Rainwater - 26-2-2022 at 14:08
I need some iron powder for an experiment and have plenty of scrap steel.
I was watching this video
https://youtu.be/8ZQ67POLiqg
At time index 7:00, he says that by making a solution of sodium bisulfate, you are able to plate out iron filings at the cathode.
I didn't have any bisulfate, but I do have some iron contaminated H2SO4
So, I added 400mL water, 100mL sulfuric acid, 2 iron rods, and 2.5volts
Before applying power, my iron rods started bubbling.
H2SO4 + Fe = H2 + FeSO4
After applying power, my anode began pulsing with bubbles.. Some times, the bubbles would come to a complete stop, and the current would jump to
3.5amps
Then, the bubbles would return and blow off a black layer; the current would drop again.
Anyways. Does anyone know if this reaction is possible? My understanding was that irons electronegativity was greater than that of hydrogen, so H2
would plate out.
I am getting a black percipitate falling off my anode. Which is magnetic
hodges - 26-2-2022 at 14:44
>Some times, the bubbles would come to a complete stop, and the current would jump to 3.5amps
Sounds like the iron that formed shorted out your power supply? Happens a lot when electroplating with high currents - you get dendrites that short
out the circuit.
>Before applying power, my iron rods started bubbling.
H2SO4 + Fe = H2 + FeSO4
Then your H2SO4 is too strong. You are going to be working against that reaction for any iron metal formed. Try diluting more. The only reason for
the acid or salt is to increase the electrical conductivity, since pure water hardly conducts at all. A small amount should be sufficient when using
an acid.
Rainwater - 26-2-2022 at 15:11
Thank you.
I removed my solution and then returned 50mL and added 450ml water.. 5 amps 2 volts.
Apparently, the iron will float.
And was shorting out the electrodes
I taped up the cathode down to the last little bit. And suspended it in the middle of the breaker with a magnet attached outside the glass. Seams to
be pulling everything to one side. Thanks again
barbs09 - 27-2-2022 at 03:11
Depending on the amount required, you could precipitate iron oxalate out of solution and heat the oxalate to decompose to Fe and CO2.
https://www.amazingrust.com/Experiments/how_to/Pyrophoric_Fe...
Rainwater - 27-2-2022 at 10:20
barbs09.
I can't figure out how to get the powder out of the test tube without it catching fire.
The oxalate seams to produce a much finer powder than what i was expecting.
My electrolysis has produced a few grams. Have them drying under vacuum now.
P.s. Your url doesn't work
EDIT:
well i just dryed carbon powder or something. Non magnetic. Guessing i used way to much acid.
Round 2
[Edited on 27-2-2022 by Rainwater]
DraconicAcid - 27-2-2022 at 10:38
Don't take it out of the test tube. Add the other reactants to it.
Rainwater - 27-2-2022 at 15:38
Round 2 results - failed
495ml water
5ml sulfuric acid
.2 amps is all i could push
Same non-magnetic black powder. Same anode bubbles pulses, not dendrites. Pasivation layer. When it covers the anode, only the tip is exposed, which
makes bubbles that knock off the layer. Then, all is good, and the layer reforms. Cool to watch but waste of power and time
Round 3 - Success
30g KHSO4
Top beaker off to 500ml mark with h2o
Applied current
Magnetic particals immediately started forming at the cathode.
(Edit) current was reduced so no gas was formed on the anode
Intresting notes. The formation of gas at the anode is directly proportional to the current density of the anode. Tested gas. Relights spent and when
combined with the gas at the cathode, boom.
And to comment on my origional post, im a fool and was reviewing the electronegativity charts, not the Standard Electrode
Potential
[Edited on 28-2-2022 by Rainwater]
mysteriusbhoice - 27-2-2022 at 23:20
if you want to make iron powder you can make iron citrate and pyrolize it.
If you want to electroplate iron using sulfates it is possible BUT it requires a membrane and a proper setup to prevent the formation of iron 3 ions.
The anode side chamber is dillute 10% sulfuric acid and the membrane used is either an IEM or porous PVC membrane.
The cathode side chamber is a mix of 5% sulfuric and ferrous sulfate along with iron nails at the bottom or some kind of source of iron not connected
to any electrical source.
The anode is lead,Pt,PbO2,Ir-Ta and the cathode is anything you want to plate iron onto like copper steel etc.
current density is 10ma/cm^2
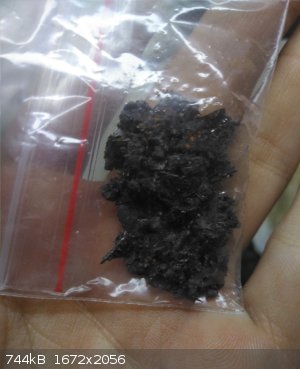
Rainwater - 28-2-2022 at 16:17
I just made pyrophoric iron again.
Steps of round 3 then dried under vacuum for 2 hours @ 100c. As soon as i started bleeding pressure back into the system, it started glowing. So i
stopped. I submerge the flask in a bath of co2 (vinegar + baking soda) then opened the flask and added mineral oil.
Id say on air, fine iron is more reactive than liquid sodium.
Rainwater - 5-3-2022 at 06:25
Final proposed procedure.
30g KHSO4
400 ml water
1 glass tubes (8mm id)
2 iron electrodes
5 amps
24 hours
1 50ml beaker
1 1000ml beaker
Okay, so a long sewing niddle for the cathode was causing partical size problems. I was pushing 5 amps on a surface area of about < 3mm. After
switching to a larger cathode, 3/16 rod, the flammable of the dry product is much less.
I'm thinking the stream on H2 was helping to reduce the partical size
By srouding the cathode in a glass tube, and suspending the electrode a few cm from the end of the tube, any orange non-magnetic floading stuff was
contained, then eventually reduced back to black non-magnetic floating powder, which after a few hours converted into black sinking magnetic
stuff.(product)
By placing the cathode and tube into a beaker, which was itself submerged inside the electrolyte, i was able to keep the product from being
contaminated by the powders falling off the anode.
As well as preventing dendrites from shorting out the leads.
As well as make collection of the product much easier.
By using a stirbar on the slowest setting i could manage, i was able to further prevent dendrites from shorting the leads
With the larger partical size, vacuum drying was no longer needed to prevent combustion of the finished product. I was able to dry the powder on the
hotplate on a watchglass with minimal red iron forming. The product dried in a vacuum contained no visual red iron.
Now, I need to figure out how to calculate yields and impurities.
Fantasma4500 - 14-3-2022 at 09:44
i know this is done with zinc using sodium zincate, ZnO dissolved in NaOH, which partially protects the zinc. the zinc you get is super fine
iron hydroxide would maybe be soluble in very concentrated NaOH, maybe molten NaOH? cheap hotplate and Al2O3 insulation would make it very doable to
keep the NaOH molten
i also did manage to produce some fine steel dust by reacting H2SO4 with steel granules from bandsaw
you may also visit a factory that works with steel and locate their belt grinder, they feature about 1L bucket underneath that catches the burning
iron, you will have a mixture of iron and Fe3O4 powder- and some stainless/aluminium incase they also grind that, oftenly when emptying these things
ive seen a lot of grey iron dust, its well packed down in there, i'd say sometimes above 100mesh particle size, depending on what grit the sandpaper
they use on the machine.
i have myself used iron oxalated "in situ", if you just mix it up with whatever and heat it, as long as the other reagent isnt organic it will do
something for you, the iron oxide resulting from this is very fine but settles within 20 minutes of standing
the FeOx reaction does also form some FeO, but this is also reducing.
as you mentioned some magnetic powder, Fe3O4 is magnetic, upon heating with air Fe3O4 turns into Fe2O3, Fe3O4 also rapidly reacts with 30% HCl- if its
iron dust it will form hydrogen with HCl and might react a lot slower