Pages:
1
..
10
11
12
13 |
tentacles
Hazard to Others
 
Posts: 191
Registered: 11-11-2007
Member Is Offline
Mood: No Mood
|
|
Well, I've got more white almost-sludge precipitate in a beaker again. It sat there all day after I made it wednesday - was it wednesday? Anyhow, I
was all set to try making the stannic nitrate again, and I decided to test the B&D heatgun I picked up - what a piece of garbage! The box said
280/540C, but my thermocouple said very differently! I only got to 10mV - a pathetic 247C or so, and the damn thing died! So I scrapped plans to do
anything useful until I got a new heatgun.
Today I picked up another replacement unit (number 3!) and am considering disabling the low setting of death. I also looked at Rona up here, they have
a few models that look much more promising, including a Makita thermocouple controlled unit, and a standard industrial type heatgun. The Makita is
rated to 600C.
|
|
Rosco Bodine
Banned
Posts: 6370
Registered: 29-9-2004
Member Is Offline
Mood: analytical
|
|
Quote: | Originally posted by tentacles
Well, I've got more white almost-sludge precipitate in a beaker again. |
You might try the precipitation conditions described in US6777477 .
Alternately try limiting concentration of the SnCl4 to the 2 to 3% level , and doing a rapid simultaneous pour mixing of cool solutions into a like
volume of cool H2O containing the bare neutralization equivalent of NH4OH .
I am going to say limit the warming I suggested earlier to more like 40C , barely warm because of the attached reference which reports 60C will
convert the alpha to the meta stannic acid . This confirms what I suspected about the
instability of the alpha form , but describes the alpha as being even more prone to polymerization to meta at a lower temperature than I expected .
Evidently the precipitation temperature will be determinate on whether the alpha or the meta form is produced .
The attached patent US2460734 describes that the SnCl4 diluted in H2O to less than 4% concentration hydrolyzes completely in one hour at room
temperature to a dispersion , a sol of alpha stannic acid , and free hydrochloric acid .
So it is simply a matter of then neutralizing the free HCl and salting out the hydrated SnO2 by destabilizing the already existing sol .
I am going to get some ammonium bicarbonate so the method of US4775412 can be followed for precipitation of the alpha stannic oxyhydroxide .
Technically , this looks the easiest sure way .
A heat gun is going to be really pressed to do the job on the
tin oxide sintering . A well insulated furnace tube and maybe even some sort of thermal breaked holder for the anode substrate is probably needed .
The pure stannic nitrate which is being made here is not going to have good stability by itself . There may be improved stability required by
addition of a small amount of
ammonium nitrate , if there isn't sufficent residual ammonia
in the precipitated alpha stannic acid to supply it when the nitric acid is used for conversion to the nitrate . Also
a small amount of acetic or tartaric acid may be needed
to stabilize .
The compositions described in the Ordway article which are
complex mixtures have better stability than pure stannic nitrate , and may prove to be better precursors . Those
complex mixtures have stability better than straight stannic nitrate , but lower stability than the chlorides derived sols or alcoholates . The
patents which mentioned the usefulness
of the tin nitrate did not specify anything about the nature
of the tin nitrate composition to be used , so there could be
some tuning of that nitrate precursor required to get it right .
For example the precursor which works best could not surprisingly turn out to be a mixture of stannic nitrate and stannic chloride with acetic acid or
tartaric acid in small amount , or the mixture most desirable could be one of
the Ordway mixtures . Or it could fit the composition of
one of the Pytlewski mixed valency sort of polymers which
are also involved in some of the Ordway described mixtures .
Stannic nitrate alone may not prove to be the single answer
as an SnO2 precursor but only a component . Just pointing this uncertainty out concerning the stannic nitrate and the
context in which it is useful , is a long way from being fully described in any existing literature .....so what we are doing
is basically pure experimentation with regards to the finer points which do involve a few unknowns . 
Attachment: US2460734 Alpha Stannic Acid process.pdf (123kB) This file has been downloaded 1238 times
|
|
Rosco Bodine
Banned
Posts: 6370
Registered: 29-9-2004
Member Is Offline
Mood: analytical
|
|
Here is a hypothetical coating scheme based
upon a combination of spinels which are known .
An interesting series of bimetal spinels which
may have usefulness has caught my notice ,
in particular because of the known application
of zinc chloride as a flux in soldering and brazing .
TiZn2O4
SnZn2O4
TiCo2O4
SnCo2O4
ZnCo2O4
This series of spinels formed from a mixed nitrates and chlorides precursor system may form a very good interface
on a titanium substrate , *if* the fluxing property of the
zinc chloride at high temperature is effective on the
titanium . This would follow something like the idea of
the Beer patents where an increased thickness of mixed
oxides involving doped titanium oxide itself is included
in the interface layer ...thickened enough that it becomes
really a working coating . If the molten zinc chloride component does indeed attack and etch into the titanium itself or any oxide of titanium during
baking , the associated
possible spinels of TiZn2O4 and TiCo2O4 might function in
a manner which mimics ruthenium with regards to the doping effect on the titanium oxide . The unreacted Zn and Co
dopants could then further react with each other to form
a bimetal ZnCo2O4 spinel , and/or could form bimetal spinels
with the Sn , SnZn2O4 and SnCo2O4 . In an excess of SnO2
as the solvent oxide .....all of these possible spinels could form and all would be expected to be electrolytically active .
The ZnCo2O4 bimetal spinel has already been reported as useful for chlorate production . The usefulness of the other
possible spinels is unknown .
This is a possible combination of materials which could be good as an interface and sealing and working coating ,
all in one . Bismuth doping might also be added .
I haven't attempted to work out what precursor proportions would seem right . All of these spinels are expected film formers themselves and should
participate in the usual
DTO scheme where the SnO2 is the major phase .
It may be possible to work up the precursor
mixture by simply making with SnCl4 in minimal H2O a slurry of the carbonates of the cobalt and zinc and possibly bismuth , and then drip in nitric
acid to clear the mixture , and maybe add a few drops of acetic acid and perhaps glycerin .
|
|
tentacles
Hazard to Others
 
Posts: 191
Registered: 11-11-2007
Member Is Offline
Mood: No Mood
|
|
Well, in absence of further messing with making tin nitrate - I have instead made another small batch of SnCl4 based precursor, baked at 546C for two
coats, whereupon heat gun #4 said it's farewell.
I put down a Co interface layer and then two coats of the SnO2 based scheme as before. I did a little bake and checking, and it seems that it really
needs to bake hot to sinter in. I took it out at 515C and this was not hot enough; at that point I decided to just get it over 540C.
I guess it's time for a different brand of heatgun. I just hope I can get the bastards to refund me for this one w/o a receipt.
edit: I dunked this one in a KCl cell for now, it is evolving chlorine aggressively. I'll check on it again when I get home from work. Cell is running
on a 5V computer PSU. 25mA/cm^2 density. The anode is a bit far from the cathodes, about 5-6cm
another edit: Good thing I checked on it before I left - the anode started eroding from under the coating, at the edges at least. It's got sort of
pock marks on the edge, like round serrations. Perhaps it just needs to be sealed better, and I should probably smooth the edges of the Ti strips
better.
[Edited on 2-4-2008 by tentacles]
|
|
Rosco Bodine
Banned
Posts: 6370
Registered: 29-9-2004
Member Is Offline
Mood: analytical
|
|
Inorganic polymers and their quasi-inhibited precursors
are a barrel of fun , huh ? 
From everything I have read the alpha stannic hydroxide
is definitely unstable and heat sensitive , as is the stannic nitrate . So it may very well be better to go the Ordway route where some mixed chloride
and nitrate , as well as mixed valency polymer is present , in order to achieve stability .
There are references to alpha stannic acid which has been precipitated via hydrolysis of a heated very dilute solution
of a stannic salt , being converted to metastannic acid
if the solution is boiled more than just briefly . It may be partly polymerized at lower temperature over longer time .
So dilution , temperature and pH influence the precipitation and obviously there is a reaction conditions window which is favorable , but there is a
time window also , as the alpha form will tend to polymerize to the meta form at some unknown rate made worse by passing time and also by heating .
It would probably be best to avoid letting the alpha stannic acid precipitate stand for any extended time as it is unknown what its half-life may be .
The higher temperatures being required for complete conversion of the SnCl4 to SnO2 is a good reason by itself
to use something else as the precursor .
[Edited on 2-4-2008 by Rosco Bodine]
|
|
Rosco Bodine
Banned
Posts: 6370
Registered: 29-9-2004
Member Is Offline
Mood: analytical
|
|
another MMO of possible interest
Here's another mixed oxide which would be on my list of
prime suspects as having possible catalytic activity
for chlorate and perchlorate .
http://dx.doi.org/10.1016/S1293-2558(02)01356-0
Pb3Mn5V2O16: a new lead manganese vanadate with double MnII/MnIV valence
[Edited on 7-4-2008 by Rosco Bodine]
|
|
chloric1
International Hazard
   
Posts: 1146
Registered: 8-10-2003
Location: GroupVII of the periodic table
Member Is Offline
Mood: Stoichiometrically Balanced
|
|
DOI not found
The link....its dead Jim.
Fellow molecular manipulator
|
|
Rosco Bodine
Banned
Posts: 6370
Registered: 29-9-2004
Member Is Offline
Mood: analytical
|
|
Fixed the bum link . I forgot to use the url prefix and suffix and the forum software seems to not register the pasted link correctly without that
detail .
Above it was mentioned that these MMO compositions
are "inorganic polymers" , and that would seem to be
correct also in regards to the "isomers" of hydrated SnO2 .
The various forms of stannic acid all appear to be SnO2
differing only in their level of hydration and polymerization with the highest level of hydration and lowest level of polymerization being stannic
hydroxide , and the next dehydration step providing alpha stannic acid , which is
also unstable and polymerizes to a five unit molecule metastannic acid , which further dehydrates to SnO2 .
There are mixtures and degrees of dehydration and polymerization which may exist between those distinct
materials , and these are likely the "sols" where the
composition is indefinite and/or in transition with regards
to its state of hydration and polymerization of the precursor for the contained SnO2 component .
Dopant materials which have similar chemistry can substitute and cross link with the SnO2 , forming
complex inorganic polymers and glasses , ceramic
materials , or spinels , and possibly other complex
crystalline MMO compounds . Temperature has significant effect on the composition of the hydrated precursor mixtures and also what the end
composition of these mixtures will be after dehydration and sintering .
These materials behave similarly to "bakelite" formaldehyde resins as their organic analogue .
There is reportedly a lead ferrite , or lead-iron spinel which might be worth an experiment . It is PbFe2O4 . Have absolutely no information on it .
Reportedly also there are
similar spinels of iron with cobalt and manganese and titanium . CoFe2O4 , MnFe2O4 , TiFe2O4 . So a mixed precursor system containing as dopants ,
lead , cobalt , manganese and iron could have usefulness as a chlorate or perchlorate anode .
[Edited on 7-4-2008 by Rosco Bodine]
|
|
Ioxoi
Harmless
Posts: 20
Registered: 24-9-2007
Location: Upstate NY
Member Is Offline
Mood: Pensieve
|
|
Plate MMO
Hi guys,
I've seen Xenoid's coating procedure for Co / MnO2 onto titanium rods. He dips them and then bakes in a heat gun. Can this procedure be applied to Ti
plate? I'm going to get Mn(NO3)2, Co(NO3)2, and a big thin plate of Ti (12" x 5") for my birthday in a few months, and I'm gonna see if I can make
strip anodes. I'll cut the plate into strips and coat them with the solution.
What I'm gonna have to figure out is how to "bake" 'em. It'd be great if you could just shove the plates into a toaster, a la Pop Tarts, but I doubt
the coatings would come out good. Any ideas before I destroy a good Ti plate? Oven? Campfire?
Chuck Norris does not uphold laws. He is the law.
|
|
Xenoid
National Hazard
  
Posts: 775
Registered: 14-6-2007
Location: Springs Junction, New Zealand
Member Is Offline
Mood: Comfortably Numb
|
|
@ loxoi
I don't want to put you off experimenting, but if you are actually more interested in the chlorate and perchlorate rather than making anodes you may
be better off getting a "commercial" MMO and/or platinised Ti anode. Several of the pyrotechnics suppliers now have them in stock.
A toaster won't get hot enough for baking, a small toaster oven with maybe an extra element added might do the job, there is a discussion in (I think)
the Cobalt Oxide Anode thread. There is no reason you couldn't use a hot air gun with a strip Ti anode rather than a rod, provided it doesn't "blow
around" too much or is too big.
I have wondered about Ti sheet, I'm not sure what the coefficient of expansion is for Ti, but perhaps with a large surface area, bonding of coatings
may not be as effective as with a rod, due to contraction and expansion during the heat cycles.
|
|
tentacles
Hazard to Others
 
Posts: 191
Registered: 11-11-2007
Member Is Offline
Mood: No Mood
|
|
It's certainly POSSIBLE to use strips of Ti sheet - I haven't done any grueling tests to see how long they last though. The Co/Mn anodes seem to work
just fine for the couple hours I've run them. I just used a heat gun + tube oven for those. There's wasn't any problem with them swinging in the
breeze, at least with the gun I used. I just drilled a hole at the top and ran a piece of SS wire through, twisted it tight to make a handle and
spread the ends to support it.
|
|
chloric1
International Hazard
   
Posts: 1146
Registered: 8-10-2003
Location: GroupVII of the periodic table
Member Is Offline
Mood: Stoichiometrically Balanced
|
|
Quote: | Originally posted by Rosco Bodine
Here's another mixed oxide which would be on my list of
prime suspects as having possible catalytic activity
for chlorate and perchlorate .
http://dx.doi.org/10.1016/S1293-2558(02)01356-0
Pb3Mn5V2O16: a new lead manganese vanadate with double MnII/MnIV valence
[Edited on 7-4-2008 by Rosco Bodine] |
The abstract seems to suggest PbO2 found in "lattices". If this oxide cannot produce perchlorate, it should be amiable to LD plating
Fellow molecular manipulator
|
|
Rosco Bodine
Banned
Posts: 6370
Registered: 29-9-2004
Member Is Offline
Mood: analytical
|
|
diva update
Nothing new on the anode project because my time has been otherwise thoroughly occupied with other pressing business.
However, it does seem long overdue for a diva update,
so ....on this father's day especially for the other fathers
of daughters as myself, but for everyone else as well ....
enjoy
To Where You Are
http://www.youtube.com/watch?v=qZiS_Purjhg&feature=relat...
Walking In The Air
http://www.youtube.com/watch?v=Sfm0qNBZo1I&feature=relat...
Going Home
http://www.youtube.com/watch?v=oHBCXi7Ckuk&feature=relat...
Winter's Light
http://www.youtube.com/watch?v=GL_ag3NQ0o0&feature=relat...
Someday
http://www.youtube.com/watch?v=E9PLU6JYYpg
When You Believe
http://www.youtube.com/watch?v=nBUhGkMUoEI&feature=relat...
|
|
Leander
Harmless
Posts: 28
Registered: 23-2-2008
Member Is Offline
Mood: No Mood
|
|
Sorry for the topicbump, but this could be interesting. According to patent CA 1083337 a dense and uniform coat of MnO2 can by applied on a substrate
(aluminium and tantalium mentioned here) by means of a slurry of Mn(NO3)2, Mn(OH)2 and NH4NO3 in H2O with some methylcellulose for viscosity. This has
a couple of advantages over the traditional method of dipping your substrate in salt solution, and then thermal decomposing it. My gues is that a much
thicker coat can by applied this way, drasticly reducting the ammount of dips required for a nice coat.
Since English isn't my 1st language I haven't been able to find out yet what kind of industrial applications this invention is ment for. Production of
chlorate or perchlore is not mentioned.
|
|
Rosco Bodine
Banned
Posts: 6370
Registered: 29-9-2004
Member Is Offline
Mood: analytical
|
|
interesting recipe
Attached here is the US issue of the same patent as
US4148131
Actually the presence of microdispersed free carbon has been reported to lower the development temperature and baking time for nitrate precursors of
metallic oxides, and likely the same is true as well for easily carbonized precursor thickeners like methylcellulose. I have a journal article
related to that and I will try to find and post it as well.
Polyvinyl Alcohol has also been reported useful as a precursor solution thickener to increase the thickness building rate for doped tin oxide films
which are based
on stannate / bismuthate precursors.
Attachment: US4148131 MnO2 Baked Coating Method.pdf (719kB) This file has been downloaded 922 times
|
|
Rosco Bodine
Banned
Posts: 6370
Registered: 29-9-2004
Member Is Offline
Mood: analytical
|
|
possibly adaptable to MnCo2O4 spinel
The above patent is possibly applicable also in benefitting
the formation of better baked coatings of mixed nitrate precursors for bimetal spinels like MnCo2O4, or for mixed Co and Ni spinel , or the monometal
spinels.
The technique could certainly be easily enough tested to see if indeed a tougher baked coating results. The photosensitivity of the precursor mixture
is certainly new information that is noteworthy.
Attached is the journal article I mentioned earlier about the
effect of carbon in reaction with the nitrate precursors. I have hypothesized that mixed valency precursor salts
where some of the nitrate oxygen is available for reaction
with the lower valence metal ion should have a similar effect on promoting the pyrolysis.
Decomposition of mixed Mn and Co nitrates supported on carbon ( attached )
Definitely time for a diva break    
http://www.youtube.com/watch?v=VRFS_WxtMoA&feature=relat...
[Edited on 7-10-2008 by Rosco Bodine]
Attachment: Decomposition of mixed Mn and Co nitrates supported on carbon.pdf (236kB) This file has been downloaded 2417 times
|
|
Rosco Bodine
Banned
Posts: 6370
Registered: 29-9-2004
Member Is Offline
Mood: analytical
|
|
Niobium DTO anti-depassivation coated Ti Anode
Bismuth has already been identified in the literature as having good effect as a dopant for tin oxide useful as an oxygen diffusion barrier ,
anti-depassivation coating on Ti substrate anodes, the Bismuth also having catalytic activity in the production of perchlorate.
Niobium (formerly Columbium), a closely similar sister element of Tantalum found intermixed in their ores the same as Nickel and Cobalt, is also
reported in the literature to
have a similar value as a barrier to oxygen diffusion caused
passivation of a Titanium substrate anode. What may be
if any catalytic activity in the production of perchlorate is unknown. The patent US4471006 Niobium DTO enhanced oxygen anti-passivation Anode
describes how the combination of 5-valent Nb2O5 as a dopant material with
4-valent indigenous TiO2 or SnO2 also applied thereon,
results in an N-type semiconductor coating which is
anti-depassivating , allowing anodic current flow.
Probably Vanadium Pentoxide, V2O5 would behave similarly
and may even have catalytic effect via an unstable pervanadic state. This is something I have postulated earlier in some of these threads, but have
done no experiments to confirm. IIRC in one of the patents posted by
JPSmith a baked coating containing vanadium doping on a hydrided Ti substrate was a successful scheme.
Niobium compounds are probably three times as expensive
as Bismuth, but this still is much less expensive than Ruthenium / Platinum series candidates for the intermediate layer or DTO coatings, and because
of the excellent oxygen
diffusion barrier anti-depassivation performance reported for Niobium, this seemed worth making note . Niobium might find
usefulness in combination with other dopants or layered MMO schemes where the "labrynth effect" of differing oxygen
overvoltages for differing sequential layers is applied, testing
another one of Rosco's postulates , of course 
And obviously ....that's right , now it's time for another diva break 
http://www.youtube.com/watch?v=YNlpxJO1Uiw&feature=relat...
http://www.youtube.com/watch?v=koi_f3fB2h8&NR=1
Other Niobium related patents of possible interest are
US3950240 Niobium Doped Tin Oxide Anode
US4873352 Niobium DTO via Oxalate H2O2
Attachment: US4471006 Niobium DTO enhanced oxygen anti-passivation Anode.pdf (140kB) This file has been downloaded 1223 times
|
|
Rosco Bodine
Banned
Posts: 6370
Registered: 29-9-2004
Member Is Offline
Mood: analytical
|
|
another organic precursor MMO of possible interest
The last part of page 172 and all of page 173 in this book preview shows use of citric acid and ethylene glycol as useful carbon donors in a pyrolytic
decomposition of metal nitrate precursors, in the intermediate precursor form of a dispersed and polymerized sol-gel, which smoothly react to produce
on pyrolysis a substituted spinel-perovskite ferrite material
with no byproducts.
http://books.google.com/books?id=GHUttThdotcC&pg=PA172&a...
Bismuth, cobalt, and iron are the metals involved in this particular spinel-perovskite, which might be an interesting
material to use as a component in a doped tin oxide scheme,
seeing that chemistry of the precursors and the pyrolysis temperatures are compatable.
|
|
Swede
Hazard to Others
 
Posts: 491
Registered: 4-9-2008
Member Is Offline
Mood: No Mood
|
|
This slightly aged thread seems a good place to kick-start a bit - alternate anodes for electrochemistry as regards perchlorate.
We've beaten PbO2 to death. I'm playing catch-up on the Bismuth, tin, and cobalt options. Now it's time to explore boehmite. I've got the three
different varieties of boehmite on hand, and the following reagents:
Cobalt nitrate
Cu nitrate
Nickel nitrate
Tin (II) Chloride
Bismuth hydroxide
Bismuth Subnitrate
Lead nitrate
Lead dioxide
Lead monoxide
And assorted other reagents, in support of an anode attempt. I've been reading the literature as much as I can, and if you google "alumina tubules
catalyst", that sort of thing, the research is on in the "real world" at a fast and furious pace. Nano is the future, apparently, of catalytic
chemistry.
I'm looking for thoughts, an "angle", towards an alternate anode. I do have a precision furnace, good from 250 to 2000 f. Sand blaster too. Looking
at options! Really, the only thing I'd like to avoid is Platinum and Palladium, due to costs, both for me, and for anyone else if an anode actually
works.
[Edited on 27-1-2009 by Swede]
|
|
jpsmith123
National Hazard
  
Posts: 764
Registered: 24-6-2005
Member Is Offline
Mood: No Mood
|
|
Hello Swede,
With the nice workshop, resources, time, etc., you seem to have at your disposal, maybe you'd like to experiment with electrolytic DLC films?
The main equipment required would apparently be an adjustable HV power supply, say 0 to 1000 VDC @ 50 to 100 ma or so.
I'm presently trying to get my hands on a decent HV power (so far with no luck), and once I get one, I plan on trying to make DLC films from DMSO and
methanol (using boric acid as a boron source).
|
|
Rosco Bodine
Banned
Posts: 6370
Registered: 29-9-2004
Member Is Offline
Mood: analytical
|
|
@Swede, Among those other reagents is there nitric acid, acetic acid, ammonium hydroxide, ammonium carbonate or bicarbonate, ammonium fluoride or
bifluoride, hydrogen peroxide, citric acid, glycerine ?
BTW with regards to soluble Niobium salts, US5419824
describes a preparation of ammonium niobate which reportedly has good solubility in water.
There may be a fair amount of surplus Niobium-Titanium alloy wire available cheaply, as an associated scrap from the Cern supercollider
project.....and maybe some other relatively exotic materials also. I have been anticipating getting my hands on some of this scrap at some point and
contemplating possible uses for it .....like superduper anodes
[Edited on 27-1-2009 by Rosco Bodine]
|
|
Swede
Hazard to Others
 
Posts: 491
Registered: 4-9-2008
Member Is Offline
Mood: No Mood
|
|
@jps - A High voltage supply is something that I am currently lacking. DLC films - yet another resource to investigate! 
@RB - Of the additional reagents you mention, I am LACKING ammonium hydroxide in any real strength, acetic acid, and the ammonium fluorides... the
others I do have.
I'm digging through some of the boehmite literature right now - there is a lot of it. The basic problems - introduction of the catalyst into the
boehmite pore structure, transition of the catalyst(s) to active oxides, and dipping/adhering the slurry to an appropriate shank. I have some niobium
metal, and the possibility exists to create salts of niobium.
One limiting factor is temperature - above 400C, apparently the boehmite breaks down and the desirable microtubule structure is destroyed.
The anode obviously must conduct, and like the traditional electrodeposited lead dioxide anode, the barrier between PbO2 and Ti must not passivate.
Perhaps once again, the commercial MMO substrate may be the material of choice.
|
|
Rosco Bodine
Banned
Posts: 6370
Registered: 29-9-2004
Member Is Offline
Mood: analytical
|
|
Hold your horses on the MMO if you mean noble metal oxide ( NMO ) variant. And the literature you can read endlessly looking for ABC - 123 that you
will be lucky to ever find, particularly if it is stuff that is known already
ten different places but is kept in shop and proprietary with regards to a niche application end use like a perchlorate anode. Most of the metal
oxide technology literature is specific for sensors, other electronic devices, optical devices and other mass production items, and
perchlorate anodes are simply *not* a mass production item but an obscure kind of proprietary "factory utensil".
You are very possibly looking for a trade secret that isn't going to be found published anywhere.
There's a lot of stuff in the literature that is "read between the lines" and figure it out how it translates to whatever you are trying to do. Have
you got a blueprint
and drafting supply shop nearby? They keep and usually sell ammonium hydroxide of exceptional purity for use
as a developer in the diazo process for blueprints. You can probably get a gallon of 26 Baume ammonia ( NH3 29.4% solution in H2O ) for under twenty
bucks.
[Edited on 28-1-2009 by Rosco Bodine]
|
|
Xenoid
National Hazard
  
Posts: 775
Registered: 14-6-2007
Location: Springs Junction, New Zealand
Member Is Offline
Mood: Comfortably Numb
|
|
Some notes on MMO/MnO2 anodes from a while back!
Whilst not wanting to return to the heady days of early '08, I've been spending the last few months experimenting with an MnO2 anode aimed at
perchlorate production. Rather than try to coat etched Ti directly or via the Co2O3 interface layers, I decided to thermally coat some MMO mesh as it
is so readily available now.
I re-examined De Nora et. al's (Diamond Shamrock) 1978 US Patent Number 4072586 which among other things mentions applying thermally decomposed coats
of beta-MnO2 over thin layers of RuO2.TiO2 on Ti (aka MMO). Beta-MnO2 is apparently isomorphous (rutile structure) with RuO2 (and TiO2) and thus bonds
well to the MMO surface. In particular my attention was drawn to column 5 (lines 22 - 54), which mentions the suitability of beta MnO2 for perchlorate
production, especially when enhanced with up to 5% As, Sb or Bi (actual element not specified).
Indeed the thermal beta-MnO2 does indeed bond well to the MMO coating and will form a thick, hard, crusty coating. It will even bond directly to
non-etched oxide coated Ti, because of the rutile structure, but will of course be non-conducting.
Because of the size, instead of dipping the anode in the coating solutions, I used painting and eventually a spray technique. For mesh material,
spraying is ideal as it is easy to coat all surfaces of a complex electrode assembly. A small (30 ml) plastic perfume sprayer proved ideal.
For thermal decomposition I used the same hot air gun technique as described earlier. Because of the larger electrode size I used a larger diameter
tube and mounted it on a stand, otherwise the set-up was basically the same. The sprayed on coating was dried over the turned down hot air gun, this
prevents drips and runs. The electrode was then baked for 10 mins at about 380 oC. Initially 25 coats of Bi-doped MnO2 were applied.
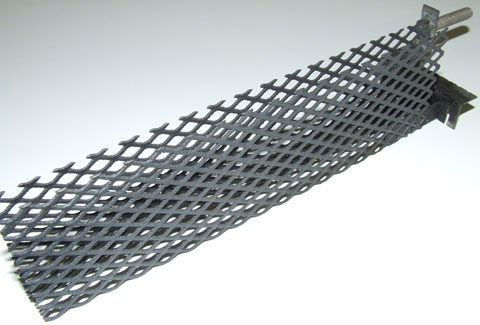
Crusty, black MnO2 thermal coating over MMO dual anode assembly.
Stock Solutions:
Mn(NO3)2 - made from pottery grade MnCO3 (31g) and 68% nitric acid (50 ml). This should fully react, may need a little more depending on purity of
MnCO3. Solution was filtered and made up to 100 ml, it contains 48.25g Mn(NO3)2 or 14.8 g Mn.
Bi(NO3)3 - crystals made by dissolving Bi metal in 68% nitric acid (see thread). 6g of moist (nitric acid) Bi(NO3)3.5H2O crystals were placed in a
small beaker and covered with 20 ml 68% nitric acid, diluted to 40 ml with water and stirred until dissolved. This solution was made up to 50 ml with
water in a volumetric flask and contains about .0635 g Bi / ml.
Co(NO3)2 - crystals made by double dissolution of CoSO4 and Ca(NO3)2 or reacting CoCO3 with 68% nitric acid (see thread). 10 g of moist crystals
(Co(NO3)2.6H2O) were dissolved in about 25 ml of water and made up to 50 ml in a volumetric flask. This solution contains .0405 g Co / ml
Dipping / Brushing / Spraying Solutions:
These are loosely based on Pat. #4072586, but are by no means definitive. They are just what I came up with for initial tests.
Pure MnO2: 16 ml of the Mn(NO3)2 stock was transferred to a 50 ml volumetric flask, along with 5 ml of isopropyl alcohol, and made up to 50 ml with
water.
Bi doped MnO2: 16 ml of Mn(NO3)2 stock was transferred to a 50 ml volumetric flask, along with 1 ml of the Bi(NO3)3 solution (.051 g Bi) and 5 ml of
isopropyl alcohol and made up to 50 ml with water. This solution is roughly 50g / litre Mn with 1.3% Bi in MnO2.
Co doped MnO2: 16 ml of Mn(NO3)2 stock was transferred to a 50 ml volumetric flask, along with 3 ml of the Co(NO3)2 solution (.121 g Co) and 5 ml of
isopropyl alcohol and made up to 50 ml with water. This solution is roughly 50g / litre Mn with 3.0% Co in MnO2.
|
|
Xenoid
National Hazard
  
Posts: 775
Registered: 14-6-2007
Location: Springs Junction, New Zealand
Member Is Offline
Mood: Comfortably Numb
|
|
Some results with the MMO/MnO2 anode.
I'll be the first to admit I have been less than scientific in testing this anode. Hopefully, because it's so simple to make, others will have a go at
evaluating it's performance as well. From the earlier work with MnO2 anodes, I knew they would make both chlorate and perchlorate, I really wanted to
test their practicality in this new configuration.
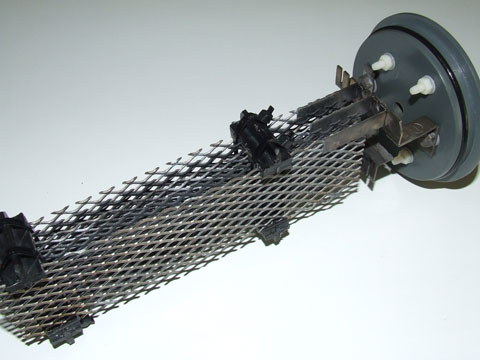
Electrode assembly, note 3 titanium cathodes and 5mm spacing!
All testing has been carried out in a 1 litre cell.
1. The anode assembly along with 3 Ti cathodes (5 mm spacing) was placed in a 100 g/L KClO3 solution (saturated at 30oC.). The pH was reduced by the
addition of 1 ml conc. HCl to about 2.8 this in an attempt to shift the Mn stability away from the wide end of the MnO4- field (high pH) and into the
region of maximum stability for MnO2. The idea behind this was to try and avoid the "Purple Haze" effect which plagued earlier efforts with MnO2
anodes. Sadly this had no effect whatsoever, and the cell turned pink within 15 mins. The cell was run at a conservative 3.8 V / 3.5 A, this limited
the temperature rise to 30oC. The cell was run for 48 hours (168 Ah), no perchlorate was detected during this time. A little, brown hydrated MnO2 was
deposited on the cathodes and the cell bottom and sides.
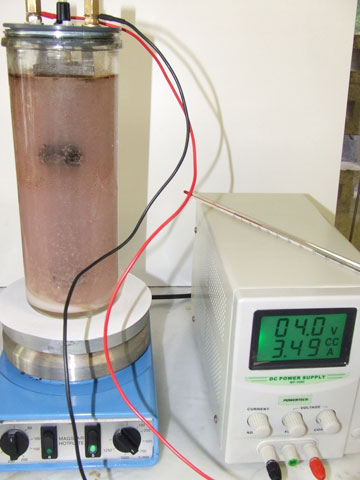
First assembled 1 litre test cell, note permanganate "Purple Haze" and MnO2 scum!
Thinking that perhaps the cell voltage was a little low for perchlorate production (industry use 5 - 6 Volts) I dismantled the cell and removed the
close spaced cathodes and replaced them with a single Ti mesh cathode spaced about 4 - 5 cm away. This had the immediate effect of raising the
required voltage to 5.7 V at 3.5 A. After a further 17.5 hours (61.2 Ah) in this new configuration there was still no positive test for perchlorate!
Disheartened, I tried an NaClO3 cell
2. The 1 litre cell was filled with 500g / L NaClO3 solution. The single cathode with 4 -5 cm spacing was retained and the cell operated at 4.8 V /
3.5 A. Cell colour was pale pink and a test for perchlorate was negative after 3 hours. The next day after 23 hours (80.5 Ah) a positive test for
perchlorate was obtained.
Heartened by this, I dismantled the cell and added another 10 coats of Bi-doped MnO2 to the anode assembly, although it still looked in good
condition. The electrode was reassembled with the original 3 Ti cathodes with 5 mm spacing, and the cell was connected to a new power supply and now
running at about 4.6 V / 7.8 A. The cell was run for a further 68 hours (530.4 Ah). Positive perchlorate tests were obtained directly from the warm
liquor.
3. The cell was dismantled and refilled with the 100 g/L KClO3 solution from earlier. The anode assembly was coated with an additional 5 coats of
Co-doped MnO2. A single Ti cathode with spacing of 5 to 10 mm was used. The cell was operated at about 5.8 V / 9.5 A for about 21 hours (199.5 Ah), no
perchlorate was detected.
4. The cell was dismantled and the anode assembly had an addditional 5 coats of pure (un-doped) MnO2 added. The reassembled cell was operated at about
5.2 V / 7.6 A for 21 hours (160 Ah), no perchlorate was detected.
5. Added 5 coats of Bi doped MnO2 to anode assembly and placed in a 300g / litre NaCl cell in an attempt to progressĀ all the way to perchlorate. The
cell was operated at about 8 - 9 Amps. After about 6 days and 1188Ah the presence of perchlorate was indicated. This became stronger, and after about
12 days (2376Ah) the cell was shut down (pH=8.3). The anode still appeared to be in good condition (still plenty of coating).
6. Started a new 1 litre cell containing about 80g / L KClO3 solution, this was mainly to test if the pink colouration was generated with well-used
(leached) MnO2 anodes. I used the anode assembly from the NaCl -> NaClO3 -> NaClO4 run. A pink colouration appeared in the cell within 15
minutes. I left the cell running at about 5.0V / 8.0A, after about 48 hours I got a positive test for perchlorate (384Ah).
7. I made 4 identical test strips of MMO coated with 5 coats of pure MnO2, 1.3%Bi/MnO2, 3.9%Bi/MnO2 and 3%Co/MnO2. I carried out some electrical
measurements with these anodes in NaClO3 solution, but there was no obvious difference in their performance.
Summary: Poor man's lead dioxide!
Pros: Very cheap, readily available, non-toxic and easy to make. Easy and quick to apply to an existing MMO coating (5 coats in an hour). Coat seems
to last quite well, and a few more can be added quickly before a run. Will make chlorate and perchlorate and will convert NaCl to NaClO4.
Cons: Contamination with pink MnO4- and brown MnO2. Not very efficient and require solutions to be highly concentrated. The low solubility of KClO3
means particularly low efficiency in this system.
[Edited on 15-3-2010 by Xenoid]
|
|
Pages:
1
..
10
11
12
13 |