Pages:
1
2 |
testimento
Hazard to Others
 
Posts: 351
Registered: 10-6-2013
Member Is Offline
Mood: No Mood
|
|
Sulfuric acid from gypsum
I have made the following research:
2 CaSO4 + 2 SiO2 + C → 2 CaSiO3 + 2 SO2 + CO2
SO2 + O2 (V2O5@400-600C) → SO3
SO3 + H2O → H2SO4
This dictates that 2720 grams of calcium sulfate would generate 1960 grams of 100% sulfuric acid by theory. The idea is that the gypsum is roasted
with sand and coke at high temperatures. I was thinking that I would attempt this process because I have the required reagents available at rate which
would cost me approx. 2-3 bucks per kg of sulfuric acid. A few questions arise:
1) The amount of carbon is probably higher than one molar amount?
2) What materials are economically viable and withstand temps up to 1500C as the container where the reduction process occurs? Common porcelain comes
up at 1300C. I have seen firebricks that are stated up to 1700C so the material isn't supposed to be inherently expensive. Tungsten carbide crucible
and piping would be ideal.
EDIT: Porcelain melting temp is stated to be as high as 1800C, and since this process is not sensitive to contamination(which will mostly be
carbon dioxide, carbon monoxide and soot), the partial melting or reagents fusing to the crucible is not a problem.
3) Should the vanadium pentoxide catalysis involve more than one overpass, aka does anyone have data how high is the single-pass efficiency?
4) What would be the best method to powderize common sand into properly small particles? I was thinking of ball-mill, but I would need carbide balls.
5) Since the process is batch-vise, for ex. 10kg of material processed each run, I would drive the SO2 into a freezer of -35C lower temp filled with
ice ballast and pre-cool the gases and drive them through a scrubber to remove soot and particles. This will condense the SO2 in pure form and the
generated CO2 is allowed to escape.
Im planning to use the following apparatus schematics attached:
PIC 1: Reaction is heated in porcelain container and gases are lead through condenser into freezer which reflux column filled with PEG and ice
crushlings is fitted at -35C temp to condense SO2 and let CO2 and CO evaporate.
PIC 2: The liquefied SO2 is then blewn with air with aquarium air pump to slowly heat and vaporize the so2 and make gas mixture of SO2 with air which
is lead through quartz pipe filled with V2O5 catalyst under propane torch at 450-500C temp to catalyze SO3 formation. SO3 is liquefied again into
condenser container, which of the unreacted gaseous reactants are furthered into another catalysis tube, and this process phase is carried out 3-5
times. The leftover SO2, if there will be any, will be leaded into a new freezer setup, and it can be returned back into the first container.
Eventually the SO3 will be added dropwise into sulfuric acid to make oleum and water is added to make sulfuric acid.
Suitable materials: porcelain, PTFE-tube, quartz or borosilicate tube, borosilicate glass, 316 steel tube.
[Edited on 19-9-2013 by testimento]
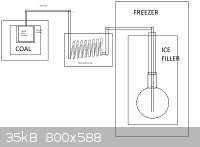
|
|
Mesa
Hazard to Others
 
Posts: 264
Registered: 2-7-2013
Member Is Offline
Mood: No Mood
|
|
By some hilarious coincidence, I've been studying exactly this process quite a bit over the past week or so.
1. While stoichiometrically only 1 carbon atom is required to produce 2 SO2, mechanics dictate that a small excess will generally be advisable.
2. You will want to be getting firebricks/furnace mortar from a specialist store(often pottery stores have it, I've seen it at one or two hardware
stores, but rarely.) You are right that Tungsten carbide would be ideal, I recently had an opportunity to have one custom made but missed the
deadline on it. That being said, furnace mortar will work quite well on its own.
3. You should be able to find this information from the patents related to the process, without knowing the design, flowrate, amount of catalyst,
catalyst support, and a myriad of other variables it's doubtful anyone can give you a solid answer here.
4. Ball mill or grinding discs, the more resistant the material is to wear and tear, the more expensive it is likely to be. You will need to figure
out what is the most economical route.
5. I don't think this is a question?
The problem arises in that the energy requirements, both in terms of preparing the precursors from whatever crude form you get them in, as well as the
immense amount of heat required for the reaction to take place, will end up costing far far more than the $2-3 per kg that you originally quoted.
Unless your batch sizes are 1 tonne+.
|
|
testimento
Hazard to Others
 
Posts: 351
Registered: 10-6-2013
Member Is Offline
Mood: No Mood
|
|
Thanks for good answer. I've played around with fire mortar, but it was rather crumble stuff and I've got to find better. Im gonna try porcelain
first, if it fails, then I'll look for more specialized stuff. 
The probable batch size would be something like 10kg. I have furnace made from firebricks and I use 1000m3 line fan and I have supply of anthracite at
flat rate of 350 bucks a ton. Gypsum will cost 50cent per kg, sand is technically free, so let's make a quick calculation..
For a batch, I'd use(abouts):
2720g of CaSO4 for 1.50
1200g SiO2 for 0.05
(240g)+300g of C, 0.12
Heating would probably consume up to 3-5kg of coal, making 1.75
Ice and freezing and other running costs 2.00 per run
Ideally this would allow for 1960g of 100% H2SO4 at cost of 5.42 per run, but probably the actual yield would be 1200-1400g max. Ok so, the budget
just doubled. Here we can see that one would need about the same for 5 times larger amount of coal and cooling, so the price per kg would rock down
from 5.42 to 3.50 or equivalent of that. The apparatus for the process from total zero would cost maybe 300-600 depending of the conditions and wether
one needs a new freezer or not.
Point being that H2SO4 can be banned, but a ban for gypsum or other sulfate salts is more difficult to come. Second, high temp device is useful for
several other processes. I am aware that hydrochloric acid and even chlorine gas can be regenerated from chloride salts by roasting.
|
|
bfesser
Resident Wikipedian
   
Posts: 2114
Registered: 29-1-2008
Member Is Offline
Mood: No Mood
|
|
This is interesting. If you can find some references for those reactions, it could be moved out of Beginnings.
|
|
Mesa
Hazard to Others
 
Posts: 264
Registered: 2-7-2013
Member Is Offline
Mood: No Mood
|
|
Quote: Originally posted by testimento  | Thanks for good answer. I've played around with fire mortar, but it was rather crumble stuff and I've got to find better. Im gonna try porcelain
first, if it fails, then I'll look for more specialized stuff. 
The probable batch size would be something like 10kg. I have furnace made from firebricks and I use 1000m3 line fan and I have supply of anthracite at
flat rate of 350 bucks a ton. Gypsum will cost 50cent per kg, sand is technically free, so let's make a quick calculation..
For a batch, I'd use(abouts):
2720g of CaSO4 for 1.50
1200g SiO2 for 0.05
(240g)+300g of C, 0.12
Heating would probably consume up to 3-5kg of coal, making 1.75
Ice and freezing and other running costs 2.00 per run
Ideally this would allow for 1960g of 100% H2SO4 at cost of 5.42 per run, but probably the actual yield would be 1200-1400g max. Ok so, the budget
just doubled. Here we can see that one would need about the same for 5 times larger amount of coal and cooling, so the price per kg would rock down
from 5.42 to 3.50 or equivalent of that. The apparatus for the process from total zero would cost maybe 300-600 depending of the conditions and wether
one needs a new freezer or not.
Point being that H2SO4 can be banned, but a ban for gypsum or other sulfate salts is more difficult to come. Second, high temp device is useful for
several other processes. I am aware that hydrochloric acid and even chlorine gas can be regenerated from chloride salts by roasting.
|
Man... I've just tried to backtrace my research via googling and the only link that comes up is to this thread .
I'm going to sort through my history page by page, but at roughly 1500 unique pages per week it might take a while before I find it.
That being said, I think you are underestimating the cost of heating. Unless you design your system to use the latent heat from the first
reaction(roasting CaSO4 + SiO2 + C) to maintain the required temperature for SO2 oxidation with V2O5, I'd say your projected fuel requirements may be
a bit on the low side. I believe the catalyst(V2O5) breaks down above 600*C, I'm not sure what temps are required for the oxidation to take place
however. It was mentioned in a few of the papers that I cannot seem to find.
Perhaps it would be possible using heat pipes(essentially vacuum sealed tubes of copper containing a compound that will undergo phase transition
within the operating temperatures, allowing efficient heat transfer, they are used extensively in CPU coolers for home PC's.)
However it will still require a fair amount of calibration.
I'll edit this post when I find my refs.
EDIT:
http://pubs.acs.org/doi/abs/10.1021/ie50531a022
It's based around the idea of recycling waste from the production of phosphoric acid, no mention is made of purification of the CaSO4 prior to thermal
decomp.
Quote: Originally posted by testimento  |
PIC 2: The liquefied SO2 is then blewn with air with aquarium air pump to slowly heat and vaporize the so2 and make gas mixture of SO2 with air which
is lead through quartz pipe filled with V2O5 catalyst under propane torch at 450-500C temp to catalyze SO3 formation. SO3 is liquefied again into
condenser container, which of the unreacted gaseous reactants are furthered into another catalysis tube, and this process phase is carried out 3-5
times. The leftover SO2, if there will be any, will be leaded into a new freezer setup, and it can be returned back into the first container.
Eventually the SO3 will be added dropwise into sulfuric acid to make oleum and water is added to make sulfuric acid.
[Edited on 19-9-2013 by testimento] |
Rather than having a series of reaction chambers, why not feed the unreacted gas back into the original feed line with a no-return valve? That way it
will have effectively 100% efficiency(Until the catalyst is poisoned)
[Edited on 19-9-2013 by Mesa]
[Edited on 19-9-2013 by Mesa]
[Edited on 19-9-2013 by Mesa]
|
|
Varmint
Hazard to Others
 
Posts: 264
Registered: 30-5-2013
Location: Near Atlanta, GA
Member Is Offline
Mood: No Mood
|
|
Cab-o-Sil should be the perfect SiO<sub>2</sub> for your needs.
DAS
|
|
violet sin
International Hazard
   
Posts: 1480
Registered: 2-9-2012
Location: Daydreaming of uraninite...
Member Is Online
Mood: Good
|
|
I would worry about the heating and cooling demands on the system staying stable enough with the SO3 production. or in your case, the method of
condensing SO3 such as to keep it liquid. I was reading up on the subject for a small set up my self, last winter mainly, and came across the alpha
explosion. violent pressure increase from solid SO3 to gas said to be able to shatter your rig.
http://yarchive.net/explosives/sulfur_trioxide.html
Melting the stable alpha form results in conversion back to the low-boiling
gamma form (the boiling point of the gamma form is below the melting
point of the alpha). This can produce a phenomenon known as the
"alpha explosion" if the gamma form is heated, causing sudden rupture of
closed or semi-closed vessels.
Can cause coughing, and severe discomfort at levels as low as 1ppm.
it seemed a distinct possibility to me as one were initially tuning injector rates, introducing the first pass back or any number of other
situations. between the high reaction temps(not super high, but considering the substance) and exothermic nature, keeping heat down but not too far
down seems dangerous.
http://en.wikipedia.org/wiki/Sulfur_trioxide
....If SO3 is condensed above 27 °C, then α-SO3 forms, which has a melting point of 62.3°C....
....Relative vapor pressures of solid SO3 are alpha < beta < gamma at identical temperatures, indicative of their relative molecular weights.
Liquid sulfur trioxide has vapor pressure consistent with the gamma form. Thus heating a crystal of α-SO3 to its melting point results in a
sudden increase in vapor pressure, which can be forceful enough to shatter a glass vessel in which it is heated. This effect is known as the "alpha
explosion".[6]....
..............ref [6]: Merck Index of Chemicals and Drugs, 9th ed. monograph 8775
wiki
SO3 Melting point 16.9 °C, Boiling point 45 °C. but if condensed >27 °C = alpha so your window is between 16.9°C and 27°C if I threw that
together correctly.
I wanted to build a small V2O5 catalized rig. shamefully slow progress considering my initial ambitions were so high. still working on the tube
furnace atm, and throwing a little time at things as I can. some info is here: http://www.sciencemadness.org/talk/viewthread.php?tid=8923
just thought I would bring it up since not every one knows about it.
-Violet Sin-
|
|
12AX7
Post Harlot
   
Posts: 4803
Registered: 8-3-2005
Location: oscillating
Member Is Offline
Mood: informative
|
|
Whatever kind of vessel you're cooking that mess in, it's going to end up as one massive glassy blob. Might as well make it single-use. Fashion an
alumina-silica (near mullite if possible) vessel, fire it, then fill with reactants. Lute the opening to the rest of your hardware.
Is carbon really necessary to make SO2, just to make SO3 again? Doesn't SO3 (i.e., at this temperature, the equilibrium between SO2 and O2) leave
anyway? Does SO2 leave faster than SO3?
Think it might be easier to try to get it into something more volatile, like ferrous sulfate. But I can't think of a simple direct route without
involving more stuff (acids, bases..).
Tim
|
|
bfesser
|
Thread Moved 20-9-2013 at 15:05 |
testimento
Hazard to Others
 
Posts: 351
Registered: 10-6-2013
Member Is Offline
Mood: No Mood
|
|
Violet Sin, It is a very good point that SO3 may react violently in such conditions, therefore a possibility of leading the vapors directly onto
concentrated sulfuric acid on order to form oleum, as industry does, should be considered instead. I can think of only single, minor synthesis where I
could need SO3.
http://www.wiley-vch.de/books/sample/3527311262_c01.pdf
According to this document, page 8, figure 3, the solubility of SO2 in sulfuric acid at 119C temperature is negligible at 80% concentration, being
about 10 grams per kg. The sulfuric acid will heat up somewhat upon contact with SO3, so a slight cooling may be needed to keep the temp little over
100C to prevent further SO2 dissolving.
http://mattson.creighton.edu/SO2/SO2_Info.html ("The solubility of SO2 in water is highly temperature dependent and is about 400 times more
soluble at 0 oC (228 g/L) than it is at 90 oC (5.8 g/L)")
SO2 seems to be quite soluble in water, being over 200 grams per liter at near zero celsius, and according to this a water tank placed in a cold
enough container could be used instead of to store the SO2 for further processing. The solubility decreases upon heating, and this should be
considered if and when the process gases are to be scrubbed to remove soot and particles. The liquor may be contaminated with small amounts of carbon
dioxide, which is not by my knowledge, harmful to the V2O5 catalysis. The gases should be dried with CaCl2 drying tube prior injecting into the
catalysis tube.
I have also done some research on refractory materials, and the porcelain itself yet seems to hold on, but as an alternative option, a common Al2O3
and MgO fireclays are rated over 1600C, which seems quite suitable for this purpose, and it is sold in economically viable bags. Because the reactants
will indeed form a monolithic glassy blob, there is two options: making a "plug" on side of the vessel where the reactants can be poured on a ceramic
basin, or simply throwing the entire vessel away and making a new one. The latter will naturally increase the cost and effort for the process into a
new scale of magnitude. Making a slightly conical mold for fireclay pot is not hard at all, taking only maybe half an hour to pour the cement in, let
it dry and extract the vessel, but yet I think it could be more efficient to think of some drain hole. This way, when the reduction is complete, the
contents could be extracted, continously adding more reagents from the top in powder form, and this way the energy content of the last batch could be
partially transferred to the new reagents. Inert atmosphere of CO2 or N2 would be required to prevent the possible combustion of the carbon content of
the mixture, and inerting the pipe the reagents are poured in could be done using the CO2 from the very heating bed of coal. If the reaction vessel is
constructed in such way, it may be even possible to make oil-sand-based mold to create a closed container.
The point of this process is to generate a fundamental reagent from literally dust. Iron sulfate and other sulfates are rather available too, but the
price per kg is yet so high that it serves mostly only a niche application and not suitable for reagent manufacturing.
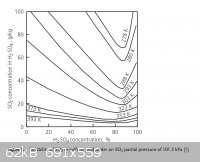
|
|
bbartlog
International Hazard
   
Posts: 1139
Registered: 27-8-2009
Location: Unmoored in time
Member Is Offline
Mood: No Mood
|
|
SiO<sub>2</sub> will react with the carbon at those temperatures; whether this is an insuperable problem or a minor side-reaction I
couldn't say. It also wouldn't surprise me if some of the CaSiO<sub>3</sub> were reduced to CaS while some of the
CaSO<sub>4</sub> remained untouched.
Rather than try to pulverize sand yourself, I would advise you to use diatomaceous earth aka kieselguhr, or else the aforementioned cab-o-sil (more
expensive, but almost certainly a purer product).
More generally, this seems like an annoyingly refractory sulfate to use as a source for SO<sub>x</sub> vapors. Copper sulfate and ferrous
sulfate were used historically, but if they seem too expensive you could at least use magnesium sulfate. It decomposes without need of any other
compounds at around 1100 deg C, or, if you prefer to do the carbon reduction, the reaction MgSO<sub>4</sub> + C --> MgO + CO
+SO<sub>2</sub> proceeds at 750 deg C. See this thread for references (h/t franklyn): http://www.sciencemadness.org/talk/viewthread.php?tid=13978
The less you bet, the more you lose when you win.
|
|
testimento
Hazard to Others
 
Posts: 351
Registered: 10-6-2013
Member Is Offline
Mood: No Mood
|
|
There is also a variation of this process as following:
http://www.lakestay.co.uk/whitehavenmininghistory.html
Wikipedia states as a reference to this:
"Up to the 1970s, commercial quantities of sulfuric acid were produced from the anhydrite of calcium sulfate. Upon being mixed with shale or marl, and
roasted, the sulfate liberates Sulfur dioxide gas, a precursor in sulfuric acid production, the reaction also produced Calcium oxide, a precursor in
cement production.[9]"
Shale consists mostly of quartz(SiO2) and calcite(CaCO3), and marl consists mostly of calcium carbonate(CaCO3). The reaction is stated to procceed by
roasting the mixture. At least one patent cited in this thread before states that temperatures featured in roasting process are between 1250 and
1350C, and the process liberates sulfur dioxide, carbon dioxide and leaves a residue of calcium oxide, and there seems to be no mention of what will
happen to the SiO2, whether it has anything to do in this process at all. I've understood that the reaction is primarily between CaSO4 and CaCO3.
The actual roasting process is still unclear to me, and I'm extremely interested to hear and know if someone has data concerning about this. The
little I've read states that the composition is blewn with very hot air, something between 1200 an 1500C, which could be done by blowing air through a
ceramic coil passing through a coal bed. If this is the case, I'd still heat the mineral mixture up to 800C.
Although this gives a reference to pre-treat the gypsum residue with coal reduction at 850C to produce calcium sulfide and after that, treat it with
hot air to generate SO2:
http://stacks.cdc.gov/objectView!getDataStreamContent.action...
In a cooperative effort between the U.S. Bureau of Mines and the Florida Institute of Phosphate
Research, with input from the phosphate industry, the conversion of phosphogypsum to sulfur has been
investigated. The first step in the conversion scheme involves reduction of phosphogypsum to calcium
sulfide. Effects of temperature, catalyst, reaction time, and type of reductant (carbon monoxide and
coal) are discussed. It was determined that phosphogypsum could be reduced to calcium sulfide at 850
0 to 1,000 0 C using either coal or carbon monoxide as the reductant. The required temperature was
lowered to 750 0 C using ferric oxide or magnetite as a catalyst for the reduction reaction. Results
indicate that as the volatiles content of the coal is increased, reaction temperature may be decreased
to obtain a given conversion, or if the reaction temperature is maintained constant, the conversion can
be increased. Best results were 95· to lOO·pct conversion using a high.volatile coal at 800" to 850" C.
Addition of a catalyst increased calcium sulfide yield when low· or medium-volatile coals were used as
reductants, but had little effect when high-volatile coals were used.
So the reaction direction could be following:
CaSO4 + 2 C → CaS + 2 CO2
3 CaSO4 + CaS → 4 CaO + 4 SO2
This is actually getting interesting, although the original reaction scheme has quite substantially changed. The document cites that this reaction requires significantly lower temperatures to procceed, temps that are very
highly on my reach at this moment with my brick furnace.
[Edited on 21-9-2013 by testimento]
|
|
12AX7
Post Harlot
   
Posts: 4803
Registered: 8-3-2005
Location: oscillating
Member Is Offline
Mood: informative
|
|
Keep in mind, industry is also quite fond of using rotary kilns -- for example, gypsum makes its way into cement manufacture, which isn't fused, but
it's close, getting sintered into clinker. Unless glass was a desirable byproduct of the process, industry wouldn't bother making a big ball of slag
-- they'd fire it into clinker. So that's at least reassuring that we don't need to make slag either, just a sintered mass.
Interesting that CaS can be made at such low temperatures!
I wonder if an excess of carbon might be used, so the mixture itself can be burned as a fluidized bed reactor?
Tim
|
|
testimento
Hazard to Others
 
Posts: 351
Registered: 10-6-2013
Member Is Offline
Mood: No Mood
|
|
Oh yes, the process would leave quite a large residue of CaO, which I first intended to use for CaOH as hydrolysis agent, but I found out that it was
not needed in ammonia process at all since it can be made from urea with pyrolysis directly, so I'll be left with bags of pretty much useless CaO.
Even a small rotary kiln of 50-100cm in length could produce nearly 100kg of
products a day.
An excess of carbon can certainly be used, since it mixes up and would generate SO2 and CO2 which could be lead into water tank or cryocondenser
through a scrubber without causing trouble. Possible side reaction could be calcium carbide formation, although it requires temps up to 2000C to
procceed (CaO + C = CaC2). It could be used to produce acetylene gas when mixed with water.
|
|
Oscilllator
National Hazard
  
Posts: 659
Registered: 8-10-2012
Location: The aqueous layer
Member Is Offline
Mood: No Mood
|
|
With regards to using coke as a fuel, I have previously managed to melt a porcelain crucible in my coke-fired forge so perhaps porcelain may not be
such a good material to use. Attached is a picture of the melted crucible.
As far as I can tell the blob on the right is actually a piece of coke fused to the crucible and is not part of the crucible itself.
[Edited on 24-9-2013 by Oscilllator]
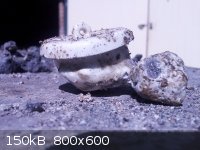
Edit: On an unrelated note, the image size limits are stupid. Why dont you have an image size limit of 3000x800 instead of 800x3000? Almost no images
have that kind of aspect ratio, they are almost always wider than they are tall. And I still cant figure out how to display images properly.
[Edited on 24-9-2013 by Oscilllator]
|
|
testimento
Hazard to Others
 
Posts: 351
Registered: 10-6-2013
Member Is Offline
Mood: No Mood
|
|
It's probably meant so one can post long texts and other posts. It's from the time the people got 800x600 resolution. I've got 1920x1200 so I need
heavy zoom for those petty pics. 
And yea, the procelain can certainly be melted even with charcoal with enough air - it's gonna melt around 1800C and coal can easily generate temps
over 2000C. I've accidentally brought one SS pot down into chunk of ore with common bbq charcoals and it melts at 1550C. Porcelain is fired at
1200-1400C and it will be probably something close to amorphous between 1400 and 1800 degrees. If one wants containers that will be like new after the
hottest possible coke oven, one would probably need to look for extremely expensive refractories. I was going to say graphite, but I think it's gonna
combust aside of the coke itself.. 
Well, gotta test it, but if the carbon reduction takes place at temps under 1000C, even common structural steel could be an option if the core temp is
brought up carefully enough and small contaminations and eventual destruction of the (inherently inexpensive) steel container are not an issue.
|
|
12AX7
Post Harlot
   
Posts: 4803
Registered: 8-3-2005
Location: oscillating
Member Is Offline
Mood: informative
|
|
Porcelain, per se, isn't a very good refractory: the difference between it, and any other common ceramic like stoneware, is its very low porosity and
very high glass content. The only reason porcelain doesn't melt to globs during firing is the strategic use of alumina, which remains solid as a
crystalline mullite network. Being glassy, it's useful for a number of things, from bowls and plates to decorations and electrical insulators. But
it's literally not useful at the temperature it's fired -- which depends on the rate, but should be around cone 10 (2100-2300F, which is in the
vicinity of 1200C). So, what happened is not at all surprising.
What is a good refractory is pure fireclay, and mixtures with other refractory materials (usually of the alumina-silica persuasion). Average fireclay
places around cone 30, which is good enough to melt steel in (1600C+). They are much less conductive, and much more brittle, than the kind of
crucible you'd buy at a foundry supply. On the upside, it's quite cheap to roll your own (as long as you don't crack them on firing!). A 50lbs
(22kg) sack of clay will run you under $10.
Tim
|
|
metalresearcher
National Hazard
  
Posts: 757
Registered: 7-9-2010
Member Is Offline
Mood: Reactive
|
|
You mean using porcelain as crucible ? Does that not crack due to temperature changes as it has a poor heat conductivity? And does it not dissolve
into slag?
What about electrical heating with a Kanthal furnace? This should reach 1100-1200C enough to calcine CaSO4.
[Edited on 2013-9-27 by metalresearcher]
|
|
12AX7
Post Harlot
   
Posts: 4803
Registered: 8-3-2005
Location: oscillating
Member Is Offline
Mood: informative
|
|
Is Kanthal resistant to SOx?
Actually, a bigass block of gypsum plus etc. ought to be self-supporting (sintering into a rather hard lump of glass in the process). It doesn't
really need a container if your kiln is well enough sealed and corrosion resistant.
Speaking of blocks... you wouldn't want blocks, or heaps of dust, or whatever. Lumps, balls, random shapes, stacked up, should have good air
circulation (better conductivity, release of gas) and less risk of cracking and spalling (shrinkage, trapped gas).
I think you'd have trouble doing it straight in a kiln, but a nice big liner with resealable, gas tight lid (luting, anyone?) could be fired in
anything.
How does one make a huge clay pot with a gas-tight lid that doesn't warp, or weld itself in place, anyway?...
Tim
|
|
metalresearcher
National Hazard
  
Posts: 757
Registered: 7-9-2010
Member Is Offline
Mood: Reactive
|
|
I don't know whether Kanthal is SO2 resistant. But when you put the reactants in a retort then the SO2 does not contact with the Kanthal. Now the
question is which material the retort is made of to withstand 1300 C. Tungsten, stainless steel, chrome steel? Porcelain won't work,it will crack.
|
|
Mesa
Hazard to Others
 
Posts: 264
Registered: 2-7-2013
Member Is Offline
Mood: No Mood
|
|
Quote: Originally posted by metalresearcher  | I don't know whether Kanthal is SO2 resistant. But when you put the reactants in a retort then the SO2 does not contact with the Kanthal. Now the
question is which material the retort is made of to withstand 1300 C. Tungsten, stainless steel, chrome steel? Porcelain won't work,it will crack.
|
Would a ceramic crucible impregnated with tungsten suffice? I have a few kg of tungsten powder but I don't have the tools required to produce a
crucible with it(MP 3422 °C.)
|
|
testimento
Hazard to Others
 
Posts: 351
Registered: 10-6-2013
Member Is Offline
Mood: No Mood
|
|
Tungsten carbide should be able to be formed into shapes using a press. Powder metallurgy is quite well researched field of study.
But how does the carbon reduction method? It does have so much lower operating temp that it'll be actually possible to carry it out with good quality
stainless steel container?
For any matter larger production scheme, one could even consider making miniature rotary kiln where the nichrome is placed in the middle and the
refractory tube made from high temp concrete just rotates around it and SO2 is lead out from the exhaust tube and the CaO is poured down.
Am I going too hardcore already? I schemed a small, maybe 1-meter long kiln
according to the pic: one could make refractory tube 30-50mm thick and insert adaptors and axle inside with nichrome wire and attach it to a motor, or
use small electric motor for low(1-3rpm), first CaSO4 + C would be passed through to get CaS and second batch would be mixed CaSO4 + CaS to get CaO
and SO2. The fittings should be decent, though, and using steel for most high temp parts would be challenging. In the lower pic, I noted that sealed
bearing is necessary only for the feeder side, where the whole device's weight is technically carried too. The idea is to use graphite gasket to seal
the tube as a sliding gasket where grapite suits well. Because the end of the kiln would be pretty much open and CaO and CaS would just pour out into
a container, the SO2 would escape too. I thought one could use air pump actually sucking air through the whole kiln to suck all the formed SO2 into
the container(freezer or water reservoir). The pipeline to the tank would be cooled, of course, to prevent the heatup of the water tank. The air pump
could be run also with the first CaSO4 reduction phase, because the CaS accumulating in the receiver bin can hydrolyze to form H2S, which could be
pumped into burner or destroyed otherwise. The kiln itself should be belt-fed with small electric engine, maybe few hundred watts is more than enough
to rpm it at such a slow rate.
Technically a tabletop model which could produce maybe 3-5kg's of stuff an hour?
[Edited on 28-9-2013 by testimento]
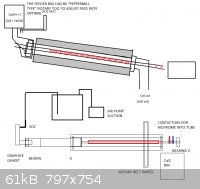
[Edited on 28-9-2013 by testimento]
|
|
watson.fawkes
International Hazard
   
Posts: 2793
Registered: 16-8-2008
Member Is Offline
Mood: No Mood
|
|
Unlikely. The Kanthal alloys, as a part of the larger class of nickel-chromium
based resistance alloys, do not perform well in reducing atmospheres. They rely on a passivating surface oxide layer to prevent the subsurface
material from oxidizing. Anything that attacks the surface oxide will lower service lifetimes. SO2 isn't as reducing as, say, CO, but I expect it's
enough.
|
|
metalresearcher
National Hazard
  
Posts: 757
Registered: 7-9-2010
Member Is Offline
Mood: Reactive
|
|
What about using KClO3 during roasting of the CaS? This will definitely oxidize the SO2 to SO3 . And KClO3 is relatively easy to make by electrolyzing
diet salt,there a. a lot of websites on this.
|
|
testimento
Hazard to Others
 
Posts: 351
Registered: 10-6-2013
Member Is Offline
Mood: No Mood
|
|
Hmm.. Would the transition be direct? Only sources I find cite that chlorine dioxide and sodium or potassium sulfate may be produced. I have 3kW
transformer and PbO2 packs for electrolysis so the price of NaClO3 is around 3-5bucks a kg for me. Heating up chlorates may though induce rather
violent reactions.
[Edited on 28-9-2013 by testimento]
|
|
metalresearcher
National Hazard
  
Posts: 757
Registered: 7-9-2010
Member Is Offline
Mood: Reactive
|
|
Use KClO3 instead of NaClO3 as the first is much easier to separate due to its low solubility in water.
|
|
Pages:
1
2 |
|