Pages:
1
..
29
30
31 |
Mabus
Wiki Master
 
Posts: 238
Registered: 3-11-2013
Member Is Offline
Mood: Energetic
|
|
Quote: Originally posted by Refinery  | Could this process work:
urea + sodium hydroxide + carbon in a furnace heated to reaction temp to produce cyanate and via carbothermic reduction to sodium cyanide + residual
of sodium hydroxide?
Then followed by purification with hot water, filtering, and crashing the sodium cyanide by adding ethanol which should reduce the solubility of NaCN
to a significant degree, but still allow the remaining sodium hydroxide to stay dissolved?
I prepared a batch of this by blending the three ingredients with blender and heating up. The solution was filtered, and adding significant amount of
ethanol caused white crystals to precipitate in a very good amount.
Should the product be mostly sodium cyanide that was produced? Unfortunately this process was done years ago and I had to get rid of my chemistry
items due to changes in other life matters, hence no more info is available. The process described is from a german chemistry board.
To obtain high purity an acid distillation for HCN to base could do the job, but if possible avoidable mostly due to the process being too laborous.
(necessary safety disclaimer: im using A2B2E2K2 filter with the infamous breaking-bad yellow chemical suit and my workspace was located outdoors and I
actually went so far as to build a 20-foot high chimney to my portable fume hood from 8" pvc tube to suck all nasties up to the sky.)
[Edited on 10-10-2019 by Refinery] |
Yes, it works. The urea+NaOH+C part. Not sure about crashing the NaCN with EtOH though. I know it doesn't work with iPrOH since the alcohol gets
salted out of the solution.
Unfortunately, the biggest drawback of using urea is that the yield is pretty bad, I never managed to get past 20%, half of the nitrogen is lost in
the reaction as ammonia, and then half of the rest simply breaks down during the reduction due to side reactions.
|
|
kmno4
International Hazard
   
Posts: 1496
Registered: 1-6-2005
Location: Silly, stupid country
Member Is Offline
Mood: No Mood
|
|
Quote: Originally posted by kmno4  |
.... reaction ends at FeK2[Fe(CN)6] step (larger amount of H2SO4 will not help). Further conversion (to FeSO4) is terribly slow. Great dilution and
boiling expels all HCN but with large amounts of water. You can add some CuCl (or even CuSO4) to the reaction mixure: it is converted to CuCN.
It has so small solubility that FeK2[Fe(CN)6] is (slowly, on boiling) converted to CuCN (-> HCN). In this way all CN can be removed as HCN.....
|
Because I used almost all my NaCN, I decided to verify the "CuCl" way. Indeed, I was able to convert all CN into HCN and absorb it in KOH-EtOH
solution. It is good method allowing to convert practically any CN containing material into HCN. Two important remarks:
1) amount of H2SO4 should be taken with (at least) 10% excess, counting on bisulfate formation (it means KHSO4 from K4[Fe(CN)6] for example, not K2SO4
- the solution must be highly acidic to prevent slow reaction rate
2) few (~5 g) grams of NaCl or KCl per ~20 g K4[Fe(CN)6] should be additionally added - it greatly speeds up reaction
The rest of information can be found in "Chemistry of cyanogen compounds" by Williams, on pages 278-279 and additional references given there (two
papers - available from the net)
Слава Україні !
Героям слава !
|
|
Refinery
Hazard to Others
 
Posts: 371
Registered: 17-2-2014
Member Is Offline
Mood: Still
|
|
My experience:
Theory
1mol urea (slight excess)
1mol NaOH
1mol C (slight excess)
= 1mol NaCN
Urea + NaOH = NaOCN (+ NH3 + H2O)
NaOCN + C = NaCN (+ CO)
It appears that urea and carbon can be excessed because the other one dissipates and the other one remains inert, easily filtered, but sodium doesn't
go anywhere.
Cyanuric acid is very slightly soluble (1/100), cyanate 10/100 and cyanide 60/100. For ethanol, the solubility crashes to almost zero at 100% and to
2% at 95%. 50-70% ABV crashes out major amount of NaCN from water. When water is added, it dissolves cyanide, cyanate and other stuff, but carbon and
possible cyanuric acid remains and is filtered. When alcohol is added, cyanide crashes out and is filtered.
Carbon is powdered using blender, and reagents are poured in SS crucible with gravity plug. Crucible is placed in ceramic wool round kiln and heated
using high power propane torch. The plug audibly rattles when NH3 and water evaporate. Rattling stops eventually, heating is continued. Crucible will
eventually visibly start to glow dark and then cherry red, and rattling begins again and visible jets of yellow flame are visible between the plug.
When jets of flame cease, heating is stopped and crubile is left to cool. Water is poured in (100mL for each 50g of NaCN theory; 60g/100mL sol @ 25C).
A lot of mechanical work is required to dissolve the concrete-like residue and a crucible with large opening is strongly preferred for this process.
When most to all is dissolved (which took total of 12 hours + lots of mechanical work), the black gunk is filtered into clear, slightly yellow liquid.
1.4x volume of 95% EtOH is added. At first, two layers are formed(a mystery?), a lower, yellowy, and upper, cloudy white, but it quickly dissipates
upon stirring, and liquid turns cloudy. Liquid is filtered again, and an amount of very slightly yellowish mass is collected and placed on a drying
pan. No final weighting has been made yet, but the yield appears to be over 50% with a margin. No tests for purity has been made yet.
Notes:
- Some crystals crashed out from filtered residues after NaCN was recovered. Cooling and refiltering the residue could increase yield.
- All residues and equipment were treated with calcium hypochlorite and rinsed thoroughly with running water after the process. Proper PPE with full
face mask and ABEK filter were used. Care was taken not to breath any fumes emitted during heating or other phases and process was carried outside to
eliminate any contamination or ventilation issues.
- If working routinely with cyanide, cyanokit (hydroxocobalamin) must be kept at person in order to reduce lethal effect if an accident, for ex. a
spillage occurs.
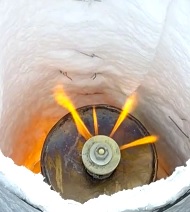
[Edited on 11-6-2020 by Refinery]
|
|
kmno4
International Hazard
   
Posts: 1496
Registered: 1-6-2005
Location: Silly, stupid country
Member Is Offline
Mood: No Mood
|
|
Quote: | Because I used almost all my NaCN, I decided to verify the "CuCl" way (...) |
Another tested variation of this method below.
To decrease H2SO4 consumption, the reaction is performed in two steps. The first step is reaction of H2SO4 and K4[Fe(CN)6] (in water) only. This leads
to insoluble K2Fe[Fe(CN)6] as end by-product, but amount of the acid is calculated (+ 10% excess) for K2SO4. No matter how much more H2SO4 is used,
K2Fe[Fe(CN)6] is very resistant to it.
When most of HCN distilled off*, the post-reaction mixture is set aside and cooled to r.t. Transparent liquid is the pipeted out as much as possible
and to the remaning "mud" of K2Fe[Fe(CN)6] another portion of H2SO4 solution is added (calculated for KHSO4 formation). Instead of CuCl, CuCN is
added, but in this case slightly larger amount of NaCl should be added. Fortunately, for this purpose CuCN does not have to be pure.
It was observed that K2Fe[Fe(CN)6] is rather easily oxidized by air (it becomes blue), especially in the second step (which lasts much longer that the
first one) and it seems to slow down its decomposition.
To prevent this, Cu tiny wire (from old coax) is added in amount of ~2 g (or more, per ~20 g of ferrocyanide). The excess of it remains in exhausted,
green transparent solution. It is easy to see that some part of it really reacted (acted as reductor).
* in the end of reaction, HCN goes off with lage (> 90%) amount of water. Optionally, it may be collected separately and added to the mixure in the
second step. It sligtly increases the KCN yield, because KOH ethanolic solution is less diluted with water.
See diagram of vapor-liquid for HCN-H2O system here:
Code: | http://www.ugr.es/~tep028/pqi/descargas/Industria%20quimica%20organica/tema_1/documentos_adicionales/a08_159_cianhidrico.pdf |
Слава Україні !
Героям слава !
|
|
Fyndium
International Hazard
   
Posts: 1192
Registered: 12-7-2020
Location: Not in USA
Member Is Offline
|
|
http://www.sciencemadness.org/smwiki/index.php/Sodium_cyanid...
Few questions:
- Doesn't the reaction of cyanate and carbon produce carbon monoxide, not dioxide? At least in the reaction a flame was emitted from the crucible for
the expected duration, and afterwards almost all carbon was gone. Carbon dioxide does not burn, to my knowledge.
- Since sodium hydroxide is reacted with cyanuric acid to form eventually sodium cyanate, there should be little to almost none left, especially if a
slight excess of urea is used, because it should completely decompose upon enough heating?
- Why use magnesium thermite reduction, when carbon does the same?
I made what is presumed to be sodium cyanide via the sodium hydroxide urea carbon method, and when the reaction was complete, the cake was dissolved
in hot water, carbon was filtered to result a yellow solution, which was mixed with equal volume of ethanol to precipitate white mass, which was
filtered dry and dried and presumed to be mostly cyanide.
Edit: also regarding the wiki page about purification by HCN distillation, should it be possible to remove carbon dioxide by condensing the HCN into
liquid form through a reflux condenser, form where it would drop into NaOH solution and CO2 would vent out and only trace amounts would travel down
into NaOH solution? For the record, the vented gas from condenser would of course be led through a long tube into a safe exit. I'm not sure how to
appropriately determine when the solution has been depleted from NaOH other than installing a syringe outlet to determine pH of the solution and cease
the generation when the solution does not show up as basic anymore. Also a third inlet with dropper funnel to add more hydroxide could be placed. I
presume this method would produce mostly highly pure sodium cyanide?
[Edited on 9-9-2020 by Fyndium]
|
|
Fyndium
International Hazard
   
Posts: 1192
Registered: 12-7-2020
Location: Not in USA
Member Is Offline
|
|
Well, it seems that no one has any knowledge of above. Or am I the only one with access to facilities suitable for making this stuff?
I found out last time that the yield I acquired was partially cut by hesitating with the filtering process. It seems that when adding in ethanol, one
should wait for good 15 minutes to allow the cyanide to settle. When I filtered it by vacuum, more kept crashing out and I found out the solution I
dumped contained quite a lot of white mass.
What I'm yet to figure is that is there CO2 formed at some point? My observations suggest that it indeed is the monoxide that is produced, because an
intense flare was emitted from the vessel exhaust tube and almost all of the carbon was gone when the cake was dissolved an filtered off from it.
Because if there is no CO2, any residual sodium hydroxide should pretty much stay in the solution when crashed.
What'd be the most effective way to determine the approx purity of obtained cyanide?
|
|
njl
National Hazard
  
Posts: 609
Registered: 26-11-2019
Location: under the sycamore tree
Member Is Offline
Mood: ambivalent
|
|
Double displacement in aqueous solution with silver nitrate.
|
|
Pumukli
National Hazard
  
Posts: 705
Registered: 2-3-2014
Location: EU
Member Is Online
Mood: No Mood
|
|
Distilling HCN into aquaeous NaOH is not a preferred method because those who tried it reported dark, discoloured product.
|
|
Calculon
Harmless
Posts: 5
Registered: 13-11-2020
Location: Europe
Member Is Offline
|
|
Someone tried the patent WO2016199944A1 ?
The method seems pretty simple, sodium carbonate + urea + additive1---> CYANATE--->reduction---> CYANIDE
I think is missing the step of separation of ammonium carbonate after first order reaction (it's necessary ?) and the addition of coal is missing in
the step for second-order reaction (reduction).
Infact in the process flow diagram is showed the addition of an unknown "additive 2"
|
|
Fyndium
International Hazard
   
Posts: 1192
Registered: 12-7-2020
Location: Not in USA
Member Is Offline
|
|
The sodium carbonate, urea and carbon process is well reckoned here. There was mention that it has somewhat lowish yields and there will be
impurities.
The carbonate can be replaced with hydroxide, and there should be little carbon dioxide contamination, as carbothermic reduction produces carbon
monoxide, which can be seen burning at the exit hole.
When dissolved in water and crashed out with plenty of ethanol, one should wait a good time before filtering the solids, because the process takes
some time. I noticed a good bunch of white residue in the filtrate when discarding it, but had no time to refilter it anymore.
|
|
Calculon
Harmless
Posts: 5
Registered: 13-11-2020
Location: Europe
Member Is Offline
|
|
Due to the low yield of the sodium carbonate, urea and carbon process I wanted to try the patent
https://patents.google.com/patent/WO2016199944A1/en
same process but good yield, that claim a content of sodium cyanide in the raw obtained product is 62-68%, it's a lot!
And after this step i can use the usual method, dissolve "metal" in water and crashed out with ethanol (i usually wait 6hours before filtering the
solid out of ethanol solution at 0°C)
|
|
Fyndium
International Hazard
   
Posts: 1192
Registered: 12-7-2020
Location: Not in USA
Member Is Offline
|
|
I'm still yet not sure if NaOH is better option as sodium source than Na2CO3. If there will be no carbonate present and if no CO2 is evolved at any
given time, it should not be in the final product. I'm not sure about reaction kinetics, though.
|
|
S.C. Wack
bibliomaster
   
Posts: 2419
Registered: 7-5-2004
Location: Cornworld, Central USA
Member Is Offline
Mood: Enhanced
|
|
Quote: Originally posted by Polverone  | The above text says that the Beilby cyanide process once provided half of the world's cyanide demand, yet there are only two unique references to it
on the whole web, one from the Sciencemadness Library and another from the Digital Library of India.
|
BTW the patent is also known as US484579. It's interesting on the semi-professional scale, once some MCN has been obtained by other means to use as
flux. The starting charge illustrated there is 20% KCN, 20-25% C, remainder K2CO3; mp below 850C. I wonder where the mp of the Na version or mixture
with K is.
|
|
Calculon
Harmless
Posts: 5
Registered: 13-11-2020
Location: Europe
Member Is Offline
|
|
My first crystals of potassium ferrocyanide.
By the KOH+urea method, in 3 steps.
|
|
Fery
International Hazard
   
Posts: 1015
Registered: 27-8-2019
Location: Czechoslovakia
Member Is Offline
|
|
Calculon - well done and beautiful crystals !!!
Could you please post more details about your experiment? It would be very useful for other chemists.
|
|
artemov
Hazard to Others
 
Posts: 181
Registered: 22-8-2018
Member Is Offline
|
|
Pray tell how!
|
|
Calculon
Harmless
Posts: 5
Registered: 13-11-2020
Location: Europe
Member Is Offline
|
|
I still need time to do a lot of tests to improve the yield, the reaction is very simple but I think that the details make the difference.
For this reason now at the end of the reaction I convert the KCN into potassium ferrocyanide, it's more stable and easier to separate to weigh it and
measure the yield.
Actual yield 15g KCN every 100g KOH
If anyone knows any tricks i can test it, however my schematic procedure is as follows:
1° step KOH + urea ==> KCNO
250-300°C for 30 minute in a SS large pot (5L) until all the water and ammonia have evaporated, mix strong meanwhile as it cools off to avoid the
cyanate from sticking to the bottom like concrete. Put this grainy powder in a mixer till finely powder, avoid contact with wet air as much as
possible.
2° step KCNO + C ==> KCN
Mix activated carbon finely powder ( I make from sugar, also charcoal works) with the crude cyanate into the mixer and chop for a few minutes. Avoid
contact with wet air as much as possible, and put in a oil filter jar up to 50% of the volume, close well with a sheet metal lid and aluminum foil to
prevent air from entering.
I use a homemade gpl furnace, start to heat slowly 200°-300°-350°C for the first 30-50 minute until the smell of ammonia stops, now raise the
temperature to medium 450°-550°C (the bottom of the jar is dark red) for 80 minute, little blue flames (invisible on daylight ) come out of the lid,
when the blu flames are disappearing raise the temperature to 700°-800°C (the aluminium foil fuse) for 30 minutes.
Switch off the flame and let cool without open the lid. Now the "metal" is more hard than concrete need hammer to crush it together with the pot.
3° step KCN + Fe ===> K4[Fe(cn)6]
Put the product with all the iron pieces of the oil filter into a glass beaker and add distilled water (the smell is like H2S), heat to 50°C for some
hours stirring sometimes, leave to rest for 48 hours stirring occasionally, filter, concentrate and separate the ferrocyanide using the temperature
solubility curve (very complicated). First forming a lot of white crystals are K2CO3 i think, instead ferrocyanide accumulates in the solution up to a
certain point start to make yellow powder or slurry crystals, now take the concentrated solution and add slowly HCl till stop bubbling CO2 to ph 8-9
(not less otherwise Prussian blue is formed, it can be seen when the drops of HCl are dropped), make saturated solution at 30°C , filter, and leave
alone for 24 hours. Crystals will be formed.
Dissolve again the crystals in distilled water, make saturated solution at 30°C, filter, leave alone for 24 hours, and beautiful big crystals will be
formed.
This is only a procedure without many details and doses, i will post when i have a better yield.
|
|
S.C. Wack
bibliomaster
   
Posts: 2419
Registered: 7-5-2004
Location: Cornworld, Central USA
Member Is Offline
Mood: Enhanced
|
|
The solubility of K ferrocyanide is an example of common ion effect, e.g. a precipitate starts to form in seconds when KCl is added.
There's probably a good reason why all the chemists of yesteryear never use hydroxide.
Quote: Originally posted by Fyndium  | When dissolved in water and crashed out with plenty of ethanol, one should wait a good time before filtering the solids, because the process takes
some time. |
A few cpds. mentioned in this thread are not entirely stable in alkaline water.
|
|
Lionel Spanner
Hazard to Others
 
Posts: 168
Registered: 14-12-2021
Location: near Barnsley, UK
Member Is Offline
|
|
Given that ChemPlayer obtained sodium and potassium cyanides by reducing potassium ferrocyanide with molten sodium metal, has anyone tried the same
with Prussian Blue?
If it works, the reaction should go as follows:
Fe4[Fe(CN)6]3 + 18 Na ---> 18 NaCN + 7 Fe
[Edited on 12-8-2022 by Lionel Spanner]
|
|
MrDoctor
Harmless
Posts: 23
Registered: 5-7-2022
Member Is Offline
|
|
Speaking of chemplayers method. if the desired end-product is benzyl nitrile, or really any other sort of similar nitrile, would it be feasible to
just add the benzyl chloride in this case, directly to the solidified melt without any further purification, since that seems to lead to unspecified
losses?
|
|
mr_bovinejony
Hazard to Others
 
Posts: 130
Registered: 20-4-2018
Member Is Offline
Mood: ASS
|
|
Ran through this thread multiple times and have yet to find a solution to my problem. I've distilled hcn from ferrocyanide and dilute sulfuric
directly into a methanolic solution of koh but as the cyanide precipitates it tends to form a gel rather than a powder. My only guess is that the shit
grade koh releases it's water into methanol and this water is causing the issue, but I haven't found anyone else having this problem. The next step
would be to try naoh in methanol instead then dry it somehow. Any thoughts on this?
|
|
conette
Harmless
Posts: 1
Registered: 25-9-2024
Member Is Offline
|
|
Can't find any info about solubility of potassium cyanide in isopropyl alcohol. My assumption that it is not soluble like in other alcohols, but can
someone confirm this, please?
|
|
Precipitates
Hazard to Others
 
Posts: 131
Registered: 4-12-2023
Location: SE Asia
Member Is Offline
Mood: Acid hungry
|
|
Given the following paper, I would expect it to have a solubility in between that of ethanol and tert-Butyl alcohol i.e., approx 1-2 g/L.
|
|
Pages:
1
..
29
30
31 |