Cyrus
Hazard to Others
 
Posts: 397
Registered: 24-4-2004
Location: Ancient Persia
Member Is Offline
Mood: No Mood
|
|
Efficient Magnalium Production
It's been a while since I've posted here, and much more time since I've been able to find the time to do any experiments. (8 months? I'm not sure.
Ceramics formulations etc. don't count as science experiments in my book, but some time I'll have to document the 2.7 cubic foot kiln I made (it can
reach >2400 degrees F. for certain), oil burner, and pottery wheel I've been working on. The glassware has been sitting neglected in a cabinet.
But summer is closer, and I bet I'll resume experimenting...)
Experimental details next, skip if you just want to see my questions...
Anyways, I decided to make some magnalium in my old furnace. Since most sites list magnalium as 50% Mg, 50% Al by weight, I used 407 g of each
substance. I had a ceramic crucible and a steel crucible, but I mis-estimated that the volume of the melt would be too large for the steel crucible,
and the ceramic crucible was already cracked (long story) so I used the ceramic crucible upside down as a macho plinth, and a steel can (refried
beans) as the crucible. After heating up the can for a while to burn off the paper, plastic, etc, and form an oxide coating, I added some CaCl2 and
NaCl (50/50 volume, roughly, as it melts well in any case). There was a bit of popping/fizzing indicating that the CaCl2 was slightly wet, then it
melted nicely, under a red heat.
Oh, the furnace was heated by a Reil EZ burner (propane burner).
I added the Al, and heated it, then realized that the Na+ in my flux might react with the magnesium (2NaCl + Mg -> MgCl2 + 2Na or similar) as it
had done with Tacho's and my experiments with sodium thermite. I added a bit of Mg to test this, and sure enough, it crumbled away and started
fizzing, with little yellow flames and popping noises leaving the melt.
Could this have been hydrogen burning from residual water in the flux as 12AX7 suggested in another thread? What on earth is water doing there at 900
degrees F?
Anyhow, I dumped out the metal, washed off the flux, poured the flux onto some slag (for some reason it "exploded", burning
my hand very slightly. That was probably from water.) and washed out the crucible.
Then I melted the Al without any flux, and gradually added the Mg. There was a crumbly oxide layer covering the molten metal, and every now and then
a bit of Mg stuck in this layer caught on fire, but overall, it went smoothly...
until the steel crucible decided to get a hole in it. A large hole.
I saw magnalium pouring out of the crucible into the lower (superheated) part of the furnace, shoved the burner out of the furnace, grabbed the
crucible with pliers, and poured the remaining metal onto a sand bed that I had prepared earlier. By this time there was a nice white-hot fire inside
and underneath the furnace (some metal had leaked out the hole in the bottom and caught the wood supports on fire) and even the metal in the sand bed
had caught fire at one corner.
Wanting to salvage most of the metal, I tried pouring sand (molding sand, actually) over the Mg to stop the burning, but that just insulated it, and
so 75% of the metal I had saved just burned away under the sand's protection. 5 minutes later it was still burning away, red hot.
Since there was refractory and sand everywhere, it wasn't too dangerous of an experiment, and the largest waste was probably the propane.
I can buy Mg (alloy of some sort) for $0.24 a lb, and the Al was from free pop cans. 
Here are my questions-
-Why did the steel crucible fail? (pictures of aftermath coming tomorrow)
I have 3 hypotheses. First, the Mg was put in and then tapped down into the melt to reduce it's exposure to the air with a steel rod, perhaps this
tapping punctured the crucible, but that would be just lame. Second, there was flux involved, and it may have attacked the steel. Finally, I'm not a
metallurgist, and so magnesium might have dissolved some of the steel, for all I know.
-What sort of flux is suitable for Mg/magnalium, in order to use the magnesium efficiently?
Ok, that's self explanatory. I just don't want it to randomly catch on fire, and I don't like wasting lots of good metal to make slag.
-Why is 50/50% the ratio used?
When the crucible failed, I hadn't put in all of the Mg, and so the resulting alloy was probably about 65% Al, 35% Mg, but it was still very brittle
and easy to powder in a mortar and pestle.
Are there any preferred alloys for reativity, etc?
Finally, here's an idea I had to reduce the risk of the operation- instead of pouring the metal out, just let it solidify in the crucible, cut open
the crucible, and smash up the magnalium. This way one could make 10 lb melts that would be dangerous to handle otherwise. Any thoughts?
Cy
|
|
12AX7
Post Harlot
   
Posts: 4803
Registered: 8-3-2005
Location: oscillating
Member Is Offline
Mood: informative
|
|
Quote: | Originally posted by Cyrus
It's been a while since I've posted here, and much more time since I've been able to find the time to do any experiments. |
WB. 
Quote: | I added the Al, and heated it, then realized that the Na+ in my flux might react with the magnesium (2NaCl + Mg -> MgCl2 + 2Na or similar) as it
had done with Tacho's and my experiments with sodium thermite. I added a bit of Mg to test this, and sure enough, it crumbled away and started
fizzing, with little yellow flames and popping noises leaving the melt. |
Nah, Cl melts are stable -- Mg could, but MgCl2 sticks around (adding to the salt melt) and any Na formed dissolves in the melt, so you get an
equilibrium MgCl2 + 2Na <--> 2NaCl + Mg, everything in liquid phase, and Na is still more reactive so it tends not to proceed.
Since AlCl3 is a gas at that temperature, it might be expected that AlCl3 would bubble out of an Al + Cl melt, but probably it doesn't because AlCl3
isn't as stable, or the Cl- melt is fully ionized and would rather not form a suprisingly covalent molecule. *shrug*
Quote: | Could this have been hydrogen burning from residual water in the flux as 12AX7 suggested in another thread? What on earth is water doing there at 900
degrees F? |
Idunno. What on earth is CO2 doing in standing water, or zinc doing in brass at 2100°F? Just another dissolved gas.
Quote: |
Then I melted the Al without any flux, and gradually added the Mg. There was a crumbly oxide layer covering the molten metal, and every now and then
a bit of Mg stuck in this layer caught on fire, but overall, it went smoothly...
until the steel crucible decided to get a hole in it. A large hole. |
Ah. How well did you wash out the crucible? Did you re-char it before use?
Quote: | I saw magnalium pouring out of the crucible into the lower (superheated) part of the furnace |
D'oh!
Quote: | -Why did the steel crucible fail? (pictures of aftermath coming tomorrow) |
Depending on what was stuck in the crucible, the straight aluminum probably did it in. Magnesium doesn't dissolve iron, but I don't know about
magnalium. Aluminum certainly dissolves iron.
Quote: | -What sort of flux is suitable for Mg/magnalium, in order to use the magnesium efficiently? |
You used the right one. It would be nice if there were a lighter salt (LiCl?), since magnesium is a bit less dense than most molten salts.
Quote: | -Why is 50/50% the ratio used? |
From about 50 to 55% Mg, you're in the gamma phase, a relatively low melting (not quite eutectic) phase that's very brittle.
There's also an aluminum-rich intermetallic Al3Mg2, but I've had bad results in that area. That could be due to silicon or other elements in my
aluminum alloy.
Not really any other reason besides mechanical weakness. You could tweak the alloy one way or the other to vary reactivity, but it may not be as
brittle.
Quote: | When the crucible failed, I hadn't put in all of the Mg, and so the resulting alloy was probably about 65% Al, 35% Mg, but it was still very brittle
and easy to powder in a mortar and pestle. |
Yeah, that's pretty close to Al3Mg2. It was probably still quite brittle
because Mg alloys aren't usually alloyed with much, and popcan aluminum is mostly Mg (to the tune of 3% or so, IIRC).
Quote: | Are there any preferred alloys for reativity, etc? |
AFAIK, reactivity varies linearly with composition.
Quote: | Finally, here's an idea I had to reduce the risk of the operation- instead of pouring the metal out, just let it solidify in the crucible, cut open
the crucible, and smash up the magnalium. This way one could make 10 lb melts that would be dangerous to handle otherwise. Any thoughts? |
I recall reading a method where you take a dutch oven out to a campsite, heap in Al and Mg, stoke up a big fire, put it on top and wait until the
whole thing is cool. Since the dutch oven comes with a lid, it tends not to burn up (although Mg burns 99% of what's in the air, I find it hard to
believe it doesn't make a mess anyway). Since the dutch oven has draft, the ingot isn't stuck in place too badly, and you still have your cast iron
pot intact.
With disposable tin cans, even if the ingot welds to the crucible, you could care less. I have no problem with that!
Tim
|
|
evil_lurker
National Hazard
  
Posts: 767
Registered: 12-3-2005
Location: United States of Elbonia
Member Is Offline
Mood: On the wagon again.
|
|
Use a dutch oven for a crucible... should be fairly sealed so no flux needed.
Let cool, then chip out the magnalium with a hammer and or chisel...
It should break very easily since magnalium is very brittle.
|
|
Cyrus
Hazard to Others
 
Posts: 397
Registered: 24-4-2004
Location: Ancient Persia
Member Is Offline
Mood: No Mood
|
|
Quote: |
WB. |
Thanks.
Quote: |
Nah, Cl melts are stable -- Mg could, but MgCl2 sticks around (adding to the salt melt) and any Na formed dissolves in the melt, so you get an
equilibrium MgCl2 + 2Na <--> 2NaCl + Mg, everything in liquid phase, and Na is still more reactive so it tends not to proceed.
|
Ah, and so this is why the sodium thermites only work when there is at least some sodium hydroxide/oxide/carbonate involved as well...
Quote: |
Since AlCl3 is a gas at that temperature, it might be expected that AlCl3 would bubble out of an Al + Cl melt, but probably it doesn't because AlCl3
isn't as stable, or the Cl- melt is fully ionized and would rather not form a suprisingly covalent molecule. *shrug* |
Or, maybe it does form, just not fast enough to detect. Speaking of fluxes/slag, I was cooling down Al slag from pop cans by adding water (after using
the furnace as a reverb. for quickly melting a lot of Al) and whenever water was added, this horrible, horrible smell came off.
Actually, it smelled like a well done piece of garlic bread without the buttery smell, but since I knew that this wasn't garlic, but some unknown
chemical causing the smell, it smelled nasty.
I've heard reports that phosphine smells like garlic... perhaps there was a bit of phosphorus in the paints on the Al. Hopefully the gas is something
nicer than phosphine, though, as it smelled really strongly for a long time!
What does AlCl3 smell like? Perhaps the water was liberating a hydrated version of aluminum trichloride from the slag? I'm going beyond my knowledge
here....
Quote: |
Ah. How well did you wash out the crucible? Did you re-char it before use? |
There were bright spots of metal at the bottom after washing, now that I think about it, although the top and sides were nicely oxidized. I guess the
Al just ate through the steel, but I think the corrosion created a weak spot that was punctured by tapping down Mg pieces into the melt. (The hottest
spot on the can probably would have been the bottom as well...)
Quote: |
Yeah, that's pretty close to Al3Mg2. It was probably still quite brittle because
Mg alloys aren't usually alloyed with much, and popcan aluminum is mostly Mg (to the tune of 3% or so, IIRC). |
Hehe, I actually remembered that, and that's why I chose to use pop cans instead of the other Al alloy I had for casting, which supposedly has lots of
silicon (10%?)
Quote: |
I recall reading a method where you take a dutch oven out to a campsite, heap in Al and Mg, stoke up a big fire, put it on top and wait until the
whole thing is cool. Since the dutch oven comes with a lid, it tends not to burn up (although Mg burns 99% of what's in the air, I find it hard to
believe it doesn't make a mess anyway). Since the dutch oven has draft, the ingot isn't stuck in place too badly, and you still have your cast iron
pot intact. |
Hmm, if I had an old dutch oven I would definitely try this...
In either case (tin can or dutch oven) there will certainly be some slag on the top, but I found that it was really easy to remove the slag from a
chunk of magnalium with a wire brush, leaving a scratched metallic surface underneath. In other words, getting a lot of "pure" magnalium will be quite
easy. 
Cy
[Edited on 19-3-2006 by Cyrus]
|
|
12AX7
Post Harlot
   
Posts: 4803
Registered: 8-3-2005
Location: oscillating
Member Is Offline
Mood: informative
|
|
I doubt you'll find AlCl3, it's rabidly hygroscopic and hydrolyzes.
The smell is from impurities in everything involved, traces of sulfates or phosphates are reduced to sulfide and phosphide, which hydrolyze in water
or moist air, producing a nasty stink.
The flux also cleans impurities ordinarily stuck firmly in the metal. Things like AlP, for instance, which as I recall is a nucleation agent for
silicon -- leading to the use of sodium, calcium or strontium as a getter in high-silicon alloys, so the melt cools a bit and becomes supersaturated
with silicon before crystallizing all at once, causing a finer grain.
Tim
|
|
Cyrus
Hazard to Others
 
Posts: 397
Registered: 24-4-2004
Location: Ancient Persia
Member Is Offline
Mood: No Mood
|
|
Take 2
This time I decided to do everything "right". (And I added photos for variety)
I didn't have a can on hand, so I bought some beans.
Next I baked the can in my furnace until the white coating on the inside fell off. I should add that this is my wimpy $7 2 year old crap furnace, not
my new kiln. Since it's garbage, I don't really worry about anything happening to it.
(interestingly, the coating turned green at high temperatures and back to white when cooled down; I'll bet there's ZnO in there.)
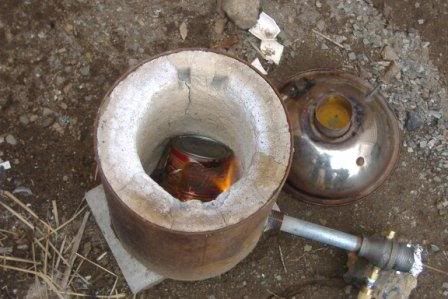
When the can was cool, I painted a mixture of Al2O3 and sodium silicate (just a rough mix, no exact amounts) on the inside of the can and baked it on.
(This was just in case the magnalium did actually dissolve Fe. I didn't want to take the chance.)
I measured out 746 g of Mg and 746 g of Al. The Mg was from some alloy at a scrap metal store, while the Al was partially from pop cans and partially
from pure Al wire.
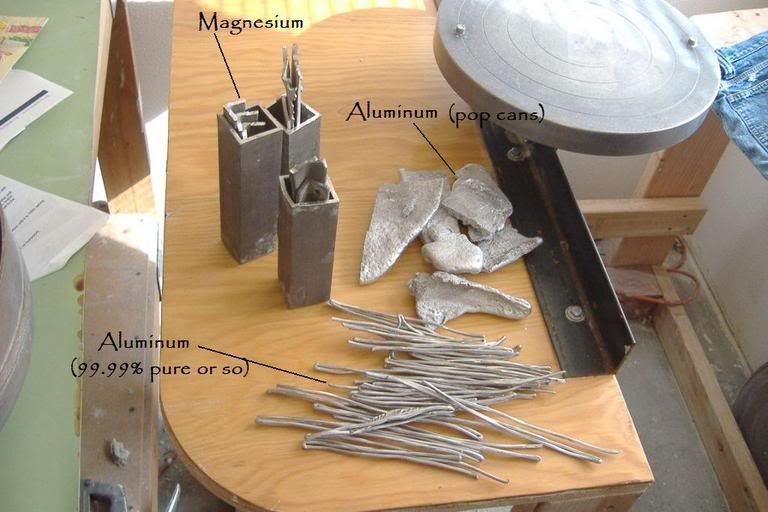
Next, I placed as much Al and Mg as I could in the crucible and melted them. Of course, I had trouble; the propane tank ran out, so I had to switch it
mid-melt, the Mg kept on catching on fire, etc. The Mg seemed to crumble instead of melting. Some parts seemed to be at a red heat and still not melt,
which would be strange. Here's a pic of the last piece being added to tthe crucible.
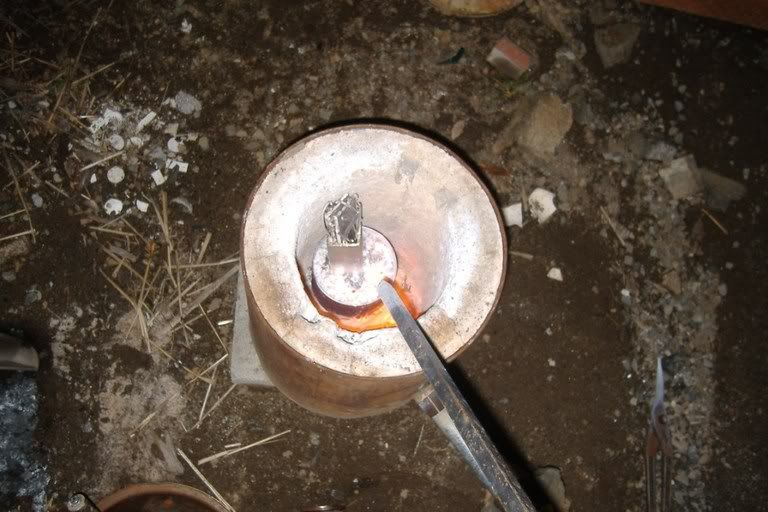
After everything was melted, I decided to just let it cool, and almost perfectly covered the steel can "crucible" with its lid, but the magnalium
wouldn't behave. It kept on burning with a propanish flame for a while (dissolved hydrogen), and continually oozed out of the crucible, constantly
igniting in spots.
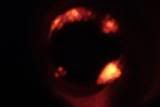
After about 45 minutes of cooling, it was still oozing and being generally annoying, and so I dumped sand on top of the crucible. That stopped it for
a few minutes, then it heated up again, so I added ice cubes to the furnace (not directly in the crucible) to cool it down.
That didn't stop it either, so eventually I just used a hose to add water to the furnace. Of course there was tons of steam, but eventually I just
sprayed water into the crucible and everything cooled down nicely. (I know Mg reacts with water violently, but most of the cooling was from the
outside, so by the time water hit the Mg, it was too cold, and there was too much water to keep it burning.)
The crucible fizzed for 20 minutes or so and I smelled ammonia- magnesium nitride must have formed, which makes sense.
I'll take apart the crucible next and add more pictures.
Cy
[Edited on 8-4-2006 by Cyrus]
|
|
Cyrus
Hazard to Others
 
Posts: 397
Registered: 24-4-2004
Location: Ancient Persia
Member Is Offline
Mood: No Mood
|
|
The Result
Ok, so I made a new post when I didn't really have to. 
After at least an hour, the magnalium was still fizzing and I smelled ammonia for sure and something like phosphine.
The rough chunk of magnalium after a bit of washing.
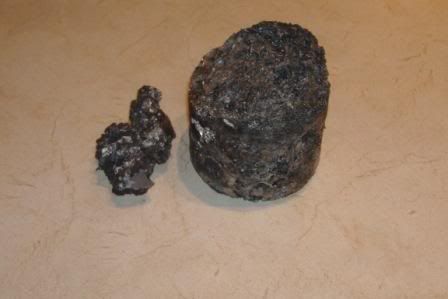
After a wire-brushing.
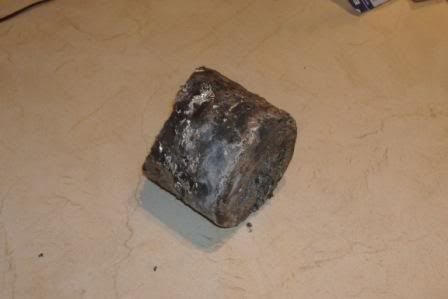
Cracking the thing open. This is the shiniest "natural" thing I have seen in my entire life! (ie no polishing, sandblasting, etc.) Woot!
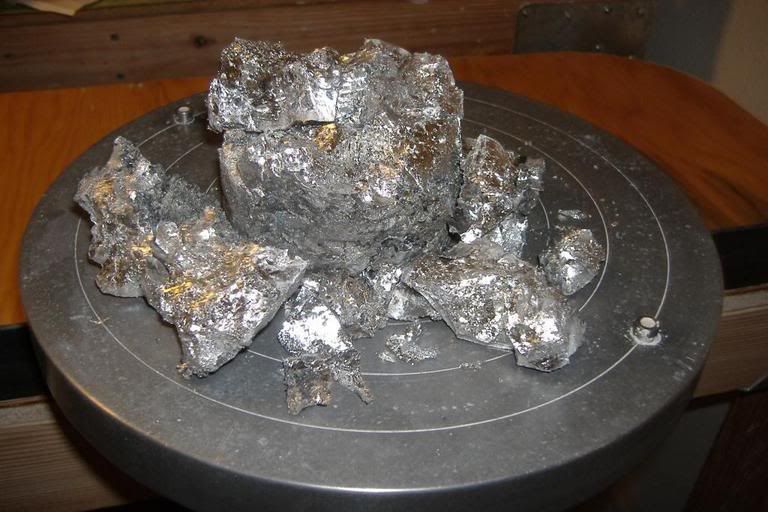
I'm sorry if I've inundated you with too many pictures. I love digital cameras. 
Edit- To make this post useful... If I were to do this "reaction" again, I would first melt the flux, then melt the Al, then shut the burner off and
add Mg. This time I added everything at once and then heated, causing needless oxidation of the magnesium. The flux was also AWOL; I never noticed
any. I suppose I didn't add nearly enough flux. (I used about 5-10 g each of CaCl2 and NaCl; there's no need to be too precise about it.)
Cy
[Edited on 8-4-2006 by Cyrus]
|
|
IrC
International Hazard
   
Posts: 2710
Registered: 7-3-2005
Location: Eureka
Member Is Offline
Mood: Discovering
|
|
Mad Science at it's best, great work Cyrus.
|
|
Mr. Wizard
International Hazard
   
Posts: 1042
Registered: 30-3-2003
Member Is Offline
Mood: No Mood
|
|
It looks like everything goes as planned until it comes time to turn off the fire and let things cool down, right? I would suggest that after the
components have been melted and mixed, you cover the air intake of the furnace with clay, mud, aluminum foil or whatever, and leave enough natural gas
or propane flowing to maintain a flame at the top of the furnace. While this flame is burning , without any venturi mixed air, slide a cover over the
top of the furnace, leaving only a small opening , and throttle down the gas at the same time. You should end up with a small flame over the opening
(don't let it go out), and an effectively inert gas over the melted magnalium. Maintain the flow of gas until the metal has cooled enough to preclude
ignition. Propane or natural gas should be an effective and cheap 'inert' atmosphere for these metals. The flow only has to be enough to keep air from
leaking in, and to maintain ignition of the vented gas.
|
|
12AX7
Post Harlot
   
Posts: 4803
Registered: 8-3-2005
Location: oscillating
Member Is Offline
Mood: informative
|
|
Note that magnalium melts almost at the same temp as zinc, it's essentially eutectic. You can get away with a much lower temperature once you've
added some magnesium to the melt, which is hard because it takes temp to dissolve the magnesium in the first place.
Tim
|
|
Cyrus
Hazard to Others
 
Posts: 397
Registered: 24-4-2004
Location: Ancient Persia
Member Is Offline
Mood: No Mood
|
|
Mr. Wizard, I like the idea of keeping a reducing atmosphere in the furnace... I decided not to try that for 2 reasons- I didn't think of that exact
idea, and explosions are a possibility (I wanted to eat dinner, not sit in the cold watching a cooling furnace).
I tried sealing the burner port with kaowool and the exhaust hole with a snug tin can, and it greatly slowed down the burning, but it took forever to
cool...
Edit- 12AX7, I noticed that the magnalium has a much lower melting point than Al but didn't capitalize on that. (I put both metals in at once in the
hope that they would form a eutectic, but they decided not to- not enough contact I guess.) Perhaps it would be best to make a small "heel" or puddle
of magnalium, then add Mg and Al while heating.
In any case, I doubt I'll be needing any more magnalium any time soon. Next
I've got to build a ball mill. (and finish my PbO2 electrodes and perchlorate electrolysis cell, and all those wonderful projects.) I bet I could
also get Al powder by ball milling Al turnings....
Cy
[Edited on 9-4-2006 by Cyrus]
|
|
Zinc
Hazard to Others
 
Posts: 472
Registered: 10-5-2006
Member Is Offline
Mood: No Mood
|
|
A little off topic but will Mg or Al dissolve bronze or brass?
|
|
12AX7
Post Harlot
   
Posts: 4803
Registered: 8-3-2005
Location: oscillating
Member Is Offline
Mood: informative
|
|
Sure, why?
|
|
Zinc
Hazard to Others
 
Posts: 472
Registered: 10-5-2006
Member Is Offline
Mood: No Mood
|
|
Quote: | Originally posted by 12AX7
Sure, why? |
I thought that I could use a crucible made of it (I don't know if it is made of bronze or brass) to make a small amount of mangalium.
|
|
garage chemist
chemical wizard
   
Posts: 1803
Registered: 16-8-2004
Location: Germany
Member Is Offline
Mood: No Mood
|
|
I made magnalium in a steel crucible (30ml, with lid) over a bunsen burner.
Melt the Al first, then stir in the Mg (it dissolves). A bit of stirring is important, if you dont do it the metals will not mix and the alloy will
not be homogenous.
|
|
ciscosdad
Hazard to Self

Posts: 76
Registered: 6-2-2007
Member Is Offline
Mood: Curious
|
|
Some Years ago I made myself some Magnalium using a steel crucible and a propane/air torch. The crucible was of 6mm hot rolled steel.
I did not bother with flux. I made a loose flat lid for the crucible with a 20mm hole in it. I then introduced a slow stream of propane through a 13mm
copper pipe. (another small propane bottle required) and the excess gas simply burned off around the entry hole.
This suppressed the burning of the magnalium and much of the oxidation of the aluminium. There was a garlicy smell to the Magnalium which at the time
I assumed to be some reaction with the stenching agent in the propane, but I expect 12AX7 is correct.
|
|
Texium
|
Thread Moved 19-11-2023 at 11:48 |
|