sarinox
Hazard to Self

Posts: 90
Registered: 21-4-2010
Member Is Offline
Mood: No Mood
|
|
My Tungsten Boat Snapped!
Hello All,
Today I was experimenting with my homemade Evaporation Coating device.
I tried to evaporate a small piece of Aluminum using Tungsten boat!
The Aluminum piece which I used for this experiment has Si in it (for sure)
I saw it with my own eyes that Al leaked from the back of the Tungsten boat!
What could caused this in your opinion?
I have attached images for your study.
Could it be that Tungsten reacted with Si and became weak?
Best,
Sarinox
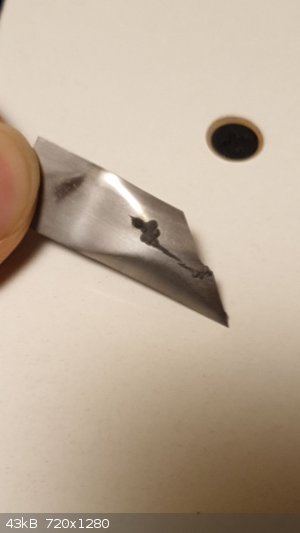
[Edited on 28-2-2024 by sarinox]
|
|
Rainwater
National Hazard
  
Posts: 987
Registered: 22-12-2021
Member Is Offline
Mood: Break'n glass & kick'n a's
|
|
Molten aluminum is very crossive. Did it eat through your boat, nm just seen the pictures. That looks like a stress fracture. Maybe bad boat
Could also be, given the angle and the way it was mounted, could have been to tight. Normally washers are used so the evaporation pan is not stressed
[Edited on 28-2-2024 by Rainwater]
"You can't do that" - challenge accepted
|
|
sarinox
Hazard to Self

Posts: 90
Registered: 21-4-2010
Member Is Offline
Mood: No Mood
|
|
But I thought Tungsten dose not react with it! I was watching the process and I literally saw it leaked from the back of the boat/pan! you can also
see it in the third photo (it shows back of the pan) it's as if Tungsten is corroded with something! I don't believe the boat was under a great
stress.
However, it snapped easily when I was trying to scrap the fused Aluminum part from it! (I think the crack started from the place of corroded area)
1-And do you know how they use Al as Evaporating specimen?
2-Can I use Nickel as a boat for Evaporating Al?
3-Can I use Ni as a boat for Evaporating of Cu?
4- Is Tungsten boat a good choice for Evaporating of Cu?
[Edited on 28-2-2024 by sarinox]
|
|
Morgan
International Hazard
   
Posts: 1729
Registered: 28-12-2010
Member Is Offline
Mood: No Mood
|
|
Don't know if this is anything but ...
"The effects of various trace elements on properties and fracture modes of heavy alloys are described. It has been found that tungsten heavy alloys
can be embrittled by traces of Al, Si and P, while various other impurities are ineffective. In all cases embrittlement is caused by deterioration of
the interfacial strength between binder and W grains. Al is not embrittling itself but preserves the oxygen, which is the embrittling element.
Fractography by SEM is recommendable for correctly assessing the significance of the AES results."
https://inis.iaea.org/search/search.aspx?orig_q=RN:20055464
An event with cobalt
https://www.lesker.com/newweb/faqs/question.cfm?id=309
"The Al12W phase formed on the Al/W interface during solid-state heat treatment starting in the temperature range from 500 ˚C to the melting point of
the matrix."
https://corescholar.libraries.wright.edu/cgi/viewcontent.cgi...
[Edited on 28-2-2024 by Morgan]
|
|
sarinox
Hazard to Self

Posts: 90
Registered: 21-4-2010
Member Is Offline
Mood: No Mood
|
|
Hi Morgan,
That could be the case! but then how can I melt Al? can I use stainless steel?
|
|
Morgan
International Hazard
   
Posts: 1729
Registered: 28-12-2010
Member Is Offline
Mood: No Mood
|
|
Quote: Originally posted by sarinox  |
Hi Morgan,
That could be the case! but then how can I melt Al? can I use stainless steel?
[/rquote
I don't know what would work not having done any vapor deposition.
"The tungsten boats, baskets and filaments are manufactured from high grade tungsten. Of all metals in pure form, tungsten has the highest melting
point (3422°C / 6192°F), the lowest vapor pressure at temperatures above 1650°C (3000°F) and has the highest tensile strength. Tungsten also has
the lowest coefficient of thermal expansion of any pure metal. This combination of properties makes tungsten the ideal material for evaporation
sources. During evaporation, it can alloy with some materials such as Al or Au. In this case, another evaporation source material should be used such
as alumina coated boats or baskets. Other materials useful for evaporation sources are molybdenum and tantalum. "
https://www.tedpella.com/vacuum_html/evaporation-boats.aspx
[Edited on 28-2-2024 by Morgan] |
|
|
Rainwater
National Hazard
  
Posts: 987
Registered: 22-12-2021
Member Is Offline
Mood: Break'n glass & kick'n a's
|
|
I have seen sputter metal placed on thick tungsten wire (2-4mm) and then melted in atmosphere with low current, once under vacuum, heated till
evaporated. I don't have any any information reguarding the longevity of the filament. And have never performed this process myself, but i have
installed and repaired this type of equipment before, both thermal and electro disposition types.
The boats used where much larger and thicker than the one shown in OP pictures, containing copper sheet used to apply transparent conductive films to
an internal glass layer of a windshield for defrosting.
[Edited on 29-2-2024 by Rainwater]
"You can't do that" - challenge accepted
|
|
averageaussie
Hazard to Self

Posts: 93
Registered: 30-4-2023
Location: Right behind you
Member Is Offline
Mood: school
|
|
do you know how hot the aluminium gets?
you just need a boat coated with a refractory with a higher melting point than whatever temperature is reached.
the refractory also cant react with the aluminium, so do some research first before choosing.
|
|
sarinox
Hazard to Self

Posts: 90
Registered: 21-4-2010
Member Is Offline
Mood: No Mood
|
|
Thank you all.
|
|
sarinox
Hazard to Self

Posts: 90
Registered: 21-4-2010
Member Is Offline
Mood: No Mood
|
|
Hello All,
Today I made another attempt to Evaporate coating of Al.
I made a home made Stainless steel boat (figure a)
[Edited on 29-2-2024 by sarinox]
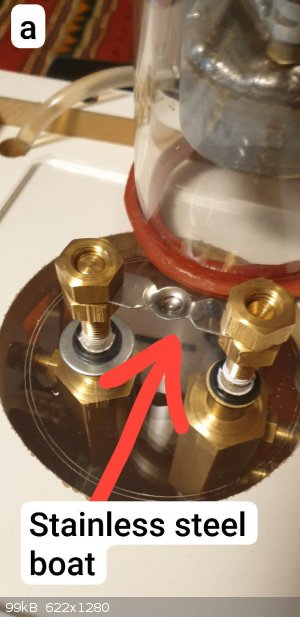
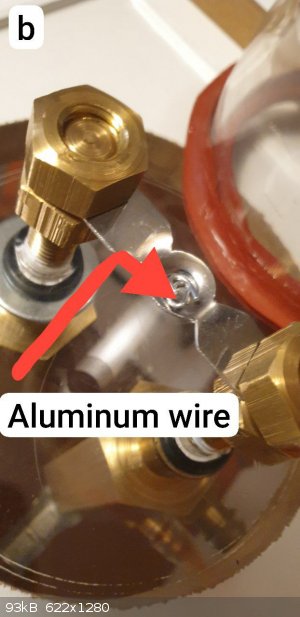
as you can see I used Al wire (grade 1100)
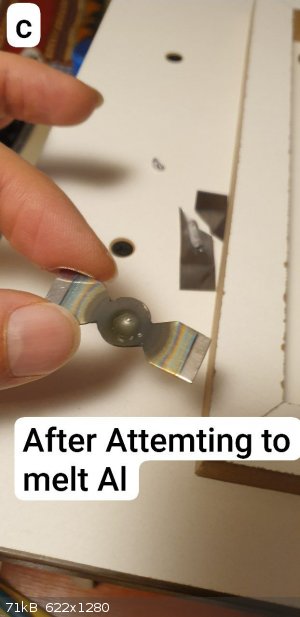
Figure c shows the boat after Evaporation attempt (As you can see it got dark in the center could it be because of Oxygen in Alumina coat of Al wire?)

Al did not fully melt and preserved its shape for a while and because I feared it might react with the boat I stopped the process. you can see how it
looks after the process is stopped.
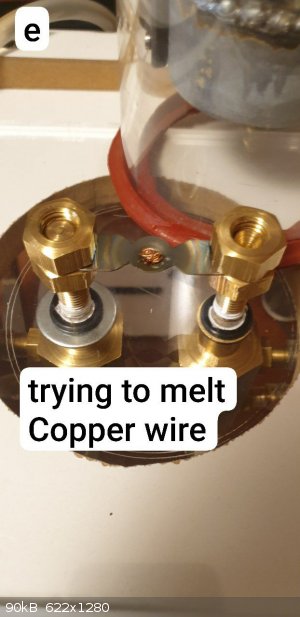
Next I tried to Evaporate Copper so I used Coper wire.
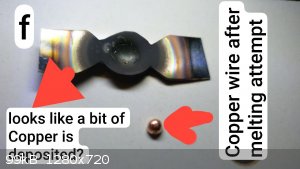
As figure f shows you can see a Copperish tint on the edges of the boat and the condition of Copper wire after Evaporation attempt! It turned into a
granule
Questions:
1- Why Al wire did not become a granule just like Copper wire?
2- Do you thing I am on the right path of Evaporation coating of Copper?
[Edited on 29-2-2024 by sarinox]
|
|
Rainwater
National Hazard
  
Posts: 987
Registered: 22-12-2021
Member Is Offline
Mood: Break'n glass & kick'n a's
|
|
1) aluminum likes to hold its shape when melted until the oxide layer is broken, all the units I have worked with have a moving part called a "nudger"
that can tap the boat. Might be worth a try.
There are some lower melting point metals you may be able to use aswell, bismuth has a low one, nice colors to Zinc is low to
2) ya, the basic process is that simple, create vacuum, heat the copper up to 2600c ish and wait.
The deeper the vacuum the better with thermal disposition.
With electro disposition you can have less of a vacuum, and even a select gas or two to create different coatings.
"You can't do that" - challenge accepted
|
|
averageaussie
Hazard to Self

Posts: 93
Registered: 30-4-2023
Location: Right behind you
Member Is Offline
Mood: school
|
|
That copper tint might be from buildup of oxide layer.
the rainbow colours in general are caused by thin film interference, a thin layer of something messing with light in funny ways, I don't do physics so
here's the wikipedia article:https://en.wikipedia.org/wiki/Thin-film_interference
if the copper colour was actually copper, you would probably expect it to be closer to the insides, but any deposited copper on the inner bit has
fully oxidised to black copper oxide. steel gets a very copper like colour when heated to the right temperature;

as for the evaporation of copper, you will probably want to upgrade your boat to a metal with a higher melting point. most steels have a melting point
no higher than 1600c, and copper has a boiling point 1000 above that.
also, depending on what you want the evaporating copper to coat, it is much easier to just make a copper sulfate bath and plate it from solution.
you can't do this with aluminium as easily though, so evaporation coating is probably your best bet there. (just melting a bunch of it and dipping the
thing you want coated might also work, or pouring molten aluminium on it, but this has obvious drawbacks)
good luck with whatever you're doing though man, and have fun. Looking forwards to seeing positive results in the future!
[Edited on 29-2-2024 by averageaussie]
|
|
Morgan
International Hazard
   
Posts: 1729
Registered: 28-12-2010
Member Is Offline
Mood: No Mood
|
|
Here's an example of Al2O3 holding an aluminum wire shape.
"During the slow heating of the aluminium wire by the current, a layer of aluminium oxide is formed (melting point: 2050°C). The insulation varnish
of the wire must of course be removed beforehand so that oxygen can reach the aluminium for oxidation. When the current is increased, the aluminium
becomes liquid inside, but cannot leak out of the aluminium oxide sheath. Aluminium has a relatively low melting point (660°C) but its boiling point
(2470°C) is very high. The parabolic shape (funicular curvedes) which the wire takes on when it is heated ensures that the oxide shell does not
break. When reducing the current (at the end of the video), the wire always breaks. At constant current the experiment works for several minutes."
https://www.youtube.com/watch?v=SbdwuuzzYqQ
|
|
sarinox
Hazard to Self

Posts: 90
Registered: 21-4-2010
Member Is Offline
Mood: No Mood
|
|
Quote: Originally posted by averageaussie  | That copper tint might be from buildup of oxide layer.
the rainbow colours in general are caused by thin film interference, a thin layer of something messing with light in funny ways, I don't do physics so
here's the wikipedia article:https://en.wikipedia.org/wiki/Thin-film_interference
[Edited on 29-2-2024 by averageaussie] |
Yes! It seems you are right! and I was wrong! because I found the same color at the back of the boat!
|
|
sarinox
Hazard to Self

Posts: 90
Registered: 21-4-2010
Member Is Offline
Mood: No Mood
|
|
Hello all,
a little bit of update:
1- I used Zinc. but I guess a layer of oxide formed around it and I think I saw it hovering on top of the boat (Please don't think it was a magical
scene, be cause it wasn't it just looked the bulk of Zinc powder was a tiny bit above the boat and was rotating around itself! Maybe I wasn't able to
see it well but it looked like that!) and then as I cranked the Voltage up the more current passed through the boat and at one point I think Zinc
exploded (it breaked free out o the protective shell) and I was able to make a Zinc mirror. (I have photos of the mirror and the oxide shell, and can
upload them for anyone who is interested.)
2- I used Soldering Wire! (I know it is made of tin and Lead!) again I was able to do Evaporation Coating but now I am concerned about Lead! I also
don't know if the soldering wire was Lead free or not! neither I have any knowledge over it's composition. But I recommend it for evaporation coating,
because it was way more easier to make it deposited on surfaces.
3- A question which has nothing to do with the experiment: Do you think Lighter flints could be melted and fused together in vacuum so a larger chunk
could be made? Could it be deposited on surfaces? Do you know any application for surfaces coated with a pyrophoric alloy ?
|
|
Sulaiman
International Hazard
   
Posts: 3779
Registered: 8-2-2015
Member Is Offline
|
|
Are you doing these tests in a vacuum?
I thought sputtering/evaporative coating is only done under vacuum.
CAUTION : Hobby Chemist, not Professional or even Amateur
|
|
sarinox
Hazard to Self

Posts: 90
Registered: 21-4-2010
Member Is Offline
Mood: No Mood
|
|
Yes, under Vacuum.
I know the lower the Vacuum is better for Evaporation Coating.
|
|
EF2000
Hazard to Others
 
Posts: 154
Registered: 10-5-2023
Location: The Steppes
Member Is Offline
Mood: Taste testing the Tonka fuel
|
|
Quote: Originally posted by sarinox  | Hello all,
a little bit of update:
1- I used Zinc. but I guess a layer of oxide formed around it and I think I saw it hovering on top of the boat (Please don't think it was a magical
scene, be cause it wasn't it just looked the bulk of Zinc powder was a tiny bit above the boat and was rotating around itself! Maybe I wasn't able to
see it well but it looked like that!) and then as I cranked the Voltage up the more current passed through the boat and at one point I think Zinc
exploded (it breaked free out o the protective shell) and I was able to make a Zinc mirror. (I have photos of the mirror and the oxide shell, and can
upload them for anyone who is interested.)
|
Zinc is quite volatile (it's even separated from other metals by distillation at 950 °C). So observed hovering is likely due to Leidenfrost effect. What was the temperature of the boat?
Wroom wroom
"The practice of pouring yourself alcohol from a rocket fuel tank is to be strongly condemned encouraged"
-R-1 User's Guide
|
|
sarinox
Hazard to Self

Posts: 90
Registered: 21-4-2010
Member Is Offline
Mood: No Mood
|
|
Yes, I can only think of Leidenfrost effect, However, I believe there was an oxide shell around the Zinc (I used Zinc powder and possibly the
particles were already oxidized, also there might be trapped air in between the zinc particles)
the thing is I think Leidenfrost effect worked even through the protective shell! Or, maybe beneath the Zinc granule there was no shell. (I cranked
temperature from 900 degree C to 1300 degree C where the protective shell cracked with an audible sound. and Zinc deposited on some parts of the
chamber as well as substrate.
[Edited on 14-3-2024 by sarinox]
|
|
bnull
National Hazard
  
Posts: 599
Registered: 15-1-2024
Location: Home
Member Is Offline
Mood: Sneezing like there's no tomorrow. Stupid cat allergy.
|
|
Please, do that.
|
|
sarinox
Hazard to Self

Posts: 90
Registered: 21-4-2010
Member Is Offline
Mood: No Mood
|
|
Hi bnull,
Here you can see the oxide shell:
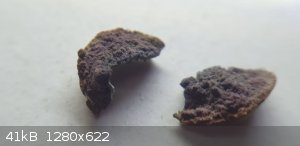
and here is the Zinc mirror. (the slide cracked because it was too close to the boat!)
Edit: and those circular shapes you see are the marks left by magnets I used to hold the slide in place.
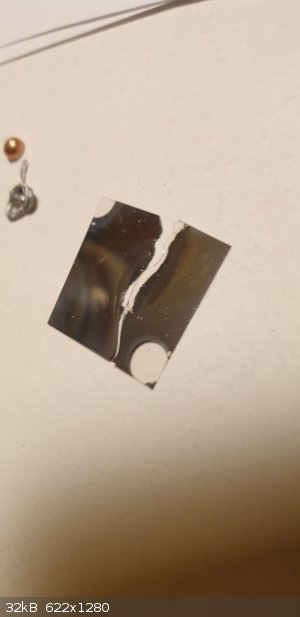
[Edited on 14-3-2024 by sarinox]
|
|
averageaussie
Hazard to Self

Posts: 93
Registered: 30-4-2023
Location: Right behind you
Member Is Offline
Mood: school
|
|
Quote: Originally posted by sarinox  |
3- A question which has nothing to do with the experiment: Do you think Lighter flints could be melted and fused together in vacuum so a larger chunk
could be made? Could it be deposited on surfaces? Do you know any application for surfaces coated with a pyrophoric alloy ?
|
Lighter flints are made of a metal alloy called ferrocerium, containing mostly iron and cerium (hence the name).
heating them and fusing them together is not the best idea in the world, working with something that reactive (pyrophoric in air when finely divided)
while molten or at least very hot is not the best idea in the world. there really isnt much information (that I could find) about the reactivity of
ferrocerium in relation to other metals and alloys, but if I had to hazard a guess I would say somewhere between magnesium and potassium (does not
blow up in water, but still is pyrophoric in air when finely divided)
A much safer and smarter idea is to go down to your local camping shop and buy a ferrocerium rod. a whole rod is going to be about as expensive as 3-4
lighters if you manage to get a good price, and you get like 50 times for metal, and no need to fuse it. plenty to play around with.
if that's not enough, you can easily find big rods of the stuff online, just look up "ferro rod" on your shop of choice.
as for the viability of depositing it... probably not. I can't speak for the properties of metal when deposited when it comes to surface area, but if
its high it will just tarnish super quick.
If you do manage to coat a thick enough layer though, if you do it on a piece of glass you could smash it and that might get you some nice sparks?
other than shits and giggles, it might make a pretty nice catalyst.
|
|
sarinox
Hazard to Self

Posts: 90
Registered: 21-4-2010
Member Is Offline
Mood: No Mood
|
|
Hi averageaussie,
The problem is that there are two different processes I have access to.
one is Evaporation coating (which you know is basically done by heating a metal to around it's boiling point under vacuum so it gets evaporated and
deposits everywhere!) this method might not be good for depositing a layer of alloy because extreme heats might cause separation of elements;
something like distillation! So, with Evaporation method one might not be able to get alloy layer deposition and instead there might be layers of
deposited elements in this case (a layer of Cerium and a layer of Iron) unless there is Azeotrope liquid ferrocerium in which the two metals will
evaporate at the same time.
(I am not expert in this area so, any help is appreciated )
The Other process is Sputter coating, I think (need to mention I am not sure!) with this method one could deposit layers of alloys because Ions of
Argon smash against the target and separate atoms randomly (well I guess even this process depends on the weight of the atoms; strength of the atomic
bonds together, etc.) However, because it is random it could be safe if I say depositing alloy layers is much more possible with sputter coating.
The problem is Ferrocerium alloy comes in shape of a rod! I can cut the rod and put in in evaporation boat and see what will happen (of course under
vacuum)
but for sputter coating I would need a disk (fairly large ;10 cm/4 inches diameter) to use as sputter coating target (which I did not see on the
market!)
[Edited on 15-3-2024 by sarinox]
|
|
averageaussie
Hazard to Self

Posts: 93
Registered: 30-4-2023
Location: Right behind you
Member Is Offline
Mood: school
|
|
Quote: Originally posted by sarinox  | Hi averageaussie,
The problem is that there are two different processes I have access to.
one is Evaporation coating (which you know is basically done by heating a metal to around it's boiling point under vacuum so it gets evaporated and
deposits everywhere!) this method might not be good for depositing a layer of alloy because extreme heats might cause separation of elements;
something like distillation! So, with Evaporation method one might not be able to get alloy layer deposition and instead there might be layers of
deposited elements in this case (a layer of Cerium and a layer of Iron) unless there is Azeotrope liquid ferrocerium in which the two metals will
evaporate at the same time.
(I am not expert in this area so, any help is appreciated )
The Other process is Sputter coating, I think (need to mention I am not sure!) with this method one could deposit layers of alloys because Ions of
Argon smash against the target and separate atoms randomly (well I guess even this process depends on the weight of the atoms; strength of the atomic
bonds together, etc.) However, because it is random it could be safe if I say depositing alloy layers is much more possible with sputter coating.
The problem is Ferrocerium alloy comes in shape of a rod! I can cut the rod and put in in evaporation boat and see what will happen (of course under
vacuum)
but for sputter coating I would need a disk (fairly large ;10 cm/4 inches diameter) to use as sputter coating target (which I did not see on the
market!)
[Edited on 15-3-2024 by sarinox] |
one big issue with working with ferrocerium is that there isn't much information you can find about it online other than "burns in air when finely
divided" and "made of cerium and iron".
melting point, boiling point, burning temperature, and just about anything other than "mischmetal" is either hard to find, inconsistent, or just not
available.
So I can't say much about its properties either, and if I had to guess the cerium would distill out of the metal when heated in bulk, under vacuum.
|
|