Pages:
1
2 |
JJay
International Hazard
   
Posts: 3440
Registered: 15-10-2015
Member Is Offline
|
|
Fitting a Ground Glass Joint to a Steel Plate
Has anyone ever managed to fit standard taper glassware to a steel plate?
I have been trying to come up with a good way to do it... the easiest way I can think of would be to drill a hole in the plate and fit a tubular PVC
or cork gasket around a glass tube with a standard taper joint and jam it into the hole, but this solution is not ideal in terms of solvent and
temperature resistance.
Wrapping the standard taper tube with lots of teflon tape might work a little bit better... I can't shake the idea that there is a simple and obvious
solution that I'm not thinking of.
|
|
Corrosive Joeseph
National Hazard
  
Posts: 915
Registered: 17-5-2015
Location: The Other Place
Member Is Offline
Mood: Cyclic
|
|
Acquire two brew-shop rubber bungs (the ones with holes in) and 60mm of 10mm dia. 1mm wall stainless tube.
Something like this.........
https://www.ebay.co.uk/itm/STAINLESS-STEEL-TUBE-10MM-OD-X-8M...
Place the 2 bungs wide-end to wide end and push the 60mm stainless tube through the holes which are now lined up.
(Think of two cones, bottom to bottom)
Drill a hole about 28-30mm in your plate and file the edges with a round file.
Push your assembled bungs through, and about where they meet will make an excellent seal.
Get a female 29/32 to female 29/32 adaptor and push on top.
Now this will take any NS29 male fitting
I have used this technique very successfully to make 500mm fractionating columns out of 32mm stainless steel tube.

/CJ
Being well adjusted to a sick society is no measure of one's mental health
|
|
OldNubbins
Hazard to Others
 
Posts: 136
Registered: 2-2-2017
Location: CA
Member Is Offline
Mood: Comfortably Numb
|
|
I believe ground glass tapers are 1:10 which is about 5.72° total included angle. There are tapered drills and reamers out there that will get you
pretty close.
I wanted to grind some tapers on some old bottles and found that those reverse-twist screw extractors have just about the right angle to them. I
loaded it up with valve grinding compound and ground the joint in a drill press with the bottle in a little tub of water.
|
|
JJay
International Hazard
   
Posts: 3440
Registered: 15-10-2015
Member Is Offline
|
|
Quote: Originally posted by OldNubbins  | I believe ground glass tapers are 1:10 which is about 5.72° total included angle. There are tapered drills and reamers out there that will get you
pretty close.
I wanted to grind some tapers on some old bottles and found that those reverse-twist screw extractors have just about the right angle to them. I
loaded it up with valve grinding compound and ground the joint in a drill press with the bottle in a little tub of water. |
I wonder if something like that could be gotten to work with PTFE... though I suspect that PTFE is very hard to machine....
Quote: Originally posted by Corrosive Joeseph  | Acquire two brew-shop rubber bungs (the ones with holes in) and 60mm of 10mm dia. 1mm wall stainless tube.
Something like this.........
https://www.ebay.co.uk/itm/STAINLESS-STEEL-TUBE-10MM-OD-X-8M...
Place the 2 bungs wide-end to wide end and push the 60mm stainless tube through the holes which are now lined up.
(Think of two cones, bottom to bottom)
Drill a hole about 28-30mm in your plate and file the edges with a round file.
Push your assembled bungs through, and about where they meet will make an excellent seal.
Get a female 29/32 to female 29/32 adaptor and push on top.
Now this will take any NS29 male fitting
I have used this technique very successfully to make 500mm fractionating columns out of 32mm stainless steel tube.

/CJ
|
This would work great for ethanol. Do you know anything about the solvent resistance of those bungs?
I was just thinking that I could get a stirrer through the plate by simply screwing a stirrer bearing together through a hole,and I found out that
large PTFE stirrer bearings have really large center holes! https://www.ebay.com/itm/Sizes-PTFE-Standard-Stopper-Teflon-...
A 10 mm hole might even be large enough for reflux....
|
|
Corrosive Joeseph
National Hazard
  
Posts: 915
Registered: 17-5-2015
Location: The Other Place
Member Is Offline
Mood: Cyclic
|
|
Quote: Originally posted by JJay  |
This would work great for ethanol. Do you know anything about the solvent resistance of those bungs?
I was just thinking that I could get a stirrer through the plate by simply screwing a stirrer bearing together through a hole,and I found out that
large PTFE stirrer bearings have really large center holes! https://www.ebay.com/itm/Sizes-PTFE-Standard-Stopper-Teflon-...
A 10 mm hole might even be large enough for reflux....
|
As far as I am aware the bungs are made of..........'rubber'
They worked well........... Forming a very good flexible seal with glass and metal.
I even distilled gasoline through that column many times and they put up a good fight.......!!
And they are so cheap, it is cake to just pull the joint apart, replace the rubbers, and off ya go again.
I got lost when you mentioned the stirring, I am sure it is possible.
Just unsure what exactly you are trying to do..........
The 10mm hole was good enough for fractionation, which is kind of like reflux.
It would allow plenty of liquid back into the 1 litre flask, which would often happen quite noticeably during 'warm-up'.
/CJ
Being well adjusted to a sick society is no measure of one's mental health
|
|
Chemetix
Hazard to Others
 
Posts: 376
Registered: 23-9-2016
Location: Oztrayleeyah
Member Is Offline
Mood: Wavering between lucidity and madness
|
|
What exactly does the OP want to achieve? If it's a joint you need to connect to a steel vessel then a local engineer/ machinist will tun up a 1:10
tapered joint for you to weld to whatever it is you want to connect to. Otherwise a compression fitting can be used with an O- ring to seal a glass
tube, I've done this many a time.
Recently I had to connect a glass column to a KF clamp fitting, so a glass tube was modded to make an O-ring groove in the glass tubing and then
inserted into a straight stainless tube on the clamp fitting.
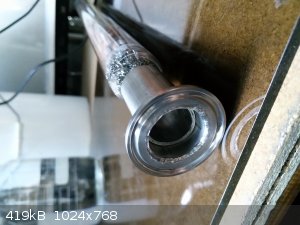
Stupid file software refuses to rotate this right 90 to make a normal pic.
anyway...you get the idea
|
|
unionised
International Hazard
   
Posts: 5128
Registered: 1-11-2003
Location: UK
Member Is Offline
Mood: No Mood
|
|
It's easy enough to cut a 1 in 10 taper on a piece of steel, then put it into (or onto) a ST glass joint.
It's also easy to break the glass when the metal heats or cools and different thermal expansions come into play.
A flexible gasket of some sort is a really good idea.
[Edited on 27-10-18 by unionised]
|
|
JJay
International Hazard
   
Posts: 3440
Registered: 15-10-2015
Member Is Offline
|
|
I would like to use a small steel drum with standard taper glassware, up to 3-4 pieces at a time. I've used compression fittings before for putting a
condenser on a pressure cooker for distillations, but they're not ideal for attaching stirrer bearings, addition funnels, columns, and Claisen
adapters.
While it would be tempting to just such a device for e.g. distilling entire kegs of beer, I actually don't plan on using it for ethanol. I would like
to use it as a reaction vessel, for steam distillations, for distilling solvents, etc.
I think O-rings would work well, but the high-end fluoropolymer types that resist common solvents are very expensive.
[Edited on 27-10-2018 by JJay]
|
|
CobaltChloride
Hazard to Others
 
Posts: 239
Registered: 3-3-2018
Location: Romania
Member Is Offline
|
|
In this video, you can see how NileRed was able to make an air-tight connection between the paint can and a male ground glass joint.
https://www.youtube.com/watch?v=X10VZeQmFDo&t=135s
[Edited on 27-10-2018 by CobaltChloride]
|
|
digga
Harmless
Posts: 44
Registered: 11-6-2018
Member Is Offline
|
|
I have used a paint can lid with a 14/20 male to 24/40 female adapter. I punched a hole in the middle of the lid top. Then I loosely fitted the male
end into the hole and put a large ring of high temp putty around it:
Permatex 84333 High Temp Epoxy Stick
then I spray painted the works with high temp grill paint.
I have used the apparatus to create benzene by decarboxylating salicylic acid over a propane flame three times.
no leakage.
[Edited on 27-10-2018 by digga]
|
|
Elrik
Hazard to Self

Posts: 52
Registered: 1-9-2018
Member Is Offline
|
|
I've toyed with the idea of attaching ground glass to metal, as well.
As stated, any direct contact would most likely result in broken glass.
My best idea to date was a protective teflon sleeve. I'd make a metal connector that is a 1:10 taper, then a teflon reducing sleeve to go in that
where the wall thickness is a minimum of 3mm and its taper is 1:10 inside and out and the inside is some standard glass size like 24/29, I would then
join that to a short glass adapter/straight connector just in case the glass somehow did crack or became fused to the teflon. At least that way only a
cheap glass connector would be ruined and not a fractionating column or worse. A stainless steel keck clip could be modified with springs to attach to
the metal or, if machine work is free, a cap could be created to screw on over the teflon insert to allow a standard keck clip to attach it to the
glass.
I wouldnt be comfortable using it at 150° and would never go above 200°.
If your machinist has never cut teflon before, suggest he uses a very sharp cutter and an emulsion of equal parts petroleum and liquid dish soap. The
one time I made teflon parts that worked well.
|
|
JJay
International Hazard
   
Posts: 3440
Registered: 15-10-2015
Member Is Offline
|
|
Quote: Originally posted by Elrik  | I've toyed with the idea of attaching ground glass to metal, as well.
As stated, any direct contact would most likely result in broken glass.
My best idea to date was a protective teflon sleeve. I'd make a metal connector that is a 1:10 taper, then a teflon reducing sleeve to go in that
where the wall thickness is a minimum of 3mm and its taper is 1:10 inside and out and the inside is some standard glass size like 24/29, I would then
join that to a short glass adapter/straight connector just in case the glass somehow did crack or became fused to the teflon. At least that way only a
cheap glass connector would be ruined and not a fractionating column or worse. A stainless steel keck clip could be modified with springs to attach to
the metal or, if machine work is free, a cap could be created to screw on over the teflon insert to allow a standard keck clip to attach it to the
glass.
I wouldnt be comfortable using it at 150° and would never go above 200°.
If your machinist has never cut teflon before, suggest he uses a very sharp cutter and an emulsion of equal parts petroleum and liquid dish soap. The
one time I made teflon parts that worked well. |
I would probably be machining/welding/fabricating myself, and tasks like welding stainless steel and machining PTFE require actual skills and
knowledge, so they are probably out of the question for me. That said, PTFE is probably good at 250 C as long as you take into account its high
thermal expansion and don't expose it to strong alkali (which will also eat glass at that temperature).
This is what I will probably end up actually doing. It may require lots of PTFE tape, but there are few downsides. It could probably hold a strong
enough vacuum to crush the paint can.
Quote: Originally posted by digga  | I have used a paint can lid with a 14/20 male to 24/40 female adapter. I punched a hole in the middle of the lid top. Then I loosely fitted the male
end into the hole and put a large ring of high temp putty around it:
Permatex 84333 High Temp Epoxy Stick
then I spray painted the works with high temp grill paint.
I have used the apparatus to create benzene by decarboxylating salicylic acid over a propane flame three times.
no leakage.
|
I could see something like that working with zinc powder... I considered using a silicone gasket maker, but the silicones I looked at don't appear to
be very solvent resistant, and I'm not sure how flexible they are at high temperatures.
FFKM is a fluoropolymer that can be used at temperatures up to 325 C, and it appears to have better compatibility than stainless steel with most
substances, but FFKM is very expensive.
If anyone makes known a cheap source of FFKM o-rings, I am sure that generations of amateur chemists will sing your praises.
[Edited on 27-10-2018 by JJay]
|
|
largenumbergoeshere
Harmless
Posts: 17
Registered: 25-7-2018
Member Is Offline
|
|
I find the best solution is to use high temprature silicon to bond metal to a glass joint from a broken flask. I've distilled water, gasoline and
small ammounts of nitric acid with sucsess. It does however react quickly with concentrated sulfuric acid. It does make somewhat fragile of a
connection because silicon sets a bit soft but you don't have to deal with heat expansion problems and it seals quite well, requiring only a keen eye
to join it without much trouble.
Once again it is a bit soft so it won't take much pressure but for general purposes I think it's the best option.
|
|
Corrosive Joeseph
National Hazard
  
Posts: 915
Registered: 17-5-2015
Location: The Other Place
Member Is Offline
Mood: Cyclic
|
|
Hylomar Blue is the industry standard fuel resistant RTV..........
https://www.ebay.co.uk/itm/Hylomar-BLUE-Universal-Gasket-Joi...
It worked well sealing fuel injection intake manifolds to cylinder heads when fitting composite thermal gaskets to race engines when nothing else
would do

/CJ
Being well adjusted to a sick society is no measure of one's mental health
|
|
largenumbergoeshere
Harmless
Posts: 17
Registered: 25-7-2018
Member Is Offline
|
|
I wouldn't count on it being resistant to acids though.
|
|
JJay
International Hazard
   
Posts: 3440
Registered: 15-10-2015
Member Is Offline
|
|
For sulfuric acid resistance, you could probably use a lead gasket, but lead melts at around 325 C and won't resist nitric acid, so FFKM really is
better. Of course, the steel drum probably won't resist nitric acid either.
Hylomar is some kind of urethane compound, so it looks like it resists heptane, but I'm not sure how it does against other solvents. I bet it holds up
great against refluxing hexane.
Chemetix has the best solution I've seen so far. Now where to get those fancy o-rings....
|
|
SWIM
National Hazard
  
Posts: 970
Registered: 3-9-2017
Member Is Offline
|
|
Some old small Virtis freeze dry flasks have a flat flange connection.
The lid for one of these is just a ground joint that flares out to a flat ground flange about 50 to 60 mm across.
To get an image of what I mean search for: Virtis flask ground joint on Ebay.
I bet one of those flat lids would work with a thick enough steel plate that it wouldn't warp. Maybe clamp it to a pipe flange.
|
|
JJay
International Hazard
   
Posts: 3440
Registered: 15-10-2015
Member Is Offline
|
|
Those Virtis freeze dry flask flanges do look like they could work well with a flange in the right size: https://www.ebay.com/itm/VirTis-Freeze-Dry-Flask-Lyphilizer-...
It might even be possible to find a pipe flange (or turn a manifold) in the right size to clamp on a reaction vessel head, but that could be
expensive.
|
|
Mr. Rogers
Hazard to Others
 
Posts: 184
Registered: 30-10-2017
Location: Ammonia Avenue
Member Is Offline
Mood: No Mood
|
|
I'm glad you brought this up.
I have a need to connect 24/40 GG to NTP pipe thread fittings.
I figured there must be something **really** obvious I'm missing, so I've been too afraid to ask...
|
|
happyfooddance
National Hazard
  
Posts: 530
Registered: 9-11-2017
Location: Los Angeles, Ca.
Member Is Offline
Mood: No Mood
|
|
At least for operations at atmospheric pressure, I have had good luck with copious amounts of ptfe tape. I use it routinely for the "solvent can"
technique famous around these parts, as well as to join copper tubing to glass standard tapers. I always use lots of tape, it costs me about a dollar
per joint sometimes. Also you have to be very aware of differing thermal CoE's and obviously stay within the operating temp of ptfe (couple/few
hundred celcius).
[Edited on 10-30-2018 by happyfooddance]
|
|
macckone
Dispenser of practical lab wisdom
   
Posts: 2168
Registered: 1-3-2013
Location: Over a mile high
Member Is Offline
Mood: Electrical
|
|
Permatex makes a clay/sodium silicate compound for sealing muffler leaks.
It is literally just clay, water and sodium silicate.
A flat flange will work but you may want to use some of that mix as a gasket.
You can also get viton and ptfe sleeves made for sealing ground glass joints.
united glass tech sells the ptfe variety.
They are thin but should allow the glass to slide without breaking against a 1:10 metal joint.
They also have lower temps than the clay.
|
|
BakingBrownies
Harmless
Posts: 4
Registered: 14-11-2018
Member Is Offline
|
|
I've been working on fitting a joint to an aluminum plate so I'm not sure if this idea will be of much use.
If the plate is thick enough all you need to do is create a hole the will perfectly fit (very close) the base of the joint then fix and seal the joint
using some kind of epoxy (between the joint and the plate).
After that, you will probably want some support which you can do on the outside of the plate using more epoxy. In my case, I will use hot glue because
the plate will never get very hot.
you could use Teflon tape for a seal between the joint and the plate and then load up with the hot glue to hold it in place.
|
|
JJay
International Hazard
   
Posts: 3440
Registered: 15-10-2015
Member Is Offline
|
|
The only major problem with that plan is that aluminum has a much higher coefficient of expansion than borosilicate glass. I am not sure about the
chemical resistance of epoxy, but I don't think it resists common solvents.
|
|
DavidJR
National Hazard
  
Posts: 908
Registered: 1-1-2018
Location: Scotland
Member Is Offline
Mood: Tired
|
|
Quote: Originally posted by JJay  | I am not sure about the chemical resistance of epoxy, but I don't think it resists common solvents. |
Can confirm this - I tried to repair a porcelain buchner funnel with epoxy and it degraded fairly rapidly and fell apart after the first use. I forget
what solvents I was using at the time but it was nothing exotic, probably either methanol or isopropanol.
|
|
markx
National Hazard
  
Posts: 646
Registered: 7-8-2003
Location: Northern kingdom
Member Is Offline
Mood: Very Jolly
|
|
Quote: Originally posted by JJay  |
I wonder if something like that could be gotten to work with PTFE... though I suspect that PTFE is very hard to machine....
|
PTFE is stupid easy to machine....just use a honed steel tool. Carbide is ok for hogging off heavy cuts on PTFE, but for precision work a nice honed
steel cutter is best.
And keep an eye on the cut off swarf, the stuff comes off in one single continuos ribbon that likes to wrap itself around the spindle chuck and
workpiece. Luckily it is soft and does not cut ....unlike stainless chip. This stuff is the razor wire from hell, almost cut my finger off once trying
to pick a stuck chip off the workpiece in a hurry. Should have known better, pain is a good teacher 
I trust you seek to do something of the following nature:
A coupling machined out of PTFE for fitting a conical glass condenser to a metal plate....
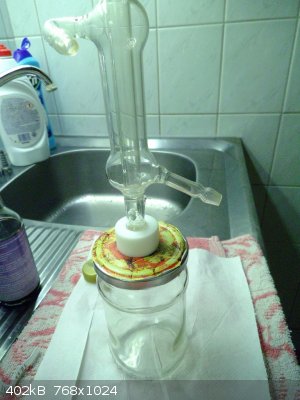
[Edited on 15-11-2018 by markx]
Exact science is a figment of imagination.......
|
|
Pages:
1
2 |