Pages:
1
..
53
54
55
56
57
..
60 |
clearly_not_atara
International Hazard
   
Posts: 2836
Registered: 3-11-2013
Member Is Offline
Mood: Big
|
|
Quote: | If you had more controlled heating would that help |
I don't think so... the observations indicate a self-sustaining exothermic reaction. The best you can do is calculate the yield, both heat and volume
of gas from the ideal gas law, and use those estimates to make sure your setup can contain it. You can probably slow the reaction down a little by
adding an inert "solvent" such as sodium bromide which will neither be oxidized nor reduced but absorbs heat.
Also if you dissolve the CO2 in the water the P4 will be less able to escape because there will be less gas to carry it; only thing is, I'm pretty
sure the gas it CO, not CO2, but I could be wrong on this point.
CO2 can be scrubbed by using alkali, weak alkali being preferable to prevent the production of phosphine. Ethylenediamine, ethanolamine, sodium
phenolate, etc are applicable.
CO on the other hand might be scrubbed by iron (II) salts or something, I'm not sure.
Possibly using a metal carbide could reduce gas production while still producing a "useful" amount of CO/CO2 evolution.
|
|
Magpie
lab constructor
   
Posts: 5939
Registered: 1-11-2003
Location: USA
Member Is Offline
Mood: Chemistry: the subtle science.
|
|
Commercial furnaces use coke (mostly carbon) rather than coal. Use of coal could produce all kinds of by-products like coal gas, etc. Coal gas is
flammable. I suggest replacing the coal with carbon.
What exactly was your charge composition, including quantities?
[Edited on 11-5-2017 by Magpie]
The single most important condition for a successful synthesis is good mixing - Nicodem
|
|
NeonPulse
Hazard to Others
 
Posts: 417
Registered: 29-6-2013
Location: The other end of the internet.
Member Is Offline
Mood: Isolated from Reality! For Real this time....
|
|
Been quite busy the past couple of weekends trying to get some P4 in OK yield. finally i had some success! after using the small scale method devised
by strepta i found the product was hard to recover and not enough. there had to be a better way. it has taken me quite some time to read this thread
in it's entirety but the knowledge discovered has been vital to success. using my gas powered forge i heated up the classic mixture of NaPO3, SiO2 and
dark Al powder plus a little NaCl flux as suggested several pages back. Also using a variation of the steel can retort Magpie was using for a while
was a great idea. previously i had tried a retort made from welded steel tube and plumbing bits but this failed. my forge was actually too hot and
melted holes in the steel. it easily pushes 1200C when it is warmed up. figuring that a brute force heating is not needed nor was the thick steel tube
setup i opted to go with the steel 500ml paint can. it is good to have it finally working but i wish the yields were better. i did another run
today with the retort exit tube deeper in the water and also a cone of steel mesh around it to try to break up the bubbles a bit better. the results
were better and there seemed to be bits of P4 caught in the mesh, however i pushed the limits of the retorts capacity and had it breach. next i will
line one with refractory of some sort.
Pretty keen to try other methods. i have a 500ml bottle of 85% phosphoric acid i bought over a year ago which i hav barely used 10mls of. also have a
bunch of mono ammonium phosphate.
maybe a carbon based reduction in the near future once i make a better setup. I also have everything I need to build an electric furnace including Hi
temp fire bricks, kaowool, Kanthal elements, PID and SSR, thermocouple and steel angle. I just need to find the time to put it together.
Here's a couple of videos:
Attempt by strepta's method: https://www.youtube.com/watch?v=Xljfwz1UMWE
a successful run: https://www.youtube.com/watch?v=mhFyVDBmDVk
And a couple of pics :
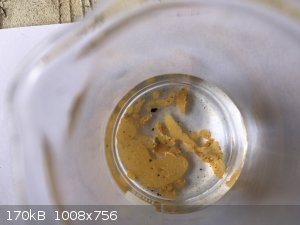
|
|
metalresearcher
National Hazard
  
Posts: 791
Registered: 7-9-2010
Member Is Offline
Mood: Reactive
|
|
I watched your videos and tried it out.
I don't have NaPO3, but I have Ca3(PO4)2. I mixed 31 parts of it with 18 parts SiO2 (hardware store fine silica sand used for mixing with stucco) and
9 parts Al powder.
6 Ca3(PO4)2 + 18 SiO2 + 20 Al => 18 CaSiO3 + 10 Al2O3 + 3 P4.
weight parts: 1860 : 1080 : 540 = 31 : 18 : 9.
I heated it to 1000 C in a steel tube retort after flushing it with Ar gas with the nozzle under water and after a few minutes bubbles appeared and
then a few flames above the water with white smoke. That should be P4, but was unable to capture it.
Here a video of the cooled retort emanating white smoke, probably slowly burning P4 to P2O5.
https://www.metallab.net/jwplayer/video.php?f=/clips/P2O5_fr...
[Edited on 2017-10-2 by metalresearcher]
|
|
metalresearcher
National Hazard
  
Posts: 791
Registered: 7-9-2010
Member Is Offline
Mood: Reactive
|
|
Another try, I used black pyro Al powder instead of gray stabilized.
After Just a few minutes after starting to heat it in a small propane furnace it started bubbling heavily in the beaker (left on the photo) and saw a
bright light with a pop, presumably P4 vapor / air mixture which had a small explosion.
After that bubbling stopped even after increasing retort temp to 800-1000 C so after 5 minutes I shut it down.
It appears that the reaction takes place in a kind of 'burst mode' : very quick reaction releasing all the P4 and then it stops.
On the photo: the white blanket on top is kaowool to keep the heat inside.
Next time I'll capture the P4 vapor in a closed tube (e.g. upside down test tube) filled with water to prevent escaping and force it to condense.
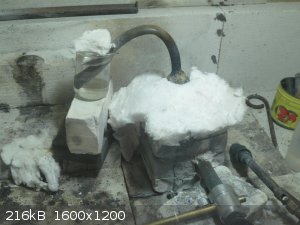
[Edited on 2017-10-3 by metalresearcher]
|
|
clearly_not_atara
International Hazard
   
Posts: 2836
Registered: 3-11-2013
Member Is Offline
Mood: Big
|
|
I think that more water is in order from the looks of your setup.
But since deeply submerging the outflow pipe in the flask led to clogging in previous trials, maybe one way to prevent P4 from condensing and clogging
the tube might be to insulate the tube from the surrounding water with e.g. a few layers of foam tape. This should keep the inside of the tube hot
enough to prevent condensation. Then you can put it in deeper water.
You could also consider a multi-stage condenser, with a pipe leading into one flask and the outgas from that flask led down another pipe into the
next, etc... hopefully condensation will then occur on the walls of the flasks and not in the tubes. Unfortunately this might not be the easiest thing
to construct.
A solution of NaHCO3 in the collection flask -- particularly in the first stage of a multi-stage setup -- would generate CO2 outgas that could help
keep the pipes in the later stages clear and thus allow them to be submerged deeper, while at the same time inhibiting combustion. This is a little
more speculative I guess.
[Edited on 4-10-2017 by clearly_not_atara]
|
|
Magpie
lab constructor
   
Posts: 5939
Registered: 1-11-2003
Location: USA
Member Is Offline
Mood: Chemistry: the subtle science.
|
|
I think the pops and bright flashes are phosphine, PH3, burning.
The single most important condition for a successful synthesis is good mixing - Nicodem
|
|
metalresearcher
National Hazard
  
Posts: 791
Registered: 7-9-2010
Member Is Offline
Mood: Reactive
|
|
That can indeed be, but after cooling and removing the retort nozzle from the flask, the retort started emanating white smoke which tells that
elemental P4 should be present (in small quantities).
clearly_not_atara: I don't think the retort tube was clogged, otherwise the clogging content would be spewed out at the time when the pop and flame
appeared.
I can put hot water (>44ºC, mp of P4) in the receiving flask to keep the P4 at least liquid.
[Edited on 2017-10-4 by metalresearcher]
|
|
metalresearcher
National Hazard
  
Posts: 791
Registered: 7-9-2010
Member Is Offline
Mood: Reactive
|
|
Now tried with carbon.
FAIL :-((
OVERHEATED !
6 Ca3(PO4)2 + 18 SiO2 (fine silica sand) + 30 C(harcoal powder) =>
3 P4 + 30 CO + 18 CaSiO3
weight ratio is 31 : 18 : 6.
I mixed 1.5g + 0.9g + 0.3g and put it into a 15mm OD steel tube of which one end is welded. That end I put in another short 30mm OD steel tube to as a
double layer due to the extreme heat.
I had to heat it up to 1200 - 1400 C in the same mini propane forge.
I put the nozzle into hot water of 60 C and started the run.
Soon i started bubbling which continued about 10 minutes and the inside of the furnace was blinding yellow.
Suddenly the bubbling stopped so I decided to shut it down and took out the yellow hot retort which sparked a bit, which means it is close to the
melting point of steel.
I let it cool and saw indeed that there is a leak in the inner tube and there were traces of melting of the steel / scale (Fe3O4, which has about the
same mp as steel). It must have been at least 1400 C.
Next time a little cooler ....
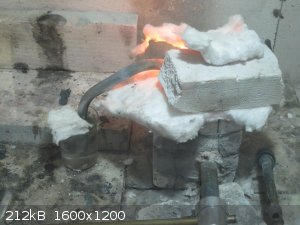 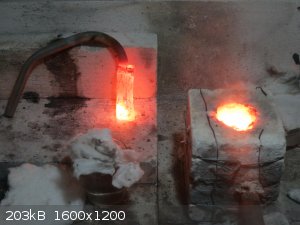
|
|
clearly_not_atara
International Hazard
   
Posts: 2836
Registered: 3-11-2013
Member Is Offline
Mood: Big
|
|
Have you considered using sodium to reduce phosphate? It could allow a much lower-temperature reaction if you're lucky...
|
|
Magpie
lab constructor
   
Posts: 5939
Registered: 1-11-2003
Location: USA
Member Is Offline
Mood: Chemistry: the subtle science.
|
|
Wow T= 1200-1400°C! If you get your condenser right you should be able to get P like clappers. This is the industrial temperature for P
production.
NaPO3 allows making P at about 800°C.
Industry makes briquettes to allow the efficient passage of gases, including gaseous P.
Temperature control of the condenser is important. Nice work.
The single most important condition for a successful synthesis is good mixing - Nicodem
|
|
metalresearcher
National Hazard
  
Posts: 791
Registered: 7-9-2010
Member Is Offline
Mood: Reactive
|
|
Another Fail :-(
I made a new double walled retort with a 3mm thick walled outer tube and silica sand between the outer and inner tube, the latter being the retort,
filled with Ca3(PO4)2, SiO2 (silica sand) and charcoal powder.
I heated it 20 minutes and now it kept bubbling, hoping some P4 vapor would appear, but it stopped again.
After shutdown and cooling it revealed a partially molten outer steel tube and leaking inner tube, so the temp must have been close to 1500 C ! With a
simple DIY natural gas burner (not propane as I said earlier) with forced air on a simple domestic supply of 30mbar (1/2 psi).
Next time a retort from iridium ;-)
I think I would revert to aluminum as reducer as the temperatures required for carbon reduction melt and destroy my steel retorts.
Magpie: How to make NaPO3 ? Or can I order this from Ebay ?

[Edited on 2017-10-5 by metalresearcher]
|
|
Magpie
lab constructor
   
Posts: 5939
Registered: 1-11-2003
Location: USA
Member Is Offline
Mood: Chemistry: the subtle science.
|
|
"Magpie: How to make NaPO3 ? Or can I order"
Order sodium hexametaphosphate from Kyantec.
FYI: mp for Ca(PO4)2 is 1657°C. With (NaPO)6 mp is about 800°C IIRC.
The single most important condition for a successful synthesis is good mixing - Nicodem
|
|
clearly_not_atara
International Hazard
   
Posts: 2836
Registered: 3-11-2013
Member Is Offline
Mood: Big
|
|
Wikipedia gives the mp of sodium hexametaphosphate as 628 C (1160 F), a good bit cooler than 800. Whether it will react at this temperature is less
obvious.
Sodium hexametaphosphate can be prepared by thermolysis of sodium dihydrogen phosphate, NaH2PO4, which is obtained by combining stoichiometric
quantities of sodium bicarbonate and phosphoric acid in a 1:1 molar ratio and heating to drive off water.
[Edited on 6-10-2017 by clearly_not_atara]
|
|
metalresearcher
National Hazard
  
Posts: 791
Registered: 7-9-2010
Member Is Offline
Mood: Reactive
|
|
Why does it need to melt ? More intimate contact ?
Do powdered solids not also have 'intimate contact' as the phosphate / SiO2 / Al powder mixture does react at 800 C ?
|
|
Magpie
lab constructor
   
Posts: 5939
Registered: 1-11-2003
Location: USA
Member Is Offline
Mood: Chemistry: the subtle science.
|
|
yes, I believe the intimate contact provided by molten aluminum/SHMP greatly augments the reaction rate. I don't understand how Monsanto and FMC get
such good production using Apatite, sand, and coke at 1200°C. Perhaps the apatite is molten at that temperature.
I wish I could find a simple way to make briquettes about 1/4" in diameter.
The single most important condition for a successful synthesis is good mixing - Nicodem
|
|
metalresearcher
National Hazard
  
Posts: 791
Registered: 7-9-2010
Member Is Offline
Mood: Reactive
|
|
What about adding a solvent such as NaCl ?
This melts at 800 C and the phosphate gets ionized. Does that work ?
|
|
metalresearcher
National Hazard
  
Posts: 791
Registered: 7-9-2010
Member Is Offline
Mood: Reactive
|
|
I tried it again, but still no P4 yet, but the flames are PH3 or P4 vapor ?
See this vid (with a slo-mo of the flames at the end taken with a GoPro Hero5 at 240 fps).
https://www.metallab.net/jwplayer/video.php?f=/clips/Failed%...
|
|
clearly_not_atara
International Hazard
   
Posts: 2836
Registered: 3-11-2013
Member Is Offline
Mood: Big
|
|
I don't know if you got the "more water" bit up there considering you used the same amount of water... but really it doesn't matter what the flames
are, probably a little of both. You need more water. (when I mentioned clogging, I was referring to problems other people had, not you)
I'm not sure if phosphates will dissolve in molten NaCl or simply form a cement... but it looks like you're getting way above 800 C anyway with your
setup so I'm not sure it matters.
[Edited on 8-10-2017 by clearly_not_atara]
|
|
Magpie
lab constructor
   
Posts: 5939
Registered: 1-11-2003
Location: USA
Member Is Offline
Mood: Chemistry: the subtle science.
|
|
Damn that retort is hot, metal researcher! Thanks for this fine video. Yes, that is PH2-PH2 burning. P would be making copious white smoke.
Can't you get some Calgon or sodium hexametaphosphate or apatite? When you get the right combination you are going to be making P like nobody has
seen before!
The single most important condition for a successful synthesis is good mixing - Nicodem
|
|
clearly_not_atara
International Hazard
   
Posts: 2836
Registered: 3-11-2013
Member Is Offline
Mood: Big
|
|
Magpie: H3PO4 is also the product of P2H4 combustion is it not? I'm struggling to think of a mechanism for his P4 to be converted to PH3 -- unless the
phosphate salt he's using is hydrated?
|
|
Magpie
lab constructor
   
Posts: 5939
Registered: 1-11-2003
Location: USA
Member Is Offline
Mood: Chemistry: the subtle science.
|
|
Yes PH3 is due to the presence of water. I don't know how phosphine is formed from water and P.
Burning phosphine:
2 PH3 + 4 O2 → P2O5 + 3 H2O
Dry all raw materials in a hot drying oven.
[Edited on 9-10-2017 by Magpie]
[Edited on 9-10-2017 by Magpie]
The single most important condition for a successful synthesis is good mixing - Nicodem
|
|
metalresearcher
National Hazard
  
Posts: 791
Registered: 7-9-2010
Member Is Offline
Mood: Reactive
|
|
Good idea. That might help, and flushing the retort with Ar gas before.
I limit temperature to 1200 C as otherwise the retort melts down, I have destroyed already a few steel retort tubes due to heating to 1400 C.
|
|
SWIM
National Hazard
  
Posts: 970
Registered: 3-9-2017
Member Is Offline
|
|
Quote: Originally posted by Magpie  | Damn that retort is hot, metal researcher! Thanks for this fine video. Yes, that is PH2-PH2 burning. P would be making copious white smoke.
Can't you get some Calgon or sodium hexametaphosphate or apatite? When you get the right combination you are going to be making P like nobody has
seen before!
|
Seems they've been screwing around with the Calgon formula.
I found an msds for Calgon water softener powder saying it's sodium citrate and 'carbonic acid, sodium salt (2:3)'
Wikipedia says it's currently zeolite and polycarboxylate.
|
|
Assured Fish
Hazard to Others
 
Posts: 319
Registered: 31-8-2015
Location: Noo Z Land
Member Is Offline
Mood: Misanthropic
|
|
Seems to me that the way forward is by using the carbothermoreduction method.
The major drawback of this it would seem is simply that the process produces waaaay too much gas to be controllable at a large scale.
So the obvious solution would be to find a way to remove the hot carbon monoxide/dioxide without removing the desirable P4, sooooo why not set up a
refluxing system above the receiver.
Like you can see in my professional looking drawing.
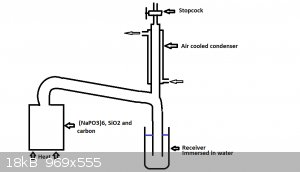
I realize dropping the temp of the condenser down to below 280*C is no gonna be easy, my drawing suggest using air cooling but if the column between
the receiver and retort was long enough then i see no reason why we cannot use water.
The stopcock would allow control over the amount of gas being let out and could be closed if too much phosphorous was escaping out the stopcock as it
would be clearly visible as phosphorous pentoxide.
The only major problem i see is that the condenser may not be enough to drop the P4 out of the gas flow, however i would imagine if there were enough
space inside and the condenser were tall enough then it should be enough to remove the P4 before it gets to the stopcock.
You wont be able to remove all the gas i know but provided the receiver was submerged deep enough you should be able to get a less intense flow of
distillate.
Obviously this would be a much larger engineering project than a typical retort but building a steel condenser and stopcock is nothing too complicated
for somebody who has a wielder.
Just my suggestion
|
|
Pages:
1
..
53
54
55
56
57
..
60 |