Pages:
1
..
36
37
38
39
40
..
60 |
Rogeryermaw
National Hazard
  
Posts: 656
Registered: 18-8-2010
Member Is Offline
Mood: No Mood
|
|
Quote: Originally posted by White Yeti  | I'm not sure if this has already been discussed, but is trisodium phosphate a suitable replacement to sodium hexametaphosphate?
|
i don't see why not. there is more sodium to account for and sometimes it comes as the hydrated form which you absolutely must dry (don't want any
hydrogen source in your reactants) but otherwise, it should be as feasible as 6(NaPO3).
|
|
learningChem
Hazard to Others
 
Posts: 182
Registered: 21-7-2011
Member Is Offline
Mood: No Mood
|
|
Success!!
experiment :
I mixed 1.7g sodium hexametaphosphate, 0.7g Al and 0.5g of something that is sold as "quartz". All three substances where already 'fine' powders when
I bought them. I didn't grind anything. The powdered Al is not pyrotechnic grade as far as I can tell - I'm assuming pyrotechnic Al is black? This
one would make your fingers silvery if you touched it.
I put half of the mix (~1.5g) in a 15cm test tube, plugged it with that yellow stuff which is supposed to be glass wool (but yellow? why?) and wrapped
a bit of wet cloth at the top.
Heated the stuff for something like 10-15 seconds. The mixture started to glow red and expanded somehwat. It took 3 or 4 more seconds for the
reaction to complete and the test tube to almost melt, as can be seen in the picture.
I put the test tube in a dark room and could see it faintly glow. Now a few hours have passed and the glow is almost invisible.
Not sure what to do next...
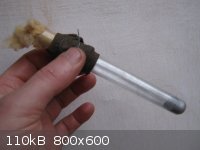 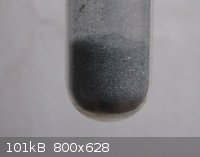
|
|
Strepta
Harmless
Posts: 44
Registered: 6-5-2004
Member Is Offline
Mood: No Mood
|
|
Congratulations learningChem. What to do next? Try heating the bottom of the test tube and forcing the free P toward the cooler end where it should
condense if the wet cloth is kept cool. The P which accumulates at the open end can be removed with a flat spatula and stored under water. Since you
are not using an inert atmosphere but a plug of glass wool, oxygen will diffuse through and consume your hard-won product!
Words of caution: this is not an experiment which should be done indoors without proper ventilation (preferably with an efficient fume hood). Also,
you are handling the test tube after the experiment without appropriate protection for your hands--be advised that white/yellow phorphous burns are
particularly nasty and painful.
|
|
learningChem
Hazard to Others
 
Posts: 182
Registered: 21-7-2011
Member Is Offline
Mood: No Mood
|
|
Hi Strepta! Thanks for your message.
I did the reaction outdoors and I kept/keep the tube outside as well. Hopefully none of my cats will try to eat it =P
I saw in your paper how you drive out the P. Quite neat.
What I'm wondering is, if I do that, what happens then when I take the plug out? Will the phosphorous catch fire at once? Or will I have time enough
to put it under water?
As to protection, I have some nitrile gloves. Are they OK for P?
|
|
Strepta
Harmless
Posts: 44
Registered: 6-5-2004
Member Is Offline
Mood: No Mood
|
|
What happens when you take the plug out seems to mostly depend on the temperature of the P. If it's warmer than ambient, it is more likely to inflame.
Why not remove the plug under water and eliminate the concern?
As regards gloves, remember the hazard is twofold with P--tendency to inflame and toxicity. Any gloves you have should not be tight fitting in case
you need to remove them quickly. A bucket of water at hand is a must--you can always immerse them in water. Tidiness is also important--clean up your
work area after experimenting to avoid having any missed particles inflame after you've left. I used to wave a torch over my ceramic work surface to
"clean up" any missed P.
|
|
learningChem
Hazard to Others
 
Posts: 182
Registered: 21-7-2011
Member Is Offline
Mood: No Mood
|
|
>Why not remove the plug under water and eliminate the concern?
Yes. That's probably the best idea. I wasn't keen on doing that because manipulation seems a bit harder under water, yet it's probably the best
solution.
As to gloves, I didn't feel at ease using them because as you noted they can't be taken off quickly.
Thanks for all the info! It's much appreciated. Soo, I'm off to the 'lab'...
|
|
Magpie
lab constructor
   
Posts: 5939
Registered: 1-11-2003
Location: USA
Member Is Offline
Mood: Chemistry: the subtle science.
|
|
Here's the results of my testing yesterday using a retort made from 3/4" EMT (steel electrical conduit). The retort is shown below.
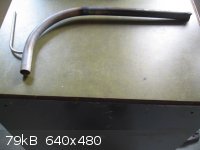
EMT retort
The closed end is about 14" long and the remainder is about 7" long. I first soaked the conduit in 6N HCl in an attempt to remove the zinc coating.
I don't think it all came off. I'm not sure why. The tube was bent to a 90 degree angle using a tubing bender. The long end was closed in a vice
then welded shut. A piece of 1/4" ss tubing was then welded to the short end.
Stoichiometric quantities of NaPO3, Al, and SiO2 were then ground together in a mortar. Basis was 6.4g of P. This powder was poured into the retort.
The retort was then placed in a tube furnace. The receiver beaker contained water which was maintained at a temperature of 50-60C using a hotplate.
Submergence of the retort outlet was 1.5". Argon was led to the retort using the 1/4" ss tube, as shown below.
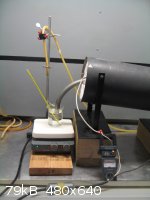
EMT retort in furnace
Run log:
t=0 min: Set furnace current I= 6.5a.
t= 32 min: Steady bubble generation due to heatup.
t= 51 min: Turned on argon bubbler. T= 419C. Turned on hood fan. Set I = 7a.
t= 67 min: T=539C.
t= 72 min: Smoke coming off receiver now. T=572C.
t=74 min: T= 597C. Smoke and phosphorus vapor burning at receiver water surface. No pops heard.
t= 75 min: phosphorus drops falling into receiver now. Only about 7 drops came over, basically all at once.
t=102 min: Still just smoky puffs. T= 772C. I=8a.
t= 142 min: T= 1055C. Managed to tease a few more drops out by introducing the argon very slowly.
t= 147 min: Turned off furnace.
The drops of white phosphorus can be seen in the picture below.
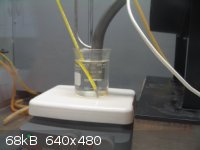
P in water receiver.
Today the receiver was heated to 45C, melting the drops of P. They were easily consolidated by pushing them together with the end of a thermometer.
The product weight was 1.2g for a yield = (1.2/6.4)100 = 19%.
Discussion & Analysis
The boiling point of white phosphorus is 280.5C and its freezing point is 44.2C. Based on my earlier tests with a ceramic retort and glass condenser
it seemed that the condenser was too cold as most of the P was subliming onto its internal surface. Therefore, I theorized that a metallic retort
might be an improvement in that the condenser temperature would likely be suitable for condensation but above the freezing point. Some dry run
testing with an empty retort confirmed this. Temperatures above 44.2C could further be assured by keeping the water in the receiver in the range of
50-60C. Taking a lesson from Rogermeryaw I constructed the above described steel retort using EMT.
When the drops of P came raining over I first thought that I had finally found a good system. However, this high production spike was short-lived.
After that the P4 vapor just continued to puff out and burn at the receiver water surface. When the hood light was turned out a green glow was
visible in the puffs.
My hypothesis for why the puffs of P4 are not condensing is as follows: the P4 vapor is simply not concentrated enough in the argon gas to reach
saturation & thereby condense. This is exactly analogous to why rain does not form in damp air until the water concentration
(humidity) is high enough. The P4 is carried by argon to the surface of the water in the receiver where it now contacts oxygen and burns giving the
green glow and white smoke.
So, this method for producing phosphorus seems to have the serious limitation of only producing yields in the vicinity of 20%. This doesn't seem to
have near as much to do with condenser design as it does with the chemical reaction itself. That is, we are using a dry powder with no agitation that
produces a viscous slag. I believe that this inherently gives poor yields and that we would find that most of the phosphorus remains locked in the
slag.
Please provide any questions, comments, or suggestions that you may have.
[Edited on 16-7-2012 by Magpie]
[Edited on 16-7-2012 by Magpie]
[Edited on 16-7-2012 by Magpie]
[Edited on 16-7-2012 by Magpie]
[Edited on 17-7-2012 by Magpie]
The single most important condition for a successful synthesis is good mixing - Nicodem
|
|
blogfast25
International Hazard
   
Posts: 10562
Registered: 3-2-2008
Location: Neverland
Member Is Offline
Mood: No Mood
|
|
It would be interesting to digest the slag (I know: it's a very hard material to grind down) to check for phosporus.
Are you sure Ar is really needed? If the free volume in the reactor is small enough the oxygen present should be 'mopped up' by the first P. Even 24 L
of air (STP) is only about 0.2 mol of O2...
Edit:
But I’m not convinced that the viscosity of the slag really is a problem, based on a single experiment of mine described way up above.
I filled a steel shot measuring cup (for measuring 1 fl.oz. of spirits in bars and restaurants) with the right mixture of NaPO3, Al and SiO2 and
simply heated it on the smallest flame of my lab gas cooker. When the bottom of the crucible began to glow dull red/brown, the reaction started and
jets of P2O5 (burning P) streamed out. I shut down the gas and the reaction seemed to continue, self-sustainingly. My IMPRESSION was that the reaction
ran to completion.
[Edited on 17-7-2012 by blogfast25]
|
|
Magpie
lab constructor
   
Posts: 5939
Registered: 1-11-2003
Location: USA
Member Is Offline
Mood: Chemistry: the subtle science.
|
|
Quote: Originally posted by blogfast25  | It would be interesting to digest the slag (I know: it's a very hard material to grind down) to check for phosporus.
|
Yes, that would be very enlightening. I'm not sure how that could be done.
Quote: Originally posted by blogfast25  |
Are you sure Ar is really needed? If the free volume in the reactor is small enough the oxygen present should be 'mopped up' by the first P. Even 24 L
of air (STP) is only about 0.2 mol of O2...
|
I agree that the Ar is likely not needed to prevent consumption of phosphorus. I had it cut way back to just barely provide a bubble. It's mostly
for my peace of mind that I'm not going to get a suckback.
Quote: Originally posted by blogfast25  |
But I’m not convinced that the viscosity of the slag really is a problem, based on a single experiment of mine described way up above.
I filled a steel shot measuring cup (for measuring 1 fl.oz. of spirits in bars and restaurants) with the right mixture of NaPO3, Al and SiO2 and
simply heated it on the smallest flame of my lab gas cooker. When the bottom of the crucible began to glow dull red/brown, the reaction started and
jets of P2O5 (burning P) streamed out. I shut down the gas and the reaction seemed to continue, self-sustainingly. My IMPRESSION was that the reaction
ran to completion.
|
Those are interesting results. Perhaps a vertical retort would be an improvement on my horizontal retort.
I feel that more such "test tube" experiments are needed to find better retort designs and perhaps better reactants.
[Edited on 17-7-2012 by Magpie]
The single most important condition for a successful synthesis is good mixing - Nicodem
|
|
blogfast25
International Hazard
   
Posts: 10562
Registered: 3-2-2008
Location: Neverland
Member Is Offline
Mood: No Mood
|
|
Prolonged boiling in conc. H2SO4 of the ground up slag should get any remaining phosphates in the watery phase. But grinding that slag, going by what
I saw, would be punishing. Then neutralise with NaOH and filter. Demonstrate phosphate with ammonium orthomolybdate.
|
|
Magpie
lab constructor
   
Posts: 5939
Registered: 1-11-2003
Location: USA
Member Is Offline
Mood: Chemistry: the subtle science.
|
|
I also find a test for phosphate using a "magnesia mixture" (MgCl2, NH4Cl, and aqueous ammonia). This solution, added to a slightly acidic solution of
the unknown, will form a white precipitate of crystalline magnesium ammonium phosphate.
But this is a qualitative test and I'm not sure of what value that would be.
The single most important condition for a successful synthesis is good mixing - Nicodem
|
|
Endimion17
International Hazard
   
Posts: 1468
Registered: 17-7-2011
Location: shores of a solar sea
Member Is Offline
Mood: speeding through time at the rate of 1 second per second
|
|
I'm trying to purify my batch. I made a dilute solution of chromic acid and melted phosphorus in it, in a beaker to use a larger surface area. As
noted, it remained molten at room temperature, but after several hours the surface got yellow precipitate, and the orange solution right above the
melt is darker, which is obviously reduced chromium.
I will leave it in the dark for several days, molten.
BTW, if you're making WP from RP, be sure to mix it with some fine quartz sand. It helps with the bumping a lot.
edit: I've set aside one smaller batch (roughly 3.9 g) and as I write this, it's being stirred molten (<60 °C), under 15% nitric acid. It's constantly being dispersed into small beads and I think it's getting less and less
orange, and going towards yellow. I'll let it go for an hour or two.
Meanwhile, there's progress with the batch being purified with chromic acid. The precipitate is half gone.
[Edited on 27-7-2012 by Endimion17]
|
|
Endimion17
International Hazard
   
Posts: 1468
Registered: 17-7-2011
Location: shores of a solar sea
Member Is Offline
Mood: speeding through time at the rate of 1 second per second
|
|
Success.
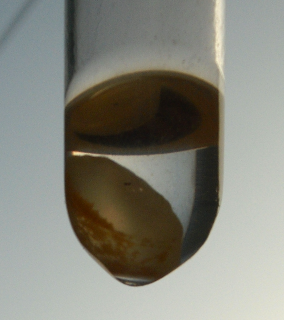
This is only a small part of the pure batch. Here you can see it resting in benzene.
The melt was completely transparent and I had quite a bit of trouble solidifying it. It took some ice and poking to finally do it. It looks like a
piece of pale amber and compared to the impure samples, the glow is even more powerful.
There's still this orange gunk sediment (probably a variety of red allotrope). However, the chromic acid method seems to be slowly eating it in the
mentioned, stil molten batch, so I suppose that if the chromic acid method preceeds the nitric acid swirling bath, one might obtain a nearly
transparent block of slightly yellow allotrope.
I'm quite excited, I've never made so much pure WP. The glow is enchanting and I'm trying to find a way to capture it properly.
The final purification is vacuum distillation in the dark, which should produce transparent and colorless WP, its true form. Unfortunatelly, I don't
have the equipment.
[Edited on 27-7-2012 by Endimion17]
|
|
learningChem
Hazard to Others
 
Posts: 182
Registered: 21-7-2011
Member Is Offline
Mood: No Mood
|
|
My experiment was a failure of sorts after all - I couldn't extract much P from reaction mix - I'm not even sure if the orange stuff that coated the
walls of the tube was P? Anyway, here are some pictures of the slag. There doesn't seem to be any P in it?
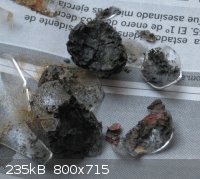 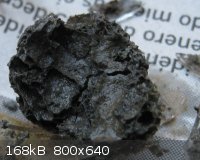
|
|
Magpie
lab constructor
   
Posts: 5939
Registered: 1-11-2003
Location: USA
Member Is Offline
Mood: Chemistry: the subtle science.
|
|
I'm going to try a new retort design for making phosphorus. Initially at least I will use the now popular Al/SiO2/NaPO3 recipe firing to about 700C.
The retort will be fired in a muffle furnace from which I have removed the door. The door is now replaced with a shaped insulating firebrick as shown
in the picture below.
The retort consists of a 1/2 pint (250ml) paint can and a section of curved 1/2" EMT (steel) pipe. The special connection of the pipe to the can lid
allows easy removal of the lid. Hopefully this will allow the pipe piece to be reused for many firings.
I just finished pre-firing the assembly to 700C to burn off the can's tin coating. The fired pieces are shown in the other picture below.
A concern I have is the cleaning of the pipe piece following its use. I believe that it will have some internal phosphorus contamination, both white
and red. What I want to be able to do is to clean the pipe so that it can be safely handled, with gloves, during reassembly for reuse.
I'm assuming that any white phosphorus will be quickly converted to P2O5 upon contact with oxygen. This then should dissolve in water and be pretty
much harmless. The red phosphorous will likely remain unchanged, however.
Ideally the pipe piece could be soaked in a solution that would convert the red phosphorus to harmless products such as a phosphate. Any
recommendations for how to do this are greatly appreciated.
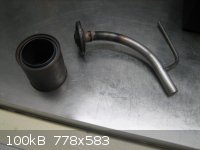
[Edited on 25-8-2012 by Magpie]
The single most important condition for a successful synthesis is good mixing - Nicodem
|
|
Rogeryermaw
National Hazard
  
Posts: 656
Registered: 18-8-2010
Member Is Offline
Mood: No Mood
|
|
you may also consider insulation/ torch/ heating wire to keep your downpipe at a temp sufficient to keep your product in the vapor phase. this should
help to minimize losses and dangerous residue in the pipe. elemental phosphorus scavenges a good deal of oxygen, so i have concerns that, if a residue
were to build up, it may not all oxidize to P2O5. love your design though. looks like it may be able to produce much larger quantities in a single run
than we have seen up till now.
i will say that in my experiments, i have not had the issue of a buildup in any of the surfaces of the reactor or piping. YMMV. can't wait to see how
it goes. best of luck magpie!
of course, for cleaning, you know CS2 is about the best solvent for phosphorus. it is only very slightly soluble in benzene and may be helped along
with a long bottle brush or carboy brush.
[Edited on 28-8-2012 by Rogeryermaw]
|
|
Magpie
lab constructor
   
Posts: 5939
Registered: 1-11-2003
Location: USA
Member Is Offline
Mood: Chemistry: the subtle science.
|
|
Thanks Roger for your helpful comments.
I had not considered keeping the P in the vapor state. My goal has been to keep it liquid. The thermal conductivity of the steel pipe seems good
for that based on my previous run.
My intent is to not permit any unsafe buildup of P on the internal (or external) surfaces of the pipe piece. I agree that it would be nice to give it
a good soak/scrub with CS2 but I have none.
The best approach I have come up with so far is to soak it in a caustic bath (say 10% NaOH), scrub with a ss wire brush, follow with a caustic rinse,
and finally do a water rinse. I will be trying my best to keep liquid waste at a minimum.
The 10% aqueous NaOH should convert the P to PH3. By doing this in my hood I should be able to safely vent off the PH3.
Reuse of the pipe piece is essential to the economics of this method. This piece is expensive as it was fabricated by SCWIM (skilled craftsman who
isn't me).
Further suggestions and comments are welcomed.
The single most important condition for a successful synthesis is good mixing - Nicodem
|
|
watson.fawkes
International Hazard
   
Posts: 2793
Registered: 16-8-2008
Member Is Offline
Mood: No Mood
|
|
Quote: Originally posted by Magpie  | I had not considered keeping the P in the vapor state. My goal has been to keep it liquid. The thermal conductivity of the steel pipe seems good
for that based on my previous run.
My intent is to not permit any unsafe buildup of P on the internal (or external) surfaces of the pipe piece. I agree that it would be nice to give it
a good soak/scrub with CS2 but I have none. | I've been thinking over issues involved in high-temperature
condensers, and while you don't have an explicit condenser here, you do have a de facto one. My original motivating example was a miniature
CS2 plant, where you've got the issue that generally there's going to be some sulfur that you want to be under reflux and not escaping with the
product, condensing in the product pipe and eventually clogging it. Similar concerns apply to other (semi-crazy) ideas such as mercury purification
stills and phosphorus production. Clearly these won't apply to your present effort, since it's already fabricated. Therefore, FWIW:You want the wall temperature of the condensing chamber above the condensation point and the condenser to be below it. This allows
you to control where the condensate goes. In practice, this means at minimum measuring these two temperatures, and possibly actively controlling them.
For the condenser itself, say, a coil in the shape of a cold finger, you'd measure the output temperature of coolant. For example, when doing
sulfur condensation, mineral oil or a glycol would make adequate coolants, since you need something with a higher boiling point than water. You don't
want to overcool the condensate and risk solidification, either. For full control, you 'd also measure the input temperature and control the pumping
rate. This leads to something like a flow calorimeter operated "in reverse", where you're measuring the heat extracted with the condenser, and thus
estimating the condensation rate.
For the wall of the chamber, you'd use temperature sensors. If insulation is insufficient to keep the operating temperature high enough, you'd
use a heater and a thermostat to keep it there.
The condenser should be demountable for cleaning. If the condensate is isolated on the condenser itself, it means you've got an alleviated issue
with cleaning the chamber, which has more surface area and is physically larger. The condenser could be dunked into a cleaning tank; not so feasible
for the chamber as a whole.
|
|
Magpie
lab constructor
   
Posts: 5939
Registered: 1-11-2003
Location: USA
Member Is Offline
Mood: Chemistry: the subtle science.
|
|
I made my first P production run with the new paint can retort configuration today. The run was a failure due to the reactant charge being way too
large. However, the retort per se performed well.
As has been my practice heretofore I filled the retort (250mL can) half full of the reactants (NaPO3/Al/SiO2). The theoretical yield for this 149g
charge was 25g of P.
After drying the charge at 120C for 1/2 hr the EMT tube w/lid was pressed onto the retort body and the assembly inserted into the furnace. The
insulating brick door was installed and the outlet of the EMT tube was submerged about 1/2" in a beaker of water. The argon supply system was made
ready. The thermostat was set for 700C and heating was commenced.
At about 400C bubbling (air expansion) was regular and there was some smoke coming out along with the bubbles. Shortly thereafter quite a few drops
of phosphorus fell into the receiver, but concurrently there was a breach of containment inside the furnace! A voluminous quantity of smoke came
pouring out along the sides and top of the firebrick door. I quickly pulled the plug on the furnace, then backed well away from the hood. My strong
hood flow was just able to keep up with the generation of smoke. I could see it pouring out of the fan duct outlet. Fortunately there was a slight
wind. In a few minutes this had abated and no more smoke could be seen emanating from the louvered outlet at the peak of my garage.
I took four pictures following this run. The first shows the system in the operating configuration.
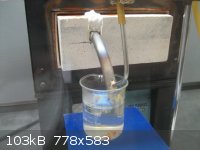
P retort in operation
The second picture shows the furnace with the firebrick door removed. The white material on the slag is a thin layer of de-laminated firebrick. You
can see smears of red P on the top of the firebrick.
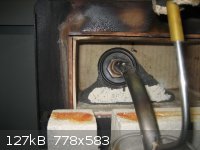
P retort with insulating brick removed
The 3rd picture shows the retort with slag, removed from the furnace.
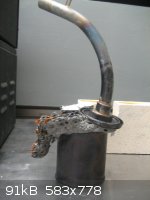
P retort following run
The final picture shows the slag on the furnace floor. This was removed fairly easily by scraping with a large screwdriver.
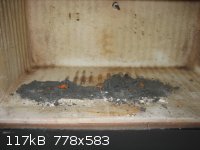
P slag on furnace floor
Disscussion
I admit that I should not have loaded the retort so full on the first run for this new retort design. But greed overcame better judgement.
Unfortunately this slag foam is a serious drawback for this formulation of reactants and significantly cuts into yield potential.
I am pleased with the paint can/EMT tube retort design, which incorporates compression seals, allowing reuse of the expensive tube. Perhaps it can be
improved to allow for a larger yield.
Although I don't think it had anything to do with causing too much foam I note that I did grind my NaPO3 in a coffee grinder prior to mixing it with
the other ingredients. This is the first time I have done this. This grinder does a fine job of pulverizing the NaPO3 to a fine powder.
As always, comments, suggestions, and questions are welcomed.
[Edited on 6-9-2012 by Magpie]
The single most important condition for a successful synthesis is good mixing - Nicodem
|
|
watson.fawkes
International Hazard
   
Posts: 2793
Registered: 16-8-2008
Member Is Offline
Mood: No Mood
|
|
Quote: Originally posted by Magpie  | Although I don't think it had anything to do with causing too much foam I note that I did grind my NaPO3 in a coffee grinder prior to mixing it with
the other ingredients. This is the first time I have done this. This grinder does a fine job of pulverizing the NaPO3 to a fine powder.
As always, comments, suggestions, and questions are welcomed. | The fine grind might have contributed. The
reaction mixture, partly liquid, had some characteristic viscosity. Gaseous products (e.g. phosphorus) would have some characteristic bubble-up time
to reach the surface and escape. If the rate of gas production exceeded the time for a bubble to escape, you'd expect to see volumetric expansion and
creation of a foam. Finely ground reactants could well have played into this by increasing the gas production rate beyond some threshold.
Suggestions. (1) (Not too helpful) Use a tall, thin reaction chamber and expect foam. That would mean a new oven and chamber, but it would allow the
foam to form without much consequence. (2) Use an inert viscosity modifier to thin the reaction mixture. CaF is what immediately comes to mind, but I
don't know if it would apply here. You could test multiple compositions in one furnace run with 1 g batches and little reaction thimbles, packed into
your reaction can. I'd suggest a simple rack also, with holes for the thimbles and a couple of bent sides for legs.
|
|
Magpie
lab constructor
   
Posts: 5939
Registered: 1-11-2003
Location: USA
Member Is Offline
Mood: Chemistry: the subtle science.
|
|
Quote: Originally posted by watson.fawkes  |
The fine grind might have contributed. The reaction mixture, partly liquid, had some characteristic viscosity. Gaseous products (e.g. phosphorus)
would have some characteristic bubble-up time to reach the surface and escape. If the rate of gas production exceeded the time for a bubble to escape,
you'd expect to see volumetric expansion and creation of a foam. Finely ground reactants could well have played into this by increasing the gas
production rate beyond some threshold.
|
Yes - good thought. Some small scale thimble testing should determine the effect of NaPO3 particle size.
Quote: Originally posted by watson.fawkes  |
Suggestions. (1) (Not too helpful) Use a tall, thin reaction chamber and expect foam. That would mean a new oven and chamber, but it would allow the
foam to form without much consequence. (2) Use an inert viscosity modifier to thin the reaction mixture. CaF is what immediately comes to mind, but I
don't know if it would apply here. You could test multiple compositions in one furnace run with 1 g batches and little reaction thimbles, packed into
your reaction can. I'd suggest a simple rack also, with holes for the thimbles and a couple of bent sides for legs. |
(1) It is unlikely that I will be buying another furnace. But I do have an old homemade furnace that I nearly threw away that might suffice. The
tricky part is finding a new form of cheap throwaway retort body that will seal to my EMT downspout.
(2) Rogeryermaw has done some runs using NaCl as a viscosity reducer. I'm not sure how much difference this made for him.
I will do some thimble testing with NaCl, CaF2, and a control. What % add of these reagents would you suggest?
[Edited on 7-9-2012 by Magpie]
The single most important condition for a successful synthesis is good mixing - Nicodem
|
|
blogfast25
International Hazard
   
Posts: 10562
Registered: 3-2-2008
Location: Neverland
Member Is Offline
Mood: No Mood
|
|
Amazing array of niggling little problems, you have to wonder if Hennig Brand with his more 'conventional' formulation also suffered these.
As regards fluxes, CaF2 is probably too high melting. Best might be a NaCl/KCl eutectic (or other inert, low melting eutectic) for maximum impact on
melt viscosity. Start at 10 w% of total charge, I would say.
[Edited on 7-9-2012 by blogfast25]
|
|
watson.fawkes
International Hazard
   
Posts: 2793
Registered: 16-8-2008
Member Is Offline
Mood: No Mood
|
|
Quote: Originally posted by Magpie  | The tricky part is finding a new form of cheap throwaway retort body that will seal to my EMT downspout.
[...]
I will do some thimble testing with NaCl, CaF2, and a control. What % add of these reagents would you suggest? | I don't know how much "throwaway" you need, but since you're using paint cans, you could consider modifying them. The machined lip
is the most important part, since it's the mating surface and difficult to duplicate. So, one possibility is to cut a paint can in half across the
middle of the cylinder. Then extend the height of the can with a tube. The problem is that this isn't exactly throwaway, given the effort to make a
gas-tight retort this way. But, you could take the same idea and use the top half of a can to make adapters for other kinds of containers, such as,
oh, gallon-sized paint cans. I should mention, although this might be in the realm of future plans, that you could split the retort into two parts:
(1) an inner reactant crucible and (2) a gas-tight retort. As long as part (1) is large enough to contain any foam, part (2) should need minimal
cleaning per run. Then only part (1) is your consumable. You might also use (3) an overflow tray, a semi-consumable.
As for percentages for flux reducers, I have no well-informed proposal about what percentages to start with. The idea came from flux modifiers, such
as those that reduce viscosity or flocculate slag particles. So you might start by looking at what they use. I have doubts about direct application,
though. My fallback position would be to look at the whole range first, from 0% to 100% in 10% increments, the endpoints being controls. This is one
extra furnace run over just guessing what might work and would give some confidence that you were in the right ballpark when you get to smaller
variations.
EDIT: copy editing.
[Edited on 7-9-2012 by watson.fawkes]
|
|
learningChem
Hazard to Others
 
Posts: 182
Registered: 21-7-2011
Member Is Offline
Mood: No Mood
|
|
Found a recipe in this book
http://books.google.com/books/about/One_thousand_processes_i...
page 61
They start with burnt bones - they add sulphuric acid to get rid of the lime as calcium sulphate - apparently the product is a solution of phosphoric
acid?
Next step, they add a solution of lead acetate to the phosphoric acid solution and "a white powder falls to the bottom"
But they don't say what this 'white powder' is - some kind of lead phosphate maybe??
Then they mix the white powder (dried) with 1/6 of charcoal, put the mix in a retort and heat it to "red hot"
So, I'm wondering two things
1) is the white powder lead phosphate?
2) is this a relatively 'low' temperature reaction?
|
|
Magpie
lab constructor
   
Posts: 5939
Registered: 1-11-2003
Location: USA
Member Is Offline
Mood: Chemistry: the subtle science.
|
|
As suggested by Watson I did some "thimble" testing today to determine what NaPO3/Al/SiO2 based formulation(s) might minimize slag formation. The
results are somewhat surprising.
Procedure
Rather than steel thimbles I used the bottoms of 100mm test tubes cut in half with a Dremel tool. I filled 5 such tubes with 1g of base
(stoichiometric) formulation modified as follows:
1. base formula - ground ingredients in a mortar per usual (the control).
2. pre-grind the NaPO3 in a coffee grinder; mix lightly in a mortar with the other 2 ingredients.
3. base formula with 10% NaCl add; grind all ingredients together in a mortar.
4. pre-grind NaPO3 + 10%NaCl in a coffee grinder; mix lightly with the other 2 ingredients in a mortar.
5. base formula w/10% add of 50 mole%KCl/50 mole%NaCl; grind together in a mortar.
The tubes were loaded with their respective powders and the height of the powder measured in mm. The tubes were then placed in a 50mL beaker in the
retort. The retort was fired to 700C and kept at that temperature for 1/2 hr.
Results
When cool the retort was opened and the tubes removed. They are shown in the picture below.
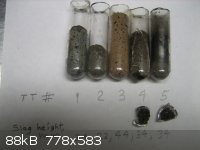
P slag volume comparison
In the order tubes 1 through 5, the unfired powder heights were 9, 10, 13, 13, and 11 mm, respectively.
Likewise, the fired slag heights are 34, 22, 44, 34, and 34mm, respectively.
The computed volume proportionalities, fired:unfired, are:
3.8, 2.0, 3.4, 2.6, and 3.1, respectively.
Conclusions
Therefore, these results show that the NaCl and NaCl/KCl adds gave mixed results. The best apparent result was with the pre-ground (by coffee
grinder) NaPO3.
The results bring up more questions. Like, what difference can be attributed to thorough grinding together in a mortar vs a light grinding in a
mortar. The better performers might just have a less complete reaction. It is impossible to say what is best without knowing the yield of P for each
formulation. This suggests that a different line of further testing is needed.
Comments, questions, and suggestions are welcomed.
[Edited on 12-9-2012 by Magpie] conclusions revised
[Edited on 12-9-2012 by Magpie]
The single most important condition for a successful synthesis is good mixing - Nicodem
|
|
Pages:
1
..
36
37
38
39
40
..
60 |