Pages:
1
2 |
ScienceSquirrel
International Hazard
   
Posts: 1863
Registered: 18-6-2008
Location: Brittany
Member Is Offline
Mood: Dogs are pets but cats are little furry humans with four feet and self determination!
|
|
Quote: Originally posted by kmno4  | There are simple and cheap wet methods for converting Pb salts (generally - any salts) to Pb.
You can use Pb/PbSO4/PbO... mixtures, all is converted to Pb.
Original idea from book:
Take two Zn plates, make paste from PbSO4 and H2O and place it between Zn plates. Immerse all in NaCl solution and wait. PbSO4 will change to Pb
sponge, Zn react to ZnSO4. It works, but can take many days to complete reaction.
Modifications:
use cut iron sheet (not powder - hard to remove), may be Zn coated, iron wire, it does not matter. Take bottle, put iron, Pb salt (or mixture), water
and some acetic acid (citric, sulfuric, etc). Stop the bottle and shake it from time to time. End of reaction can be indicated by immersing a piece of
clean iron for some time (in slurry) - surface of iron should not be covered by Pb sponge.
Remove remaining iron, decant, wash, dry, melt Pb. Do not store prepared dry Pb for a long time, because it slowly covers with oxide.
I tested Al sheets but I got hard to remove "Al(OH)3" hard particles. I think it is question of bad conditions (just tested it only to see if it works
at all). Maybe NaOH instead of acidic solution would be better ? Not tested, but if someone wants, worth trying.
Important : Pb in car battery always contains some Sb, even few %. |
Quite a lot of 'lead' is actually a lead antimony alloy as the antimony make it harder eg bullets, shot, wheel balancing weights, etc.
|
|
watson.fawkes
International Hazard
   
Posts: 2793
Registered: 16-8-2008
Member Is Offline
Mood: No Mood
|
|
Quote: Originally posted by Bezaleel  | When cold, I am left with an opaque dark grey mass, which on breaking proves to be virtually homogenous. No sheen of metal there. So in this case, the
dark grey colour is all through the substance.
Of course, it could be that it consists of microscopic lead crystals with a dark grey outer layer. Note that the dark grey mass is insoluble.
| I'd have to guess that you've got significant lead (II) chloride, which is poorly soluble in water. I'd have
to guess that this chloride is also more soluble in lead than in the alkali chloride flux, given your result. If that's true, the lead chloride would
have partitioned into the lead.
I recommended a cover flux, but I didn't put any consideration into what it ought to be. I should have recommended you look up what's already known to
work; my apologies. Fluxes take some experience to understand, and I might have pointed out that a bit of research was warranted.
I looked into a bit just now. Borax and other borates are used as covers for cleaning lead when casting. Lime and limestone are both used in recovery
smelting. So it seems that you want a flux based on oxides, carbonates, and borates. Lime can help suppress some of the SO2 formation by forming
CaSO4. Borax will lower the melting temperature. These are all glass-forming materials, I'll note, which leads me to think that soda ash (principally
Na2CO3) might be useful as well.
You've got a new problem, however, in that you've got to get out the chloride. It'll likely need to come off as either Cl2 or HCl, so that it gasses
out rather than redissolves. If it doesn't come off as Cl2 (try that first), you'll need to add a hydrogen reducer of some form. For cleaning lead,
folks are using hydrocarbons such as paraffin wax or even motor oil. They flame off fairly soon after addition, so beware.
And don't take me on faith. I did a bit of reading, but you probably should do your own at this point.
|
|
blogfast25
International Hazard
   
Posts: 10562
Registered: 3-2-2008
Location: Neverland
Member Is Offline
Mood: No Mood
|
|
I had a lot of trouble dissolving battery lead in nitric acid (70 %), which I believe is due to these hardeners (Ca seems also to be used). Pure
(reagent) lead dissolved much more easily. Very frustrating...
|
|
AJKOER
Radically Dubious
   
Posts: 3026
Registered: 7-5-2011
Member Is Offline
Mood: No Mood
|
|
Quote: Originally posted by kmno4  | There are simple and cheap wet methods for converting Pb salts (generally - any salts) to Pb.
You can use Pb/PbSO4/PbO... mixtures, all is converted to Pb.
Original idea from book:
Take two Zn plates, make paste from PbSO4 and H2O and place it between Zn plates. Immerse all in NaCl solution and wait. PbSO4 will change to Pb
sponge, Zn react to ZnSO4. It works, but can take many days to complete reaction.
Modifications:
use cut iron sheet (not powder - hard to remove), may be Zn coated, iron wire, it does not matter. Take bottle, put iron, Pb salt (or mixture), water
and some acetic acid (citric, sulfuric, etc). Stop the bottle and shake it from time to time. End of reaction can be indicated by immersing a piece of
clean iron for some time (in slurry) - surface of iron should not be covered by Pb sponge.
Remove remaining iron, decant, wash, dry, melt Pb. Do not store prepared dry Pb for a long time, because it slowly covers with oxide.
I tested Al sheets but I got hard to remove "Al(OH)3" hard particles. I think it is question of bad conditions (just tested it only to see if it works
at all). Maybe NaOH instead of acidic solution would be better ? Not tested, but if someone wants, worth trying.
Important : Pb in car battery always contains some Sb, even few %. |
I agree with Kmno4 on the use of wet methods as the thought of lead metal fumes is a safety issue for me.
This reference "Level Course in Chemistry", by J. G. R. Briggs, page 275, link: http://books.google.com/books?id=449tWjfDgVUC&pg=PA275&a... notes that PbO dissolves in hot aqueous NaOH (or in hot dilute HNO3):
PbO + 2 NaOH --> Na2PbO2 + H2O
Actually, I have dissolved Pb only the slow way with Acetic acid and H2O2, so I cannot testify as to the speed of this reaction.
Then, per the authors comment on page 276, if so desired, the lead salt can be oxidised to a brown precipitate of PbO2 by an alkaline H2O2 or alkaline
hypochlorite (done this).
|
|
Bezaleel
Hazard to Others
 
Posts: 444
Registered: 28-2-2009
Member Is Offline
Mood: transitional
|
|
Okay, well, that's a lot of comments . Let me post two pictures of the 'ingot' I
cast in my effort to clean the jug. The piece of material pictured weighs 20 g. Total amount of lead electrode used was 50 g, not 100 as estimated
earlier. Total amount of flux was around 20 g, based on hydrated CaCl2 (hydrate still unknown, not tested).
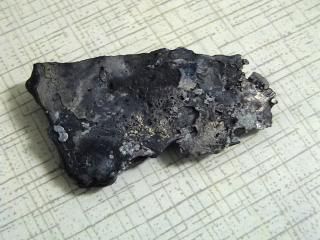
Left: on top of the 'ingot', a few small spheres of lead can be seen.
Right: bottom of the 'ingot' (has a metallic sheen here and there, but cannot be seen on picture).
Closer inspectation reveals that the bottom contains very impure lead. The top seems to be a hard still undetermined mixture.
Before starting to test with completely different types of lead regaining experiments, my next step should be redoing the experiment with more and
clean flux.
A second step could be the use of borax. Lime and sodiumcarbonate melt at 825 C (aragonite) and 850 C, which both lie above the temperatures I can
reach.
I know that both antimony and calcium are probably present in the lead. These experiment are of exploratory nature, so to speak. A real nice workup of
lead from these electrode plates is still far away.
Edit: I dissolved pieced of a Pb electrode in 70% HNO3, but lower concentrations (40-50%) worked better for me. There was a large amount of gunk
coming off that plate though, which was difficult to separate. I managed to do this through a fine fritte, but nothing would then work to clean the
fritte, neither acids, nor lye, nor ammonium sulphate, which is capable of dissolving PbSO4.
I decided that I'd like to have reasonably pure lead ingots, and work their purity up when needed.
[Edited on 4-5-2013 by Bezaleel]
|
|
12AX7
Post Harlot
   
Posts: 4803
Registered: 8-3-2005
Location: oscillating
Member Is Offline
Mood: informative
|
|
The mass should be a composite matrix of salts, amorphous carbon (I can't imagine the sugar left anything else behind, it should be fully pyrolyzed),
and lead in varying oxidation states.
I agree with watson, my understanding of smelting is that CO is required. With no access to catalytic oxygen, nor solubility for gas*, the oxides
just kind of sit there. I doubt PbO has too much solubility in chlorides (an addition of fluorides would probably change that, however), so reaction
would then be limited by solubility of CO and PbO, and solid-state diffusion (on the lucky particles that are touching). Otherwise, if you continue
to raise the temperature (until PbO melts, at which point the chlorides will be evaporating nicely, too), you'll get good reaction rates (I will note
that PbO is corrosive towards Fe, even though the Pb metal sloughs off without dissolving iron or its oxide).
*Hydrogen and steam appear to be pretty soluble in salt, which is unfortunate when it comes to aluminum, which loves to om nom nom hydrogen gas when
molten. Of course, the gas comes out when it freezes, mushrooming and ruining castings. The traditional solution is bubbling either inert gas
(remove H2 by dilution) or chlorine (consume it as HCl, much more reactive, faster).
I don't see any way PbCl2 would form. Well, maybe not entirely. I suppose there's an outside chance that the double displacement CaCl2 + PbO
<--> CaO + PbCl2 could occur. PbCl2 isn't the most stable salt out there (though more stable than, say, CuCl2), but CaO (at least in bulk form)
has comparable binding energy to MgO, which as we know, is a powerful endpoint in certain reactions.
The salt should fall apart, slowly but surely, with an extended soak in water. Bash it up beforehand to make smaller pieces. I have found that, when
using a large excess of chlorides to clean aluminum slag, the oxides form a tough composite which does, however, dissolve in water, releasing the
oxides within. Test for pH: if it's basic, some PbCl2 may've formed...and since disproportionated...hmm...never mind.
Next time, try heaping lead into the container and heating it. Then add charcoal on top. I'm guessing you'll start with a mushy powdery mess, of
various lead-related colors (until it begins glowing too bright to see its own color). The charcoal will start out cold, then start sparking to life
on top. Stir it in. You should start to see metal droplets appearing. Let it cook for a while, stirring occasionally. Eventually, you should
notice the liquid level underneath has risen, while the amount of crap on top has decreased. If you want to coalesce better, you can melt some salt
on top (but use pre-melted salt ingots, don't introduce moist raw chemicals to a hot melt!), then pour everything off. Borax and silica based slags
are traditional, of course, but the powder will have more surface area for reduction, so don't go nuts (otherwise, think about trying to reduce metal
out of a lump of lead crystal glass!).
Tim
|
|
Bezaleel
Hazard to Others
 
Posts: 444
Registered: 28-2-2009
Member Is Offline
Mood: transitional
|
|
Thinking about what may have been formed, two things came to mind, that might explain the insolubility of the product: CaSO4, and CaPbO2/CaPbO3. Mixed
with PbCl2, metallic lead and carbon, I could imagine a hard solid may form.
|
|
watson.fawkes
International Hazard
   
Posts: 2793
Registered: 16-8-2008
Member Is Offline
Mood: No Mood
|
|
Quote: Originally posted by Bezaleel  | A second step could be the use of borax. Lime and sodiumcarbonate melt at 825 C (aragonite) and 850 C, which both lie above the temperatures I can
reach. | All these oxides melt together, with a wide variety of eutectics with locally minimal melting points.
Don't take the isolated melting points as anything like determinative. I pulled up a couple of eutectic mixtures from a ceramics site:
Lead Oxide and Boric Oxide Eutectic 493 °C
Lead Oxide, Boric Oxide and Silica Eutectic 485 °C
The site isn't comprehensive, unfortunately, but it is indicative.
Also, remember that high-melting oxide combinations in this context are also called "slag" or "dross".
|
|
Bezaleel
Hazard to Others
 
Posts: 444
Registered: 28-2-2009
Member Is Offline
Mood: transitional
|
|
I just tried to clean the "crucible", but after pouring out all that could be poured out, and melting new salt, and repeating this twice, the result
was still a grey mass. This looks far from promising.
When I cleaned the "crucible" afterward, I also found it now has a small hole in it, so appaerently the mixeture has eaten itself a way through the
stainless steel. I decided that for now, this will end my activities in melting the battery lead under salt mixtures.
The last post on page 1 of kmno4, mentiones a different procedure, based on the difference in oxidation potential of Pb and Zn. Maybe this will be a
better starting point. The result from that method will still need melting and work up, but maybe it will remove much of the lead compounds. Supposed
it will yield a mixture of Pb an Pb oxides, then melting it together under borax could provide a good route to a relatively pure metal, as
watson.fawkes has mentioned.
[Edited on 6-5-2013 by Bezaleel]
|
|
Pages:
1
2 |
|