arkoma - 17-5-2022 at 23:14
first, using a virtual kb so capitalization etc will suffer.
i recently got an ender three pro and i love it and since fourth of july is rapidly approaching im going to need to mill pyro mixtures. i looked on
thingiverse and found a drum which i printed, and i clobbered up some rollers with bearings out of a wheel chair, half inch pvc and some printed hubs
and supports. for a drive, i used a six rpm motor scavenged from a microwave, attached to a stick with a printed hub that friction fits a hub on the
drum.
i cant provide specific build instructions as this was clobbered together from what i had laying around and a budget of zero, but yall can get the
gist and it works well. the pla filament is surprisingly durable and im using buckshot as grinding media
drum with hub i attach drive to
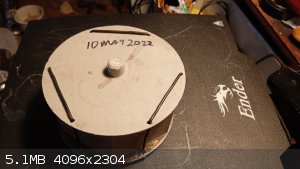
ghetto way of fastening it shut. one side glued on
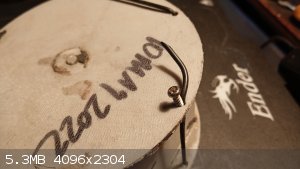
cardboard gasket
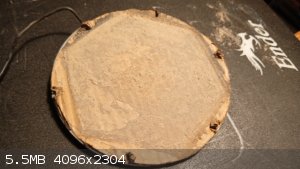
drive connecting hub
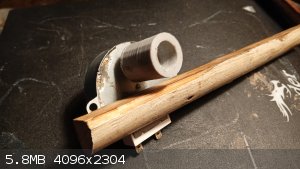
motor
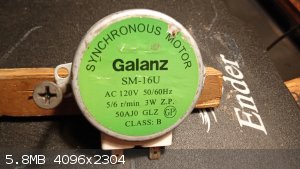
clobbered bearings for rollers. the base is from an old hp lcd monitor
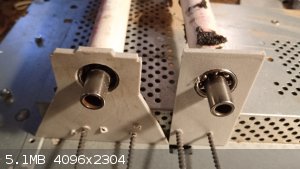
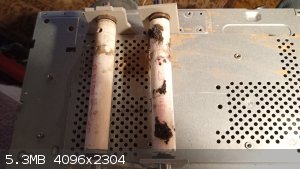
hey, it works
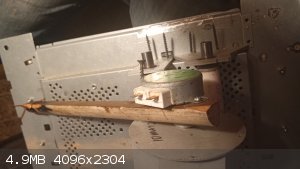
[Edited on 5-18-2022 by arkoma]
Mateo_swe - 18-5-2022 at 06:03
Thats very cool, good work.
DIYing something together from old stuff and 3D printed parts that gets the job done.
Nice idea with the microwave motor to get about right speed of the drum.
Did you cover the inside of the drum with anything or is it just PLA?
arkoma - 18-5-2022 at 21:01
just PLA, and it seems to be amazingly durable.
Now, if only i had a molecule printer. would only need carbon, hydrogen, nitrogen and oxygen lolol
wg48temp9 - 18-5-2022 at 22:14
I think you need a more powerful and faster motor, about 100 times faster.
See Attachment: ballmill-5.0030531.pdf (560kB)
This file has been downloaded 286 times
Mateo_swe - 19-5-2022 at 03:11
100 times the speed?
That would be 600rpm or 10 revolutiuons per second on the drum.
At that speed i think the balls would stick to the sides by centrifugal force and wouldnt fall and crush the material.
I have no experience with ball mills, anyone know what speed range is usually used?
A stepper motor with a driver could be used to make the speed adjustable.
I would guess a speed like a 1 to 2 revs per second on the drum is enough for the topspeed.
One could use a section of a big plastic pipe for the drum but then i think some ridges must be placed inside to make it effective.
The 6-side drum design is probably good.
Arkoma, what is the diameter of the drum on your DIY ballmill and how much powder can you mill per run?
[Edited on 2022-5-19 by Mateo_swe]
Fulmen - 19-5-2022 at 04:54
The optimal speed depends on several factors including jar and media size. For a 4" jar it will be around 100rpm, for a 6" around 75.
Mateo_swe - 19-5-2022 at 05:06
OK, but is that motor rpm or the drums rpm?
Most ballmills have a reduction in the motors rpm by a gearbox, like the pic below.
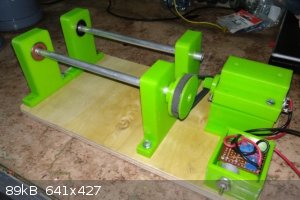
arkoma - 19-5-2022 at 07:14
This thing cost me $0.00 and has been running almost continuously since i clobbered it together. my drum speed is six rpm. sixty seems ridiculously
fast.
Bottom line: It works, and the grandkids and I will have a BLAST lolol
drum diameter about six inches and i am milling fifty grams at a time, using four shotshells worth of double ought buckshot as grinding media.
(I AM the forum redneck lololol!)
[Edited on 5-19-2022 by arkoma]
about 8 hours of milling
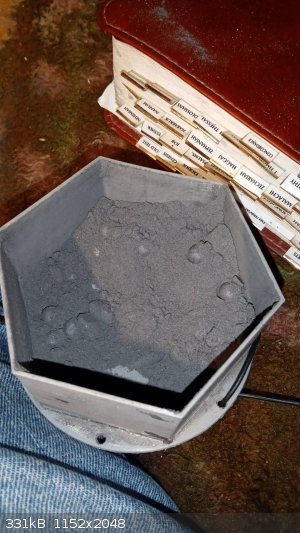
[Edited on 5-19-2022 by arkoma]
Fulmen - 19-5-2022 at 11:07
@Mateo_swe: Drum RPM. Lloyd Sponenburgh published a booklet on ball mill theory for black powder mfg, it might be available online. It covers
everything you need to know to optimize the process, a good mill should be able to produce commercial quality meal in 2-3 hours.
Fantasma4500 - 19-5-2022 at 11:32
depending on what material is to be grinded- long rods have also been applied, rods that spans from one end of the container to the other
i believe a bunch of nuts and bolts could also work quite well
a very large vibrator might also work if the material is porous, such as MgAl
as for the speed of the drum- the ideal is that the balls fall from the back and down at the front- so you also wanna use appropriate amount of
grinding media to get the ideal grinding effect
https://www.youtube.com/watch?v=L6sgGXXYdEU
having an oddly shaped container will help the process greatly and will work well for slower rpm as the media gets alternated around a bit with each
time it hits a corner, but can be extremely noisy- i worked at a metal workshop where we made our own ballmill for knocking the oxide coating off as
well as the nasty edges from plasma cutting- it was unbearably loud, and it had maybe 12 "corners" around
wg48temp9 - 19-5-2022 at 12:50
Assuming the OP is in 50Hz land that means the motor rotates at 5 rpm.
If the ratio between the drive rod diameter and the drum diameter is 5 then the drum will rotate just once a minute.
If the motor rpm was increased x100 the drum would rotate 100rpm thats once every 0.6s. That's about optimum for that size of drum
judging from the rpm of a stone tumbler I once had. For more accurate drum rpm consult the note I posted.
Below is a diagram showing the ideal path of the ball as described by Antiswat.
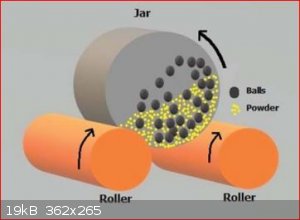
The above is abademic as the OP is happy/accepts the performance he has achieved with the motor he had available.
PS: Incidentally the rods, bearings or bushings, motor and gearing can all be found in old big printers particulier powder type. The rubber covered
rollers bars are great for grip and reducing noise.
Plunkett - 19-5-2022 at 14:20
You can even print the bearings if you are so inclined. I have used the design linked below (not my design) for a jig I built and it has held up well
running for 20 hours at 40 rpm. I drive the bearing with a 3D printed gear bolted to the inner race.
https://youtu.be/5o4Fj8OxkB8
arkoma - 20-5-2022 at 03:07
wg, i have 60 hz power and DIRECT drive the drum, hence it turn at SIX revolutions per minute NOT one. I admit its NOT elegant but it WORKS.
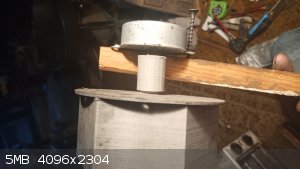
edit--this thread has garnered some activity at least. been like a ghost town up in here lately!
[Edited on 5-20-2022 by arkoma]
Mateo_swe - 20-5-2022 at 09:58
The drum rotation on Arkomas model is made so the motor drives the drums centre axle directly, ie. the motor rpm is the same as the whole drums rpm.
If you have a ballmill where the motor drives a roller that the drum is placed on then the drum will rotate slower than the motor rpm.
Most ballmills i have seen have some kind of gearbox reduction to lower the motors rpm to fit the drums rpm.
So what is the good rpm span on the motor for a ballmill will depend on how its constructed but also on the drums size.
If you have a large drum, lower revolutions per second will be needed.
But 5 rpm seem to work good on Arkoma´s 6 inch diameter drum and 50g material each run seem a nice amount for some homemade firework mixes.
I think i must DIY together a similar ballmill as i have motor parts and 2 types of 3D printers.
Its just going to cost me some time and fireworks is fun.
Mateo_swe - 30-5-2022 at 05:58
I see the ballmills for sale has a rubber drum. I guess thats a good thing if one want to ballmill firework powders.
I see there are rubber joint couplings for sale that is used to connect two pipes.
These might be a good starting point for a DIY rubber drum. The metallic fasteners on the ends must be perfect for securing the endplugs.
Only drawback is that these are completly round inside. Maybe some ridges can be put inside to make the drum more effective.
They come in 4 and 6 inch diameter variants.
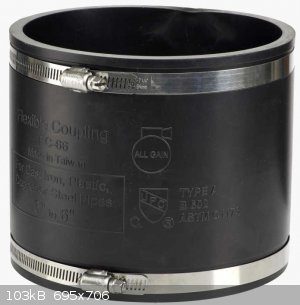
Rubber drum
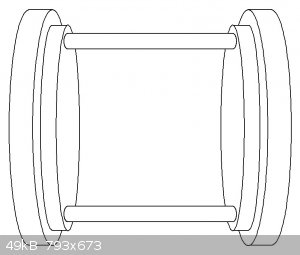
Maybe some wood/plastic rods in the endplugs to make it more effective.
[Edited on 2022-5-30 by Mateo_swe]
[Edited on 2022-5-30 by Mateo_swe]
Fulmen - 30-5-2022 at 11:36
I'm not sure you need any lifters. In a properly charged mill the rubber would most likely have enough friction for normal milling (cascade). Rubber
is also quite abrasion resistant, sounds like a great idea.
Fyndium - 31-5-2022 at 08:25
You can do as I did. I clamped two plywood flanges together with threaded rods and between them I clamped a PVC tube to act as a drum. I glued it to
the other plywood piece to make it more like jar. You can seal the other one by gluing a thin rubber sheet (1mm for example) to the other flange. Main
problem: noise. It was not an issue back then when I ran the mill in a remote building where it could rattle on it's own. You needed hearing
protection when in the same space. Rubber tube, or rubber lined tube would mitigate most of this issue.
That system was direct mid drive with reduction V-belt system with 300W single phase electric motor scavenged from a drill press, as it was made about
10 years ago and discarded about 5. Now I would 3D print most of the parts and use rollers to drive the drum directly with the flanges.
For electric motor, there are kits with speed controllers on Aliexpress I see. They're not that cheap, but at least it's plug and play. Stupid it is
that 750W motor costs less than 100W motor, but at least it's dual use then.
I want it to run sufficiently fast, from 30 to 180-300rpm, because it has dual use as a wet tumbling polisher. The drum should not need ridges or
angles, if the rotational speed is sufficient, as the ball mill is based on principle that centrifugal force lifts the medium to the apogee which is
close to the top of the drum, where it gravitates down, and the impact causes most of the effect. Too slow, and the mill just merely rolls everything
like a hamster wheel, too fast and it becomes a centrifuge.
Someone 3D printed a tumbler that was driven with a stepper motor and it was just awkwardly slow, it merely made a single revolution in 10 seconds if
even less. The guy demonstrated tumble polishing, ran the thing for a week and had very little effect on parts. Meanwhile, when I run my current
tumbler at half speed, I can get shot burnished parts in 1-2 hours.
[Edited on 31-5-2022 by Fyndium]
macckone - 31-5-2022 at 11:15
my ball mill has been through a number of iterations of motor.
anything less than 250w just isn't going to last and provide the required speed.
the ideal speed is about 75% of centrifugal, which for a four inch container is around 149 rpm
that is about 111 rpm.
shaded pole motors have been unable to give the required torque and brushed motors simply wear out.
it really requires a 1/4HP minimum unless you are running very lightly loaded.
Mateo_swe - 31-5-2022 at 23:02
Well i have different brushless motors from erlier RC hobby things with controllers and a motor with 0-600rpm that i erlier had plans to use for a DIY
rotovap idea.
I also have a big brushless motor meant for skateboards and a suitable controller.
I dont know how the brushless controllers will do if run for long times, maybe with good cooling it will work.
The speed must be adjusted to right area so it doesnt go to slow and also doesnt make the balls and media stick to the walls by centrifugal forces.
But i guess i can adjust that speed to the right one with some trials.
Fyndium - 2-6-2022 at 03:10
Yeah the issue with small motors and controllers is if you are running them at full load they will quickly burn out, especially when they are not
designed to be ran 24/7. Big motors will run with 10-20% duty cycle when fully loaded by the smaller ball mill and should last pretty much
indefinitely. Most of those recreational device motors are intended to be ran for very short duty cycles.
I 3D printed a 3-phase planetary reduction helical gear set just for fun, but I think that these gears could be used as reduction for these types of
applications as well. The gears are pretty quiet, unless ran at high rpm, naturally the reduction ratio is way too high, something like 1:72, but
changing ratios and dropping an extra phase off it could work great. It could also be attached directly on axial line of the ball mill.
Better yet, I would likely use PolyV belt with 3D printed pulleys. You can swap the pulleys as you wish to get the best torque to RPM ratio, pulleys
are very quiet and efficient and easy to adjust. Belts are also cheap and come in almost any size. Gears have serious drawbacks in all of these areas.
Mateo_swe - 5-6-2022 at 01:50
I was thinking about using my big brushless motor designed for a skateboard and a belt and pully like the one in the pic.
Its a 1 to 3 reduction with 20 and 60 teeth.
I have a driver for the motor but i dont know if it can do long runtimes.
I find out i guess.
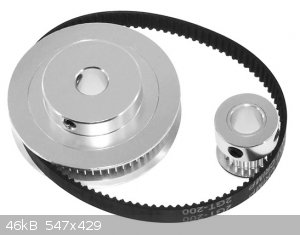
Fyndium - 6-6-2022 at 00:58
Check out PolyV belts. They are more flexible, efficient and quiet than toothed belts and should not cost more.
If the driver current capacity is rated high, it will have no trouble. Controllers burn because they are too small and are being run at 100% power to
their rated. E-bike controllers of bad origin are exactly this, and my friend burned _six_ of them under warranty over one spring, until the importer
just called it a day and sourced an improved unit, and the problem went away. If your max power is 10A, you wanna have at least 15-25A controller.
Fulmen - 6-6-2022 at 11:52
One way to extend the life of such components is additional cooling.
Mateo_swe - 7-6-2022 at 09:11
The big brushless motor i have is 120kv, max 150A, several kilowatt in max rating.
Its meant for electric skateboards and it takes much power to get a 100kg person going on these things.
I dont have a skateboard motor driver board but i have another driver board.
Its nowhere near the wattage needed for the motor in a skateboard application but it works with the motor.
It´s max 36V but it drives the motor nicely with enough rpm for my ball-mill i think and it has a heatsink.
If its get too hot i have to figure out another solution.
So these PolyV belts are those with the grooves lengthwise.
I guess i could use those if i find wheels in the right dimensions.
I look into it, thanks.
One question, I read one should´t use PVC pipes for the ball-mill drums.
Does it not have enough strength or cant handle the pounding of the lead balls?
I ask because i fix my house now and have some 100mm or 125mm diameter PVC pipes in the trash bin.
I could use those for extra smaller ballmill drums, if they can be used for this.
[Edited on 2022-6-7 by Mateo_swe]
Fulmen - 7-6-2022 at 10:47
I don't know of any reason for not using PVC, in fact Lloyd who pioneered these mills back in the day recommends it.
Could it be that you're thinking of PVC mortars? These are not recommended as PVC produces hard fragments that don't show up well on x-ray. A mill is
a bomb filled with lead shots, a little bit of PVC will be the least of your problems.
[Edited on 7-6-22 by Fulmen]
Mateo_swe - 8-6-2022 at 00:47
I searched for the info where it said PVC was not suitable for ball-mill drums but i cant find it now.
Maybe i was mixing it up with mortars as you said.
I see many uses PVC as ball-mill drums for example ElementalMaker on youtube.
Thats good news as i can use the PVC pipes for many drums and have one for aluminium, one for blackpowder, one for charcoal etc.
Good to have dedicated drums for a specific materials.
It would be fun if i can make some fireworks that actually look good or even better than the store bought fireworks.
Where i live there has been many new regulation regarding fireworks in recent times.
Now they cant sell stick rockets any more and the bigger tube fireworks were removed 2 years ago after a accident where a kid looked down the tube
when it fired.
Also fireworks have been used in riots and fired at the police so unfortunately there probably is more restrictions coming.
Good to know how to make your own fireworks, soon its going to be gone in the stores even at new year.