
[Edited on 13-11-2014 by Hennig Brand]
"A risk-free world is a very dull world, one from which we are apt to learn little of consequence." -Geerat Vermeij
|
|
Rosco Bodine
Banned
Posts: 6370
Registered: 29-9-2004
Member Is Offline
Mood: analytical
|
|
The microcrystalline nitrocellulose would seem to be promising for making extremely fast small mesh powders for small caliber pistol or small caliber
rimfire loadings which may be able to tolerate hotter loadings that could damage larger caliber arms. This might even be a niche application for PETN
based or hybrid double or triple base mixture powders as a way of increasing energy for small caliber loadings using hot loads that would not be
tolerated in larger caliber arms. There has been commercial development of hotter and hotter powders for rimfire .22 and .22 magnum and there is an
even smaller BB or .17 caliber rimfire.
|
|
Hennig Brand
International Hazard
   
Posts: 1284
Registered: 7-6-2009
Member Is Offline
Mood: No Mood
|
|
Assuming that a stabilizer such as diphenylamine needs to be added to a microcrystalline nitrocellulose powder; do you think that simply washing the
powder with a solution of the stabilizer might be acceptable?
"A risk-free world is a very dull world, one from which we are apt to learn little of consequence." -Geerat Vermeij
|
|
Rosco Bodine
Banned
Posts: 6370
Registered: 29-9-2004
Member Is Offline
Mood: analytical
|
|
What are the long term storage stability characteristics for microcrystalline nitrocellulose I don't know. It may be easier to stabilize it since it
already has higher purity from synthesis and less inherent instability caused by impurities or occluded acidity. So something like a betaine or
cyanoguanidine solution soak and drying may be sufficient stabilization if stabilization is even needed. Testing is really the only way to find out
what is needed and what works.
|
|
Hennig Brand
International Hazard
   
Posts: 1284
Registered: 7-6-2009
Member Is Offline
Mood: No Mood
|
|
Wow, what a great thread! Here is a link to the "Tri-Nitrocellulose" thread, where the couple quotes above were taken from, and where microcrystalline
nitrocellulose is discussed in depth.
http://www.sciencemadness.org/talk/viewthread.php?tid=1007&a...
"A risk-free world is a very dull world, one from which we are apt to learn little of consequence." -Geerat Vermeij
|
|
Ral123
National Hazard
  
Posts: 735
Registered: 31-12-2011
Member Is Offline
Mood: No Mood
|
|
I don't know how one can get completely rid of the H2SO4 in the NC. I wonder if NC can be made with HNO3 only(with less yields then RDX or PETN). Such
cotton I guess will be very easy to purify and stabilize. Do you think such cotton can be used instead of lead styphnate, as a kick starter in fuse
cannons or as last option for blast cap base charge(I'd say the power is between AP and TNP)?
|
|
Rosco Bodine
Banned
Posts: 6370
Registered: 29-9-2004
Member Is Offline
Mood: analytical
|
|
sulfoester free nitrocellulose is possible
see this linked post for a patent US2776965
for the manufacture of sulfoester free nitrocellulose , where no sulfuric acid at all is present in the nitration mixture , but magnesium nitrate is
used in the place of sulfuric acid as a substitute dehydrating agent.
http://www.sciencemadness.org/talk/viewthread.php?tid=4701&a...
|
|
Hennig Brand
International Hazard
   
Posts: 1284
Registered: 7-6-2009
Member Is Offline
Mood: No Mood
|
|
According to COPAE and other sources it is impossible to completely remove residual acidy, and other contaminants produced during the nitration, from
nitrocellulose without additional special techniques that go way beyond simple washing. This is true at least for traditional nitration methods.
Nitrocellulose fibers are tubular in structure which act like little capillaries locking in residual acidy and preventing its removal by simple
washing and neutralization techniques. COPAE describes mechanical methods which process the nitrocellulose in such away so as to open up the fibers
exposing the interior more which then allows the removal of the impurities by washing and boiling processes. The text, "Military Explosives",
describes a poaching process where the nitrocellulose is boiled in a dilute sodium carbonate solution (2% solution IIRC), which as well as removing
acidity is supposed to break down and remove other impurities produced during the nitration (other esters, etc), which would otherwise lower
stability. I have kept several samples of highly nitrated cellulose in small quantities for a couple years or more and have always noticed that it is
significantly degraded in a matter of months even though it was extremely well washed and the residual acidity (at least on the exterior of the
fibers) was neutralized.
One very nice property of microcrystalline nitrocellulose is that it apparently does not have the tubular structure and so is very easy to wash and
stabilize. This is discussed in the thread I just linked to in the last post.
I don't know how well nitrocellulose would work as a base charge, but the microcrystalline nitrocellulose type would likely have the best chance of
performing well. From reading "Military Explosives", it seems that nitrocellulose can be at least as powerful as TNT when used as a detonating
explosive. Not entirely sure how even MCNN would perform in the small diameter of a blasting cap though. I may give it a try. The percentage nitrogen
and purity of RDX, PETN and NG, for instance, can be easily increased to very near the theoretical maximum by very simple washing and
recrystallization techniques which remove lower nitrates and other impurities. These simple purification processes are not possible with
nitrocellulose mostly because it is a polymer from what I understand. This makes production of high nitration level and high purity nitrocellulose
relatively labor intensive/difficult and expensive. Nitrocellulose makes fantastic propellants though.
"A risk-free world is a very dull world, one from which we are apt to learn little of consequence." -Geerat Vermeij
|
|
Pages:
1
2
3
4
5
..
10 |