Pages:
1
2
3 |
quino
Hazard to Self

Posts: 91
Registered: 19-11-2006
Member Is Offline
Mood: No Mood
|
|
http://138.23.152.128/protocols/Preparing%20glyoxal.pdf
http://www.springerlink.com/index/L351W055X3WL48M0.pdf
Preparation of glyoxal by the action of acetylene on gold chloride or gold bromide
Kindler, Karl
Berichte der Deutschen Chemischen Gesellschaft [Abteilung] B: Abhandlungen (1921), 54B, 647-9
The Au is quant. pptd. by C2H2 from aq. solns. of its halides containing not much more than 1.5% Au; the org. products are only glyoxal and
small amts. of CO2; the finely divided Au can again readily be converted into its halides by means of Cl or Br. The C2H2, purified according to
Gottig's directions (Ber. 32, 1877(1899)) and, to free it from any AcH which might have been formed, further washed with 30% NaHSO3 and then with 30%
NaOH, was passed into 2.6 g. of the Au halide in 100 cc. H2O at 70-80° in a flask connected with a condenser, cooled receiver and NaOH wash bottle
protected from atm. CO2 with sodalime. With a moderate stream of C2H2, the reaction is complete in about 2 hrs. The yield of CO2 was about 12%; no AcH
could be detected in the receiver. The filtrate from the pptd. Au with PhNHNH2 in dil. AcOH gave 86% of glyoxal osazone, m. 169-70°.
[Edited on 16-2-2007 by quino]
|
|
quino
Hazard to Self

Posts: 91
Registered: 19-11-2006
Member Is Offline
Mood: No Mood
|
|
Preparation of stable glyoxal
PATENT NO. FR 1342537
Acetaldehyde (I) (50%) and 40% HNO3, each dild. with deionized H2O in a molar ratio of 2.5:1 were charged continuously with stirring into the
top of one reactor at 38-9° and withdrawn from the bottom of a second reactor at the same temp. A little NO2 was introduced into the first reactor as
an initiator. Reaction time in each reactor was about 3 hrs. A feed of 11 parts I and 6.74 parts HNO3 gave 39.2 parts aq. mixt. contg. 9.1% glyoxal
(II), 6.3% org. acids, 1.4% HNO3, and 16.5% I. This aq. mixt. was concd. at 50° and 50 mm. until HNO3 reached 5% and heated further at 50° for 2
hrs. after addn. of 0.6 part I to consume remaining HNO3. The mixt. was then passed through an anion exchanger to yield 8.9 parts soln. contg. about
40% II and less than 0.8% org. acids. This soln. was passed through a cation exchange column (0.6 part acid type resin) and shelf stored at 35-40°
for two months with no discoloration. A similar soln. prepd. with crude HNO3 and non-purified H2O and not treated by cation exchange was yellowish
brown in only two weeks.
|
|
quino
Hazard to Self

Posts: 91
Registered: 19-11-2006
Member Is Offline
Mood: No Mood
|
|
Preparation of pure glyoxal
Brudz, V. G.; Drapkina, D. A.; Markovich, I. S.
Sb. Statei, Vses. Nauchn.-Issled. Inst. Khim. Reaktivov i Osobo Chistykh Khim. Veshchestv (1961), (No. 24), 98-101
Glyoxal (I) was prepd. by the action of oleum on Cl2CHCHCl2 (II). Optimal 71.5% yields were achieved when II was added dropwise during 1.5 h. to
15% excess H2SO4 contg. 60 .+-. 2% SO3 in the presence of 0.15% HgCl2 and heated 3.5 h. at 58-60°. Glyoxal sulfate (III) was filtered from the cooled
mixt. which contained chlorosulfonic acid. An aq. soln. of III was treated with CaCO3 to free I and ppt. CaSO4.
|
|
quino
Hazard to Self

Posts: 91
Registered: 19-11-2006
Member Is Offline
Mood: No Mood
|
|
Glyoxal preparation
Toyoda, Yoshiaki;
Patent Information
US 4555583 A
(CHO)2 (I) was prepd. in high yield and with very little formation of HOCH2CHO as the reaction intermediate, by gas phase oxidn. of HOCH2CH2OH
(II) at 450-650° in presence of a Ag (particle size 1 .times. 10-3 mm) catalyst and a P compd. Thus, a reactor contg. Ag and tri-Et phosphite, and
charged with II, steam, air, and N at 502° resulted in 100% conversion of II, a I selectivity of 80.1%, HCHO selectivity of 2.1% and HOCH2CHO of
trace amt.
|
|
quino
Hazard to Self

Posts: 91
Registered: 19-11-2006
Member Is Offline
Mood: No Mood
|
|
Continuous preparation of glyoxal
Sauer, Wolfgang; Hoffmann, Wolfgang
Patent Information
PATENT NO. DE 2922599 A1 The product gases (450-800°) from glyoxal prepn. (by oxidn. of glycol over Ag)
were quenched (after at most 1 s after leaving the catalyst) with droplets (0-130°) of H2O or aq. glyoxal entering at an angle of 2-85° with the
stream axis. Several examples were given in terms of numbered app. diagrams.
|
|
quino
Hazard to Self

Posts: 91
Registered: 19-11-2006
Member Is Offline
Mood: No Mood
|
|
Preparation of glyoxal, alkylglyoxals, and their acetals
PATENT NO.
AT 379799 B
The title compds. RCOCHO and RCOCH(OR1)2 (R = H, C1-6 alkyl; R1 = C1-6 alkyl) are prepd. by the ozonolysis of RC(:CH2)CH(OR1)2 at -80° to 0°,
followed by hydrogenation of the ozonolysis product at pH 2-7 while keeping the peroxide content .ltoreq.0.1 mol/L. Thus, H2C:CHCH(OMe)2 in MeOH was
ozonolyzed at -15 to -10° and the product hydrogenated over Pt (prepd. in situ by the redn. of PtO2) at pH 2-4. The stream of H was regulated in such
a way as to keep the peroxide content .ltoreq.0.02 mol/L. The product was purified by ion exchange and rectification, to give 81% OCHCH(OMe)2.
|
|
quino
Hazard to Self

Posts: 91
Registered: 19-11-2006
Member Is Offline
Mood: No Mood
|
|
Glyoxal preparation
Toyoda, Yoshiaki;
PATENT NO.
US 4555583 A
(CHO)2 (I) was prepd. in high yield and with very little formation of HOCH2CHO as the reaction intermediate, by gas phase oxidn. of HOCH2CH2OH
(II) at 450-650° in presence of a Ag (particle size 1 .times. 10-3 mm) catalyst and a P compd. Thus, a reactor contg. Ag and tri-Et phosphite, and
charged with II, steam, air, and N at 502° resulted in 100% conversion of II, a I selectivity of 80.1%, HCHO selectivity of 2.1% and HOCH2CHO of
trace amt.
|
|
quino
Hazard to Self

Posts: 91
Registered: 19-11-2006
Member Is Offline
Mood: No Mood
|
|
Title
Continuous preparation of glyoxal
Sauer, Wolfgang;
PATENT NO.
DE 2922599 The product gases (450-800°) from glyoxal prepn. (by oxidn. of glycol over Ag) were quenched (after at most 1 s after
leaving the catalyst) with droplets (0-130°) of H2O or aq. glyoxal entering at an angle of 2-85° with the stream axis. Several examples were given
in terms of numbered app. diagrams.
|
|
quino
Hazard to Self

Posts: 91
Registered: 19-11-2006
Member Is Offline
Mood: No Mood
|
|
Preparation of glyoxal by nitric acid oxidation of acetaldehyde
Chen, Zhangming;
Fujian Res. Inst. Struct. Matter, Acad. Sin., Fuzhou, Peop. Rep. China
Shiyou Huagong (1987), 16(8), 547-50
Glyoxal (I) was prepd. in 50% yield by HNO3 oxidn. of AcH at 40° and at HNO3/AcH mol ratio of 0.5-1.16. The effects of catalysts, NaNO3, and
AcOH on the yield of I were detd. The reaction mechanism was briefly discussed.
|
|
quino
Hazard to Self

Posts: 91
Registered: 19-11-2006
Member Is Offline
Mood: No Mood
|
|
Preparation of glyoxal from ethylene glycol at gas phase
Wakimura, Kazuo;
PATENT NO.
JP 03232835 A
Glyoxal is prepd. by gas-phase oxidn. of ethylene glycol with mol. O in the presence of Ag supported on silicon carbide powders as a catalyst
and P (derivs.). A gaseous mixt. contg. ethylene glycol, H2O, air, N, and tri-Et phosphite was passed through a reactor packed with silicon
carbide-supported Ag at 585° to give glyoxal in 99.9% conversion and 84.3% selectivity, vs. 99.9% and 64.8%, without silicon carbide, resp.
|
|
quino
Hazard to Self

Posts: 91
Registered: 19-11-2006
Member Is Offline
Mood: No Mood
|
|
Preparation of glyoxals
Wakimura, Kazuo;
PATENT NO.
DE 19519426 A1 The title process comprises oxidative dehydrogenation of glycols in the presence of P or a P compd. and a
catalyst comprising Ag and .gtoreq.1 of Au, Pt, Rh, and Pd. Thus, MeCH(OH)CH2OH, (MeO)3P, air, water, and N were passed through a reactor contg. a
catalyst comprising Ag and Au at 491° to give 99.8% conversion with 69.7% selectivity for MeCOCHO.
|
|
franklyn
International Hazard
   
Posts: 3026
Registered: 30-5-2006
Location: Da Big Apple
Member Is Offline
Mood: No Mood
|
|
Quote: | Originally posted by The_Davster
For Acquisition, contact your favorite photography supplier and ask them to get it for you, it is slowly replacing formaldehyde as it is less toxic,
some suppliers already have it in stock. |
Not much use to me but for those who care I discovered this source _
http://www.photoformulary.com/DesktopModules/StoreProductDet...
But even for me, two hundred twenty thousand dollars a pint seems a bit steep . 
.
|
|
Sauron
International Hazard
   
Posts: 5351
Registered: 22-12-2006
Location: Barad-Dur, Mordor
Member Is Offline
Mood: metastable
|
|
There was another item on that page Chemicals - G that ought to interest the members who read PIHKAL all the time.
Gallic Acid 100 g $80
|
|
franklyn
International Hazard
   
Posts: 3026
Registered: 30-5-2006
Location: Da Big Apple
Member Is Offline
Mood: No Mood
|
|
Glyoxal from Ozonolysis of Benzene
What I don't get is that this is exactly how the Ozonide is made
http://www.sciencemadness.org/talk/viewthread.php?tid=1172#p...
DMSO solvation then determines the product. Cool if it works.
- If anyone can obtain this article please post it in References -
http://pubs.acs.org/doi/abs/10.1021/i360029a017
Glyoxal from Ozonolysis of Benzene
William P. Keaveney, Raymond V. Rush, James J. Pappas
Industrial & Engineering Chemistry Product Research & Development
1969, 8 (1), pp 89–92
It would seem too that Ethandial is becoming an industrial staple.
http://www.entrepreneur.com/tradejournals/article/198473070....
.
|
|
jnik
Harmless
Posts: 5
Registered: 11-2-2012
Location: Winterfall
Member Is Offline
Mood: No Mood
|
|
Full article "Glyoxal from Ozonolysis of Benzene"
Attachment: Glyoxal from Ozonolysis of Benzene.pdf (509kB) This file has been downloaded 2211 times
|
|
AndersHoveland
Hazard to Other Members, due to repeated speculation and posting of untested highly dangerous procedures!
   
Posts: 1986
Registered: 2-3-2011
Member Is Offline
Mood: No Mood
|
|
Glyoxal can be made by reacting acetaldehyde with selenium dioxide. yield is about 60%; the selenium can be recycled by oxidation with nitric acid or
hydrogen peroxide. Acetic acid acts as an inhibitor against the undesirable rearrangement to glycolic acid. The temperature is ideally kept between
65–80 °C
Alternatively, dichloro-dioxane ( with four chlorine atoms [C2H2Cl2O]2 ), can hydrolyzed to glyoxal. Dichloro-dioxane is considered a "chloro-ether",
and can be made by the reaction of acetyl chloride with ethyl acetate. Myolo (1911)
A less practical, but more interesting route is to use 2-Iodoxybenzoic acid, which can oxidize methanol to formaldehyde in 94% yield, and can
similarly oxidize ethylene glycol (vehicle anti-freeze) to glyoxal. However, dimethyl sulfoxide (DMSO) can not be used as a
solvent for the latter, as its pressence will cause the ethylene glycol to be oxidized to formaldehyde instead. The 2-Iodoxybenzoic acid can then be
re-oxidized and recycled after completion of the reaction.
[Edited on 16-4-2012 by AndersHoveland]
|
|
CMOS
Harmless
Posts: 14
Registered: 27-2-2009
Member Is Offline
Mood: No Mood
|
|
Hi
Does anyone know how to get glioxal from ethylene glycol solution? I think that precipitating glioxal with NaHSO3 would be the easiest way, but will
it work in glycol solution?
|
|
CMOS
Harmless
Posts: 14
Registered: 27-2-2009
Member Is Offline
Mood: No Mood
|
|
So, I've tried making glioxal by method described in polish patent PL126434B2 (by passing air/ air/oxygen /pure oxygen through ethylene glycol with
catalyst, Me(RCOOH)xnH2O where Me=Cu,Co,Mn or other transitional metal, heated to 140-160*C for 20h. Yield: 7-10% molar conversion ). Catalysis
supposed to stay unchanged, but mine (I used copper acetate) got reducted to metallic copper so, I filtered it out. I've made Benedict's test and it
turned out positive. I want to use NaHSO3 to precipitate aldehyde, but how? Should I just add glioxal/glycol to solution of NaHSO3 ?
[Edited on 16-8-2013 by CMOS]
|
|
IPN
Hazard to Others
 
Posts: 156
Registered: 31-5-2003
Location: Finland
Member Is Offline
Mood: oxidized
|
|
Yeah, just add your glyoxal-containing solution to an excess of ethanolic solution of sodium bisulfite and the adduct should precipitate out.
A 50/50 EtOH/H2O solution should be fine (usually 40% in NaHSO3), you can wash the precipitate free of water and organics with ethanol followed by
ether.
The adduct can be broken with formaldehyde.
|
|
WGTR
National Hazard
  
Posts: 971
Registered: 29-9-2013
Location: Online
Member Is Offline
Mood: Outline
|
|
Glyoxal Synthesis
Here is a reference that might be useful to someone who wants a simple lab prep for glyoxal. I haven't tried it yet, but intend to shortly. It
uses sodium bisulfite and tartaric acid as starting materials, and looks pretty simple if it works.
The book is in German, and here is the link in Google Books:
http://books.google.com/books?id=AQ42AQAAMAAJ&dq=edition...
Here are the pages in German:
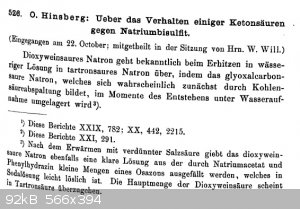 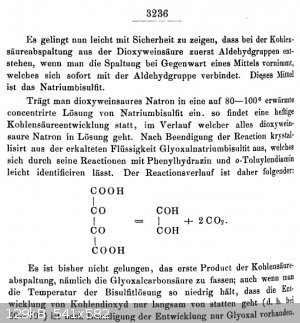
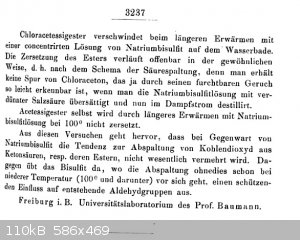
I have typed out and google-translated the article to the best of my ability, but would appreciate it if someone would like to clean it up. Here it
is in English:
"O. Hinsberg: About the ketonic against some sodium bisulfite:
Dioxy wine soda is well known, when heated in aqueous solution in tartronsaures soda over by the glyoxal carbon soda, which probably formed initially
by carbon dioxide elimination, is rearranged in the moments of occurrence under water absorption.
It is possible now easy to show with certainty that in the carbonic acid elimination from the first dioxy tartaric acid aldehyde arise when one
carries out the cleavage in the presence of an agent which immediately binds with the aldehyde group. This agent is sodium bisulfite.
Plotting dioxy wine soda into a warmed to 80-100 ° concentrated solution of sodium bisulfite, a violent bubble formation takes place during which all
dioxy wine soda dissolves. After completion of the reaction, crystallizes from the cooled liquid from Glyoxalnatriumbisulfit, which can easily
identify it by its reactions with phenylhydrazine and o-toluene diamine. The Reactionsverlauf is therefore:
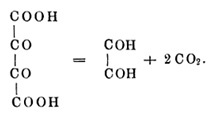
It has not been successful, the first product of carbon dioxide elimination, namely to take the Glyoxalcarbonsäure; also if you keep the temperature
of the bisulfite solution is so low that the development of carbon dioxide slowly of goes (ie, 60-70 °) after completion of the development only
glyoxal available.
Since the dioxy tartaric acid is easily generated from nitro tartaric acid, it seemed possible that these also go on in Glyoxal on heating with acid
sulphite salts. The experiment has shown that, in fact, a reaction in the indicated direction occurs, however, the yields of glyoxal are always low;
were obtained about 20 per cent of the theoretical amount at best. The method is thus suitable for the production of glyoxal bisulfites.
The favorable course of the experiments just described, gave rise, some other ketonic acids, their esters, respectively, to check on their behavior
towards sodium bisulphite.
The pyruvic acid, which has been studied for this purpose, showed against the reagent a resistance which at least that is equivalent to diluted
mineral acids, for even as it was heated pyruvic acid with sodium bisulfite solution in the tube to 170 °, by far the greater part of the organic
acid was unchanged. Products of decomposition of pyruvic acid could not be detected.
Chloro acetoacetate disappears on prolonged heating with a concentrated solution of sodium bisulfite on the water-bath. The decomposition of the ester
appears to proceed in the usual way, ie according to the scheme of the acid cleavage, because you will get no trace of chlorine acetone, which is so
easy erkeunbar yes by his awful smell when the supersaturated sodium bisulfite solution with dilute hydrochloric acid and then distilled in steam
power.
Acetoacetic ester itself is not decomposed by prolonged heating with sodium bisulfite solution at 100 °.
From these experiments it appears that in the presence of sodium bisulfite, the tendency to separation of carbon dioxide from ketonic acids, esters
thereof, respectively, is not substantially increased. In contrast, the bisulfite exercises where the spin-off without this already at a low
temperature (100 ° and below) is going on, a protective influence on resulting aldehyde groups from."
|
|
Praxichys
International Hazard
   
Posts: 1063
Registered: 31-7-2013
Location: Detroit, Michigan, USA
Member Is Offline
Mood: Coprecipitated
|
|
Weinsäure is tartaric acid and Weinsäures Natrium is sodium tartarate. "Dioxyweinsäure" I think is dihydroxytartaric acid. See http://pubs.acs.org/doi/abs/10.1021/ja01442a013
Quote: |
When sodium dihydroxytartarate is poured into a warmed 80-100° concentrated solution of sodium bisulfite, a violent bubble formation takes place
during which all of the sodium dihydroxytartarate dissolves. After completion of the reaction, glyoxal sodium bisulfite crystallizes from the cooled
liquid, which can easily be identified by its reactions with phenylhydrazine and o-toluene diamine.
...
It has not been successful to isolate the product of a single carbon dioxide elimination, namely to take the glyoxylic acid; even if you keep the
temperature of the bisulfite solution is so low that the development of carbon dioxide slowly of goes (ie, 60-70 °) after completion of the
generation of gas, only glyoxal is available.
Since the dihydroxytartaric acid is easily generated from nitrotartaric acid, it seemed possible that these could convert to Glyoxal on heating with
acid sulphite salts. The experiment has shown that, in fact, a reaction in the indicated direction occurs, however, the yields of glyoxal are always
low; were obtained about 20 per cent of the theoretical amount at best. The method is thus suitable for the production of glyoxal bisulfites.
|

Glyoxal sodium bisulfite addition compound hydrate from the Aldrich website.
Nitrotartaric acid, US 1506728 A:
Quote: |
As an illustration 200 pounds of tartaric acid may be first dissolved in 100 pounds boiling water, and stirred until dissolved. The dissolved tartaric
acid is then added to 1500 pounds of mixed acid, containing twenty five per cent nitric acid. The entire mixture is then agitated and the temperature
is maintained at approximately 75 degrees centigrade. When the entire mixture has been thoroughly stirred, it is cooled and the nitrotartaric acid
will settle or precipitate in the form of large crystals, which may be readily separated in an almost pure form.
|
Dihydroxytartaric acid
The nitrotartaric acid is very easily hydrolyzed.
Journal of the American Chemical Society, Volume 43, Issues 1-6. Free Google ebook. pp. 577
Quote: |
When solutions of nitrotartaric acid are allowed to stand, they soon turn blue, gases are given off, and much heat is evolved. If the temperature is
kept under control by water cooling, the process lasts from one to two days. The gases consist at first of nitrogen trioxide; later they become
colorless, and are composed of nitric oxide and carbon dioxide. The solution contains chiefly dihydroxy-tartaric acid, which may be precipitated by
addition of sodium acetate or carbonate as the very insoluble sodium dihydroxy tartarate; it also contains tartronic and oxalic
acids. The yield of sodium dihydroxy-tartarate is from 75-80%.
|
In a nutshell:
1. Nitrate some tartaric acid.
2. Hydrolyze the nitrotartaric acid in water with cooling. Precipitate with sodium carbonate, filter.
3. Mix with a solution of sodium bisulfite at 80-100C.
4. Cool solution to precipitate glyoxal sodium bisulfite hydrate.
And now remains the task of isolating the glyoxal from the bisulfite addition compound. Apparently this can be done with formaldehyde but that is
equally annoying to get.
[Edited on 16-10-2014 by Praxichys]
|
|
WGTR
National Hazard
  
Posts: 971
Registered: 29-9-2013
Location: Online
Member Is Offline
Mood: Outline
|
|
Thank you very much for posting this. The information is indispensable, and makes up for my poor German translation skills. I was struggling
through another translation of that when you posted.
I have been thinking of perfecting a glyoxal synthesis for a while, and have tried very small-scale reactions of various types. Some different
pathways that I have tried/considered:
1. Nitric acid oxidation of ethanol/acetaldehyde (30-35°C) with copper catalyst.
2. Nitric acid oxidation of ethylene glycol at 25°C.
3. Sodium bismuthate oxidation of tartaric acid.
4. Selenium dioxide oxidation of acetaldehyde.
5. Dehydrogenation of ethylene glycol in the gas phase over copper.
6. Dehydrogenation of ethylene glycol in the liquid phase with copper oxide (≈180-190°C).
7. Reaction of Dihydroxytartaric acid with sodium bisulfite.
8. Ozonolysis of Acetylene.
I can certainly buy it (and I have, just to obtain a reference sample), but it would be an interesting chemical to make. Ultimately it will be used
to make imidazolium-based ionic liquids. These can also be bought, but they are quite expensive. It would be kind of cool to do a total synthesis
of an expensive ionic liquid.
I can make it using any of the above methods, but I'm trying to reduce the process down to something that doesn't use significant amounts of expensive
or uncommon reagents. Yields need to be good, or else the desired product should be easy to separate from the side products (or the contaminants
should not interfere with the following reactions) . Also, if custom equipment is needed, then it needs to be something that can be made or obtained
by a wide variety of people. Ideally it should not be a process that is unnecessarily dangerous. Anyway, I have my work cut out for me. I have to
run, if I have time later I'd like to add some references for the processes above. I have them buried in my stack of papers on the desk.
|
|
Praxichys
International Hazard
   
Posts: 1063
Registered: 31-7-2013
Location: Detroit, Michigan, USA
Member Is Offline
Mood: Coprecipitated
|
|
I too am searching for as reliable way to make glyoxal in the laboratory. I need it for some furazan derivatives I am working on, and for a simple
compound it sure is expensive!
So far I have started by dehydrogenating ethanol to acetaldehyde (with awful yields) in a hot copper coil, and plan to go the HNO3 oxidation route, or
perhaps try directly the gas phase oxidation of ethylene glycol. The yield is so bad for a single hydroxyl that I am doubtful if I can get anything
useful at all with the glycol.
Bismuthate oxidation
I am very interested in your third reference with the bismuthate oxidation. I have done some quick online searching, and it looks like sodium
bismuthate and tartaric acid in a 2:1 ratio in 3N sulfuric acid gave a 70% yield of glyoxal. I found that here. The sticking point with this one is the regeneration of the bismuthate which is no easy task.
I found a thread here where plante1999 states:
Quote: |
I made a solution of 7g of KOH in 10ml of water. I added 2g of Bi2O3 and I heated the solution to boiling. When the solution was boiling I passed
chlorine in, until chlorine started to escape from the solution. The yellow bismuth trioxide turned violet-brown during the oxidation. The solution
was dumped in 200ml of cold water. The cold water was decanted, and the precipitate washed with 100ml of cold water.
| Not too bad, really.
Cu, Co, Mn catalyzed air oxidation in liquid phase
There is also a reference to polish patent PL126434B2 written above in this thread that uses the air oxidation of liquid phase glycol at 140-160C with
a catalyst of Cu, Co, or Mn acetate. Reaction time is ~20h and yields are low, (something like 7-10% allegedly) but all the reagents are all readily
available and inexpensive. Theoretically the glyoxal might distill off of such a mixture during the reaction and could be collected continuously.
I think I am going to give this one a try. I know no Polish but I will run a Google translate on it.
Attachment: PL126434B2.pdf (336kB) This file has been downloaded 1292 times
[EDIT]
From the translation (cleaned up a bit):
Quote: | It was found that the most effective catalysts for the oxidation of ethylene glycol acid in the liquid phase with molecular oxygen, are complexes of
transition metals, szcze¬ cially copper (II) and cobalt (II) of the formula: M (RCOO) xin H2O (where M = Cu, Co, Mn, V or other The transition metal
R = H, alkyl). The oxidation may be carried out with pure oxygen, air or enriched air oxygen. |
Quote: | Example IV. In [a reactor] as in Example II provided ethylene glycol which was dissolved 0.5 mol of Cu (CH3COO) 2H20. Oxidation air flow 2501 / hr.
(I assume this is 250 liters per hour) carried out at 140 ° C for 20 hours. Conversion of ethylene glycol the
glyoxal was 7.0 mol%.
EXAMPLE The oxidation reaction as in Example IV was carried out at a temperature of 160 ° C. The conversion to glyoxal was 9.2 mol%. P r of y k ³ d
VI. The oxidation of ethylene glycol was carried out as in Example V używa¬ ing ethylene glycol as the solvent in a weight ratio of dimethyl
sulfoxide to
ethylene glycol as a 4: 1. Obtained in this case, the conversion of ethylene glycol to glyoxal was 14.5 mol%.
|
It would appear that they have bubbled air at 250 L/hr into one liter of ethylene glycol at 160°C with 0.5mol copper II acetate dihydrate dissolved
in, in a mixture 4:1 DMSO to glycol/acetate solution, for 20 hours, yielding a 14.5% conversion to glyoxal.
It also says that the glyoxal is easily separated by distillation, the catalyst does not need regeneration, and the glycol can be recycled for the
next run.
The difference in BP suggests that the glyoxal might be removable continuously, as the paper makes mention of a reflux condenser. I think this is a
winner.
[Edited on 16-10-2014 by Praxichys]
Attachment: translation.txt (7kB) This file has been downloaded 1042 times
|
|
WGTR
National Hazard
  
Posts: 971
Registered: 29-9-2013
Location: Online
Member Is Offline
Mood: Outline
|
|
Yes, the reference that you uploaded is the one that I am thinking of. There is one thing that bothers me about it, though. They isolate glyoxal
by extracting with ether, which they neutralize with aqueous sodium carbonate. This might work if small amounts of carbonate are used, but if the
product was completely neutralized, I think it would have resulted in sodium glycolate instead of glyoxal. Glyoxal is sensitive to pH, and
rearranges to glycolate in basic conditions. In every other method I've seen, calcium carbonate is used instead, as it doesn't react with glyoxal.
Maybe they were just careful, but it's always possible that they didn't actually do the experiment. I got distracted making sodium bismuthate, so I
haven't tried to duplicate it yet.
For some simple sodium bismuthate experiments, I neutralized basic bismuth nitrate with sodium hydroxide. An excess amount of 30% hydrogen peroxide
was added, and then sodium hydroxide pellets were added gradually with heavy stirring until the color started darkening, and gas began escaping. Over
the next half hour or so the color began yellowing, and then a brownish color. The color varied from batch to batch. Some more peroxide was added
just to be sure that the reaction would go no further. I can't say that this is sodium bismuthate; no reference that I saw mentions making it this
way. When I acidified it with sulfuric acid, though, it would turn reddish, and this substance would be decolorized by room temperature ethanol. I
didn't go much further with this method than this. The process of making it either this way, or the common way, is too costly considering the
desired end product (glyoxal).
Are you dehydrogenating ethanol first to save on nitric acid? Nitric acid can act on ethanol directly. Anyway I used the method outlined in
"US3429929 A", but only on mL quantities of ethanol, not acetaldehyde. I haven't scaled it up yet, or tested the products. I was more interested
initially in how exothermic the reaction was, how hard it was to initiate (with nitrite), and some of the logistical issues in conducting the
reaction. I'm not sure that I'll go this route, though, because a stoichiometric amount of nitric acid is needed for each quantity of glyoxal.
Nitric acid is going to be hard to get for people in Europe, and it's a little expensive anyways.
Direct dehydrogenation of ethanol can be done. Sabatier did it, and I've had some success with it myself. The main thing is that time and effort
need to be spent getting the reactor set up correctly. The catalyst beads were easy. They were made from copper and magnesium hydroxide. I
strung them up like a necklace, and when dry, shoved everything down the reactor tube. It was essentially a "single-bead-string reactor". Heating
of the reactor was not a problem. It took some firebricks and a short roll of Kanthal wire. I have pictures of this experiment, but I'll have to
post them later if I have time. The main issues that I haven't resolved yet are the alcohol vaporization and metering. Once the alcohol vapors
form, I don't want any condensation anywhere in the system until after the reactor. This avoids alcohol droplets getting pushed directly into the hot
reaction tube (think: explosive catalyst bed deconstruction!) Without metering the alcohol, the experiment is not very informative. I need to think
up a way to meter the alcohol into a device that will vaporize it instantly and smoothly, without allowing it to superheat and explode randomly.
Anyway, it sounds like part of your problem is the fineness of the catalyst. Copper wire will not work well for ethanol dehydrogenation. It may
work for methanol, though. For ethanol, catalyst beads made from fine powder are needed.
One thing to keep in mind about glyoxal, is that it is weird. If formed in a vapor phase reaction, it will be happy to remain in the vapor phase
unless it is allowed to condense in the presence of water. Once it contacts liquid water, it polymerizes instantly, becoming essentially
non-volatile up to its decomposition point. It can be dehydrated and distilled again, but only from something strong, like P2O5. This is mainly why
it is sold in aqueous solutions.
I wish that I could expand on all of this right now, but I'm a little short on time right at the moment. Hopefully things will slow down a bit
later.
[Edited on 10-17-2014 by WGTR]
|
|
Praxichys
International Hazard
   
Posts: 1063
Registered: 31-7-2013
Location: Detroit, Michigan, USA
Member Is Offline
Mood: Coprecipitated
|
|
That is a lot of helpful information about the dehydrogenator. I am interested in how you have prepared your catalyst beads.
Yes, the dehydrogenation was to save nitric acid, which I make myself. I am also not a big fan of the potential to generate ethyl nitrate, and the
manufacture of good nitric acid is labor-intensive.
My reactor has no discreet catalyst and is simply a coil of bare copper tubing held in a hot flame. I chose the dehydrogenation route over oxidation
because of the potential for an explosion, and the difficulties encountered while trying to regulate the ratio of alcohol vapor and air. The reactor
did work to some extent but I found it in need of a pre-chiller because the absorption solution would get quite warm and reek of the aldehyde. I could
tell it was working by the presence of small amounts of gas that would not be absorbed at the absorbtion stage - presumably the hydrogen. A redesign
is in progress, since the apparatus would mean an unlimited supply of very cheap formaldehyde and acetaldehyde.
I suppose I should have mentioned that aq. glyoxal is sufficient for my purposes - no need for anhydrous/monohydrate, etc.
It does appear in the Polish patent that
- The mixture of glycol and glyoxal is separated from the catalyst by distillation (possibly under reduced pressure)
- The resulting mixture of glycol/glyoxal is used directly for organic synthesis
I wonder how readily the polymerized hydrates reconvert to aqueous glyoxal? This could be a useful isolation step. I think the hydrates compare to
trioxane or paraldehyde. Perhaps acidifying the glycol/glyoxal solution with an aqueous acid will force much of the polymerized stuff back to free
glyoxal which could be distilled. Furthermore, the BP of the mixture of DMSO and ethanediol is probably >190C - maybe sufficient to depolymerize
any hydrates in the first place? Maybe a splash of sulfuric acid would allow glyoxal to distill out. I intend to absorb the vapor into deionized
water.
Either that, or maybe warm the finished glyoxal/glycol with just enough water to form the dimer and trimer hydrates, then crash into water and filter
them out.
I will have to run a big batch and split the resulting solution to see if I can get anywhere with this.
There are some interesting methods for interconverting glyoxal polymer hydrates to glyoxal in US2463030, specifically using 1,4-dioxane as a solvent
and azeotropic water removal with toluene.
|
|
Pages:
1
2
3 |
|