Pages:
1
2 |
Xenoid
National Hazard
  
Posts: 775
Registered: 14-6-2007
Location: Springs Junction, New Zealand
Member Is Offline
Mood: Comfortably Numb
|
|
Hanovia Bright Platinum coated anodes!
Has anyone here had any experiences trying to coat Titanium with Hanovia Bright Platinum Lustre (Engelhards), as used by potters, etc.
I saw it mentioned on the UK pyro society forums a few years ago, but I couldn't find any follow up!
http://www.pyrosociety.org.uk/forum/index.php?showtopic=426&...
Basically you paint it on to a substrate (ceramic, glass or metal) and fire it at about 800oC, it forms a thin film of Pt after the binders have
burned off.
It comes in a 2g container and you use thinners (dispersant) with it, I'm not sure of the coverage, you can put on multiple layers.
My local pottery supplier here in the land of the long white cloud (who charges like a wounded bull) says he can get it for about NZ$40, but it is
available on eBay at Merlins Ceramics for about US$19 and the dispersant is about US$8
I would appreciate any feedback on this product!
Xenoid
[Edited on 13-12-2007 by Xenoid]
[Edited on 13-12-2007 by Xenoid]
|
|
Xenoid
National Hazard
  
Posts: 775
Registered: 14-6-2007
Location: Springs Junction, New Zealand
Member Is Offline
Mood: Comfortably Numb
|
|
Platinum and Gold Lustres for Electrodes and Catalysts
Can someone change the title of this (very short) thread to the following;
Platinum and Gold Lustres for Electrodes and Catalysts
Hmmmm..... Guess I have to reply to my own post... not a good sign!
I did some further research and got a lot more hits by dropping the "Hanovia" and using "bright platinum lustre" for the search. I gather that
"Hanovia" is an Engelhard trade name, referencing the the early Hanoverian Period, when the technique became popular in Europe.
'Because of a scarcity of gold during the Napoleonic Wars, most potters turned to a silver lustre that was produced with platinum chloride and was
known as “poor man's silver” for its resemblance to the more expensive Sheffield plate.'
'Lustre decoration is carried out by applying a colloid suspension of finely powdered gold, silver, platinum, or copper to the glazed and fired
object. On a further, gentle firing, gold yields a purplish colour, silver a pale straw colour, platinum retains its natural hue, and copper varies
from lemonish yellow to gold and rich brown'
'To simulate silverwork, wares were completely covered with platinum lustre, which remains unchanged in colour after firing (silver itself yields a
pale straw colour); the amount of metal used was extremely small. Such wares were known as poor man's silver....'
'Silver Lustre was first made in 1791 by applying a solution of platinum chloride, which is subsequently reduced to a metallic deposit on the surface
of the pottery. Early ware was lustred inside and outside, but later the lustre was applied only to the outside. Silver lustre "resist" comes into
this second period. This ware was made as an imitation of silver ware, and the models follow the designs of the silversmith frequently.'
It is interesting to note that at this time silver was considered to be more valuable than platinum..... how times have changed, with Pt being about
two orders of magnitude more expensive now.
I also got in touch with a pottery supplier here in NZ who had this to say;
"We do not stock the Hanovia lustres - not sure if they are obtainable now in New Zealand. We do stock Liquid Bright Platinum in 2g bottles, 5g
bottles or 100g or parts thereof. 2g of English Platinum is $15.00, larger quantities become cheaper per gram. We also stock Fay Good lustres,
including platinum, this being a little more expensive than the English Platinum."
On requesting further detailed information they replied thus;
"I have been perusing our technical data, have always believed that the platinum lustre actually contains platinum, just as the gold contains gold.
Have no reason to believe otherwise, however, have not come up with the composition of the lustre. Have sold this for many years - we do not know the
purpose you need this for. Our platinum comes from Johnson Matthey, England. We have bought direct from them for the past 25 years. We sell to
potters and porcelain artists, and they are quite satisfied with these products. Firing temperature is recommended 750C to 800C. Have never heard of
using glycerine or glycerol with these lustres. Would definitely not recommend this. Also, we do not recommend thinning lustres unless they have
become dehydrated. You should not need to thin these down, otherwise you end up with thin metal. However, we do have special Gold, Platinum and
Lustre Thinners if required. The only way is to try it."
The price quoted, NZ$15 (US$12) is very cheap from what I have seen advertised in ceramics suppliers worldwide (US$15 - 50), it must be old stock. I
am definitely going to order some to experiment with. It should be possible to paint this on Ti to make platinized titanium electrodes or dilute it
with an organic solvent and soak asbestos (or whatever the modern equivalent is) to make platinized asbestos catalyst. The gold and copper lustres
could be useful for making electronic devices such as sensors, by painting on glass surfaces, etc. The 750oC temperature required for firing can be
easily obtained by the home amateur. If you do not have access to a kiln, a baffled hot air gun would probably get that high.
The platinum lustre presumably consists of platinum tetrachloride or more likely hydrochloroplatinic acid mixed with a viscous, reducing, organic
paint. The mention above of gold producing a purple colour, may be a reference to the "Purple of Cassius" produced from stannous, stannic and gold
chlorides and resulting in a solid solution of gold in colloidal stannic acid. The gold lustre on porcelain is probably derived from straight auric
chloride or more likely chloroauric acid.
Xenoid
[Edited on 13-12-2007 by Xenoid]
|
|
dann2
International Hazard
   
Posts: 1523
Registered: 31-1-2007
Member Is Offline
Mood: No Mood
|
|
Hello,
Guess I will throw in my 2 (or is it one) cents worth.
Reports of Ti plated with thin coatings of Pt from (Per)Chlorate makers have not been very incouraging. If the coating is not thick (min. about 80
micron AFAIK) it will soon disappear and this seems to happen even if anode is not abused.
What thickness will the Pt luster give on a Ti substrate?
I suppose you could put on a few coates, firing each as you go.
Could the luster be used to make DSA perhaps.
I tried inquiring about this stuff way way back but came to the conclusion that "Pt luster" was just brass or some such. Guess I was wrong.
Dann2
|
|
dann2
International Hazard
   
Posts: 1523
Registered: 31-1-2007
Member Is Offline
Mood: No Mood
|
|
Hello,
I fotgot! The platinised/plated Ti might be a good substrate for a Lead Dioxide anode.
Easier than DTO on Ti ......
Dann2
|
|
dann2
International Hazard
   
Posts: 1523
Registered: 31-1-2007
Member Is Offline
Mood: No Mood
|
|
Hello Xenoid,
Do you have a link to ebay describing the Potters Platinum from Merlins Ceramics . I am unable to find Merlins or the Potters Pt.
Cheers,
Dann2
|
|
Xenoid
National Hazard
  
Posts: 775
Registered: 14-6-2007
Location: Springs Junction, New Zealand
Member Is Offline
Mood: Comfortably Numb
|
|
Hi Dann2
The web page I came across was;
http://cgi.ebay.ca/Hanovia-Bright-Platnum-2-grams_W0QQitemZ2...
Most pottery supply places have "liquid bright platinum" though not necessarily the "Hanovia" brand. As I mentioned above, there is a WIDE VARIATION
in price, so shop around.
I have just ordered 5g from the NZ pottery supplier I mentioned above, I thought I would get some for experimenting with whilst it was at a
comparitively low price... 
I came across these other snippets, whilst perusing the subject;
From the Engelhard site (Engelhard are now owned by BASF);
NOTE - They also have a liquid Palladium which could be useful for making catalysts.
Gold, Platinum and Palladium Coatings
Precious metals are the premier engineered coatings offered by BASF. Gold, the metal revered by all cultures in all recorded times, remains the most
highly sought metal throughout the ages. Platinum, also known as “white gold,” has become immensely popular in recent decades, often exceeding the
value of gold in the marketplace. Palladium speaks a grandeur all its own with a spectacular silver-white appearance. All of these precious metals are
available in liquid and paste form to be applied and fired in your process, and they can raise your product to the epitome.
How they work.
BASF precious metals are applied as thin films by brush, roller, screening, pad stamping or spray. The film in the unfired “raw” state is black,
brown or sometimes reddish and resembles shoe polish in both sight and aroma.
The film is fired onto the glass or ceramic product and the result is a rich metal coating of gold, platinum or palladium. Products BASF offers gold,
platinum and palladium coatings for glass, glazed ceramic, glazed earthenware, china, porcelain and porcelain enamel. There are preparations available
for application techniques including direct screening, machine lining and brushing.
Gold preparations for glass are 8 - 20% gold by weight with fired films ranging from 18-23 karat. Products have been specially formulated for soda
lime, silica and Pyrex® glass. Additional offerings can be used for borosilicate, zinc, silica and bismuth based glazes. Gold preparations for
ceramic use are 6 – 25% gold by weight. Products for glass fire in process at 1050 - 1150ºF and product for ceramic fire at 1300 - 1500ºF.
Particular durability and service requirements can be addressed with BASF MicroPruf™ gold and platinum products. These products have been used in
microwave ovens. Additionally, these products are renowned for their dishwashing durability. They have the highest resistance to mechanical abrasion
of all precious metal decorative products available anywhere.
Here is a description of a platinum coated anode, it was stuck in with a whole bunch of ruthenium based anodes in a patent application.
EXAMPLE 5
26.7 gm of `Hanovia 05X` liquid bright platinum paint manufactured by Engelhard Industries Limited was diluted with 13.3 gm of thinning essence. To
this solution 4.5 gm "Zircosil 5" was added. The paint was thoroughly mixed and applied to an etched experimental titanium anode section similar to
that described in Example 4.
In this case the sample was dried at 180.degree. C. and then fired at 450.degree. C. after each application of paint so as to produce a coating
consisting of a matrix of electrocatalytically active platinum metal in which was dispersed the inorganic refractory additive. The total final loading
was equivalent to 36 gm of coating (platinum plus ZrSiO.sub.4) per meter square projected anode area. This loading corresponded to a composition by
volume of approximately 9% platinum and 91% zirconium silicate (ZrSiO.sub.4). The titanium strips thus coated had a low overpotential for chlorine
evolution (80 mV at 10 kA/m.sup.2) and passed a current of only 2 to 4 amps/cm of titanium strip when immersed to a depth of 4 mm in flowing mercury
with an applied voltage of 4.2 volts. A similar coating prepared from `Hanovia 05X` paint but this time without the addition of "Zircosil 5", allowed
a heavy current (greater than 100 amps/cm), to flow as soon as the anode sample touched the mercury surface.
Another reference for the use as an electrode;
The electrode patterns can be produced by spray coating a glass slide and mask combination with dispersions of metallic (preferably platinum)
particles in an organic or aqueous carrier. A preferred dispersion of platinum particles in an organic carrier is the inexpensive paint product sold
under the tradename LIQUID BRIGHT PLATINUM by Wale Apparatus (Hellertown, Pa.). The patterned slide is then baked in a high temperature oven in the
presence of oxygen or air to produce a thin conductive layer of pure platinum. This technique enables production of thin, high surface area,
mechanically robust, low resistance, platinum electrodes on glass slides.
Xenoid
[Edited on 7-1-2008 by Xenoid]
[Edited on 7-1-2008 by Xenoid]
|
|
Rosco Bodine
Banned
Posts: 6370
Registered: 29-9-2004
Member Is Offline
Mood: analytical
|
|
@dann2
Oxalic acid is reportedly good for etching the titanium according to US3650861 , in preparation for a platinum plating applied by baking or
electroplating .
The DTO coatings on titanium should and would very likely go better if you tried some of the alternatives which were suggested . The volatility and
corrosiveness of your mixed chlorides is simply incompatable with what you are trying to do . The patents you were following simply did not tell the
whole story in any one example as a verbatim "how to" , and almost certainly left out details which were
"mission critical" in the abbreviated descriptions which were given .
Attachment: US3650861 Etching_TITANIUM_by_Oxalic_Acid.pdf (134kB) This file has been downloaded 1191 times
|
|
Xenoid
National Hazard
  
Posts: 775
Registered: 14-6-2007
Location: Springs Junction, New Zealand
Member Is Offline
Mood: Comfortably Numb
|
|
An inauspicious start.............. 
Well, my liquid bright platinum arrived. It's a viscous, dark reddish-brown liquid with a strong pine resin smell.
For a initial attempt at using it, I thought I would try coating a strip of glass (about 10cm x 1.5cm). The strip was washed with detergent and wiped
with acetone. The platinum lustre was then painted on (a single coat looked a bit patchy) so I applied another, which gave a good solid coat. The
slide was dried with a hot air gun on low heat (maybe 50oC).
It was then "baked" in stainless steel bowl, on a gas ring. The bowl had a small hole in the base and the lid for ventilation. The slide was supported
on a "W" shaped piece of stainless steel. The temperature was slowly raised so as not to crack the glass. I am not sure of the exact temperature
achieved, but the base of the bowl was glowing "red hot". During this time much resinous smelling smoke issued from the hole in the lid. After about
15 mins. the temperature was slowly lowered.
When the slide was examined, it did indeed have a platinum coating but it had many imperfections and the lustre was hardly "bright" (see lower image).
I decided to give it a bit of a wipe with a tissue moistened with a little detergent, unfortunately this resulted in the coating being wiped off.....

Needless to say the coating is extremely thin, but I'm not sure why it didn't adhere to the glass. I gather there are slightly different compositions
for glass vs. porcelain but it shouldn't have made this much difference. Perhaps the temperature was too low!
Xenoid
|
|
evil_lurker
National Hazard
  
Posts: 767
Registered: 12-3-2005
Location: United States of Elbonia
Member Is Offline
Mood: On the wagon again.
|
|
Porcelain is somewhat porous, glass is not.
Thats probably why it didn't stick too good.
Not all chemicals are bad. Without chemicals such as hydrogen and oxygen, for example, there would be no way to make water, a vital ingredient in
beer.
|
|
nazcalito
Harmless
Posts: 1
Registered: 13-10-2009
Member Is Offline
Mood: No Mood
|
|
Metallic lusters like liquid bright palladium need to be fired in a kiln between 600 and 1000 C. for a couple of hours at least. Underfired luster
will rub off as you discovered.
If you have flat pieces of glass that can be heated to that temperature without melting them, you can use those. Otherwise, you need flat pieces of
porcelain that have been glazed with a clear or neutral lead free glaze. If you use unglazed porcelain, the luster will sink into the pores and will
not be shiny. I don't know whether that will work for anode purposes but I suspect not.
You can use thick ceramic paper as the substrate for the electrode but this will need to be bisqued, glazed, and high-fired in an electric kiln (not
gas) before applying the luster.
You can make an even coating of the luster by using a Badger fingernail airbrush. Look in a ceramics manual for directions on how to fire ceramic
lusters. I imagine that once you fire the initial coating, you can probably build up a thick layer of palladium via electroplating.
Obviously, these electrodes will be somewhat fragile. . .
[Edited on 13-10-2009 by nazcalito]
[Edited on 13-10-2009 by nazcalito]
[Edited on 13-10-2009 by nazcalito]
[Edited on 13-10-2009 by nazcalito]
|
|
Xenoid
National Hazard
  
Posts: 775
Registered: 14-6-2007
Location: Springs Junction, New Zealand
Member Is Offline
Mood: Comfortably Numb
|
|
Thanks for that information nazcalito. I'll have to admit I didn't try very hard!
There are several potters around where I live, I should probably have got more advice and asked to use their kilns. I tried coating Ti rod and sheet
(in another thread) also with little success. In the mean time I purchased a commercial platinum coated Ti mesh anode which has proved to be rugged
and reliable for a number of electrolysis experiments.
As I have mentioned previously, Pt lustre resin would be useful for the amateur in preparing catalysts on substrates like fibre glass etc. I still
have plans to try some diluted resin soaked into unglazed porcelain and fired, to make a fuel cell electrode.
Xenoid
|
|
Swede
Hazard to Others
 
Posts: 491
Registered: 4-9-2008
Member Is Offline
Mood: No Mood
|
|
Interesting old thread that I had missed. This sort of material seems to me to have a decent potential. A section of MMO has a velvety appearance
under a microscope, making a surface that would probably be an excellent substrate. The manufacturers of MMO over Ti do all the difficult and tricky
grunt work in preparing the bare Ti for coating with the MMO; we may as well leave that to them, and simply paint this stuff over the MMO and pop it
into a bench muffle or similar.
|
|
Xenoid
National Hazard
  
Posts: 775
Registered: 14-6-2007
Location: Springs Junction, New Zealand
Member Is Offline
Mood: Comfortably Numb
|
|
Yes, I agree Swede, plenty of scope for experimentation, I never tried it on MMO. Not having a temperature controlled muffle furnace or kiln was a big
drawback. BTW a little goes a long way, my 5g phial is still half full.
Go for it - I would like to see some experimental results.
|
|
12AX7
Post Harlot
   
Posts: 4803
Registered: 8-3-2005
Location: oscillating
Member Is Offline
Mood: informative
|
|
My experience with electroplated platinum goes similarly: it wipes off unless fired. I went into the 800C range for a few minutes, with so-so
results. Supposedly, I should use dinitro diammine platinate or something to that effect.
Incidentially, Brauer p.1566 seems to give a remarkably familiar formulation: turpentine, lavender oil, alcohol and pitch are variously used.
Tim
|
|
dann2
International Hazard
   
Posts: 1523
Registered: 31-1-2007
Member Is Offline
Mood: No Mood
|
|
Hello Folks,
On page 31 of the attached doc there is some reading on Pt 'Paints'. Perhaps paints have changed/moved on from then. (This doc would have been
uploaded before somewhere or other)
They are definately an interesting route to possible Pt Anodes. The deposition on top of MMO sounds interesting. I think bare (etched) Ti is OK
though.
Does the potters Pt paint have a finite shelf life?
Dann2
Attachment: pmrj_pt.pdf (580kB) This file has been downloaded 962 times
[Edited on 14-10-2009 by dann2]
|
|
PolarSmokes
Harmless
Posts: 14
Registered: 26-10-2009
Member Is Offline
Mood: No Mood
|
|
800-1000C seems like a very high temperature for glass. I'm sure there are other ceramics that could be used, but many of them are porous. Magnetite
may be ideal. If we are thinking of an anode for a perchlorate cell, magnetite does not show very much wear, and would conduct electricity to the
platinum, should any electrical pathways get disrupted.
|
|
ChrisWhewell
Hazard to Self

Posts: 66
Registered: 22-12-2009
Location: Austin
Member Is Offline
Mood: No Mood
|
|
The issue is substrate preparation, if the Ti isn't a nascent surface free of oxide, adhesion of the noble metal is greatly diminished. Even two
seconds in the air adversely affects it, although not visible to the naked eye - it must go immediately from the anodizing bath into the plating bath.
|
|
Fleaker
International Hazard
   
Posts: 1252
Registered: 19-6-2005
Member Is Offline
Mood: nucleophilic
|
|
I've mentioned this numerous times before. Titanium can be platinum plated, but it must go wet (and soon) from its etchant solution directly into the
plating bath.
Neither flask nor beaker.
"Kid, you don't even know just what you don't know. "
--The Dark Lord Sauron
|
|
ChrisWhewell
Hazard to Self

Posts: 66
Registered: 22-12-2009
Location: Austin
Member Is Offline
Mood: No Mood
|
|
If you can, check out Eltech's early DSA(TM) electrode patents from the 80's, I recall the name of the first inventor is Beer. Described ewre
chloride-bearing paintable/fireable paste compositions which after application to the substrate decompose during baking to effectively clean the Ti
surface in situ to provide superior bonding. Eltech probably made billions from that invention. Wet methods for cleaning Ti are not the way to go.
|
|
Sedit
International Hazard
   
Posts: 1939
Registered: 23-11-2008
Member Is Offline
Mood: Manic Expressive
|
|
I don't think its been mentioned yet but have you tryed etching the glass with NaOH prior to coating attempts? I would think that it would aid in
holding the material on much better then plain smooth glass would.
Knowledge is useless to useless people...
"I see a lot of patterns in our behavior as a nation that parallel a lot of other historical processes. The fall of Rome, the fall of Germany — the
fall of the ruling country, the people who think they can do whatever they want without anybody else's consent. I've seen this story
before."~Maynard James Keenan
|
|
dann2
International Hazard
   
Posts: 1523
Registered: 31-1-2007
Member Is Offline
Mood: No Mood
|
|
Easy Pt Anode??????????
Hello,
Easy Pt Anode??????????
See bottom for patent. Pt, HCl, Nitric and Hydroxylamine Hydrochloride is all you need (+ bake). They used Ta.
From Lambda's book from page 579 of actual book:
9.7.3.2.9 Platinized Titanium and Niobium Anodes (70/30 Pt/Ir)
The improvement of the noble-metal-coated-titanium anodes was the starting point of the
study and preparation of platinized titanium anodes by the thermal decomposition of
a precursor with the pioneering work of, for example, Angell and Deriaz, both from ICI.98,99 The
precursor consisted of a given mixture of hexachloroplatinic (H2PtCl6) and hexachloroiridic
acids (H2IrCl6) dissolved in an appropriate organic solvent (e.g., linalool, isopropanol, or ethyl
acetoacetate). Prior to applying the painting solution, the titanium substrate was thoroughly
sandblasted to increase roughness and chemically etched to remove the passivating layer.
Etchants included various chemicals such as hot concentrated hydrochloric acid, hot 10 wt.%
oxalic acid, and hot 30 wt.% sulfuric acid. After each application the treated piece underwent a
long thermal treatment at high temperature in air between 400 and 500°C. At that temperature
thermal oxidation of the underlying titanium substrate is negligible. This original protocol
was inspired by Taylor’s works100 used in the 1930s to obtain reflective coatings of Pt on glass
for the manufacture of optical mirrors. The study of the thermal decomposition of these particular
painting solutions was conducted by Hopper101 in 1923 and more recently by Kuo102 in
1974. Other companies interested in platinized titanium anodes prepared by thermal decomposition
were Engelhard103 and Ionics.104 After long-term trials, the formulation and procedure
were finally optimized. These anodes were initially commercialized in 1968 by IMI (Marston)
under the trade name K-type® or 70/30 Pt/Ir.105 For optimum performance, the commercially
pure titanium must be from ASTM grade 1 or 2 with equiaxed grain sizes ranging between 30
and 50 μm. The electrocatalytic coating consists of platinum and rhodium present in their
metallic forms either as separate phases or as platinum-iridium intermetallic. In fact, after
thermal decomposition titanium is coated with a highly divided mixture of metal oxides consisting
essentially of 70 wt.% PtOx to 30 wt.% IrOx. The common anode loading is 10 g.m–2.
Later, Millington106 observed that niobium, tantalum, and even tungsten107 could also be used
as substrates, but they were only considered by certain suppliers108 when titanium showed
deficiencies owing to their greater cost. These anodes were rapidly used in numerous processes
requiring a long service life under severe conditions. For example, they were employed for the cathodic protection of immersed plants such as oil
rigs, storage tanks, and
subterranean pipe-lines,109,110 in the electrolytic processes for the production of sodium hypochlorite,
111 electrodialysis, for regeneration of Ce(IV) in perchloric or nitric acid,112 and for
oxidation of sulfuric acid in peroxodisulfuric acid.113 It is interesting to note that De Nora registered
a patent on a Pt-coated anode in which the base metal was a ferrosilicon with some
amounts of chromium.114 Other formulations consisted of clad platinum metal on a copperclad
titanium or niobium core by roll bonding or a sandwich of platinum-titanium (or niobium)-
copper. This technique, which provides a thick, dense, and impervious platinum coating,
is now commercialized by Anomet in the USA for the cathodic protection of oil rigs. This
continuous research effort, always developed under pressure from industry, resulted in the
1960s in a new generation of anodes that are still widely used in all electrochemical fields and
are discussed below. Nevertheless, although platinized titanium electrodes were found active,
they still were found to be unsatisfactory for chlorine production. It was for this reason that
Beer patented a new type of anode, discussed in the next section
Reading the book that Lambda has uploaded I came accross a patent for thermal decomposition of Pt compounds for Anodes.
Chloro-Platinic acid (from Pt metal + Aqua Rega) and Hydroxylamine Hydrochloride was painted onto Ta and baked.
Sounds simple enough. Only a few grams of Pt required.
Is Hydroxylamine Hydorchloride easy/hard to come by?
Dann2
Attachment: US 3117023 Pt Thermal deposition.pdf (177kB) This file has been downloaded 793 times
[Edited on 19-1-2010 by dann2]
|
|
dann2
International Hazard
   
Posts: 1523
Registered: 31-1-2007
Member Is Offline
Mood: No Mood
|
|
Hello,
Attached is two patents on making Pt + Ir Anode by paint and bake methods.
Essential Oils are used as carriers for the Pt + Ir compounds. The Kooks will be up in arms at their use for making Anodes!
Might try this out some time.
The advantage with paint and bake over electroplaing for the Platinum Garage Perk. Guru is that only very small amounts of Pt (and Ir) are needed, the
exact final amount of Pt (+ Ir) that you have decided to invest in actually. If you are going to coat (say) 20cm squared of Ti, you only need whatever
amount of Pt (+ Ir) that is finally going onto that surface area. Approx. 50 to 100 grams per square meter is the usual 'loadding'. 20cm squared will
need 0.1 grams of Pt @ 50g/m^2 loading (if using just Pt). 40cm squared, you will need 0.2 grams etc.
This is in total contrast to electroplating where you are going to have to make up a Pt solution that is large enough to hold the sheet of Ti + room
for Cathodes + you need extra solution (extra Pt) as you are not going to be able to plate untill the Pt has been depleted out of the solution. Also
you cannot plate Pt + Ir at the same time? (Pt + Ir are best for Chlorate I think but it's probable not that important and may not be best for
Perchlorate)
Paint and bake in the way to go for homemade Pt Anodes!
Am I right
OR
Am I right, I ask? 
Dann2
Attachment: painted_pt.rar (1MB) This file has been downloaded 775 times
|
|
Xenoid
National Hazard
  
Posts: 775
Registered: 14-6-2007
Location: Springs Junction, New Zealand
Member Is Offline
Mood: Comfortably Numb
|
|
Since there seems to be some renewed interest in the "bright platinum" product used by potters, I carried out a few more tests.
I took a piece of "fairly worn" black MMO mesh (9 cm x 2.5 cm), and applied a single coat of "bright platinum" resin paint. I placed the mesh in my
previously described, primitive, stainless steel bowl oven which had been preheated to "around" 500 oC and put the lid on. There was an immediate
"pooof" as the volatiles ignited, and smoke issued from the bowl. After about 1 minute, when the smoke had stopped, I lifted the lid to be greeted by
the fine looking Pt electrode shown below.
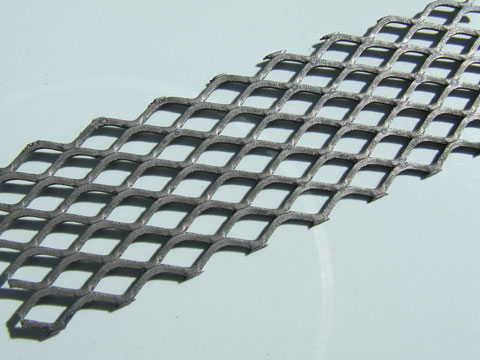
The Pt coat appeared well bonded (didn't rub off with a finger) so I popped it in a small cell containing saturated NaClO3 solution at 4.0 V / 2.5 A.
After about 10 mins. I could see that it was eroding (especially in the headspace region just above the solution surface). I removed the electrode and
examined it with a lens, the remaining Pt appeared to be well adhered, it just "looked thin". I put it back in some KClO3 and ran it at up to 3.6 amps
for several hours, there was still some areas of Pt remaining.
Deciding that one coating was just too thin, a further 5 coats (painting and baking each) were applied, this took only about 10 mins. I didn't take a
photo. because it looked similar to the image with 1 coat. This was run for several hours at various currents up to 3.6 A and various current
densities (increased by pulling the electrode further out of the solution). The parts of electrode in solution held up fairly well, but again the
headspace region was badly eroded.
So, thermally applied Pt does bond readily to MMO coatings. It is even feasible that a working perchlorate electrode could be built by applying more
coats. Alternatively it could be used as a base coat for electroplating Pt over MMO. Although it may be possible to plate Pt directly on to MMO.
|
|
dann2
International Hazard
   
Posts: 1523
Registered: 31-1-2007
Member Is Offline
Mood: No Mood
|
|
Hello Xenoid,
You may be better off going with a bare etched piece of clean, new, (or sandpapered) Ti as opposed to an MMO coated piece of Ti. In your particular
case you do not know what state the MMO is in or if there is indeed MMO on particular parts of the Ti. ( I am assuming you are using a piece of second
hand MMO out of one of the used pool Chlorinator Anodes). It is a very 'unknown' substrate to start with.
I have never heard of Pt being put on top of MMO, though there is always a first time.
I think that alot (if not all) of the Pt Anodes that are being offered for sale are made by the thermal Pt deposition method (what you are doing) and
are not electroplated Pt Anodes. Could be wrong though.
'Smooth' Pt or smooth Pt/Ir (that's solid Pt or electroplated Pt) is the best for Perchlorate making AFAIK because it wears less.
The best for cathylitic activity is actually an 'alloy' of 30/70 Ir/Pt thermally deposited alloy but it seems to wear more than the smooth though of
course Industry will chase small advantages sometimes
Try a small piece of new, etched Ti for the luster.
Two good reads on Pt thermal deposited (and electroplate) coatings (first half of paper (II) only) for Chlorate production below. (These papers
appeared somewhere or other on SM before)
The thermaly deposited Anodes lasted 8 to 10 years (not bad, huh).
The thermally deposited 30/70 Ir/Pt is not actually an alloy of metals at all. It's 30% Ir as Ir Oxide and 70% Pt metal.
Cells need to be kept above 80 grams per litre Chloride (better above 100g/l) to stop erosion. At low Chloride concentrations (few g/l) the Anodes can
erode away in a few hours! (that's in Chlorate cells)
Pt metals review Part (I) (this paper has been posted up the thread a bit)
Pt metals review Part (II)
Cheers,
Dann2
[Edited on 25-1-2010 by dann2]
|
|
Xenoid
National Hazard
  
Posts: 775
Registered: 14-6-2007
Location: Springs Junction, New Zealand
Member Is Offline
Mood: Comfortably Numb
|
|
Quote: Originally posted by dann2  | You may be better off going with a bare etched piece of clean new (or sandpapered) Ti as opposed to an MMO coated piece of Ti. In your particular
case you do not know what state the MMO is in or if there is indeed MMO on particular parts of the Ti. ( I am assuming you are using a piece of second
hand MMO out of one of the used pool Chlorinator Anodes). It is a very 'unknown' substrate to start with.
|
Hi dann2
I have already tried etched (standard HCl treatment) Ti sheet and rod, I mentioned it in a post earlier in this thread. It didn't last long, although
it was only one coat. You are correct about the chlorinator anodes, some which are black, are in fact fully passivated. One needs to check carefully
before use. In the case above, I checked the coating first.
I have recently been doing some thermal baking of oxides over MMO with some limited success, that's why I thought I'd give Pt a try. Also Swede
mentioned it earlier in the thread. It's actually not too bad, but the "headspace" erosion is particularly marked, possibly due to trace amounts of
chlorine - strange.
Ten coats would possibly make a working perchlorate anode, and that is much less than a gram of the paint, and could be done very quickly (less than
30 mins.). I have some Pt "scrap", I may get back to the thermal application of Pt at a later date.
|
|
Pages:
1
2 |