Pages:
1
2
3 |
Hexabromobenzene
Hazard to Others
 
Posts: 151
Registered: 27-4-2021
Member Is Offline
|
|
Homemade carbon electrodes
The inert anode is a very important thing for electrochemistry. Both organic and not organic. Typically, such products are inaccessible and expensive.
Here is a technology on which you can produce carbon anodes of any shape and size having a small stove or heating boiler.
The idea was taken from this video, but improved https://www.youtube.com/watch?v=N9B2OAiu95Y
This technology is similar to the industrial technology of the production of graphite electrodes, but from available raw materials and without
graphitization, since this requires high temperatures
The main idea of this technology of baking of the conducting carbon with a binder at 1000 degrees and then impregnation with any varnish or glue.
As a conductive carbon, I used charcoal from the furnace. Charcoal was sprinkled from the stove into an iron jar and closed for colling and protection
from air. Next, you will need a multimeter. You must choose the most conductive pieces of coal. I use pieces with a resistance of less than 10om.
Small pieces are usually baked better and have less resistance up to 2 Ohms.
After you have chosen coal, which is well conducting the current, you must grind it. Be careful. Charcoal is very dusty. Next, I cook concentrated
sugar syrup and mix it with carbon powder. So much sugar syrup is necessary that the mixture with coal becomes like a warm bitumen. Next, this mixture
is pressed into the cardboard tube of the desired diameter, closed on one side with a paper. If you do not have a cardboard tube, you can make a paper
pipe from a newspaper. To press the mixture conveniently steel reinforcement. After pressing the mixture, the tube is closed with paper. Then the
finished baking dish is wrapped with aluminum foil for insulation from air when baking.
Next, you need to place your baking dish in a steel container. It is important! Without a steel container, the electrodes burns significal. I used
metal from a tin can. The baking dish was wrapped in a thin iron sheet
A steel container with a baking dish is placed in the furnace and heats up to 800-1000 degrees for about an hour. An ordinary heating furnace is
easily capable of giving a temperature of 1000 degrees if you place a lot of small firewood in it and surround them with a steel container.
After baking, the thin metal usually crumbles into the scale powder. The steel container is disposable. After extraction, we have a ready -made porous
carbon electrode. As a rule, it is of poor quality,paper baking with paper and it must be separated.
Next, the electrode must be impregnated with any polymer resin. I used alkyd varnish for wood, but you can use a lot of different options. It is
recommended to process electrodes with sandpaper before impregnation.
Also in industry repeat the baking cycles of the electrode several times. I saturated the electrodes with sugar and baked up to 3 times, but did not
see a significant difference. Repeated baking makes sense if you have too many defects on your electrode.
After the varnish dries, we have a ready -made electrode. It has less strength than graphite electrodes. I do not recommend drilling it for the
current supply. To create electrical contact, the electrode must be treated with sandpaper and covered with copper with electrolysis or wrapped with
copper foil on one side.
In this way, I made electrodes with a diameter of up to 50 mm and up to 35 cm long. The maximum size depends only on your furnace. It makes no sense
to make small electrodes. They are cheap and affordable. And large electrodes are expensive and rare.
As a replacement of charcoal, you can use activated charcoal, graphite powder from different sources, a powder of metallurgical coke is possible.
A coal tar is used as a binder in industry. But he is inaccessible. You can try to use wood tar. But sugar also does not work bad
As a resin, you can use a solution of any polymer convenient for you such as PVC, polystyrene. You can also use epoxy resin. You can even soak the
electrode in molten polypropylene, but the process goes for a very long and technically not just to keep the molten polymer for many hours. You can
also use home-made phenol -formaldehyde resin if you have components.
I checked made electrodes by a multimeter. They have a resistance less than 10 Ohms (3-8) with a point touch. When coating with copper and in liquid
electrolyte, the resistance will be significantly lower
[Edited on 14-5-2023 by Hexabromobenzene]
|
|
mysteriusbhoice
Hazard to Others
 
Posts: 477
Registered: 27-1-2016
Member Is Offline
Mood: Became chemistry catboy Vtuber Nyaa
|
|
graphite foil and carbon fiber sleaves actually lasts longer than dense graphite plates and is a good alternative.
This video below is an example of graphite foil being used for long periods.
https://www.youtube.com/watch?v=f5sY3rEAdes
Below is carbon fiber sleave electrode
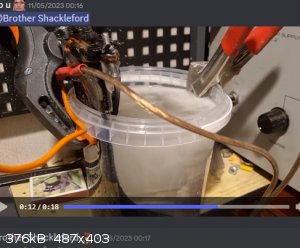
[Edited on 14-5-2023 by mysteriusbhoice]
[Edited on 14-5-2023 by mysteriusbhoice]
|
|
Hexabromobenzene
Hazard to Others
 
Posts: 151
Registered: 27-4-2021
Member Is Offline
|
|
Yes, but this need to buy it. My method allows you to make an electrode of any size and shape yourself. You only need charcoal, sugar, a simple
furnace and a little garbage that can be found in a trash can
|
|
Jome
Hazard to Others
 
Posts: 154
Registered: 10-6-2004
Location: Soutwest sweden
Member Is Offline
Mood: desiccated
|
|
This sounds rather cool, I always expected the process to turn carbon decently conductive would require 2000+ K temperature.
|
|
mysteriusbhoice
Hazard to Others
 
Posts: 477
Registered: 27-1-2016
Member Is Offline
Mood: Became chemistry catboy Vtuber Nyaa
|
|
Quote: Originally posted by Jome  | This sounds rather cool, I always expected the process to turn carbon decently conductive would require 2000+ K temperature. |
Yea and its possible to do this DIY using a 12V car battery or rewound MOT.
Basically after you put it into the furnace you will then use 2 electrodes to pass 800 amps through the carbon electrode and this allows you to
convert it into both graphite and conductive vitreous carbon. Note that conductive vitreous carbon if doped with boron can make perchlorate so an
addition of trimethyl borate can help improve the quality of these electrodes.
|
|
NickBlackDIN
Harmless
Posts: 10
Registered: 10-5-2023
Member Is Offline
|
|
Edit: I'm an idiot lol
[Edited on 16-5-2023 by NickBlackDIN]
|
|
Hexabromobenzene
Hazard to Others
 
Posts: 151
Registered: 27-4-2021
Member Is Offline
|
|
Quote: Originally posted by mysteriusbhoice  | Quote: Originally posted by Jome  | This sounds rather cool, I always expected the process to turn carbon decently conductive would require 2000+ K temperature. |
Yea and its possible to do this DIY using a 12V car battery or rewound MOT.
Basically after you put it into the furnace you will then use 2 electrodes to pass 800 amps through the carbon electrode and this allows you to
convert it into both graphite and conductive vitreous carbon. Note that conductive vitreous carbon if doped with boron can make perchlorate so an
addition of trimethyl borate can help improve the quality of these electrodes. |
Charcoal, heated to 1000-1100 degrees already conductive. Charcoal heated to 1200 have compatible conductivity with graphite. But you need close
porous and protect him from destruction during elecrolysis. I think impregnate with epoxy or molten polypropylene best.
Soon i try alternative technology. I will carbonizate patcricleboard or mdf then impregnate with sugar and heating again to close porous and threat
with varnish or something polymer
[Edited on 16-5-2023 by Hexabromobenzene]
|
|
mysteriusbhoice
Hazard to Others
 
Posts: 477
Registered: 27-1-2016
Member Is Offline
Mood: Became chemistry catboy Vtuber Nyaa
|
|
The graphitization temperature is between 1900 and 2000C and hence the need for high current because allows the carbon to reach those temperatures
briefly which graphitizes it.
|
|
metalresearcher
National Hazard
  
Posts: 790
Registered: 7-9-2010
Member Is Offline
Mood: Reactive
|
|
Interesting. Never tried, but I might try.
You probably mean an Acheson furnace which graphitizes the baked electrodes described here to real graphite at extremely hot temperatures of 3000 C, using the
resistance of the electrodes.
Amateurs can do it if you indeed have a current source of 800 amps and a low voltage. Probably by embedding the electrode in sawdust and / or sugar
and then sand around it. But the duration of graphitizing in large scale commercial Acheson furnaces can take days. In China they make large
electrodes for electric arc furnaces this way.
|
|
mysteriusbhoice
Hazard to Others
 
Posts: 477
Registered: 27-1-2016
Member Is Offline
Mood: Became chemistry catboy Vtuber Nyaa
|
|
you infact dont want full graphitization because some amorphous carbon can have catalytic properties when doped with boron which also makes it
conductive and even catalytic giving a very high O2 evolution potential but idk if this mixed with graphite will be good for use in such cells or if
it will last long. It only takes 800C to boron dope amorphous carbon into a conductive version by trimethyl borate or boric acid.
|
|
Hexabromobenzene
Hazard to Others
 
Posts: 151
Registered: 27-4-2021
Member Is Offline
|
|
As i know charcoal is hard carbon. Its not grapitizate. But strong heat may increase conductivity. Not so far. Mainly conductivity increase occurs up
to 1000 degrees.
If you need graphitizing carbon you can try PVC coke PET plastic coke or polycarbonate coke. Also phenol formaldehyde resin produces interesting
material like glass carbon
https://en.wikipedia.org/wiki/Hard_carbon
https://en.wikipedia.org/wiki/Graphitizing_and_non-graphitiz...
[Edited on 18-5-2023 by Hexabromobenzene]
[Edited on 18-5-2023 by Hexabromobenzene]
|
|
mysteriusbhoice
Hazard to Others
 
Posts: 477
Registered: 27-1-2016
Member Is Offline
Mood: Became chemistry catboy Vtuber Nyaa
|
|
yea and boron doping may increase catalytic activity up to perchlorate forming potential like BDD electrodes.
|
|
Hexabromobenzene
Hazard to Others
 
Posts: 151
Registered: 27-4-2021
Member Is Offline
|
|
For the preparation of electrodes, a denser coal was tested. It was made from laminated MDF fiberboard from the floor.
The board was broken and placed in a closed tin can, which was placed in a wood-fired furnace. After pyrolysis, coal takes up less volume than the
original board, unlike pure wood. Next, the coal was ground in a coffee grinder and, according to proven technology, baked with sugar at 900. The
electrode turned out to be noticeably denser than charcoal electrodes. However, it is still porous due to sugar, which, boils during pyrolysis. One of
the electrodes had a high resistance on one side (up to 70 ohms), when an ideally baked electrode in a furnace has a resistance of about 3 ohms,
regardless of the place where the multimeter probes are applied. He was badly calcined on one side.
Initially, poorly conducting coal was taken from fiberboard, which was pyrolysed at no more than 700 degrees, in contrast to the partial combustion of
charcoal at 1000-1100. This created some problems.
The length of the electrode was 27 cm diameter 30mm. Large electrode diameter 40mm
To eliminate this defects, the electrode will be impregnated with sugar and calcined again. Repeated baking with sugar impregnation makes the
electrode denser and reduces the number of defects.
Fiberboard coal was denser than charcoal. I think the ideal coal for baking is phenol-formaldehyde resin char(for example bakelite products) or
calcined anthracite
Charcoal electrodes are very porous. They can probably be used for catalytic electrosynthesis, but they are not very good for high current density
electrolysis. Also, all carbon electrodes need to be impregnated with a polymer.
[Edited on 22-5-2023 by Hexabromobenzene]
[Edited on 22-5-2023 by Hexabromobenzene]
|
|
metalresearcher
National Hazard
  
Posts: 790
Registered: 7-9-2010
Member Is Offline
Mood: Reactive
|
|
@C6Br6: Good idea.
I want to try it out baking with sugar, I don't need them for KClO3 / KClO4 electrolysis as I already have both MMO and platinized Ti anodes which
work well.
But I use carbon electrodes for arc melting or making CaC2 and other extremely high temperature applications using a DC welder. Yes I can purchase
these carbon rods online, but would like to make them myself on own size and shape.
So I can use crushed particle board waste and bake it with sugar to 1100 C ?
|
|
Ubya
International Hazard
   
Posts: 1247
Registered: 23-11-2017
Location: Rome-Italy
Member Is Offline
Mood: I'm a maddo scientisto!!!
|
|
If coal tar is unavailable, what about bitumen/asphalt? Vacuum impregnation of hot thin bitumen could solve for the added porosity caused by the
sugar?
---------------------------------------------------------------------
feel free to correct my grammar, or any mistakes i make
---------------------------------------------------------------------
|
|
Hexabromobenzene
Hazard to Others
 
Posts: 151
Registered: 27-4-2021
Member Is Offline
|
|
The electrodes were saturated with sugar syrup and again in the furnace. They became better. Now the electrodes are close to the reference resistance
from 3 Ohms to 10 Ohms. Satisfactorily
Porous electrode made of charcoal can be used for electrocatalytic hydration covering it with nickel galvanically
metalresearcher, Ubya
Grinding the fiberboard is difficult. I first made char from mdf and then char grinded and baked with sugar
This is probably the denser available coal. Only anthracite is even denser. It must also be pre -calcined for electrical conductivity. But I do not
have anthracite at the moment. Previously, anthracite uses as fuel for heating and it was lying a lot on the ground near the roads and on the
landfills of old cities.
Electrodes made of charcoal and sugar burn in the furnace when air access to electrode if you poorly isolated a steel container. They burn much more
slowly than charcoal, but faster than graphite. You also probably will have to cover them with galvanically copper for electrical conductivity
Bitumen will also work, but I don’t have bitumen at the moment with it is more difficult to work with it than sugar. It must be heated or diluted
with a solvent. I poured the roof with bitumen for a long time in my house
Probably, instead of bitumen, you can use heavy fractions of oil from pyrolysis of wood and various plastics
The baking form is also important. I usually use a cardboard pipe into which a baking mixture is pressed. The cardboard form is wrapped with a sheet
of iron from a canning can and placed in furnace. But you can press a mixture without paper or cardboard in a steel container. I recommend using
aerosol cylinders. Metal from cans and aerosol cylinders after baking oxidizes and crumble. But he performs his protective function at least 1 time.
And you can find a lot of aerosol cylinders
|
|
Hexabromobenzene
Hazard to Others
 
Posts: 151
Registered: 27-4-2021
Member Is Offline
|
|
Here is a graph of the conductivity of carbon from fiberboard as a function of temperature. For charcoal and other coals, it is similar
See more here:
https://www.academia.edu/48186506/Evaluation_of_carbonized_m...
|
|
Hexabromobenzene
Hazard to Others
 
Posts: 151
Registered: 27-4-2021
Member Is Offline
|
|
I also conducted experiments on the manufacture of carbon electrodes. This time I tried catalytic graphics. Hard carbon is catalytically graphitized
in the presence of iron compounds.
I mixed coal from MDF with a solution of iron chloride (from rust from the old pipe) 1 to 10 by weight and dried it . Further, the carbon electrode
was made using ordinary technology with sugar
The results are as follows. Not noticeable changes in mechanical strength were not noticed. Electrical conductivity increased slightly but weakly.
However, the appearance has become different. The electrode has become black, matte and a little brilliant. He stopped dusting and getting his hands
dirty with black mud and also significantly became more resistant to burning probably due to the loss of the microporous structure. The electrode also
has noticeably more defects due to the decomposition of iron chloride. One electrode even broke in half. It is probably better to add another
catalyst, which, when decomposed, does not emit gases or graphite the coal mass before sintering with sugar. You can also remove iron oxide particles
with hydrochloric acid
I do not know how this electrode will show itself in electrolysis, but in my opinion, catalytic graphitization makes sense for electrodes for electric
arc furnaces due to more better burning resistance.
In the manufacture of carbon electrode there are several important rules:
You must use the MINIMUM amount of sugar syrup, sugar syrup should be as MAXIMUM CONCENTRATION as possible. You must CORRECTLY PRESS the coal mass
with sugar. It is necessary to press the piston with the diameter of the paper sleeve with significant force. You can’t press everything at once.
Add the coal mass in small portions. The carbon electrode after calcining has poor mechanical strength. However, after IMPREGNATION with polymer, it
becomes a STRONG COMPOSITE MATERIAL
In the following posts I will publish testing these electrodes in an electrolyzer
You can read an article about catalytic graphitization here
https://pubs.rsc.org/en/content/articlelanding/2022/ta/d1ta0...
|
|
mysteriusbhoice
Hazard to Others
 
Posts: 477
Registered: 27-1-2016
Member Is Offline
Mood: Became chemistry catboy Vtuber Nyaa
|
|
add maybe SnO2 but it may reduce to tin in that environment sadly. Pb salts are another option as it forms PbO2 when anodized. Antimony and bismuth
may help also.
|
|
Sulaiman
International Hazard
   
Posts: 3779
Registered: 8-2-2015
Member Is Offline
|
|
I love experimentation, it's why I'm on SM,
presently there is massive investment in carbon materials,
relative to this discussion are electrodes for
arc furnaces, EDM, batteries and electrolysis.
So, great as an experiment,
but probably no so useful or cheap as using or modifying commercial electrodes.
For no particular reason other than curiosity stimulated by this thread
I bought a couple of sheets (100x100x2 mm) of graphite
manufactured for use as Edm electrodes.
I believe isotropic, sawn from a large block. they are:
. Cheap (usd 4.27 for two w/p&p)
. Hard (the sheets 'ring' at c600 Hz when flicked with a fingernail)
. Highly conductive (I had to check my meter because I didn't believe the measurement)
. High current capacity (designed for EDM 'roughing' at 5 to 25 A/cm2)
For (my) amateur purposes
where high temperatures and pressures are inconvenient
it may be best to design around existing shapes,
or carve a block to the required shapes.
I now want to look at boron (or similar) surface treatment.
CAUTION : Hobby Chemist, not Professional or even Amateur
|
|
Hexabromobenzene
Hazard to Others
 
Posts: 151
Registered: 27-4-2021
Member Is Offline
|
|
Lead salts under these conditions form lead. During electrolysis, it forms lead dioxide. But I do not think that such an electrode will be reliable.
Iron salts are needed for catalytic graphitization. However, I do not see the obvious advantages of these graphitized electrodes over hard carbon
electrodes for electrolysis. For an electric arc furnace, they have the advantage of burning much more slowly.
To make carbon electrodes, I use a wood-burning furnace for heating. Furnace gives temperatures up to 1000 degrees. It takes me 5 kg of firewood to
prepare the electrodes
[Edited on 17-6-2023 by Hexabromobenzene]
|
|
Hexabromobenzene
Hazard to Others
 
Posts: 151
Registered: 27-4-2021
Member Is Offline
|
|
Experiments with homemade carbon electrodes have been completed. Here is the information that was obtained during the experiments
The manufacture of a carbon electrode consists of 3 stages
1. Obtaining conductive carbon
2. Sintering of carbon powder with a binder containing carbon
3. Impregnation of the electrode with various substances
To obtain conductive carbon, we need carbon raw materials. As experiments have shown, the best raw materials are hardboard or laminate flooring. The
ideal raw material is phenol-formaldehyde resin. Carbon from it is the densest. However, it is difficult to find sufficient quantities of phenol
formaldehyde resin and it is usually contaminated with fillers. Charcoal has high porosity and is not very dense and is also difficult to heat in a
furnace to a conductive state due to the thickness of the pieces.
First we must carboniazte our feedstock. Usually this is hardboard. It must be calcined in a closed container in an oven until complete carbonization
and removal of volatile substances.
Once we have carbon, there are 2 ways to make it conductive. They are all associated with high fever
The first method is partial combustion in an air stream in any furnace. During the combustion process, carbon heats up to 1200-1300 degrees, which is
enough to make it conductive after holding it for about a minute. The carbon must then be quickly extinguished. I don't recommend using water. It is
extremely difficult to remove from carbon without repeated calcination. Carbon can be easily extinguished by placing it in a steel container and
covering it with a lid. Carbon from hardboard is especially convenient for this method since it has the shape of thin plates and is heated completely,
unlike charcoal.
This method allows you to obtain pure conductive carbon without impurities and without the use of additional reagents. However, the partial combustion
process can burn up to half its weight in carbon.
The second method is catalytic graphitization. Heating to high temperatures promotes the growth of graphite nanostructures in carbon and increases its
conductivity. It grows quickly up to 1000 degrees and then increases about 3 times from 1000 to 1400 degrees. During catalytic graphitization, carbon
is impregnated with a soluble iron compound of 1 to 10 to 1 to 30 by weight. Iron also promotes the growth of graphite nanostructures, but at 900
degrees its conductivity is the same as at 1400 degrees for ordinary carbon. With a further increase in temperature, the conductivity does not
increase. Typically, carbon is ground and mixed with an iron salt such as chloride and the powder is calcined in a closed container in an oven at 900
degrees.
This method has a significant drawback. Carbon is contaminated with iron. For some syntheses this is unacceptable. Acid leaching does not completely
remove iron and requires careful drying before sintering.
Carbon pieces can be tested for conductivity with a multimeter. Ideal carbon shows a resistance of about 3 ohms. To make electrodes, it is permissible
to use carbon with a resistance of up to 10-20 ohms.
Ideally calcined carbon up to 1400 degrees has 3 times greater resistance than pure graphite.
2 Sintering
After we have received the conductive carbon powder for making an electrode, it must be mixed with any chemical compound capable of significant
carbonization and calcined in a furnace, protected from exposure to air.
I used sugar as the most accessible substance. But it should probably be replaced with something
Sugar has disadvantages. It requires water to dissolve. Water during carbon sintering can lead to cracks and even breakage of the electrode.
Therefore, sugar syrup should be as concentrated as possible. 1 to 4 water sugar by weight approximately. Sugar dissolves completely when heated, but
you must have time to press the carbon mass with sugar syrup before cooling. The amount of sugar syrup should be MINIMUM to prevent cracking. The
ratio of dry sugar to carbon powder is usually approximately 1 to 1 for optimal wetting. You also have to press the carbon powder into the mold with
SIGNIFICANT FORCE. I pressed my hands with a wooden piston with a force of about 30-50 kg with impacts on an electrode with a diameter of about 2.5
cm, which corresponds to a range of about 1 megapascal. According to studies, electrical conductivity increases during pressing to 2 megapascals.
Pressing also increases the mechanical strength of the finished electrode. I used cardboard tubes as a mold for pressing. After sintering, they become
carbonized and are easily separated from the electrode. The cardboard tube must be covered on one side with paper.
After the carbon powder is pressed into the mold, it must be calcined. The mold with the mixture must be placed in a steel container to protect it
from combustion. I recommend thin metal from aerosol cans and cans. It is enough for 1-2 firings. The container with the mold must be placed in an
already preheated oven to quickly carbonate the sugar.
After cleaning from paper residues, a properly prepared electrode should not have cracks, be straight and have a smooth surface. This result is not
easy to achieve.
3 Electrode impregnation and current supply
If you want to use an electrode for the electrolysis of aqueous solutions, it must be impregnated with some kind of organic substance. The simplest
option is paraffin or linseed oil. But it is better to impregnate with resin. Epoxy resin would probably be the best option. I used alkyd resin from
old paint whose filler had precipitated. The electrode must be soaked until it stops absorbing liquid. You'll be surprised how much they can absorb.
After the resin hardens, the electrode turns into a durable composite material similar to industrial carbon electrodes.
In order to ensure contact with the electrode, it may be coated with copper, wrapped with copper wire and the contact coated again with copper. A more
affordable option is to wrap it with copper foil, but such contact will have greater resistance. The current lead can also be placed inside the
electrode during sintering.
|
|
Hexabromobenzene
Hazard to Others
 
Posts: 151
Registered: 27-4-2021
Member Is Offline
|
|
I also conducted experiments with the production of carbon electrodes.
The main problem from the electrodes of sugar and charcoal is that they are similar to foam in structure. Repeated sugar impregnation and heating does
not solve this problem. This operation increases the strength of the electrode, reduces porosity, corrects defects
To obtain monolithic carbon, you need thermosetting polymer. It's IMPORTANT.
I saturated the electrodes with an old alkyd paint, which had a filler out to the bottom. Once I decided to burn him for an experiment in the
furnace. Oh miracle! I received a monolithic hard piece of carbon, which does not scratch with a fingernail. You can use epoxy resin. I used the old
alkyd paint since it was free. To save resin, you can make an electrode of char from laminate or phenol -formaldehyde resin. It is less porous and you
need less resin to impregnate your product. You can also impregnate your electrode several times with sugar and burn it. This will increase the
strength of the carbon frame and reduce porosity
Thus, you can make the glass -hot electrode itself.
You can also make graphite from the glass carbon electrode. I wrote about catalytic graphitization. However, during the experiments it was found that
an iron catalyst can only be used once. Therefore, you need to soak the finished glass -carbon electrode with iron salt and burn it
Catalytic graphite of more resistant to combustion and probably to electrolysis, but graphite is difficult to eliminate iron residues after heating
Thus, having a simple wood furnace, you can make glass carbon and graphite electrodes of any shape and large sizes.
|
|
RU_KLO
Hazard to Others
 
Posts: 245
Registered: 12-10-2022
Location: Argentina
Member Is Offline
|
|
Can Li-ion battery graphite be used, instead of "conductive carbon"? (I have a lot -like a kg - from disasemblng Li ion batteries
Of course it will be very contaminated.
I can boil it 1hr with water, then HCl boiling / washes to try to remove as most contamination as possible.
how do you meassure "first" resistance (before making the electrode).
I have a powder.
You add it to a cardboard or plastic tube, compress it and then meassure resistance?
Go SAFE, because stupidity and bad Luck exist.
|
|
Hexabromobenzene
Hazard to Others
 
Posts: 151
Registered: 27-4-2021
Member Is Offline
|
|
If you have a lot of graphite, you can use it. The task of the first baking to form an electrical conductive carbon matrix. It can be used as an
electrode after impregnation. But for better stability, the electrode must be impregnated with thermosetting resin(epoxy, polyurethane and other) and
baked again
I usually measure the resistance of pieces of wood coal from the furnace before grinding into dust. You can also measure the resistance of the
electrode after baking
A cardboard pipe is a form for the electrode. You press carbon powder with sugar into it. I did it with the help of a large wooden piston. If you use
the jack, you can achieve better results
P.S I did not use a plastic tube and I do not know if it is suitable for baking. If you do not have a cardboard tube, you can turn any newspaper or
better the magazine into the tube and use tape to fix the form. Use pressed paper like a plug
After baking with sugar, conductivity may fall due to sugar coal isolates the conductive carbon. You probably need to bake the final electrode up to
1000 degrees
[Edited on 24-1-2024 by Hexabromobenzene]
|
|
Pages:
1
2
3 |