Pages:
1
2 |
Magpie
lab constructor
   
Posts: 5939
Registered: 1-11-2003
Location: USA
Member Is Offline
Mood: Chemistry: the subtle science.
|
|
Homemade Autoclave
Homemade Autoclave
by Magpie 10/12/10
Introduction
The reason I constructed an autoclave is twofold. Firstly I wanted it to make N,N-dimethylaniline which requires a pressure of 30atm. Secondly, I
wanted to see if I could with only the help of a skilled welder.
Design Basis
The SM library book Autoclaves and High Pressure Work, by Goodwin outlined the various options for autoclave construction. I opted for the
simplest design to minimize the resources needed. It would be expensive enough without machined surfaces, an agitator, or special alloys. Therefore,
I chose to fabricate a flanged head vessel made of carbon steel. I chose the smallest diameter pipe, 2.5”, for a body that would still accommodate
a thermowell and a pressure/fill tap penetration. The capacity is 350mL.
The pressure holding capability was first estimated using the well known Barlow’s Formula and an assumed operating temperature of 400F (204C). At
this temperature Perry’s Chemical Engineers’ Handbook, 4th ed. pp. 24-41 gives a yield stress for pipe steel (A106 Gr B carbon steel) as
17,250 psi. This gave a burst pressure of 2866 psi. Then I performed a 2nd calculation using a more conservative formula found in a paper by Fred
Gasche, founder and president of Autoclave Engineers, ie, “Design of Reactors and Closures,” Industrial and Engineering Chemistry, vol
48, No 5, p.838, May 1956. This calculation yielded a burst pressure of 2730 psi. Lastly, the internet delivered the ANSI/ASME B31.1 table A106
Grade B Carbon Steel Pipes – Pressure and Temperature Ratings. The maximum allowable pressure from this table for 2.5” pipe was interpolated
between that for 2” and 3” pipe at 400F to be 2485 psi.
Therefore I felt there was adequate factor of safety for a test of methanol at 215C which would give a vapor pressure of ~ 760 psia.
Construction
I procured all the parts through local and internet suppliers. I spent some time searching for a qualified welder. At first I found one whose bid
was way too low. Another welder really wanted the work but his shop was at least an hour away. The third welder seemed perfect: a semi-retired
business owner who at one time had a staff of 20 welders and machinists. He had done almost any kind of metal work that I could imagine. I didn’t
even ask him for a bid. I just gave him the job.
He also constructed a carbon steel tripod stand to support the autoclave when in use.
Cold Hydrostatic Testing
Way before putting the autoclave into service I conducted a series of tests. Initially the testing was hydrostatic using a discarded brake master
cylinder and brake fluid. This testing indicated numerous leaks at the threaded fittings. After trying a couple different sealants I asked my welder
to seal the connections with silver solder. I left only two threaded connections: a ¼” female port for the pressure gauge, and a ¼” female
opening for the fill port. Once the leaks had been stopped the pressure was brought up 1500psi with brake fluid where it held steady.
Heaters
A silicone oil bath was used to heat the lower portion of the autoclave below the flanges. Temperature was controlled via thermocouple and PID
controller. The flange head was heated with a 1000w calrod element formed into the shape of a sine wave and held in place with a radiator hose clamp.
Power to this heater was controlled manually with a variac. A thermometer inserted in the thermowell was used to indicate autoclave internal
temperature. The flange head was heavily insulated using kaowool overlayed with cheap firberglass insulation.
Hot Testing
This was done first with silicone oil in the autoclave and water in the bath. Then a test was done with silicone oil in the bath and water in the
autoclave. For this second test the water was brought up to 215C. The final test was done with methanol, also bringing the temperature in the
thermowell up to 215C.
Gasket & Thread Sealant
For all testing the gasket was a Garlock Bluegard 3000, 1/8”, ring gasket. This is composed of nitrile filled with Aramid fiber. In any use the
gasket material must be compatible with the chemical compostion at the conditions of the process. Each gasket has a bolt torque requirement. In this
testing phase 100 or 120 ft-lbs was used. Bolts must be torqued in 4 or 5 steps in a certain sequence.
Thread sealant for the fill port and the pressure gauge is Ace TFE.
Drawings & Pictures
The attached drawings were used to communicate my design to the welder. All parts are shown on sheet 2, “Bill of Materials,” except the ¼”
pipe and fittings. These were obtained locally at a hydraulic fittings supplier.
Pictures are also attached. There are quite a few, so will post separately.
Conclusions
The autoclave did perform as intended and N,N-dimethylaniline was prepared from aniline and methanol in a 75% yield. Boiling point of the product was
a steady 192C per procedure.
As noted on sheet 3 of the drawings the autoclave weighs 33lbs. It is difficult to move back and forth from its “drydock” to my hood. Also, the
bolt torquing is a challenge and a two-man job.
If one could locate the pressure/fill port tree and thermowell in a smaller area, use of a smaller pipe, say 2” or even 1.5”, would be possible.
The autoclave could then be made smaller and with a longer body. The autoclave book referenced above recommends a length to diameter ratio of 2 to 3.
My ratio is a little less than 2.
Heating of the flanges is another possible area of improvement. With a smaller autoclave one could consider total oil immersion, thus guaranteeing a
more even heating and a more trustworthy temperature indicated at the thermowell.
I would use welded fittings right from the start, minimizing use of any threaded connections.
Building and commissioning an autoclave is not quick or cheap, even with my cost saving measures. But it can take you into an area of chemistry not
ordinarily accessible to the home chemist.
Errata:
Obviously the checker didn't catch the error on the number of nuts required in the "Bill of Materials." It should be 16.
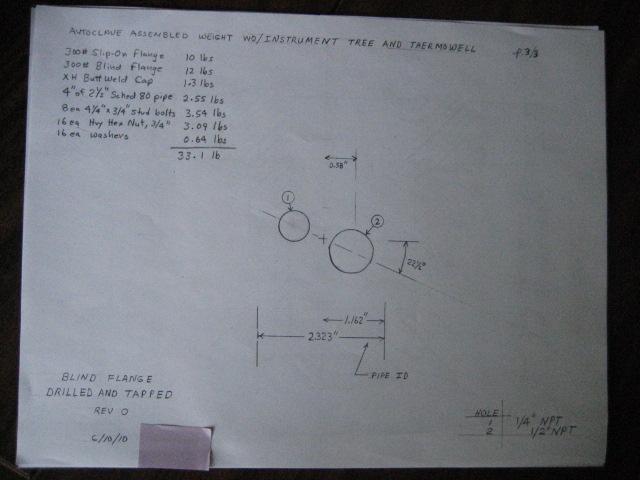
[Edited on 13-10-2010 by Magpie]
[Edited on 2-11-2010 by Magpie]
The single most important condition for a successful synthesis is good mixing - Nicodem
|
|
psychokinetic
National Hazard
  
Posts: 558
Registered: 30-8-2009
Location: Nouveau Sheepelande.
Member Is Offline
Mood: Constantly missing equilibrium
|
|
Looking good there Magpie.
Superbly fitting with your signature
“If Edison had a needle to find in a haystack, he would proceed at once with the diligence of the bee to examine straw after straw until he found
the object of his search.
I was a sorry witness of such doings, knowing that a little theory and calculation would have saved him ninety per cent of his labor.”
-Tesla
|
|
Magpie
lab constructor
   
Posts: 5939
Registered: 1-11-2003
Location: USA
Member Is Offline
Mood: Chemistry: the subtle science.
|
|
Thanks psycho. Here's the pictures:
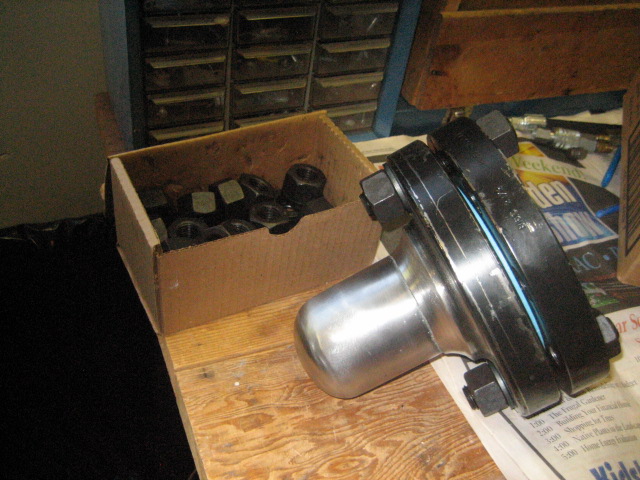 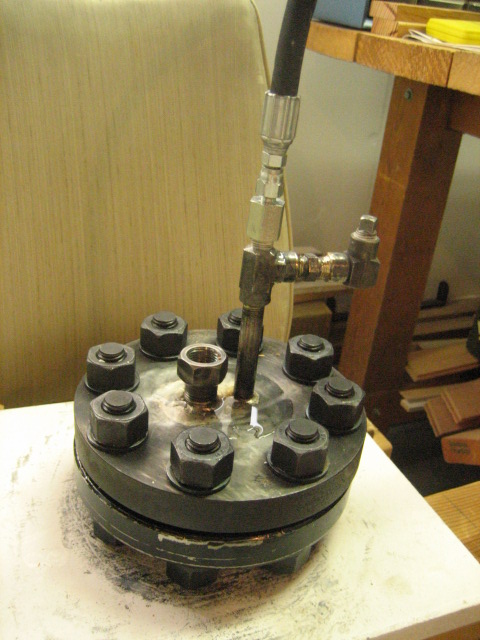 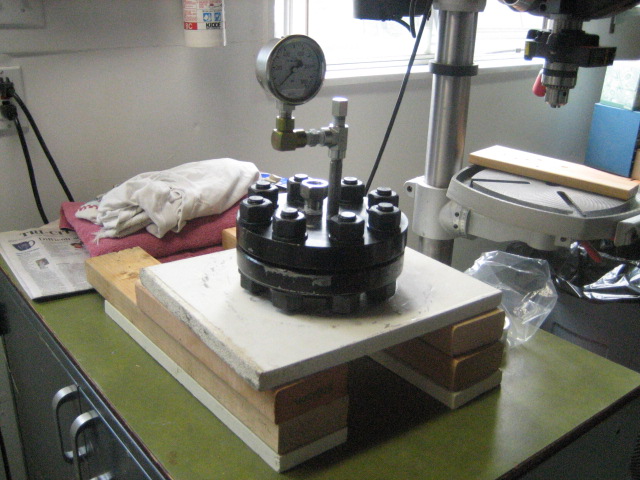 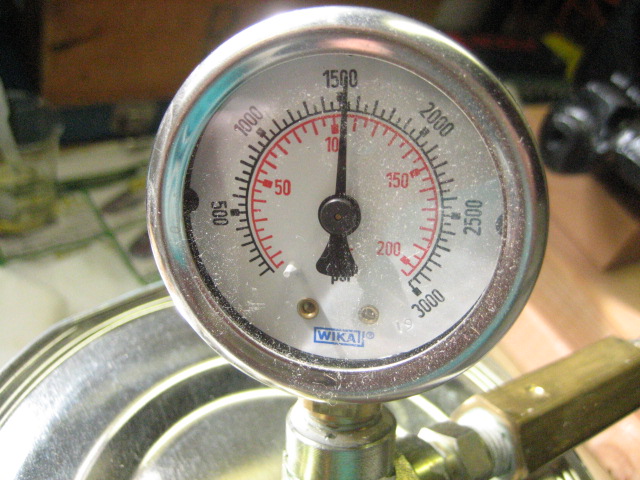 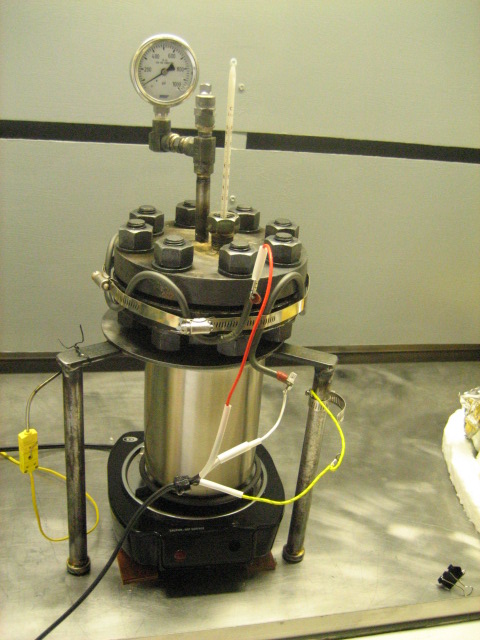 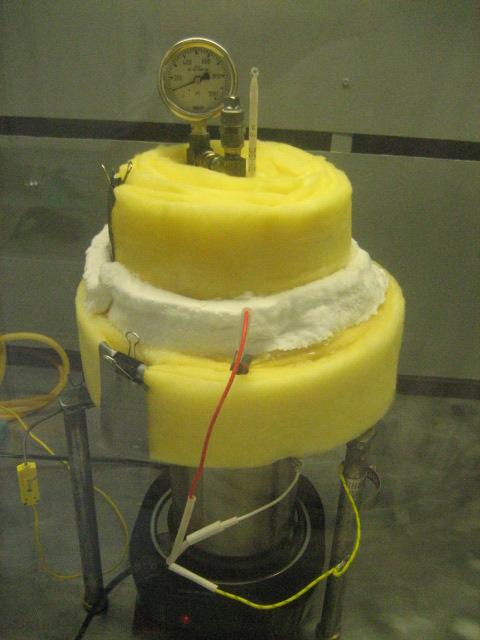
The single most important condition for a successful synthesis is good mixing - Nicodem
|
|
gsd
National Hazard
  
Posts: 847
Registered: 18-8-2005
Member Is Offline
Mood: No Mood
|
|
Very nice Magpie! well done.
But I am wondering for such a small autoclave, why start with a pipe, a cap and pair of flanges with lot of high-skill welding?
Why not do it with a bar-stock and one flange and lot of skilled machining? - especially if you are using MS and not SS.
gsd
|
|
Magpie
lab constructor
   
Posts: 5939
Registered: 1-11-2003
Location: USA
Member Is Offline
Mood: Chemistry: the subtle science.
|
|
Quote: Originally posted by gsd  | Very nice Magpie! well done.
But I am wondering for such a small autoclave, why start with a pipe, a cap and pair of flanges with lot of high-skill welding?
Why not do it with a bar-stock and one flange and lot of skilled machining? - especially if you are using MS and not SS.
gsd |
Thanks gsd.
I don't see where that would be much easier or cheaper. Also I have no experience with something like that.
I know that modern small autoclaves like those of Parr and Autoclave Engineers do use special machined heads, possibly then requiring special gaskets.
But this is a totally different closure system than what I used.
I tried to stay as close to ancient technology as possible, keeping with SM traditions and all.
The single most important condition for a successful synthesis is good mixing - Nicodem
|
|
psychokinetic
National Hazard
  
Posts: 558
Registered: 30-8-2009
Location: Nouveau Sheepelande.
Member Is Offline
Mood: Constantly missing equilibrium
|
|
I think I just got jealous.
“If Edison had a needle to find in a haystack, he would proceed at once with the diligence of the bee to examine straw after straw until he found
the object of his search.
I was a sorry witness of such doings, knowing that a little theory and calculation would have saved him ninety per cent of his labor.”
-Tesla
|
|
aonomus
Hazard to Others
 
Posts: 361
Registered: 18-10-2009
Location: Toronto, Canada
Member Is Offline
Mood: Refluxing
|
|
Very well done Magpie. That autoclave is pretty comparable to commercial ones in terms of pressure range and build quality. Commercial autoclaves tend
to have more engineering put into the closure mechanism to allow for fast(er) opening and closing without compromising strength. They do involve
gaskets made of special (read: expensive!) inert materials. They have the ability to make vessels out of materials other than 316 SS (titanium and
hastelloy C)
A few questions for future development:
- Have you considered modifying a beaker (ie: cutting off the 'lip' and flame polishing) to act as a glass insert for the autoclave?
- What about mechanical stirring? I know a bit about the Parr magnetic stirring system used on their hydrogenators, and if you do decide to
investigate further, send me a message and I'd be happy to help.
- Have you thought about additional ports on the lid of the autoclave? Parr and Buchi pressure vessels have ports for dip tubes, internal cooling
loops, vent lines, addition funnels, etc. It all depends on your chemistry though.
|
|
watson.fawkes
International Hazard
   
Posts: 2793
Registered: 16-8-2008
Member Is Offline
Mood: No Mood
|
|
Your welder did really good work. The pipe-cap joint is barely detectable from the photo. It's pretty clear that he ground bevels before welding. Did
he put it on a lathe with a tool-post grinder to clean up?
It looks like there's a quarter-round sub flange on the unit as constructed that's not in the drawing. Am I seeing that right? It seems like too much
material to be weld metal.
It there a reason you didn't weld the bottom nuts on? It's quick and makes it much easier to tighten. If the nuts need to be replaceable,
welding/brazing on bits of square rod stock on two sides of a nut provides a built-in second wrench. Another option, not very applicable at the point,
would be to have used automobile wheel studs and use a built-in bolt with a free nut.
As for being a two-person process, a simple plywood jig with a single central circle, holes for nut/bolt around the perimeter, and a quarter-wedge of
the whole cut out to provide a space to tighten a bolt. You'd have to lift it up and rotate for each bolt.
Another small modification that would make manipulation easier is to weld on handles, either to the top or bottom or both.
I would be interested in seeing final costs by line item, to go with your bill of materials.
|
|
Magpie
lab constructor
   
Posts: 5939
Registered: 1-11-2003
Location: USA
Member Is Offline
Mood: Chemistry: the subtle science.
|
|
Quote: Originally posted by aonomus  |
A few questions for future development:
- Have you considered modifying a beaker (ie: cutting off the 'lip' and flame polishing) to act as a glass insert for the autoclave?
- What about mechanical stirring? I know a bit about the Parr magnetic stirring system used on their hydrogenators, and if you do decide to
investigate further, send me a message and I'd be happy to help.
- Have you thought about additional ports on the lid of the autoclave? Parr and Buchi pressure vessels have ports for dip tubes, internal cooling
loops, vent lines, addition funnels, etc. It all depends on your chemistry though. |
Thank you anonomus.
- I really like that idea about a glass beaker insert. Having a glass-lined autoclave would be the cat's meow.
- Mechanical shaft stirring would mean a packed gland or a mechanical seal and there is no room for one. A magnetic stirrer, however, would be great!
Thanks for the offer of help on that.
- There's just room now for the pressure/fill port tap and the thermowell, so couldn't add anything more.
The single most important condition for a successful synthesis is good mixing - Nicodem
|
|
Magpie
lab constructor
   
Posts: 5939
Registered: 1-11-2003
Location: USA
Member Is Offline
Mood: Chemistry: the subtle science.
|
|
Quote: Originally posted by watson.fawkes  | Your welder did really good work. The pipe-cap joint is barely detectable from the photo. It's pretty clear that he ground bevels before welding. Did
he put it on a lathe with a tool-post grinder to clean up? |
No, I don't believe he did. He does have a complete machine shop, however.
Quote: Originally posted by watson.fawkes  |
It looks like there's a quarter-round sub flange on the unit as constructed that's not in the drawing. Am I seeing that right? It seems like too much
material to be weld metal. |
No, he just welded the slip-on flange as is.
Quote: Originally posted by watson.fawkes  |
It there a reason you didn't weld the bottom nuts on? It's quick and makes it much easier to tighten. If the nuts need to be replaceable,
welding/brazing on bits of square rod stock on two sides of a nut provides a built-in second wrench. Another option, not very applicable at the point,
would be to have used automobile wheel studs and use a built-in bolt with a free nut. |
The welder suggested those tack welds on the bottom nuts too. But I like being able to take everything apart for inspection and cleaning.
Quote: Originally posted by watson.fawkes  |
As for being a two-person process, a simple plywood jig with a single central circle, holes for nut/bolt around the perimeter, and a quarter-wedge of
the whole cut out to provide a space to tighten a bolt. You'd have to lift it up and rotate for each bolt. |
I thought about that also. But at 90-120 ft-lbs it's a 2 man job anyway. Unless your jig was bolted to the floor and some strong vertical force
applied the autoclave would just pop out.
Those would help.
I'll pull something together.
For the real cost I would include tools (1/2" drive torque wrench), silicone oil and can for same, insulation, aux heater, tripod stand, small
diameter thermometer, gaskets, 1/4" piping and fittings, and most of all: welding costs. I'm afraid to add that all up.
The single most important condition for a successful synthesis is good mixing - Nicodem
|
|
Magpie
lab constructor
   
Posts: 5939
Registered: 1-11-2003
Location: USA
Member Is Offline
Mood: Chemistry: the subtle science.
|
|
Quote: Originally posted by watson.fawkes  |
It looks like there's a quarter-round sub flange on the unit as constructed that's not in the drawing. Am I seeing that right? It seems like too much
material to be weld metal.
|
I see what you are saying here now. The drawing is just representational in that area.
The single most important condition for a successful synthesis is good mixing - Nicodem
|
|
Magpie
lab constructor
   
Posts: 5939
Registered: 1-11-2003
Location: USA
Member Is Offline
Mood: Chemistry: the subtle science.
|
|
Quote: Originally posted by aonomus  |
- Have you considered modifying a beaker (ie: cutting off the 'lip' and flame polishing) to act as a glass insert for the autoclave?
|
The outside dimensions for a Berzelius tall form beaker are 57mm x 104mm. That would be nearly perfect as the inside dimensions for the autoclave
straight side body portion are 61.5mm x 101.6mm.
What's the best way to cut that lip off? Will a diamond wheel on a Dremel tool do the job?
The single most important condition for a successful synthesis is good mixing - Nicodem
|
|
Magpie
lab constructor
   
Posts: 5939
Registered: 1-11-2003
Location: USA
Member Is Offline
Mood: Chemistry: the subtle science.
|
|
Autoclave Material Costs
4” of pipe…………………….6.50
Pipe cap………………………6.83
Slip-on flange……………12.35
Blind flange………………18.94
8 stud bolts………………11.62
16 nuts………………………18.70
16 washers.................4.15
Thermowell................34.50
Pressure gauge.........37.08
TOTAL.....................$150.67
The single most important condition for a successful synthesis is good mixing - Nicodem
|
|
aonomus
Hazard to Others
 
Posts: 361
Registered: 18-10-2009
Location: Toronto, Canada
Member Is Offline
Mood: Refluxing
|
|
There is a catch to the magnetic stirring used on Parr hydrogenators which means the bearings and seals don't need to withstand the pressure
differential between inside and 1atm, just a tiny bit of pressure until it equalizes, and then keep the reaction mixture out of the stirrer mechanism.
|
|
Magpie
lab constructor
   
Posts: 5939
Registered: 1-11-2003
Location: USA
Member Is Offline
Mood: Chemistry: the subtle science.
|
|
Kimax makes a Berzelius beaker without a lip, otherwise same dimensions.
I really don't want to even think about seals and bearings for an agitator shaft.
The single most important condition for a successful synthesis is good mixing - Nicodem
|
|
aonomus
Hazard to Others
 
Posts: 361
Registered: 18-10-2009
Location: Toronto, Canada
Member Is Offline
Mood: Refluxing
|
|
Probably the best way to cut the lip off is to score the circumference and use heat-shock to break the seam.
See: http://www.youtube.com/watch?v=sFXngPx3w3M
Because borosilicate glass has a lower thermal expansion coefficient, you might have trouble using heat-shock to make a nice crack propagate around
the circumference.
You should come up with a plan to fill the bottom semi-circular portion of the vessel with some sort of heat transfer medium (metal BB's come to mind)
so that all sides of the glass insert are evenly heated.
Again, cool work for super-cheap autoclaving goodness. Look forward to seeing the actual writeups from using it for chemistry.
|
|
Magpie
lab constructor
   
Posts: 5939
Registered: 1-11-2003
Location: USA
Member Is Offline
Mood: Chemistry: the subtle science.
|
|
Quote: Originally posted by aonomus  |
You should come up with a plan to fill the bottom semi-circular portion of the vessel with some sort of heat transfer medium (metal BB's come to mind)
so that all sides of the glass insert are evenly heated. |
Yes, the heat transfer to the glass beaker would be terrible because of the air gap, not just on the bottom, but also on the side of the beaker. What
is needed is a heat transfer fluid that is inert to reaction conditions and gases.
I might do that for N,N-dimethylaniline.
The single most important condition for a successful synthesis is good mixing - Nicodem
|
|
watson.fawkes
International Hazard
   
Posts: 2793
Registered: 16-8-2008
Member Is Offline
Mood: No Mood
|
|
The yellow pages
under "hydraulic equipment and supplies" should yield adequate seals. You'd likely need a stack of V-seals, just like those used to seal hydraulic
actuator cylinders. They do come in Viton; not sure about PTFE.
The bearings aren't any special problem, since you can use a pair of them outside the pressure zone. The sequence on the shaft look like stirrer >
seal stack > bearing > bearing. A taper bearing is adequate for one of those, I don't see a need to add a thrust bearing. Remember, the outward
force on, say, a 3/8" shaft at 200 psi is about 221 lbs, which a decent taper bearing will handle.
The expensive part is the machining, as you've no doubt learned. Speaking of which, how much was your outside labor cost? I was curious about the
material vs. labor expense for the project.
|
|
aonomus
Hazard to Others
 
Posts: 361
Registered: 18-10-2009
Location: Toronto, Canada
Member Is Offline
Mood: Refluxing
|
|
Regarding mechanical stirring: http://www.parrinst.com/default.cfm?Page_ID=164
The way Parr does it is by having a chamber above the vessel that is at pressure with the rest of the vessel, and the seal in the lid just has to be
good enough to exclude any liquids from the compartment. Inside a shaft with embedded magnets transfers the rotation from the motor to the shaft
inside. The seals are PTFE with cooling water running through the gland area to keep the temperature cool. It would appear that you might even be able
to order one of those from Parr (at an arm and a legs cost!)
Edit: Another potential use comes to mind: supercritical fluid extraction of compounds from products using CO2. I'd suspect if you loaded the
autoclave with the right amount of say, coffee beans and dry ice, sealed, then heated, you could get a stable SCF extraction going, then release the
pressure to let your caffeine just appear at the bottom. This could be an interesting development
[Edited on 14-10-2010 by aonomus]
|
|
Magpie
lab constructor
   
Posts: 5939
Registered: 1-11-2003
Location: USA
Member Is Offline
Mood: Chemistry: the subtle science.
|
|
welding........................................240
blind flange drill & tap ................65
silver soldering............................60
silver solder.................................42
TOTAL......................................$407
The single most important condition for a successful synthesis is good mixing - Nicodem
|
|
Rosco Bodine
Banned
Posts: 6370
Registered: 29-9-2004
Member Is Offline
Mood: analytical
|
|
Here is another idea which might work okay. What about converting a tie rod hydraulic cylinder assembly, removing the operating rod and piston,
leaving an empty chamber ? The way the cylinder sleeve fits into a bored socket in the end plates having an O-ring annular seal, there is not any
real torque requirement on the tie rods, so nuts lightly tightened just sufficiently for mechanical takeup would do the trick of just holding the
assembly together. The conversion could be done more simply than building something entirely from discrete parts.
[Edited on 14-10-2010 by Rosco Bodine]
|
|
Magpie
lab constructor
   
Posts: 5939
Registered: 1-11-2003
Location: USA
Member Is Offline
Mood: Chemistry: the subtle science.
|
|
A further enhancement that might be possible for my autoclave is enameling. But I understand from Wiki that this is a tricky process and might not be
an option for pipe steel due to high carbon content. I would also need access to a kiln as used in pottery making. If I couldn't do it myself I
would think labor costs would be high.
The single most important condition for a successful synthesis is good mixing - Nicodem
|
|
aonomus
Hazard to Others
 
Posts: 361
Registered: 18-10-2009
Location: Toronto, Canada
Member Is Offline
Mood: Refluxing
|
|
I wouldn't bother with enameling the surface, if you set it down too hard you risk chipping the surface and wasting your effort. Additionally it
introduces additional material that may react with the reaction mixture in the headspace. If you're looking for corrosion resistance, maybe try bluing
the steel?
|
|
Waffles SS
Fighter
  
Posts: 998
Registered: 7-12-2009
Member Is Offline
|
|
Excellent Magpie
Maximum how much pressure your auto clave can take?
|
|
Magpie
lab constructor
   
Posts: 5939
Registered: 1-11-2003
Location: USA
Member Is Offline
Mood: Chemistry: the subtle science.
|
|
Thank you. In the ANSI/ASME B31.1 table A106 Grade B Carbon Steel Pipes – Pressure and Temperature Ratings - the maximum allowable pressure for
2.5” pipe was interpolated between that for 2” and 3” pipe at 400F to be 2485 psi.
I did not test the autoclave to destruction so we have to go with the calculated value. Using a safety factor of 2 an upper limit would be:
2485psi/2 = 1243 psi = 84.5atm at 400F (205C). If a higher temperature is used the maximum safe operating pressure would have to be de-rated
accordingly.
Keep in mind that this is not my field of expertise.
The single most important condition for a successful synthesis is good mixing - Nicodem
|
|
Pages:
1
2 |