Pages:
1
2
3
4 |
User
Hazard to Others
 
Posts: 339
Registered: 7-11-2008
Location: Earth
Member Is Offline
Mood: Passionate
|
|
That is indeed what I meant (english is not my native language).
The practical issue with this would be that one can not see what is actually going on, oke slightly inconvenient.
Could you try to sketch your idea for me?
Letting the tube shrink after being filled wouldnt be such a bad idea I guess.
Only it would be diffucult to get an even width , or maybe not with a jig around it...
Pressure could be applied while filling, and released afterwards..
(just trying to think out of the box here)
[Edited on 10-8-2011 by User]
What a fine day for chemistry this is.
|
|
Hennig Brand
International Hazard
   
Posts: 1284
Registered: 7-6-2009
Member Is Offline
Mood: No Mood
|
|
In the last two or three lines of the paragraph decribing jig construction, there is a basic description of a simple way to make a viewing slit/window
for the jig.
Here are a couple of simple diagrams done with Google Sketchup for the detcord Jig I had in mind. You will notice the jig is split down the middle so
that it can be taken apart to add tubing and remove finished cord. The three through holes are for threaded rod (ready rod) to go through. The ends of
the rods need wing nuts and washers, for easy tightening and loosening.
This should make what I was describing more clear.
note: The dimentions may need to be different, this is only to illustrate the concept.
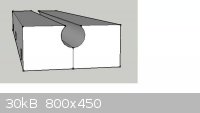
edit:
The channel for the tube probably shouldn' t have gone all the way through, or a butplate of some sort could be added on the far end. Also a plate on
the front end with a hole just big enough for the bore of the tube and perfectly aligned with it would lock in the tube from that end nicely as well.
[Edited on 10-8-2011 by Hennig Brand]
|
|
User
Hazard to Others
 
Posts: 339
Registered: 7-11-2008
Location: Earth
Member Is Offline
Mood: Passionate
|
|
I already thought you meant something like that 
Maybe a top plate made out of transparent plastic would provide a way to see whats going on inside...
I think this should work, plus it allows more pressure to be applied.
Filling proves to be time consuming and I am trying to come up with something that makes it easier, or at least quicker.
Things like using a jack came to mind, but i soon realized that this will also synthesize new problems along the road.
At least some substance that isnt completely solid(moldable) will make it much easier to fill, working with powder in this case seems impractical imo.
Or one could use a powder and add something like PGDN afterwards(also causing new problems on the way.)
Once again just spitting out some thoughts.
There has to be a better way... 
[Edited on 11-8-2011 by User]
What a fine day for chemistry this is.
|
|
AndersHoveland
Hazard to Other Members, due to repeated speculation and posting of untested highly dangerous procedures!
   
Posts: 1986
Registered: 2-3-2011
Member Is Offline
Mood: No Mood
|
|
Could thick, loosely woven cotton rope be nitrated to cellulose nitrate rope? Cellulose nitrate can actually be detonated, although its rapid
deflagration is more typical.
Vinylon rope, which is a form of polyvinyl alcohol, could also potentially be nitrated to polyvinyl nitrate, although this might not be as feasible
since vinylon is less porous than cotton.
Polyvinyl nitrate takes the form of tough white strands if the starting polymer had a high molecular weight. The detonation velocity is variable,
depending on density, but can be up to 6560 m/s. The substance was once used as a component in propellants.
synthesis from RS:
Over a period of 1 hour, very slowly add 5 g of finely pulverized polyvinyl alcohol (containing 10% moisture) to 100 mL of 99-100 nitric acid in a
250-mL beaker. The beaker should be in a salt-ice bath to provide cooling during the addition. Maintain constant stirring and a temperature of -8 °C
throughout the addition, and for an additional 2 hours after the addition. The resulting slurry is slowly drowned in an equal volume of ice water
while vigorously stirring. Filter this to collect the white powder that should have formed, wash the powder with water until neutral to litmus, then
put it in clean water for 12 hours. Repeat the washing and standing process using 95% ethyl alcohol, and again repeat the process with 12% sodium
bicarbonate solution. Finally, the powder is washed with water until neutral to litmus, dried in the open air, then in a vacuum desiccator. The yield
is about 96%. You will need a graduated cylinder for measuring liquids, a stirring rod or magnetic stirrer for mixing, and a thermometer to monitor
the temperature.
Supposedly, higher yields may be obtained by starting with polyvinyl acetate instead, and using more nitric acid.
If it works, nitrated polyvinyl rope may make for an ideal improvised det-cord, being both safer than most of the other alternatives, and very
durable/ convenient to work with.
http://www.tysonsriggers.co.uk/vinylon-rope
[Edited on 11-8-2011 by AndersHoveland]
I'm not saying let's go kill all the stupid people...I'm just saying lets remove all the warning labels and let the problem sort itself out.
|
|
Hennig Brand
International Hazard
   
Posts: 1284
Registered: 7-6-2009
Member Is Offline
Mood: No Mood
|
|
I just wanted to point out one thing about the drawing above. If the "tubing channel" in the jig is made to fit the tube perfectly or nearly
perfectly, the force due to static friction could be tremendous. Translation, if the thing is made well and is clamped down onto a meter of vinyl
tubing, the tubing isn't going anywhere under any normal working conditions.
I guess in that case the jig could be pretty much used the way it appears in the drawings above. It just needs a hopper. I would suggest pins or a
strip or something permanently attached to both sides of the jig that the hopper can slide down onto and off of. Actually what would be best is a
track (just something simple) so that when the hopper is slid into place it is locked in (can' t move up and down, or side to side).
This is a pretty sorry looking hopper, and the proportions of everything are off, but it shows a hopper sitting on the jig. As described earlier the
hopper should be able to be installed on the jig and removed easily. Once the tubing is in place and the jig tightened around it, the hopper is
installed. Once the cord is full, the hopper is removed and the jig can be loosened and the cord removed.
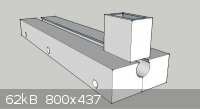
I know the diagram has inaccurate dimentions, however imagine a tube in the jig, and the hopper in place. A notch would have been cut out of the
tubing for the hopper to feed into, prior to installing the hopper.
I think once the tooling was made, loading the cord would be fairly pain free. If the tooling was made well, it would last a very long time and be
usful to load a meter or so of detcord at a time.
[Edited on 12-8-2011 by Hennig Brand]
|
|
Hennig Brand
International Hazard
   
Posts: 1284
Registered: 7-6-2009
Member Is Offline
Mood: No Mood
|
|
I have another idea that should increase safety greatly. A blast shield could be installed between the detcord jig and the operator. A viewing window
made of heavy plexiglass might be a good option for a viewing window in the shield. With a vibrating hopper and an explosive of the right crystal
structure it should feed itself with no need for the operator being involved with that part of the process at all. The operator just needs to stay
behind the blast shield and run the loading dowl. The dowl could still be a dangerous projectile if not kept in mind where it is pointed. A heavy
leather glove could be used to protect the operator' s hand, in the event of an accident were the dowl could fly out of his hand at high speed.
Though not shown, the jig and shield could be bolted down (or otherwise attached) to a table or base plate of some kind.
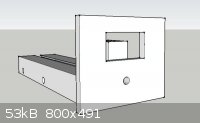
[Edited on 13-8-2011 by Hennig Brand]
|
|
Hennig Brand
International Hazard
   
Posts: 1284
Registered: 7-6-2009
Member Is Offline
Mood: No Mood
|
|
I guess I made the last couple of posts, but that was nearly two months ago, so I hope it is all right if I post again.
Here is a picture of my birch, 1/4" circular channel, 1 meter long detcord jig. It still needs a good hopper, and the vibrator out of an old cell
phone or something for the hopper, but it works very nicely.
The loading dowel slides in just as smooth as silk now. This is not only very
beneficial from a loading efficiency and loading ease perspective, but also from a safety perspective. Friction is very low now in comparison to what
it was using more improvised techniques. No matter how much time and care I put into taping the tubing onto a dowel, I never got it really straight
for loading. This gets it perfectly straight. Nothing is ever really perfect but, you get the idea, close enough for anyone.
I will get back with some detailed loading results.
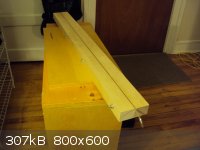
edit:
A material other than wood might have been better for the jig, maybe some kind of polymer/plastic. The birch was nice and dry, but with humidity
changes the wood could still bend and/or twist a certain amount. I guess I will find out in a while if wood was a good choice.
[Edited on 9-10-2011 by Hennig Brand]
|
|
quicksilver
International Hazard
   
Posts: 1820
Registered: 7-9-2005
Location: Inches from the keyboard....
Member Is Offline
Mood: ~-=SWINGS=-~
|
|
I was looking at that for a few minutes and it occurred to me that it would take a very unique polymer not to make a weak link at the seam. However if
you would construct TWO jigs; one slightly larger than the "core" unit and have THAT seam on the opposite side - you may work through the mechanics
of bending with a solid core [pressing against the seam].
Vinyl has always been a problem from a standpoint of longevity and elasticity, they also have a poor shelf life when under pressure, UV, &
retaining a bend. There may be other candidates for the tubing that could solve a lot of these issues.
I looked into the whole issue of a "weave machine" when we had originated this discussion re: fuse, cord, etc. I could only find the same run-of-the
mill industry machines until I looked into the development of fuse in history. The Japanese had that is today called a "Kumi Loom" that is perhaps
many hundreds of years old. It is designed to make a round hollow cord covering and was used in fuse and could certainly be applied to cover a
water-proof tube. The weaving is done by hand and is rather fast when one gets to understand who it's done. It would place a tight weaving which is
hollow around most any size flexible tube. This was actually the original method of hand-making time-fuse but any material could be substituted in an
inner tubular container. It could also be as long as one wished. And using the "sealed "inner tube" concept you illustrated, it may lend a great
degree of professionalism to the fuse as it would withstand any type of extreme bending.
|
|
Hennig Brand
International Hazard
   
Posts: 1284
Registered: 7-6-2009
Member Is Offline
Mood: No Mood
|
|
Yeah, the jig is a little vulnerable at the upper edge where the tubing meets it on both sides. I plan on gluing a strip of something (wood?) on both
sides to strengthen those edges. This will make those edges stronger and will not interfere with the assembly or disassembly of the jig, when
inserting tubing or removing cord.
The main purpose of the jig is to hold the tubing perfectly straight while incrementally press loading the explosive filler. The density of the
explosive filler is normally much less (around 1-1.2 g/cc ?), than what it is for a blasting cap. I found that it was not a problem to get the
explosive filler up to the required density even without the jig when using the dowel and tape method.
Vinyl is definitely an inferior material relative to what the professional cord is made from. It is not as easy to tie, it does not have as much
tensile strength, it is sensitive to UV radiation and probably some more problems that I haven't thought of. Vinyl is however readily available and
the cord made from it is capable of the same main functions as the professional variety, ( I think).
Edit:
BTW, the jig was left bulky in the hope that a more substantial piece of wood, would be less likely to twist and bend from humidity changes.
[Edited on 11-10-2011 by Hennig Brand]
|
|
quicksilver
International Hazard
   
Posts: 1820
Registered: 7-9-2005
Location: Inches from the keyboard....
Member Is Offline
Mood: ~-=SWINGS=-~
|
|
I am interested to see whether it functions (seals). I only wish I knew of a commercial platform for experimentation and further development. I had
looked quite a bit once and didn't find any commercial "flexible tubular binding".
[Edited on 12-10-2011 by quicksilver]
|
|
Hennig Brand
International Hazard
   
Posts: 1284
Registered: 7-6-2009
Member Is Offline
Mood: No Mood
|
|
I am not sure I know exactly what you are saying. I do think that you are putting too much significance on the tubing/cord material. I think the
explosive core is the most important component, which has the most influence over the function of the detcord.
In my previous post I said that the jig's main function is to hold the tubing straight. I left something out; it also provides a stable platform from
which to work and to install a hopper for the explosive feed.
I also don't think that the UV sensitivity thing is a big deal because for most hobbyist detcord applications the exposure would be limited. It is not
good practise to expose explosive materials to UV radiation for any significant length of time anyway. If a cord resistant to the effects of UV
radiation was desired, I imagine a suitable coating could be found.
As was already mentioned in this thread the tensile strength of vinyl tubing is less than the professional cord material, however it is still high
enough for any normal use. Unless of course you require that your detcord double as parachute cord or climbing rope.
I think the biggest limitation of the vinyl tubing detcord is that it does not tie as easily as the professional material.
[Edited on 13-10-2011 by Hennig Brand]
|
|
quicksilver
International Hazard
   
Posts: 1820
Registered: 7-9-2005
Location: Inches from the keyboard....
Member Is Offline
Mood: ~-=SWINGS=-~
|
|
Hennig Brand: This is the patent from the polymer extruded det cord concept.
There are some concepts that are fairly cutting edge here Du Pont purchased it (or subsidized the research). The element was simple start from a
single micron level powder-crystal, polymerize and extrude.
They could go up to ten grains per foot. It's from 1983. It uses concepts from British Pat. No. 815,534 and U.S. Pat. No. 3,311,056
which was a flexible sheath of a thermoplastic polymer (could an existing vinyl be a fast stand in???).
It was a very interesting idea. Extruding nozzle concepts also illustrated.
Attachment: det-cord_4369688_full.pdf (1.2MB) This file has been downloaded 825 times
|
|
Hennig Brand
International Hazard
   
Posts: 1284
Registered: 7-6-2009
Member Is Offline
Mood: No Mood
|
|
Thanks Quicksilver, that detcord patent is very interesting. I am not up to that level of sophistication when it comes to detcord manufacture. Even
making a detonating cord as small as the patent proposes would be next to impossible by most normal means. Also ETN probably wouldn't work nearly as
well as PETN in a small diameter low energy detcord.
Vinyl is often called the world’s most versatile plastic. Vinyl in one form or another has been used for so many different things that it boggles
the mind. I imagine that a suitable form of vinyl could be found for your low energy detcord, one with the right melting point, stiffness and
durability. There would undoubtedly be forms of vinyl much more appropriate for detcord manufacture than the soft vinyl tubing obtained from hardware
stores.
|
|
quicksilver
International Hazard
   
Posts: 1820
Registered: 7-9-2005
Location: Inches from the keyboard....
Member Is Offline
Mood: ~-=SWINGS=-~
|
|
No problem. When I first looked at polymer chemistry I winced but you'd be surprised how eventually all the "little things" add up. I (generally)
still have to keep a book open when reading a lengthy dialog in come patents, etc but they make more and more sense as time goes on. I do think you're
on to something with the vinyl concept.
|
|
Hennig Brand
International Hazard
   
Posts: 1284
Registered: 7-6-2009
Member Is Offline
Mood: No Mood
|
|
Well, I have what I think is a reasonably good detcord jig. I am still pondering about what to do for a hopper. In the following pictures is shown a
much improvised hopper made from cardboard and tape (very temporary).
When comparing to the picture I posted a few posts ago, it can be seen that a strip of maple has since been glued to the top of each half of the jig
and cut at an angle to make a V-groove above the tubing channel.
In the pictures above I only had ~10g of ETN to load, which gave me a little more than 2/3 of a meter of detcord. At 1g/m loading density (which is
approximately what I have been loading at) my 0.17" ID vinyl tubing has over 14.6g of ETN per m of cord length.
I can load a meter of detcord in ~20minutes (not counting setting up for loading, removing cord, etc). I am sure I can do it much more quickly once I
figure out a few more things.
A few observations in regards to the hopper. I found while loading the detcord that simply putting a spoonful of ETN into the V-groove over the
cut-out notch in the tubing and coaxing the ETN into the tubing with a bamboo skewer while operating the loading dowel was probably more efficient
than the cardboard hopper thing. The cardboard hopper was improvised and not well thought out.
Here are a few pictures I took yesterday while loading ~2/3 of a meter of cord for fun.
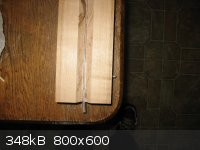
[Edited on 13-11-2011 by Hennig Brand]
|
|
Jimbo Jones
Hazard to Others
 
Posts: 102
Registered: 15-10-2009
Member Is Offline
Mood: No Mood
|
|
Nice work! Why not a funnel and vertical setup?
|
|
Hennig Brand
International Hazard
   
Posts: 1284
Registered: 7-6-2009
Member Is Offline
Mood: No Mood
|
|
Thanks,
There are many reasons, but for now I will say that this horizontal set-up allows greater control over the loading process and consequently the
specifications of the finished cord. By loading the tubing this way it is easy to control the size of each increment pressed into the tube as well as
maintain a uniform charge density.
There may be a vertical set-up that also works well, but so far I have not seen one that facilitates the loading process like this does.
Think about the ergonomics of a horizontal system versus a vertical system. I can set this up at waist height, on a sturdy flat surface, and the
loading motion is a very easy natural motion for the body.
The support provided by the jig allows me to increase the density beyond what would normally be possible.
The biggest benefit of a jig, as I see it, is that it holds the tubing perfectly straight while loading (I suppose a vertical jig would also do this).
I think it is intuitive to think that a vertical setup would take advantage of gravity, when in fact gravity just causes problems like loss of control
(I think).
There are more things to consider, but those are a few things off the top of my head. There may be a good way to do a vertical system that I haven’t
thought of.
[Edited on 13-11-2011 by Hennig Brand]
|
|
Jimbo Jones
Hazard to Others
 
Posts: 102
Registered: 15-10-2009
Member Is Offline
Mood: No Mood
|
|
I see your points. The idea was that in vertical position the jig will be very efficient for small scale gravity press. The funnel act as dispenser.
Put the maximum amount powder explosive, than press with suitable weight to get uniform density.
|
|
Hennig Brand
International Hazard
   
Posts: 1284
Registered: 7-6-2009
Member Is Offline
Mood: No Mood
|
|
In order to get uniform density the charge must be incrementally pressed into the cord, the smaller the increments the better the uniformity. Without
incremental loading it would also be impossible to achieve a high enough overall charge density let alone uniformity.
If a screw-conveyor type loading system could be setup that would be perfect I think. One turn of the crank giving the exact quantity of explosive
desired, (adjustable of course), then press it home with the loading dowel. With a little ingenuity a screw conveyor could also be automated so that
every time the loading dowel was pulled back a sensor would signal the screw conveyor to push out another charge. Of course it would need to be
designed in such a way that friction was reduced to an acceptable level.
Anyway, I had to test that bit of cord I made, so I went into the back yard to find a victim. I found an aspen tree, which was about 3.5 inches in
diameter (from the picture with the measuring tape it looks a little smaller than it is). The 2/3 meter of detcord had ~9.5g of ETN in it at ~ 1g/cc.
It was wrapped tightly on the tree and held in place with some electrical tape (I went a little over board with the tape).
It was getting dark during the 15 minutes I was at this, which is why the last pictures are darker.
I should have picked a bigger tree because the explosion cut the tree off the stump like it was a twig.
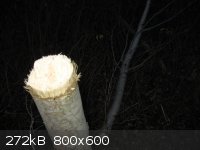
[Edited on 15-11-2011 by Hennig Brand]
|
|
Hennig Brand
International Hazard
   
Posts: 1284
Registered: 7-6-2009
Member Is Offline
Mood: No Mood
|
|
I have a small note to add regarding the loading dowel. The inside diameter of the vinyl tubing I am using is 0.17 inches, but all the common dowel
sizes are either quite a bit too small or too large. I have been using a 1/8" loading dowel which was the most suitable thing I found on the store
shelves, but loading with it was tedious with often as much as half the powder slipping by the tip of the dowel during a loading stroke. I noticed the
old cannon ram-rods were often a long rod which was considerably smaller in diameter than the bore of the cannon and only the last bit of the rod was
close to (but not quite) the size of the bore. It is hard to get a perfectly straight dowel especially in very small diameters, and even if you found
one it wouldn't stay straight for long. Using a smaller diameter dowel for the bulk of the length of the rod makes a perfectly straight rod much less
necessary, as well as reducing the overall frictional forces (greater ease of loading and greater safety).
You could get an oversized dowel and turn, or otherwise remove material until you had the diameter you wanted for the rod and the plunger end, but I
found a simpler way. BTW, this would probably be obvious for anyone used to working with wood, but not me. I took the 1/8" long dowel that I had been
using to load with all along and a short piece of oversized dowel which I drilled a 1/8" socket into, wood glue was applied to both the end of the
long rod and the socket of the short piece and then the two were jammed together. After the glue had cured, a drummel type rotary tool with a grind
stone bit was used to sand down the short plunger tip until it was just a little smaller than the inside diameter of the vinyl tubing. A picture of
the new dowel plunger tip is included below.
BTW, loading a meter of cord in 15-20 minutes is quite possible now. I didn't time the last loading with the new rod tip, but it was quite straight
forward.
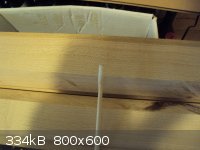
[Edited on 21-11-2011 by Hennig Brand]
|
|
Hennig Brand
International Hazard
   
Posts: 1284
Registered: 7-6-2009
Member Is Offline
Mood: No Mood
|
|
This will be the last post for a while in this thread, because I am mostly talking to myself, and my repeat posting is probably aggravating others.
I have a couple more things of interest to report. It was mentioned to me that detcord in 1 m lengths was of limited usefulness. While I disagree in
general, I do think that longer lengths could be useful for certain applications.
The first idea is simply to double up or kink 2 m of tubing then load one end in the jig before flipping it around straightening the tubing out again
and loading from the other end to give 2 m of detcord. A picture of the jig with 2 m of tubing clamped in the middle with a paper clamp is shown in
the picture below. BTW, this idea of doubling up tubing in order to load a double length was mentioned in passing in another detcord thread by the
forum member Marsh back in 2007. I think he would have had a hell of a time with a 2 m rod however, in my opinion 1 m is already pushing it.
Quote: |
Of course you could kink a 4m tube in the middle, pack with a 2m rod, unkink and then pack from the other end for a 4m length of detcord.
|
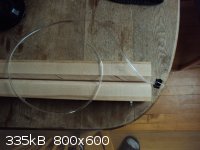
The second idea allows one to make as long a length of cord as they want. I recently discovered that vinyl tubing can be glued with PVC
cement/solvent. Couplings for the detcord can be easily made for about $0.02 each from short pieces of vinyl tubing that has an inside diameter the
same as the outside diameter as the detcord (1/4” in my case). I have included a couple of pictures which demonstrate the strength of the joint, as
well as a picture of a 2 m length of detcord made from two 1 m long pieces coupled together. In the strength test the tubing used was only 3/16”
outside diameter, with one side glued with PVC cement and the other glued with PVC to ABS transition cement. The PVC cement joint failed while holding
up half of the 50 lb load for ~3 seconds. When destructive testing the PVC to ABS transition glued joint, it was the tubing and not the glued joint
that eventually failed.
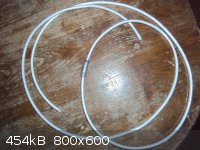
In a strength test I did on tubing glued with the PVC to ABS transition solvent /glue it was the tubing which eventually failed, not the glue. The PVC
to ABS transition glue may be the way to go. Keep in mind that I have only done a couple of simple tests. Anyway, I doubt I will ever be pulling on my
detcord with even 25 lbs of force.
For best results the pieces to be glued should probably be sanded a bit so that there is room for the solvent/glue to get between the two pieces. I
have found that the inside and outside diameters often match so closely that sliding them together removes most of the glue and produces a weaker
joint. This could be one of the biggest reasons for some of my joints having much greater strength than others.
BTW, when shopping for tubing make sure it has as close as possible to a perfectly circular cross section from end to end. I mistakenly bought some
tubing recently that was flattened out and twisted a bit (must have gone on the roll hot), and it was a nightmare to load.
[Edited on 27-11-2011 by Hennig Brand]
|
|
Jimbo Jones
Hazard to Others
 
Posts: 102
Registered: 15-10-2009
Member Is Offline
Mood: No Mood
|
|
Keep talking.
Nice work as always. The idea for the joints was good move. In mine tests I used strong duct tape, but the vinyl joint make the finished product way
more durable. Congratulations!
“In order to get uniform density the charge must be incrementally pressed into the cord, the smaller the increments the better the uniformity.
Without incremental loading it would also be impossible to achieve a high enough overall charge density let alone uniformity.”
I just read your previous post. The idea was to load the maxim amount powder explosive, which allowed seamlessly movement of the dowel. Than press
with suitable weight to get the desired density. Than repeat the process again and again…..
[Edited on 27-11-2011 by Jimbo Jones]
|
|
Hennig Brand
International Hazard
   
Posts: 1284
Registered: 7-6-2009
Member Is Offline
Mood: No Mood
|
|
Thanks for the approval.
Sounds like you have the right idea regarding loading, I was (initially) just a little unsure of what you meant in your previous post. As you say, a
vertical setup with weight would provide for a consistent applied force time after time. This is a feature of the vertical setup that I do appreciate.
There are probably at least "a couple different ways to skin the cat".
[Edited on 27-11-2011 by Hennig Brand]
|
|
Pages:
1
2
3
4 |