Pages:
1
..
8
9
10
11
12 |
plante1999
International Hazard
   
Posts: 1936
Registered: 27-12-2010
Member Is Offline
Mood: Mad as a hatter
|
|
Very interesting work markx, looking forward new experiments
I never asked for this.
|
|
roXefeller
Hazard to Others
 
Posts: 463
Registered: 9-9-2013
Location: 13 Colonies
Member Is Offline
Mood: 220 221 whatever it takes
|
|
Quote: Originally posted by VladimirLem  |
yepp...its pretty hard to get it these days cause you can make diacetylmorphine with it....and many many interesting explosives too IF you had it...
|
I have to pull the thread on this one. What other EM come from Ac2O?
|
|
markx
National Hazard
  
Posts: 646
Registered: 7-8-2003
Location: Northern kingdom
Member Is Offline
Mood: Very Jolly
|
|
Well...HMX via modification of the Bachmann process is one of the most rewarding options. But only imagination is the limit, since nitric acid + Ac2O
form a powerful nitrating agent with catalytic properties in some instance.
Exact science is a figment of imagination.......
|
|
Dornier 335A
Hazard to Others
 
Posts: 231
Registered: 10-5-2013
Location: Northern Europe
Member Is Offline
Mood: No Mood
|
|
Hardly of any practical interest, but nitric acid + Ac2O can nitrate cellulose to more than 13.5% N, something that nitric acid + sulfuric acid fails
to do. Other than that, I agree with markx.
|
|
Motherload
Hazard to Others
 
Posts: 245
Registered: 12-8-2012
Location: Sewer
Member Is Offline
Mood: Shitty
|
|
Markx.
Great work.
Since Glacial Acetic Acid is a lot easier to come by and probably cheaper.
Have you tried using GAA to "concentrate" the HNO3 ?
One would think it would have a tendency to "hold" water like many other concentrated acids do, thereby letting you get away with less AcAn.
I couldn't find a chart on affinity of liquids towards water.
I wanted to try similar method, but using conc. H3PO4 to "hold" water in the reaction.
I can buy AcAn for the chem supply guy ... As long as I only buy a litre every few months. "It's to remove lead out of barrels for customers that
shoot cast bullets."
So I like to conserv it and it is like $60 a litre.
"Chance favours the prepared mind"
"Fuck It !! We'll do it live !!"
|
|
markx
National Hazard
  
Posts: 646
Registered: 7-8-2003
Location: Northern kingdom
Member Is Offline
Mood: Very Jolly
|
|
Quote: Originally posted by Motherload  | Markx.
Great work.
Since Glacial Acetic Acid is a lot easier to come by and probably cheaper.
Have you tried using GAA to "concentrate" the HNO3 ?
One would think it would have a tendency to "hold" water like many other concentrated acids do, thereby letting you get away with less AcAn.
I couldn't find a chart on affinity of liquids towards water.
I wanted to try similar method, but using conc. H3PO4 to "hold" water in the reaction.
I can buy AcAn for the chem supply guy ... As long as I only buy a litre every few months. "It's to remove lead out of barrels for customers that
shoot cast bullets."
So I like to conserv it and it is like $60 a litre. |
I doubt very much that glacial acetic acid has the needed affinity towards water to overcome the affinity of nitric acid. Basic reasoning in terms of
similar to similar center interactions tends to suggest against it. Besides, dilution of the reaction media with acetic acid will tend to push the
reaction mechanism towards the formation of HMX:
http://www.sciencemadness.org/talk/viewthread.php?tid=32296#...
Basivcally it is the same Bachmann system, but diluted with glacial acetic acid.
What I have considered though is the MAGNAC process for concentrating of nitric acid above the azeotropic point:
Attachment: US2860035.pdf (445kB) This file has been downloaded 818 times
In theory it looks quite excellent....the dessicant Mg(NO3)2*2H2O is regenerable under vaccuum, dirt cheaply
available as the heptahydrate and no fear of sulfate contamination in the end product. In fact I have already constructed a pump operated closed loop
aspirator station for the purpose. I also managed to aquire a lovely brand new czhechoslovakian belt driven 2 stage vacuum pump for free (built in
1982), but after realizing the beauty of the thing I found no heart to use it for the acid process. I know for sure that it will be a short death
sentence for the pump, no matter what kind of scrubbers are used. Therefore I opted for the aspirator station which can handle all kinds of corrosive
crap and still be virtually indestructible.
If that fails, then there is always the possibility to use the vacuum station to dehydrate the Mg nitrate heptahydrate to the dihydrate state and use
sulfuric acid to perform the classic nitric acid distillation from the nitrate salt of magnesium. The appeal of using Mg nitrate is in the fact that
MgSO4 is formed instead of the bisulfates (hydrogen sulfates HSO4- ), hence double the yield is possible with the same amount of H2SO4 as compared to
Na or K nitrate. Even if we consider the 2 moles of remaining water in the dihydrate (which is presumably the limit for dehyrating Mg nitrate befor
decomposition occurs even under vacuum), the yield is still better than using Na or K nitrate.
Exact science is a figment of imagination.......
|
|
markx
National Hazard
  
Posts: 646
Registered: 7-8-2003
Location: Northern kingdom
Member Is Offline
Mood: Very Jolly
|
|
I did regenerate an old batch of RFNA by redistillation and addition of urea yielding about 50ml of near anhydrous HNO3 (measured density of 1,5g/ml).
The resulting acid was ever so slightly yellow colored and I decided to try it in the Bachmann synthesis without further purification. The resulting
outcome was observed:
Raw materials:
Feed I- 3,36h hexamine + 5g glacial acetic acid
Feed II- 5,5g AN + 5ml WFNA (slight contamination of NO2)
Feed III- 15g Ac2O
As the AN and HNO3 were combined in flask, a rather noticeable amount of NO2 was released and the mixture remained slightly yellow. An indication of
persistant NO2 contamination and a clear sign of the need to further purify the acid before synthesis.
Heel in reactor:
3g glacial acetic acid
3g Ac2O
0,6ml Feed II
Synthesis temperature 75C (PID controlled), magnetic stirring was applied to the reactor chamber.
The heel was let equlibriate to 65C and additions of liquid feeds proceeded during 20minutes in 7,5 parts as follows:
1ml Feed I
1ml Feed II
2ml Feed III
Immediately after the first addition of feeds a heavy precipitate of RDX started to form. But the shape of crystals was different this time. Not a
dense granular form, but a more flocculent voluminous sedimentation was observed. The exotherm was very violent and after the second feed the
temperature spiked upwards of 82C for a short period of time. PID control was shut off at that point and addition of ice to the waterbath was used to
keep the temperature in the range of 75C optimum. In retrospective the feeds should have been divided into more portions to avoid the spiking of
temperature and a more consistant reaction. In spite of that, the precipitate gathered at amounts that turned the reactor contents into a thick sludge
and made stirring very inefficient. Before the last portion of feeds was introduced, the reactor contents were resembling more a solid phase than a
liquid. An amazing difference compared to the synthesis with 70% HNO3.
After the completion of liquid feeds the reaction was run for an additonal 15min at 75C. The cristals were filling the liquid phase to the full amount
and no separation of phases occurred. The cristals were all in the flocculent voluminous form. A suspicion of side reactions having taken place and
low melting contaminants in the product arised.
After the 15 minutes the temperature of water bath was raised to 97C and 50ml of warm water was added to the reactor chamber. There was no phase
separation even as the volume of the reactants was more than doubled by the addition of water. The flocculent mass filled the liquid to full extent
and energetic evolution of gas was observed in the cristalline mass. A clear sign of side products decomposing in the acidic media. A decicion was
made to digest the products in the reactor at 97C for an extended time until no more signs of decomposition are seen.
After 3 hours of digestion at 97C the cristalline mass had decreased in volume by four times and acquired a more dense and slightly granular
appearance. Still the precipitate looked nothing like the product formed in pervious synthesis. No more evolution of gas was observed and the heating
was shut off. Product was crashed into 400ml of cold water, filtered, washed with water, neutralised by sodium bicarbonate and washed with water again
to remove the salts.
Dried yield was registered as 7,1g (67% of theoretical)
Melting point could not be measured at the moment as the heating element only reached a temperature of 175C...no signs of softening were observed at
that point though.
I must reconstruct the MP apparatus on a smaller base to allow for higher temperatures...the rectifier diode heat sink that I use as the substrate is
clearly too much for the 100W heating elemant and does not allow for higher melting substances to be analysed correctly at the moment.
Product is clear white and of a very fine cristalline appearance. I sucpect the slight NO2 contamination in the acid is responsible for the side
products and the alteration of the cristalline structure of the resulting RDX. Also the fluctuations in temperature due to high feeding rate might be
the cause of inconsistency. Further investigations will follow....
Exact science is a figment of imagination.......
|
|
roXefeller
Hazard to Others
 
Posts: 463
Registered: 9-9-2013
Location: 13 Colonies
Member Is Offline
Mood: 220 221 whatever it takes
|
|
That is an interesting theory for contamination. It seems hard to separate the effect of the inconsistent temperatures. Will you be able to test it
by fully cleaning the acid first?
|
|
markx
National Hazard
  
Posts: 646
Registered: 7-8-2003
Location: Northern kingdom
Member Is Offline
Mood: Very Jolly
|
|
Quote: Originally posted by roXefeller  | That is an interesting theory for contamination. It seems hard to separate the effect of the inconsistent temperatures. Will you be able to test it
by fully cleaning the acid first? |
The reaction system is rather complicated, that much is true, but by doing a minimum of two dedicated synthesis runs I believe that some light can be
shed upon the cause of the observed effects.
1) Synthesis with same conditions and feed rates with similar temperature fluctuations, but a highly purified acid being used.
2) Synthesis with the contaminated acid, but with smaller and more frequent additions of the feeds, allowing for a better temperature control.
I tend to lean towards the NOx contamination being the main cause for changing the synthesis course and structure of the product (and the side
products). The reason being that I also attemtpted the synhtesis with true RFNA and this run produced only 20% of impure yield with the same
flocculent appearance. As the synthesis failed I did not report it, but in light of recent observations I think it can serve as a guide to the
cause....
Exact science is a figment of imagination.......
|
|
roXefeller
Hazard to Others
 
Posts: 463
Registered: 9-9-2013
Location: 13 Colonies
Member Is Offline
Mood: 220 221 whatever it takes
|
|
The Bachmann synthesis is also focused on dilution of the nitric acid with acetic acid. Your first run was effectively dilute nitric/acetic acid
after the acetic anhydride dried out the 70% nitric acid. The second run wasn't nearly so. That could also be an effect that might confound the
result.
|
|
markx
National Hazard
  
Posts: 646
Registered: 7-8-2003
Location: Northern kingdom
Member Is Offline
Mood: Very Jolly
|
|
Right...I conducted the synthesis 2 (same contaminated acid, but better temp control and smaller more frequent additions of feeds). To achive better
temperature control I added the feeds in 20 portions timed according to the internal temperature of the reaction mixture. That meant a reaction time
of approximately double the duration (30min). Hence I also lowered the reactor temperature to 65C. The Bachmann patent specifically mentions the
lowering of reaction temperature if a longer addition time of feeds is expected. Lo and behold....heavy, sandy, glistening crop of cristals started
to form immediately after the first addition of feeds and continued to grow in bulk to the completion of the feeds. A sight almost identical to the
one observed in my very first synthesis with the 70% acid and double anhydride amount. The temperature hovered between 63-70C during the
reaction....as more portions of feeds were added, the amount of thermal mass in the reactor grew and fluctuations decreased accordingly.
After the additions were complete, the layer of heavy coarse cristals occupied about a third of the volume of liquid phase...a profound difference
compared to previous run where the contents of reactor resembled cottage cheese at the end of reaction and liquid phase was almost nonexistent.
The reaction was let run at 65C for an additional 10minutes and then removed from the hot water bath and placed into a cool one to bring the
temperature down to 30C. A profound amount of crystals precipitated during the cooling phase up to the extent of almost filling 3/4 of the liquid
phase. The crystals that formed during the cooling phase were not as coarse and resembled the product of previous run after digestion phase at 97C.
The contents of reactor were crashed into 400ml of warm water, filtered, washed with water, neutralised with sodium bicarbonate and washed again with
water to remove any remaining salts. The yield was squeezed more or less dry between filter papers and the wet mass was registered as 21,7g.
The synthesis was conducted with 4,5g of hexamine and the respective amounts of reagents....comparing to the result of first synthesis which had a wet
product mass of 14,75g registered under similar conditons (and using 4,2g hexamine). Should not be too shabby at all. The expected dry yield could be
up to 12g (84% theoretical)......but tomorrow will tell
I guess my suspicions about the slight NOx contamination being the cause of altered state in previous run were unfounded....seems that slow and
continuous additions of feeds are the key to a successful reaction.
[Edited on 5-9-2014 by markx]
Exact science is a figment of imagination.......
|
|
roXefeller
Hazard to Others
 
Posts: 463
Registered: 9-9-2013
Location: 13 Colonies
Member Is Offline
Mood: 220 221 whatever it takes
|
|
Quote: Originally posted by markx  |
The reason being that I also attemtpted the synhtesis with true RFNA and this run produced only 20% of impure yield with the same flocculent
appearance.
|
That is a good thing to report. I can't seem to find the solubility of NOx in nitric acid, but I suspect it can be very high for degraded acid.
Hoping for good news on the dried product.
|
|
NeonPulse
Hazard to Others
 
Posts: 417
Registered: 29-6-2013
Location: The other end of the internet.
Member Is Offline
Mood: Isolated from Reality! For Real this time....
|
|
Great work! it looks like you are getting closer to the ideal conditions for this type of RDX synthesis. i 'm interested to see how your yield looks
when dried properly. are you going to replicate this procedure to be sure of the same yield or tweak it a little more? 84% of theroretical is nothing
to be sneezed at and seems pretty optimal already.
|
|
markx
National Hazard
  
Posts: 646
Registered: 7-8-2003
Location: Northern kingdom
Member Is Offline
Mood: Very Jolly
|
|
I just weighed the product and the dry mass registered as 10,47g (73%).....not the 12g that I was hoping, but still a very noticeable improvement.
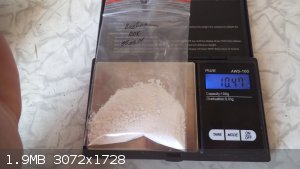
The product is of nice granular appearance with very little fine fraction. Looks like very fine white sand,,,,would almost be a shame to recristallise
it 
Actually the yield is exactly on par with the one reported in Bacmann patent 2798870: 74%
I guess the seventies will be a realistic expectation for overall yield with the Bachmann process, although the maximum is stated as up to 90%. Still
I believe that this will be more an exception that enforced the rule.
If I take into account that I just managed to conjure 10,5g of nitramine by using 6,7ml of HNO3 and 24ml of Ac2O then I find this is really excellent.
I shall reconstruct my melting point apparatus this weekend and then hopefully we can have a preliminary peek at the purity of the product.
[Edited on 6-9-2014 by markx]
Exact science is a figment of imagination.......
|
|
markx
National Hazard
  
Posts: 646
Registered: 7-8-2003
Location: Northern kingdom
Member Is Offline
Mood: Very Jolly
|
|
I reconstructed my melting point apparatus and got it to a state where it can reach upper limit of 290C.....should be appropriate for most energetics
now 
As for the RDX, the melting points were as following:
1) Flocculent product from the "strange" synthesis - 195C with previous softening at 185C
2) Granular product from last synthesis - 195C with previous softening at 180C
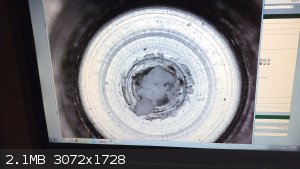
It actually seemed that the flocculent product had less impurities (makes sense as it was simmered in acid for 3 hours), but the difference was quite
small and again corellated very well with the values from the patent (196C-197C ). Not a absolutely pure product, but very well within limits of
acceptance.
Meanwhile I have also aquired a set of TLC plates and further analysis can be performed...
Exact science is a figment of imagination.......
|
|
markx
National Hazard
  
Posts: 646
Registered: 7-8-2003
Location: Northern kingdom
Member Is Offline
Mood: Very Jolly
|
|
I had remnants (15ml) of last years WFNA in my cold depository that had really degraded to the point of questionable functionality. Still I decided to
throw it all in the pot and cook up a last batch Bachmann style with the "not so white" NA. To my amazement it worked beautifully:
http://www.youtube.com/watch?v=slH2iGKyv3w
The video is from the purification stage of the process. The percipitate is the crude rdx formed in the synthesis stage (about 20g worth). The reactor
contents are diluted with water and simmered for several hours at 95-97C to decompose unstable impurities. The heavy evolution of gas that can be seen
in the flask will continue for at least 2 hours and is a clear sign of the side products decomposing. Sometimes it can become so intense that the
contents overflow an spew out of flask. All the flocculent fraction disappears during the simmering and the precipitate becomes uniformly granular
and very heavy in texture. This is also accompanied by a quite sizeable decrease in the volume of precipitate, but the mass loss is reasonably
negligible.
[Edited on 5-1-2015 by markx]
Exact science is a figment of imagination.......
|
|
ScubaDiver
Harmless
Posts: 1
Registered: 8-2-2015
Member Is Offline
Mood: No Mood
|
|
Call me frugal but is not 50 cents per gram a bit pricey?
|
|
Hennig Brand
International Hazard
   
Posts: 1284
Registered: 7-6-2009
Member Is Offline
Mood: No Mood
|
|
That is because he is working at lab scale, once the process is finalized and he increases production to pilot scale and then to plant scale prices
will significantly drop. 
Found a good journal article on HDN production a while back which I thought others might find useful.
Attachment: Hexamethylenetetramine Dinitrate (HDN) - The Precursor for RDX Production by Bachmann Process.pdf (976kB) This file has been downloaded 1713 times
"A risk-free world is a very dull world, one from which we are apt to learn little of consequence." -Geerat Vermeij
|
|
Hawkguy
Hazard to Others
 
Posts: 326
Registered: 10-10-2014
Location: British Columbia (Canada eh!)
Member Is Offline
Mood: Body is Ready
|
|
What are the pros to making RDX through a separate HDN synth? I just go straight from Hexamine, and so far the only hangup is the waste of the excess
Nitric Acid....
|
|
Hennig Brand
International Hazard
   
Posts: 1284
Registered: 7-6-2009
Member Is Offline
Mood: No Mood
|
|
That is the big advantage, much less highly concentrated, high purity, nitric acid is required.
"A risk-free world is a very dull world, one from which we are apt to learn little of consequence." -Geerat Vermeij
|
|
Hawkguy
Hazard to Others
 
Posts: 326
Registered: 10-10-2014
Location: British Columbia (Canada eh!)
Member Is Offline
Mood: Body is Ready
|
|
True, I see where you're coming from. But still.... The time and effort of doing two separate Nitrations would be a pain in the ass.
|
|
Hennig Brand
International Hazard
   
Posts: 1284
Registered: 7-6-2009
Member Is Offline
Mood: No Mood
|
|
The laborious and technically demanding part for most people is getting the nitric acid as concentrated as possible and at the same time as free of
nitrogen oxides as possible. When distilling nitric acid from a mixture of it and sulfuric acid a fraction can be collected first which is suitable
for the last stage (HDN to RDX) and once the distillate concentration starts to drop below what is acceptable the next fraction collected can be used
to produce the HDN feed from hexamine.
"A risk-free world is a very dull world, one from which we are apt to learn little of consequence." -Geerat Vermeij
|
|
markx
National Hazard
  
Posts: 646
Registered: 7-8-2003
Location: Northern kingdom
Member Is Offline
Mood: Very Jolly
|
|
I've actually found that the nitric acid distillation is very much like the distillation of fermented alcohol fractions...at first a highly
concentrated fraction that is heavily contaminated with nitric oxides comes over (like the "heads" or aldehyde ester fraction-EAF of alcohol) and can
be separately collected. Then the "heart" starts to distill over, this being a pure, almost white, highly concentrated fraction that is most suitable
for the nitration of heterocyclics. After that a gradually less concentrated "tail" distills over. The "heads" and "tails" can be used for less
demanding nitrations.
Preparation of HDN is very straight forward and quick from the point of conducting the actual reaction....the more tricky part is dealing with the
hygroscopic, poisonous and water soluble nature of the stuff and yet getting it completely dry before further nitration to heterocyclics. Vacuum
drying and storage under desiccant is the way to go for an anhydrous HDN precursor. If that is not done, the benefits of getting by with less acid go
out the window very quickly. But really, apart from scientific curiosity and having a personal inclination towards performing extra work I see no
point in using the HDN route in amateur practice. Just way too much complications for a rather questionable end gain. It might hold the promise of
cost saving in commercial scale enterprises where waste nitric acid from e.g. PETN nitration is used to form the HDN. But I guess such things are not
in our league of operations
Exact science is a figment of imagination.......
|
|
Hennig Brand
International Hazard
   
Posts: 1284
Registered: 7-6-2009
Member Is Offline
Mood: No Mood
|
|
Yes, I failed to mention that the "heads" (the tiny fraction which comes over at the start of the distillation with high nitrogen oxide(s) content)
should be collected separately from the first main fraction to be collected. The size of the fractions collected does depend on the proportions and
concentrations of nitric and sulfuric acid in the boiler as well as how it is run. From what I have read, most of the problems with HDN occur because
of contact with water and using heat in attempts to dry it. If the wet HDN is quickly washed with a suitable volatile solvent to remove water and then
the solvent is quickly removed (ideally with vacuum) before placing the HDN in airtight storage (ideally with a desiccant) the problem should be
solved for the most part. I think that waste acids can sometimes be very effectively used, even in an amateur setting.
I made an Excel spreadsheet a while ago, to help determine the quantities of nitric and sulfuric acids of various strengths to use and when and what
to collect when conducting a distillation. Here is a link to where the spreadsheet is attached:
http://www.sciencemadness.org/talk/viewthread.php?tid=15676&...
They are only small files so I might as well attach them here since they could be useful to others.
Attachment: Concentrating HNO3 - Overcoming the HNO3_H2O Azeotrope Using H2SO4.xlsx (79kB) This file has been downloaded 777 times
Attachment: Concentrating HNO3 - Overcoming the HNO3_H2O Azeotrope Using H2SO4 (compatibility mode).xls (97kB) This file has been downloaded 708 times
[Edited on 9-2-2015 by Hennig Brand]
"A risk-free world is a very dull world, one from which we are apt to learn little of consequence." -Geerat Vermeij
|
|
Rosco Bodine
Banned
Posts: 6370
Registered: 29-9-2004
Member Is Offline
Mood: analytical
|
|
Quote: Originally posted by roXefeller  |
That same thread where underground got the Mg(NO3)2 concept from also has relevant discussion from Rosco (http://www.sciencemadness.org/talk/viewthread.php?tid=4701&a...). Using 12:1 by mass HNO3 to hexamine is wasteful of acid (Rosco thinks it can be
done with 100ml HNO3: 40 g HDN, or ~8.3:1 acid:hexamine by mass). It was discussed that the yield was dependent on final reaction temperature. So it
seems the patent authors increased the HNO3 to compensate for the 30C reaction. BTW that patent just seems odd. Why are they using a hexahydrate to
dehydrate? And why are they writing new patents on a 70 year old process (direct nitration of hexamine from HNO3)? As far as trying Mg(NO3)2 to
dehydrate, go ahead, someone has to put patents to practice. You should probably dehydrate the salt first. But you should keep in mind other
concepts that reduce the acid use, detailed in that RDX thread, such as urea nitrate stabilized decomposition at high temps, and ammonium nitrate
supplementation. And you should read Bachmann's work. He suggests varying cleaving mechanisms of hexamine depending on temperatures and dilutions,
which result in different paths to the nitramine. |
With regards to the possible usefulness of Mg(NO3)2 as a reagent in nitrolysis and nitrations where its dehydration property towards nitric acid may
have favorable effect by tying up any water that is known to reduce the yield, I have continued to look at the literature and learn more, posted in
another thread where several mixed nitrate systems have been identified which have potential usefulness.
http://www.sciencemadness.org/talk/viewthread.php?tid=4457&a...
The journal article and patent of Griffith relates to the binary system of NH4NO3 and Mg(NO3)2 and of particular interest is the composition based on
weights that would be 65% Mg(NO3)2 and 35% NH4NO3 expressed as percentage for the anhydrous materials.
There are conflicting articles about the dehydration of Mg(NO3)2 alone being possible to achieve at atmospheric pressure using heat alone to drive off
the water, without some decomposition leading to impurity of the basic salt.
I believe that the acidic nature of NH4NO3 in a combined melt with Mg(NO3)2 tends to oppose decomposition that would occur for Mg(NO3)2 heated alone,
and that using vacuum to aid the final dehydration of a 65/35 mixture of Mg(NO3)2 + NH4NO3 would produce a mixture which could be useful in nitrolysis
and nitration reactions for sequestration of water.
The journal article by Griffith describes that the 65% Mg(NO3)2 mixture with NH4NO3 is an anhydrous melt which is prone to form a monolith of a
supercooled glass upon cooling, which is a definite complication to simple manipulation and is undesirable.
However, Griffith also describes that if the solidified glass is reheated to 110C, the metastable glass suddenly crystallizes with a large exotherm.
Whether this results in a spontaneous crumbling and disintegration of the material I do not know for certain, but that would be likely to be the
effect. If true, the reagent would be self milling and when cooled would be ready for the uses it is anticipated it would be valuable.
There are lower percentage mixtures where the content of Mg(NO3)2 on the anhydrous basis is below 38% of the combined mixture with NH4NO3 which are
not prone to glass formation as the potential issue that would require breaking up a monolith of a solidified melt, since those lower percentage
Mg(NO3)2 mixtures with NH4NO3 do crystallize on cooling. And those lower Mg(NO3)2 content mixtures could likewise still be useful even with their
lower content of the material that would have the desired ability to tie up water, there would still be present only to a lessened extent the
dehydrating property adjusted downward for the lower Mg(NO3)2 content.
An advantage for the lower Mg(NO3)2 content mixtures would be a lower melting point and easier dehydration during preparation of the anhydrous
reagent, and elimination of the issue of glass formation which would require reheating to 110C to cause crystallization for the 38% to 65% or greater
Mg(NO3)2 mixtures.
[Edited on 27-3-2015 by Rosco Bodine]
|
|
Pages:
1
..
8
9
10
11
12 |