Pages:
1
..
14
15
16
17
18
..
48 |
Swede
Hazard to Others
 
Posts: 491
Registered: 4-9-2008
Member Is Offline
Mood: No Mood
|
|
I'm still trying to find some titanic, intergalactic alumina corporation to send me, a peon, some colloidal boehmite. No luck yet, but I've got some
leads.
Nickel Nitrate - the patent calls for some, I believe as a grain refiner. It is complexed with .6H2O, and I tried a simple experiment to dehydrate a
10g sample. Into a stainless bowl, furnace fired up to 250, a standard dehydration temp, and 6 hours later, I had a molten puddle of green,
carcinogenic goo. WTF? 6 hours at 250 should have driven off every speck of water. Then I looked up the characteristics of nickel nitrate. melts
at 57??!! BOILS at 137?! What exactly is boiling off? The water? I can see it decomposing, but not boiling. Am I turning it into Nickel Oxide and
various nitrogen oxides? Weird stuff. You're paying a lot of money for water with Ni(NO3)2.6H2O Can anyone elaborate on the decomp mechanism?
All that remains is enough lead nitrate to stock the big bath. I am going to try several micro setups so that I do not ruin a lot of lead nitrate
with additives like surfactants, Bismuth and nickel salts, etc.
|
|
tentacles
Hazard to Others
 
Posts: 191
Registered: 11-11-2007
Member Is Offline
Mood: No Mood
|
|
Swede: If it's anything like copper nitrate, it might be forming a ligand with the water.. Did you see any red/yellow gas over the hot salt, or in the
furnace? I got some copper nitrate to the point of being a gooey mass, it was like a semi-liquid puck at room temp. You pretty much just stop when NO2
starts evolving - that's as dry as you're going to get it.
Do you have a buchner funnel and vacuum flask? If not, I HIGHLY recommend getting one. Absolutely invaluable, either a vacuum filtration setup or a
pressure filter. You could fabricate either one out of random stuff, though. IE make a vacuum adaptor for a glass carboy and just have a hose going to
nested buckets or some arrangement providing the filtration aspect.
|
|
Rosco Bodine
Banned
Posts: 6370
Registered: 29-9-2004
Member Is Offline
Mood: analytical
|
|
You can't dehydrate nickel nitrate by heating without decomposing it to a basic nitrate and then to an oxide.
The hexahydrate is the normal stable form and is gotten
by gentle evaporation at below 57C of solutions. Quantifying
what you have from the solubility data for saturated solutions is close enough for this sort of work, and you shouldn't really need to make up
solutions from a previously isolated hexahydrate crystal form, if that is inconvenient.
From the following chart it would appear there is also a stable trihydrate which would crystallize from cooling hot solutions above 57C ,
transitioning to the hexahydrate for evaporative crystallizations at below 57C. For our purposes it should be accurate enough to stipulate that at
room temperature a saturated solution of nickel nitrate is 50% by weight nickel nitrate, calculated on the anhydrous molecular weight basis of 182.7
g/mole. The hexahydrate is 290.8 g/mole. These figures reconcile with the molar water ratio
charted at 20C, confirming the percentage solubility is expressed on the basis of the anhydrous salt.
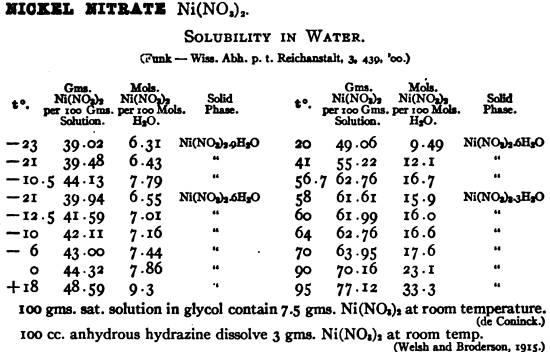
[Edited on 11-12-2008 by Rosco Bodine]
|
|
Swede
Hazard to Others
 
Posts: 491
Registered: 4-9-2008
Member Is Offline
Mood: No Mood
|
|
Thanks, gentlemen. The Nickel Nitrate was more of an oddity than anything else. I knew there'd be people who would have an insight.
I ran an H2O test with the plating rig and heater commbination. I attached an old Ti mesh cathode to the rotating anode arm, and fired everything up.
The heater, and the cartridge inserts, worked perfectly, and a 500 watt, 120V heater encased in copper JUST approached boiling, in the sense that the
water surrounding the Cu tube was close to, but did not actually boil. Temp came right up and stabilized nicely.
Bad part. Bubbles formed, even with no electricity. Rotation kicked off the larger, but tapping on the boom arm, and forcing a bit of vibration
worked better, so I would conclude that vibration is a superior method to eliminate bubble formation. Fortunately, I have a lot of room on the boom
arm, and am going to attach a vibrator, so I will have the option of switched rotation, vibration, or both.
An ohmmeter connected between the bath, and the anode connector, showed good continuity through the structure and especially the carbon brush.
Interestingly, turning ON the rotation REDUCED resistance. It was almost as if the brush is in a superior, preferred state when the system is
rotating.
|
|
watson.fawkes
International Hazard
   
Posts: 2793
Registered: 16-8-2008
Member Is Offline
Mood: No Mood
|
|
Quote: | Originally posted by Swede
Interestingly, turning ON the rotation REDUCED resistance. It was almost as if the brush is in a superior, preferred state when the system is
rotating. | Think about the difference between static and dynamic coefficients of friction. I suspect there's
a connection, although it's not immediately apparent to me what it might be at the nano-level.
|
|
chief
National Hazard
  
Posts: 630
Registered: 19-7-2007
Member Is Offline
Mood: No Mood
|
|
Platinum is used in sparc-plugs; maybe that could be some source for electrodes ? :
http://staging.platinum.pncl.co.uk/uploaded_files/Pt%202006/...
|
|
Rosco Bodine
Banned
Posts: 6370
Registered: 29-9-2004
Member Is Offline
Mood: analytical
|
|
Please indulge my off topic diva break, this is too beautiful to go unlinked and worth the listen
http://www.youtube.com/watch?v=a69KFAdUhIk&feature=relat...
http://www.youtube.com/watch?v=XizWzGkBjow&feature=relat... (with lyrics)
http://www.youtube.com/watch?v=O-19fSeKcXs&feature=relat... (with kisses)
and of course with love
[Edited on 12-12-2008 by Rosco Bodine]
|
|
Swede
Hazard to Others
 
Posts: 491
Registered: 4-9-2008
Member Is Offline
Mood: No Mood
|
|
Some simple updates - I'm waiting on my big Chemsavers 10kg lead nitrate delivery. I've got 1 kg currently, and am tempted to do some mini
experiments. The two big things are the completion and successful testing of the heating system. The cartridge heaters have exceeded my
expectations, with one caveat... it is important to keep the wattage density as low as possible, yet still have sufficient power to heat and hold the
bath in weather that's pretty damned cold. The way to do this is run them at reduced voltages. This in itself presents problems. A 240VAC cartridge
heater that is listed as a kilowatt can be a bulky beast. I've got a pair of them, and their dimensions are 1/2" diameter by about 7" long. At
120V, they will put out 250 watts apiece. Singly, or paired, they will raise a 2 gallon bath of ice water to near boiling in about an hour. BUT (big
but) the entire heater needs to be immersed, or you end up with a hot section above the liquid.
This may or may not be a problem. The incoloy sheathes can handle complete air exposure. The sheathe will turn gray, and my guess is there just
might be a visible glow if the watt density is high enough. But this is simply too concentrated a heat, and for a liquid bath, it needs to be spread
a bit by some sort of additional sheathing which conducts heat well, OR using multiple, lower-wattage devices strategically placed in the bath.
In my freebie "bonus" bunch of cartridge heaters, there are a pair of 120V micro-heaters about the size of a pencil perhaps 3" long. I'm trying to
figure out a material that I can drill and install these heaters into, which I can them immerse in the bath, with no ill effect to the chemistry of
the plating reaction.
Cu is a good choice, but I worry - if the Cu is not tied to the cathodes electrically, will there be a problem? As the nitric acid concentration
increases, the Cu sheathes will begin to dissolve, donating Cu++ ions to the bath, not necessarily a bad thing.
Titanium would work, but Ti has very poor heat conductance. Plus, I have no thick slabs of Ti. Aluminum? I have a massive stock of aluminum in all
shapes, sizes, and alloys, but again, I am concerned about pollution of the plating bath with unwanted metals. Nickel would work, but I have no pure
Ni in an appropriate form.
My original plan to rotate is still the plan. The shape of the cathode(s) will be hemispherical, with the spinning anode on the convex side. I
originally planned on two cathodes, but if the anode spins, what's the point in two? I can simplify things by using a single cathode, and this in
turn will allow for smaller test baths.
Xenoid's idea of vibration was simply genius, and I decided to incorporate a vibrational system into the boom arm suspending the anode. An old
Pittman DC motor was cannibalized, and mounted:

Part of the system is an adjustable weight. When combined with a variable DC supply to the vibration motor, the effect is amazing... I can go from a
gentle, high-frequency pulsation, to a vibration so intense, the entire rig will walk off the bench. Somewhere in between is a good setting! Ive got a dual DC lab supply that will take care of both plating and vibration.


I worked hard at using quality wiring for most of this rig, especially things such as extension wired for the RTD probe. A good source of PTFE-coated
wire is surplaus aviation wire off eBay. Like everything else for aircraft, it is top-quality stuff.

Note the waxed polyester cord to secure wire bundles. Infinitely better than cable ties.
I guess my real question today is the use of oddball metals in this plating bath for the cartridge heaters. Attaching the Cu heater sheathe to the
cathode will work, but it's a bit limiting. I'm curious espeially about Al. If Al has no problems, I will be all set.
The way this thing is turning out, if the plating fails,it will be in my technique, not the hardwer. I think I've got a system hat should plate well.
|
|
Swede
Hazard to Others
 
Posts: 491
Registered: 4-9-2008
Member Is Offline
Mood: No Mood
|
|
I forgot to add in the previous post... I mentioned that I have been talking with a guy who can hook me up with some very pure boehmite for
experimentation, but he needs further detail. Perhaps Roscoe can help with some of the data he's looking for. He's asking for a rough crystallite
size. They stock/produce 5 nm to 60nm, with a pore volume ranging between 0.4 to 1.2 ml/g. He's a really nice guy who is bending over backwards to
help me out here.
I'm thinking a moderate to larger pore volume in a smaller crystallite size would be ideal, so long as they are not mutually exclusive.
Quote: |
We also make calcined aluminas if you are looking for gamma or delta alumina and also we have dispersible aluminas whnich are fully dispersible in
aqueous or mildly acidic media |
Suggestions?
|
|
Rosco Bodine
Banned
Posts: 6370
Registered: 29-9-2004
Member Is Offline
Mood: analytical
|
|
Kaowool and a blender maybe 
I would try the long fiber stuff and low porosity, specify
a filler reenforcing fiber material like is added to plastics for strengthening and the previously calcined dispersible
stuff would be good. Gamma whiskers is what you want.
First you crawl through the high grass just before dawn
when the gammas are known to feed , 
Well it's about the middle of Advent,
so maybe you'd like this other pretty one too.
I mean things are supposed to gradually become more cheerful and celebrative
http://www.youtube.com/watch?v=nKIPMMPPcu4&feature=relat...
[Edited on 12-12-2008 by Rosco Bodine]
|
|
tentacles
Hazard to Others
 
Posts: 191
Registered: 11-11-2007
Member Is Offline
Mood: No Mood
|
|
I got that Ti mesh material today for cathodes - I'd like you fellas to put an eyeball on this and tell me what you think...
http://pyrobin.com/files/sdc10065.jpg
I took a picture of a section where some of the coating had rubbed off due to poor packing methodology. This is a dead ringer for MMO mesh, and I got
a crapton of this stuff, dirt cheap. Specifically, I paid about $30 for 3 3x30" (with a 1" bent portion) strips. The guy is still selling some on
ebay, off and on.
|
|
12AX7
Post Harlot
   
Posts: 4803
Registered: 8-3-2005
Location: oscillating
Member Is Offline
Mood: informative
|
|
Put voltage to it and see if it works!
|
|
jpsmith123
National Hazard
  
Posts: 764
Registered: 24-6-2005
Member Is Offline
Mood: No Mood
|
|
Dann2 thanks for the interesting paper (but now how do I get rid of the annoying black helicopters that have been harassing me since I downloaded
it?).
Anyway, what I found very interesting, was the inconsistent results regarding the tests with cold-rolled steel. I wonder why did 123-57c experience
such limited corrosion compared to 154-7a and 154-11-4, when they were all just plain untreated cold rolled steel?
Unfortunately they didn't say whether or not 123-57c made any perchlorate, but if it did, I would say that the result was promising.
|
|
Swede
Hazard to Others
 
Posts: 491
Registered: 4-9-2008
Member Is Offline
Mood: No Mood
|
|
Update - ready to plate. 11 kg lead nitrate on hand, PbO, Pb sheet, K Na Tartrate, and all the necessary gadgets.
Ever since Roscoe mentioned a boehmite or similar coating/catalyst carrier, I have been in contact with a salesman from an excellent company, who is
helping me a bit in selection of a boehmite that might be suitable for this process. We've narrowed it down - sample almost inbound.
He sent me an interesting PDF file with info and data on dispersible aluminas. I have posted it to my web site for download. I have not read it,
just glanced at it, but it looks excellent. Enjoy:
Boehmite dispersion and rheology brochure
|
|
garage chemist
chemical wizard
   
Posts: 1803
Registered: 16-8-2004
Location: Germany
Member Is Offline
Mood: No Mood
|
|
What's wrong with "alumina hydrate" from pottery supply shops?
I got me 2kg of this, it was EUR 2,95 a kg. It's a very fine, soft, heavy white powder. It evolves lots of water vapor and turns into a "fluidized
bed" at ca. 300°C.
|
|
Rosco Bodine
Banned
Posts: 6370
Registered: 29-9-2004
Member Is Offline
Mood: analytical
|
|
The type of alumina we were curious may have value is a nano structural whisker, a fiber form of material which can act as a reenforcing material and
adhesive in pyrolytically formed oxide coatings for anodes. They use the stuff commercially in bonding the catalyst oxides to the honeycomb ceramic
substrate in catalytic converters,
to produce an extremely tenacious and durable coating.
It just seemed natural to see if it would similarly be of benefit in making baked MMO coatings on anodes more
durable as well. But it is a very specific physical form
of alumina which is useful, as only this whisker form
has the necessary strength as a reenforcing fiber.
The stuff is also used as a filler in polymers and paints,
and for thermoset gluing teflon to glass and metal substrates. It is also used as a reenforcing fiber in
strengthening refractory ceramics.
[Edited on 18-12-2008 by Rosco Bodine]
|
|
Swede
Hazard to Others
 
Posts: 491
Registered: 4-9-2008
Member Is Offline
Mood: No Mood
|
|
What I find very interesting is the "pore size". A typical Boehmite alumina has a pore volume of 1.4ml per gram, meaning it can capture and carry
significant catalytic materials. If it sticks, if the catalysts adequately conduct, it could be a player.
And it's free. Can't hurt to play with it!
|
|
Swede
Hazard to Others
 
Posts: 491
Registered: 4-9-2008
Member Is Offline
Mood: No Mood
|
|
On my recent trip, I went through several of the patents relating to lead dioxide plating, and learned quite a bit. One of them is that the cathode
current density should be 2x to 3x the current density of the anode... this means a fairly small cathode. Question - do we count the entire surface
area of the Cu cathode, or only the portion exposed to the flow of electrons? If I've got a sheet Cu cathode in there, do you ignore the side away
from the anode?
The impression I got was that this process should be well within the reach of the average home chemist. Obviously, this is not the case, and hundreds
or thousands of failed PbO2 anodes attest to this fact.
I've got everything... got the temp controller, the correct surfactants, Cu and Ni nitrates, Bi salts, NaF, got a rig that will rotate, vibrate, do
both, or neither. Good power supplies. Lead nitrate (lots) and PbO, sheet Pb too. THIS WILL WORK! IT MUST! 
I've had some thoughts unrelated to the patent description. None of the patents I read discussed PbO2 over MMO... they were using graphite, tantalum,
Ti, and other substrates, with success. My thoughts related to the preparation of the substrate. Obviously, it must be clean, but there are
different definitions of clean.
Under a microscope, the MMO surface is quite rough, and probably ends up containing quite a bit of air trapped in pores as it enters the plating bath.
I was thinking about a pre-plate dip or etch, using one of these three solutions:
1) Pure water, or water with a minute amount of surfactant
2) dilute HNO3
3) a small amount of the actual plating electrolyte
THEN, pulling a vacuum. Get the air out, get the liquid into every single crack or crevice, so once the plating starts, it will be 100% coverage.
For a substrate like Ti, I think using an abrasive blaster on it would be an excellent preparatory step, or failing that, a scotch-brite pad to
mechanically and minutely score the metal surface; then, into the etch/prep bath.
Sound good? Or a waste of time? I'm going to try plating one of my small test anodes probably tomorrow.
|
|
watson.fawkes
International Hazard
   
Posts: 2793
Registered: 16-8-2008
Member Is Offline
Mood: No Mood
|
|
Quote: | Originally posted by Swede
I was thinking about a pre-plate dip or etch, using one of these three solutions: [...]
1) Pure water, or water with a minute amount of surfactant [...]
THEN, pulling a vacuum. Get the air out, get the liquid into every single crack or crevice, so once the plating starts, it will be 100% coverage.
| Sounds like a good idea. Go with plain water and surfactant, then rinse with plain water. I don't see any
advantage to nitric acid; it would just remove oxide coating without contributing anything particular to surface characteristics. Using your plating
bath would be fine, but unnecessary and requiring more cleanup.
|
|
dann2
International Hazard
   
Posts: 1523
Registered: 31-1-2007
Member Is Offline
Mood: No Mood
|
|
Hello Folks,
Quote: | Originally posted by Swede
On my recent trip, I went through several of the patents relating to lead dioxide plating, and learned quite a bit. One of them is that the cathode
current density should be 2x to 3x the current density of the anode... this means a fairly small cathode. Question - do we count the entire surface
area of the Cu cathode, or only the portion exposed to the flow of electrons? If I've got a sheet Cu cathode in there, do you ignore the side away
from the anode?
|
Patent No. US 4444642 is a LD over MMO. It's the only one that I know of. This patent was mentioned before here somewhere.
Can you remember the patent number that said the current density on the cathode should be 2 or 3 times the CE on the anode when plating LD?
Hard to know if you should count the total area of Cathode.
Are you going for an Alpha coat (Tartrate bath, or high CE in Nitrate bath at the start) before a Beta coat with the anode you are going to make?
With a tank the size that you have you are going to have excellent anodes (unless you are going to make absolutely huge anodes).
Plating Ti mesh (or flat plate with lots of holes), as opposed to a flat plate or rod, greatly alleviates the adhesion problem IMO. It will be
unlikely that the LD will start to flake off. Substrate and LD are simply married like wire and concrete!
The big issue is electical contact between LD and Ti, or to put it another way, the lack of electrical contact because of the dreaded formation of Ti
Oxide. The interface coat looks after that aspect. Pt, Tin Oxide, MMO and Ebonex (a conductive Oxide of Ti) are the only interface coats mentioned in
the patents etc that I am aware of.
As far as cleaning the MMO, I would give it a wash in some solvent to degrease it, alcohol sounds good. Try to avoid handling it in the first place.
Don't go near the MMO coated Ti with an abrasive or an etch bath. 
If you were starting from scratch (no pun intented) making MMO coated Ti you would of course etch and abrade the Ti.
Dann2
|
|
dann2
International Hazard
   
Posts: 1523
Registered: 31-1-2007
Member Is Offline
Mood: No Mood
|
|
Quote: | Originally posted by jpsmith123
Dann2 thanks for the interesting paper (but now how do I get rid of the annoying black helicopters that have been harassing me since I downloaded
it?).
Anyway, what I found very interesting, was the inconsistent results regarding the tests with cold-rolled steel. I wonder why did 123-57c experience
such limited corrosion compared to 154-7a and 154-11-4, when they were all just plain untreated cold rolled steel?
|
FIRSTLY, about the helicopters. Did you try pegging you shoes at them? Or a welly (with a brick in it!!).
I did not get time to read/study the paper. I just can't see Steel making Perk.
I did notice that they got Magnetite to melt at about 1000C by adding some other Oxides. 1000C is more easily done than 1500C (pure Magnetite). It's
not a great Anode material though.
Sorry about double post.
Dann2
[Edited on 22-12-2008 by dann2]
|
|
Rosco Bodine
Banned
Posts: 6370
Registered: 29-9-2004
Member Is Offline
Mood: analytical
|
|
I'll go out on a limb here and suggest something untried and unreported which might make an interesting "primer-activator-bonding agent" over the MMO
as a possible sealant and adhesion enhancing strategy for the electrodeposited PbO2.
After you have baked your spinel interface and MMO coating , maybe dip the anode into a Bi / Sn Pytlewski polymer and then simply dry it, or only dry
the final coat
if earlier coats of the polymer have been baked. Then put the anode into the plating bath and apply the PbO2.
|
|
Swede
Hazard to Others
 
Posts: 491
Registered: 4-9-2008
Member Is Offline
Mood: No Mood
|
|
Quote: | Originally posted by dann2
Hello Folks,
Patent No. US 4444642 is a LD over MMO. It's the only one that I know of. This patent was mentioned before here somewhere.
Can you remember the patent number that said the current density on the cathode should be 2 or 3 times the CE on the anode when plating LD?
Hard to know if you should count the total area of Cathode.
Are you going for an Alpha coat (Tartrate bath, or high CE in Nitrate bath at the start) before a Beta coat with the anode you are going to make?
With a tank the size that you have you are going to have excellent anodes (unless you are going to make absolutely huge anodes).
Plating Ti mesh (or flat plate with lots of holes), as opposed to a flat plate or rod, greatly alleviates the adhesion problem IMO. It will be
unlikely that the LD will start to flake off. Substrate and LD are simply married like wire and concrete!
The big issue is electical contact between LD and Ti, or to put it another way, the lack of electrical contact because of the dreaded formation of Ti
Oxide. The interface coat looks after that aspect. Pt, Tin Oxide, MMO and Ebonex (a conductive Oxide of Ti) are the only interface coats mentioned in
the patents etc that I am aware of.
As far as cleaning the MMO, I would give it a wash in some solvent to degrease it, alcohol sounds good. Try to avoid handling it in the first place.
Don't go near the MMO coated Ti with an abrasive or an etch bath. 
If you were starting from scratch (no pun intented) making MMO coated Ti you would of course etch and abrade the Ti.
Dann2 |
Dann2, the patent that describes cathode current densities at 2X to 3X anode is 2,945,791, Gibson, who plated graphite. He went on in patent
3,463,707 with further refinements. To me, the most useful has been 4,038,170, Rhees. He goes into great detail on acidic bath plating with added Bi
salts (improves efficiency) and Ni nitrate, for a finer grain, which I feel is very important for both adhesion and protection of the substrate.
For my initial experiments, I am going to start with an acid plate setup. I understand the problems of the electrolyte getting at the Ti and forming
non-conducting oxides. But unless the guys in these patents are flat-out lying, the plating quality can be such that (hopefully) the chlorate
electrolytes simply cannot reach the Ti. That means a coating of adequate thickness, fine grain, and excellent coverage and adhesion, must be
executed.
I haven't plated a single molecule yet, but I'm hopeful. I'm going to start with the MMO. For the cathode, given the current density question, I am
going to use the Cu-encapsulated immersion heaters as cathodes... the surface area should be close.
FWIW I took a scrap of MMO mesh and immersed it in concentrated nitric, with no effect whatsoever that I could see, although the nitric was a bit old
and probably not the strongest.
The other problem is the use of surfactants. They may be an important key in getting a good plate, but the patents definitely describe the breakdown
of the surfactant molecules in a highly acidic bath... as it breaks down, the bath is rendered ineffective. This would no doubt suck if 4 kg lead
nitrate is ruined in this manner, so keeping the acid concentration on the low end of the acceptable range might be a good idea. The offending
surfactant fragments CAN be removed with amyl alcohol and a sep funnel (or decant) once the bath is neutralized, so there is a way to rescue a
polluted lead nitrate bath.
If this works, and I gain some experience, it would be an awesome thing to plate pure Ti successfully and have it perform in a chlorate cell.
|
|
Swede
Hazard to Others
 
Posts: 491
Registered: 4-9-2008
Member Is Offline
Mood: No Mood
|
|
Roscoe, I am interested in all forms of this process, and I appreciate your suggestions. My chemistry is not strong anymore, and I need to research
some of what you are saying before I can even comment on it! It's a bit above me. But any sort of conductive surface prep over Ti that would help
PbO2 adhere would be nothing but good, and would be an interesting field of experimentation all by itself. The experimental process wouldn't be
difficult... prepare a few mini-anodes, with the variable being surface prep, then either mechanically test the adhesion, or better yet prepare small,
identical (per)chlorate cells and see how they do, using identical currents and electrolyte concentrations.
I do have the boehmite guy in correspondence, and hopefully he'll come through for me. That would be fun to play with. Have to figure out what sort
of catalyst could fill those pores, and the best way to create a coating with the colloidal boehmite/catalyst that will adhere to Ti or some other
suitable metal.
|
|
Rosco Bodine
Banned
Posts: 6370
Registered: 29-9-2004
Member Is Offline
Mood: analytical
|
|
Quote: | Originally posted by Swede
Roscoe, I am interested in all forms of this process, and I appreciate your suggestions. My chemistry is not strong anymore, and I need to research
some of what you are saying before I can even comment on it! It's a bit above me. |
Don't sell yourself short there. It's the same effect achieved with the Pytlewski polymer as is gotten with the fibrous alumina in terms of the
electrostatic effect which makes it a
"wetting agent" that sticks even to teflon as an adherent film
residue after drying alone. The firing of the material in place
reverses the electrostatic charge for the completely dehydrated oxides that result , so the new hydrated material
sticks by electrostatic attraction to the oxide or different oxides of underlying coatings, or overcoatings as the case may be. The unfired Pytlewski
film should therefore act as
an indigenous "wetting agent" for the MMO and also likely attract the electrodepositied PbO2, acting like a glue between the two. If this works like
I think it might, then
it might eliminate the need for a surfactant in the plating bath, and it might also act as an oxygen barrier. I'm not really sure if the conductivity
is there and good enough for the unfired film of Pytlewski polymer, but I suspect it is probably okay, only an experiment would tell for sure.
Quote: |
But any sort of conductive surface prep over Ti that would help PbO2 adhere would be nothing but good, and would be an interesting field of
experimentation all by itself. The experimental process wouldn't be difficult... prepare a few mini-anodes, with the variable being surface prep,
then either mechanically test the adhesion, or better yet prepare small, identical (per)chlorate cells and see how they do, using identical currents
and electrolyte concentrations.
I do have the boehmite guy in correspondence, and hopefully he'll come through for me. That would be fun to play with. Have to figure out what sort
of catalyst could fill those pores, and the best way to create a coating with the colloidal boehmite/catalyst that will adhere to Ti or some other
suitable metal. |
I'll have to go back and compare again the parallel for
the hydrated boehmite and Pytlewski polymer materials again, but I think I made the correct observation on the
similar properties for those materials in terms of their
usefulness as "wetting agents". These two materials
act as sort of a molecular scale "electrostatic powder coating"
which settles onto certain surfaces like a magnet and doesn't come off, having a natural adhesion. It would seem like a candidate material to use as a
carrier for a dopant for an interface film also on a baked coated Ti substrate, where
you use a Pytlewski polymer having the desired dopant such as cobalt, or bismuth, or perhaps vanadium, ect. in the polymer, dry the film on the
substrate, and then bake it.
Multiple layers should stick like glue to the previously applied layers below, since the electrostatic charge reverses for the pyrolyzed oxides
material, with respect to the wet or merely dried on freshly applied material. I suppose there is a sort of covalent cross linkage between the
"active" polymer and the heat depolymerized oxide, or similar oxide. If it works like I am thinking, the stuff would literally be like epoxy in terms
of adhesion, it would be there to stay, married to the
surface on a molecular level.
[Edited on 22-12-2008 by Rosco Bodine]
|
|
Pages:
1
..
14
15
16
17
18
..
48 |
|