Pages:
1
..
65
66
67
68 |
PLSHY
Hazard to Self

Posts: 91
Registered: 30-7-2023
Member Is Offline
|
|
Yes, four-stage stretch forming, and I also tinned it
|
|
Microtek
National Hazard
  
Posts: 869
Registered: 23-9-2002
Member Is Offline
Mood: No Mood
|
|
And some trumpet shaped cones as well I see. How big are they?
|
|
PLSHY
Hazard to Self

Posts: 91
Registered: 30-7-2023
Member Is Offline
|
|
11cm diameter
|
|
Microtek
National Hazard
  
Posts: 869
Registered: 23-9-2002
Member Is Offline
Mood: No Mood
|
|
I can see why you need such large amounts of HE then. I think you should go for plasticized PETN rather than the ETN/PETN melt we are discussing in
the other thread.
|
|
PLSHY
Hazard to Self

Posts: 91
Registered: 30-7-2023
Member Is Offline
|
|
Electroformed medicine cover, but it produced spiral patterns! Very strange! Can someone tell me how this spiral pattern is produced? Is it caused
by the mold rotating too fast? My mold speed is 120 rpm
|
|
Tsjerk
International Hazard
   
Posts: 3032
Registered: 20-4-2005
Location: Netherlands
Member Is Offline
Mood: Mood
|
|
Do you have a link to the process you used?
|
|
PLSHY
Hazard to Self

Posts: 91
Registered: 30-7-2023
Member Is Offline
|
|
My process is as follows:
Electrolyte: {150 g copper sulfate (anhydrous), 50 g sulfuric acid, 20 mg thiourea}/per liter.
Current density 3A/square decimeter.
The cathode rotation speed is 120 rpm.
The area of the anode is twice that of the cathode.
The distance between anode and cathode is 6cm.
Temperature constant 30 degrees
|
|
PLSHY
Hazard to Self

Posts: 91
Registered: 30-7-2023
Member Is Offline
|
|
Found the reason! The current density is too high! After electroforming for 24 hours at a current density of 3A, it was removed and the effect was
very poor
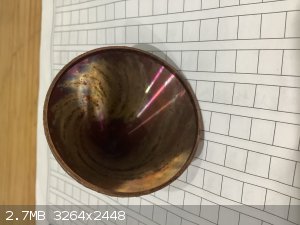
[Edited on 18-10-2023 by PLSHY]
|
|
PLSHY
Hazard to Self

Posts: 91
Registered: 30-7-2023
Member Is Offline
|
|
Then I lowered the current density and re-electroformed it using a current of 1.5A. This time the effect was much better. You can see the surface and
even reached a partially reflective level without polishing. This means that the grains are very So thin!(photo)
Finally, it can be found that there are still some imperfect structures on his surface, so I decided to repeat the electroforming again using a
current density of 1A. (In the photo, the medicine-shaped mask has undergone stress relief treatment at 200 degrees Celsius for one hour, so there is
some discoloration)
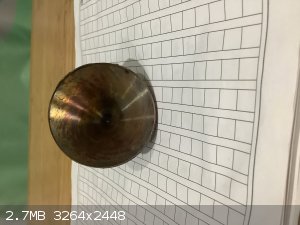
|
|
PLSHY
Hazard to Self

Posts: 91
Registered: 30-7-2023
Member Is Offline
|
|
1A
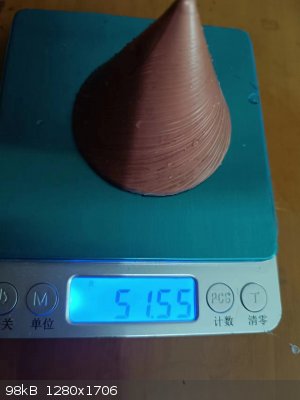 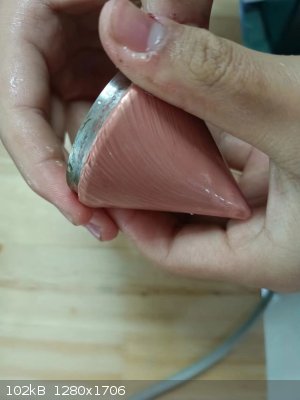
|
|
PLSHY
Hazard to Self

Posts: 91
Registered: 30-7-2023
Member Is Offline
|
|
I tried modern electroforming additives again, and the effect was very powerful! It can be completely reflective as soon as it is electroformed!
|
|
Microtek
National Hazard
  
Posts: 869
Registered: 23-9-2002
Member Is Offline
Mood: No Mood
|
|
I think the spiraling striations look as if they might reduce performance of the charge. Similar to the known fact that spinning conical liners on a
lathe introduces spin to the jet when the charge is fired. This defocuses the jet, and reduces performance.
|
|
PLSHY
Hazard to Self

Posts: 91
Registered: 30-7-2023
Member Is Offline
|
|
Quote: Originally posted by Microtek  | I think the spiraling striations look as if they might reduce performance of the charge. Similar to the known fact that spinning conical liners on a
lathe introduces spin to the jet when the charge is fired. This defocuses the jet, and reduces performance. | It's true that surface swirl patterns can have undesirable consequences, but the spiral arrangement of the internal crystal
structure is beneficial. Just like the Spin processing cover is similar to stamping in the static armor breaking state, but it is much higher than
stamping in the rotating state. However, considering that I mostly conduct static armor-breaking experiments, I thought about reducing the spiral
patterns on the surface as much as possible, or eliminating the spiral patterns through polishing.
[Edited on 2-11-2023 by PLSHY]
|
|
Microtek
National Hazard
  
Posts: 869
Registered: 23-9-2002
Member Is Offline
Mood: No Mood
|
|
I don't understand what you are trying to say here. What cover are you talking about? What do you mean by "stamping". What do you mean by "static
armor breaking state"? Your non-standard terminology is really throwing me off.
|
|
PLSHY
Hazard to Self

Posts: 91
Registered: 30-7-2023
Member Is Offline
|
|
Quote: Originally posted by Microtek  | I don't understand what you are trying to say here. What cover are you talking about? What do you mean by "stamping". What do you mean by "static
armor breaking state"? Your non-standard terminology is really throwing me off. | "Stamping" means the same as
"deep drawing" you mentioned before, and they both belong to the same processing method. Static armor piercing is to test the warhead without
rotation or initial speed. I'm sorry for my bad English. I'm working hard to learn English
|
|
dettoo456
Hazard to Others
 
Posts: 242
Registered: 12-9-2021
Member Is Offline
|
|
Has anyone looked into the use of wrought iron (or better yet, pure iron) sheet as an EFP or shaped charge liner material? I’ve seen the use of
‘Armco’ Iron (pretty much pure iron) a couple of times and it seems to have very good performance especially compared to copper. https://www.sciencedirect.com/science/article/abs/pii/073474...
Wrought iron should be close enough in terms of C content to the pure iron, as to not drastically affect workability or explosive performance, and it
is extremely cheap. The only issue I see is that it is hard to find wrought iron sheet. And almost no one produces pure iron sheet anymore.
|
|
underground
National Hazard
  
Posts: 702
Registered: 10-10-2013
Location: Europe
Member Is Offline
|
|
https://www.youtube.com/watch?v=KMLye177nqo
|
|
Laboratory of Liptakov
International Hazard
   
Posts: 1386
Registered: 2-9-2014
Location: Technion Haifa
Member Is Offline
Mood: old jew
|
|
Also you can try normal steel and do it 3x annealing. Heating by PB on red color shining and insert to dry ash on 15 minute. And repeatedly...
Development of primarily - secondary substances CHP (2015) Lithex (2022) Brightelite (2023) Nitrocelite and KC primer (2024)
|
|
dettoo456
Hazard to Others
 
Posts: 242
Registered: 12-9-2021
Member Is Offline
|
|
Are you referring to using Fe as a liner? After reading around a little bit, I figured that very low carbon steel (commercially sourced) can get close
to substituting pure iron if it’s annealed multiple times (>5 times to get best results) in either a vacuum, nitrogen, or just low airflow
atmosphere at around 780C for long dwell times - 10hrs or more. Working the hot sheet as well, through rolling or pressing, and then repeating the
annealing process will gradually convert the metal to purer Ferrite, which is what the pure iron (Armco) principally is.
Plus, since steel is easy to laser cut, annealed and worked Fe discs could be a very economically friendlier alternative to copper. And the
performance of the pure Fe is well-worth the price in my opinion.
Sadly, I don’t have any verifiably very low carbon steel, but I do have a kiln, so I plan to try this process whenever I get time and a sheet off
McMaster. I figure that once a steel disc of suitable size is cut, the annealing procedure combined with EFP pressing can just be combined; the deep
drawing steps can just be lengthened to also convert the steel to Ferrite. In the end, the finished liner would be exactly as required - both
geometrically for the EFP and phase-wise for ductility.
|
|
Laboratory of Liptakov
International Hazard
   
Posts: 1386
Registered: 2-9-2014
Location: Technion Haifa
Member Is Offline
Mood: old jew
|
|
I grabbed some old picture for construction EFP with results. Distance between liner and target was 50 cm. Copper liner 1 mm of thickness. Other
described.
I mean that was used Liptex as EM.......
Development of primarily - secondary substances CHP (2015) Lithex (2022) Brightelite (2023) Nitrocelite and KC primer (2024)
|
|
Cubane538
Harmless
Posts: 18
Registered: 30-7-2023
Member Is Offline
|
|
Hi guys,
I've a question regarding shape charge liner material,
I want to make shape charge liner with pure copper, I was using lost PLA casting method.
i tried to melt the copper in my furnace but it was getting cold very quickly before putting the liq. copper in the mold, The copper didn't melt well
anyway.
So I am thinking if I use bronze for making liner instead of pure copper.
will bronze work for shape charge liner??
|
|
dettoo456
Hazard to Others
 
Posts: 242
Registered: 12-9-2021
Member Is Offline
|
|
Bronze will work but much less so, and casting (with copper, bronze, or any other material) will likely require annealing after the fact to produce an
actually useful charge - for organized grain orientation in the metal. Tin also will affect ductility, so the resulting jet would travel at faster
speeds, have greater elongation, but lower penetration. Its density is also lower, which compounds the aforementioned qualities.
A lead-copper alloy, with <5% lead, might be better simply due to higher density. Lead itself can also be used as a liner but it performs quite
poorly. Though, I’d stay away from anything Pb related, simply due to me wanting to keep my precious few IQ points.
Have you tried to just cast Cu discs instead of full liners? The pressing process wouldn’t be too difficult if you already have say 3-5mm thick
discs on-hand.
|
|
Cubane538
Harmless
Posts: 18
Registered: 30-7-2023
Member Is Offline
|
|
Can I use 80% copper and 20% zinc
[Edited on 30-3-2024 by Cubane538]
|
|
PLSHY
Hazard to Self

Posts: 91
Registered: 30-7-2023
Member Is Offline
|
|
No, the boiling point of zinc is too low
|
|
PLSHY
Hazard to Self

Posts: 91
Registered: 30-7-2023
Member Is Offline
|
|
I tried the electroformed and the penetration reached 17cm. And it penetrated.
https://youtu.be/D57O5nhHSVU?si=hWjNyZZzxerBPPNv
|
|
Pages:
1
..
65
66
67
68 |