Pages:
1
2
3
..
12 |
B(a)P
International Hazard
   
Posts: 1139
Registered: 29-9-2019
Member Is Offline
Mood: Festive
|
|
Nickel aminoguanidine diperchlorate
I was recently inspired by Dr L to try some experimentation with transition metal perchlorates and aminoguanidine following on from the thread on
copper and lithium hexamine perchlorates, titled ‘LL8 from Dr. Liptakov’.
Having nickel perchlorate hexahydrate at hand I thought that would be a good start.
There is not a lot of information on this compound, but I did find a link to patent EP2450330A2 in another thread on SM.
Firstly, I wanted to check my basic workings in case I have missed something. The patent calls for 1.36 g of aminoguanidine bicarbonate slurried with
10 mL of dH2O to be reacted with 1.4 g of nickel perchlorate hexahydrate dissolved in 1 mL of dH2O.
Based on my calculations that is a vast excess of aminoguanidine bicarbonate.
1 C2H8N4O3 + 1 Ni(ClO4)2.6(H2O) --> 1 CO2
+ 1 CN4H6Ni(ClO4)2 + 7 H2O
compound | mm | #M | m (g)
C2H8N4O3 | 136.1 | 0.009992652 |1.36
Ni(ClO4)2.6(H2O) | 365 | 0.003835616 | 1.4
CN4H6Ni(ClO4)2 | 332 | 0.003835616 | 1.273424658
Surely more like 3.5 g of nickel perchlorate hexahydrate would be required?
Molar ratios aside, I decided to try and replicate the patent first to see if I could get the reaction to work.
The above mentioned two solutions were mixed, heated and taken to a boil for approximately 5 minutes then left to cool for 4 hours.
Small needle like dark orange crystals of presumably nickel aminoguanidine diperchlorate were present as was a fine metallic precipitate present as a
sheen on top of the reaction mixture. The fine precipitate is not metallic nickel as it is not magnetic. It also dissolves readily in concentrated
hydrochloric acid to form a straw-coloured solution. I am guessing it may be nickel oxyhydroxide? Given this is forming when aminoguanidine
bicarbonate is in great excess, maybe yields cannot be improved, but this will be tested soon.
The yield was 0.51 g or 4%, which is what they reported in the patent. Later in the week when I have time, I will try again with a stoichiometric
amount of nickel perchlorate hexahydrate.
I have also tried reacting aminoguanidine bicarbonate with perchloric acid then adding nickel perchlorate, but no reaction occurs. The pH must be
adjusted to greater than 8 before a reaction occurs and then it proceeds as described above.
I have not yet accurately measured friction or impact sensitivity, but both seem low on initial testing. It is very flame/heat sensitive and detonates
confined from about 5 to 10 mg of mass.
Once I have the reaction better optimised I will do some tests on its performance and report back.
In the meantime any insight on my questions above (repeated below for clarity) would be greatly appreciated.
1. Have I missed something in my workings or is aminoguanidine bicarbonate in great excess in the reaction as reported by the patent?
2. What is the fine black sheeny side product?
Thanks in advance for any assistance.
If anyone is interested I can post more detail on my reactions to date.
More to come following some performance testing.
Edit
typo in reaction scheme
[Edited on 13-2-2022 by B(a)P]
|
|
MineMan
International Hazard
   
Posts: 1013
Registered: 29-3-2015
Member Is Offline
Mood: No Mood
|
|
All of those reactions call for excess bicarbonate. I don’t know why, I am not educated in chemistry. Though, I would have expected your yield to be
much better. When ammonium perchlorate is used ammonia raises the PH of the solution.
Remember it’s bicarbonate, your formula shows mono carbonate.
[Edited on 14-2-2022 by MineMan]
|
|
katyushaslab
Hazard to Self

Posts: 81
Registered: 19-1-2021
Member Is Offline
Mood: precipitating
|
|
I think Microtek would be the person to ask about this, maybe he can share his procedure?
He references using this material in this post: https://www.sciencemadness.org/whisper/viewthread.php?tid=15...
|
|
B(a)P
International Hazard
   
Posts: 1139
Registered: 29-9-2019
Member Is Offline
Mood: Festive
|
|
I tried the reaction again, but this time with stoichiometric amounts and the yield was much better (68%). The reaction also did not produce the
previous unwanted side product. Still plenty of yield optimising required. One of the issues is that the product is very soluble in water so I am
going to start trying some different solvents.
Strange that the patent had such an obvious error.....
|
|
MineMan
International Hazard
   
Posts: 1013
Registered: 29-3-2015
Member Is Offline
Mood: No Mood
|
|
Quote: Originally posted by B(a)P  | I tried the reaction again, but this time with stoichiometric amounts and the yield was much better (68%). The reaction also did not produce the
previous unwanted side product. Still plenty of yield optimising required. One of the issues is that the product is very soluble in water so I am
going to start trying some different solvents.
Strange that the patent had such an obvious error.....
|
That’s a good idea. Please keep us updated. From watching videos my understanding is that it is not only soluble but in time the water destroys the
product and a black mass results. You don’t want that, we don’t want that, nobody, I mean nobody wants that!!!
|
|
Microtek
National Hazard
  
Posts: 872
Registered: 23-9-2002
Member Is Offline
Mood: No Mood
|
|
Regarding the molar ratios, remember that it bis(aminoguanidine)nickel diperchlorate so you need two moles of AQ per mole of nickel perchlorate. I
don't know why you say that the product is very soluble in water, mine is not, although it does react with water.
I think maybe the AQ ligands are sufficiently labile that they are replaced (partially?) with H2O. At any rate, the complex loses the red colour and
turns a pale tan that then darkens to blackish.
I looked at one of the papers that the patent references. It's about complexes of aminoguanidines and nickel, and one of the things they talk about is
that some of the compounds are very readily oxidized by atmospheric oxygen. This may account for the black colouring.
[Edited on 24-2-2022 by Microtek]
|
|
B(a)P
International Hazard
   
Posts: 1139
Registered: 29-9-2019
Member Is Offline
Mood: Festive
|
|
Thanks Microtek that helps a lot.
I have redone my calculations based on it being (bis)aminoguanidine and can now assess my yield properly.
I had noticed when I was washing the product with water I could see crystals very quickly disappearing, I thought they were going into solution rater
than decomposing, the decomposition explains why I could not get it back out of solution.
I had also read the about the oxidation by atmospheric oxygen that you reference, which I was convinced was the big killer on my yield. I had proposed
to try and do the reaction in an atmosphere or argon to avoid this, but I think in the first instance I will try again with the correct stoichiometric
amounts based on the product being (bis)aminoguanidine and as little water as possible.
|
|
B(a)P
International Hazard
   
Posts: 1139
Registered: 29-9-2019
Member Is Offline
Mood: Festive
|
|
So the rain has finally eased allowing some further testing of this product.
I don't have the means to accurately assess friction, though I have not been able to set it off using friction.
I have a crude impact tester with a 2 kg weight and the material was set off reliably from a drop height of 5 cm. For comparative purposes I get 3 cm
for mercury fulminate.
400 mg was loaded into a brass cavity 4.5 mm ID with 0.5 mm walls at 1.23 g/cm3.
Fuse was inserted and packed in place with NC.
The target was 30 mm mild steel RHS with 1.5 mm walls.
The results can be seen in the attached.
I was hoping to get full penetration. I was also a bit disappointed with the density that I could achieve. More to come when I can improve the
density.
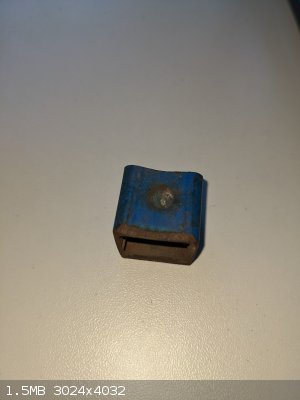
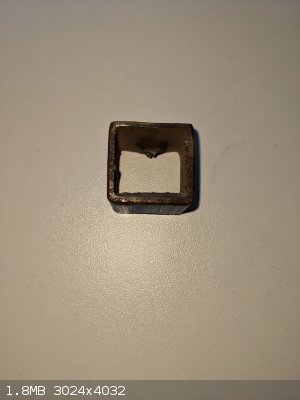
Edit - corrected an error in the cavity dimensions.
[Edited on 10-3-2022 by B(a)P]
|
|
Microtek
National Hazard
  
Posts: 872
Registered: 23-9-2002
Member Is Offline
Mood: No Mood
|
|
When preparing this material, I recommend continuing the stirring throughout the 4 hour precipitation period. This way you get uniform small crystals
rather than the relatively long needles that are usually obtained if you let it sit undisturbed. This might help with the loading density, as well as
the impact sensitivity.
|
|
Laboratory of Liptakov
International Hazard
   
Posts: 1411
Registered: 2-9-2014
Location: Technion Haifa
Member Is Offline
Mood: old jew
|
|
400mg in cavity inner diameter 0,45 mm ....? Wall 0,05 mm...?...
It is diameter syringe needle.... ...?
Development of primarily - secondary substances CHP (2015) Lithex (2022) Brightelite (2023) Nitrocelite and KC primer (2024)
|
|
B(a)P
International Hazard
   
Posts: 1139
Registered: 29-9-2019
Member Is Offline
Mood: Festive
|
|
Ha ha ha, good catch. If I got that performance out of that diameter I would have been very happy. The correct dimensions are 4.5 mm ID and 0.5 mm
walls.
[Edited on 10-3-2022 by B(a)P]
|
|
Laboratory of Liptakov
International Hazard
   
Posts: 1411
Registered: 2-9-2014
Location: Technion Haifa
Member Is Offline
Mood: old jew
|
|
Brass wall 0,5 mm and ID 4,5 mm is good result for examined compound. Into 1,5mm steel. Basic ratio between ID and thickness of steel is 3:1.
It is base for measurement. Similarly as ID 6 mm (examined compound) and 2 mm steel target. Also 3:1....
Development of primarily - secondary substances CHP (2015) Lithex (2022) Brightelite (2023) Nitrocelite and KC primer (2024)
|
|
B(a)P
International Hazard
   
Posts: 1139
Registered: 29-9-2019
Member Is Offline
Mood: Festive
|
|
Quote: Originally posted by B(a)P  | So the rain has finally eased allowing some further testing of this product.
I don't have the means to accurately assess friction, though I have not been able to set it off using friction.
I have a crude impact tester with a 2 kg weight and the material was set off reliably from a drop height of 5 cm. For comparative purposes I get 3 cm
for mercury fulminate.
400 mg was loaded into a brass cavity 4.5 mm ID with 0.5 mm walls at 1.23 g/cm3.
Fuse was inserted and packed in place with NC.
The target was 30 mm mild steel RHS with 1.5 mm walls.
The results can be seen in the attached.
I was hoping to get full penetration. I was also a bit disappointed with the density that I could achieve. More to come when I can improve the
density.
|
This was tried again with a finer crystal size.
The same cavity dimensions, loading weight and target material were used. This time the achieved loaded density was 1.62 g/cm3. Not a lot
of difference was observed in the outcome. The smaller piece on the left is loaded at 1.23 g/cm3 (previous attempt) and on the right 1.62
g/cm3. The higher density cap seemed to have slightly more penetration, though more was expected. Without some replications this can not be
seen as significantly different.
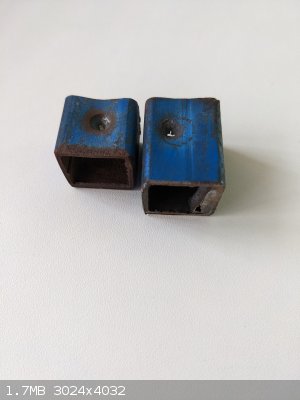
|
|
MineMan
International Hazard
   
Posts: 1013
Registered: 29-3-2015
Member Is Offline
Mood: No Mood
|
|
Quote: Originally posted by B(a)P  | Quote: Originally posted by B(a)P  | So the rain has finally eased allowing some further testing of this product.
I don't have the means to accurately assess friction, though I have not been able to set it off using friction.
I have a crude impact tester with a 2 kg weight and the material was set off reliably from a drop height of 5 cm. For comparative purposes I get 3 cm
for mercury fulminate.
400 mg was loaded into a brass cavity 4.5 mm ID with 0.5 mm walls at 1.23 g/cm3.
Fuse was inserted and packed in place with NC.
The target was 30 mm mild steel RHS with 1.5 mm walls.
The results can be seen in the attached.
I was hoping to get full penetration. I was also a bit disappointed with the density that I could achieve. More to come when I can improve the
density.
|
This was tried again with a finer crystal size.
The same cavity dimensions, loading weight and target material were used. This time the achieved loaded density was 1.62 g/cm3. Not a lot
of difference was observed in the outcome. The smaller piece on the left is loaded at 1.23 g/cm3 (previous attempt) and on the right 1.62
g/cm3. The higher density cap seemed to have slightly more penetration, though more was expected. Without some replications this can not be
seen as significantly different.
|
You should be able to get a density of 1.8-1.9.
|
|
MineMan
International Hazard
   
Posts: 1013
Registered: 29-3-2015
Member Is Offline
Mood: No Mood
|
|
Quote: Originally posted by B(a)P  | Quote: Originally posted by B(a)P  | So the rain has finally eased allowing some further testing of this product.
I don't have the means to accurately assess friction, though I have not been able to set it off using friction.
I have a crude impact tester with a 2 kg weight and the material was set off reliably from a drop height of 5 cm. For comparative purposes I get 3 cm
for mercury fulminate.
400 mg was loaded into a brass cavity 4.5 mm ID with 0.5 mm walls at 1.23 g/cm3.
Fuse was inserted and packed in place with NC.
The target was 30 mm mild steel RHS with 1.5 mm walls.
The results can be seen in the attached.
I was hoping to get full penetration. I was also a bit disappointed with the density that I could achieve. More to come when I can improve the
density.
|
This was tried again with a finer crystal size.
The same cavity dimensions, loading weight and target material were used. This time the achieved loaded density was 1.62 g/cm3. Not a lot
of difference was observed in the outcome. The smaller piece on the left is loaded at 1.23 g/cm3 (previous attempt) and on the right 1.62
g/cm3. The higher density cap seemed to have slightly more penetration, though more was expected. Without some replications this can not be
seen as significantly different.
|
You should be able to get a density of 1.8-1.9.
|
|
B(a)P
International Hazard
   
Posts: 1139
Registered: 29-9-2019
Member Is Offline
Mood: Festive
|
|
I pressed the nickel aminoguanidine diperchlorate to approximately 50 MPa, which is about as far as I can go with my setup. What pressure would you
need to achieve that kind of density?
Obviously this depends on crystal size. I tried continuous stirring to reduce size. The only other thing I can think of is to increase the reaction
temperature more rapidly, then cool rapidly to make the crystals form faster.
|
|
Microtek
National Hazard
  
Posts: 872
Registered: 23-9-2002
Member Is Offline
Mood: No Mood
|
|
I just tried pressing mine. I don't have a way to easily measure the pressure I'm exerting, but I would estimate perhaps 100 kg on a 7mm coloumn of
NAP. This would be about 20 MPa. The density I got was 1.96 g/cc.
I'm not sure that it is advantageous to press it to such high densities however.
Are you contemplating using this material as a secondary or as a single material cap filler? Personally, I would rather fill my caps with PETN, RDX or
HMX and then use 50 mg NAP to set it off. Even more preferably, I would separate the NAP (or other primary) from the rest of the explosive filler and
keep it in the fuse insert.
|
|
Diachrynic
Hazard to Others
 
Posts: 226
Registered: 23-9-2017
Location: western spiral arm of the galaxy
Member Is Offline
Mood: zenosyne
|
|
Regarding the synthesis, there is also this video: https://www.youtube.com/watch?v=aqdKN4KBqjM
He mentioned in a comment:
Quote: | I made that Ni 2Agu perchlorate by dissolving nickel acetate 1M and ammonium perchlorate 2M first in just enough cold (room temperature) water, added
all the Agu bicarbonate 2M at once, then heated on water bath with mixing, when the max. temp reached (slightly below 100°C, the bicarbonate
dissolved with effervescence), I left it for 5 minutes, then removed from the bath and left stand for a few hours. The crystals appear slowly,
gradually on standing. Then filtered and washed. The whole process was not optimized. I found if a small amount of acetic acid is added, the yields
were higher. |
This is useful since no perchloric acid is needed, but the yields are lower, I estimate around 40-50% of the theory based on used nickel.
we apologize for the inconvenience
|
|
B(a)P
International Hazard
   
Posts: 1139
Registered: 29-9-2019
Member Is Offline
Mood: Festive
|
|
Quote: Originally posted by Microtek  | I just tried pressing mine. I don't have a way to easily measure the pressure I'm exerting, but I would estimate perhaps 100 kg on a 7mm coloumn of
NAP. This would be about 20 MPa. The density I got was 1.96 g/cc.
I'm not sure that it is advantageous to press it to such high densities however.
Are you contemplating using this material as a secondary or as a single material cap filler? Personally, I would rather fill my caps with PETN, RDX or
HMX and then use 50 mg NAP to set it off. Even more preferably, I would separate the NAP (or other primary) from the rest of the explosive filler and
keep it in the fuse insert.
|
Thanks very much for trying the density and reporting back. I have found that I was not actually applying the pressure that I thought, as my press was
bottoming out on the blast guard. After modifying the guard I have just tried again and got 2.01 g/cm3 by applying to approximately 50 MPa.
The purpose of what I am doing is just to see the effects on performance by modifying loading pressure with this compound.
Thanks for the link. I had not seen that video. It appears he is doing essentially the same as I posted above (first post). He makes nickel
perchlorate from nickel acetate and ammonium perchlorate, then his procedure is more or less the same from then on.
|
|
B(a)P
International Hazard
   
Posts: 1139
Registered: 29-9-2019
Member Is Offline
Mood: Festive
|
|
I have my press guard reconfigured and now it is working perfectly. I repeated the above test, but this time managed to press to 2.01
g/cm3. Here is the result.
On a side note I have also been trying the lithium equivalent, but with no success thus far. I will report back if I manage to create anything of
interest.
|
|
Laboratory of Liptakov
International Hazard
   
Posts: 1411
Registered: 2-9-2014
Location: Technion Haifa
Member Is Offline
Mood: old jew
|
|
Good work, wall is 2 mm ? Inner diameter cavity 6 mm ?. If yes, it it good result.....
Development of primarily - secondary substances CHP (2015) Lithex (2022) Brightelite (2023) Nitrocelite and KC primer (2024)
|
|
B(a)P
International Hazard
   
Posts: 1139
Registered: 29-9-2019
Member Is Offline
Mood: Festive
|
|
The target had 1.5 mm walls and the cavity is 4.5 mm ID. I note that in this instance I inadvertantly placed the detonator over the join in the RHS.
In previous tests i had avoided the join.
|
|
Laboratory of Liptakov
International Hazard
   
Posts: 1411
Registered: 2-9-2014
Location: Technion Haifa
Member Is Offline
Mood: old jew
|
|
It are basically same ratios. Good results. Only the variable value according to the law of proportions comes into play. When the strength (behavior)
of a material varies significantly according to size. This is given by the final size of the atom and molecule...
Development of primarily - secondary substances CHP (2015) Lithex (2022) Brightelite (2023) Nitrocelite and KC primer (2024)
|
|
PellePeloton
Harmless
Posts: 2
Registered: 21-6-2022
Member Is Offline
|
|
Just a small cautionary note: Try to avoid the smoke!
I did some work at our university with this compound (which is very nice, except for this one thing) in an ordinary hood. The quantities were 30 - 100
mg and visibly the hood was capable of sucking the smoke completely from the charges.
However, every night after the tests I had a sore throat very much like after ozone exposure. Also a minor feeling of not getting oxygen out of air...
not difficulty in breathing but a strange and very unpleasant feeling.
After the third time this happened I came to think about the reaction products... the compound is ever so slightly oxygen negative, so the result is
guaranteed to contain CO and metallic nickel... the nickel is atomic having the ultimate surface area, and the products cool very fast as the gas
cloud expands. I have no knowledge or even estimate how much nickel tetracarbonyl is formed, but a little goes a long way.
The slight feeling of drowning lasted for a year, but is now completely vanished. I am not allergic to nickel.
|
|
B(a)P
International Hazard
   
Posts: 1139
Registered: 29-9-2019
Member Is Offline
Mood: Festive
|
|
Sorry to hear that this happened to you and thanks for passing on the warning. Glad to hear that you got over it eventually, a year is a long time to
be suffering such symptoms. I have always worn respiratory protection when working with nickel compounds because of their toxicity. I will be extra
careful after hearing this.
|
|
Pages:
1
2
3
..
12 |