Pages:
1
..
48
49
50
51
52
..
60 |
halogen
Hazard to Others
 
Posts: 372
Registered: 18-4-2004
Member Is Offline
Mood: No Mood
|
|
Zinc oxide is known as a particularly volatile metallic oxide. Historically, zinc was discovered because it was noticed that when the sublimated
deposits of zinc oxide in the flues for copper smelting were added back into the copper, the quality and color of the metal changed, producing what we
now call bronze.
Aluminum also forms a phosphide. It used in semiconductor technology. Only lead and bismuth (of the relevant metals to this topic, afaik) refuse under
all conditions to combine with phosphorus.
F. de Lalande and M. Prud'homme showed that a mixture of boric oxide and sodium chloride is decomposed in a stream of dry air or oxygen at a red heat
with the evolution of chlorine.
|
|
Metacelsus
International Hazard
   
Posts: 2539
Registered: 26-12-2012
Location: Boston, MA
Member Is Offline
Mood: Double, double, toil and trouble
|
|
Quote: Originally posted by halogen  | Historically, zinc was discovered because it was noticed that when the sublimated deposits of zinc oxide in the flues for copper smelting were added
back into the copper, the quality and color of the metal changed, producing what we now call bronze. |
Sorry to nitpick, but I think that would be brass, not bronze.
|
|
clearly_not_atara
International Hazard
   
Posts: 2787
Registered: 3-11-2013
Member Is Offline
Mood: Big
|
|
Quote: | Only lead and bismuth (of the relevant metals to this topic, afaik) refuse under all conditions to combine with phosphorus. |
Silver phosphide exists, but it does not hydrolyse to release PH3 except by reaction with hydrogen, since the electronegativity of silver (1.9) is so
close to phosphorus (2.2) that the compound is essentially nonpolar, but the phosphorus atom is still easily oxidized:
https://books.google.com/books?id=qKQl6Ypl4KoC&pg=PA9&am...
Quote: | 2 Ag3P + 3 H2O + 5/2 O2 >> 6 Ag + 2H3PO4
2 Ag3P + 3 H2O + 3/2 O2 >> 6 Ag + 2 H3PO3 |
Since AgO is not a product it stands to reason that PH3 production is unfavorable (and realistically Ag+ should oxidize phosphine). Notably, silver
metaphosphate (AgPO3) melts at a surprisingly low temperature, 482 C if you believe Wikipedia -- so maybe you can melt the phosphate, not the
reductant!
https://en.wikipedia.org/wiki/Silver_phosphate#Other_silver_...
https://books.google.com/books?id=aDI9AAAAIAAJ&pg=PA300&...
[Edited on 18-3-2016 by clearly_not_atara]
|
|
BluePlanet1
Harmless
Posts: 41
Registered: 30-1-2016
Member Is Offline
Mood: No Mood
|
|
Alright, I got my camera set up yesterday & recorded a demo cook that was a bit dark. So today I built some hand held 200 watt clamp lights for
good lighting. With the lights set up the video comes out in true HD which is cool. Then there's a higher HD setting I haven't tried yet so this
camera is great. Very happy with it.
The bad news is apparently I left the seals on my retort too long (like 10 hours). I came back with my camera today to undo the seals. Now it seems to
be permanently bonded. I boiled it in water for like 30 mins. Beat it with a hammer like last time. Tried the biggest wrench I have. I can't break,
shake, losen or get these seals off no matter what.
I also noticed some weird properties that occur when conc sodium silicate and silica dust sit for too long. The adhesive I made yesterday I had left
over that I left in a SEALED air tight bottle. It was a small bottle with very little air.
I looked at it and thought it was still liquid. Then turned the bottle upside down and noticed it wasn't moving. Then opened the bottle and noticed
the adhesive in the bottle somehow cured. And it cured soo hard I can't even break it with a hammer and nail. It's really weird as the nail goes in a
bit through the surface but it's almost like the adhesive is partially elastic and pushes back on the nail head.
So then I did some more reading and noticed that silicates are used in BULLETPROOF MATERIALS ? There are patents right online for using potassium
silicate to stop bullets lol.
The only thing I can think of is the conc silicate solution sat with the silica so long that the silica pulled the water from the silicate. So
basically, the silica "dried" the waterglass. And the polymer that forms afterwards is a very weird material. When there's moisture still in it
although it's "rock hard" it gets a tacky, elastic type of.... it's like concrete rubber. Very hard to explain.
Anyway, I gotta pick up another retort tomorrow. And I'm gonna put this all on camera with some weird questions. Maybe there are chemists on here who
can explain how a polymer like this can cure and form in an air tight bottle. It seems like more than just silica drying the water glass as water
should be able to break that bond but after a certain point it does not. I may wind up just molding my own retort out of this material. Then I'll use
a steel housing in the cook area for easy cleaning. And possibly some compression seal rather than threads. Either way I got videos to upload they
should be up soon. :/
[Edited on 20-3-2016 by BluePlanet1]
|
|
BluePlanet1
Harmless
Posts: 41
Registered: 30-1-2016
Member Is Offline
Mood: No Mood
|
|
OK! I've spent a couple days doing more research.
From nuclear powerplants to the nazi death-gas concentration camps ... to reddit, to the national plumbers forum then finally to mythbusters and
popular science I've learned quite a bit.
First things first, I learned a neat "plumbing technique" for removing sealed pipes.
You need a real & LONG pair of plumbers pliers. Then ice water with salt is optional. What you do first is cool down the pipe. I should mention a
lot of plumbers said you don't need ice water and the salt part I added. But what you do is hold the pipe firm so it can't move. I don't have a vice
so I stepped on it. Afterwards you put the long pliers on the piece you're trying to get off. Then you simply apply PRESSURE to that cold part and
bang it in a circle all around.
They said as the pipes contract if you hammer with strong pressure applied (in 1 direction) the seal cracks.
I personally think just having longer plies did the job.
Here's what else I learned. As I was reading I noticed a pattern of many people on reddit, national plumbers, etc mentioned the same compound over and
over.
It's called "x-pando" : http://www.vatoraccessories.com/catalog.php/vatoraccessories...
More info here: http://www.xpando.com/xpando.php
MSDS here: http://www.xpando.com/msds/X-PANDO%20PIPE%20JOINT%20COMPOUND%20SDS%20(US)%203-9-16.pdf
But here's the cool part. I found this article from Popular Science called "Mythbusters Workshop: Extreme Plumbing."
In the article Adam & Jamie talk about how they spend a lot of time in plumbing stores. And how they usually head to the NPT section. They talk
about some crazy plumbing stuff they've done, explosives, high pressure, etc. And the part at the end (2nd to last paragraph) talks about a 250lb
rocket they built in 3 days with NPT fittings. They said they needed a sealant that can handle high temperatures and pressure and the product was once
again X-Pando: http://www.popularmechanics.com/science/a1455/4213140/
X-pando is also the site I learned the technique from.
It uses magnesium chloride, limestone, magnesium oxide, graphite and dextrin.
I've been using sodium silicate and silica.
But I'm gonna pick up this product tomorrow and compare them. The main issue I'm facing right now is I can create a strong seal. But the questions are
"how strong does the seal need to be?" and "is there a way to make the seal *weaker so it still works but comes off easier?"
What I like about my "SS" seal is it's instantly curable. The problem is even a thin film around the pipe will expand in open to about 5xs is size. So
inside the pipe that stuff is expanding and getting extremely dense.
I'm basically on a mission to make or find the perfect pipe dope. Fiber and ceramic paper have to be ruled out cause they tear. Then the high grade
stuff is really expensive. I'm also not confident about woven glass fibers being very airtight. Maybe in a gasket compressed flat. But wrapped around
a pipe I see the threads ripping right through it.
It could be possible that the talc I added... which I thought ruined the bond (it does make it less sticky)... maybe the right % of talc will soften
up the cure. The way I see it, talc is the softest mineral known to man. I need a high refractory material which could be anything (silica, alumina,
etc). I need a binder like waterglass or dextrin. Dextrin I'm against cause I've never fire cured it. At the same time the goal isn't to cure
anything. The binders are simply to get the refractory around the threads then tightened. After that point the binder is useless. So maybe I can
experiment with dextrin. The way I see it, you only need 2% or so. That gets the material in the pipe. You fire it. Ideally (somehow) control
expansion. Less expansion would be better. And if there's just a bit of talc in that seal it should make it brittle enough to pop right off.
This is all just useless theory.
These next few days I'll be cooking phosphorus but very small amounts just to test and remove the seals. One way or another I'll find the right
balance of whatever I need that creates an airtight seal but also comes off easily.
ps. I still have a video to upload I just gotta edit it and have been busy with this pipe dope stuff. :-)
[Edited on 22-3-2016 by BluePlanet1]
|
|
chemrox
International Hazard
   
Posts: 2961
Registered: 18-1-2007
Location: UTM
Member Is Offline
Mood: LaGrangian
|
|
Over 1200 post? Why all the interest? Could someone re-post the method for conversion of red P to the pyrophoric version? "pyrophoric" is not in the
dictionary?
"When you let the dumbasses vote you end up with populism followed by autocracy and getting back is a bitch." Plato (sort of)
|
|
BluePlanet1
Harmless
Posts: 41
Registered: 30-1-2016
Member Is Offline
Mood: No Mood
|
|
I went shopping today and figured I'd just line up most of what I'm working with.
There's a few things missing like vermiculite, carbon, torches, blah... but this is most of my P4 lab.
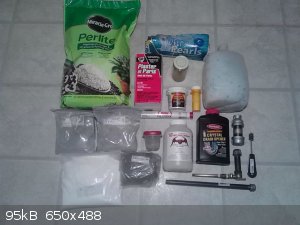
This shows the long back up retort I bought as a plan B just encase. I can heat and bend the pipe myself then that would reduce it to 1 seal instead
of 2.
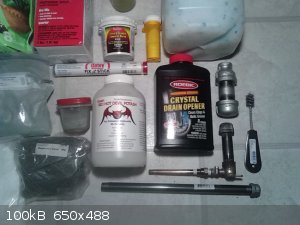
My NaPO3, Al & MG.
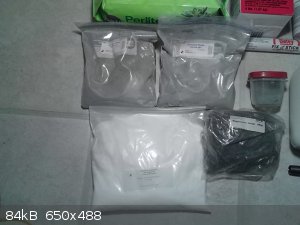
This shows the new sealants I bought and am working with. Perlite, vermiculite (not shown), water glass, silica dust, Imperials furnace cement &
mortar ($6.00 at Lowest) and Oakleys high temperature silicate putty. Then the plaster of paris I just bought to have.
The Imperials furnace cement says it can cure and tolerate temps as hot as firebrick (1093C). It makes gas tight seals. Best of all it cures with fire
rapidly unlike the putty. And it's not suppose to expand like the "x-pando" which I couldn't find.... I figured that'll make it easier to crack off.
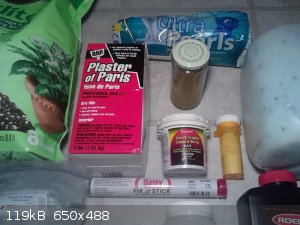
Close up of the sodium silicate
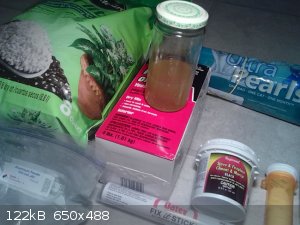
Just to show how the SS homemade stuff seals. This is a permanent seal I did with sodium silicate + silica dust. Mixed to a paste, applied, that seal
right there is rock hard and air tight.
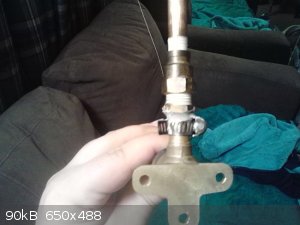
This is a close up of the firebrick cement. I tried to get the temperature but it looks blurry.
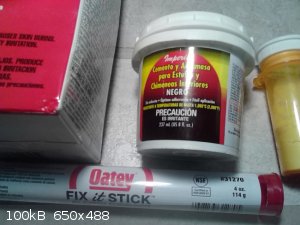
Either way I got 5 new supplies to work with. Vermiculite, perlite, plaster of paris, fire brick cement and silicate putty.
Some mixture of some type here will work how I need. I'm putting my money on the firebrick cement. Then once I get this sorted we move to the testing
stage of reductants & measuring yields. Oh and the zinc dust is on it's way. There was only 1 seller on ebay selling it but I promise we'll get
there soon.
Stay tuned as I'll be video taping how all these different seals work. ;-)
edit: I accidentally showed the wrong (spanish) side of the fire cement but you can see the temp if you zoom in.
[Edited on 23-3-2016 by BluePlanet1]
|
|
Daffodile
Hazard to Others
 
Posts: 167
Registered: 7-3-2016
Location: Highways of Valhalla
Member Is Offline
Mood: Riding eternal
|
|
Where did you get that refractory brick cement? Just to get bricks, I had to go to 4 hardware super centers, and the final product left something to
be desired (and I had to wait 40 minutes and talk to manager). After all that, they obviously had no cement like you have.
EDIT I know that the stuff isnt restricted, but its just uncommon.
[Edited on 23-3-2016 by Daffodile]
|
|
BluePlanet1
Harmless
Posts: 41
Registered: 30-1-2016
Member Is Offline
Mood: No Mood
|
|
Quote: Originally posted by Daffodile  | Where did you get that refractory brick cement? Just to get bricks, I had to go to 4 hardware super centers, and the final product left something to
be desired (and I had to wait 40 minutes and talk to manager). After all that, they obviously had no cement like you have.
EDIT I know that the stuff isnt restricted, but its just uncommon.
[Edited on 23-3-2016 by Daffodile] |
Lowes! I was surprised myself and it was the hardest to find. If you go to the aisle where they keep PTFE tape / plumbers tape you should see stuff
like "RectorSeal5", fluxes and solder.... at the very top of that shelf I noticed these big brown boxes. So I pulled a ladder over myself, climbed up,
opened the boxes and it was like x-mas.
I didn't see any on the shelf (idky) they just had it in boxes at the top. Your Lowes will obviously be different but hopefully they have it.
|
|
BluePlanet1
Harmless
Posts: 41
Registered: 30-1-2016
Member Is Offline
Mood: No Mood
|
|
So I was watching an interesting documentary a few days ago. It shows old, african tribes smelting iron from scrap. They literally dug the clay from
the ground, build everything by hand, charcoal by hand, iron ore by hand... then managed to melt and shape iron with one of their furnaces.
After seeing them do this 98% with their hands I thought "I'm retarded." If people can do stuff like this with no fancy tools I'm clearly
overestimating what it takes to build a stupid seal.
Then I took some plaster of paris out and put the paste around a pipe, capped it on and let it sit. I was awfully surprised how well it sealed the
pipe. So I fired it up.... the plaster outside the seal contracted and made hair line cracks. Inside the seal it still seemed air tight. The problem
is the plaster loses water leading to contraction in it's pure form. Although I firmly believe that a mix of:
1 tablespoon plaster of paris
1/2 tablespoon silica dust
bit of water to paste it
a few drops of conc water glass
That mix should stop the contraction. As as the plaster loses water when fired the water glass expands. It would bind better. Should also create a
softer seal that's easier to break. So I'll test that seal after this test.
RIGHT NOW I'm using furnace cement as it fires great. You take it out of the bottle and within 5 minutes it seals up rock hard. It doesn't contract.
No cracks. It also gets hard as steel when fired cured. The bottle says you need to wait 1 hour before firing it. It also says you have to PREFIRE
first. That was a huge mistake I made skipping the prefire as it will distort if you don't.
The 2nd time I let it sit 1 hour. Then threw it in the oven at 220F for 30 mins. Then I fired it and there was no distortion, expansion or cracks.
Even the thin parts on the steel I tried to flicker off with my fingers and it wouldn't budge or flake. What I'm banking on here is the fact this
stuff is for INTERIOR USE. I've thrown it in water after firing. It does lose its strength very fast, get flaky and break off. That should make seal
removal easy.
Here is what the pipe looks like with the black furnace cement....
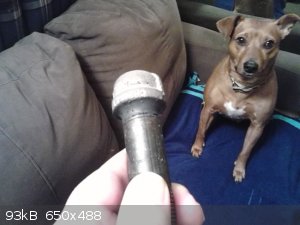
It's really good stuff. Here's another angle that looks like a weld:

After it air cured (1 hour) I charged the retort then sealed the 2nd seal:
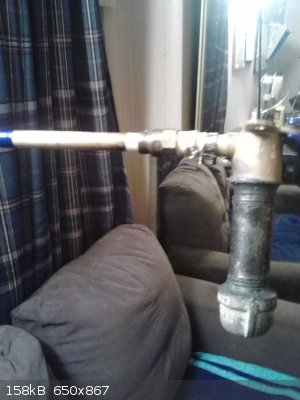
Here's a closer pic. The bottom seal is a bit messier as I wasn't aware how fast it would cure. So it looks a bit rough. But that inner seal (under
the surface & in the threads) went on as smooth as it gets. Adding a bit of water helps slow the cure time which I did on the 2nd seal.
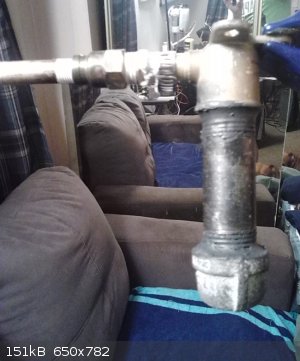
This was after I took it out the oven. Literally no change in appearance. And it looks the same exact way when you hit it with hot air-propane.
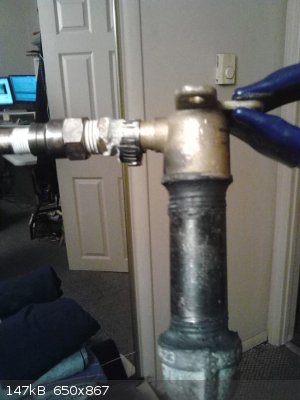
There is NO WAY in hell this retort is breaching or locking up.
According to the MSDS it contains:
Silica, Quartz - 40-70%
Hydrous Aluminium Silicate - 15-40%
Sodium Silicate - 10-30%
Sodium Hydroxide - 1-5%
That's a smart formula imo. As my homemade stuff was around 60% silica with 40% conc sodium silicate solution. The issue was my stuff expanded too
much and was very resistant to water. But I never thought of adding more lye. It makes sense that by doing that... when it's fired the lye reacts with
a small portion of silica to form more sodium silicate.
But I still don't get why their stuff breaks down fast when exposed to water and mine doesn't.
I can only assume the aluminum silicate and (or) unreacted lye is making it more vulnerable to water. That has to be what it is. Cause molten lye will
react with silica to form more sodium silicate and a stronger bond. But the reaction is very slow even when done in pure stoich ratios. So in this
impure state, there HAS TO BE unreacted lye left over after firing. And that little bit of unreacted lye which is highly water soluble allows the
materials to quickly break down when exposed to water. That's gotta be what's happening. I need to add a small % of lye to my own stuff and test.
Anyway, I could fire this right now but it's a bit late so I'll film it tomorrow... which is Easter ... uh, we'll have to see. Either way I know this
is gonna work great and it's making me a lot more confident to begin using my larger retort. I'll fire regular Al first. Next fire I'll do Al/MG/C
possibly with a different seal. Then I'll move to my larger retort if all goes as planned. 
ps. I know that P4 + lye = phosphine but we're talking a very low potential amount of lye and tight seals mostly blocked by silica and silicates... I
don't think it'll be an issue.
[Edited on 27-3-2016 by BluePlanet1]
|
|
Magpie
lab constructor
   
Posts: 5939
Registered: 1-11-2003
Location: USA
Member Is Offline
Mood: Chemistry: the subtle science.
|
|
Nice dog you have...seems interested in your work too.
I can't help but think that your pipe assembly could be simpler and cheaper. It looks like you are going from 1.25" or 1.5" steel to 1/2" brass.
If you used a 1.5" x 1/2" street ell reducer street ells, then a 1/2" coupling, then a piece of 1/2" pipe you could stay all steel. This should be cheaper and simpler. What do you think?
Is there some reason you want brass on the condenser?
The single most important condition for a successful synthesis is good mixing - Nicodem
|
|
BluePlanet1
Harmless
Posts: 41
Registered: 30-1-2016
Member Is Offline
Mood: No Mood
|
|
Quote: Originally posted by Magpie  | Nice dog you have...seems interested in your work too.
I can't help but think that your pipe assembly could be simpler and cheaper. It looks like you are going from 1.25" or 1.5" steel to 1/2" brass.
If you used a 1.5" x 1/2" street ell reducer street ells, then a 1/2" coupling, then a piece of 1/2" pipe you could stay all steel. This should be cheaper and simpler. What do you think?
Is there some reason you want brass on the condenser? |
Thanks. It's actually a 1" steel pipe brought down to 1/4".
The reason I used 1/4" brass is because I thought a sharp drop in size would force the P4 to liquefy better. And the problem is Lowes doesn't sell 1/4
threaded steel pipe.
However, after this last cook it's clear I have no idea what on Earth I'm doing. I'm not even gonna bother explaining since all 30 mins of this
disaster is on video.
Right now I'm compressing the file down. I wanna get this on YT asap cause it shows how dangerous & unpredictable this reaction really is. It also
shows everything that can possibly go wrong all in 1 take.
I'll be back very soon with a link. 
[Edited on 29-3-2016 by BluePlanet1]
|
|
BluePlanet1
Harmless
Posts: 41
Registered: 30-1-2016
Member Is Offline
Mood: No Mood
|
|
Ok, video is done but in the wrong format at 360p. I had to read and Google forums said it's a "glitch". I also had to edit it down from 28 mins to 12
mins. If someone kind knows how to embed it I'd appreciate it. 
https://www.youtube.com/watch?v=1kisHHTqi7M
That brass was hot as heck so why so much P4 got stuck in it... when it should have been liquid... I have to switch to steel.
|
|
j_sum1
Administrator
      
Posts: 6320
Registered: 4-10-2014
Location: At home
Member Is Offline
Mood: Most of the ducks are in a row
|
|
Congratulations on your success -- of a sort.
Some thoughts.
1. I am glad that someone has paved the way before me. It is so good to learn from watching someone else before attempting for myself. The phosphine
was good to witness from a distance.
2. I think a bigger diameter is needed for your retort. Switching to steel would be good too. (See point 3) you have your P clogging up inside the
pipe.
3. Your temperature control is not quite right. That I think contributed to the clogging. MP is 44C. BP is 280C so you should be in the range to get
liquid in the pipe. However, because copper conducts heat so well, it may be that you get solidification before the P hits the water. Steel would
help here. Using hot water would also help. I would be inclined to put an immersion heater in the water and keep it around 80C.
4. There is a problem with your setup in that you cannot let your gear cool down without drawing water up into the retort. I don't know that you want
sudden cooling and possible steam formation added to a tricky setup. The ability to feed some argon or something through a hose in the water and into
the retort as it cools would help a lot. I envisage a kind of a "J" shaped tube that you can simply immerse into water and into the retort and let a
slow stream of argon bubble out. Then you have no hurries. You can let the whole apparatus cool at your leisure and retrieve the phosphorus later.
5. You need a better scraper than a fork. You need a better method for reclaiming the product.
6. If it was me, I would immerse the whole thing into a tub of water once it has cooled and then disassemble it under water. Then you don't get any
losses. You can have already prepared an appropriate sized plunger to push the contents out of the pipe. Again, this buys you time. You don't need
to rush anything. You can do a physical separation of your product and anything else that you find in the retort. You can expose it to air when you
decide to and not during transfer.
7. You already know this but some better protective clothing is probably warranted here. Nice to have a gas mask. For this one, I think outside is
preferred to a fume cupboard. I'd prefer some running distance.
|
|
clearly_not_atara
International Hazard
   
Posts: 2787
Registered: 3-11-2013
Member Is Offline
Mood: Big
|
|
I'm a little curious as to how phosphine production might be minimized when blowing P2 (g) into H2O.
I know there are some metal salts (only Ag+ and Cu+ come to mind, but I know there are others) that will form insoluble phosphides by reaction with
phosphine in solution -- condensing phosphorus into a solution of such a salt should trap any PH3 that forms as a result, maybe?
Obviously precautions related to H3P must be taken nonetheless but even with a fume hood that PH3 has got to go somewhere, and I'd prefer it be
nowhere, lest it react with a piece of Al somewhere and only hydrolyze months to years later.
A slightly cheekier idea is blowing the phosphorus into 3% aqueous H2O2, but that could easily start a fire.
|
|
Magpie
lab constructor
   
Posts: 5939
Registered: 1-11-2003
Location: USA
Member Is Offline
Mood: Chemistry: the subtle science.
|
|
A "wife beater" and no gloves is not adequate PPE! I cringed as I watched you poke the burning P out of the condenser. If you get some of that
burning P on your skin you will rue the day you decided to experiment with it.
Keeping the condenser at the right temperature is something I struggled with also.
[Edited on 31-3-2016 by Magpie]
The single most important condition for a successful synthesis is good mixing - Nicodem
|
|
BluePlanet1
Harmless
Posts: 41
Registered: 30-1-2016
Member Is Offline
Mood: No Mood
|
|
Thank you all for the feedback. I will definitely use PPE next time I promise.
Temperature control is a serious issue so I figured it's time for a "tune up". I went back to Lowes today to buy a 10PSI bayou regulator ($22). I also
bought an addition $8 propane knob, $12 350PSIG hose, brass fittings ($16) and a badass 6" steel burner pipe with a flared (reverse reducer) end. The
propane was also very cheap it use to be $25 for a refill but right now Lowes is charging $15.
So now I have both a 10PSI regulated hose and an unregulated hose. Very similar to this: https://www.youtube.com/watch?v=eO8NwseRxSA except the unregulated hose is complete overkill. The 10PSI one sounds like a jet engine. The
unregulated hose even when turned on super low is like a blast furnace. I've never seen anything like it cause I was standing 5 ft away from the flame
(behind it) and started sweating.
Tomorrow I'm building 2 forges. 1 small forge dedicated to my smaller full steel retort. It now has a steel elbow and wider steel distiller.
Then a bigger forge for my 300gm retort which is also all steel. I know I can probably use just 1 forge but I want them both sized appropriately.
I read when air-propane is optimized right it can get up to 1995C or 3623F. Then from the tests I did today, I put a huge steel pipe in front of the
flame and instead of orange it got very bright yellow to the point the vice grips closed (pancaked) the steel in half then it fell in a bucket of
clay.
With this set up I'll be reaching much hotter temperatures, much more even heat distribution, the elbow will get yellow hot, the distiller will
probably stay orange. My goal is to vaporize every bit of WP out of the retort straight into water.
When I look back at the video... I was underpowered BTU wise and had poor heat distribution & insulation. Then also brass... the differential
expansion between steel and brass, breaching right at that point and no other tells me all steel should work much better.
I'll be working on this over the weekend and will get back to more trials early next week. I really think the forums gonna love this. :-)
|
|
BluePlanet1
Harmless
Posts: 41
Registered: 30-1-2016
Member Is Offline
Mood: No Mood
|
|
Hey all.
I doubt many are wondering but I'm waiting on a drill bit set in the mail. The small, #61-#80 size which are due to arrive next monday.
It's a long story but the propane burner I built was way too big as stores don't sell drill bits smaller than 1/16". And when I turn it down low it
doesn't burn optimally.... the pipes just too big for such a small forge.
So instead of using the "gasblaster" design (from Grant, King Of Random on YT) I'm building this burner instead: https://www.youtube.com/watch?v=uIRTcmR6sSk . I never realized you can hack the regulator on the small tanks so they can burn like that. And you
can also refill the small tanks easily with 1 bigger tank.
Right now I got all the pieces for the burner I'm just waiting to drill 1 hole. This way I'll have a more compact / efficient design and in the end
it'll be plenty hot enough for 50-300+gm charges. My forge is also very cool. I put a small metal brace in to prop the retort right in the middle.
When it's complete it should work beautifully. It actually looks somewhat like rogers retort just smaller and in a coffee can sized forge. I'll start
posting pics & videos by the middle of next week!
-BP
|
|
OldPhart
Harmless
Posts: 2
Registered: 13-4-2016
Member Is Offline
Mood: No Mood
|
|
I for one am glad for the update-no news for nearly 2 weeks on a project like this one could have any number of potentially negative/unhappy endings.
The smells on a burn unit are truly unforgettable and was definitely hoping you weren't occupying a bed in one-or worse...
|
|
OldPhart
Harmless
Posts: 2
Registered: 13-4-2016
Member Is Offline
Mood: No Mood
|
|
PS-
You can now get micro drill bits at Harbor Freight! $3.99 for an assortment of 30. I have not yet tried them but the reviews seem to be more
positive than negative.
http://www.harborfreight.com/high-speed-steel-micro-drill-bi...
|
|
halogen
Hazard to Others
 
Posts: 372
Registered: 18-4-2004
Member Is Offline
Mood: No Mood
|
|
Sodium metal the old way involves similar temperature and apparatus. It was distilled from a mixture of sodium carbonate and carbon. You wouldn't do
it inside, the byproduct is carbon monoxide. The process for potassium metal was the same, substituting potash for soda ash.
Intimate mixture of carbon and the alkali carbonate salt is the most important factor. No finer mixture can be obtained than by charring the tartrate
without air; this was impractical on larger scales so combination of pulverized charcoal were optimized. Presumably other organic salts work to some
extent. Cream of tartar, a byproduct of winemaking, is used in hollandaise sauce, beating eggs and other culinary inventions.
The book Aluminum (Joseph W. Richards 1890) has a chapter on sodium, which was required for aluminum production before the Hall (electrolytic)
process. Other sources can be found, for example one describes a gun barrel as the ideal retort for demonstrating the production of some potassium
droplets from potassium tartrate.
Due to potassium's greater reactivity with carbon monoxide it could form a black "explosive" deposit on the sides of the condensing flue. This wasn't
a problem with sodium.
F. de Lalande and M. Prud'homme showed that a mixture of boric oxide and sodium chloride is decomposed in a stream of dry air or oxygen at a red heat
with the evolution of chlorine.
|
|
JJay
International Hazard
   
Posts: 3440
Registered: 15-10-2015
Member Is Offline
|
|
Quote: Originally posted by halogen  | Sodium metal the old way involves similar temperature and apparatus. It was distilled from a mixture of sodium carbonate and carbon. You wouldn't do
it inside, the byproduct is carbon monoxide. The process for potassium metal was the same, substituting potash for soda ash.
Intimate mixture of carbon and the alkali carbonate salt is the most important factor. No finer mixture can be obtained than by charring the tartrate
without air; this was impractical on larger scales so combination of pulverized charcoal were optimized. Presumably other organic salts work to some
extent. Cream of tartar, a byproduct of winemaking, is used in hollandaise sauce, beating eggs and other culinary inventions.
The book Aluminum (Joseph W. Richards 1890) has a chapter on sodium, which was required for aluminum production before the Hall (electrolytic)
process. Other sources can be found, for example one describes a gun barrel as the ideal retort for demonstrating the production of some potassium
droplets from potassium tartrate.
Due to potassium's greater reactivity with carbon monoxide it could form a black "explosive" deposit on the sides of the condensing flue. This wasn't
a problem with sodium.
|
This thread is about phosphorus.
|
|
halogen
Hazard to Others
 
Posts: 372
Registered: 18-4-2004
Member Is Offline
Mood: No Mood
|
|
It's probably not common knowledge and the present participants in the extended conversation
F. de Lalande and M. Prud'homme showed that a mixture of boric oxide and sodium chloride is decomposed in a stream of dry air or oxygen at a red heat
with the evolution of chlorine.
|
|
blogfast25
International Hazard
   
Posts: 10562
Registered: 3-2-2008
Location: Neverland
Member Is Offline
Mood: No Mood
|
|
It's been mentioned in the sticky potassium thread (it works with potassium too).
|
|
WGTR
National Hazard
  
Posts: 971
Registered: 29-9-2013
Location: Online
Member Is Offline
Mood: Outline
|
|
Quote: Originally posted by halogen  | The book Aluminum (Joseph W. Richards 1890) has a chapter on sodium, which was required for aluminum production before the Hall (electrolytic)
process. |
Thanks for the source. That was an interesting read.
I've made small amounts of phosphorus in a borosilicate tube before, using the general hexametaphosphate/aluminum method before. The tube was under a
good vacuum, and the borosilicate was barely able to handle the heating without completely caving in. Soda lime glass wouldn't have been up to the
task, due to its lower softening point.
However, 1000C+ temps aren't hard to achieve with Kanthal or nichrome resistance wire. If I did this reaction again, I'd probably use a sleeved
reactor design. Both the reactor and its jacket would be under vacuum, so the reactor would be protected from both air oxidation and pressure
differentials. The resistance wire would be wrapped around the reactor, and the jacket would be air or water cooled. I'd probably put a window at
the bottom of the jacket, so that I could monitor the reactor temperature. I'd probably use a steel alloy for the reactor.
At about 1000C, the reduction with carbon might be feasible in this type of design.
|
|
Pages:
1
..
48
49
50
51
52
..
60 |