Pages:
1
..
63
64
65
66
67
68 |
infinity
Harmless
Posts: 6
Registered: 16-9-2019
Member Is Offline
|
|
Quote: Originally posted by greenlight  | Thankyou..
The next variable to be changed was indeed the flyer thickness up to 2mm.
The projectile from that test did hit in one spot with minimal breakup, the other marks are from previous tests.
Unfortunately it hit on the very top and transferred a third of its energy off the damn plate
|
a simple LASER pointer will help you to aim the impact point on target. If feasible you can try out variable thickness to improve penetration. Sof
iron will be a good option for coherent projectile as it has better resilience.
|
|
greenlight
National Hazard
  
Posts: 755
Registered: 3-11-2014
Member Is Offline
Mood: Energetic
|
|
I did have one that I always used to use but the battery went dead that day so I was forced to try and sight it by eye
Be good, otherwise be good at it
|
|
Brightthermite
Hazard to Others
 
Posts: 133
Registered: 26-6-2019
Member Is Offline
|
|
A .45 jacket soldered into half inch pipe with 4.5 grams of melt cast ETN.
[Edited on 5-10-2020 by Brightthermite]
[Edited on 5-10-2020 by Brightthermite]
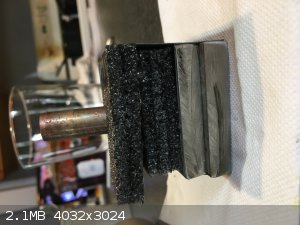
[Edited on 5-10-2020 by Brightthermite]
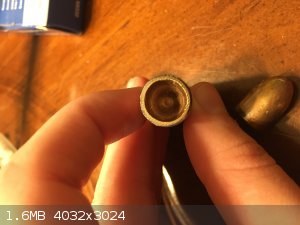
|
|
dettoo456
Hazard to Others
 
Posts: 250
Registered: 12-9-2021
Member Is Offline
|
|
Found this new paper on truncated charge shapes. The addition of a thicker plate behind the cone allows for a slower forming (think a subtle push of
the cone into its inverse jet) and sharper jet that has better properties than its original counterpart. It acts as sort of an explosive lens-version
of a shape charge. Maybe even incorporating the design of a lens into the shape charge might allow for tighter compression and inversion of the cone.
https://onlinelibrary.wiley.com/doi/10.1002/prep.202100162
|
|
specialactivitieSK
Hazard to Self

Posts: 94
Registered: 21-10-2014
Member Is Offline
Mood: No Mood
|
|
https://youtu.be/XtDoPvaCbFQ
|
|
Bert
Super Administrator
       
Posts: 2821
Registered: 12-3-2004
Member Is Offline
Mood: " I think we are all going to die. I think that love is an illusion. We are flawed, my darling".
|
|
Very little of what video is coming out of that conflict is exactly what it appears or is described as.
I note in one video segment, someone is just walking along next to the "death ray" and just KEEPS WALKING NORMALY?! I assure you, IRL someone in that
position would hit the dirt or go into a higher gear, be it away from kaboom or towards his squad mates smoking remains, not just keep plodding.
From video quality, could be CG animation.
From detail level visible, even if real, could equally likely be Ukrainians getting hit. I've found several videos where Uk propagandists changed
titles on some RF drone video of their guys getting whomped and claimed "glorious victory over the evil moskals"! Easy to do when they're carrying
same weapons, wearing pretty much the same gear and at least initially were operating very similar vehicles.
Rapopart’s Rules for critical commentary:
1. Attempt to re-express your target’s position so clearly, vividly and fairly that your target says: “Thanks, I wish I’d thought of putting it
that way.”
2. List any points of agreement (especially if they are not matters of general or widespread agreement).
3. Mention anything you have learned from your target.
4. Only then are you permitted to say so much as a word of rebuttal or criticism.
Anatol Rapoport was a Russian-born American mathematical psychologist (1911-2007).
|
|
Bert
Super Administrator
       
Posts: 2821
Registered: 12-3-2004
Member Is Offline
Mood: " I think we are all going to die. I think that love is an illusion. We are flawed, my darling".
|
|
Quote: Originally posted by dettoo456  | Found this new paper on truncated charge shapes. The addition of a thicker plate behind the cone allows for a slower forming (think a subtle push of
the cone into its inverse jet) and sharper jet that has better properties than its original counterpart. It acts as sort of an explosive lens-version
of a shape charge. Maybe even incorporating the design of a lens into the shape charge might allow for tighter compression and inversion of the cone.
https://onlinelibrary.wiley.com/doi/10.1002/prep.202100162 |
Obvious next step is test with a truncated 90° cone primary liner and a proportionally designed disc as secondary liner sitting on top-
A stupid simple bit of machining to accomplish that claimed 70+% increase in depth.
Rapopart’s Rules for critical commentary:
1. Attempt to re-express your target’s position so clearly, vividly and fairly that your target says: “Thanks, I wish I’d thought of putting it
that way.”
2. List any points of agreement (especially if they are not matters of general or widespread agreement).
3. Mention anything you have learned from your target.
4. Only then are you permitted to say so much as a word of rebuttal or criticism.
Anatol Rapoport was a Russian-born American mathematical psychologist (1911-2007).
|
|
Herr Haber
International Hazard
   
Posts: 1236
Registered: 29-1-2016
Member Is Offline
Mood: No Mood
|
|
Quote: Originally posted by Bert  |
Very little of what video is coming out of that conflict is exactly what it appears or is described as.
|
You are absolutely correct. I belive both the title and the level of the comments below the video have one common cause.
It's posted by The Sun ! My expectancies from tabloids are pretty low
The spirit of adventure was upon me. Having nitric acid and copper, I had only to learn what the words 'act upon' meant. - Ira Remsen
|
|
Fantasma4500
International Hazard
   
Posts: 1681
Registered: 12-12-2012
Location: Dysrope (aka europe)
Member Is Offline
Mood: dangerously practical
|
|
one youtuber that oftenly does shaped charges had a video where he had a liner that was made out of copper PLA wire- 3D printed copper cone
90% copper POWDER and 10% PLA plastic
the rolls are iirc 10m/60 euros- spicy.
it doesnt have to be pure metal, the liner displayed very great properties, maybe better than solid copper plate liner even
now, this opens up many possibilities for the amateur community- im a practical man. why bother with 3D printing if this mixture can maybe be heated
up and pressed- CAST? low temperature cast??
i came up with these ideas before i got out of bed this sunday:
1. pressed copper powder
2. pressed copper powder with glue or binder
3. CAST copper powder/lowmelting plastic
4. aluminium foil
5. pressed copper wires into cone
6. glass powder/sand
1/2. first up copper powder is very easy, CuCl2 (HCl + Cu - set and forget) + Al (a bit of HCl seems to help this reaction)
or copper salts + ascorbic acid or other reducing agents
one time i managed to make what seemed to be nano copper powder- the colloidal community seems to gatekeep their methods for making colloidal copper
because of toxicity- nanopowder is probably unnessecary and would require more binder anyhow
as for binder, i think something as basic as milk could work as it dries up and the proteins in milk gets quite hard, PIB works for RDX in a ratio of
about 5% PIB- tar, asphalt, clay, pine resin? a angled steel rod could be covered with aluminium foil for very easy release of a somewhat sticky
pressed cone
maybe a cone could be pressed then inserted into a spotwelder, i have seen some small devices made out of tiny little brass bb's that was somehow
welded together- possibly pressed and spotwelded, they are used as suppressors for pressurized air systems - a spot welder is easy to fabricate from
microwave
3. now.. PLA or maybe even polyethylene could be interesting, hotglue maybe even for a very low melting combination of copper powder and plastic,
acrylic doesnt quite melt but rather decomposes if you go much above glass-transition temperature, milk cartons and plastic bags are oftenly made of
polyethylene
4. since copper powder/plastic does work- why wouldnt something of similar quality work, aluminium foil? only chance this wouldnt i see is the
aluminium oxide which is quite high in quantity since the aluminium foil is thin- and relative to aluminium metal there will be a lot more aluminium
oxide than in typical liners- but if this can work we have really wrecked the system in terms of DIY shaped charge liners- having pressed and rammed
much aluminium foil into discs for recycling i remember it to reach about 2g/cm3, these discs may then be pressed into cones- or just from start
rammed into cones- BBQ / grill aluminium foil is a bit thicker, this may be utilized instead of regular aluminium foil
5. copper wires are found in most cables- selfexplanatory, but might require a lot more pressure - can be done somewhat with wood and a hammer, maybe
several tonnes of force and a small diameter would make for some very nice cones? naturally, some cables also contain aluminium- typical super pure
aluminium so very soft
https://www.youtube.com/watch?v=oTlD6rvQGbA
6. glass/sand, glass is easy to powder, if that can be used in a kinda binded state it would be very easy to manufacture whatever shape and especially
very cheap, although glass seems to be less effective than metal liners
seeing that ETN can be pressed to about 1.2g/cm3- yielding approximately 6250m/s - then theres not much reason to go for fancy stuff, by my opinion
increasing VoD shouldnt really make the whole thing much better, too much brisance could maybe crush the liner? i recall nitromethane mixtures being
used for shaped charges and they also reach just about 6000m/s
oh- heres the 3D printed liner
https://www.youtube.com/watch?v=BBruJJfs8fI
edit: the video with the death ray is actually an type of anti tank mine that shoots out EFP projectiles, so theyre kinda being hit by anti-armor
RPG's or shells, in some of the clips you can see it flying in, this explains the accuracy and why its even an anti armor ammunition fired at
personnel
[Edited on 5-2-2023 by Antiswat]
yet another edit: a jackhammer could possibly be used to hammer/press cones- steel rod with 45* tip, then a hole drilled in the back of this to insert
jackhammer bit, a bolt with impact driver and a nut could also work to get a very high pressure to press foil or powders with
[Edited on 5-2-2023 by Antiswat]
|
|
Microtek
National Hazard
  
Posts: 872
Registered: 23-9-2002
Member Is Offline
Mood: No Mood
|
|
I saw that video, and frankly, 48mm penetration from 120g HE is not very impressive. I got 19mm from 1.6g PETN using a handrolled sheet of copper 12mm
diameter at the base of the cone. Much easier than working with powders, and more robust as well. I have done some experimenting with pressed copper
powder, but didn't get much penetration. Aluminum is not a very good liner for shaped charges, its density is too low (the penetration depth is
dependent on the ratio of liner density to target density).
Sintered liners do work, and are used in oil drilling to perforate the well lining to allow the oil to flow out. The reason they use sintered powder
in this instance is simply that it doesn't leave a carrot (the solid slug formed from the base of the cone) in the hole, as that would reduce the oil
flow.
|
|
Herr Haber
International Hazard
   
Posts: 1236
Registered: 29-1-2016
Member Is Offline
Mood: No Mood
|
|
@Antiswat: Just read through all your points and two things come to mind.
- Find information on the shaped charges used in the oil industry. You'll find some common ideas with what you said. Though I'd be surprised if you
dont know all that already 
- About your fifth point, if you got all this pressure, why not sinter your powder ?
About the video it appears to be a DM22 mine with a tandem shaped charge, not an EFP. Might be wrong though.
Edit: of course it's only after posting that I see Microtek's comments ! Woopsie !
Microtek, it's interesting to compare penetration values given for EFP"s and shaped charges. It's not a surprise that EFP's are worst, but they can be
set off from further without disrupting the jet. Every tool its has it's function right ?
[Edited on 6-2-2023 by Herr Haber]
The spirit of adventure was upon me. Having nitric acid and copper, I had only to learn what the words 'act upon' meant. - Ira Remsen
|
|
Fantasma4500
International Hazard
   
Posts: 1681
Registered: 12-12-2012
Location: Dysrope (aka europe)
Member Is Offline
Mood: dangerously practical
|
|
Quote: Originally posted by Herr Haber  | @Antiswat: Just read through all your points and two things come to mind.
- Find information on the shaped charges used in the oil industry. You'll find some common ideas with what you said. Though I'd be surprised if you
dont know all that already 
- About your fifth point, if you got all this pressure, why not sinter your powder ?
About the video it appears to be a DM22 mine with a tandem shaped charge, not an EFP. Might be wrong though.
Edit: of course it's only after posting that I see Microtek's comments ! Woopsie !
Microtek, it's interesting to compare penetration values given for EFP"s and shaped charges. It's not a surprise that EFP's are worst, but they can be
set off from further without disrupting the jet. Every tool its has it's function right ?
[Edited on 6-2-2023 by Herr Haber] |
im looking on google and im not finding much about oil industry shaped charges- seems they just use copper sheet metal cones, .. i mean- they got
plenty money?
sinter, wouldnt that require both heat and pressure? my concept is to press it and haveit cure- no need for a gas torch, im sure it also requires many
many tonnes, last i looked into it, it was way out of my hands to sinter anything- maybe unless if you use explosives to-.. sinter
can you extrapolate on the things you have found in oil industry's shaped charges? i know shaped charges for rocks are normally aluminium cones as
they give plenty penetration
edit: nvm i see microtek already blurted out the oil industry's secret
@microtek 48mm really? didnt they claim it worked even better than their actual copper cone- or at least very close to that? how did you roll that
copper up anyhow, .. did it overlap, did you solder it? 1.6g and 19mm sounds very impressive, it must have been quite a sharp cone i imagine? how
thick was this liner?
[Edited on 6-2-2023 by Antiswat]
|
|
MineMan
International Hazard
   
Posts: 1014
Registered: 29-3-2015
Member Is Offline
Mood: No Mood
|
|
Quote: Originally posted by Antiswat  | one youtuber that oftenly does shaped charges had a video where he had a liner that was made out of copper PLA wire- 3D printed copper cone
90% copper POWDER and 10% PLA plastic
the rolls are iirc 10m/60 euros- spicy.
it doesnt have to be pure metal, the liner displayed very great properties, maybe better than solid copper plate liner even
now, this opens up many possibilities for the amateur community- im a practical man. why bother with 3D printing if this mixture can maybe be heated
up and pressed- CAST? low temperature cast??
i came up with these ideas before i got out of bed this sunday:
1. pressed copper powder
2. pressed copper powder with glue or binder
3. CAST copper powder/lowmelting plastic
4. aluminium foil
5. pressed copper wires into cone
6. glass powder/sand
1/2. first up copper powder is very easy, CuCl2 (HCl + Cu - set and forget) + Al (a bit of HCl seems to help this reaction)
or copper salts + ascorbic acid or other reducing agents
one time i managed to make what seemed to be nano copper powder- the colloidal community seems to gatekeep their methods for making colloidal copper
because of toxicity- nanopowder is probably unnessecary and would require more binder anyhow
as for binder, i think something as basic as milk could work as it dries up and the proteins in milk gets quite hard, PIB works for RDX in a ratio of
about 5% PIB- tar, asphalt, clay, pine resin? a angled steel rod could be covered with aluminium foil for very easy release of a somewhat sticky
pressed cone
maybe a cone could be pressed then inserted into a spotwelder, i have seen some small devices made out of tiny little brass bb's that was somehow
welded together- possibly pressed and spotwelded, they are used as suppressors for pressurized air systems - a spot welder is easy to fabricate from
microwave
3. now.. PLA or maybe even polyethylene could be interesting, hotglue maybe even for a very low melting combination of copper powder and plastic,
acrylic doesnt quite melt but rather decomposes if you go much above glass-transition temperature, milk cartons and plastic bags are oftenly made of
polyethylene
4. since copper powder/plastic does work- why wouldnt something of similar quality work, aluminium foil? only chance this wouldnt i see is the
aluminium oxide which is quite high in quantity since the aluminium foil is thin- and relative to aluminium metal there will be a lot more aluminium
oxide than in typical liners- but if this can work we have really wrecked the system in terms of DIY shaped charge liners- having pressed and rammed
much aluminium foil into discs for recycling i remember it to reach about 2g/cm3, these discs may then be pressed into cones- or just from start
rammed into cones- BBQ / grill aluminium foil is a bit thicker, this may be utilized instead of regular aluminium foil
5. copper wires are found in most cables- selfexplanatory, but might require a lot more pressure - can be done somewhat with wood and a hammer, maybe
several tonnes of force and a small diameter would make for some very nice cones? naturally, some cables also contain aluminium- typical super pure
aluminium so very soft
https://www.youtube.com/watch?v=oTlD6rvQGbA
6. glass/sand, glass is easy to powder, if that can be used in a kinda binded state it would be very easy to manufacture whatever shape and especially
very cheap, although glass seems to be less effective than metal liners
seeing that ETN can be pressed to about 1.2g/cm3- yielding approximately 6250m/s - then theres not much reason to go for fancy stuff, by my opinion
increasing VoD shouldnt really make the whole thing much better, too much brisance could maybe crush the liner? i recall nitromethane mixtures being
used for shaped charges and they also reach just about 6000m/s
oh- heres the 3D printed liner
https://www.youtube.com/watch?v=BBruJJfs8fI
edit: the video with the death ray is actually an type of anti tank mine that shoots out EFP projectiles, so theyre kinda being hit by anti-armor
RPG's or shells, in some of the clips you can see it flying in, this explains the accuracy and why its even an anti armor ammunition fired at
personnel
[Edited on 5-2-2023 by Antiswat]
yet another edit: a jackhammer could possibly be used to hammer/press cones- steel rod with 45* tip, then a hole drilled in the back of this to insert
jackhammer bit, a bolt with impact driver and a nut could also work to get a very high pressure to press foil or powders with
[Edited on 5-2-2023 by Antiswat] |
I saw that video. It was 80 percent copper powder. They quoted it wrong. It is hard to duplicate the filament. They were wrong, it was not better than
solid copper, which should get 6 diameter penetration… they got less than two with the printed ones.
I agree, the 3D printed filament is an interesting idea. I was really excited about it for a while, but couldn’t justify the costs for the
filament. I ultimately determined SLA is better for this application than filament. Keep in mind 80 percent copper by weight is only half the density
of real copper.
|
|
Microtek
National Hazard
  
Posts: 872
Registered: 23-9-2002
Member Is Offline
Mood: No Mood
|
|
@ Antiswat: It's possible the printet copper cone worked better than the solid copper one they made, but that just means something about their design
was suboptimal. About my rolled up cone, I cut out a circle from a thin (0.2 mm IIRC - it was a long time ago) copper sheet, and made a cut along the
radius. Then I used small needle nosed pliers to roll it up to make a double layer all the way round. You can do the same with a piece of paper to
illustrate the principle. I didnt solder it, but I might have used some glue between the layers to keep them together. As I said, it was a long time
ago and I can't really remember.
A little math and the angle of the cone comes out at 60 degrees (ignoring the thickness of the liner). I wasn't expecting much from the charge, but
placed it above a stack of 4 mm mild steel plates to see how many it could penetrate. I think I used abut 1 diameter standoff. Without doubt, some
penetration was lost in the small gaps between the plates.
Nevertheless, given that I got less than two diameters of penetration (and as MineMan says, 6-7 diameters is achievable), the only impressive things
about my experiment was the small scale since SCs generally perform better at larger scales, and of course that such relatively good performance could
be had from a simple rolled up sheet.
@ Herr Haber: Yes, EFPs are certainly both interesting and useful in some situations. I was just commenting on the video about 3d printed copper
powder cones.
[Edited on 7-2-2023 by Microtek]
|
|
Bert
Super Administrator
       
Posts: 2821
Registered: 12-3-2004
Member Is Offline
Mood: " I think we are all going to die. I think that love is an illusion. We are flawed, my darling".
|
|
They make a 2.3 mil thick pure copper tape with electrically conductive adhesive, commonly used to line and shield the electronics compartments of
electric guitars. I suspect it would lend itself to a multiple layer buildup to a desired thickness- or a single layer might be formed into a cone as
a substrate for electoplating to desired thickness without the discontinuity between layers.
Rapopart’s Rules for critical commentary:
1. Attempt to re-express your target’s position so clearly, vividly and fairly that your target says: “Thanks, I wish I’d thought of putting it
that way.”
2. List any points of agreement (especially if they are not matters of general or widespread agreement).
3. Mention anything you have learned from your target.
4. Only then are you permitted to say so much as a word of rebuttal or criticism.
Anatol Rapoport was a Russian-born American mathematical psychologist (1911-2007).
|
|
MineMan
International Hazard
   
Posts: 1014
Registered: 29-3-2015
Member Is Offline
Mood: No Mood
|
|
Quote: Originally posted by Bert  | They make a 2.3 mil thick pure copper tape with electrically conductive adhesive, commonly used to line and shield the electronics compartments of
electric guitars. I suspect it would lend itself to a multiple layer buildup to a desired thickness- or a single layer might be formed into a cone as
a substrate for electoplating to desired thickness without the discontinuity between layers. |
Bert! Your a true handyman in this field!
|
|
Bert
Super Administrator
       
Posts: 2821
Registered: 12-3-2004
Member Is Offline
Mood: " I think we are all going to die. I think that love is an illusion. We are flawed, my darling".
|
|
Quote: Originally posted by MineMan  | Quote: Originally posted by Bert  | They make a 2.3 mil thick pure copper tape with electrically conductive adhesive, commonly used to line and shield the electronics compartments of
electric guitars. I suspect it would lend itself to a multiple layer buildup to a desired thickness- or a single layer might be formed into a cone as
a substrate for electoplating to desired thickness without the discontinuity between layers. |
Bert! Your a true handyman in this field! |
"If the women don't find you handsome, at least they can find you handy"
https://www.amazon.com/ELK-Copper-Foil-Conductive-Adhesive/d...
Rapopart’s Rules for critical commentary:
1. Attempt to re-express your target’s position so clearly, vividly and fairly that your target says: “Thanks, I wish I’d thought of putting it
that way.”
2. List any points of agreement (especially if they are not matters of general or widespread agreement).
3. Mention anything you have learned from your target.
4. Only then are you permitted to say so much as a word of rebuttal or criticism.
Anatol Rapoport was a Russian-born American mathematical psychologist (1911-2007).
|
|
arkoma
Redneck Overlord
     
Posts: 1763
Registered: 3-2-2014
Location: On a Big Blue Marble hurtling through space
Member Is Offline
Mood: украї́нська
|
|
I love Red Green. Don't run out of duct tape!
"We believe the knowledge and cultural heritage of mankind should be accessible to all people around the world, regardless of their wealth, social
status, nationality, citizenship, etc" z-lib
|
|
Fantasma4500
International Hazard
   
Posts: 1681
Registered: 12-12-2012
Location: Dysrope (aka europe)
Member Is Offline
Mood: dangerously practical
|
|
Quote: Originally posted by Microtek  | @ Antiswat: It's possible the printet copper cone worked better than the solid copper one they made, but that just means something about their design
was suboptimal. About my rolled up cone, I cut out a circle from a thin (0.2 mm IIRC - it was a long time ago) copper sheet, and made a cut along the
radius. Then I used small needle nosed pliers to roll it up to make a double layer all the way round. You can do the same with a piece of paper to
illustrate the principle. I didnt solder it, but I might have used some glue between the layers to keep them together. As I said, it was a long time
ago and I can't really remember.
A little math and the angle of the cone comes out at 60 degrees (ignoring the thickness of the liner). I wasn't expecting much from the charge, but
placed it above a stack of 4 mm mild steel plates to see how many it could penetrate. I think I used abut 1 diameter standoff. Without doubt, some
penetration was lost in the small gaps between the plates.
Nevertheless, given that I got less than two diameters of penetration (and as MineMan says, 6-7 diameters is achievable), the only impressive things
about my experiment was the small scale since SCs generally perform better at larger scales, and of course that such relatively good performance could
be had from a simple rolled up sheet.
@ Herr Haber: Yes, EFPs are certainly both interesting and useful in some situations. I was just commenting on the video about 3d printed copper
powder cones.
[Edited on 7-2-2023 by Microtek] |
aha, thanks a lot for that writeup, very interesting to see these kinda unholy constructions do well- .. this could surely imply aluminium foil would
work.
i have managed to come across an old timer toolmaker which happily went into hours long talk about making a cone press die over and under piece and
made it with proud perfection to me same day so im stoked to see how easy it will be to press metalplates into cones, a 40mm wide 45 degree incline
should make it possible to press at least 30mm wide discs, with some scientific approximates, 37.5mm wide would equal 30mm wide cone- maybe.
copper foil can be had from wish, i suspect foil may crimp a fair bit when pressed, but if it can simply be rolled up an amount of times with still
very good penetration thats very promising- and surely worrying to anyone that gets paid to read these forums ..
i have some zinc metal discs to try out as well- seemingly zinc metal shaped charges are a thing, .. one could cast their own zinc metal plate and,
well or just press a cone in a tool, adjusting the height the top part comes down, 400ish melting point is fairly doable especially in smaller amounts
https://patents.google.com/patent/WO2000039519A2/en
"At least the capsule consists of an alloy of, by weight, between about 4 and 12 percent copper, 2 and 4 percent aluminum, and the balance zinc and
impurities."
|
|
Fantasma4500
International Hazard
   
Posts: 1681
Registered: 12-12-2012
Location: Dysrope (aka europe)
Member Is Offline
Mood: dangerously practical
|
|
oh boy.. do i have something to share. to my understanding attempts ive seen every now and then of pressing copper cones .. or producing such, best
bets were to electrodeposit copper- im hearing something about cast lead/tin cones- with possibly poor performance, but now it seems that i have with
a few tools that was produced on a lathe made copper cones that appear as if they were bought.
so i tested both a 2 tonne hydraulic press with my press frame, and measured it against my homemade handcrank press frame- this device relies on a
nut, a 30mm mild steel "C" and a 30mm threaded rod- and of course the cone pressing tool being a 30mm threaded rod attachment that connects with a
30mm nut, and a 10mm mild steel rod at top for manual cranking, this then gets mounted in an also homemade vice- as weak and fragile as 8mm threaded
rod on this little vice, simply mounted on wooden table with 8 10mm SCREWS as small as 4mm- very doable sizes.
the hydraulic jack produced cones sure- but the handcrank device surprisingly gave me better results, results that i measured as in how tall this cone
would get. on hydraulic press i got to 8.3mm at most, handcrank gave me 8.6! very significant difference
the handcrank is simply 220mm to center of the rod where its mounted through a 10mm hole
the 97% copper plate i used was 21.5mm wide and 1.35mm thickness. after conification it measures 19.25mm wide and 8.6mm tall
theres a slight challenge with having the metal get situated in the middle properly, some help can be had for placing the point center by drawing a
dot on the piece of metal before pressing it- and simply pressing plenty until you get a hang of it and/or discarding the ones that didnt go too well
https://i.gyazo.com/thumb/1200/f6121de1d5d1c117f12dc99060d72...
all the joints were chamfered well before welding, the bottom part was left plane so that it could properly contact a vice to keep it in position,
alternatively plate with holes in it could be used to attach to a table with screws or bolts to bypass vice- a vice could be taken apart and welded
together to shappily manufacture the pressing frame- the spike could maybe be attached directly to the vice jaw with a few welds- as could the lower
part very easily and super accurately by pressing the jaws together with both upper and lower parts stuck together
with this construction im willing to sell an amount of these cones that i can now massproduce effortlessly, shipping as far away as australia is about
15 euros- unsure what i would charge for each little cone, 19mm x 1.35x 45* cones is what ill be making for now
|
|
Microtek
National Hazard
  
Posts: 872
Registered: 23-9-2002
Member Is Offline
Mood: No Mood
|
|
Nice. If you make a couple of dies with successively more severe angles, you can get to a 60 degree cone without problems (just remember to anneal the
copper often). I made such a series of dies and matching punches on my CNC milling machine, and have made flawless copper liners with just these tools
and a hammer. My only problem is the base of the cone - I would like to find a good way to repeatably machine the base perpendicular to the axis of
symmetry. The best I've found so far is to mount the cone on a mandrel that is identical to the final punch, and then cut off the excess on the lathe
while using an adapter for the live center to hold the cone onto the mandrel. It works but isn't as convenient as I would like.
|
|
Fantasma4500
International Hazard
   
Posts: 1681
Registered: 12-12-2012
Location: Dysrope (aka europe)
Member Is Offline
Mood: dangerously practical
|
|
hammer, copper liners- would it be possible to hammer through copper plate if one was to make a setup that lined up the punch - upper tool, vs the
undertool, or maybe sharpened the punch concave? maybe wood underneath to avoid damaging the punch. it seems 1mm copper can be pushed through with
just a 16mm BOLT with vaguely fitting hole underneath with about 2 tonnes of force, maybe with just below 2 tonnes if you actually put effort into it.
softer metals would require less difference between the upper and lower tool-
i did argue the machinist about making the device more complicated, having it placed exactly in the center, he told me that he could make it so that
it would have a little groove where i would fit in a soft metal plate, and then the upper tool would be fixed so that its always centered- my hand
crank wiggles about 1 millimeter at the start, but it still works somehow.
we then settled on just making it 40mm wide and no groove- because groove would mean i would be needing more accurate pieces of metal plate, less
versatile. with my current press i can go up to 40mm width of plate, groove would limit its versatility
maybe a hand-cranked hole-punch would be the best, a rod moving into a tube, more force = longer / harder handle
this old tony on YT produced a holepunch in which around the upper tool, theres a mechanism with a spring and a washer of some sort- once this goes
down and contacts the plate, it keeps the plate from deforming while punching the hole, but also when withdrawing the tool
anyhow heres some pics of my unholy aluminium foil cones, made from a bunch of aluminium foil i rammed in a tube with a rod and a hammer many years
ago. i also found it that if you wanna use aluminium foil right off the roll, ideal is not to roll it up and wrap it around itself, you wanna shape it
into a ball, and really press it hard by hand, then press this slightly into the die- and then lower in the upper tool- or just pre-shape the al foil
discs, they feel very solid, it sounds like metal if you slam it on something of metal, very plausible this will actually work as a liner.
one drawback is that it sticks to the upper tool when the initial foil piece of larger than the tip
https://gyazo.com/0dede25826fcdf24226929b234d9f70f
|
|
dettoo456
Hazard to Others
 
Posts: 250
Registered: 12-9-2021
Member Is Offline
|
|
@Fantasma4500 In theory, by finding the hardness and ductility of each pressing and molding material you can deduce if anything can be made through
your method but ofc there are exceptions. Your machinist was right, you should first find the exact radius of your plate to be pressed, cut to exact
size (a hole saw and drill press makes that easy and fairly accurate), and center your plate (now a disc) in your concave mold in a sort of edge
chamfer so it doesn’t move when being pushed into the mold. Pressing copper with a steel die into a steel or Al mold should be fine.
|
|
Fantasma4500
International Hazard
   
Posts: 1681
Registered: 12-12-2012
Location: Dysrope (aka europe)
Member Is Offline
Mood: dangerously practical
|
|
copper is a slight bit harder than ALUMINIUM*- so al mold def not a good idea- besides the softer your mold the more easily it will scratch and deform
i get the drift, perfection is nice- but i have some limits and i dont plan to produce thousands of cones- and then you wanna also consider, how much
time would it cost to produce the perfect tool, how much time would that really save you in the end? i think a good start would be to draw a dot in
the center of the plate to be pressed
lead has some potential for liner- maybe electroplating copper on a lead cone- or layering copper lead and other similar property materials would make
for a better working one? i still wanna try pressing copper powder and glue- biggest issue is making it release smoothly from the mold, aluminium foil
to the rescue.
[Edited on 17-2-2023 by Fantasma4500]
|
|
Bert
Super Administrator
       
Posts: 2821
Registered: 12-3-2004
Member Is Offline
Mood: " I think we are all going to die. I think that love is an illusion. We are flawed, my darling".
|
|
If any of you have access to a lathe, or even a large drill press, metal "spinning" of soft copper is an achievable thing. I have made a few shapes
this way, even easier, I've modified the shapes of existing commercially "drawn" copper pieces by spinning as well- Realize, while the work piece is
normally spun past a tool rest, the TOOL can be spun against a stationary piece as well-
Rapopart’s Rules for critical commentary:
1. Attempt to re-express your target’s position so clearly, vividly and fairly that your target says: “Thanks, I wish I’d thought of putting it
that way.”
2. List any points of agreement (especially if they are not matters of general or widespread agreement).
3. Mention anything you have learned from your target.
4. Only then are you permitted to say so much as a word of rebuttal or criticism.
Anatol Rapoport was a Russian-born American mathematical psychologist (1911-2007).
|
|
Pages:
1
..
63
64
65
66
67
68 |