Pages:
1
2 |
Magpie
lab constructor
   
Posts: 5939
Registered: 1-11-2003
Location: USA
Member Is Offline
Mood: Chemistry: the subtle science.
|
|
pipe thread sealing
I have built a 350mL autoclave and am attempting to hydrostatically pressure test it using DOT 3 brake fluid. This mixture of glycols is one of the
most penetrating fluids I have ever seen.
I'm attempting to seal a 1/4" NPT connection. My first choice of a thread sealant (Rector Seal No. 7) was a miserable failure. After getting this
black gunk cleaned out of the threads I tried Ace's PTE sealant. This has sealed every joint except one. When I bring the pressure up to 500 psi it
starts leaking after a few seconds. I have not tried a combination of the Ace sealant and PTFE tape, but am thinking about it.
I had so many leaks on the TI thermowell and PI tree that I had them silver soldered. I'm really getting tired of trying to seal this thing up. At
500 psi all other connections, including the vessel flange head, are holding pressure.
Any recommendations or discussion will be greatly appreciated.
|
|
watson.fawkes
International Hazard
   
Posts: 2793
Registered: 16-8-2008
Member Is Offline
Mood: No Mood
|
|
I wish I could be more definitive about it, but I believe that
higher-pressure systems like this one are often built with threads of a higher class than ordinary plumbing fittings. So I'd first try re-threading
your parts. This isn't much more than chasing the threads with the appropriate tap and die. The goal is to get thread shapes that more closely match.
In particular, you should be able to get sharper crests and roots in the thread profile. All this should make your sealants work better.
|
|
gardenvariety
Harmless
Posts: 41
Registered: 19-1-2010
Member Is Offline
Mood: No Mood
|
|
Try finer threads, and absolutely use some PTFE tape. Two turns are best, more is a waste and sometimes a cause for leaks.
|
|
Magpie
lab constructor
   
Posts: 5939
Registered: 1-11-2003
Location: USA
Member Is Offline
Mood: Chemistry: the subtle science.
|
|
@watson:
The female threads are brand new so I don't see much point in chasing them. But that might do the male threads some good.
@garden:
I would love to have finer threads on the system but it's too late now. Every connection except the two that must be threaded have been sealed with
silver solder, ie, the fittings are welded in place.
I've learned that there are threads called NPTF for NPT Fuel. They would be better as there is no spiral gap at the thread root-peak interface. The
peaks deform into and fill the root when tightened. But it's too late for those also.
The leaking connection is for a fill pipe and will be capped when in actual use. Right now it connects to the pressurization device.
The other 1/4" NPT connection is for a PI that will be installed later for actual use of the autoclave. This connection now has a plug in it and is
holding pressure with the ACE PTE dope.
|
|
watson.fawkes
International Hazard
   
Posts: 2793
Registered: 16-8-2008
Member Is Offline
Mood: No Mood
|
|
Quote: Originally posted by Magpie  | The female threads are brand new so I don't see much point in chasing them. But that might do the male threads some good. | Your manual pipe thread tap may well cut the roots in the female thread deeper than originally manufactured. The point I'm making is
that the tolerances on a mass produced part are looser than you can cut them manually, using greater care and sharper tooling.
As a backup, you might consider silver-soldering on a bolted flange fitting and using that kind of connection rather than screw threads.
|
|
Magpie
lab constructor
   
Posts: 5939
Registered: 1-11-2003
Location: USA
Member Is Offline
Mood: Chemistry: the subtle science.
|
|
Quote: Originally posted by watson.fawkes  | Your manual pipe thread tap may well cut the roots in the female thread deeper than originally manufactured. The point I'm making is that the
tolerances on a mass produced part are looser than you can cut them manually, using greater care and sharper tooling.
As a backup, you might consider silver-soldering on a bolted flange fitting and using that kind of connection rather than screw threads.
|
I think I see what you are driving at. By using a tap and die I would cut new threads for both pieces of hopefully sharper definition. This would
make just a small difference in the take-up, but the length of thread engagement would be the same. Is this correct?
Welding on a flange would work but be a PITA. Welding on a compression fitting might be easier/cheaper. I'm finding that compression fittings can be
made leak tight much easier than threaded fittings.
I'm just hoping that the PI threaded joint will hold when I remove the plug and install the PI. I don't think it would be advisable to weld anything
onto the bourdon pressure guage.
|
|
Ozone
International Hazard
   
Posts: 1269
Registered: 28-7-2005
Location: Good Olde USA
Member Is Offline
Mood: Integrated
|
|
I have had good results with PTFE tape, alone. These joints (swagelock) did not leak at 15k psi (OK, once it blew the tube out of the ferule/nut
fitting and mangled it...but it did not leak beforehand).
Man, that will blow out more than the tube when it happens!
Best of luck,
O3
-Anyone who never made a mistake never tried anything new.
--Albert Einstein
|
|
watson.fawkes
International Hazard
   
Posts: 2793
Registered: 16-8-2008
Member Is Offline
Mood: No Mood
|
|
Quote: Originally posted by Magpie  | By using a tap and die I would cut new threads for both pieces of hopefully sharper definition. This would make just a small difference in the
take-up, but the length of thread engagement would be the same. | As I understand you, yes. The male would
screw in a little further, but since these are pipe threads the depth of contact is the same.
What's different though, is the total spiral-shaped volume between the male and female threads. When you cut the threads to tighter tolerances, that
volume goes down. Because the length of that cavity is pretty constant, what you've done is to decrease the effective size of the orifice that the
thread mating makes. The smaller that average cross-section, the higher the contribution that frictional forces contribute to flow rate
(surface/volume ratio), all of which mean that your sealants have less work to do. Once you get below the threshold (whatever it be), your sealant
holds perfectly.
The whole point of so-called dry-fit pipe threads is that the geometric match is good enough that the working fluid being contained acts as its own
sealant.
|
|
Contrabasso
Hazard to Others
 
Posts: 277
Registered: 2-4-2008
Member Is Offline
Mood: No Mood
|
|
Several pipe seal types don't actually seal at the threads they seal on the tip. The pipe end is cut to fit the end of the female threaded socket
perfectly, the nut just holds it all together.
Have you a test schedule for your vessel? 1/ you don't want to test it to destruction as you only have the one, but 2/ you need to test it within it's
elastic limit or there will be a permanent shape change.
What working pressure are you anticipating? What safety factor have you calculated into the design. You ARE going to fit safety and blowout valves I
trust so that accidental overpressure releases somewhere safely. You don't want steam spraying near you when you have to drop pressure anytime
I've seen a diver's air cylinder that was tested to destruction hydraulically -the side split all its length (IIRC 4x rated pressure) the mess there
is just sprayed oil. If there is a failure with gas inside it really is like a bomb going off with heavy shrapnel going all ways.
|
|
Mr. Wizard
International Hazard
   
Posts: 1042
Registered: 30-3-2003
Member Is Offline
Mood: No Mood
|
|
Why not convert the connections to the same used for hydraulic brakes? IIRC the pressure on a normal brake system is around 900psi. You won't be
relying on the semi plastic sealants to fill the gaps in the threads, but will be relying on metal surfaces mechanically held together.
I would second Contrabasso's caution about making sure there is NO gas in the system when pressure testing. Gas can store energy when being pumped up,
and will release it catastrophically.
|
|
densest
Hazard to Others
 
Posts: 359
Registered: 1-10-2005
Location: in the lehr
Member Is Offline
Mood: slowly warming to strain point
|
|
@watson.fawkes - according to "Machinery's Handbook", NPTF (F=fuel) threads are designed such that the crests of the threads deform when fully
engaged. That is supposed to form (at least part of) the seal.
@contrabasso - that's a good idea. There are several families of compression fittings for copper pipe/tubing & stainless steel tubing. There are
two major families I've seen: one requires flaring the end of the tubing/pipe and compresses that against a corresponding tapered end. The other
compresses a metal or plastic ferrule around the diameter of the tubing. That family is also used for plastic tubing (often with a supporting insert
inside the tubing.
Both families can be purchased (at least in the USA) for working pressures up to 3000 psi (200+ bar) or more. Correspondingly strong tubing can be
purchased - it's not horribly expensive as long as the diameter is small.
|
|
franklyn
International Hazard
   
Posts: 3026
Registered: 30-5-2006
Location: Da Big Apple
Member Is Offline
Mood: No Mood
|
|
No need to re-invent the solution , selct from Permatex , Loctite or Hercules
http://www.accentshopping.com/product.asp?P_ID=148706
Before application threads must be cleaner than merely wiping.
Google " High Pressure " " Thread Sealant "
http://www.google.com/search?hl=en&source=hp&q=%22hi...
.
|
|
Magpie
lab constructor
   
Posts: 5939
Registered: 1-11-2003
Location: USA
Member Is Offline
Mood: Chemistry: the subtle science.
|
|
Today I chased the pipe threads, filled the hose with oil, and ran another pressure test. It held at 500 psi for about a minute before leaking at the
same fitting. It's a fair amount of work to set up for a test as it's a pain getting all the air out of the connecting hose. But apparently my
technique is successful as I only have to take a few turns on my pressurization device to start building pressure rapidly.
Here's a couple pictures of the autoclave during testing. The first shows the male thread of the leak point. The second shows the connection to the
pressurization device and the leaked fluid.
Contrabasso, I appreciate your questions about the autoclave design, with my safety in mind: The body of the autoclave is a capped 2.5" schedule 80
mild steel pipe, welded construction. The flanges are "300 lb" class, mild steel. I can't find my calculations right now but, using a conservative
tensile strength for the steel I calculated a burst pressure in the 3-4000 psi range. I plan to hydrostatically test the autoclave at 1500 psi, and
limit myself to 500 psi during actual use. I should put a pressure relief device on it, and could install it on the fill pipe instead of a cap.
Edit1: I found my calculations. Using Barlow's formula and assuming a minimum yield strength of 30,000 psi for pipe steel, I calculate a burst
pressure of 5760 psi.
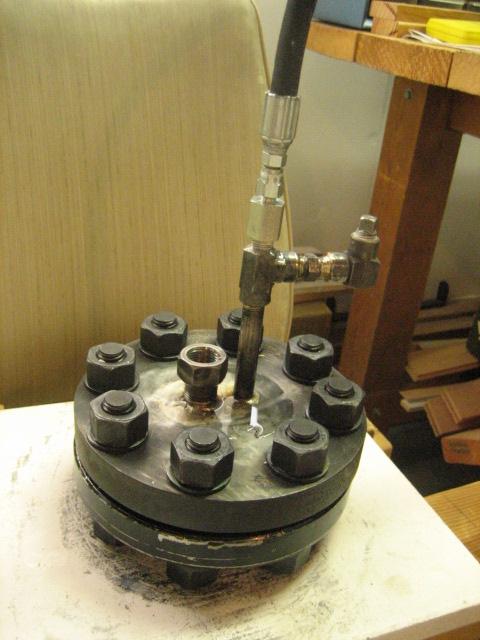
[Edited on 12-8-2010 by Magpie]
|
|
watson.fawkes
International Hazard
   
Posts: 2793
Registered: 16-8-2008
Member Is Offline
Mood: No Mood
|
|
Quote: Originally posted by Magpie  | Today I chased the pipe threads, filled the hose with oil, and ran another pressure test. It held at 500 psi for about a minute before leaking at the
same fitting. | My immediate thought is that the brass female fitting is deforming (by expanding) and
generating a spiral leak. What's the material of the male thread? It's conceivable that if the materials have a different enough modulus, that the
outer one is expanding more than the inner one with respect to pressure.
My other thought, just looking at the length of the threads, is that it might be bottoming out in the female side before the threads are fully
engaged.
Also, the crests on the male threads don't look particularly sharp, although it's kind of hard to tell from the photo.
I should also mention that I don't have particular confidence that any of these remarks get to the point of the problem.
|
|
Magpie
lab constructor
   
Posts: 5939
Registered: 1-11-2003
Location: USA
Member Is Offline
Mood: Chemistry: the subtle science.
|
|
Quote: Originally posted by watson.fawkes  | My immediate thought is that the brass female fitting is deforming (by expanding) and generating a spiral leak. What's the material of the male
thread? It's conceivable that if the materials have a different enough modulus, that the outer one is expanding more than the inner one with respect
to pressure. |
The male and female pieces are made of mild steel. The female looks like brass as it has a dichromate plating.
Quote: Originally posted by watson.fawkes  |
My other thought, just looking at the length of the threads, is that it might be bottoming out in the female side before the threads are fully
engaged. |
That's a possibility.
They're not. I meant to mention that when I was chasing the male threads I couldn't go very far down due to the shoulder on the tee. So I didn't cut
much metal.
|
|
merrlin
Hazard to Others
 
Posts: 110
Registered: 3-4-2009
Member Is Offline
Mood: No Mood
|
|
Quote: Originally posted by Magpie  |
The nominal hand-tight engagement length for a 1/4 NPT thread is about 1/4", so it looks like bottoming out is a good bet. If you scuff the face of
the male fitting with a fine grit abrasive paper and assemble it without a sealant, you should be able to see the contact area if it is bottoming out.
|
|
|
Magpie
lab constructor
   
Posts: 5939
Registered: 1-11-2003
Location: USA
Member Is Offline
Mood: Chemistry: the subtle science.
|
|
from merrlin:
Quote: |
The nominal hand-tight engagement length for a 1/4 NPT thread is about 1/4", so it looks like bottoming out is a good bet. If you scuff the face of
the male fitting with a fine grit abrasive paper and assemble it without a sealant, you should be able to see the contact area if it is bottoming out.
|
My hand tight take-up is about 8mm, so that's close to 1/4". This took 3.5 turns, which I believe is nominal. But the strange thing is that I would
only get 1 turn with the wrench when I last assembled it with the sealant. I quit when I felt the threads start to deform. But what I have read is
that you should get 3 turns with the wrench.
I'm not sure I understand what you are saying about scuffing the face with abrasive paper. Please explain this in more detail.
|
|
watson.fawkes
International Hazard
   
Posts: 2793
Registered: 16-8-2008
Member Is Offline
Mood: No Mood
|
|
If the fitting is bottoming out, the easiest thing to do is to just file down the male piece by a thread pitch or two. And by "file", I really mean
"angle grinder".
|
|
Magpie
lab constructor
   
Posts: 5939
Registered: 1-11-2003
Location: USA
Member Is Offline
Mood: Chemistry: the subtle science.
|
|
Quote: Originally posted by watson.fawkes  | If the fitting is bottoming out, the easiest thing to do is to just file down the male piece by a thread pitch or two. And by "file", I really mean
"angle grinder". |
If, by "bottoming out" you mean that the end of male is hitting the bottom of the female, that's definitely not happening. The female will take 17mm,
and I'm only getting about 10-11 mm of take-up of the male. You can see how much excess male thread there is in the picture of the assembly. The
threads in the female go very deep into the fitting.
Does the fact that I can only get 1 wrench turn seem strange to you?
|
|
watson.fawkes
International Hazard
   
Posts: 2793
Registered: 16-8-2008
Member Is Offline
Mood: No Mood
|
|
Yes. Since you've chased the threads,
it's likely not a burr interfering. In my experience with tapered threads, there's a first point where there's that metal-yielding feeling, but that's
OK, since it's the taper engagement. Around 3-4 turns later, there's a second version of it that kicks in, and that's the one not to go past. I
believe the first one is the motion of all the imperfections in the first pair of screw faces to mate. The second one seems like it's the second pair
of faces, and this time there's no where for the metal to go.
|
|
merrlin
Hazard to Others
 
Posts: 110
Registered: 3-4-2009
Member Is Offline
Mood: No Mood
|
|
Quote: Originally posted by Magpie  | from merrlin:
Quote: |
The nominal hand-tight engagement length for a 1/4 NPT thread is about 1/4", so it looks like bottoming out is a good bet. If you scuff the face of
the male fitting with a fine grit abrasive paper and assemble it without a sealant, you should be able to see the contact area if it is bottoming out.
|
My hand tight take-up is about 8mm, so that's close to 1/4". This took 3.5 turns, which I believe is nominal. But the strange thing is that I would
only get 1 turn with the wrench when I last assembled it with the sealant. I quit when I felt the threads start to deform. But what I have read is
that you should get 3 turns with the wrench.
I'm not sure I understand what you are saying about scuffing the face with abrasive paper. Please explain this in more detail.
|
Using #600 grit silicon carbide paper will produce a fairly uniform matte finish consisting of shallow scratches from the abrasive grains. Unless the
male fitting is much harder than the female fitting, the shear contact upon bottoming out will smear the scratch pattern and provide a visual
contrast.
If the fitting is not bottoming out and you are getting only one turn with a wrench, you could be hanging up on the last few threads at the large
diameter end of the taper on the male fitting. These threads can be too shallow due to die chamfer.
|
|
Magpie
lab constructor
   
Posts: 5939
Registered: 1-11-2003
Location: USA
Member Is Offline
Mood: Chemistry: the subtle science.
|
|
Thanks, merrlin.
I rechased both threads, again not being able to do the male threads properly because of the shoulder on the tee. I redoped then began screwing on
the female fitting. Again 3-4 turns on hand tightening, and only one turn possible with the wrench. I used a 12" crescent wrench to stabilize the
tee and an 8" box wrench on the female fitting. I tightened it as much as I could, likely much more torque than specification. Again the pressure
test at 500 psi failed.
I'm convinced there is something wrong with the male or female threads, or both. I'm not sure how to proceed from here. One possibility is to weld
on a coupling then a nipple having verified good male threads. Or better yet, figure out how to have a compression fitting on the bitter end.
|
|
densest
Hazard to Others
 
Posts: 359
Registered: 1-10-2005
Location: in the lehr
Member Is Offline
Mood: slowly warming to strain point
|
|
I'm not sure I understand "3-4 turns on hand tightening, and only 1 turn possible on the wrench". Does that mean you can hand tighten 3-4 turns and
then can only go 1 turn more?
Where did you get the fittings? McMaster-Carr? Local plumbing supply?
Can you put something on the threads to reveal the engagement (like some Dykem blue?)
Is there any reason to use a (what looks like) 1/4" pipe for your high pressure area? Could some 1/8" do? Could you move the 1/4-1/8 reducer to the
main pipe and use a 1/8" tee? The threads are finer and should work better.
There are fittings available for high pressure gases (Harris, the regulator maker comes to mind) rated over 3000 psi which I've found are made to
close tolerances. They go together quite cleanly.
|
|
Magpie
lab constructor
   
Posts: 5939
Registered: 1-11-2003
Location: USA
Member Is Offline
Mood: Chemistry: the subtle science.
|
|
Quote: Originally posted by densest  | I'm not sure I understand "3-4 turns on hand tightening, and only 1 turn possible on the wrench". Does that mean you can hand tighten 3-4 turns and
then can only go 1 turn more?
Where did you get the fittings? McMaster-Carr? Local plumbing supply?
Can you put something on the threads to reveal the engagement (like some Dykem blue?)
Is there any reason to use a (what looks like) 1/4" pipe for your high pressure area? Could some 1/8" do? Could you move the 1/4-1/8 reducer to the
main pipe and use a 1/8" tee? The threads are finer and should work better.
There are fittings available for high pressure gases (Harris, the regulator maker comes to mind) rated over 3000 psi which I've found are made to
close tolerances. They go together quite cleanly.
|
*Yes.
*Fittings are Tompkins or Brenan from a local high pressure hydraulic hose and fittings supplier.
*I might be able to do this but I don't see how it will lead to solving my problem.
*The reason is I'm welded in all the way to the 300lb flange head. I'd prefer to find a solution that works with what I have.
*The fittings I have are, no doubt, made in China. Using Harris, Parker, or Swagelok might be a step in the right direction.
|
|
merrlin
Hazard to Others
 
Posts: 110
Registered: 3-4-2009
Member Is Offline
Mood: No Mood
|
|
Quote: Originally posted by Magpie  | Thanks, merrlin.
I rechased both threads, again not being able to do the male threads properly because of the shoulder on the tee. I redoped then began screwing on
the female fitting. Again 3-4 turns on hand tightening, and only one turn possible with the wrench. I used a 12" crescent wrench to stabilize the
tee and an 8" box wrench on the female fitting. I tightened it as much as I could, likely much more torque than specification. Again the pressure
test at 500 psi failed.
I'm convinced there is something wrong with the male or female threads, or both. I'm not sure how to proceed from here. One possibility is to weld
on a coupling then a nipple having verified good male threads. Or better yet, figure out how to have a compression fitting on the bitter end.
|
At this point I would be inclined to epoxy a stainless 1/4NPT coupling to the male stub at the tee. Before epoxying the coupling, I would plug the
coupling and attach it to the hose with PTFE tape and pressure test it. That way you can verify the coupling before epoxying it to your existing
plumbing.
|
|
Pages:
1
2 |