Pages:
1
..
40
41
42
43
44
..
60 |
blogfast25
International Hazard
   
Posts: 10562
Registered: 3-2-2008
Location: Neverland
Member Is Offline
Mood: No Mood
|
|
Very nice work and reporting, Magpie, as usual. At near 50 % yield that becomes a more viable way to produce some P.
Am I right in saying the retort internal volume (bearing in mind also the liner) is slightly larger than say, a can of pop? 35 g of charge shouldn’t
take up more than say 20 ml, so the content of the retorts must expand hugely during reaction.
Thermite like behaviour, probably self-sustaining, would be in line with my own single data point contribution here (p.17): once ‘lit’ it
‘burned’ furiously for about 30 seconds.
Re. using warmer water for the condenser to avoid P solidifying in the retort’s outlet, that was mentioned in one of the many cited papers on
reduction of phosphates, very high up in the thread (I was re-reading the bulk of it last night)
Have we any certainty that in the slag a borate is formed, instead of aluminate?
6 NaPO3 + 10 Al == > 6 NaAlO2 + 2 Al2O3 + 6 P
Then the low melting boric acid would really be just a (important) slag fluidiser.
Banal question: what’s your source of (NaPO3)n?
|
|
Magpie
lab constructor
   
Posts: 5939
Registered: 1-11-2003
Location: USA
Member Is Offline
Mood: Chemistry: the subtle science.
|
|
Thanks. Yes, this last yield is starting to make all this R&D look worthwhile.
Quote: Originally posted by blogfast25  |
Am I right in saying the retort internal volume (bearing in mind also the liner) is slightly larger than say, a can of pop? 35 g of charge shouldn’t
take up more than say 20 ml, so the content of the retorts must expand hugely during reaction. |
A can of "pop" (US slang - also used in UK?) here is 355mL. I measured my nominal 1/2 pint paint can at 270mL, as received. But, yes, the slag takes
up a lot of volume. And since I don't like furnace fires I tend to load it conservatively - at least the first time around with a new formulation.
There was a fair amount of freeboard in the fired can of the last run as you can see in the photo. So this formula could probably be loaded safely to
45g, maybe even 50g. The formation of P vapor and the high viscosity of the molten slag expand the volume of the slag greatly. During this last run
there was no slag in the inlet of the snorkel for the first time.
Quote: Originally posted by blogfast25  |
Have we any certainty that in the slag a borate is formed, instead of aluminate?
6 NaPO3 + 10 Al == > 6 NaAlO2 + 2 Al2O3 + 6 P
Then the low melting boric acid would really be just a (important) slag fluidiser. |
I'm really not sure about the chemical makeup of the slag. It does tend to dissolve after a few days sitting outside in a bath of 5% NaOH. When I
placed some in 14% NaOH at 50C there was rapid bubbling. This gas was flammable and I take it as H2 generated by unreacted Al.
Boria seems to present a distinct advantage over SiO2 in reduced slag volume and viscosity. I'm not sure yet about its effect on yield.
Dharma Trading.
The single most important condition for a successful synthesis is good mixing - Nicodem
|
|
m1tanker78
National Hazard
  
Posts: 685
Registered: 5-1-2011
Member Is Offline
Mood: No Mood
|
|
Quote: Originally posted by Magpie  | I want to say a little about the hazards of making and handling phosphorus. [...] Phosphorus is a very interesting element to make and experiment
with, but if you become complacent in handling WP you may pay dearly. |
Good timeout reminder Magpie. There's a lot of info here that one generally won't come across on the net or Wiki concerning the personal dangers and
encounters with WP.
I plan to do a few trials with TSP as that's the easiest for me to obtain. I plan to substitute the silica portion of the charge with a slight excess
of 'food grade' diatomaceous earth (very fine powder).
I'm still not sure whether all or part of the Al/Mg can be replaced with an alkali metal (specifically, sodium). I see a few potential problems with
this:
*Sodium probably won't mix intimately with the reactants.
*Na3P formation. I gather that in theory, the phosphides of Al/Mg can form in this reaction as well so that may be a non-factor.
*Sodium boils at 800+ degrees C. From Magpie's reporting this is slightly above the temp at which the reaction kick starts but the reaction (if any)
might drive off sodium.
The TSP and DE would be roasted prior to the trials. I'll likely try using Mg powder well before I experiment with other reducing metals. I won't be
attempting to collect WP at first. Mostly observing (at small-ish scale) if and how the reaction proceeds. These trials will be done outside and
upwind.
Can anyone comment on possible drawbacks of using DE as well as feasibility of using sodium in the reaction mix?
Tank
Chemical CURIOSITY KILLED THE CATalyst.
|
|
blogfast25
International Hazard
   
Posts: 10562
Registered: 3-2-2008
Location: Neverland
Member Is Offline
Mood: No Mood
|
|
@m1tanker78:
There are indications that orthophosphates (like TSP) are much harder to reduce than metaphosphate, upthread. Still, it would be nice to
confirm/inform that. Start with a test tube test?
DE isn't pure silica. That doesn't mean it won't work though.
Metal phosphide as by-products doesn't really seem to be an isuue in the strepta/magpie method.
|
|
Magpie
lab constructor
   
Posts: 5939
Registered: 1-11-2003
Location: USA
Member Is Offline
Mood: Chemistry: the subtle science.
|
|
I think one advantage of the use of Al/B2O3/NaPO3 is that all reactants are liquid prior to reaction initiation, which seems to be about 750C. This
is not true when using silica as the reaction fires off at around 550C, where all ingredients may still be solids. Lack of mixing is surely a
hindrance in these reactions so it seems that having all or even some of the reactants in the liquid state would be an advantage.
orthophosphate as precursor
There are some references to the fact that the main P producing reaction is:
P2O5 + reductant ---> P + oxide
So, the easier the phosphorus bearing ingredient can be converted to P2O5, the easier for the above reaction to occur.
For NaPO3 we have:
2NaPO3 + high heat ---> P2O5 + Na2O
For the P2O5 generating reaction to occur in the industrial reaction with an orthophosphate (PO4---) like Na3PO4, a temperature of 1200-1500C in an
electric arc furnace is required.
sodium as reductant
Sodium is a powerful reductant and more reactive than even magnesium, I presume. And it would definitely be a liquid at the reaction temperature.
And as you say it would very possibly be a vapor at the reaction temperature. This would cause havoc coming into a water receiver, let alone
contaminating your product. And how would you keep it from reacting with oxygen - you would surely have to have a cover gas in the reactor.
The above are just my thoughts, as per your request. In the end, as BromicAcid's signature so eloquently states: "Theory guides, experiment
decides."
[Edited on 7-10-2012 by Magpie]
The single most important condition for a successful synthesis is good mixing - Nicodem
|
|
m1tanker78
National Hazard
  
Posts: 685
Registered: 5-1-2011
Member Is Offline
Mood: No Mood
|
|
I performed a small test. I combined Mg, TSP and DE (in slight excess) in a small stainless steel cup. I placed an inverted SS cup over this and
secured it with a brick. The total charge was just over 1g. I didn't bother roasting the reactants in this test...

I used a propane torch to create a hot spot right at the bottom of the container (from the side). After ~ 5 minutes, there were 2 consecutive pops and
accompanying flame exited between the shell halves. I moved the torch around the bottom just to make sure the reaction had completed. I noted no
further reaction so I allowed everything cool for a few minutes.
When I removed the top shell half, the side walls immediately became engulfed in a thick white smoke. I dunked this in a container with water I had
prepared before the reaction even though I don't expect to recover any WP just yet. This all took place in a split second so no chance for a pic.
I did this outside and was upwind the whole time. I also put some distance between me and the 'reactor' whenever possible since I didn't know how
swift the reaction would be.
I hope to build upon this since apparently TSP + DE worked well although it's hard to say if it will scale up well. I'm also eager to try this
reaction with sodium or lithium instead of Mg/Al. In the meantime, I'll stick with Mg..
+++++++++++++++++++++++++++
EDIT:[/B]
Thanks for the reply Magpie. I inspected the spent mixture and noted no expansion nor bubbles. In fact, the mixture doesn't look like it liquefied -
presumably because I used DE (silica) rather than boria as you've been doing. I hope to be able to replicate the above experiment with sodium instead
of Mg. Should I use a lower molarity of sodium??
Tank
[Edited on 10-7-2012 by m1tanker78]
Chemical CURIOSITY KILLED THE CATalyst.
|
|
Magpie
lab constructor
   
Posts: 5939
Registered: 1-11-2003
Location: USA
Member Is Offline
Mood: Chemistry: the subtle science.
|
|
I don't know what to tell you here. I think you are in uncharted territory! Be careful and have fun.
The single most important condition for a successful synthesis is good mixing - Nicodem
|
|
Maya
Hazard to Others
 
Posts: 263
Registered: 3-10-2006
Location: Mercury
Member Is Offline
Mood: molten
|
|
Do you think that 96% Na6O18P6
would give a better yield than the commercial stuff?
|
|
Magpie
lab constructor
   
Posts: 5939
Registered: 1-11-2003
Location: USA
Member Is Offline
Mood: Chemistry: the subtle science.
|
|
Phosphorus run #8 was carried out yesterday with the following objectives:
1. Evaluate the effects of a larger batch size (45g vs 35g).
2. Evaluate the effects of a heated water receiver (55-60C).
As in run #7, boria and a 15% excess of aluminum were used. The water receiver was kept heated using a hotplate.
The retort was loaded into the furnace and brought up to 750C. At this time a 15 minute soak was started. However, after about 3 minutes the
reaction initiated and was quickly finished. There was less burning phosphine and smoke than before. The P came nicely into the receiver. Again it
was chocolate brown, as can be seen in the photo below:

Run #8 product
The yield was 3.2g for a %yield of 42.0%. That for run #7 was 41.7%.
Although the outlet of the condenser was at all times heated to around 55-60C by the water in the receiver there was some P deposits found in the end
of the condenser. They would catch fire as I pulled them out with a spatula.
The retort was difficult to open and was found to be full of slag. The disassembled retort is shown in the photo below:
Attachment: phpqQu8nV (129kB) This file has been downloaded 1044 times
Disassembled retort ass’y for run #8
The snorkel and condenser inlets are plugged solid. This is shown in more detail in the photo below. The condenser inlet is shown at the top; the
snorkel inlet is shown at the bottom.
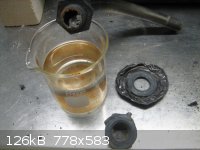
plugged snorkel and condenser inlets for run #8
This is due in part to a charge that is apparently too large. A 2nd factor is the inadvertent use of too much furnace cement lining. The lining
weighed 189.3g vs 57.9g for the last run. Also, this lining had bulged out in several places thereby decreasing working volume. This is thought to
be due to the addition of too much water to the cement, which was added to improve workability. Actually the cement can be rammed into place without
the addition of water.
Discussion
It appears that 45g is a tad high for charge size. If the lining had been correctly sized and installed this might not have been a problem. In
addition, the yield would probably have been greater if plugging had not occurred.
The heated receiver definitely facilitated the flow of P by keeping it liquid.
Questions, comments, and suggestions are welcomed.
[Edited on 12-10-2012 by Magpie]
The single most important condition for a successful synthesis is good mixing - Nicodem
|
|
blogfast25
International Hazard
   
Posts: 10562
Registered: 3-2-2008
Location: Neverland
Member Is Offline
Mood: No Mood
|
|
It seems you're approaching the outer limit of the capacity envelope of your set up.
|
|
Magpie
lab constructor
   
Posts: 5939
Registered: 1-11-2003
Location: USA
Member Is Offline
Mood: Chemistry: the subtle science.
|
|
With the present formulation, yes. There are a couple of variations I have been considering, however:
1. Ball mill the mixed reactants (under argon)
2. Substitute pyro grade flake Al for my currently used spherical, 100-200 mesh Al, per Strepta's recommendation
---------------------------------------------------------------------------
Would it be safe to ball mill a mix of NaPO3/Al/B2O3 in the ratio 1.00/0.51/0.34 using steel balls?
In general, can thermite mixtures be ball milled using steel balls?
[Edited on 14-10-2012 by Magpie]
The single most important condition for a successful synthesis is good mixing - Nicodem
|
|
Magpie
lab constructor
   
Posts: 5939
Registered: 1-11-2003
Location: USA
Member Is Offline
Mood: Chemistry: the subtle science.
|
|
Phosphorus run #9 was completed today. The charge was 35.6g, using boria, and aluminum in 15% excess. The purpose of this run was to evaluate the
effect of ball milling the mixed reactants.
The NaPO3 was first ground in a coffee grinder for 2 minutes. This was then mixed with boria and Al in a capped bottle. This mix was then ball
milled with ½” chromed steel balls for 6 hours.
The paint can retort was lined with 75.1g of furnace cement, an apparent minimum for complete coverage. The liner was slowly cured up to 500F. Then
the assembly was heated to 750C to burn off the tin plating on the can and remove liner water. There was no bulging of the liner.
The charged retort assembly was placed in the furnace and the thermostat set at 750C. Just before reaching this temperature the reactants ignited.
There was some burning phosphine and smoke and then chocolate colored P came rapidly into the receiver, which was heated to 47C. The weight of this
dirty P was 3.7g, for a %yield of 62.9%.
Weight loss of the reactor assembly was 412.9 – 409.5 = 3.4g.
The opened assembly is shown in the pictures below:
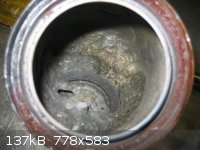
Opened retort for run #9
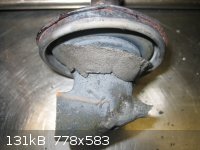
snorkel, run #9
I was ready to stop this series of testing, then mirabile dictu, on opening the retort I found that there was hardly any slag! The can was
mostly empty! So, it seems that at least one more test should be run, ie, that with a much larger ball milled charge.
Discussion
I’m not sure what is responsible for the contamination of the P that is giving it a chocolate color. Most likely it is just finely divided
reactants and/or slag carryover blown out with the rush of P vapor. This coloration first started back on run #7, which was the first successful
boria run using the larger (35g) charge. Hopefully the P can be cleaned up to remove this contaminant. I will try the cleaning methods using chromic
acid and HNO3 used by Endimion17.
The 62.9% yield is significantly higher than my previous best at 42.0% for run #8. So apparently the improved mixing and possibly finer particle size
provide significant advantage. Since all reactants should be liquid at 750C it seems that improved mixing would be the main factor responsible for
the increased yield.
Comments, questions, and recommendations are welcomed.
The single most important condition for a successful synthesis is good mixing - Nicodem
|
|
DJF90
International Hazard
   
Posts: 2266
Registered: 15-12-2007
Location: At the bench
Member Is Offline
Mood: No Mood
|
|
I haven't really been paying attention too much to this thread but nice work Magpie. It definately seems as though ball milling the mixture has had a
positive effect on the progress of the reaction. I guess this is kind of what you'd expect, although I'm suprised it isnt more subtle given that at
the reaction temp of 750*C its no longer a solid state reaction (everything should melt?!). Hopefully your chocolatey phosphorus will clean up nicely
without too much of a loss.
|
|
Strepta
Harmless
Posts: 44
Registered: 6-5-2004
Member Is Offline
Mood: No Mood
|
|
Magpie: Once again, nice job! you appear to be producing evidence that intimate mixing is the key to better yield, along with the unexpected slag
reduction. I'm very interested to see your next attempt (larger charge). Will you also ball-mill for 6 hours? You'll have to decide whether the extra
effort/time is worth the 20% increase or if it makes more sense to quickly mix and run a few morebatches at 42%. (U2U reply sent)
|
|
watson.fawkes
International Hazard
   
Posts: 2793
Registered: 16-8-2008
Member Is Offline
Mood: No Mood
|
|
Quote: Originally posted by Magpie  | The 62.9% yield is significantly higher than my previous best at 42.0% for run #8. So apparently the improved mixing and possibly finer particle size
provide significant advantage. Since all reactants should be liquid at 750C it seems that improved mixing would be the main factor responsible for
the increased yield. | One thing I find significant is that with finer particle size the character of the
bubble boundaries left in the slag is quite different. It seems to my eye that there's an interesting phase change happening. My guess is that with
the finer sizes the mixture becomes something like a colloid when it all melts, that is, having much higher interfacial surface area and significant
boundary energy. In such a mixture, the excess of Al you've been using may not need to be so large.
I would also caution directly comparing yield percentages between these later runs before purification. If indeed some of the initial reagent mixture
gets carried over, either unreacted or partially reacted, then it shouldn't count properly as yield. Determining that at this stage isn't obvious,
clearly. The first thing I'd try, assuming an infinitely equipped analytical lab (clearly an assumption contrary to fact), is to put the yield into a
heated centrifuge and see what separates.
|
|
blogfast25
International Hazard
   
Posts: 10562
Registered: 3-2-2008
Location: Neverland
Member Is Offline
Mood: No Mood
|
|
Magpie:
6 h of ball milling the reagent mixture must be a pain in the proverbials, but it does seem to have paid off very nicely: the increase in yield (I
second Watson’s motion, though) and spectacular decrease in slag volume do seem to open up the way to larger charges and better yields. Will soon we
see you produce 10 g (or more) of crude P per run? :-)
Since as the brown contamination seems to loosely correlate with the introduction of boria into the mix, could part of the contamination be amorphous
boron?
Another thought just occurred to me. Was the heating cycle used in all of the recent runs held rigorously the same? My reasoning is as follows.
Clearly the much larger volume of slag in the previous runs is due to foam. But if you maintain heat post-reaction, eventually and as long as the
material remains liquid the foam should collapse (faster so if the melt was of lower viscosity), even though that could take some time. If on the
other hand you shut off heat abruptly after reaction you’d ‘freeze’ the foam and prevent any possibility for it to collapse. Maintaining heat
post-reaction might thus be a way of reducing slag volume…
[Edited on 20-10-2012 by blogfast25]
|
|
Magpie
lab constructor
   
Posts: 5939
Registered: 1-11-2003
Location: USA
Member Is Offline
Mood: Chemistry: the subtle science.
|
|
Quote: Originally posted by Strepta  | I'm very interested to see your next attempt (larger charge). Will you also ball-mill for 6 hours? You'll have to decide whether the extra
effort/time is worth the 20% increase or if it makes more sense to quickly mix and run a few morebatches at 42%. |
Yes, I will ball mill for 6 hr. For routine production it's value would be a time & effort decision. At this point I'm mostly after the
knowledge of what works and what doesn't work. Actually ball milling is easy - the mill does all the work. You just have to babysit it a little -
while doing your regular activities. You just want to make sure it doesn't overheat or stop I guess, and I've never had any problems. I've already
proven this mix won't explode on me. You do have to pick the balls out (quickly, to keep moisture absorbtion to a minimum) and then clean and dry
everything when finished.
Quote: Originally posted by watson.fawkes  |
I would also caution directly comparing yield percentages between these later runs before purification. If indeed some of the initial reagent mixture
gets carried over, either unreacted or partially reacted, then it shouldn't count properly as yield. Determining that at this stage isn't obvious,
clearly. The first thing I'd try, assuming an infinitely equipped analytical lab (clearly an assumption contrary to fact), is to put the yield into a
heated centrifuge and see what separates. |
Yes, that last batch was very dirty - I would even call it crusty. Right now I'm cleaning it up and have removed the bulk of the contamination using
chromic acid. This will definitely decrease the yield from my reported 62%. I like your idea of the heated centrifuge. I will try just heating it
up to say 60C then giving it a spin in my unheated centrifuge.
I haven't dared hope for anything that large.
Quote: Originally posted by blogfast25  |
Since as the brown contamination seems to loosely correlate with the introduction of boria into the mix, could part of the contamination be amorphous
boron? |
I suppose it is the right color. You know better than I whether that is thermodynamically possible or even likely.
Quote: Originally posted by blogfast25  |
Another thought just occurred to me. Was the heating cycle used in all of the recent runs held rigorously the same? My reasoning is as follows.
Clearly the much larger volume of slag in the previous runs is due to foam. But if you maintain heat post-reaction, eventually and as long as the
material remains liquid the foam should collapse (faster so if the melt was of lower viscosity), even though that could take some time. If on the
other hand you shut off heat abruptly after reaction you’d ‘freeze’ the foam and prevent any possibility for it to collapse. Maintaining heat
post-reaction might thus be a way of reducing slag volume… |
The heating cycle is somewhat rigorous up to the time of ignition as it is controlled by the furnace and retort characteristics, ambient temperature,
and when I turn on the hood fan. When I turn off the furnace has been pretty much right after ignition since I started using boria. There's no point
in beating a dead horse.
The single most important condition for a successful synthesis is good mixing - Nicodem
|
|
blogfast25
International Hazard
   
Posts: 10562
Registered: 3-2-2008
Location: Neverland
Member Is Offline
Mood: No Mood
|
|
"There's no point in beating a dead horse."
Except perhaps as I suggest, to 'kill' the foam and obtain only a small amount of (more or less non-porous) slag.
|
|
Magpie
lab constructor
   
Posts: 5939
Registered: 1-11-2003
Location: USA
Member Is Offline
Mood: Chemistry: the subtle science.
|
|
I finished cleaning the crude phosphorus of run #9. I first used a chromic acid wash (K2Cr2O7/H2SO4) on a magnetic stirrer. Improved but still a bit
crusty, I heated the P to 65C then centrifuged it for 1 minute. This gave no separation. Finally, I heated the P in 6M HNO3 with agitation on a
magnetic stirrer/hotplate. This further cleaned it to where, although still off color, it now looks like phosphorus. This is shown below:
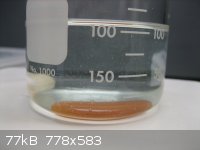
phosphorus from run #9, cleaned
Loss of weight due to cleaning was from 3.7g to 2.8g. %yield then decreased from 62.9% to 47.6%. This is still my best yield so far.
The single most important condition for a successful synthesis is good mixing - Nicodem
|
|
Magpie
lab constructor
   
Posts: 5939
Registered: 1-11-2003
Location: USA
Member Is Offline
Mood: Chemistry: the subtle science.
|
|
The P from runs #7 and #8 was also quite dirty so I decided to clean it also. My plan was to use a chromic acid wash followed by a 6M HNO3 wash, as I
did with the P from run #9. To my surprise the P was clean enough after just one wash with the chromic acid as can be seen below.
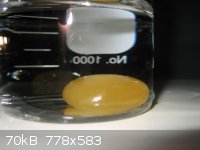
The reagent consisted of 20mL water + 20mL con H2SO4 + 2.25g K2Cr2O7. This was heated and stirred on a magnetic stirrer/hotplate, and the dirty P
added to it. This reagent turned from orange to a murky green/brown during the cleaning process.
The single most important condition for a successful synthesis is good mixing - Nicodem
|
|
White Yeti
National Hazard
  
Posts: 816
Registered: 20-7-2011
Location: Asperger's spectrum
Member Is Offline
Mood: delocalized
|
|
Just as a random query, wound zinc be a good reducing agent for this reaction? I'm thinking that it would be a strong enough reducing agent to reduce
phosphorus, but not silicon, thus potentially increasing yields. There's always the problem of producing zinc phosphide, but zinc phosphide has a
relatively low melting point, as does zinc metal itself, so if phosphide were to form, it would remain molten and available, perhaps for an oxidation
back to phosphorus. Perhaps it's worth a try; the reaction may even take place at lower temperatures owing to the lower MP of zinc.
"Ja, Kalzium, das ist alles!" -Otto Loewi
|
|
blogfast25
International Hazard
   
Posts: 10562
Registered: 3-2-2008
Location: Neverland
Member Is Offline
Mood: No Mood
|
|
Zn? It’s not very likely. Such aluminothermic reduction reactions are really driven by the huge heat of formation (HoF) of alumina (- 1676 kJ/mol).
The HoF of ZnO is only – 350.5 kJ/mol (NIST value). To be fair we have to compare 3 mol of ZnO with 1 mol of Al2O3, so 3 x (-350.5) = - 1051.5 kJ/3
mol. That’s still a lot lower than the competing value of - 1676 kJ/mol. From it can be deduced that the reduction with Al is much, much more
exothermic than with Zn (about 600 kJ difference is a huge difference).
|
|
Magpie
lab constructor
   
Posts: 5939
Registered: 1-11-2003
Location: USA
Member Is Offline
Mood: Chemistry: the subtle science.
|
|
Phosphorus run #10 was completed today. The charge was 52.7 g, with boria as slag former, and aluminum in 15% excess. The purpose of this run was to
evaluate the effect of running a larger ball milled charge vs the 36.3g ball milled charge of run #9.
The NaPO3 was first ground in a coffee grinder for 2 minutes. This was then mixed with boria and Al in a capped bottle. This mix was then ball
milled with ½” steel balls for 6.45 hours.
The paint can retort was lined with 87.1g of furnace cement. The liner was slowly cured up to 500F then the assembly was heated to 750C to burn off
the tin plating on the can and remove liner water. There was no bulging of the liner.
The loaded retort assembly was placed in the furnace and the thermostat set at 750C. At about 710C the reactants ignited. This resulted in an
explosive reaction – a scary event. The products shot out of the condenser, causing some water and bits of burning phosphorus to get knocked out
of the receiver. There was also the usual burning phosphine, and quite a lot of smoke. The silver solder rebuild on the condenser was virtually
ruined, apparently due to the intense heat developed. This can be seen in the picture below:
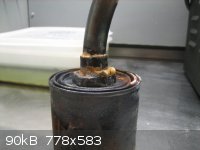
Fired retort, run #10
As on run #9, on opening the retort I found that there was hardly any slag. This confirms the much reduced volume of slag that occurs with the ball
milled charge.
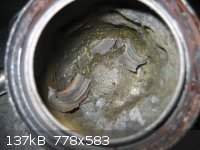
Retort slag, run #10
The slag, although sparse, did plug the snorkel, as shown below:
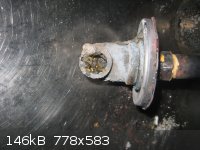
Plugged snorkel, run #10
Additional slag deposited on the outside of the snorkel is shown here:
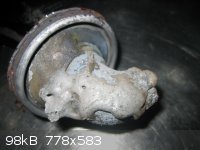
Slag on snorkel, run #10
The product was a very dirty looking rust colored P, as shown below:
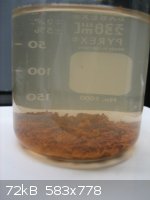
Dirty P, run #10
The P was cleaned in heated chromic acid followed by cleaning in heated 6M HNO3. The yield is 2.0g of P for a %yield of 23.0%. The cleaned P is
shown below:
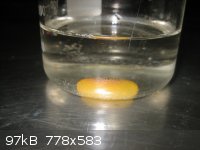
P, run #10
Weight loss of the reactor assembly was 445.4 – 442.3 = 3.1g.
Discussion
The results of run #9 showed that ball-milling increases the efficiency of the reaction. However, as shown by the results of run #10 the reaction of a
larger charge size is too powerful to be conducted safely.
Additionally, the yield and %yield were decreased due to the explosive discharge of the reaction. Much of the P was apparently deposited in the
condenser as I had to burn off a lot after the reaction during cleanup. I believe that much of the rust colored crud in the receiver is red P,
further contributing to the loss of yield.
A further danger was noted in that examination of the snorkel showed that it was plugged, or very nearly so, for this larger run.
Comments, questions, and suggestions are welcomed.
The single most important condition for a successful synthesis is good mixing - Nicodem
|
|
12AX7
Post Harlot
   
Posts: 4803
Registered: 8-3-2005
Location: oscillating
Member Is Offline
Mood: informative
|
|
Larger charges are better ran with coarser reactants, is this the case here as well?
The boria with excess aluminum may've contributed some exotherm.
Tim
|
|
Magpie
lab constructor
   
Posts: 5939
Registered: 1-11-2003
Location: USA
Member Is Offline
Mood: Chemistry: the subtle science.
|
|
See the results for run #8 above.
[Edited on 2-11-2012 by Magpie]
The single most important condition for a successful synthesis is good mixing - Nicodem
|
|
Pages:
1
..
40
41
42
43
44
..
60 |