Pages:
1
2 |
Broken Gears
Hazard to Self

Posts: 96
Registered: 7-8-2005
Location: Northern Europe
Member Is Offline
Mood: No Mood
|
|
Acid neutralizing on industrial scale
I manage a process where an ethylene oxide scrubber is a part of it.
EO is washed through a 5% sulfuric acid solution. When the ethylene glycol content reaches 30%, the efficiency falls, and the emission goes up.
Disposing of the mixture is expensive. Mostly because of the corrosive properties. I don’t have a separate tank to do a neutralizing with a base;
soda lime, NaOH or maybe Na-Carbonate.
But can I do the neutralizing when the tank is drained? If I know the volume and the acid conc. I can calculate the amount of base needed, according
to whatever base is chosen. But can it be mixed by or in a mixing valve, or is that too risky?
Any ideas on how this could be managed?
|
|
BromicAcid
International Hazard
   
Posts: 3253
Registered: 13-7-2003
Location: Wisconsin
Member Is Offline
Mood: Rock n' Roll
|
|
What volume are you talking about? You could do a slick setup with two metering pumps going to a inline mixing element with an inline pH probe and
quench it in a continuous flow process or a skid mounted setup. I mean, if you're saying you don't have a mixing tank and adding one is not an option
then this might be your best bet.
|
|
Broken Gears
Hazard to Self

Posts: 96
Registered: 7-8-2005
Location: Northern Europe
Member Is Offline
Mood: No Mood
|
|
We are talking about 9000 L
No a bad idea :-) I'll do some research on that setup.
Heat could be a concern. Could it reach 100 degrees celsius resulting in pressure in the pipes?
[Edited on 12-4-2022 by Broken Gears]
|
|
draculic acid69
International Hazard
   
Posts: 1371
Registered: 2-8-2018
Member Is Offline
|
|
Quote: Originally posted by Broken Gears  | We are talking about 9000 L
No a bad idea :-) I'll do some research on that setup.
Heat could be a concern. Could it reach 100 degrees celsius resulting in pressure in the pipes?
[Edited on 12-4-2022 by Broken Gears] |
Neutralization of h2so4 produces lots of heat
Depending on concentration,solvent,water content, solution
temperature,speed of mixing, possibility of cooling etc etc 100'c is definitely
a possibility but not a certainty.
|
|
Tsjerk
International Hazard
   
Posts: 3032
Registered: 20-4-2005
Location: Netherlands
Member Is Offline
Mood: Mood
|
|
Can't you take 10 liters or so and dump in the NaOH to see what happens?
|
|
Metacelsus
International Hazard
   
Posts: 2539
Registered: 26-12-2012
Location: Boston, MA
Member Is Offline
Mood: Double, double, toil and trouble
|
|
I would do some very careful calculations and a few smaller scale experiments before doing anything at 9000L scale!
And I wouldn't rely on this forum for chemical engineering advice.
|
|
clearly_not_atara
International Hazard
   
Posts: 2799
Registered: 3-11-2013
Member Is Offline
Mood: Big
|
|
Using NaHCO3 for neutralization will reduce the heat production significantly, but also releases plenty of gas. Foam is the major concern, though; gas
can be vented.
Olivine - MgSiO3 - has been proposed for neutralization of waste acids; it is / can be very cheap and not too exothermic, but it produces silica
powder as a byproduct and can self-passivate under the wrong conditions:
https://www.sciencedirect.com/science/article/abs/pii/S03756...
Ordinary magnesium oxide/hydroxide might do well enough to limit ∆H, and has neither of the above concerns, though I'm not sure of the price.
Probably still cheaper -- and definitely easier to handle -- than NaOH. Not sure if it's worth trying to recover/sell MgSO4.
|
|
Sulaiman
International Hazard
   
Posts: 3721
Registered: 8-2-2015
Location: 3rd rock from the sun
Member Is Offline
|
|
maybe obvious;
if neutralizing with KOH or NaOH the heat of solution (enthalpy of dissolution) is massive,
(easier to boil water than with Az. sulphuric acid)
so use a pre-cooled solution, rather than dumping in solid base.
CAUTION : Hobby Chemist, not Professional or even Amateur
|
|
Tsjerk
International Hazard
   
Posts: 3032
Registered: 20-4-2005
Location: Netherlands
Member Is Offline
Mood: Mood
|
|
Quote: Originally posted by clearly_not_atara  | Using NaHCO3 for neutralization will reduce the heat production significantly, but also releases plenty of gas. Foam is the major concern, though; gas
can be vented.
Olivine - MgSiO3 - has been proposed for neutralization of waste acids; it is / can be very cheap and not too exothermic, but it produces silica
powder as a byproduct and can self-passivate under the wrong conditions:
https://www.sciencedirect.com/science/article/abs/pii/S03756...
Ordinary magnesium oxide/hydroxide might do well enough to limit ∆H, and has neither of the above concerns, though I'm not sure of the price.
Probably still cheaper -- and definitely easier to handle -- than NaOH. Not sure if it's worth trying to recover/sell MgSO4. |
He wants to neutralize inline with a mixing valve, how would solids or gas releasing agents work there?
If heat is the problem, use colder or more dilute NaOH.
|
|
unionised
International Hazard
   
Posts: 5128
Registered: 1-11-2003
Location: UK
Member Is Offline
Mood: No Mood
|
|
You could, in principle, just run the effluent through a trough full of limestone chippings.
That will strip out most of the acidity and allow the CO2 to escape.
Is it possible to recover the glycol by distillation?
|
|
WGTR
National Hazard
  
Posts: 971
Registered: 29-9-2013
Location: Online
Member Is Offline
Mood: Outline
|
|
I have a 6000L tank, and my neighbor has a 9000L one, so I have an idea of how much solution this is. 
How quickly must the tank be drained? In one hour, overnight, one week, etc.?
What pH range is required for the "cheaper" disposal? It is likely not exactly 7.000, but a range I would think. This would be useful to know.
One idea is to continuously pump the tank volume through a mixing valve, and then run the mixed solution through a heat exchanger before it is
circulated back to the tank. If neutralizing with NaOH (for example), mix in much less than what is stoichiometrically required for the solution flow
rate through the mixer. Continuously monitor the pH of the tank over hours/days. When it achieves your target range then you're ready for disposal.
The tank itself may need some mixing/circulation.
|
|
Bmoore55
Hazard to Self

Posts: 85
Registered: 23-7-2018
Location: Texas
Member Is Offline
|
|
You should strongly consider not using either NaOH or Soda Lime as you could push this too far and risk creating a strongly basic solution that can
cause stress corrosion cracking in the base metal of your tank. Sodium bicarbonate will release a lot of CO2, but the end result should be much safer
for your tank metal and it will mitigate the thermal release when mixing.
|
|
clearly_not_atara
International Hazard
   
Posts: 2799
Registered: 3-11-2013
Member Is Offline
Mood: Big
|
|
Quote: Originally posted by Tsjerk  |
He wants to neutralize inline with a mixing valve, how would solids or gas releasing agents work there?
If heat is the problem, use colder or more dilute NaOH. |
I may not have considered the situation carefully enough.
|
|
Rainwater
National Hazard
  
Posts: 937
Registered: 22-12-2021
Member Is Offline
Mood: Break'n glass & kick'n a's
|
|
Im no expert but i like recycling in my processes. Saves money.
it sounds as if a distillation apparatus would be useful.
First the spent solution has the water removed @ 100c and returned to the start of the process, then around 150c the ethylene glycol distills out.
Next the cruid sulfuric acid can be purified or simply returned to the system.
As a result you have a useful by product to sell, less of a mess to pay disposal fees for, and less neutralizing agents to purchase.
Your basicly exchanging neutralizing reagents for distillation energy
Maybe vacuum distillation might save on the energy requirements.
There could be another method to separate these compounds.
What are your other perdicted/observed byproducts?
Edit: just did a little more research and discovered my suggestion will result in dioxane perduction as well as a lot of other byproducts
[Edited on 16-4-2022 by Rainwater]
"You can't do that" - challenge accepted
|
|
Texium
Administrator
      
Posts: 4618
Registered: 11-1-2014
Location: Salt Lake City
Member Is Offline
Mood: PhD candidate!
|
|
Also, distilling 9000 liters of liquid requires a tremendous amount of energy...
|
|
Tsjerk
International Hazard
   
Posts: 3032
Registered: 20-4-2005
Location: Netherlands
Member Is Offline
Mood: Mood
|
|
Besides the tremendous amount of energy, a 9000 liter distillation rig is huge and expensive. OP mentioned he doesn't have a vessel where he can do
the neutralization, I doubt he has the right standing by.
|
|
draculic acid69
International Hazard
   
Posts: 1371
Registered: 2-8-2018
Member Is Offline
|
|
I think the only way forward was suggested above: take 10 liters of solutin, get a few 20L buckets and a thermometer & try a few different
neutralization products & get some data. There's no going forward without doing this to see what works best for you and what doesn't & what
can be managed with what you got.
[Edited on 16-4-2022 by draculic acid69]
|
|
unionised
International Hazard
   
Posts: 5128
Registered: 1-11-2003
Location: UK
Member Is Offline
Mood: No Mood
|
|
Quote: Originally posted by Rainwater  | Im no expert but i like recycling in my processes. Saves money.
it sounds as if a distillation apparatus would be useful.
First the spent solution has the water removed @ 100c and returned to the start of the process, then around 150c the ethylene glycol distills out.
Next the cruid sulfuric acid can be purified or simply returned to the system.
As a result you have a useful by product to sell, less of a mess to pay disposal fees for, and less neutralizing agents to purchase.
Your basicly exchanging neutralizing reagents for distillation energy
Maybe vacuum distillation might save on the energy requirements.
There could be another method to separate these compounds.
What are your other perdicted/observed byproducts?
Edit: just did a little more research and discovered my suggestion will result in dioxane perduction as well as a lot of other byproducts
[Edited on 16-4-2022 by Rainwater] |
If you boil glycol with acid it turns into dioxane which is carcinogenic.
(Not dioxin which is more famous).
But if you neutralised it first then that's a much better approach.
Selling the glycol, together with savings on waste disposal costs might pay for the still.
Incidentally, the heat evolved is well documented.
https://en.wikipedia.org/wiki/Enthalpy_of_neutralization
[Edited on 16-4-22 by unionised]
|
|
Tsjerk
International Hazard
   
Posts: 3032
Registered: 20-4-2005
Location: Netherlands
Member Is Offline
Mood: Mood
|
|
I was just doing some calculations on the back of an old envelope and the solution won't get close to boiling, even if you would dump in solid NaOH.
Unless you start at ridiculously high temperatures of course.
|
|
Broken Gears
Hazard to Self

Posts: 96
Registered: 7-8-2005
Location: Northern Europe
Member Is Offline
Mood: No Mood
|
|
Thank you all so much for all the input.
I think I have underestimated the extent of this project...
With a pH at pH 6-9 we can deliver it to a Biogas-plant free of charge, and it will be converted to district heating = helping the local community.
Another solution is to neutralize it and dump it in the industrial sewer and it would be the wastewater plants problem. It's all within the law, but
it seems backwards thinking to me.
The neutralization tank I can manage, but I think the inline model will be more favorable. Does that kind a equipment come ready-made? What would be
the process time for pumping and neutralizing 9000 L with out too much heat generated?
The current downtime is 4 hours for draining the scrubber tank, refilling with water and adding conc. H2SO4. In 6 mouths time the sterilization
process is doubled, add pressure to the scrubber system, but it give me a possibility to have accepted downtime of 24 hours.
|
|
Rainwater
National Hazard
  
Posts: 937
Registered: 22-12-2021
Member Is Offline
Mood: Break'n glass & kick'n a's
|
|
You have the potential to produce a lot of very profitable products or a lot of very toxic pollution. I hope you figure out a good method for dealing
with your byproducts.
The local market will help determine the best end products.
If you're in the farming area, neturalizeing with ammonia, then purifying the ammonia sulfate could be an option, and the pure product would be a
great fertilizer.
A city or industrial area, neturaling with aluminum, will produce aluminum sulfate, which is a common chemical used in waste water treatment. Which
seams a little arronic taking your waste water and using it to treat waste water.
Hopefully, you'll get this worked out before you produce all that waste
"You can't do that" - challenge accepted
|
|
Rainwater
National Hazard
  
Posts: 937
Registered: 22-12-2021
Member Is Offline
Mood: Break'n glass & kick'n a's
|
|
After some more research into industrial practices and making a few phone calls, calcium hydroxide is the standard neturalizeing reagent due to the
easy use of a settling tank to separate the products.
Why is the scrubbing solution being acidified? To encrease the conversion of Eo to ethylene glycol.
The separation and treatment time/cost would be greatly reduced if the acid was not present. As well as eliminating the production of several
byproducts.
A greater surface area would be required to react ethylene oxide with water at an equally efficient rate, but the problem with neturalizeing the wash
water would be eliminated.
An additional problem that arises is self solving with a properly designed production process. That is the purity of the scrubbing media. For the
greatest efficiency, the water should be free from glycol.
For example
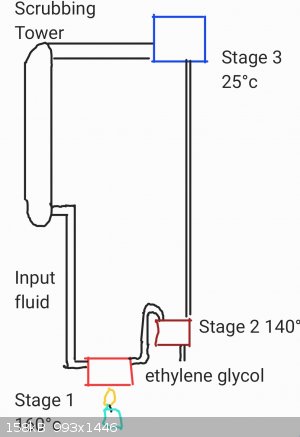
At that point, a continuous distillation apparatus could be used to consentrate ethylene glycol and return the purified water back to the scrubbing
reactor.
The apparatus could be constructed of common items such as old car radiators and copper tubing. Which would result in high thermal loss but could
still be cost effective.
Proper heat exchangers would preheat the stage 1 solution with heat from stage 3, recycling energy and saving money
Temperature monitoring would ensure proper separation.
Further optimizing the system to a 2-stage reaction would result in less energy required and produce a less pure ethylene glycol solution but greatly
reduce initial investment cost and construction requirements.
Also, by using a continuous recycling method, and by controlling the rate of glycol production to match removal, you can create a non-stop process
that will increase overall production.
Edit:
if co2 emissions are not a consequence, conversion by acid catalyzed reactions to volatile products followed by combustion could supplement the
distillation heat source.
Properly controlled with appropriate safety measures, complete combustion of the byproducts can occure and sulfuric acid can be
recovered and recycled.
[Edited on 21-4-2022 by Rainwater]
"You can't do that" - challenge accepted
|
|
SWIM
National Hazard
  
Posts: 970
Registered: 3-9-2017
Member Is Offline
|
|
Well yeah, but if the OP is trying to avoid buying (or doesn't have room for)a neutralization tank it sounds like these more elaborate setups are off
the table.
Looks like simple is a big priority here.
|
|
Bonee
Harmless
Posts: 29
Registered: 20-12-2010
Member Is Offline
Mood: No Mood
|
|
Could try multi stage reverse osmosis or electrodialysis as well. Although the ethylene glycol may complicate things.
see patent.
https://patents.google.com/patent/US7976710B2/en
|
|
WGTR
National Hazard
  
Posts: 971
Registered: 29-9-2013
Location: Online
Member Is Offline
Mood: Outline
|
|
Quote: Originally posted by Broken Gears  | Thank you all so much for all the input.
I think I have underestimated the extent of this project...
With a pH at pH 6-9 we can deliver it to a Biogas-plant free of charge, and it will be converted to district heating = helping the local community.
Another solution is to neutralize it and dump it in the industrial sewer and it would be the wastewater plants problem. It's all within the law, but
it seems backwards thinking to me.
The neutralization tank I can manage, but I think the inline model will be more favorable. Does that kind a equipment come ready-made? What would be
the process time for pumping and neutralizing 9000 L with out too much heat generated?
The current downtime is 4 hours for draining the scrubber tank, refilling with water and adding conc. H2SO4. In 6 mouths time the sterilization
process is doubled, add pressure to the scrubber system, but it give me a possibility to have accepted downtime of 24 hours. |
Your reply is helpful and helps with understanding the scope of what you are trying to do. Yes, unfortunately this sounds like a big project, because
4 hours is very little time to empty and refill a tank of this size if we add a neutralization step. This can be done of course, but there is so
little room for error that no solution that I can offer will likely be useful, and it may take an engineer to design the process (due to the lack of
room for error).
Anyway, is the tank pumped out, or is it emptied via gravity flow? If by gravity, the simplest method that I can conceive would be to have a second,
equally-dimensioned tank, that is at the same height as the process tank. The second tank would contain pre-mixed neutralization solution (whether
this is NaOH or something else) with a calculated concentration. The two tanks are joined with a 'Y' fitting through valves at their outputs for
mixing. The output of the mixer would need to go to a small retention tank so that the pH could be constantly monitored as the tanks empty. Beyond
this I wish you success.
|
|
Pages:
1
2 |